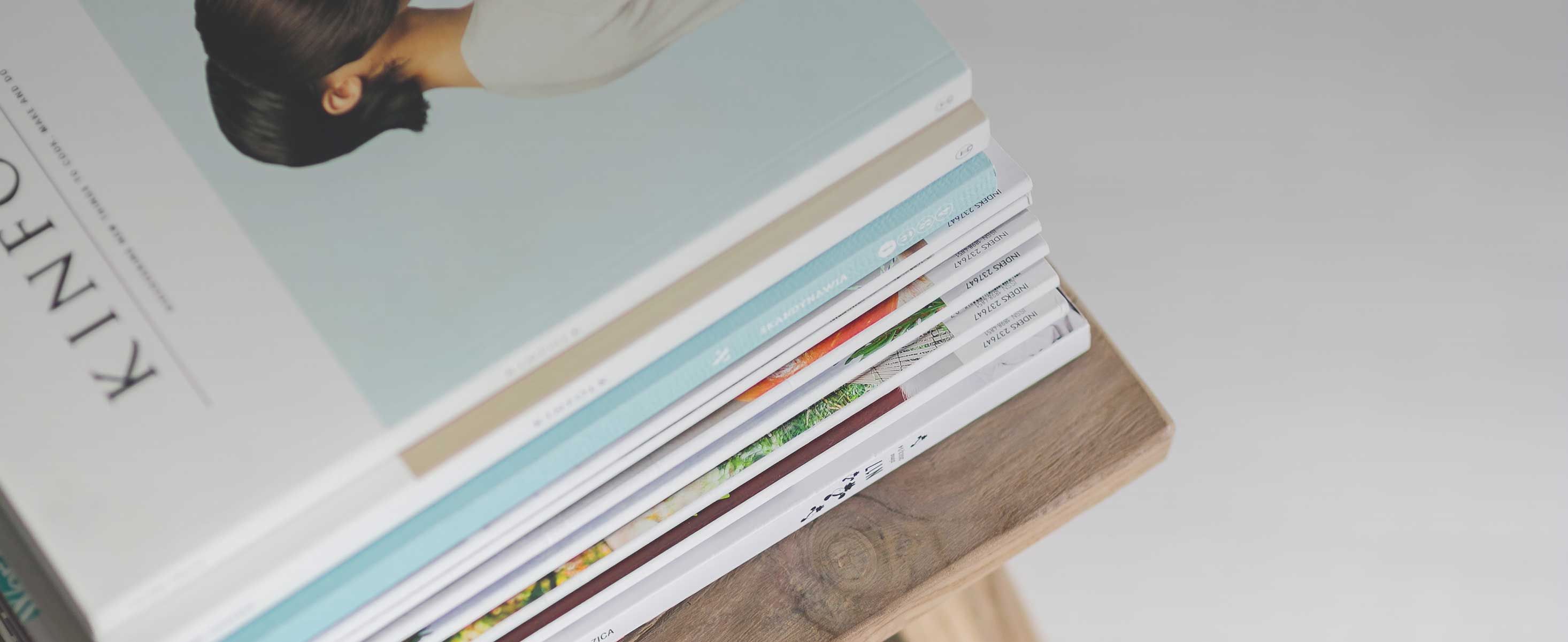
3 minute read
Inventories and Trade Receivables
Further, the trade receivables are to be bifurcated between undisputed-considered good, undisputed considered doubtful, disputed considered good and disputed considered doubtful.
As per Ind AS 109 - “Financial Instruments”, any expected credit loss on trade receivables is required to be recognized as impairment loss allowances (ILA). The amount of impairment loss allowance is not required to be reduced from the amount of trade receivables, but the same is required to be shown as separate line item as deduction from the gross amount of trade receivables.
The separate details of goods-in-transit with respect to each item of the inventory is required to be shown in the notes to the balance sheet.
The mode of valuation of each class of inventory is also required to be disclosed separately.
Why is it important?
Separate disclosure is required to be made for inventories pertaining to stockin-trade. Therefore, if the inventory includes stock-in-trade in the case of a manufacturing or processing entity, it indicates that the entity is also doing trading activities. Therefore, the sales may also include trading sales as there is inventory pertaining to trading. If the trading activity is not a part of the business activities, it may indicate that the entity has undertaken the trading activity, may be for achieving the top line or may be for meeting the growth in the revenue, as projected.
Sometimes, it is also found that the major amount of profit before tax (PBT) is due to trading activities, whereas overall volume of such trading activities as against manufacturing activities is nominal.
Further, which are the items of various inventories which have been carried to balance sheet, can be learnt only when one analyses the details of the inventory. On the basis of analysis of details of inventories, it is also possible to know how much stock is kept by an entity and whether the level of such stock is low or high can be ascertained by comparing the inventory level with the annual sales. Similarly, what amount of sales made during the year or even earlier year remained unrealized can be learnt only on analysing trade receivables.
How to analyse to unlock?
Inventories
For the purpose of analysis of inventories, the first step is to look at what are the items of the inventory. For example, in the case of a manufacturing entity inventories will be relating to raw material, work-in-progress and finished goods. In the case of a trading concern, the inventory will pertain to stock-in-trade. In the case of a finance company, there will be no inventory. As against this, in the case of a construction entity, the inventory will relate to unsold units or construction under development. Therefore, the first point is to look at the items of inventories and find out whether they match with the business operations of the entity. If inventory items are not related with the business carried out, one needs to ask for the details and find out the reasons.
Thereafter, the most important part of the analysis of the inventory is to find out the holding period of each item of the inventory. For raw materials the holding period is calculated on the basis of average monthly cost of material consumed and dividing the same by the total value of the raw material. The logic behind considering the cost of material consumed for the holding period is that raw material is valued at cost or market price, whichever is less, and normally raw materials are valued at cost.
Cost of material consumed is also based on the actual cost incurred and therefore, used for the purpose of finding out the holding period. In case of workin-progress, the manufacturing or the processing cost is also added to cost of materials consumed to find out the holding period of work-in-progress. While working out the holding period of work-in-progress, one should also keep in mind the normal processing/manufacturing cycle. The work-in-progress inventory normally should not exceed the processing/manufacturing cycle. For example, in the case of a textile unit if the processing cycle is 15 days from raw material to finished goods, the stock of work-in-progress, should be less than 15 days. Similarly, holding period of finished goods is calculated based on the cost of material consumed and complete manufacturing cost. After finding out the holding period, the trend with respect to earlier years and industry trend needs to be compared. If there is too much deviation, the reasons thereof need to be examined.
If the inventory includes packing material, stores and spare parts, fuel etc. the holding period on the basis of average monthly consumption needs to be worked out. Normally, the holding period of these items should be around 3 to 6 months, unless it is imported item or where such items is not readily available. In such a case, the inventory of these items may be higher. Therefore, for the purpose of inventory of packing material, stores and spare parts, fuel etc. the type of industry/business is relevant. For example, in the case of ship manufacturing units the inventory of stores and spare parts may be substantially higher than steel manufacturing units.
CHAPTER 15