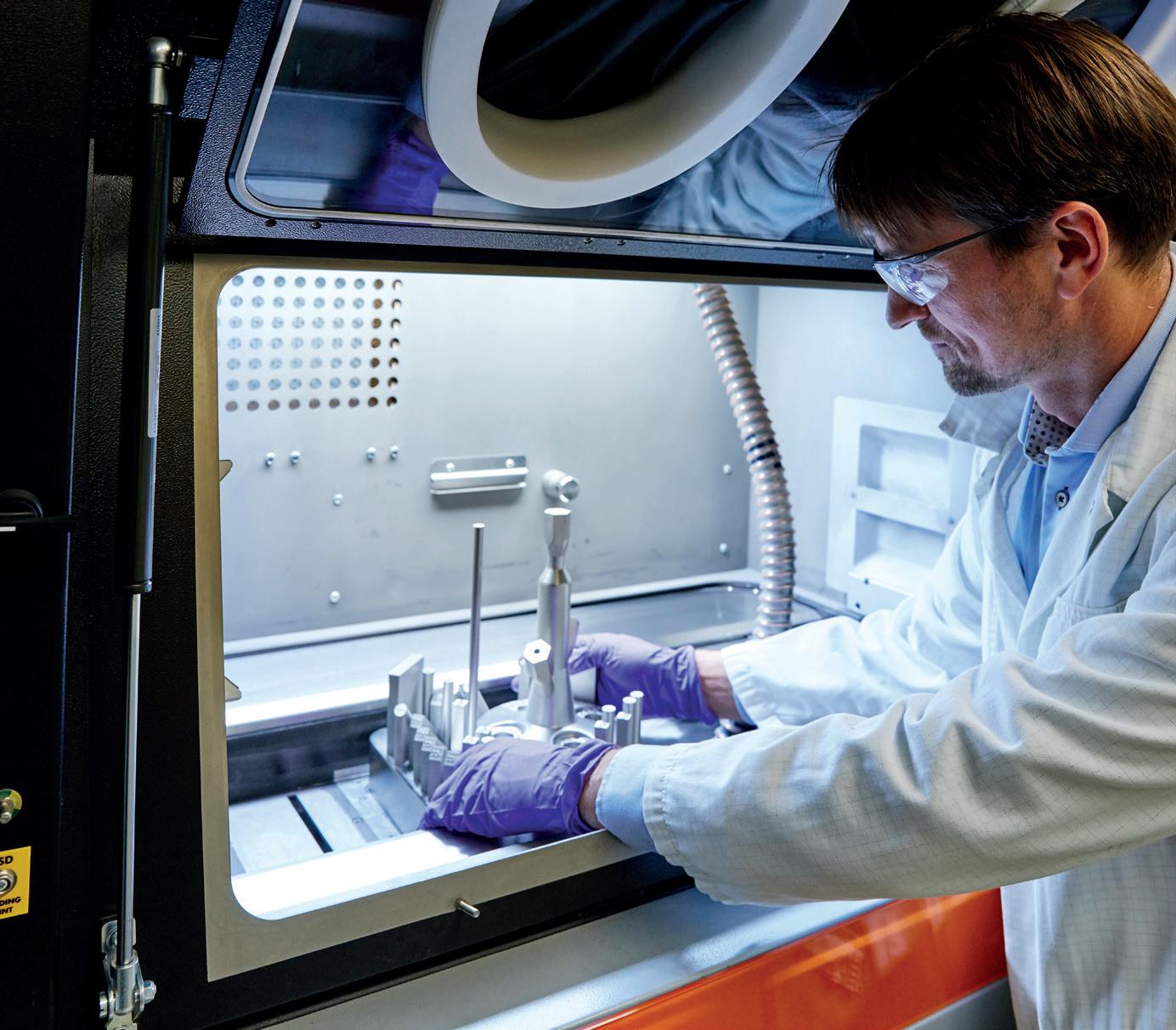
6 minute read
SHELL, SPARE PARTS AND SUPPLY CHAIN
from TCT Europe 29.4
by TCT Magazine
WORDS: LAURA GRIFFITHS
SHELL, SPARE PARTS & SUPPLY CHAIN
Oil and gas giant Shell has been deploying 3D printing at its Lloyd’s Register-qualified Amsterdam-based facility since 2011. Here, Angeline Goh (AG), Shell’s 3D Printing Technology Manager speaks to TCT about supply chain, digital warehousing and introducing new technology to a traditional industry.
TCT: Shell’s 3D printing focus is on spare parts, novel designs, and visualisation. Can you talk about any particular components or projects that have shown the advantages AM affords? AG: The case we worked on in Shell Nigeria is an example of how one could extend equipment life by replacing just what is absolutely needed and in doing so, reducing production downtime and risk in performing the maintenance work. [Editor: For this particular case, engineers used 3D scanning and printing to replace the polymer seal cover on the mooring buoy of an offshore structure in just two weeks and achieved a maintenance cost saving of 90%.]
At a different site, we experienced a few valves that were obsolete and where repair kits were not available. We were able to successfully print the valve internals and continue to use the valves, instead of throwing these away as scrap metal. This presents an agility for us to respond to our operational needs as we have assets that are aging and reaching end of life. AM presents an option to extend the use of equipment and reduces precious resources to produce new spare parts. We are therefore very keen to review repairing parts via 3D printing.
Another way that AM supports our operations with the shorter lead-time to obtaining parts, is that it creates a shift towards buying just-in-time as opposed to just-in-case. The traditional way of buying spare parts at the onset of installing new equipment, may not be necessary if we could print the required parts with the same or improved quality. Spare parts stored in a warehouse require proper storage and preservation and do not provide agility when operating conditions change and the original spare parts may no longer be suitable.
TCT: How easy or challenging is it to get a new AM part from design to production and finally installed at Shell? AG: This is dependent on the type of spare part as well as location. We have a preference to source a 3D printed part for our end users closer to the site of the repair and maintenance. The distribution of qualified service providers could be limited in some regions.
For example, the non-critical and polymer part that we executed for Shell Nigeria took two weeks from scanning the part to printing, to testing and packing for shipment, even though no technical drawings or documentations were available. However, for functional parts with high criticality, we ensure rigour is built into starting with a build process qualification and this takes additional time in the process. The administration of the procurement process requires time, so the ideal situation is when this is already established upfront.
TCT: Shell’s 3D printing strategy is not to manufacture parts itself. How are you qualifying partners and OEMs to source 3D printed components? AG: Shell has a quality management system in which we qualify vendors for materials that we use in our operations. This process already exists. In the case of 3D printing, we adhere to the build process qualification with vendors as per the DNV standard for additive manufacturing of metallic parts [DNV GL ST 203]. There are many service
SHELL, SPARE PARTS & SUPPLY CHAIN
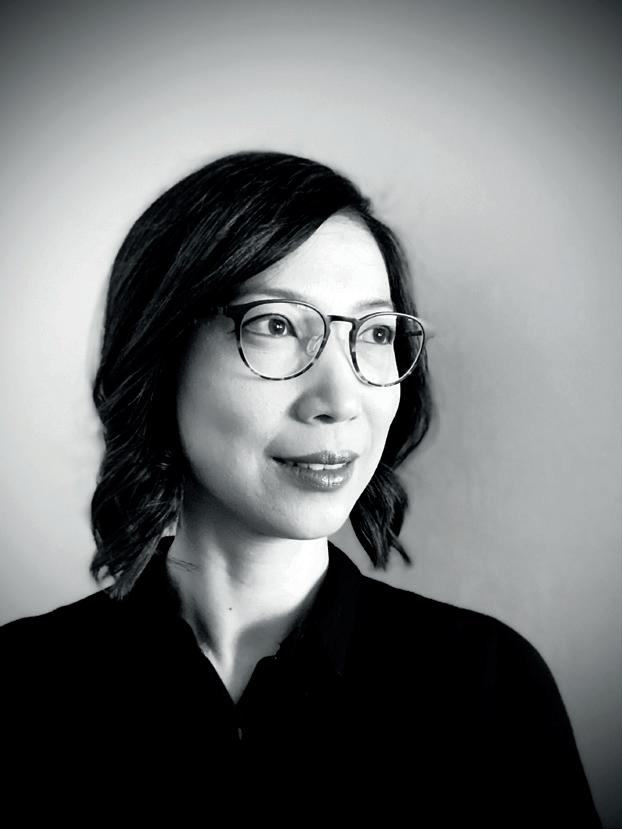
3LEFT: 3D PRINTED PRESSURE VESSEL
6BELOW:
ANGELINE GOH, SHELL
SHOWN:
3D PRINTED MODEL OF A HIGHPRESSURE ELECTROCHEMICAL COMPRESSOR providers for 3D printing but not many with experience to print functional parts for the energy sector and it is important that we have confidence that the service providers can supply quality parts for our operations.
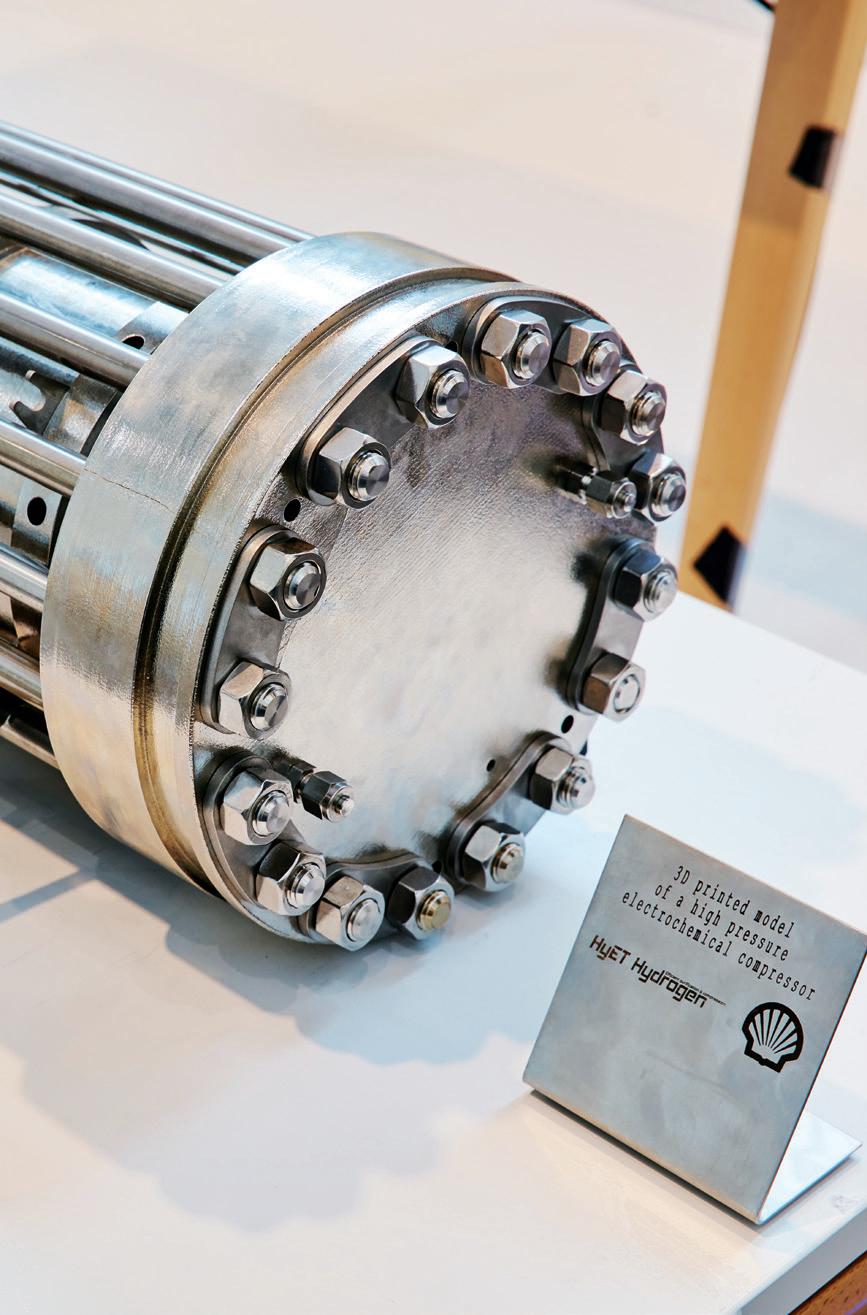
TCT: Can you talk about the benefits that digital warehousing and AM can provide within Shell's supply chain? AG: Having in-house 3D printing capacity was an advantage for us during the pandemic as we could support the community with printing medical devices required by front-line workers.
Digital warehousing combined with distributed manufacturing will provide delivery time reduction for spare parts required by our operations and allows for buying and manufacturing what we truly need. Having a digital copy of the spare parts ensures that we have a way to produce what we need, and not run into obsolesces.
TCT: Are there any challenges that may prohibit the acceleration of AM within the energy sector? AG: Standards bodies and organisations that are responsible for international standards and legislation are still playing catch up to provide the necessary guidance and approve for the use of 3D printed parts in energy sector. For example, work is still ongoing in our service conditions and pressure equipment, etc. As an industry, we do not yet have a standardised way to qualify AM service providers yet.
TCT: Can you talk about the process of converting a traditional industry to a digital mindset? AG: Tremendous effort is taken to ensure a high level of technical assurance when introducing new technology, including 3D printing. We are a heavily regulated industry and introduction of technology needs to be done with a management of change process, and risk mitigation is detailed and thorough. We take our time where needed in implementing technology. Here is where knowledge sharing across the industry can help in providing a level of confidence on what has been investigated and proven to work.
We pride ourselves on our engineering skills. We would rise to the challenge of commissioning the world's largest floating liquefied natural gas platform and apply the same penchant of detailed
planning, analysis, and data acquisition to devise a perfect solution. Diversity in the team and multi-disciplinary approach, including the involvement of external partners towards introduction and scaling up of new technology helps us to gain external perspective and ensure risks have been evaluated from different angles and managed.
TCT: What opportunities for sustainability do you see AM bringing to Shell? AG: One may argue that in AM, transportation of the raw materials such as powder and wires are still required, so the emission issue remains. The game changer here is instead of shipping multiple spare parts to a warehouse only when we need it, only a fraction of the weight in powder is shipped to print what we really need. Ideally, the design has also been optimised so less material is required and higher integrity and performance of the part can be achieved. It is about extending the equipment life, being able to repair a part rather than to throw away a piece of equipment because a small spare part is not available. These steps add up quickly towards responsible use of resources.
Additionally, we see AM as a possible technology to recycle materials, such as end of life windmills whereby blades can be grinded to create feedstock back to 3D printing instead of going to a landfill. This applies to electrical as well as organic waste material.
TCT: To date, Shell has installed over 50 3D printed spare parts. Can you give us a sense of Shell’s ambitions with 3D printing and how much you envision that number growing? AG: We move away from setting a hard target for 3D printed parts as we believe it should be value-driven and achieving the objective of solving problems for our operations. Right now, the demand and growth in the number of parts have grown exponentially [compared to] when we started and we are moving onwards digitalising the inventory at our sites.