
7 minute read
Getting to the Bottom of the Solution
from RV News March 2022
by ⌘ ⇧ ⌥
Hanwha Azdel gained a reputation with its plywood replacement composite panels. The supplier is now placing its panels in a new place: subflooring.
By Diane Bishop | Photos by Robert Bruce Photography
Since 2006, Azdel Onboard composite panels have slowly replaced the plywood used in RV roofs, ceilings, front walls, rear walls, slide outs and cab-overs.
After two-and-a-half years of extensive prototyping and testing, Hanwha Azdel now recommends using the panels in RVs’ sub oors and has created new options for doing so. e supplier says its oor panels provide a strong, lightweight ooring solution durable enough to eliminate moisture-related warranty claims.
“ Softening of ooring is a potential manufacturing warranty issue,” said Joe Dumeah, Hanwha Azdel’s non- automotive/RV sales director. “ e OEMs requested we develop ooring because the way the oors are being made now, replacement of a oor is an extensive and costly repair. is is similar to the reason RV OEMs use Azdel on the exterior walls.”
Azdel’s panels feature a patented polypropylene and berglass blend that provide an insulation value double that of wood but weigh 50% less.
“A lot of our OEM customers expressed a desire to get rid of wood altogether because of the formaldehyde, as well as the rot, mold and mildew issues related to wood,” said Troy Robertz, Hanwha Azdel’s senior application development engineer. “ e more areas where we can help the customer eliminate and replace the plywood with Azdel boards, which are formaldehyde-free and not subject to water damage, the less risk the manufacturer undertakes.”
– Joe Dumeah
Adding a sub ooring option to OEM vehicles increases Azdel’s total square footage usage in each RV. at equates to massive weight savings tied to construction materials. e reduced weight not only impacts towability but can make adding other features that increase weight possible as well. Dumeah said by the time manufacturers requested an Azdel ooring product, engineers were preemptively working on a solution.
Testing, Testing Rigorous sub oor testing began. Engineers examined aspects such as cost per square inch, glue adhesion and repetitive exposure to vibration, impact and bounce.
One of the most important tests Hanwha Azdel conducted was whether the panels could support the weight sub oors are expected to hold. To determine the panels’ ability to bear weight, Azdel tested a large, unsupported oor section and measured the oor’s de ection capabilities under load. Performance varied depending on the construction, Robertz said, but most testing showed a de ection of just a few millimeters under a 500-pound load.
“ is is one of the most extensive studies we have done before launching any product outside of the original launch of our walls,” he said.
After two years of sub oor testing, working closely with OEMs, engineers proved that Hanwha Azdel’s new sub ooring product is about 30 percent lighter than wood alternatives and has no issues with rot, mold, delamination or structural failure, Dumeah said.
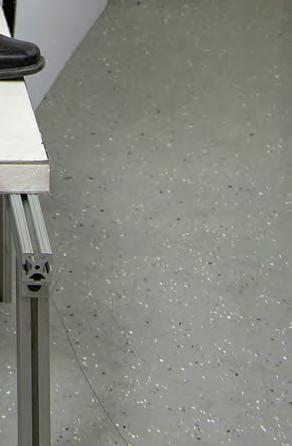
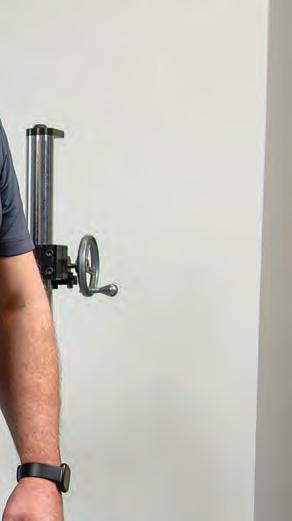
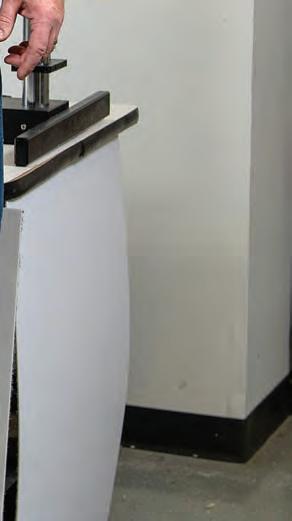
(L to R) Joe Dumeah, Hanwha Azdel Hanwha Azdel non-automotive/ non-automotive/ RV sales director, RV sales director, and Troy Robertz, and Troy Robertz, senior application senior application development engineer, development engineer, stand on a composite stand on a composite panel to be used in an panel to be used in an RV’s sub-fl ooring. RV’s sub-fl ooring.


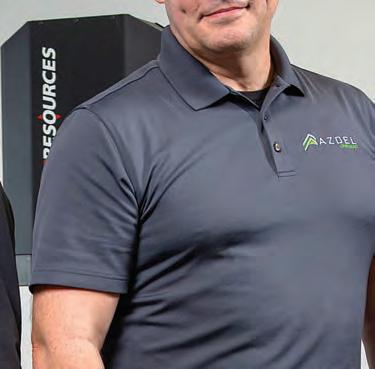
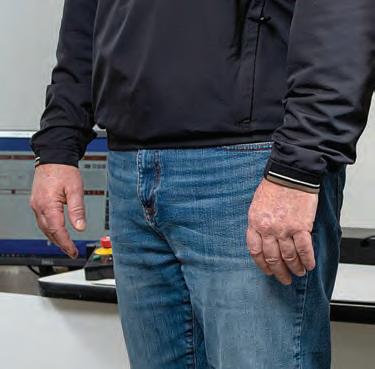
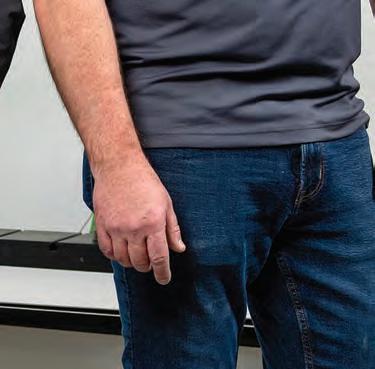
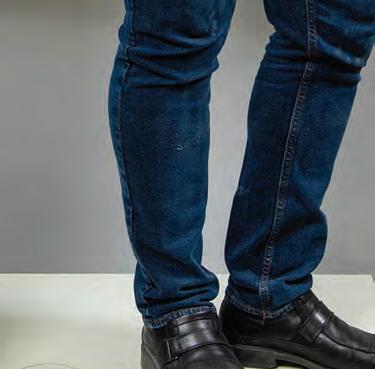
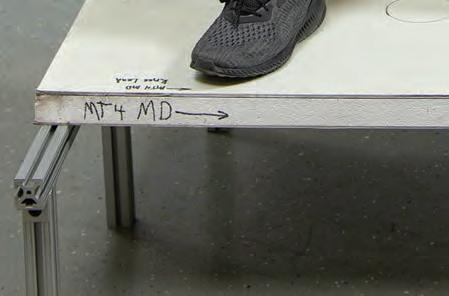

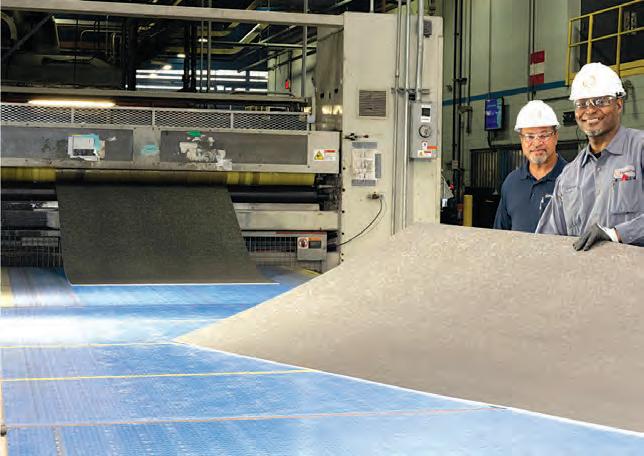
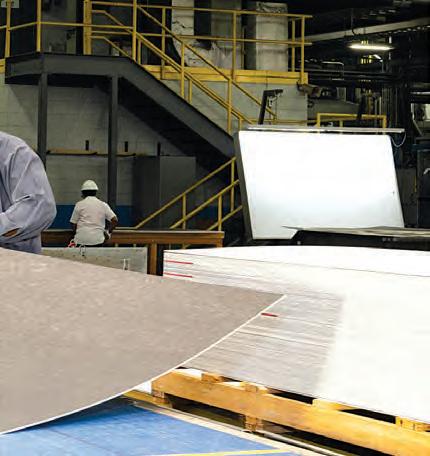
(L to R) Barry Wimbish and Larsen Manning remove panels from the line after they are cut to size.
Rick Sandidge loads scrim rolls. The scrim adheres to the panels to give them a softer feel.
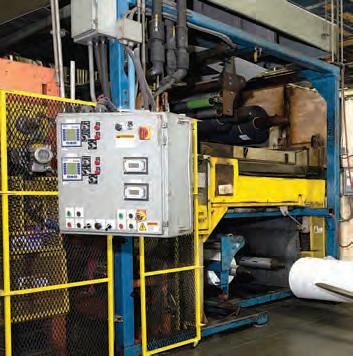
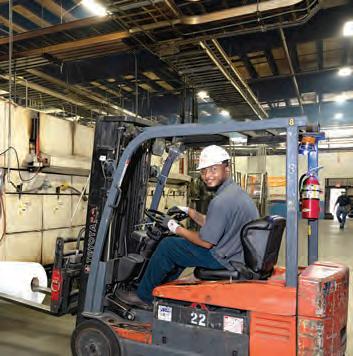
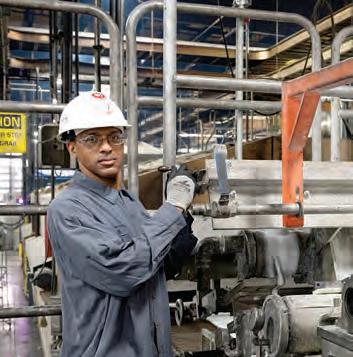
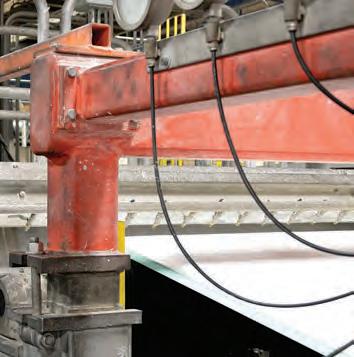
“ Hanwha Azdel started with competitive benchmarking,” he said, “and we feel that we have created a better product.”
Although numerous ooring products are available in the market, Robertz said Azdel ooring panels stand out. He said the panels are in line with competitive products’ sti ness, impact and durability ratings.
Weight is a key OEM and consumer consideration. Azdel’s 30% reduction is a big win, Dumeah said, especially when manufacturers factor in how the material will impact warranty claims. Dumeah said manufacturers will appreciate the products’ reliable consistency.
“Some of the existing products they are using may vary quite a bit in squareness, atness, repeatability and
We are not somebody coming in with a new product .... We are always looking for new applications for our product, and subflooring was an obvious answer.”
– Joe Dumeah

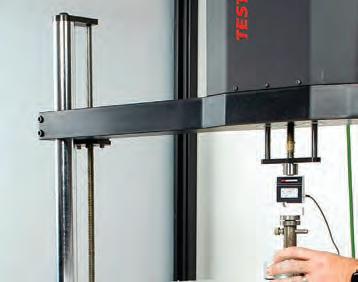
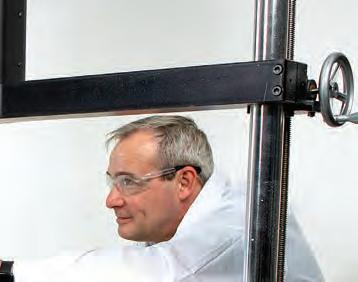
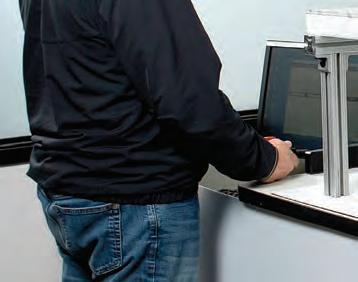
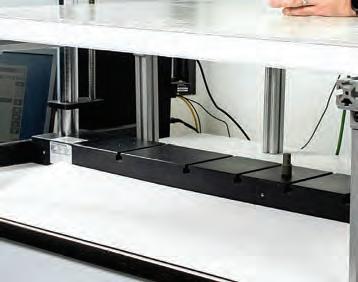
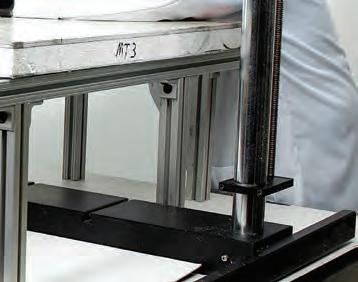
Dumeah and Robertz set up a testing device to determine the panel’s defl ection capabilities under weight.
performance,” he said. “Our product is consistent from lot to lot, so manufacturers know what to expect.”
Dumeah said panel customization was important to make the product viable for numerous applications. He cited toy haulers and heavier fth wheels as examples of vehicles requiring specialized panels.
“ ere are a lot of available variations including thickness, weight and impact resistance, and our boards are completely customizable based on customer preferences for each application,” Dumeah said. “It is like an erector set. It is the manufacturers’ choice on how they put it together.”
Coming in 2022 Azdel Onboard sub ooring is being tested on prototypes at speci c RV manufacturers, which Hanwha Azdel declined to name. According to Dumeah, Hanwha Azdel’s well-established reputation and existing partnerships with OE distributors and OEMs are making the launch and subsequent product adoption much easier than what many new products experience.
“We are not somebody coming in with a new product,” Dumeah said. “We have something we have been selling since 2006. We are always looking for new applications for our product, and sub ooring was an obvious answer.”
The more areas where we can help the customer eliminate and replace the plywood with Azdel boards … the less risk the manufacturer undertakes.”
– Troy Robertz
He said Hanwha Azdel could have launched an Azdel ooring solution 18 months ago, but quickly releasing the ooring without extensive testing would have raised questions. Instead, the company ensured the sub ooring panels were low risk for all involved, with proven data.
“ ere is always a little bit of concern when you are getting ready to go to market,” Dumeah said. “Our testing brings us to a point where we have validated the product and can prove to OEMs how it makes sense for them to make an investment.”
Early manufacturer conversations indicated OEMs liked Azdel’s performance under duress, he said. RV prototype durability and wear testing can take up to a year for some OEMs to complete. Hanwha Azdel representatives assist manufacturers during the testing phase, he said. ose experiences make Dumeah con dent 2023 RV models will feature Azdel.
“It is not something where we just sell a product and hope manufacturers have success with it,” Dumeah said. “We want to be part of that success with them. By working together, we have developed partnerships and collaborations to ultimately give the end customer a better RV and a better experience.”
