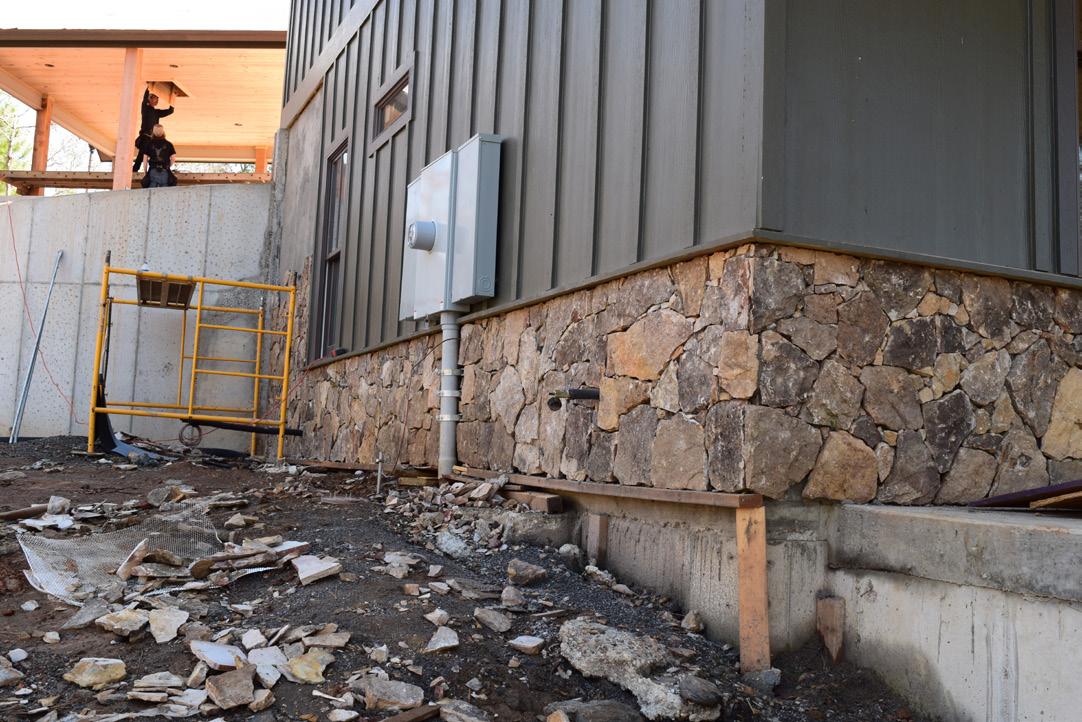
4 minute read
BUILDING DURING A PANDEMIC
COVID and supply chain delays added several months to the Chesnutts' building schedule
COVID hit the crew as foundations were poured
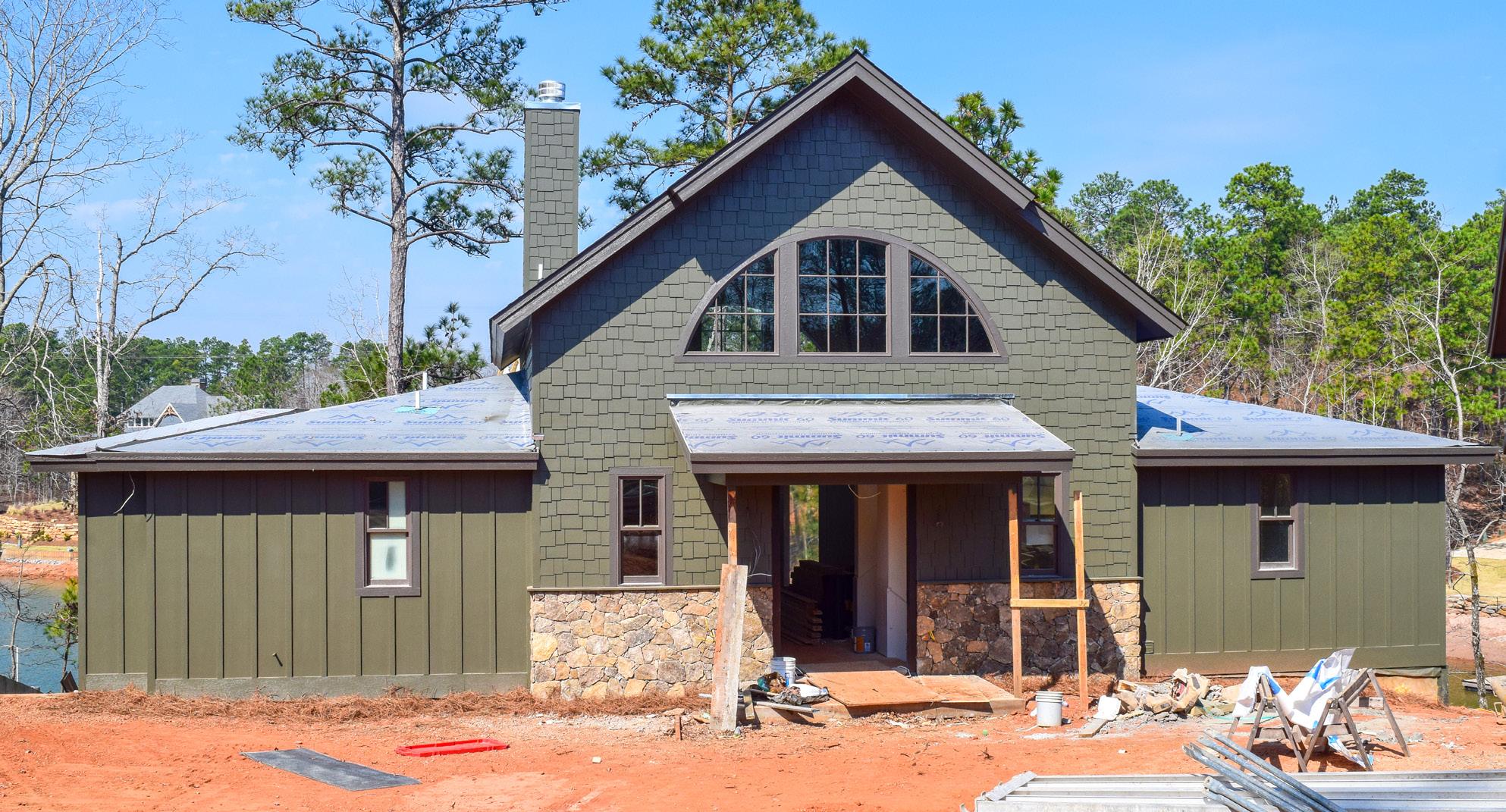
STORY & PHOTOS BY ERIN CHESNUTT
When my husband, Charlie, and I purchased our lot in South Ridge Harbor in 2019, “COVID” and “supply chain” were not part of everyday conversation. Little did we know that these events would greatly affect how our dream home on Lake Martin would be built. Decisions, delays and frustration were a direct result of how the world changed during the pandemic.
After selling our townhome in The Ridge in November 2020, construction began on our lot in late December 2020. We were excited and planning the normal 10 to 12 months for the building process for our 3,400-squarefoot house. The home includes four bedrooms, three full baths and two powder rooms with a loft area that will serve as an office and extra sleeping space. There is a kitchenette/bar in the basement with a large family room. We also planned a wine room off the bar area and a lake prep area in the basement, as
Wwell as storage in the back of the house. The porches run the length of the house, so there is about 1,400 square feet of outdoor living space. The upper porch will be screened, and there is a grilling area of the upper and lower porches. While the permitting process wasn’t much trouble, our plans to get the dock in early did not work out. Because of all the rain and COVID, the dock was delayed a year. We had to get the permit for the dock renewed by Alabama Power at additional cost. The cost actually went up once the construction boom started. The dock was installed last summer. As soon as construction began, our builder, Chad Stearns, told us to get the windows ordered because of manufacturing delays. We learned that this was great advice, considering the challenges we were faced with at the time due to manufacturing issues. This was also the first clue that
this was not going to be a normal build. So as soon as we broke ground, we had windows on order.
We soon found out that many of the materials and finishes required to build a new home were going to require extended lead time. We began construction with lumber prices at an all-time high. We were advised to wait a while to see if the price would come down. This was an unexpected delay, but we took the advice. Then, we were in the process of pouring the foundation walls when COVID hit the crew. The lumber was able to be ordered, but construction was now off schedule while we waited for the crew to recover and come back to our site to complete the job.
The next big decision before we even began construction was appliances. Lead time on most of the appliances was eight-to-10 months or more. Many of the manufacturers were not even providing possible delivery dates. We had to decide to do the best we could in an environment that was out of our control.
In addition to appliances, plumbing fixtures were also a challenge due to supply chain and manufacturing issues. We quickly learned that selecting a faucet design did not mean that the matching showerhead would be available in time. It required hours of searching and making changes. We finally got everything ordered, and we were fortunate that we had been informed ahead of time about how COVID was causing severe delays in many areas.
As COVID cases increased, more construction crews began to get sick. Almost every crew, including framers and tile installers, took weeks off the job to recover. This created a domino effect, causing crews to postpone their schedules on our house. We had to wait weeks to get back on track, testing our patience, but still enjoying watching our lake house become a reality.
We had decided to use a cabinet maker and kitchen designer that we had used at our home in Atlanta. By using Dining in Design and Laser Line Cabinets, our hope was to minimize the delay with so much building demand on the lake. The cabinets were scheduled with a delivery date of early March. Our final delay was flooring.
The wood floors had not come in, causing another timeline delay. The floors needed to be installed prior to the cabinet installation, which meant everything was postponed until the end of March.
While we had hoped to move in mid-March, we are now happily looking forward to April. Some of the furniture we ordered is actually coming in ahead of schedule, so we will be able to get settled in our new home quicker than we expected.
We know that we will love our home, and the future memories that we will create with our family will be worth the wait. We’ll have unique stories to pass down about how we started our home at the beginning of a pandemic and the challenges of working through COVID. We’re hopeful that our first summer in our new home hosting family and friends will be sunny and the threat of COVID will be gone.
We’re counting on the old saying “Good things come to those who wait.”
Lumber prices reached an all-time high during construction

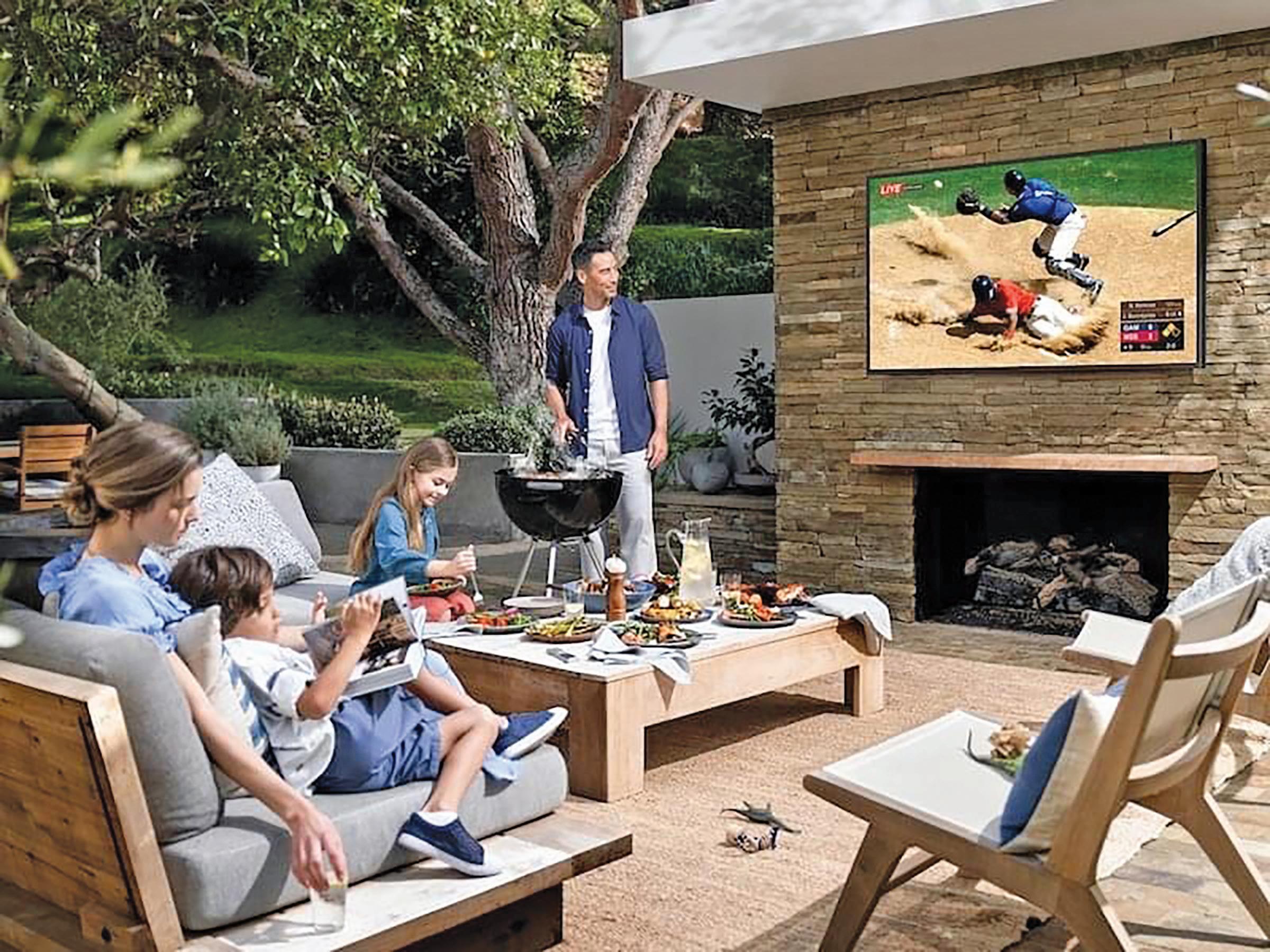


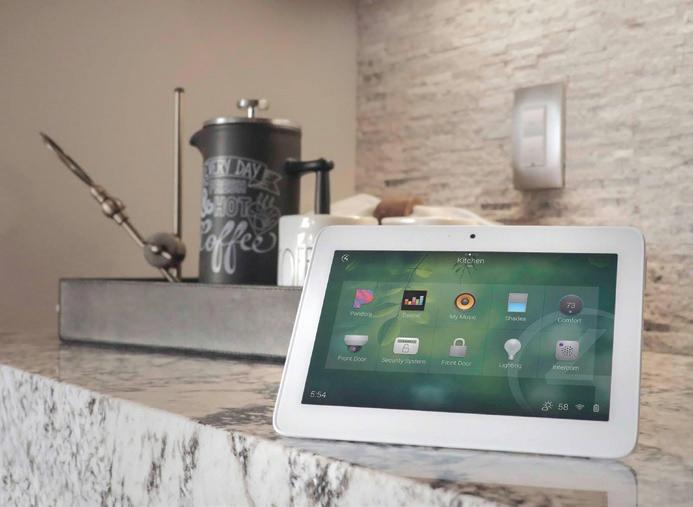
