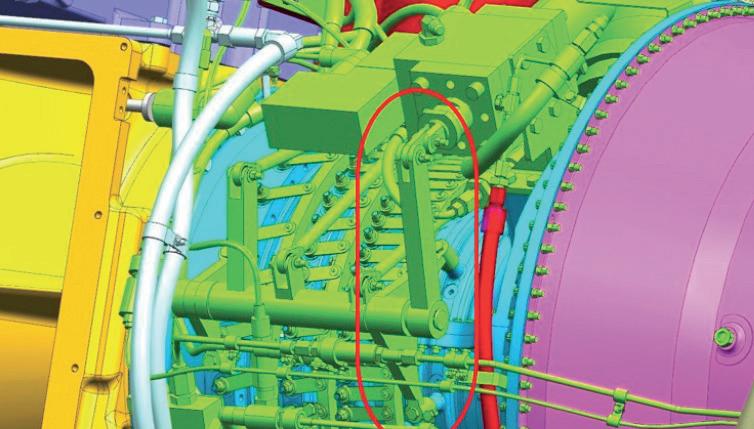
5 minute read
LIGHT WORK OF HEAVY
from TCT EU 28.4
by TCT Magazine
LIGHT WORK OF HEAVY INDUSTRY WORDS: LAURA GRIFFITHS
When faced with the challenge of part obsolescence – perhaps spares haven’t been in production for a long time, your original tooling no longer exists, or the original vendor is no longer in business – you have a choice: you can either find new suppliers or find a new way of doing things.
When recently presented with such a request and nothing but large blueprint sheets to hand, Advatech Pacific, a U.S. aerospace and defence contractor, saw an opportunity to adapt a legacy gas turbine engine family to new prospects in power generation using topology optimisation and additive manufacturing (AM).
“For some of these parts, instead of investing the time and money to create the new casting tooling, it makes more sense and saves money to make them through additive manufacturing,” Matt Humrick, Engineering Manager at Advatech Pacific, told TCT. “As part of that effort, we wanted to combine with topology optimisation and show the customer how these two technologies complement each other and give them some new solutions for the problems they're facing.”
To demonstrate, the team chose a simple short torque arm part which connects a linear actuator to a bellcrank assembly and adjusts inlet guide vanes within the gas-turbine engine. The first step was to create a CAD model of the assembly using the original geometry and structural analysis data from ANSYS simulation as a foundation. From there, a torque arm model containing extra material was placed into ANSYS Mechanical to perform topology optimisation and “iterate and decide what it [the software] thought would be the best solution,” as Matt explained.
The reimagined design needed to save weight but also match the bending stiffness of the original torque arm. Advatech engineers were able specify geometric and surface constraints between the torque arm and shaft, and predict the uneven pressure between contact faces with significant load transfer along the inner edge and almost no load transfer at the outer edge of the shaft. After performing the analysis, the optimised, organic shape was then exported into a separate CAD program for clean-up and further iteration before preparing for test printing in ABS.
Pam Waterman, 3D Printing Applications Engineer at PADT, an authorised reseller of ANSYS simulation software with 25 years of AM experience, who worked with Advatech on the project, said the goal was to show that a seemingly simple part could be redesigned with less material. Prototyping in plastic provided an inexpensive way to demonstrate the new geometry before graduating to printing in stainless steel.
Pam commented: “It's clear that this would have been virtually impossible to produce with traditional machining so additive was the perfect solution to actually create the final part.”
Comparing the geometry of the original part with the new, optimised version with intended stainless-steel material properties, the new torque arm design achieved a 45% weight reduction and matched the original part’s stiffness. However, aside from weight reduction, Matt believes one of the more interesting benefits of topology optimisation is in its capabilities as a design tool.
“What topology optimisation does is allow the designer to break away from preconceived notions and pre-existing design guidelines from [their] company and present novel solutions that you otherwise wouldn't have thought of,” Matt said. “That could either save weight or save cost or produce just an overall better performing part.”
Matt believes test cases like this are a light bulb moment for demonstrating the potential for AM in overcoming part obsolescence, reducing tooling costs, and improving design. In this particular instance, that also meant redesigning to meet new exhaust-emissions requirements.
Matt said: “If you're dealing with a customer that has no experience with additive before, sometimes just taking an existing part without any modification and just printing it, so that they have a part to hold in their hand […] then that sort of opens the door to other possibilities.”
Pam added: “It's not just redoing what you had, even though that can be valuable, it's what's the next step.”
SHOWN:
LEGACY GAS-TURBINE ENGINE DESIGN WITH ORIGINAL TORQUE ARM CONNECTING LINEAR ACTUATOR TO BELLCRANK
SHOWN:
ANSYS MECHANICAL STATIC-STRUCTURAL STRESS RESULTS OF TOPOLOGY-OPTIMISED TORQUE ARM
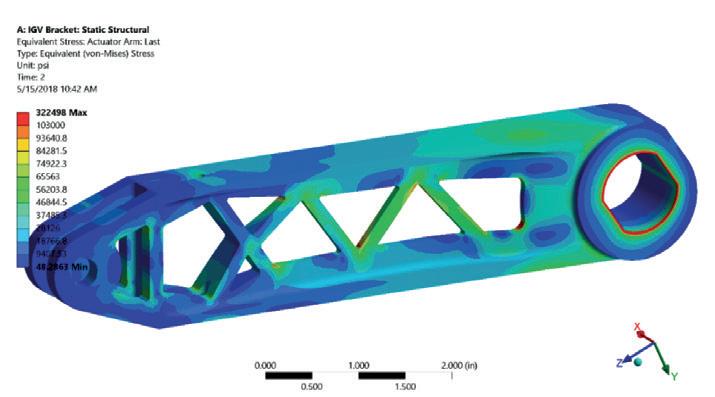
SHOWN:
FINAL VERSION OF CAD SOLID MODEL BASED ON OPTIMISED ANSYS STRESS RESULTS
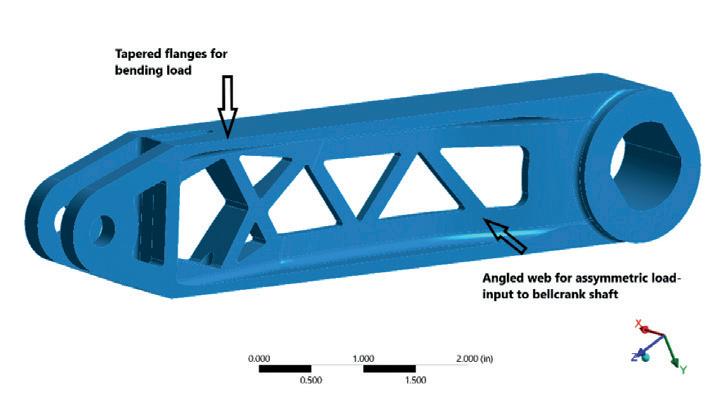
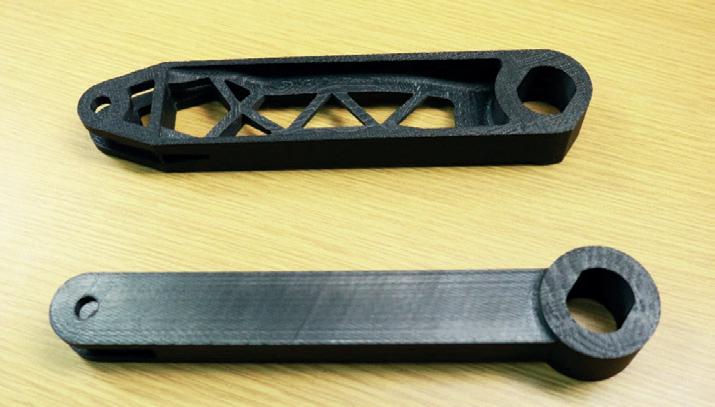
SHOWN:
ORIGINAL (BELOW) AND TOPOLOGY-OPTIMISED (ABOVE) DESIGNS, PRINTED FOR VISUAL COMPARISON IN ABS. FINAL PART COULD BE 3D PRINTED IN STAINLESS STEEL
Make the future with proven powders created by Praxair

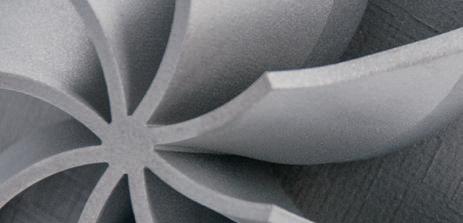
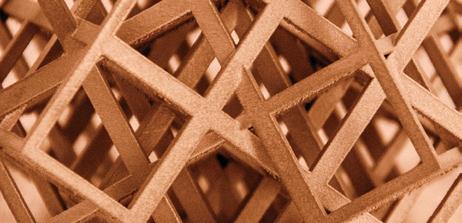
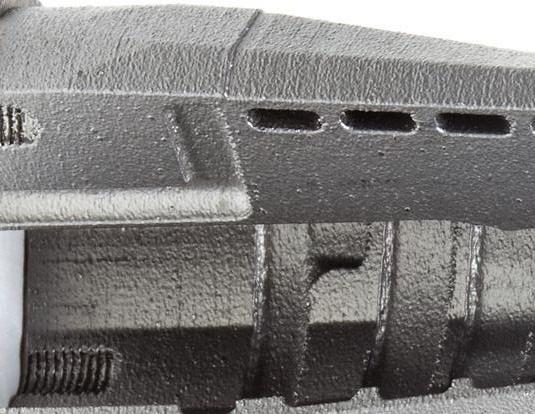
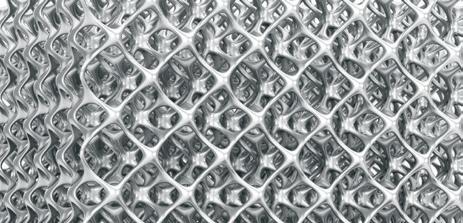
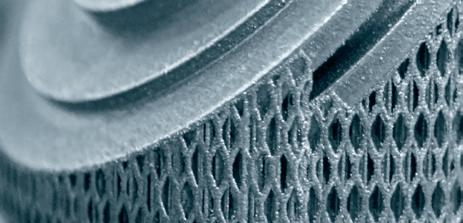
TruForm ™ metal powders support every part you make with capacity, quality and experience. • Used by leading OEMs across AM industry • Custom alloys and particle sizing available
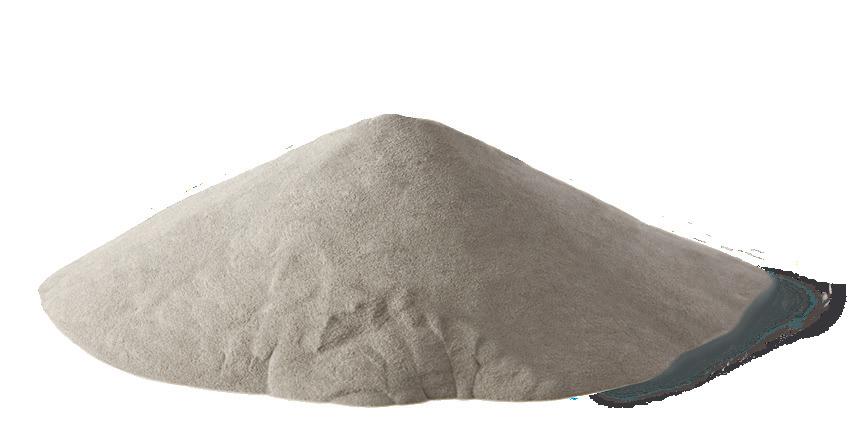
• Aerospace-grade
Learn more: To order: praxairsurfacetechnologies.com/am Praxair Surface Technologies GmbH Am Mühlbach 13, 87487 Wiggensbach Germany Tel: +49 (0) 837 0 9207 0 Fax: +49 (0) 837 0 9207 20 Email: AME_Europe@praxair.com
It’s Tru:
Tru2Spec ™ is the leading custom alloy formulation process for OEMs looking to go beyond conventional powders.
© Copyright 2019 Praxair S.T. Technology, Inc. All rights reserved.
Creative:Clients:Praxair:5701-25931 Updated Half Page TruForm Print Ad for Germany:5701-25931 Updated Half Page TruForm Print Ad for Germany - 192mm x 136mm_v02.indd
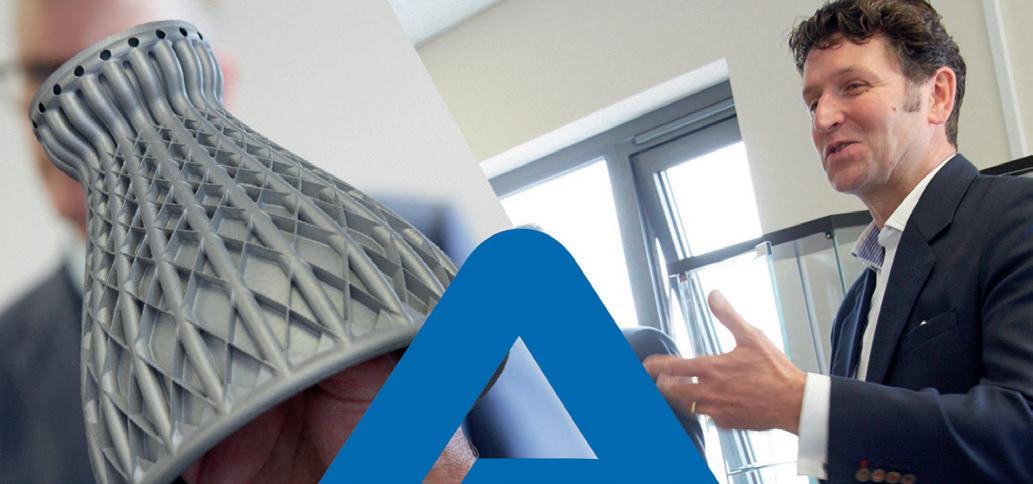
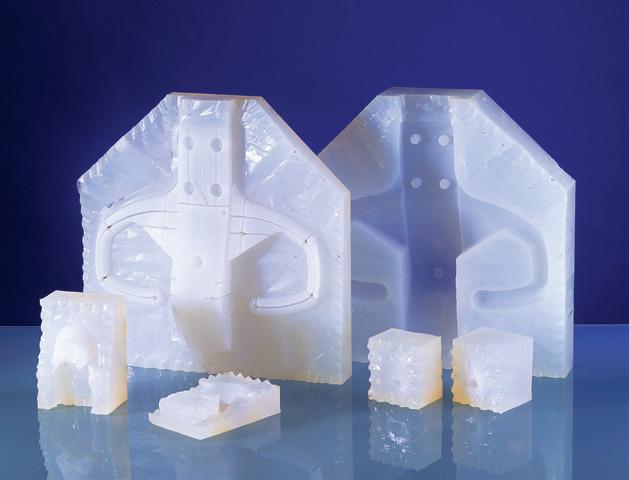
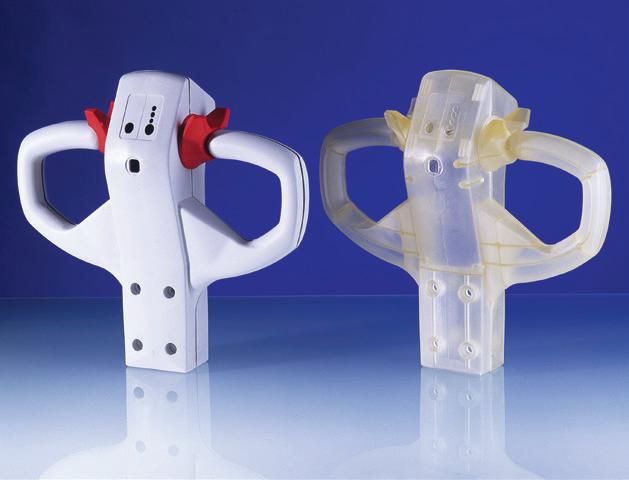
December 19, 2019 11:45 AM
Scott AM specialises in advanced manufacturing technologies to support product design and prototype development, low volume production and rapid prototyping. We work with a range of industries including automotive, healthcare, consumer goods and industrial products.
STOCK & SUPPLY:
• Extensive range of Polyurethane vacuum casting resins • Silicone tooling materials • Accessories and consumables
OFFER:
• Range of vacuum casting systems and ancillaries, including the
ScottAM 1000 and ScottAM 4000 vacuum casting machines • Fully qualified engineers, experienced in service, applications support and training for vacuum casting machines from MTT,
MCP, Renishaw and ScottAM.
With our expertise, qualified and experienced staff, we are here to support you. For more information, please contact us at sales@scott-am.com or visit
www.scott-am.com
ScottAM Ltd
Sutherland Works | Beaufort Road | Longton Stoke-on-Trent | Staffordshire | ST3 1RH Aerospace
Automotive Healthcare Motorsport
Official suppliers of Pelnox and H&K resins from Japan, regarded worldwide for their quality, performance, and safety.