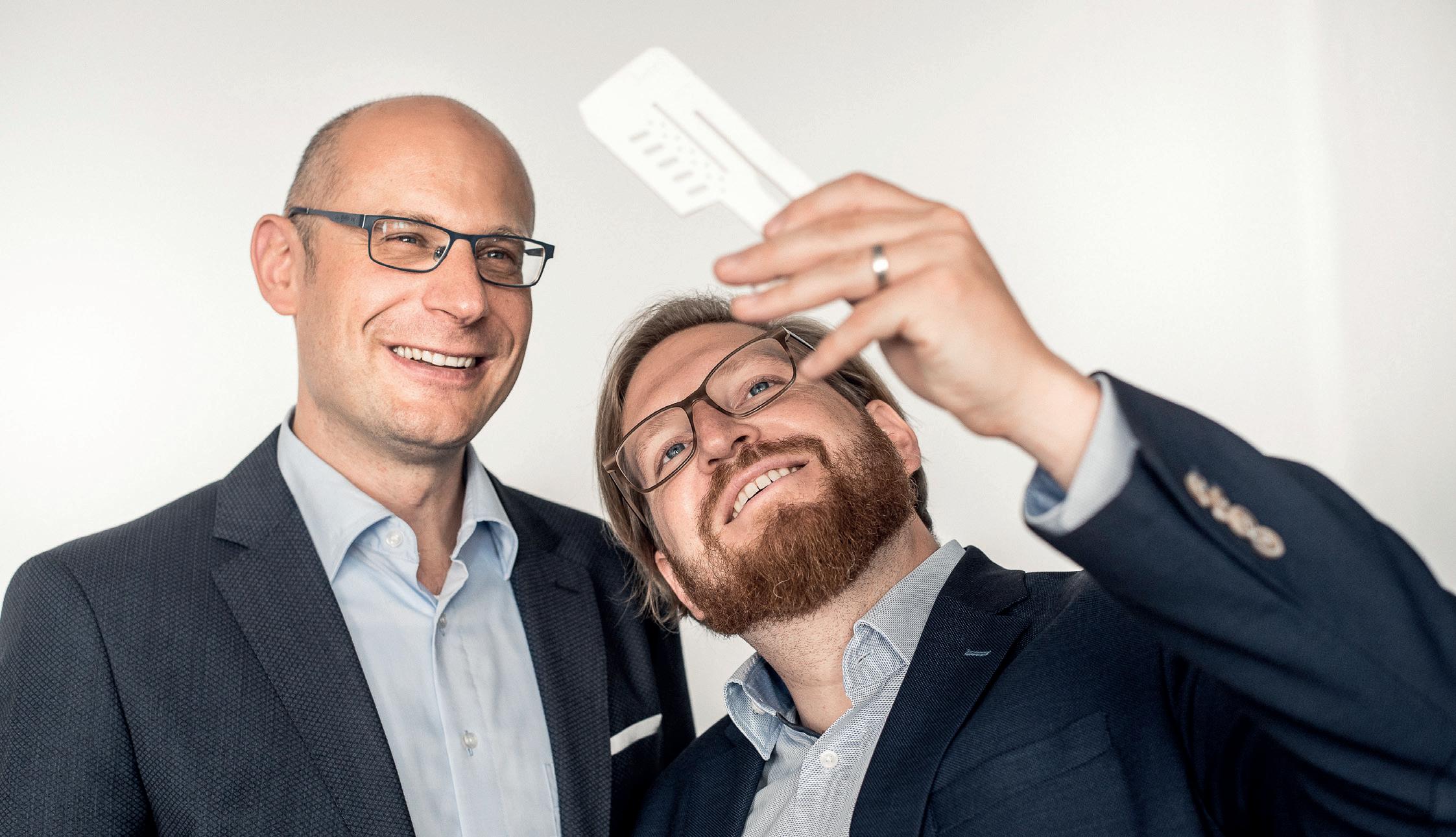
3 minute read
LITHOZ AT 10
from TCT Europe 29.6
by TCT Magazine
LITHOZ AT 1O
Lithoz CEO Dr Johannes Homa reflects on a decade of 3D printing ceramics.
TCT: In the beginning, what demand was there for a ceramics additive manufacturing technology that could be used for production?
JH: At the beginning, it was difficult to clearly vision the demand for it. We knew that 3D printing was already well established in plastics and metals but ceramics was still reluctant to use it and the question was, 'why was this?' And it was because there was no technology on the market which could fulfil the demand of the ceramic industry, which is a very highquality standard. We didn't make any deep market research but the gut feeling was if we solve this problem, there has to be a similar demand as in plastics and in metals. And at the end it was true.
TCT: What unique challenges do ceramics pose for AM compared to other materials like polymers and metals?
JH: Ceramics are used in very harsh environments, usually where you have very high temperatures, where you have high abrasion, where you have high chemical corrosion, all of these harsh environments. So, to sum this up ceramics are used where other materials fail. If you want to use a 3D printed ceramic, it has to have the same or equal material properties as the conventionally formed because otherwise, you can use any other material. In the beginning, I was very much working in plastics and there, I would just make a prototype. It just [had] to look like [the part], it doesn't have to have the same properties, it just had to withstand the test and that's all. But here in ceramics, you have to have the same material properties and there is nothing like, in the sense of plastic, like prototyping, we have just production with lot size one. And that's a huge difference. You don't want to have a geometry prototype or to make a fit test, you really want to use it in the real conditions and that's the big challenge here.
TCT: You’ve emphasised how your work is rooted in academia and how this feeds into Lithoz’s ongoing story. Can you talk about the importance of this feedback loop between academia and industry?
JH: Since we have an academia background we are still working a lot with academia in order to further develop our process and our products because on the one hand, you need a very deep understanding of the process and of the parameters behind the process if you want to modify or develop things further, and on the other hand, you need somebody who takes a very close look at the microstructure, for example, or at failures which are in the part to really solve all the issues because at the end, the industry is only interested in an application which works. They are not interested in developing something, they want to have applications. This is, I think, where we had a really good match or where we have built up our company on this academia background and still with this academia support to provide a technology where the industry can use it very quickly for their application and it already fulfils their needs.
TCT: You recently stated that you believe Lithoz will be “the first in history to set up geographically independent, yet digitally connected, machine parks for the global mass production of 3D printed applications.” Can you elaborate on that vision?
JH: First of all, we are really the only ones in the ceramic industry […] where [our] customers are doing really serious production and they are starting to build their factories and developing everything for future growth. We are now, I would say, fairly well established in doing serial production but the vision of us and of our customers [is] that it's completely independent from where the machine is situated. They want to produce maybe something here or something there and there is one division or one guy who prepares the parts and they could print it in Europe, they could print it in Asia, they could print it in the United States. So that's globally independent, but everything is well connected. And that's where we have now worked on the technical requirements to be able to perform that and we have achieved very good results and this will be rolled out in the next years.
Listen to the full interview on the Additive Insight podcast: mytct.co/Lithoz10