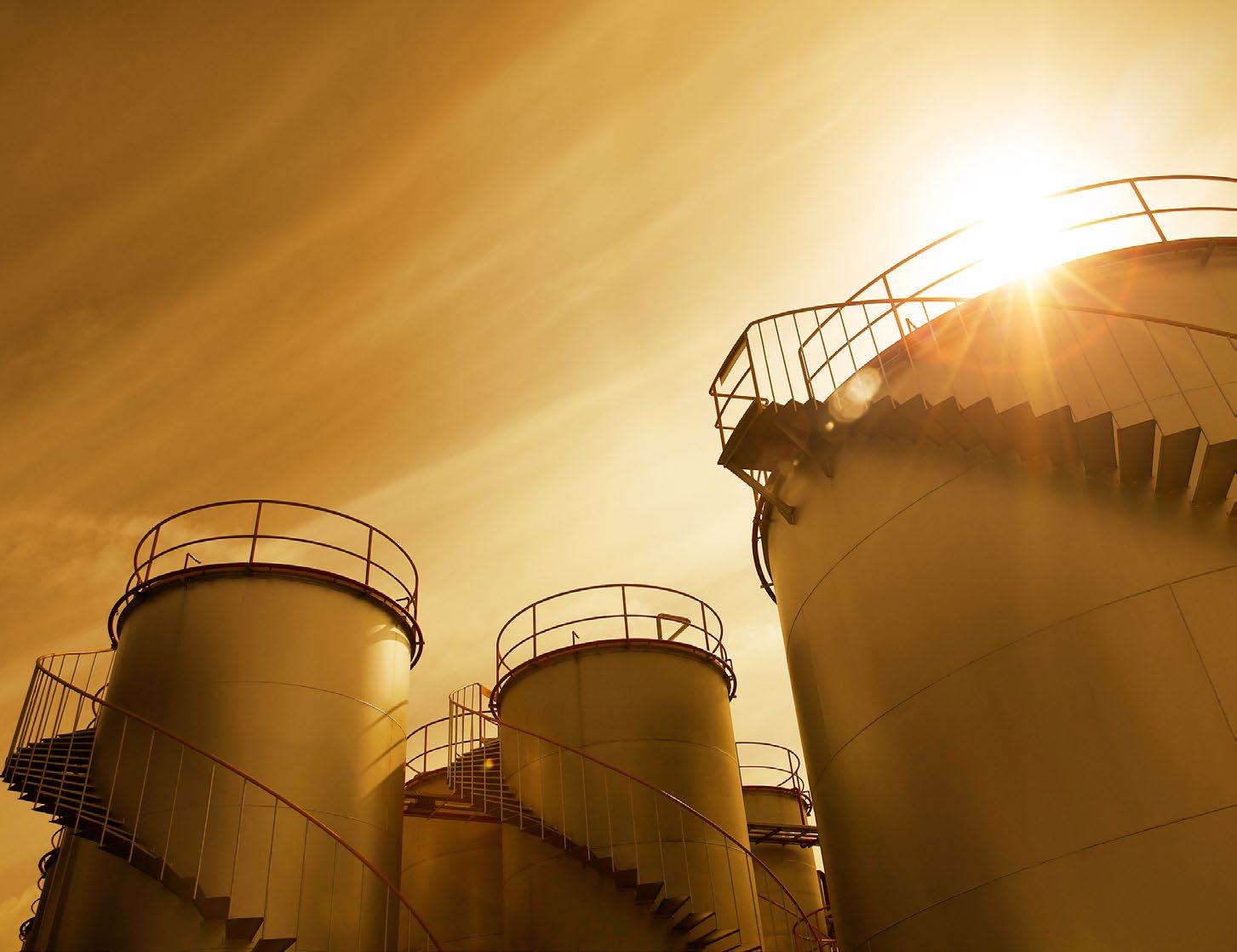
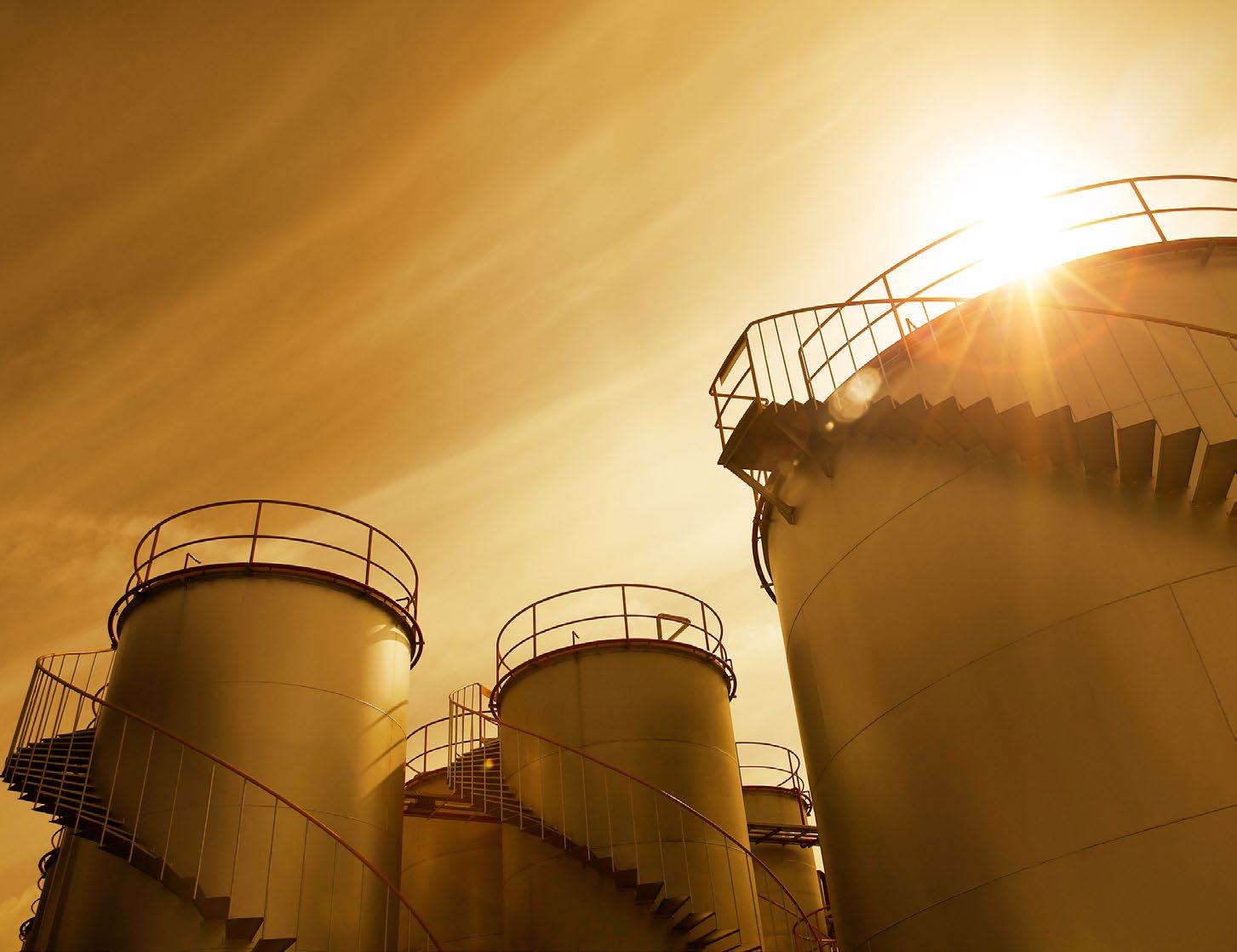
NEWS UPDATE
TRAMMO ACQUIRES LEMM CORP
Trammo’s wholly owned subsidiary Trammo Terminals has acquired Lemm Operations (Lemm Corp) an operator and provider of engineering and terminal management services to large chemical facilities throughout the United States.
Edward Weiner, CEO of Trammo comments: ‘We are pleased to announce this exciting acquisition which complements Trammo’s strategic core businesses. We look forward to the Lemm Corp team continuing to serve our existing ammonia and nitric acid facilities and expanding our business operations.’
Trammo’s president of North America Trading, Jeffrey Minnis, says: ‘This acquisition will further our close relationship with Lemm Corp and provide for future expansion in the US and abroad to better serve our customers and suppliers as well as third parties requiring top-notch chemical storage and terminalling operations.’
John Lemm, president of Lemm Corp, adds: ‘We have had a close bond with Trammo for over 35 years and are delighted to become part of the Trammo family. We look forward to continuing to meet and exceed safely all of Trammo’s and our other clients’ operational requirements.’
VARO LABORATORY ACCREDITED WITH EN 17025 STANDARD
Varo Energy’s CEO Dev Saynal has announced that Varo’s laboratory in Geertruidenberg, Netherlands, has been accredited under the EN 17025 standard.
The lab analyses fuel samples to ensure the quality of fuels Varo delivers from its Benelux terminal and retail network to our customers. With the ability to analyse 19 different specifications and over 20,000 samples annually, we have built a solid reputation for trust and reliability in our products. In a post on LinkedIn, Saynal said: ‘This significant achievement underscores our commitment to high-quality standards and technical excellence.’
‘Supporting our customers to help them achieve their sustainability goals, the EN 17025 accreditation now covers our bio & renewable content and density analyses,’ says Saynal. ‘By integrating advanced technologies, we assure the quality and authenticity of our biofuels whilst enhancing efficiency and accuracy. Additionally, this enables us to adapt swiftly to changes in renewable fuel regulations, ensuring our customers always have access to compliant solutions.’
ABP & PX GROUP PLAN FOR CLEAN GROWTH HUB
Associated British Ports (ABP), the UK’s leading ports group, and px Group, the owner and operator of high-growth Saltend Chemicals Park, have announced plans for the Clean Growth Hub at the Port of Barry in South Wales.
The project aims to transform a large area of the operational port into an area of low-carbon, high-growth infrastructure investment. The site has in excess of 100 acres of development land earmarked for investee companies who are:
• Specialists in rare earths processing;
• Battery materials manufacturers;
• Manufacturers who are part of green energy and net zero supply chains and;
• Developing carbon capture and utilisation (CCU) business models.
MITSUBISHI TO INVEST €296 MILLION IN SALTEND CHEMICALS PARK
Mitsubishi Chemical Group UK has committed to invest £250 million (€296 million) in a new production line at Saltend Chemicals Park, UK, based within one of the three Humber Freeport tax sites.
Preparatory works have started to make way for construction of the new production line, which will double Mitsubishi Chemical Group’s capacity at the site, east of Hull. The new production line is expected to become operational in 2026.
The new production line will help to meet growing demand for Soarnol, the brand name for a grade of Ethylene Vinyl CoPolymer (EVOH) which is primarily used in food packaging to extend product shelf life.
Since opening in 2002, Mitsubishi Chemical Group’s Saltend facility has seen a significant increase in demand for Soarnol, driven by food manufacturers seeking packaging that can be recycled while also having a lower environmental impact.
Humber Freeport chair Simon Bird comments: ‘We are delighted that Mitsubishi Chemical Group has chosen to make this very significant new investment at Saltend on a site benefiting from being within the Humber Freeport footprint. The substantial advantages offered by freeport status were an important factor in securing this new inward investment.’
NESTE & LOTTE CHEMICAL TEAM UP ON RENEWABLE CHEMICALS AND PLASTICS
Neste and South Korean chemical company Lotte Chemical are teaming up to make chemicals and plastics more sustainable. The companies embark on a strategic collaboration to replace fossil resources with renewable raw materials in the manufacturing of chemicals and plastics. This will enable products and applications with a lower carbon footprint compared to those produced from fossil resources.
The collaboration will see Neste providing renewable Neste RE, a raw material for chemicals and plastics, that is made from 100% renewable raw materials. Lotte Chemical will use Neste RE at the company’s Korean sites to produce various common types of plastics and chemicals in Lotte Chemical’s broad product portfolio. These plastics and chemicals may be used in multiple applications and in supply chains for various products ranging from packaging to construction and from textiles to electronics. The quality and performance of the end products remain unchanged. With chemicals and plastics still largely depending on fossil resources, both companies see an urgent need to make a switch to more sustainable alternatives.
South Korea


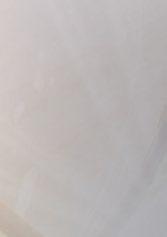
2 Packed Days


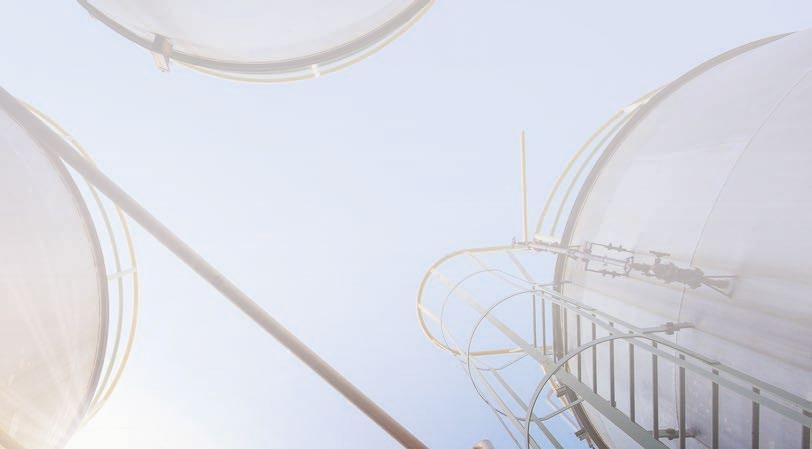
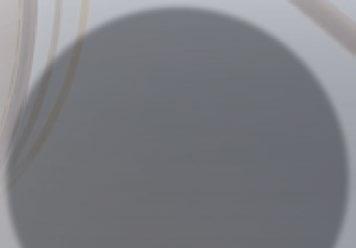
600+ Leading Exhibitors
Operations & Logistics

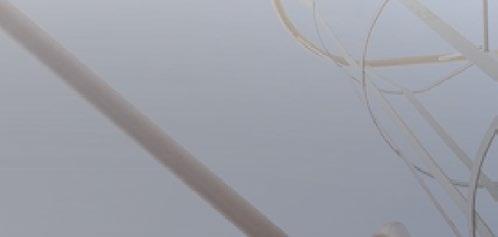
Tank Storage Solutions


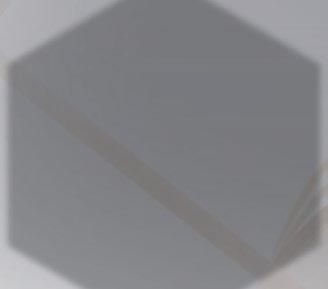
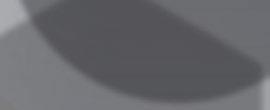
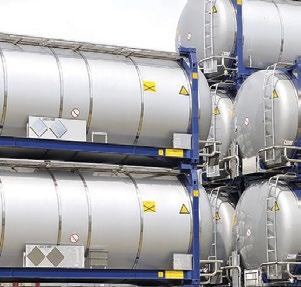
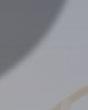
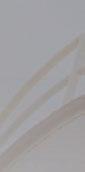
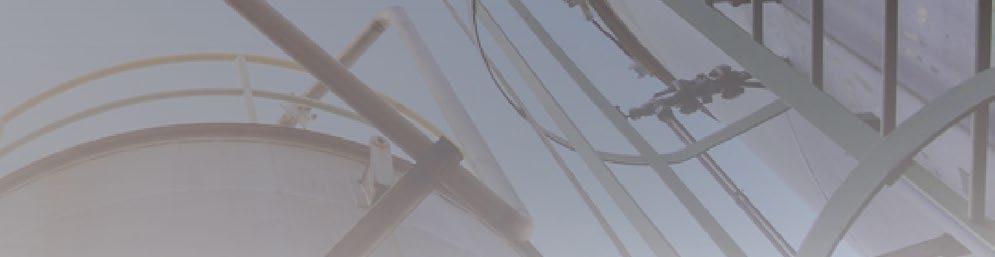
Plant, Process & Asset Management
Chemicals & Materials Sourcing
150+ Speakers
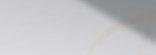
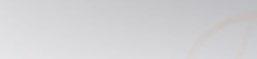



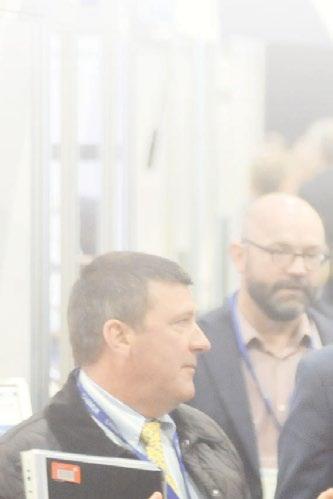
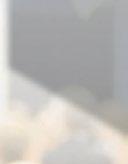
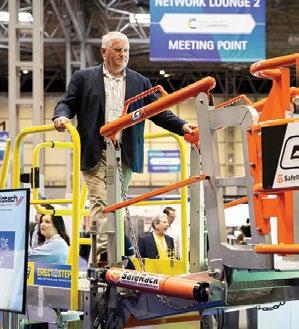
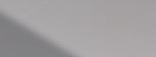




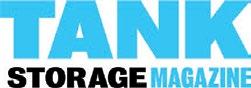
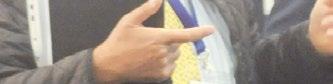

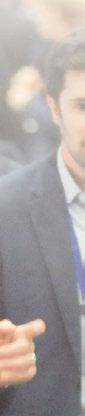
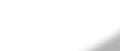


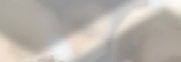




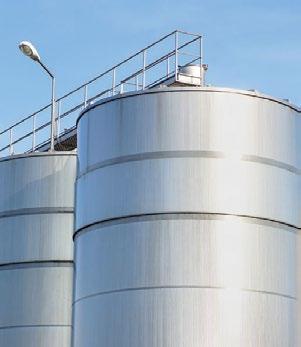
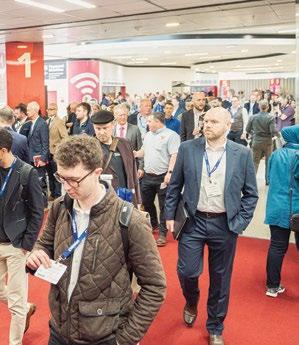
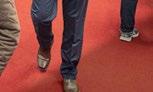
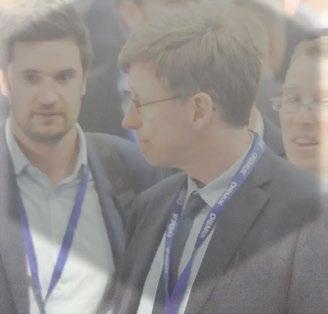

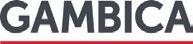
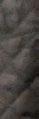

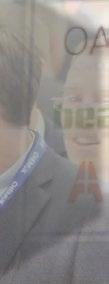
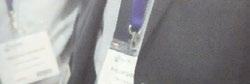



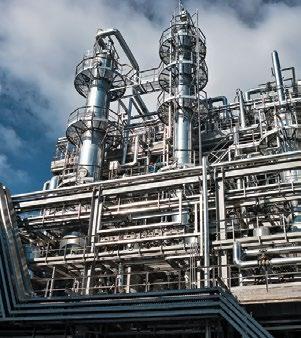






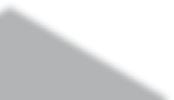
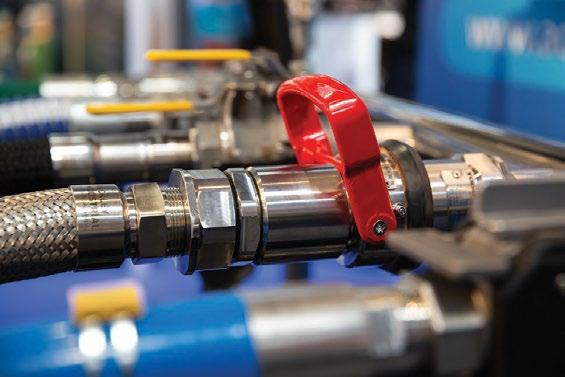
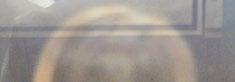
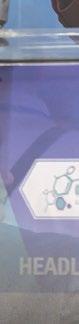
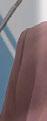

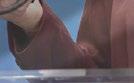
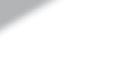
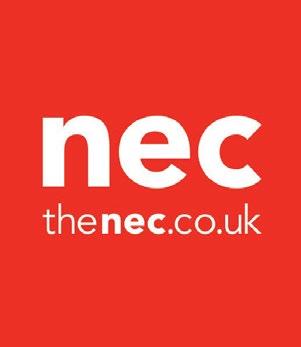
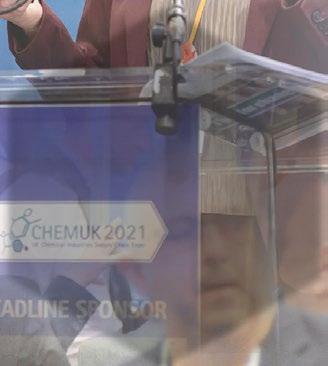

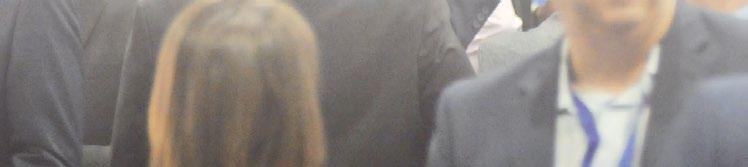
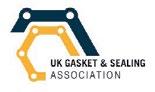
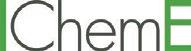
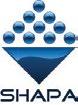




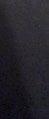
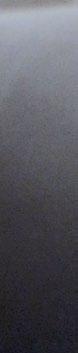

DIGITAL-FIRST TERMINAL
ACTAD’s operations manager, Frank de Leng, explains how involving ToolKitX from the beginning helped the team build a future-thinking terminal
ARABIAN CHEMICAL Terminals
Abu Dhabi (ACTAD) is an independent commercial tank terminal located at Khalifa Port, Abu Dhabi. Completed in 2024, the greenfield terminal is strategically positioned between Abu Dhabi, Ruwais, and Dubai to offer multi-modal connectivity with access to the sea, extensive road networks, and the future GCC railway network. ACT handles a variety of operations, including large marine tankers, smaller feeder barges, and intermodal transport with ISO tanks.
Having constructed the first ever commercial terminal in Abu Dhabi, ACTAD intends to service the ever-expanding import and export of liquid chemical products, catering to the local industries.
Frank de Leng, ACTAD’s operations manager, adds: ‘Also having operated terminals for four decades in Saudi Arabia, this footprint in Abu Dhabi, UAE, will help our existing international chemical clients to have a further regional hub for storage and breakbulk operations.’
STATE-OF-THE-ART SOLUTION
Key to ACTAD’s terminal is prioritising operational efficiency, safety and the customer experience. Wanting to ensure the terminal would be a futureproofed and forward-thinking facility, de Leng looked into digital solutions that could meet their needs.
‘During the construction of the new terminal, ToolkitX was selected as the preferred software solution due to its comprehensive coverage across all terminal departments,’ he says.
ToolKitX’s Integrated Terminal Management System (ITMS) is a stateof-the-art SaaS solution designed for administratively processing liquids’ and gases’ bulk storage handling and custody transfers. It ticked – almost – all the boxes for ACTAD, enhancing operational efficiency, safety, and cost-effectiveness.
‘The only gap identified was the absence of a specific ‘Order to Cash’ module tailored for terminal operations. However, by developing this module in-house with ToolkitX’s collaboration, we were able to create a custom solution that adhered to all industry-specific regulations, including considerations such as density calculations and Fahrenheit-to-Celsius conversions,’ explains de Leng.
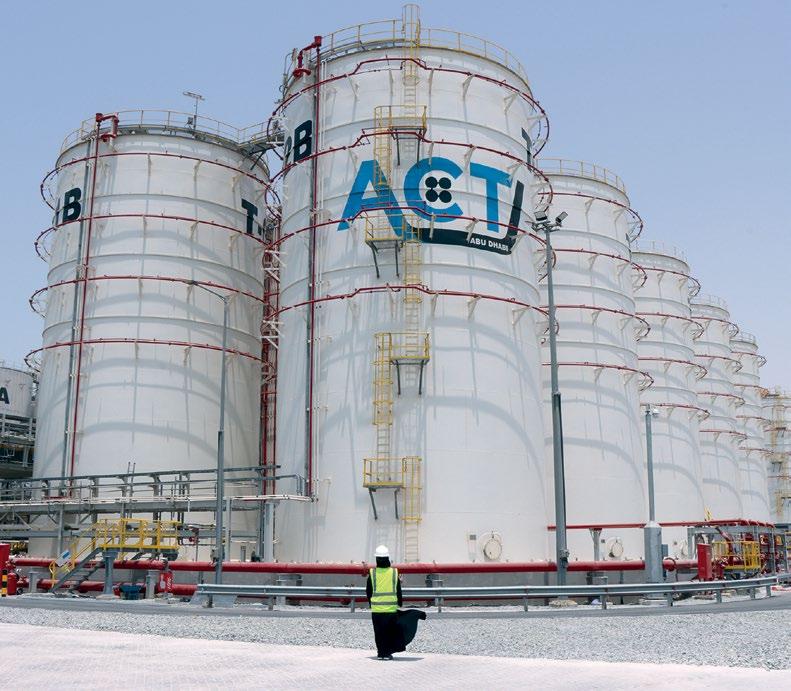
At first, ACTAD was primarily seeking digital solutions focused on safety, such as electronic permit-to-work (e-PTW), lockout/tagout (LOTO), and incident management systems. However, as the team explained their vision to ToolKitX, it became clear that they needed a more holistic and integrated digital solution; one that would not only cover safety and operational aspects but also address the commercial aspects of things.
This realisation led to a close collaboration between ACTAD and ToolKitX, beginning with a thorough consultation phase. ToolKitX worked closely with ACTAD to understand the team’s comprehensive requirements. Detailed discussions with stakeholders from the various departments ensured that the system would be tailored to address all critical aspects of terminal management.
Throughout the development, ToolKitX maintained close communication with ACT to ensure the system met their expectations. Regular feedback sessions allowed for continuous input and adjustments, making the system not only technically sound but also user-friendly and practical for daily operations. After development and rigorous testing,
the system was implemented at ACTAD’s terminal. ToolKitX provided comprehensive training to ACTAD’s staff, ensuring a smooth transition to the new system, and continued to support ACTAD after launching the system, making further refinements based on real-time feedback.
This ongoing partnership ensures that the ITMS remains up-to-date and continues to meet the evolving needs of ACTAD’s operations.
COLLABORATION & CUSTOMISATION
Each terminal facility is different, and ACTAD had a laundry list of requirements that would need to be met. The team wanted a cloud-based, integrated endto-end order management solution that would bridge the gap from IT to OT and manages all fulfilment processes.
The ToolKitX platform is highly customisable, designed to adapt to the specific needs of each client. The platform’s modular architecture allows for flexibility, enabling clients to select and configure the features most relevant to
‘...We were able to create a custom solution that adhered to all industryspecific regulations...’
their operations. This includes customising workflows, safety protocols, inventory management, and customer interfaces.
Furthermore, the system is scalable, meaning that as the client’s operations evolve or expand, the ITMS can be adjusted or enhanced to accommodate new requirements.
This level of customisation ensures that the platform can grow with clients, providing long-term value and adaptability in a dynamic industry.
ACTAD played a pivotal role in shaping theToolKitX solution, sharing detailed insights into their processes, challenges, and goals, which guided the customisation of the ITMS. ToolKitX’s Sultan Irshaidat says: ‘ACT’s feedback was crucial at every stage, from the initial consultation and design to the iterative development and testing phases. This collaboration ensured that the final system aligned perfectly with their vision for a holistic digital solution.’
IMPROVED TERMINAL MANAGEMENT
ACTAD has enjoyed numerous benefits from implementing the ToolKitX ITMS for managing its liquid and bulk terminal facility at Khalifa Port.
One of the most significant advantages is the ability for customers to interact with the system directly through the Customer Product Management (CPM) functionality. This feature allows ACTAD’s customers to place orders online, monitor their inventory in real time, and track the entire process up to invoicing. This transparency and control have greatly enhanced customer satisfaction.
For ACTAD’s operational staff, ITMS streamlines the entire workflow by making the process paperless and highly automated. From receiving orders and executing operational prerequisites to ensuring safety measures are in place, the system handles everything digitally. This not only reduces manual input but also ensures that all client contracts and handling procedures are predefined, which minimises errors and increases efficiency.
Moreover, ITMS tracks technical availability and client inventory in real time, enabling ACTAD to maintain a high level of operational readiness. All internal workflows, including work orders, safety procedures like electronic permit-to-work and lockout/tagout, and
QUICK LOOK: TOOLKITX SOLUTION
Sultan Irshaidat from ToolkitX explains what sets their solution apart from other terminal management systems on the market:
Fully Integrated Solution: One of the standout aspects of ToolKitX is its ability to offer a fully integrated terminal management system that encompasses safety, operations, and commercial functions within a single platform. Unlike many other systems that focus on just one or two areas, ToolKitX provides a holistic approach, allowing for seamless coordination across all aspects of terminal management. This integration is particularly valuable for clients like ACTAD, who needed a system that could handle everything from safety procedures to customer order management without relying on multiple disparate systems.
High Customisability: The platform is highly adaptable, allowing it to be tailored precisely to the client’s needs. Whether it’s adjusting workflows or incorporating specific safety protocols, ToolKitX can be customised to fit any operational requirement.
Real-Time Data and Analytics: ToolKitX provides real-time insights and advanced analytics, enabling informed decision-making and proactive management. This helps optimise performance, reduce downtime, and cut operating costs.
Mobile Support: The system supports mobile and handheld devices, allowing the workforce to manage operations and safety checks in the field, enhancing safety and efficiency.
Continuous Innovation: ToolKitX is committed to evolving with industry needs, offering ongoing support and continuous improvements to ensure the platform remains cutting-edge.
operational processes, are managed electronically, ensuring smooth and consistent operations.
‘The implementation of ITMS has led to significant cost savings, cutting operating expenses related to product handling compared to traditional paper-based methods,’ says Irshaidat. ‘It also provides accurate, real-time inventory reports to customers through an online self-service portal, fostering better product segregation and avoiding issues like contamination or unwanted blending.’
Additionally, ITMS supports on-premise workforce operations with mobile and handheld devices, which not only improves safety and compliance but also mitigates risks associated with hazardous work. Overall, the system has transformed how ACTAD manages its terminal, making operations safer, more efficient, and more customer-centric.
For more information: www.act-uae.com www.toolkitx.com
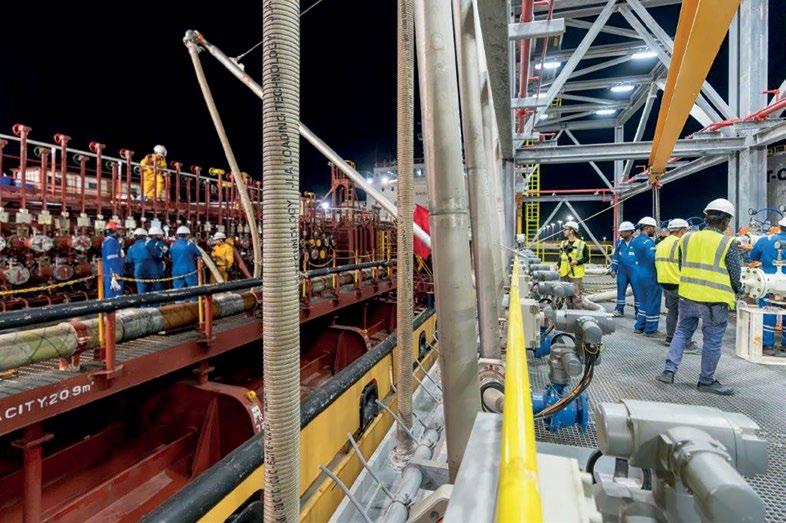
SUSTAINABLE STORAGE EVERY DAY
In the wake of Tepsa’s rebrand, Tank Storage Magazine sits down with managing director Nuria Blasco for an exclusive interview
TEPSA’S BEGINNINGS date back to 1877, delivering asphalt for the streets of Paris and expanding into fuel storage by the 1920s. By the 1950s, Tepsa developed its storage capabilities, venturing into blending biofuels and storing alternative products like chemicals in the 1990s. ‘Today, we continue to adapt to a changing market,’ says managing director Nuria Blasco. ‘Our new name, Tepsa, embodies our legacy of evolution and our commitment to future progress.’
STORING FUELS, CHEMICALS & NEW PRODUCTS
Tepsa operates 15 strategically located storage facilities across Europe, boasting a total capacity of 4 million m3 and close to 1,000 tanks. These facilities handle a diverse range of products, including fuels, biofuels, chemicals, and agrifood products. Each terminal is uniquely equipped and tailored to accommodate different capacities and specific product requirements, ensuring optimal storage solutions for a variety of sectors.
This includes preparing for the energy transition. ‘At Tepsa, we believe that the energy transition will result in a diverse mix of co-existing fuels. This includes new fuels like ammonia and more familiar ones such as e-kerosene and methanol,’ says Blasco.
The transition will be gradual, and Tepsa’s primary goal is to offer the right storage solutions at the right time for its customers. ‘To achieve this, we prioritise maintaining an open dialogue not only with our customers but also with key industry decision-makers who are influential in setting trends. This proactive communication helps us anticipate and adapt to market changes,’ adds Blasco. Tepsa is also strengthening its technical and business teams by bringing in experienced professionals with expertise in specific product areas – including ammonia and CO2. ‘This strategic reinforcement ensures that we are wellequipped to handle the complexities of the evolving energy landscape,’ says Blasco. ‘We value the varied backgrounds and expertise of our employees, which enhances our ability to manage a diverse
range of products. This range of skills fosters flexibility, allowing us to adapt to changing market demands, and customer needs effectively.’
To prepare for the increasing demand for greener fuels, Tepsa is focusing on five key strategic areas:
1. Market adaptation: Tepsa recognises the growing demand for sustainable energy and is planning and proposing solutions to meet both traditional and emerging fuel demands.
2. Expansion and biofuels: Tepsa is capitalising on the global growth of biofuels, supported by EU legislative targets. For example, its expansion projects in France aim to enhance the company’s market position and increase its capabilities in chemicals and biofuels to meet evolving customer needs.
3. Chemical and agrifood storage: The stable chemicals market and the increasing need for fertilizer imports in the agrifood sector drive Tepsa’s commitment to adapt and provide necessary storage solutions.
4. Green fuels projects: Tepsa is exploring projects in green fuels, including hydrogen and secondgeneration biofuels. The company’s decentralised approach encourages innovation and allows its teams to identify and lead projects with headquarters’ support.
5. Technological and sustainable advancements: We are leveraging solar panels, exploring carbon capture and hydrogen projects. Our technical expertise in managing hazardous products ensures safety and reliability.
‘70% of our revenues already come from sustainable products and services,’ says Blasco. ‘The objective is to grow our portfolio and revenues to best serve customers. Our mission is to sustain innovation and decarbonisation while upholding the highest safety and efficiency standards. We strive to provide flexible, reliable, and responsible solutions, connecting industries to society and ensuring prosperity for our stakeholders.’
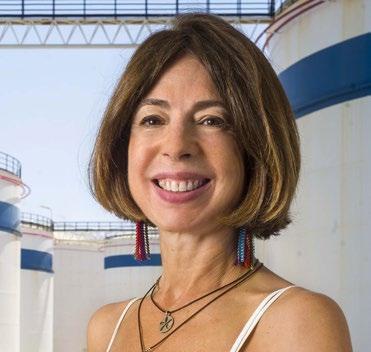
CHEMICAL TRENDS FOR STORAGE TERMINALS
Primarily working in the chemical industry, Tepsa anticipates a growing demand for specialty chemicals storage, due to ongoing disruptions in European chemical production. This situation is likely to result in increased imports of specialty chemicals and commodities such as caustic soda and methanol.
‘Since 2020, the pandemic and Russian aggression against Ukraine have put a light on our rather unknown industry,’ says Blasco. ‘Despite the complexities, we have delivered our logistic services. In fact, what we have experienced during this very peculiar period is going to be the new norm. We will face increased demand for versatility, driven by various factors such as geopolitical risks and trade tensions.’
Additionally, as green fuels diversify in terms of quality grades, there will be a heightened need for more segregated storage. ‘Customers are increasingly interested in tracking product origin and ownership with greater precision,’ adds Blasco.
Obtaining permit authorisations will become crucial, requiring terminal companies to work more closely with administrative authorities. Blasco says: ‘This collaboration is essential to ensure timely project completion while maintaining the highest safety standards. CSR and ESG aspects will also play a central role in the management of our business, including such collaboration.’
REBRANDING FOR THE FUTURE
‘Our decision to rebrand stems from our maturity as a company and our unique identity, coupled with our forward-looking ambition,’ says Blasco. ‘It was the right moment to embrace a brand that truly reflects our evolution.’
Through extensive market research, the company evaluated various options, including entirely new names, ultimately choosing ‘Tepsa’ – a name with a 60-year legacy that carries significant weight in the tank storage industry. ‘Tepsa is a name recognised and respected by our clients, known for its strong reputation,’ says Blasco. ‘It’s meaningful, simple, and easily pronounced across all the languages we operate in. This rebrand symbolises a new beginning, uniting us under one name, Tepsa.’
Building on this 60-year legacy, Tepsa’s extensive experience in greenfield infrastructure projects is a significant asset for the changing market. The company is well-positioned to construct new, customised infrastructure for
‘Our decision to rebrand stems from our maturity as a company and our unique identity, coupled with our forward-looking ambition.’
complex energy projects, as well as handling green fuels – which often share traits with chemical products. ‘This unique combination of strategic locations and specialised expertise enables us to excel in the evolving energy market,’ says Blasco.
Tepsa’s future growth is built on three core pillars:
1. Outperforming in fuels: While the company will continue using and storing traditional fuels for some time, Tepsa is committed to enhancing and maximising customer service. The company has strong ambitions in the areas of sustainable aviation fuel (SAF) and e-Kerosene, reflecting its dedication to advancing cleaner energy alternatives.
2. Expanding in chemicals and biofuels: Tepsa aims to strengthen its position in the chemicals market by continuing to grow its existing locations and expanding significantly in France. This strategy supports Tepsa’s commitment to meeting the increasing demand for biofuels and specialty chemicals. ‘Additionally, we have a strong management team with extensive experience, providing us with a solid foundation to identify and capitalise on growth opportunities. We believe that the combination of our management’s longevity, our attractive growth profile, and our proactive approach to new projects
positions us well for continued success in the future,’ says Blasco.
3. Diversifying in new products and embracing the energy transition: Tepsa is fully committed to embracing the energy transition. As the transition evolves in various forms, the company aims to be the preferred partner for storage, regardless of the energy vectors involved. Its adaptability and multi-product approach are crucial to this goal. Tepsa is already active in emerging markets such as hydrogen and its derivatives, CO2, and various e-fuels, with several projects currently under development.
By focusing on these pillars, Tepsa is wellpositioned to lead in the evolving energy landscape and to support the shift towards more sustainable energy sources.
For more information:
www.tepsa.com
01 Nuria Blasco, managing director, Tepsa
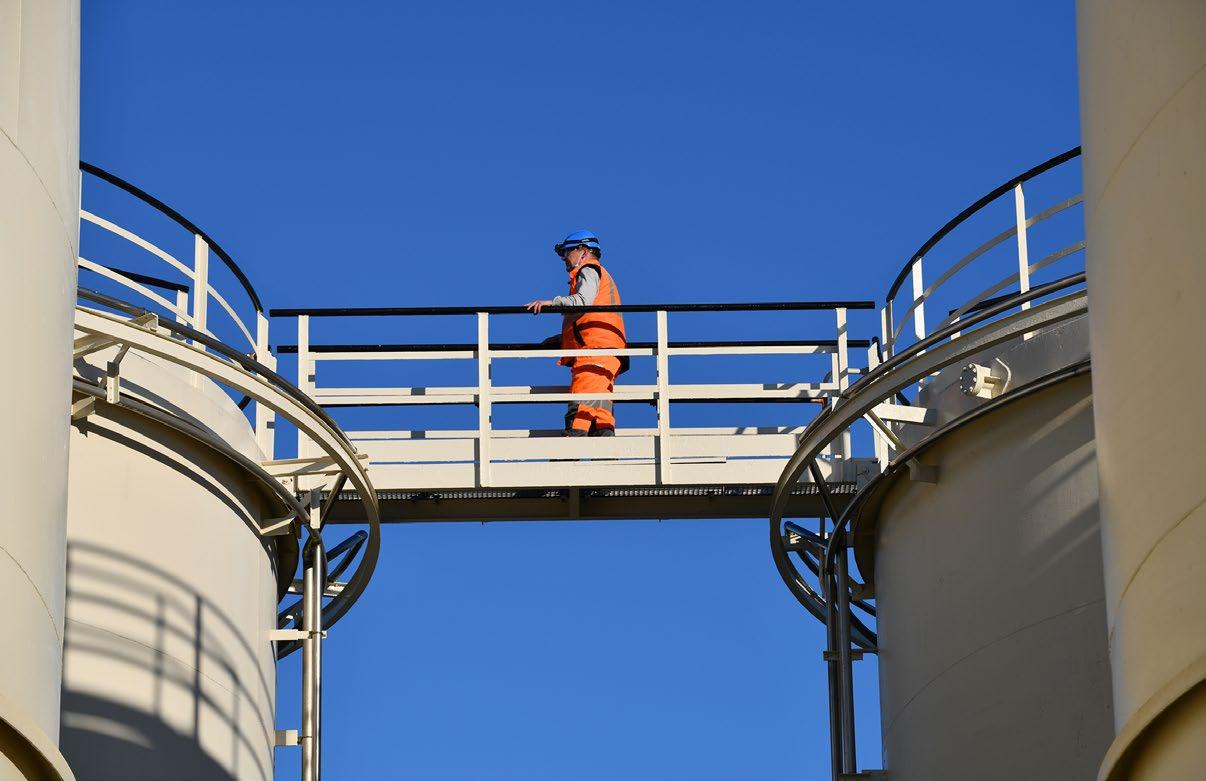
SUSTAINABILITY IN THE CHEMICAL INDUSTRY
Deloitte’s Alexander Keller and Johannes Trueby explore how Europe’s sustainability transformation will impact the storage and logistics sectors
THE ONGOING and intensifying sustainability transformation of the European economy, and the chemical industry in particular, offers significant potential for logistics and storage providers. Not only will the existing rise in petrochemical imports continue, but the required influx of green energy, especially in the form of green ammonia and methanol, demands huge additional logistics facilities at import harbours and inland.
This a critical cornerstone and a business opportunity, and the logistics sector must make timely investments – a fact that is often overlooked in the focus on where to source and how to use the volumes of green hydrogen and derivatives. Furthermore, this development should be viewed in the overall societal context: governments must create frameworks that allow and enable the logistics industry to do what is necessary.
CHALLENGING REGIONAL COMPETITIVENESS
Despite ongoing economic headwinds, the sustainability transformation is in full swing in the European chemical industry. On average, companies have committed to reducing their GHG emissions by 44% by 2030 and to reach net zero by 2043. Since the beginning of 2022, this has coincided with a strong economic headwind of rising energy prices and sluggish demand development, not to mention substantial government support in competing regions, such as the Inflation Reduction Act (IRA) in the USA. Consequently, Europe has seen closure announcements and actual shut-downs of European chemical assets like BASF’s caprolactam, adipic acid, cyclohexanol and TDI plants in Ludwigshafen and Dow’s communication to review the future of European assets in the context of its US$1 billion (€0.9 billion) cost-saving program. More concretely, we have seen announcements in the first quarter of 2024 by ExxonMobil and SABIC to permanently close down naphtha crackers in Gravenchon, France and Geleen, Netherlands, respectively. Due to this, downstream assets like
polyolefin and other derivatives units will be affected as well.
This does not come as a surprise; rather it is the continuation of an ongoing development – and one which may well accelerate in the future. Looking at European import statistics from 2012 to 2023, we observe that organic chemicals imports steadily rose from 21.8 million tonnes to more than 26.6 million tonnes in 2022, an increase of 22% and fertilisers imports from 12 million tonnes to 18 million tonnes or by 50% in the same time. Only 2023, driven by significant slow-down of European chemicals production rates showed declining import volumes, compared to the previous year (eurostat, 2024). Given the recent closure announcements in the European petrochemicals asset base there is little doubt that volumes will continue to increase further again.
DECARBONISATION, GREEN ENERGY & CARRIER LOGISTICS
Europe’s pathway to decarbonisation will largely depend on green hydrogen, alongside other energy carriers. It is undisputed that climate conditions and other limiting factors like land availability affect the supply of local green electricity and put pressure on local green hydrogen generating costs. Consequently, there can be no debate that large quantities of green hydrogen and its derivatives must be imported into Europe.
According to Deloitte modelling and estimates, Europe’s green hydrogen demand will increase from approximately 26 million tonnes in 2030 to 95 million tonnes by 2050. Of this, roughly 43% (over 40 million tonnes) will need to be imported. These are hydrogen equivalents; assuming that 40% of imports will be in the form of green ammonia, the figure translates into an additional 100 million tonnes of green ammonia landing on European shores by 2050 (Deloitte, 2023), compared to 2.7 million tonnes in 2022 and 2.0 million tonnes in 2023 (eurostat, 2024). The major exporting region will be Northern Africa, with Sub-Saharan Africa and the Middle East distant followers.
INCREASED IMPORT REQUIRES INFRASTRUCTURE INVESTMENT
Consequently, compared to the steadier increases in petrochemicals imports, ammonia and other hydrogen derivatives will rise much more steeply and require a rapid extension of harbour infrastructures.
Taking ammonia as an example; together with the direct unloading and storage of ammonia in import terminals, at least some reconversion infrastructure must be built to convert ammonia to hydrogen and feed it into a pipeline network. An estimated €400-500 million of annualised investment is needed by 2050 for import terminal infrastructures only, additional sums for reconversion infrastructure will most likely exceed pure storage investment by multiples, according to the Clean Hydrogen Partnership.
Given the impressive numbers regarding future volumes and investments, it is clear this represents a significant business opportunity for the logistics and storage sector – an industry familiar with long-term investment (and return) cycles. At the same time, governments must provide stable and reliable frameworks to make this happen. Alongside government and industry, (future) suppliers and consumers must come together to jointly align on the vision, the time plan, and the required infrastructure.
Bibliography
Clean Hydrogen Partnership. (2023). Study on hydrogen in ports and industrial coastal areas, Report 1. Clean Hydrogen Partnership.
Deloitte. (2023). Green hydrogen: Energizing the path to net zero.
eurostat. (2024, July 27). EU trade since 2002 by HS2-4-6 and CN8: https:// ec.europa.eu/eurostat/databrowser/ view/ds-045409__custom_12332518/ default/table?lang=en
For more information: www.deloitte.com


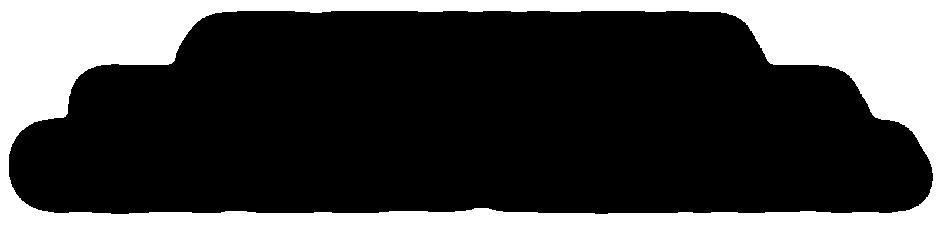

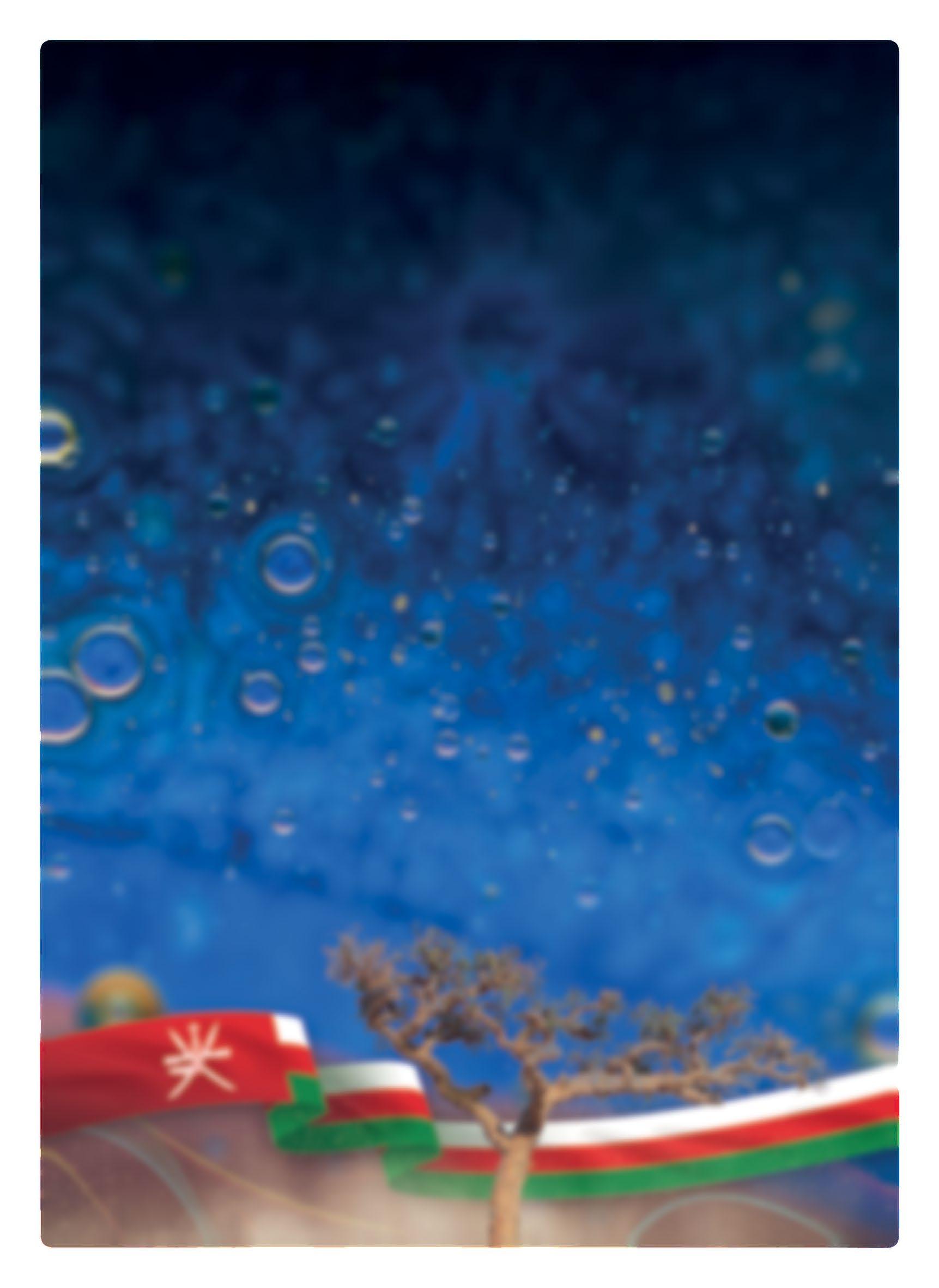
BROADENING THE CHEMICAL SKILLS HORIZON
The Chemical Business Association explains how it’s working to attract new generations to the industry, and encourage experienced workers to stay
THE CHEMICAL industry is reliant on a vast and varied global chemical supply chain that encompasses manufacturing, distribution, storage, warehousing and logistics. It requires people to carry out a multitude of specialised roles. Maintaining a skilled workforce therefore, not only for the tank storage industry, but the wider chemical supply chain, is vital for the chemical industry, and indeed the UK as a whole with over 97% of manufacturing having a chemical input.
SKILLS AVAILABILITY ISSUES
It has been widely reported that many industries are suffering from an acute shortage of workers and, while there is not necessarily an urgent issue in the chemical supply chain, there is an increasing ‘war on talent’ as well as other factors that are likely to have an impact.
According to Brunel University, the UK’s post-Brexit immigration policy has resulted in a shortfall of 460,000 EU workers with the number of EU citizens emigrating back to Europe rising from 86,000 to 151,000 a year. Similarly, the temporary closing down of businesses during the pandemic resulted in many migrant workers returning home, many of whom have not returned. The Ukraine-Russian war, meanwhile, has seen large numbers of Ukrainian haulage drivers recruited into the armed forces, depleting some eastern European HGV fleets workforce by a third. And, despite wages in the chemical sector being around 50% higher than the UK national average, the industry faces domestic recruitment issues. All this is at a time when a significant proportion of the most experienced people in the industry are approaching or considering retirement, with too few students taking relevant courses at universities and many young people not understanding or recognising the value of the chemical supply chain as an employer of choice.
One key issue is that, instead of understanding that the sector is helping solve many of society’s problems, younger generations see it as the cause of issues like pollution, waste and the overuse of pesticides. For associations
like the CBA, addressing those negative perceptions and encouraging more people to consider a career in this sector is essential to maintaining a sustainable workforce with the skillsets the chemical supply chain and wider industry requires.
The sector also needs to do more to upskill the current workforce and improve retention, to prevent experienced employees moving to other sectors due to a lack of career development prospects. Facilitating opportunities for ongoing training and learning can help address both these issues, enabling businesses and employees to acquire the stackable skills they need for future growth, while providing staff with the means to build successful and rewarding careers.
Choosing a career in the chemical supply chain provides a unique opportunity to make a positive impact, contribute to global sustainability efforts, and work alongside talented professionals in a dynamic and innovative field. While many of those already working within it might be aware of this, it is our collective responsibility to share our own experiences and to encourage others to join us and find their own pathway to personal and professional fulfilment, while contributing to the advancement of society as a whole.
To address the skills shortages and the recruitment and retention issues facing the chemical supply chain, the CBA has launched several key initiatives. At the same time, it is actively participating in and supporting other initiatives in partnership with government, industry associations and other stakeholders.
GENERATION STEAM
One of the most dynamic initiatives is Generation STEAM, which recognises the need for creativity and innovation and seeks to ensure that the chemical supply chain workforce has the qualifications needed for the future.
For this reason, the acronym STEAM not only includes the traditional STEM subjects of science, technology, engineering and maths; it also includes an ‘A’ for the Arts as well as Attributes such as Attitude, Ability and Ambition.
In doing so, it recognises the value of creativity and problem-solving within the chemical supply chain, in turn helping attract a talent pool that can work with advanced, creative technologies, like artificial intelligence (AI) and intelligent automation. STEAM subjects will be vital for ensuring tomorrow’s roles – many of which don’t even exist yet – can be filled, not just in traditional manufacturing, laboratory, storage and logistics roles, but in areas, like finance, HR, IT, etc.
Generation STEAM is also about making STEM subjects more appealing. It challenges preconceptions that learning areas are separate by transcending the current way of thinking and changing the way STEM is perceived. It creates a new, much more positive dynamic, that is both engaging and multifaceted.
Extending and complementing the CBA’s existing outreach, Generation STEAM aims to increase young peoples’ awareness of the career opportunities within the chemical supply chain, the various pathways into them and the skills and qualifications needed. It also seeks to address industry perception by highlighting the positive impact the sector has on society and the valuable contributions employees can make.
Generation STEAM also focuses on accessibility, equity, diversity and inclusion, which are central to future growth and success. It also acknowledges that if we only focus on STEM subjects, we risk alienating talented people that may not necessarily consider the sector as a viable career path.
PEOPLE & SKILLS HUB
Another major CBA initiative is the People & Skills Hub (P&SH), a new centre for outreach, training and upskilling. Launched in 2023, the P&SH won the Trade Association Forum (TAF) Skills Development Award 2024 and provides a network where member companies, along with other chemical supply chain organisations and stakeholders, including the government, industry experts, education providers, thought leaders and aspiring professionals, can collaborate and share knowledge.
To meet workforce needs, the P&SH focuses on engaging emerging talent and nurturing and developing existing talent. Besides facilitating collaborative projects, job placements and internships, it offers training programmes, access to the latest research and coverage as well as a wealth of professional development resources.
The P&SH also works to promote the industry as an employer of choice where young people can have meaningful careers and make positive contributions to society. In doing so, it showcases the various career pathways available for those with different interests and skill sets, including non-traditional and newly evolving roles.
To attract talent from a wider range of backgrounds, the P&SH promotes equality, diversity and inclusion across the supply chain through initiatives like the Early Talent Pipeline, which seeks to identify potential future candidates by establishing relationships with education providers at career fairs. During 2023, the P&SH’s student outreach engaged with over 18,500 individuals across 24 educational establishments.
THE FUTURE COUNCIL
Launched in 2022, the Future Council is an initiative that seeks to nurture aspiring talent from within the chemical supply chain. Bringing together a wide range of skills and experience from across the CBA membership, the Future Council enables its current 21 young members to broaden their understanding of the chemical supply chain beyond their day-to-day roles, empowering them to contribute to wider industry policies. Initiating its own events and projects, members share skills, increase their awareness of the sector and learn from each other. Such a strong professional network encourages excellence and helps change perceptions of the industry by promoting the work of the chemical supply chain and the value of STEM education, in order to attract future talent.
5050VISION
While young people are the future of the supply chain, the CBA fully recognises the merits in embracing seasoned professionals over the age of 50, and that employers must create a workplace that values and utilises the talents of
all employees, regardless of age. The CBA’s 5050Vision highlights the value of this segment of the workforce, and proudly showcases the benefits of retaining and actively engaging with these experienced individuals, who can offer a wealth of knowledge, expertise, and institutional insight, while driving innovation, enhancing safety protocols and mentoring the next generation of talent. It also seeks to attract those that may be returning to work after a career break, or looking for a career switch.
TRAINING
As an association that promotes upskilling to members, the CBA is also committed to providing staff training and career development opportunities for its own staff. It frequently supports employees through training in areas such as relevant industry qualifications as well as self-development, management or leadership training. These further benefit the CBA membership as staff are able to support members on a wider range of subjects. The CBA also offers member training opportunities throughout the year in areas such as DGSA, and COMAH, even through to topics such as personal financial planning.
PARTNERSHIPS & COLLABORATIONS
The complex and interconnected nature of the chemical supply chain makes it essential that stakeholders from across the industry collaborate on areas of mutual interest and concern. Leading from the front, the CBA is no exception and is committed to its ongoing support not only of its membership but of the wider industry.
An outreach initiative that is vital for the entire chemical industry, is Generation Logistics, a hugely successful industrywide UK initiative, it showcases the various roles available within logistics, which employs over 8% of the UK’s workforce. Like many of the CBA’s internal initiatives, this seeks to encourage more young people to take up careers within the logistics side of the supply chain, such as the tank storage industry. Launched in August 2022, backed by the Department for Transport (DfT), and with the support of 40 leading organisations and associations, the CBA is proud to continue its official
partnership and leading role with the initiative. Tim Doggett, together with several other members of the CBA’s staff, are ambassadors of Generation Logistics. Generation Logistics has achieved some impressive results, since its launch, it has had over 1.2 million website sessions, over 5.7 million social media engagements, and created a reach of over 1.47 billion.
With some young people avoiding careers in the chemical supply chain because of its perception as a polluter, addressing sustainability is key, not just for driving environmental improvements, but to recruiting the next generation of talent. The chemical industry is the key to a sustainable future – in fact, sustainability is the golden thread that runs through everything, and the CBA is committed to weaving it into every aspect of the organisation’s culture and operations.
The chemical supply chain is playing a pivotal role in the pursuit of a sustainable future, and as the world transitions towards a net-zero carbon economy, it is crucial to equip the industry with the right talent and skills to drive innovation, address complex challenges, and embrace sustainable practices.
The Carbon Literacy Project is an initiative that provides sustainability training for organisations with over 105,937 individuals from over 7,800 organisations now Carbon Literate. It aims to educate employees on environmentally friendly practices, carbon consumption and wider sustainability action. Over recent years, the CBA has delivered multiple free Carbon Literacy training sessions to its membership, enabling those who complete the training and become Carbon Literate to deliver the same training to their teams or organisations.
SUSTAINABLE OPERATIONS & WORKFORCE
For long-term success, the chemical supply chain and tank storage industry needs a sustainable pipeline of talented people with skills and experience in a huge variety of fields. As the world transitions towards a net-zero carbon economy, it is crucial to equip the industry with the right talent and skills to drive innovation, address complex challenges, and embrace sustainable practices.
For more information: www.chemical.org.uk

MAXIMISING MARGINS
LBC Tank Terminals’ Alexander Dorhout Mees explains the sales power of a digitised supply chain and how chemical companies can reap the benefits
IN THE HIGHLY demanding chemical industry, companies are continuously seeking to improve their margins in order to remain competitive. Given the complexity of their global supply chains, it is crucial for these companies to partner with service providers who can play a pivotal role in enhancing their margins. Whether through digitising information exchange to boost operational efficiency, or by ensuring that accurate data is available at the right time to mitigate losses, the digital readiness of service providers is becoming increasingly critical to the success of chemical companies.
LBC Tank Terminals recognises this growing reliance and understands that there is still significant untapped potential when it comes to maximising margins through a digitised supply chain. By focusing on improving digital capabilities, LBC aims to be a trusted partner that chemical companies can rely on to navigate the complexities of their supply chains and achieve better financial outcomes.
HOW DO STORAGE TERMINALS FIT IN HERE?
Storage terminals like LBC are an integral component in global supply chains. They serve as central hubs where large quantities of chemical products are stored, managed, and prepared for further distribution. LBC Tank Terminals’ primary role of providing storage services and enabling make and breakbulk operations is only possible through collaboration with other port service providers. This collaboration ensures that the transition of goods through various stages of the supply chain is seamless, minimising delays and maximising efficiency.
This port ecosystem is responsible for the safe and efficient distribution of chemical products on behalf of its owners. By working together within this ecosystem, we maintain the integrity and security of these sensitive materials, ensuring that they reach their destinations safely and on time. Storage terminals are dynamic partners in the global logistics network, enabling the smooth and reliable movement of products that are essential for everyday life.
As with any service provider, the efficiency of internal processes
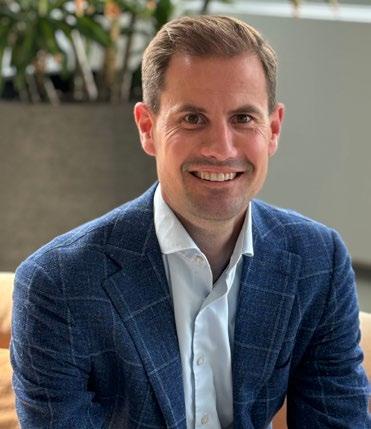
determines how well a company’s primary service is perceived by its customers. Streamlined and wellcoordinated internal operations are essential for delivering the high-quality, reliable service that storage customers expect and rely on.
External processes that rely on information exchange with customers and other port service providers are more complex. These external processes demand careful coordination and clear communication, as they involve multiple stakeholders, each with their unique systems and requirements.
Nowadays, a storage terminal needs to focus on improving both to help increase margins for its customers. By optimising both internal efficiencies and external collaborations, a terminal not only enhances the overall customer experience but also contributes to the financial success of its clients. In a competitive market, this dual focus is key to driving value, ensuring smooth operations, and strengthening the storage terminal’s position as a trusted partner in the global supply chain.
The chemical industry, with its long-standing history in which digitalisation played a minimal role, is gradually recognising the need to adapt.
WHAT IS LBC DOING TO HELP MANAGE THESE CHALLENGES?
LBC Tank Terminals is dedicated to helping its customers effectively manage their supply chains by addressing key challenges throughout the journey. The company understands that its role as a terminal is crucial in the broader context of its customers’ operations. For instance, during the process of loading products into tank trucks, continuous information exchange between the customer and the terminal is essential. While LBC’s direct involvement ends once the product is loaded and the transport mode departs, the customer’s journey continues. Their responsibilities may extend until the product reaches their customer’s warehouse, and the process concludes only after they have sent an invoice and received payment.
To support its customers in this journey, LBC ensures that the necessary information is provided at the right time. Recognising that traditional communication methods, such as email and phone calls, can be cumbersome and impact efficiency, LBC is developing various tools that will improve the flow of information between customers and its terminals. The team recognises the diversity in the size and needs of its customer portfolio, and is leveraging a range of technologies in its digital toolkit to be able to service all those customers.
For example, LBC has developed a data exchange platform allowing customers to integrate their ERP systems via EDI (electronic data interchange) and/or API (application programming interface). Although EDI has been an industry standard for more than 30 years and remains popular due to its familiarity, the terminal industry is seeing a shift toward APIs. APIs offer a more costeffective and flexible solution, and LBC is committed to facilitating this transition for its customers. By implementing these advanced technologies, LBC aims to streamline communication, enhance process efficiency, and ultimately support its customers in achieving better margins and smoother operations.
HOW DOES THIS HELP CUSTOMERS MAXIMISE THEIR MARGINS?
In the example of loading, managing product movement requests via email
involves considerable manual labour, ranging from $20 to $40 (€18 to €36) per order. This expense includes various administrative tasks such as data entry, error checking, and followup communications for both parties involved. Additionally, the manual entry of Bill of Lading (BoL) quantities into customer ERP systems after loading further exacerbates these costs.
The manual process increases labour expenses and contributes to delays in updating critical information. These delays can have significant financial repercussions. Specifically, the postponement in updating BoL quantities and processing invoices prevents sellers from issuing final invoices promptly. Consequently, this delay extends the time before sellers receive payments, leading to increased opportunity and carrying costs. The longer capital remains tied up, the higher the costs and reduced financial flexibility for businesses.
Digitising the information exchange process offers a compelling solution to these issues. By removing manual tasks and enabling real-time updates of BoL quantities in ERP systems as soon as the truck departs, automation streamlines operations and enhances accuracy. This transition could result in a margin increase of approximately $50
to $80 (€45 to €72) per order, thanks to reduced manual work and accelerated invoicing. Automation therefore not only cuts administrative costs but also speeds up payment cycles, improving overall financial efficiency.
The setup costs for an EDI connection vary between $20,000 and $50,000 (€18,000 to €45,000) depending on complexity and message volume. The complexity of the connection depends on the mode of transport; for instance, truck load nominations are less complex compared to vessel load nominations. Due to the higher frequency of truck movements, establishing an EDI connection for trucks presents a more favourable business case. LBC believes that customers nominating 500 or more truck movements annually will see a notable enhancement in profit from implementing an EDI connection.
This example highlights how digital connections can significantly improve operational efficiency. The potential for margin enhancement extends even further with the adoption of APIs. APIs provide greater integration and data accessibility, offering extensive opportunities for increased efficiency and cost savings as the industry continues to evolve.
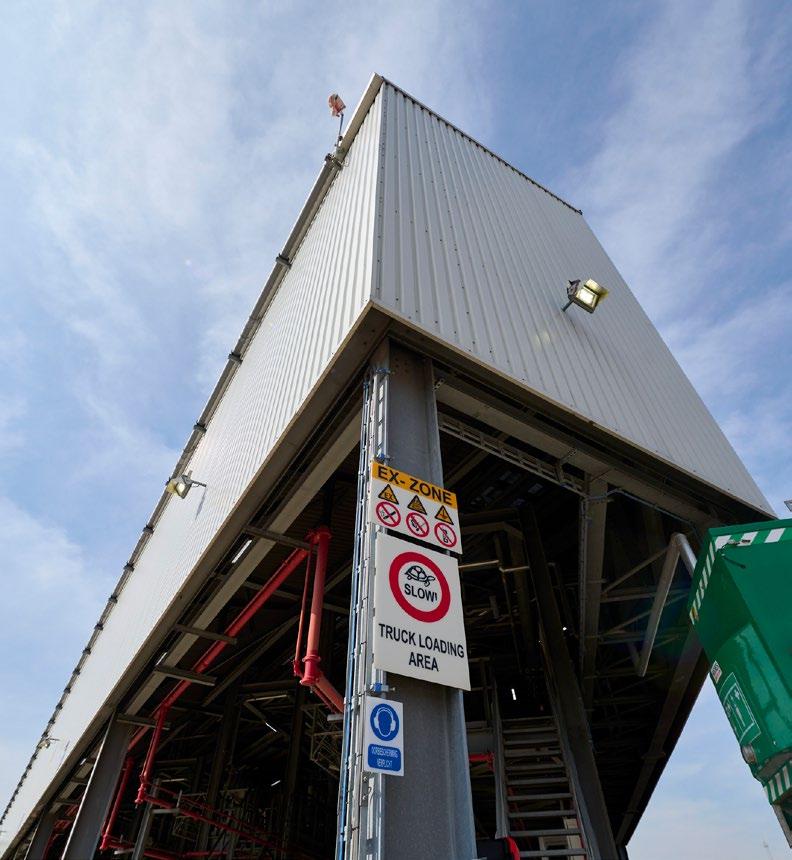
SPEARHEADING THE DIGITAL TRANSITION
Having worked extensively in customer service and commercial roles across both the US and the ARA region, product manager Alexander Dorhout Mees has gained a comprehensive understanding of the various external processes that tank storage companies manage.
‘This experience not only deepens my insight into the operational challenges our customers face but also empowers me to identify significant opportunities where digitisation can add substantial value – not just for LBC, but for all parties involved in the supply chain,’ he says.
Mees joined LBC a year ago, driven by the company’s clear and ambitious strategy to enhance customer service through digitisation. ‘What attracted me to LBC was its management’s commitment to translating this strategy into action,’ Mees says. The executive team has invested considerable time and resources into various digital initiatives, firmly positioning LBC on the path to becoming a digital leader in our industry.
The chemical industry, with its longstanding history in which digitalisation played a minimal role, is gradually recognising the need to adapt. As globalisation increases competition, industry players must explore new avenues to maximise margins – making digitisation not just an option, but a necessity. Mees explains: ‘We at LBC have accomplished a great deal over the past years and are ready to help our customers benefit from our efforts. Regarding digital connectivity, we are actively assisting our customers in developing their EDI business cases, helping them realise the tangible benefits of digital integration.’
‘Understanding that this transition requires time, we are also developing alternative solutions, expanding the digital tools available for all our customers. These solutions are designed to enhance the ease and efficiency with which our customers can communicate with our terminals, ensuring that all our clients, regardless of their digital readiness, can benefit from improved interactions with LBC.’
For more information: www.lbctt.com
01 Alexander Dorhout Mees, product manager, LBC Tank Terminals


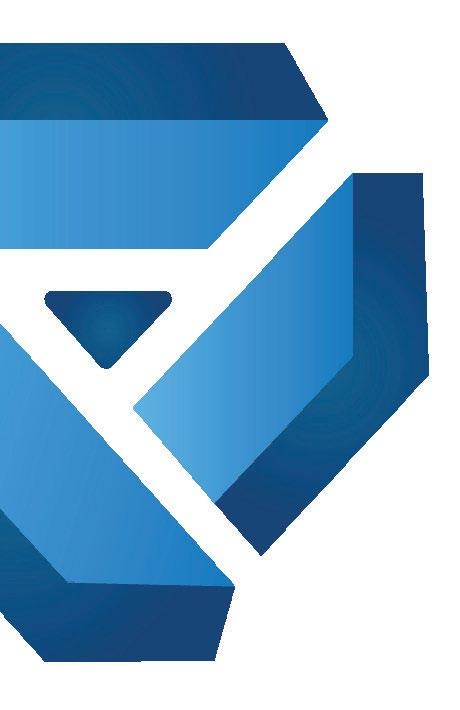
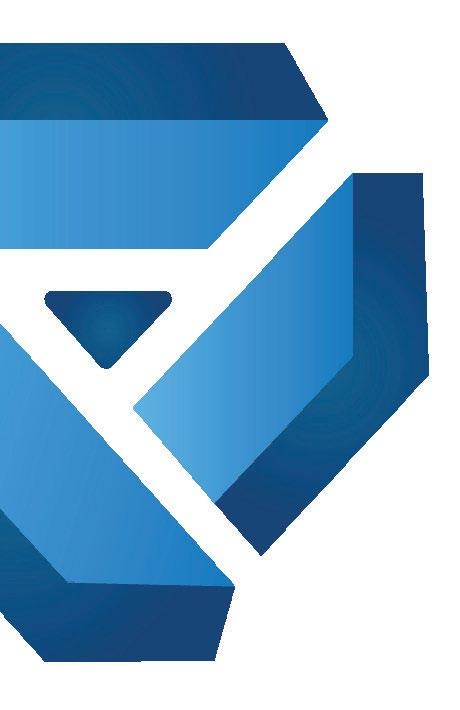
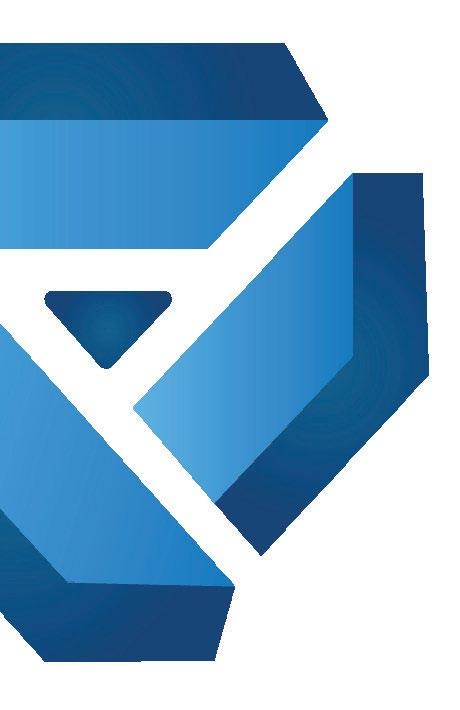


MOBILE STORAGE ADVANCING BITUMEN OPERATIONS
The experts at TEC explain how its new mobile solution will meet evolving storage needs for bitumen
AS THE demand for efficient bitumen storage and distribution continues to grow, the need for advanced solutions has become increasingly important. Recognising these evolving needs, TEC Container Solutions has introduced the MEST Bitutainer (Mobile Equipped Storage Tank), designed to enhance how bitumen is stored, transported, and managed, setting new benchmarks in the industry.
Scaling up capacity to react to changing demand and being able to relocate storage is not traditionally something that can be implemented quickly.
The MEST can offer simple relocation of storage capacity, that can be strategically placed and can also be used in the short term for individual product grades without the need for expensive cleaning operations.
Building on the success of the HighPerformance Storage Bitutainer, the MEST is a self-contained, 40ft storage unit that integrates a variety of features aimed at streamlining operations and
boosting efficiency. Whether used as a standalone solution or as part of a bespoke storage facility, the MEST Bitutainer is to become a key asset in the bitumen logistics sector.
HOW DOES IT WORK?
The MEST Bitutainer functions as a comprehensive storage system, equipped with a secure recessed area that houses various equipment options for recirculation, pump operations, heating, level management and operational control, all of which are tailored to meet specific customer needs. This all-in-one unit is doublewalled with high value insulation for enhanced thermal efficiency and safety. Key to its functionality is the MEST’s ease of transportation and installation. The MEST’s robust design includes reinforced plates and corner twist locks, providing superior durability during transit and handling. The container can be loaded onto a standard trailer or

side loader and placed on any stable, level ground, eliminating the need for expensive civil works or foundations. This not only reduces setup time but also makes the MEST a cost-effective solution for both temporary and permanent storage needs. From this location, the MEST Bitutainer can act as a filling station for multiple smaller capacity trucks and sprayers during road construction projects, for example.
CAPACITY, COST & EFFICIENCY
The MEST Bitutainer offers a significant upgrade in terms of capacity and flexibility. With up to 54,000 litres of storage, it allows operators to manage larger volumes of bitumen than can be stored in tankers, without the need for frequent transfers, reducing downtime and improving service reliability. The ability to customise each unit to meet specific project needs also means operators can offer more tailored solutions to their clients, enhancing their competitive edge.
The MEST’s streamlined design leads to significant cost savings and time efficiencies. By eliminating the need for expensive bund walls and reducing the time required for installation and
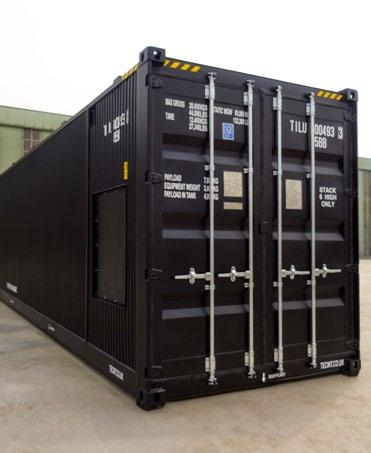
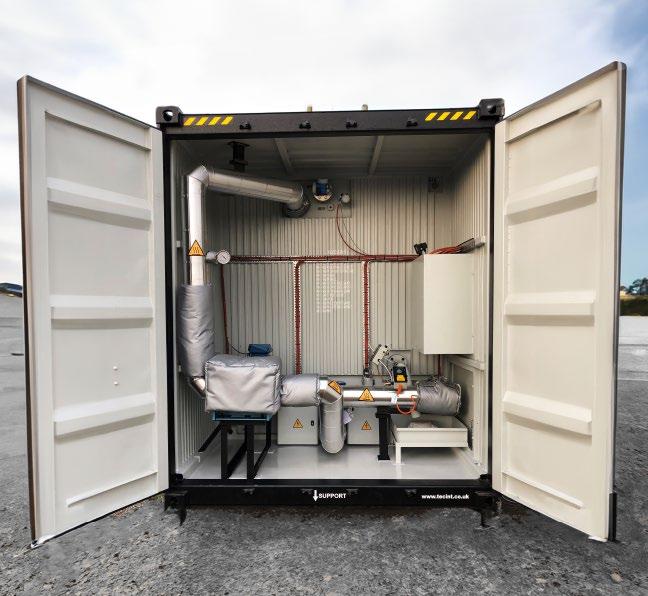
transport, operators can achieve faster project turnaround times and lower overall operational costs. The integrated heating, agitation, and monitoring systems further ensure that bitumen is maintained at the correct temperature and consistency, preventing delays and reducing waste.
The MEST’s enhanced insulation and efficient heating system reduce energy consumption, contributing to lower carbon emissions. Additionally, by reducing the need for multiple transport trips and minimising waste, the MEST supports more sustainable practices in bitumen logistics.
USING THE MEST IN NORWAY
The benefits of the MEST Bitutainer can be seen in action in Norway, where one of the region’s largest contractors utilises multiple tanks distributed around the country to improve sprayer logistics. Previously, the company was using eight tonne spray trucks to drive from their storage site to the road project location, often travelling over 100 km for each fill. This long-distance transport operation was proving too inefficient with rising fuel costs, so the MEST Bitutainer system was implemented. By placing these highcapacity storage tanks closer to project sites and filling them using conventional 30 tonne tanker trucks, the cost per tonne of transport was greatly reduced. Furthermore, the sprayer trucks were able to increase the speed of work,
and distribution with an approach that combines flexibility, cost-effectiveness, and sustainability. Whether it is a small project, or overseeing a large-scale operation, the MEST Bitutainer is capable to meet all expectations.
For more information:
www.teccontainersolutions.com
01 MEST equipment render
02 MEST front profile
03 Inside a MEST Bitutainer
04 MEST Bitutainers on site
meaning less equipment was required per project and application times improved, marking a huge gain in both efficiency and profitability.
In an industry where efficiency, safety and reliability are paramount, the MEST Bitutainer from TEC Container Solutions is a key practical solution. It addresses the challenges of bitumen storage
