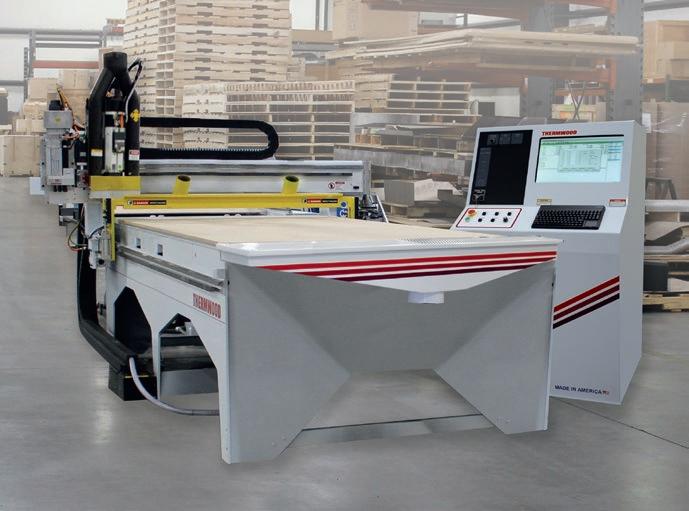
10 minute read
The Push of a Button
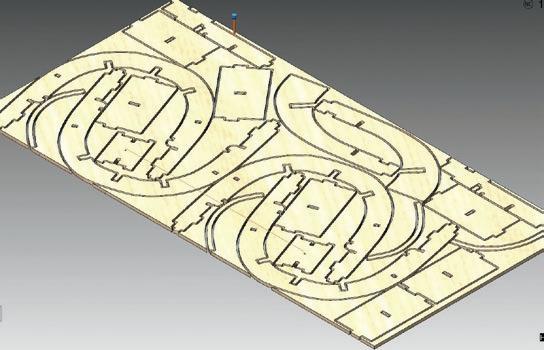
CNC TECHNOLOGY IS ONLY GETTING BETTER, SAVING MANUFACTURERS TIME, MONEY, AND RESOURCES IN THE PROCESS
BY AMBROSIA BRODY

CNCmachinery and CNC routers continue to disrupt the design and woodworking industries as these machines make creating unique and intricate designs as easy as a push of a button.
Uses of these machines are vast. CNC mills are powerful thanks to a high torque, making them ideal for harder materials, such as iron, steel, titanium, and aluminum, although they can also cut other materials like wood and plastic. These machines share the same pros as a CNC router, but they work at a slower speed. But what CNC machines lack in speed they make up for in precision, accuracy, and strength. Whereas, CNC routers are known for their highspeed spindles and ability to cut wood, plastic, aluminum, MDF, and larger sheet materials and non-metals, such as foam.
Shops need to consider the pros and cons of each machine and router before hitting purchase. Surface & Panel spoke with a few manufacturers and distributors to get the latest information on CNC machinery, routers, and software, to learn how companies are using this software and technology to their advantage.
Gone are the days of “measure twice, cut once,” for those companies that have invested in the power of CNC capabilities. “This time-consuming practice of manufacturing often did not utilize material effectively and led to inaccurate parts,” explained Kenny Belfatto, national sales manager, CIM-Tech.com inc. “Today, assemblies can be modeled in 3D, and efficiently nested onto sheets, to provide the best material yields. With a CNC machine and good
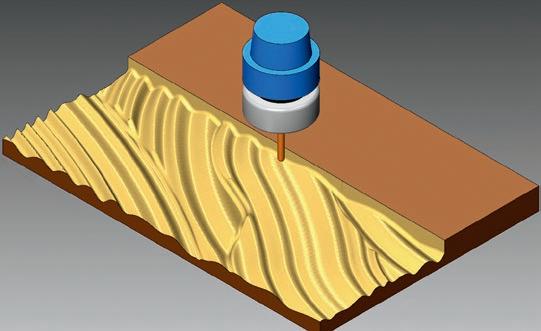
CNC-SOFTWARE SOLUTIONS FROM CIM-TECH
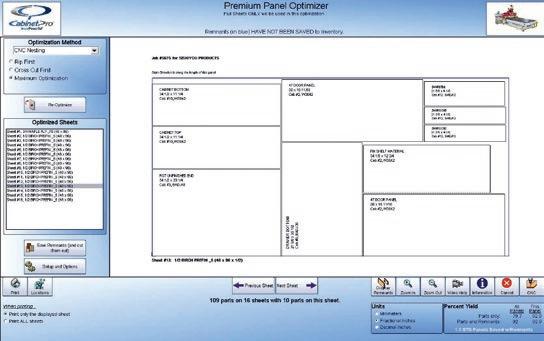
FRANK D. JIMENEZ, PRESIDENT OF CABINET PRO LLC
LEFT: CNC OPTIMIZATION FROM CABINET PRO. BELOW: SHOPBOT’S TOOL CAROUSEL ALLOWS FOR UP TO 16 DIFFERENT TOOLS TO BE SWAPPED AUTOMATICALLY INTO THE SPINDLE DURING A CUT. THE CAROUSEL DROPS BELOW THE TABLE WHEN NOT IN USE, MAKING IT MUCH EASIER TO SLIDE MATERIAL ON AND OFF THE TABLE.
programming software, you will absolutely save time, money, and material compared to manual manufacturing methods.”
Efficiency, design precision, streamlined processes, and a large output are only a few reasons why these machines are all the rage in 2022. Ease of use and timesaving also make this technology a must-have for manufacturers.
“CNC routers save time and resources in two ways; because the operation of a CNC is automated, a carpenter is free to do assembly and finishing work while the machine is cutting out the next batch of parts,” said Brian Owen, chief operating officer, ShopBot Tools, Inc. “Because of the way that parts are laid out on a computer, material can be used more efficiently with more parts being cut on each sheet of material.”
Not to mention they are resource savers. Duane Marrett, vice president of marketing, Thermwood, said, “Our CNC routers save time and resources by efficiently machining the desired product and keeping track of any scrap material. This scrap, or ‘offal’ is then labeled and can later be re-used to get the best yield out of your material with the least amount of material waste.”
It's that time-saving feature that makes these machines so attractive. These automated routers save companies both time and resources in several ways as the machine frees up a carpenter’s time to focus on assembly and finishing work while the machine cuts out batches of parts, and more parts are being cut on each sheet of material thanks to this system.
“The other benefit of automation is reliability—the CNC can produce the same part all day long without ever getting tired or losing focus,” said Owen. “Once you've got your product designed, you can rely on the machine to consistently create high quality parts for the entire run of the product.”
As a manufacturer of CNC routers for more than 25 years, ShopBot understands what makes an effective CNC. “We've come a long way since the early machines,” Owen added. “Our current equipment uses a rigid gantry beam and linear rails from THK to

CONTINUED ON PAGE 42 ›
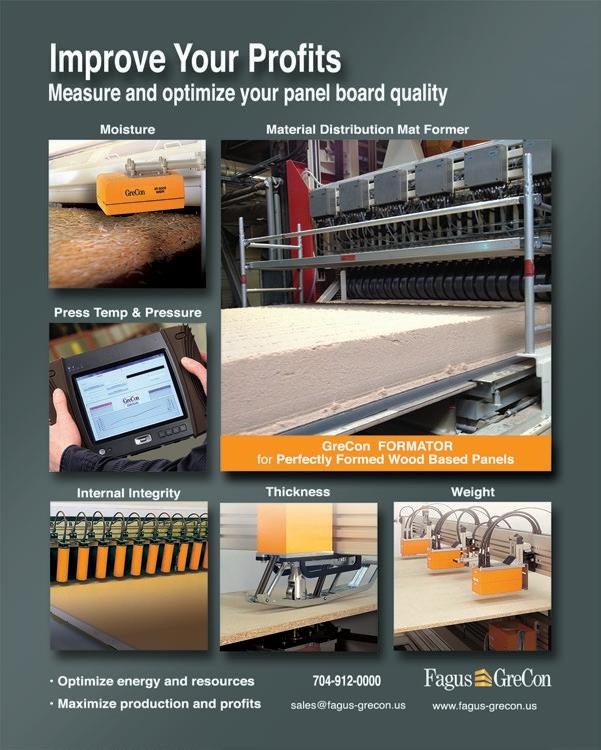
BRIAN OWEN, CHIEF OPERATING OFFICER, SHOPBOT TOOLS, INC.
‹ CONTINUED FROM PAGE 41
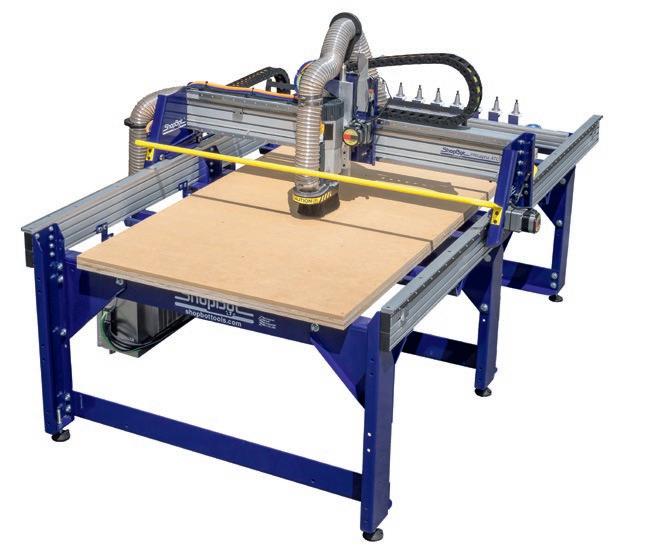
minimize vibration of the cutting head. The drive system employs alphaStep High Torque motors capable of 30IPS (1,800IPM) rapid rates and 12IPS (720IPM) feed rates—making it possible to process an entire sheet of plywood into typical cabinet components in under 10 minutes from the moment you hit ‘go.’”
Available with a range of cutting heads, including spindles capable of automatic tool changing and air powered drilling heads, ShopBot is also offering more CNC options. Owen said, “We have just recently begun expanding our options for cutting heads with a tangential oscillating knife and C-Axis-style aggregate heads available on machines now—and more options coming for high output shops like line boring heads. We're also working on upgrades to our Automatic Tool Change system, mounting the swappable tooling on a rotary carousel-which will allow for up to 16 different bits to be used with our typical 4'x8' ATC machine.”
As technology and software continues to evolve overtime, CNC routers can only get better.
Ken Frye, director of sales, KCD Software, noted, “A huge trend we’ve recently noticed is more CNC router companies offering auto labeling along with load and unload options for their nested-base routers. The more these options are available, the lower the cost is to the average consumer. By making these options available to the cabinet and closet industry, more companies will take advantage to help streamline their manufacturing processes.”
For instance, Thermwood recently released a new CNC machining center, the AutoProcessor 43, a complete, nested-based CNC routing system for machining cabinet boxes, custom furniture, and any nested type of sheet product automatically. “It simultaneously and automatically labels each part area on the sheet and automatically positions the sheet on the table,” said Marrett. “It machines the material while labeling the next sheet, simultaneously off-loads the finished parts and reloads the next sheet and continuously repeats this process to ensure rapid production.”
These days, distributors are focused on improving machine efficiency, streamlining processes, optimizing workflow and enhance the user experience.
“We have been working extensively on streamlining the model to machine process through complete automation, as well as some additional projects such as a five-axis programming solution and simulation,” said Belfatto, who noted the company recently completed a project for a CNC automation line that includes automatic robotic load and unload, automated sheet flipping, and label printing.
Companies that rely on these machines are also witnessing the return on investment, while others are incorporating the technology into their workshops.
“The companies that have CNC routers are purchasing more CNC routers,” Frye explained. “Smaller to mid-size companies that have held off from purchasing in the past are now buying CNC routers. After years of anticipating the increase in demand for CNC routers, the time has arrived where most cabinet or closet companies can and will buy a CNC router.”
And this technology continues to leave its mark on the industry.
“Probably the most notable way in which CNC routers impact the cabinet industry is by allowing small cabinet shops to easily compete with extremely large shops,” explained Frank D. Jimenez, president of Cabinet Pro LLC. “A cabinet shop with a CNC router and software can perform far greater than those shops without a router, regardless of shop size.”
“Cut Ready-capable machines have made a huge impact in the industry,” Marrett added. “They have allowed shops to get into CNC without the typical steep learning curve of trying to figure out the software and the machine. With Cut Ready machines, like the Cut Center, the machine doesn't require a skilled programmer. The operator simply tells it what they want to make via either a simple
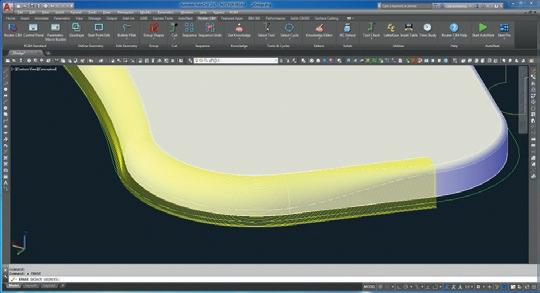
touch screen interface (or by sending jobs from eCabinet Systems), and the machine makes it.”
This capability removes any extensive programming knowledge or machine training as Cut Ready machines essentially walk the operator through the entire process. It’s that user-friendly technology and software that makes CNC machining and routing so easy to use. Rather than spend funds, time and resources on extensive training, operators need only to do their research to find the best CAD/CAM software for their individualized needs.
“It has been said that a new CNC machine is only as good as your ability to program it. Modern CNC machines can have complex features like multiple tables, spindles, tool changers, gang drills, various aggregates, programmable head spacing, automatic load and unload, on machine label printing, and much more. All of these features require an effective programming method. It is important to do your research on what it takes to program these amazing features when looking at a new CNC machine,” said Belfatto.
Utilization of an industry standard software, such as AutoCAD, is one option. According to Belfatto, this software makes it easier for employers to hire talent that’s capable of coming up to speed quickly with minimal training. “Our advanced nesting provides faster cycle times and higher nesting yields which saves material, that is in short supply, while maintaining high production efficiency,” he said.
Companies on the fence about whether to invest in CNC mills and CNC routing are advised to do their research when deciding on a machine or software. Asking questions is also key to ensuring that you’re investing in the right CNC software, router, or machine. Aside from the machine’s price tag, find out about the manufacturer’s service and support, reach out to those who own the machine to get a first-hand review, ask about replacement parts, training, and installation support. Another tip, “Always look at the number of steps to accomplish day to day tasks,” said Belfatto.
And be mindful of the software before purchasing.
“All shops, face frame and frameless, small and large, should seriously consider CNC machines and software,” Jimenez said. “And make sure the software you choose also provides solid and timely technical support, otherwise that software is of no value to you.”
Don Casebier, president, Bierson Corporation, added, “Software that is associated with heightening productivity, such as AutoDesk’s BIM (Building Information Modeling) software, CAM ComputerAided Manufacturing) and CAD (Computer-Aided Design) software, can enhance a company’s scalability.”
Whether your company is looking to upgrade its machinery or add a CNC mill or CNC router—or both—to its service offerings, rest assured both lower the risk of human error, save time, resources, and people power, while maintaining accuracy and quality. s p
For more information, visit cabinetpro.com, cim-tech.com, thermwood.com, shopbottools.com, kcdsoftware.com, and bierson.net.
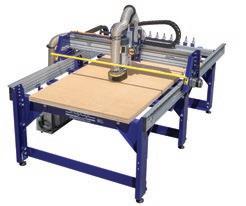
Panel Process Like a Pro Without the Pro Price Tag
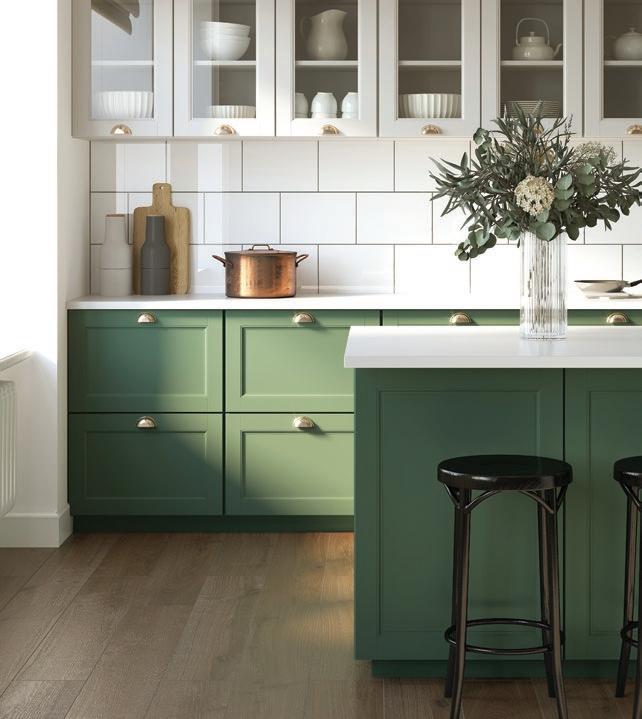
With a ShopBot CNC, you can increase production throughput while minimizing material handling. For example, you can drill shelf pin holes, cut rabbets and dados, and profile-cut the completed panel. The operator only needs to handle the full sheet once to load the machine, and then remove the perfectly cut parts that are ready for assembly.
Thanks to the affordability of ShopBot’s professional grade CNC tools, the technology of manufacturing cabinet boxes, doors, drawer fronts, shelves, and even countertops, is now well within the reach of smaller shops, not just large cabinet manufacturing facilities.
See our full line of tools at ShopBotTools.com. Then give us a call at 888-680-4466. We’ll find the tool that works best for your cabinet making needs.