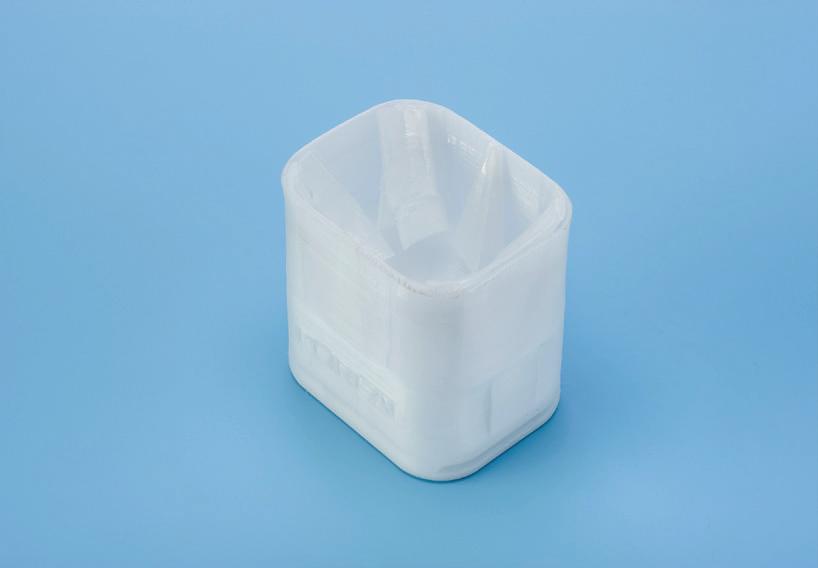
3 minute read
AM? IT’S WORTH IT
from TCT Europe 30.3
by TCT Magazine
WORDS: LAURA GRIFFITHS
In 2018, I hopped on a plane to Atlanta, Georgia to judge a competition that would see university teams put forward unique solutions for 3D printing in one of the industry’s most challenging materials. Founded and hosted by chemical and materials specialist Solvay, the Additive Manufacturing (AM) Cup demonstrates how open-source AM innovation can lead to new solutions.
For 2021, that meant teaming up with cosmetics giant L’Oreal and Ultimaker. Sixty international teams were tasked with putting forward an application that could transform production line agility using Solvay’s Solef PVDF AM filament, a highly non-reactive thermoplastic fluoropolymer that’s inherently flame retardant. It’s not the most glamorous of applications for a company specialising in beauty products but the benefits of 3D printing along manufacturing lines cannot be understated.
Miguel Calvo, CTO at Ultimaker, said of the company’s role in the competition: “Put simply, it's leveraging the expertise around the ecosystem, bringing them into the platform so that we can deliver a greater, wider spread of applications to our users. This challenge perfectly highlights that.”
3D Fab from the University of Lyon, France took home first prize with a versatile monobloc design that could be used on a packaging line to hold unstable products in place. The design is based on a reversible deformable puck that can be printed quickly and applied to everything from mascara tubes to tall shampoo bottles.
“They have invented a solution that can basically work for all the bottles,” Andrea Gasperini, Business Development Manager at Ultimaker, explained.“There's a lot of noise because we have 400 pucks moving around and touching each other all the time but here, the bottle was really firm. The bottle is not allowed to move at all because every movement outside of the pack would imply a spill or a defected product that needs to be removed somehow before it gets packed.”
Matthew Forrester, Head of Material Transformation & Recycling Science at L’Oréal, an engineer by trade, knows first-hand what is expected from this kind of application from considerations around environmental impacts at every stage of the supply chain to consumers who want their products quicker than ever before.
“As soon as you click on the Amazon button, you want the part to be at your door, which obviously means that we need to have the industrial tools which are capable of replying as quickly as this,” Forrester said. “So being able to quickly change between products, ramp up production, slow down production, move production between countries […] these are the kinds of challenges that engineers are having, and this is exactly what we wanted to share with the participants by opening up a window into our industrial processes.” The winners were taken on a guided tour of two L’Oreal sites where they were able to put their pucks on the line. While L’Oreal’s facilities have been equipped with FDM 3D printing for the last four years, in some cases just metres away from the production line, the collaborators have been impressed by the ideas put forward.
Forrester said. “They're not plug and play solutions. We can’t just throw it straight onto the production line but what they have come up with is different solutions which can inspire our teams, and we can integrate some of their ideas and ways of thinking as well which is just as important as the finished product.”
Brian Alexander, AM Global Product & Application Manager at Solvay, remarked how the winning parts were able to “virtually match the performance and quality” of their conventional injection moulded equivalent, affirming not only the success of the winning team but the value of accessible 3D printing technologies in industry.
Calvo added: “It was nice to see people outside of the 3D printing industry really leveraging the abilities of this technology to unlock their design, innovation and design freedom.”
SHOWN:
AGILE MANUFACTURING USED FOR LIPSTICK MANUFACTURE WITHIN ONE OF L’ORÉAL’S PRODUCTION FACILITIES (CREDIT: L’ORÉAL)
SHOWN:
WINNING DESIGN BY 3D FAB LYON
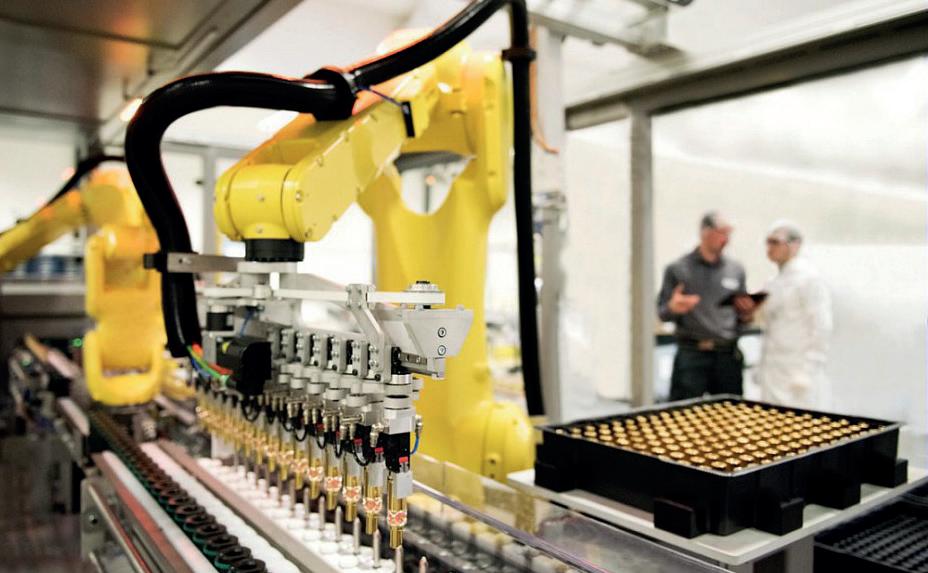
VISIT ULTIMAKER AT TCT 3SIXTY