
6 minute read
LEADING THE WAY IN REMANUFACTURING
For over three decades, Lexmark has been at the forefront of promoting sustainability and circular economy principles in the printing industry. With a steadfast commitment to reducing environmental impact, Lexmark has taken innovative strides in Original Equipment Manufacturer (OEM) remanufacturing. Through initiatives like the Lexmark Cartridge Collection Program (LCCP), we have not only set an example but also actively developed the ways OEMs can take steps to a more sustainable future, through our role as print industry leaders on the European Remanufacturing Council (CER).
DRIVING THE CIRCULAR ECONOMY: LCCP & REMANUFACTURING SUCCESS
Remanufacturing is a key contributor to the circular economy, as it lengthens the lifetime of a product using materials from retired products. While many in the print industry have adopted recycling programmes and the use of post-consumer recycled materials (PCR), remanufacturing practices aren’t as widespread. With the many benefits of remanufacturing such as lower raw material usage and reduced landfill waste, Lexmark wishes to set an example for the industry to promote a wider adoption of remanufacturing in Europe
Lexmark’s journey towards circular economy excellence began in 1991 with the introduction of the Lexmark Cartridge Collection Program (LCCP). More than just a recycling effort, the LCCP marked a significant step towards creating a closed-loop process. This programme, available in over 60 countries representing 90% of Lexmark’s global market, enables customers to return used cartridges, which are then returned to the manufacturing facilities and disassembled. The components are then evaluated for reuse, selected, and reincorporated into the production system.
Lexmark offers customers two choices of cartridges for use in their printers: Regular cartridges which are standard-priced original cartridges that may be refilled and/or remanufactured by any third party and Return Programme cartridges. The Return Programme cartridges are sold at a discounted price, on the condition that the customer returns the cartridge to Lexmark for no additional cost, so that the cartridge can be reincorporated into the LCCP system after its use. Thanks to Lexmark’s sophisticated remanufacturing technology and intentional, born circular supplies approach, Return Programme cartridges have been designed and tested to be remanufactured up to an impressive 10 times before they go into recycling. If a returned cartridge is not a good candidate for reconditioning, it is disassembled in such a way to maximise the materials recovered for use in secondary products. Examples of materials given a second life include toner as an asphalt additive to improve quality and performance, and post-consumer recycled plastic integrated into new parts.
In 2022 alone, an impressive 36% of toner cartridges worldwide were returned through the LCCP, evidencing Lexmark’s efforts to make the LCCP process seamless and user-friendly. Lexmark is also an industry leader in the use of reclaimed plastic with 41% of plastic content, by weight, across all Lexmark branded toner cartridges, derived from postconsumer sources, including our own LCCP closed-loop process. Lexmark’s goal is to increase the use of reclaimed plastic through the PCR and reuse processes by 50% by 2025.
Since 2014, we have been manufacturing and remanufacturing cartridges in Poland to meet the requirements of our customers in Europe. This also shortens transport routes and times, thereby generating a positive effect on carbon emissions. In this way, the LCCP programme not only reduces waste but also reduces Lexmark’s environmental impact from a logistics point of view. In addition, this strategy creates and secures jobs within the European Union.
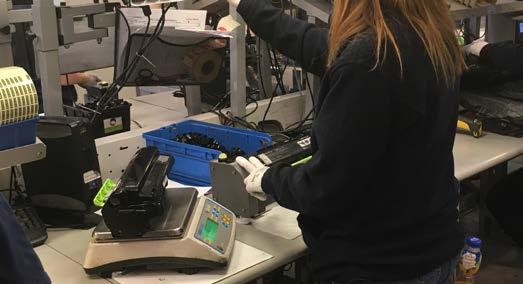
AN INDUSTRY LEADER IN PRODUCT POST-CONSUMER RECYCLED (PCR) CONTENT
Lexmark’s commitment to sustainability extends to every stage of our products’ lifecycles – it’s not limited to consumables; it extends to hardware as well. Through innovative processes developed by their engineers, Lexmark has qualified over 145 components to incorporate up to 100% post-consumer recycled (PCR) plastic. The Lexmark Equipment Collection Program (LECP) ensures the responsible disposal of electronic waste, including end-of-life printers.
This initiative aligns with the European Union’s Waste Electrical and Electronic
Equipment (WEEE) directive, reflecting Lexmark’s commitment to sustainable practices on a global scale. Private households in the EU can take their end-of-life equipment to locally authorised collection centres, while Lexmark customers can also choose to utilise Lexmark’s individual collection system for transporting used products to Poland, where the equipment is processed for repair, remanufacturing, and recycling.
EU-FUNDED PROJECTS: ACCELERATING OEM REMANUFACTURING
Lexmark’s role as an industry leader is further evidenced by our active participation in EU-funded projects. Projects like C-SERVEES aim to implement circular economy models and enhance remanufacturing practices. Lexmark has played a pivotal role in establishing business models which will have a massive impact on the industry, such as optimising reverse logistics, ensuring easy and digitalised product returns and enabling analytics to extend the lifetime of products.
Leading The Way In Oem Remanufacturing
In addition to the C-SERVEES project, Lexmark has recently been awarded with two new research and innovation projects funded by the European Union under the Horizon Europe programme, DiCiM and CERISE. These EU projects are aimed toward implementing circular economy models and accelerating the move towards remanufacturing, not only in the EU but globally. Participation in these projects will help Lexmark build upon our findings and continue our research into boosting cartridge and printer remanufacturing solutions while optimising the reuse of secondary raw materials (SRMs).
Utilising our IoT and Digital Product Passport expertise for the projects will be key to continuing the critical work of developing circular economy solutions for the business world, and will help Lexmark further improve our own offering, as well as developing circular economy solutions which can be adopted elsewhere in the industry.
Lexmark has also been recognised for its achievements in sustainability by prominent award bodies such as EcoVadis, from which we were awarded the Platinum (highest achievable) medal. This certification places Lexmark in the top 1% of all companies assessed, signifying the success of our initiatives.
Lexmark’s journey towards a circular economy through OEM remanufacturing is ongoing. We have already come a long way and we know that we still have some way to go but we are well on track to set new and pioneering standards for the printing industry.
With initiatives like the LCCP and a commitment to EU-funded projects, Lexmark continues to set new standards for the printing industry. Read more about Lexmark’s sustainability efforts here. c Read
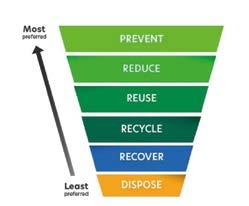