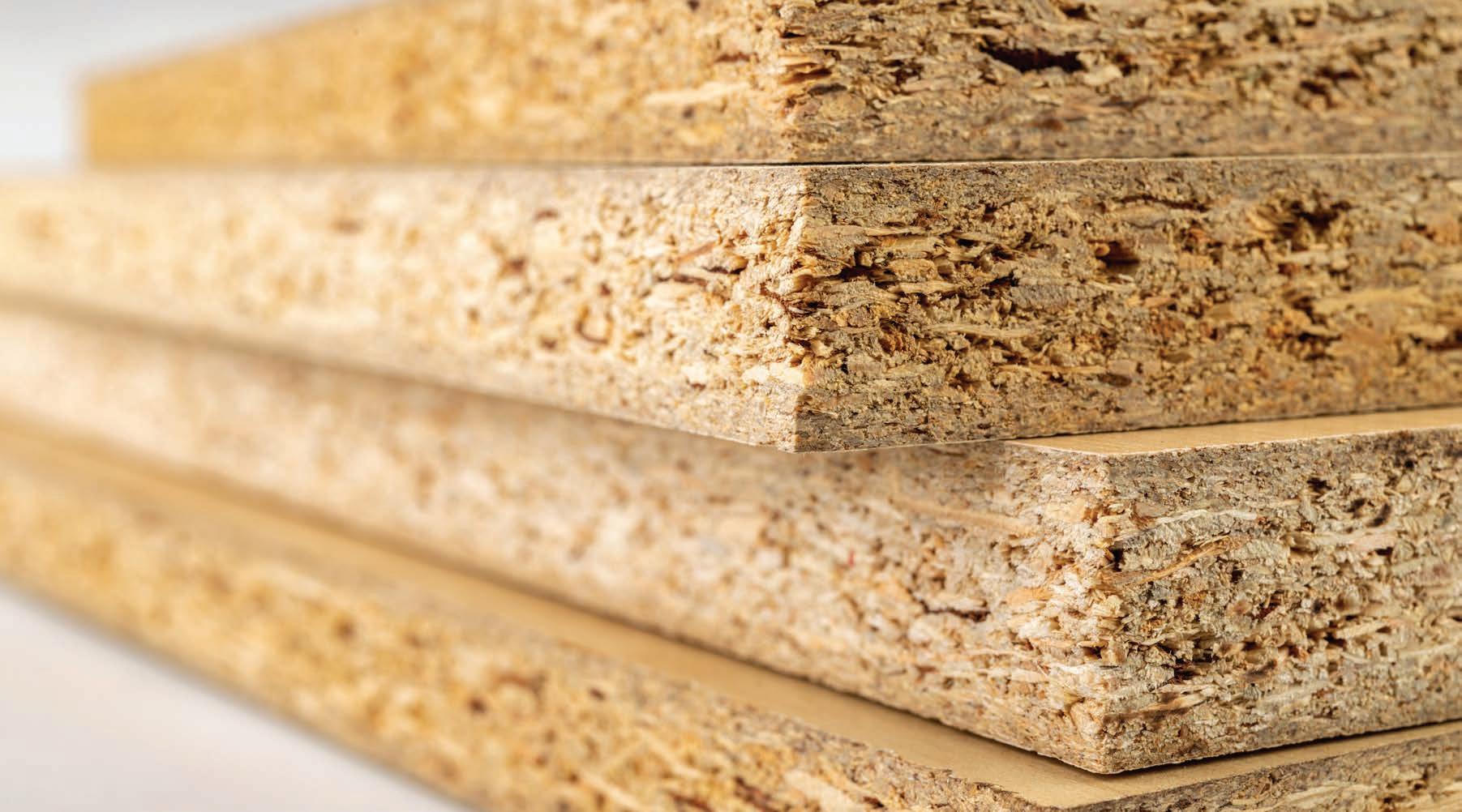
4 minute read
Green Giant:
WHY WOOD IS TODAY’S SUSTAINABLE NO-BRAINER
Sustainability is more than a buzzword these days but runs the risk of being overused.
Companies are seeking to be as “green” or environmentally friendly as possible. The good news for the wood industry is that their products, including plywood, MDF and particleboard, are rapidly proving to have a negative net carbon footprint. This means that the carbon emitted in their production is more than offset by the carbon that is stored within the product and not released into the atmosphere.
Particleboard and MDF make up the bulk of today’s furniture production. These engineered products use wood chips and shavings that otherwise would be waste material, but have suffered from a negative environmental image due to some of the production processes that can emit problematic gases. But with stricter regulations and the introduction of formaldehydefree particleboard, this perception is rapidly changing.
With people all across the industry concerned about effects on the environment, many people and organizations are keeping a closer tab on this subject.
Jeff Easterling, president of the Northeastern Lumber Manufacturers Association, recently looked into just how sustainable wood is with Mississippi State University’s Dr. Rubin Shmulsky.
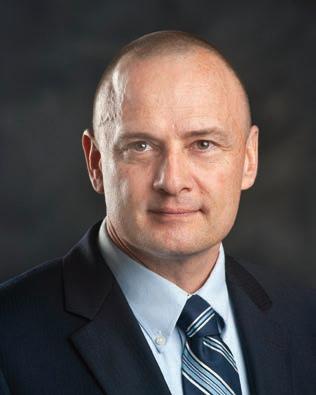
EASTERLING: Tell us who you are and what you do at Mississippi State.
SHMULSKY: At Mississippi State University, my role is that of professor and department head of the Sustainable Bioproducts (formerly Forest Products) Department. As professors, my colleagues and I teach, perform research, and provide technical assistance/Extension outreach to forest products-related stakeholders. This department, and Mississippi State University, are in the heart of the nation’s pine and mixed hardwood timber basket. For people who are passionate about sustainable forestry and wood products, this is among the best places on earth to work.
EASTERLING: What does the Department of Sustainable Bioproducts do?
SHMULSKY: The Sustainable Bioproducts Department seeks to educate the next generation of professionals regarding how to glean as much value as possible from the nation’s timber resource. We provide formal education for college students as well as short course- and workshop-type training opportunities for working people, either online or in-person. We try to meet people where they are. When we can make small accommodations regarding content delivery timing and location, we see much greater participation, particularly at the national level. We are also a strong research laboratory with targeted research focusing primarily on lumber yield, properties, and value; wood protection and preservation; automated wood identification; engineered wood composites; and nondestructive evaluation. The gulf-south part of the country is home to some of the nation’s most productive pine and hardwood forests. To keep this land base forested, landowners need robust and perpetual markets. Our personnel are passionate about these values. I’m personally very fortunate to get to work every day with people who share a deep commitment to these goals.
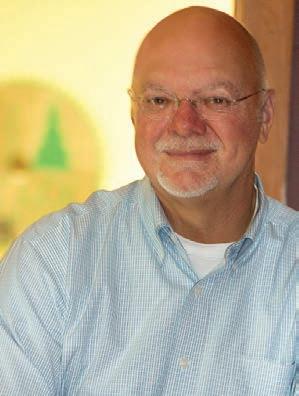
EASTERLING: What challenges do you see in the lumber industry right now?
SHMULSKY: One major challenge is rising interest rates. Lumber is routinely the largest market for timber and lumber markets are driven by housing starts. As interest rates rise, housing starts typically flatten. Two other major challenges are markets for small diameter-12–15-year-old-pine timber and structural products from underutilized hardwoods. Small diameter pine trees are produced as foresters seek to grow larger high-grade trees for sawtimber. Previously, these small trees were converted to pulp and paper. With increasing digital communications and less demand for paper, we are challenged with developing economically viable products and markets from these small trees. The other big challenge is developing structural markets for hardwoods. NeLMA plays a key role in this effort because they write the rules for structurally graded oak, maple, hickory, and other hardwoods. As an example of market development, we are seeing a national effort to more thoughtfully evaluate the strength and stiffness of hardwood timbers that go into industrial matting–we are excited about the future opportunities.
EASTERLING: What lumber industry trends is your department watching?
SHMULSKY: One of the most promising trends is that of nondestructive evaluation. This technology lets one assess the strength and stiffness of a piece of wood–whether new or in-service. For railroad ties, utility poles, building products, engineered beams, other industrial products, this technology is key with respect to capturing the highest possible value at the time of production and for determining the point at which a wood member, structure, or building should be taken out of service and replaced. Nondestructive evaluation thus improves both value and safety. Our scientists get a great deal of satisfaction from knowing they are helping address national housing and infrastructure issues. Another major issue on the horizon is the increase of mass-timber construction. With larger and stronger engineered products, we can build taller structures and span greater distances, which continues to support wood-based architectural freedom.
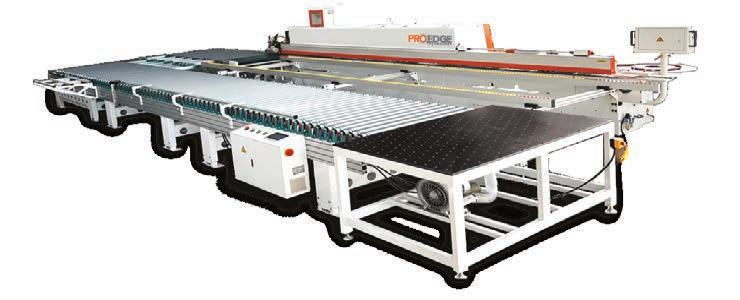
EASTERLING: Using the research lens, what do you see in the future of the lumber industry?
SHMULSKY: The Sustainable Bioproducts Department’s research program has a strong history and future commitment to working with external stakeholders. Among these, we are proud to claim industry producers, engineers and specifiers, user groups, trade associations, government agencies like the U.S. Forest Service, Agricultural Research Service, and Department of Defense. During the past six years, our department has worked closely with several grading agencies like NeLMA and Timber Products Inspection, along with sawmills, mat producers, engineers, lift planners, and utility companies to form the North American Matting Association [which] brings together access to mat-related stakeholders to help improve the economic and utility value of mats while also improving jobsite safety and environmental protection. My sense is that this effort will continue and grow as the Association works to develop minimum voluntary standards for timber mat production [and will result in] speaking with a more unified voice and working toward the common goal of sustainable production of timber products. With that as a backdrop, I’ve never been more proud or excited to be a part of the forest products research and development sector. s p