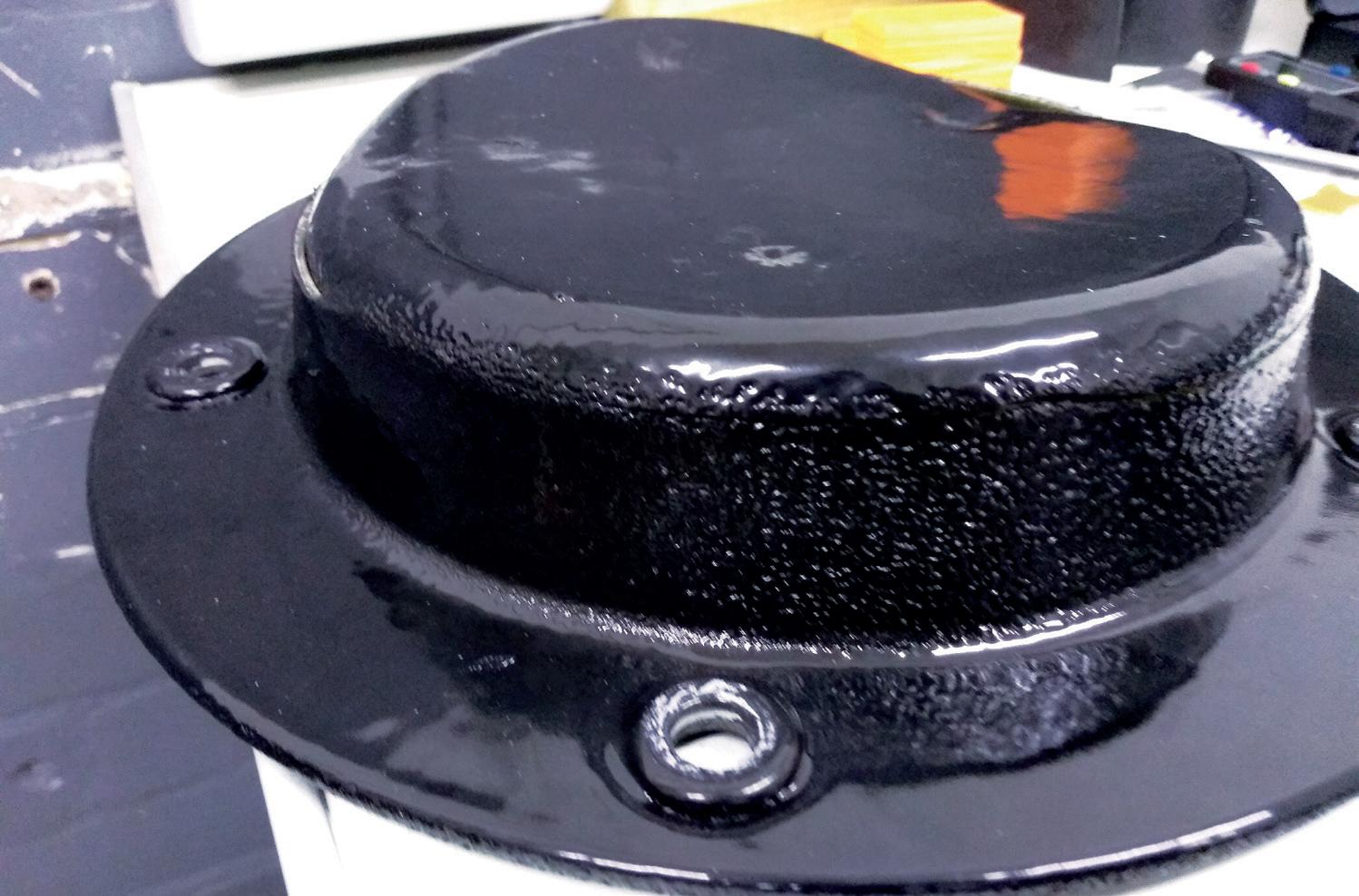
3 minute read
THE RIGHT TRACK
from TCT EU 28.5
by TCT Magazine
THE RIGHT TRACK
Angel Trains Data and Performance Engineer James Brown details the stringent compliance standards 3D printed parts must meet before installation within the rail sector.
No one is more trusted compounded by the very high duty than a transport cycles of our vehicles, with many of engineer; every minute, our trains running 20 hours a day millions of people (at for over 40 years. Hence fatigue least in pre-pandemic times) turn performance of any structurally their car’s ignition, fasten their loaded part is critical. The load cases aircraft seatbelt or board their train, for design of rail vehicles in the UK putting their faith in the underlying are given in standard GM/RT2100. engineering to see them safe to Meeting these are a challenge given their destination. the lack of fatigue data for most 3D
This trust is partly why when the exterior of a vehicle, a further things do go wrong, it can be so requirement is impact resistance due shocking, yet it is the learning from such disasters, codified in countless to the exterior of rail vehicles regularly being struck at high speed by rocks SHOWN: PEKK TESTED TO ISO 5658-2: 2006 SPREAD OF FLAME standards and regulations, that bouncing up from the track. makes the transport industry so safe and so trusted. The high duty cycle of rail vehicles have now taken a number of materials and parts also poses longevity challenges through the process and are seeing numerous
The railway industry, as the for 3D printed parts. Trains can see parts from train armrests to toilet components oldest transportation industry, incredibly high passenger densities being rolled out across our train fleets. For new has the longest history of safety from the rush hour commute, to rowdy suppliers looking to enter the market we are incidents to learn from. However, football fans travelling to a match. To always open to new materials that are cheaper or this means it also tends to have the survive this, 3D printed parts must be better than those we use currently, and with our most comprehensive compliance incredibly hard wearing and easy to partners in the trade body Mobility Goes Additive requirements, which can be a clean, yet the post-processing and we can assist in getting new materials approved. barrier to new technologies, such as coating of 3D printed parts can be However, we do expect those companies additive manufacturing. their Achilles heel, and this is the area marketing “Industrial” solutions to have at least we have struggled the most with in done some research and testing into compliance
Railway fire standards are the getting parts approved. For UK rail issues prior to approaching industrial customers. most stringent of all transport vehicles we require coatings with sectors; exceeding even those of sufficient adhesion to meet a crosscut aviation, driven by the rationale that test with a score of 0 or 1 as specified even in case of a train fire the safest by BS EN ISO 2409:2013. option is still to keep passengers onboard, moving carriages away from While the above compliance the fire. Hence trains are designed requirements do seem onerous, they for very long fire survivability. These can be overcome. At Angel Trains we requirements are codified in the standard EN45545-2. Frustratingly for suppliers, the tests specified by EN45545-2 are bespoke, making it difficult to read across results from fire tests used in other industries. As a rule of thumb, 3D printed materials rated V-0 should meet EN45545-2 requirement set R24 – which allows parts of up to 500g. Currently, we have only managed to get two materials, ULTEM 9085 (black) and Antero 800NA, to meet all railway requirements allowing them to be used without constraint. SHOWN:
The railways are also a high IMPACT TESTING OF COATED PEKK AT 82MPH vibration environment, and this is printed materials. For parts fitted to
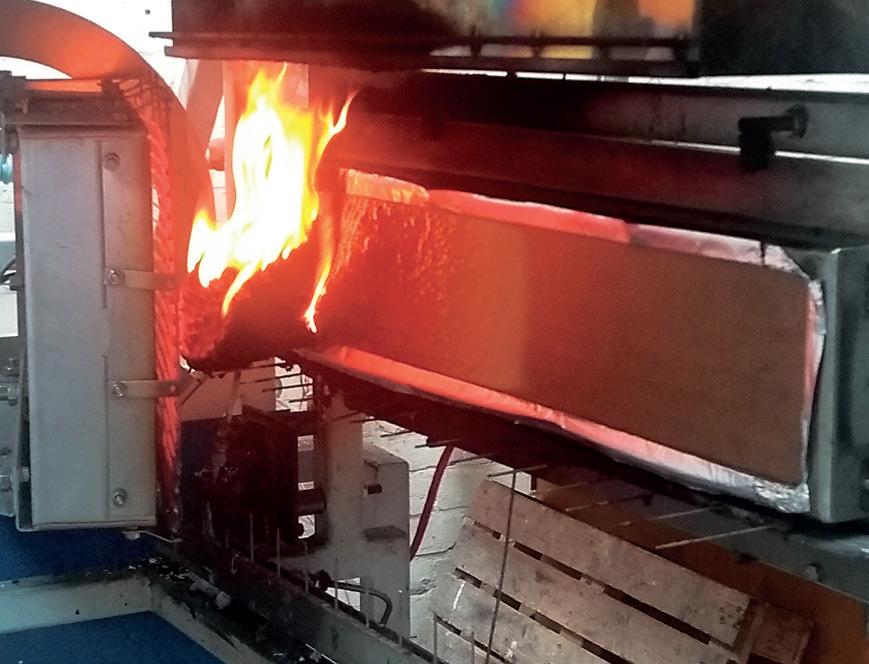