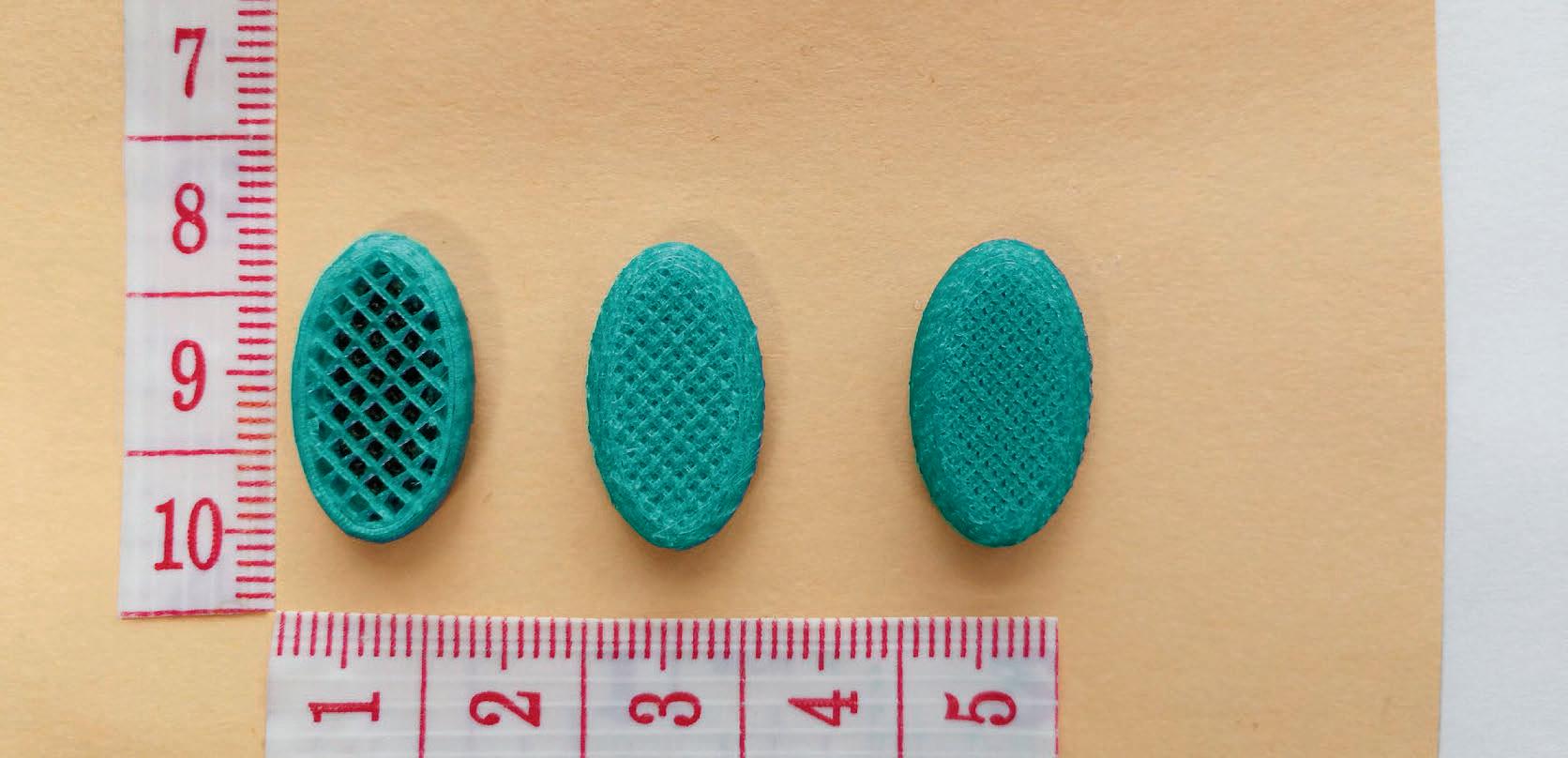
5 minute read
MINDFUL MANUFACTURING
from TCT Europe 29.5
by TCT Magazine
WORDS: SAM DAVIESMINDFUL MANUFACTURING
The governments are debating legislation, the public are making lifestyle changes, the activists continue to protest, but what are corporations doing to address the climate emergency?
Increasingly, it’s appointing people like Rosa Coblens to positions like VP of Sustainability. As one of the pioneers of 3D printing technology, Stratasys likes to consider itself a leader in the additive manufacturing space, the leader on the polymer side, and it has decided it should also demonstrate leadership on the sustainability front. In the space of two weeks earlier this summer, it joined the Additive Manufacturer Green Trade Association (AMGTA) as a founding member, and promoted Coblens from a communications role to head up its sustainability efforts.
The aim, after much talk about 3D printing’s sustainability benefits, is to look deeper at the Environmental, Social and Governance and start providing the evidence to those claims.
“We’re not looking to share a message, we’re looking to do,” begins Coblens. “A lot of what we know about the value of additive manufacturing doesn’t have data behind it. We say that we know it’s less wasteful – you only use the material you need to create the part, it’s by definition more sustainable – but we don’t have the research around that, we don’t have the specific data points and we can’t improve year on year because we didn’t create the baseline.”
In her new role, Coblens will lead efforts in achieving a series of UN Sustainable Development Goals (SDG) relating to responsible consumption and production; industry, innovation and infrastructure; climate action; and quality education. It will see Stratasys reduce waste and reuse materials; promote inclusive research and make information more accessible; reduce the company’s carbon footprint; and develop education and learning opportunities around sustainability.
As Coblens gets to work, the driving force for these initiatives has come from above, in particular CEO Dr Yoav Zeif, but in landing on these SDGs, it was the employees who directed the company’s initial focuses by responding to a series of surveys. They too, per Coblens, share the leadership’s passion for these efforts.
“I think that they believe 3D printing is a solution that, in terms of climate, can really change the world,” she says. “It can bring less inventories, digital iterations before you print them, there’s so many savings in adopting and adapting this technology that I think it’s why our workforce wakes up every day, because they know what they’re developing is part of this… it’s more of an evolution than a revolution.”
This evolution will see Stratasys set up projects around its SDGs, implement key performance indicators to track progress, establish forums to foster discussion, and allocate budgets to support the endeavours. Coblens describes it as a ‘serious undertaking’ at the company and hopes the work she and her team carry out could contribute to the creation of best practices for the additive industry. Such is the nature of AM technology, there’s recognition that the processes can never be perfect, but the reality of the situation is that Stratasys and co need to do all they can.
“We’re moving into manufacturing. It’s resource intensive, we’re not going to be a green company, we’re not selling a green product,” Coblens says, “but we’re making a commitment to always make improvements, to impact climate in a positive way while we do this.”
Such is the value proposition of additive manufacturing and all it can offer – from lightweight designs to digital inventories and localised production – Coblens believes that more people need to be appointed to roles like hers within the AM space. As the application of 3D printing grows to include more production parts, so too does the responsibility of those who provide the technology platforms.
“Sustainability and profitability, they work together, meaning that the more that we build our business, the more impact that we can have on each of these ESG elements,” Coblens says. “The stronger the companies are, the more responsibility we have to introduce mindful manufacturing, where you’re thinking about what you’re creating before you go into the process of creating it. We’re not just trying to incrementally change manufacturing, we’re probably going to shift the face of what manufacturing looks like over the next decade, so do it with a deep thought process about the people around you in the room, in the innovation process, the communities you serve, your customers and their needs.”
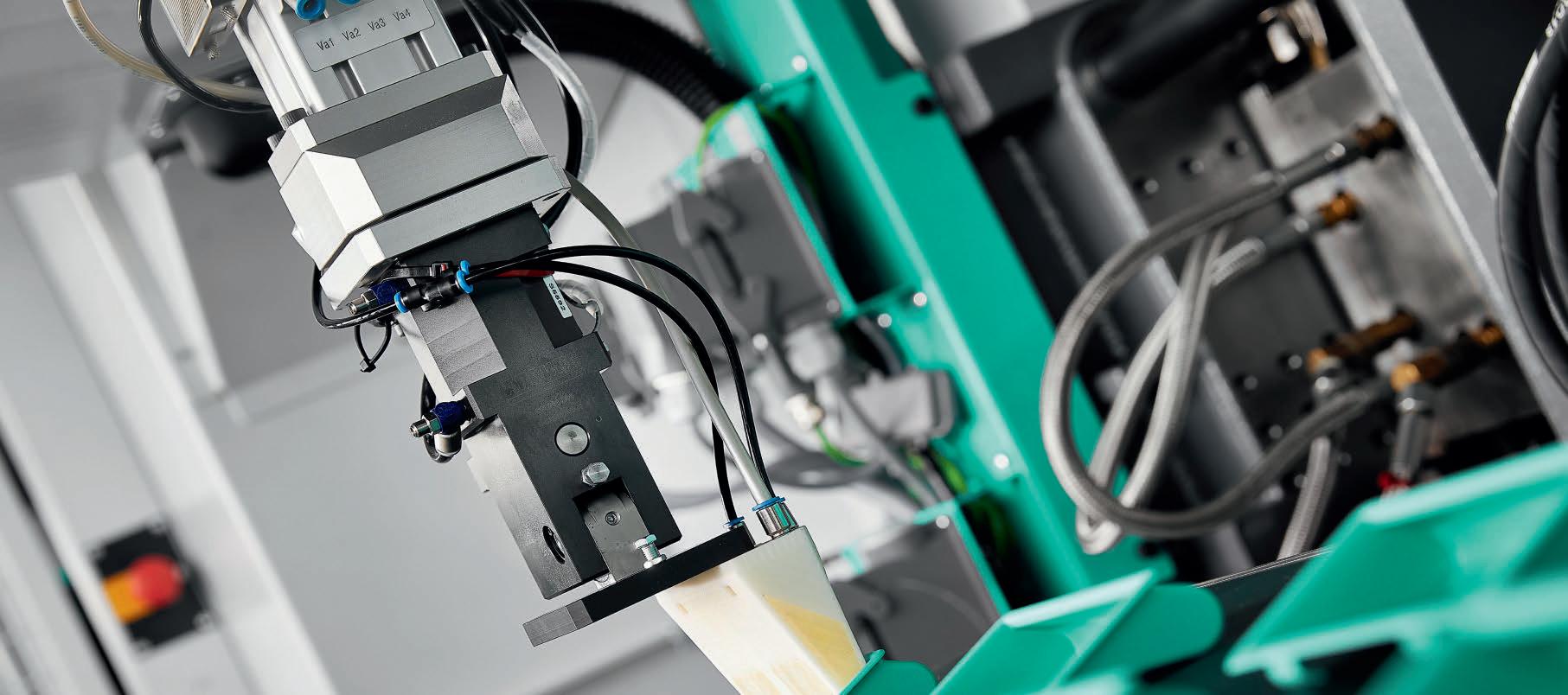
THERAPEUTICS FOR THE FUTURE
Tablets containing indivdualized fillers and active ingredients can be additively manufactured using the freeformer.
PERSONALIZED MEDICATION
Additive manufacturing has become an important production method in the healthcare sector. In one area – patient-specific therapeutics and drugs – there are still a number of technological restrictions to overcome.
Pharmaceutical engineer Dr. Sheng Qi, a scientist in the School of Pharmacy at the University of East Anglia (UEA) in the United Kingdom, has dedicated herself to the research of novel drug delivery technology development. Her research group focuses on pharmaceutical materials and innovative processes. This also includes ARBURG Plastic Freeforming (APF). The freeformer additively manufactures various tablet variants and release patterns. The APF process has the potential to manufacture entirely new personalized healthcare products.
Dr. Sheng Qi is proposing offering more personalized medicine: “Customized tablets can be a solution for pediatric, geriatric, and patients with complex chronic conditions.“ The APF technology and the freeformer, designed as an open system, enabled UEA to make direct use of standard granulate from common pharmaceutical polymers and active ingredients. With no additional plasticizers, the plastic melt could be discharged in the form of tiny droplets and used to additively manufacture tailored drugs. Using the freeformer, a wide range of filling level variants were able to be tested and created at UEA. The porosity of the tablet allowed the active ingredient’s release rate to be regulated.
The APF process provides UEA with a considerable advantage when it comes to testing and evaluating various active ingredient combinations and their release rates. It is even conceivable to blend several drugs with specific dosages and package them in a 3D-printed tablet with sophisticated functional micro-structures designed to speed up patient recovery.
Thanks to its unique advantages in terms of material processing and droplet discharge, this AM technology is an ideal instrument for research projects. Pharmaceutically approved production materials can be blended and deployed in an additive manufacturing process tailored to each individual patient.
i
Further information: www.arburg.com