
1 minute read
FIBERBOARD PRODUCTS
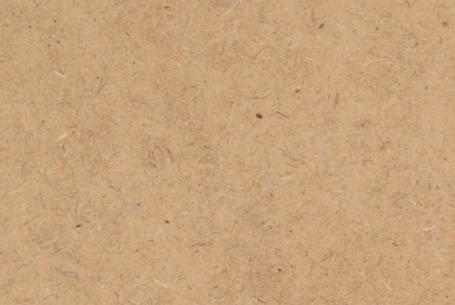
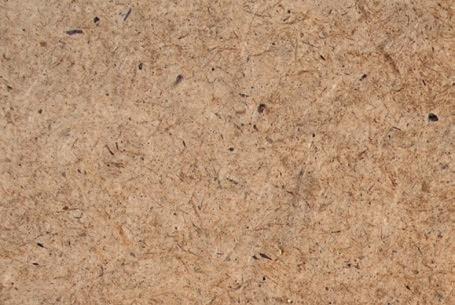
HARDBOARD/HDF MEDIUM DENSITY FIBERBOARD (MDF) PARTICLEBOARD (LDF)
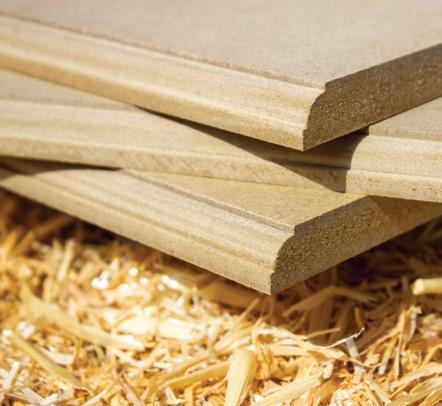
With solid wood becoming more scarce and expensive to use in recent years, and the increased emphasis on using more sustainable and environmentally friendly materials, fiberboard has rapidly grown in popularity and has replaced many solid timber products in the building and construction industries.
Made from the leftovers and byproducts of working with wood, the more-affordable fiberboard has also found a place in budget-conscious projects both large and small. Fiberboard products have changed the entire industry.
These fiberboard products are most often used as substrates and a basis for various surfaced panels. Fiberboard can be coated in a wide variety of materials, colors and patterns. The most popular coating traditionally has been that of a wood-look veneer, but recent advances in technology, scanning and printing have opened the world to limitless surfacing possibilities.
The use of fiberboard is very popular in construction and various other applications, from ready-to-assemble furniture to boat building.
Some form of fiberboard has been around for more than a century, but a happy accident led to a standardized method of creating the material. William Mason, an inventor and friend of Thomas Edison, sought a way to utilize the huge amounts of wood chips and shavings left over and discarded by booming lumber mills. The story goes that one evening in 1925, he forgot to shut down his equipment and the next morning, he discovered a thin, durable sheet had been created. He then played with the method, using pressure, heat and resin and patented what became known as Mason’s Method to create this thin, durable product—a method still used today.
Mass production of fiberboard took a few more decades to establish, but today, manufacturers continue to innovate and find new ways to create and use this product.
Traditionally, the resin and binders used to create fiberboard contained formaldehyde, but manufacturers today are increasingly finding alternative methods and materials to make the products.
Some manufacturers now offer no-added formaldehyde (NAF) products for customers who want to minimize their exposure to the potential volatile organic compounds (VOCs) that can “off-gas” out of wood panels into the breathable air.