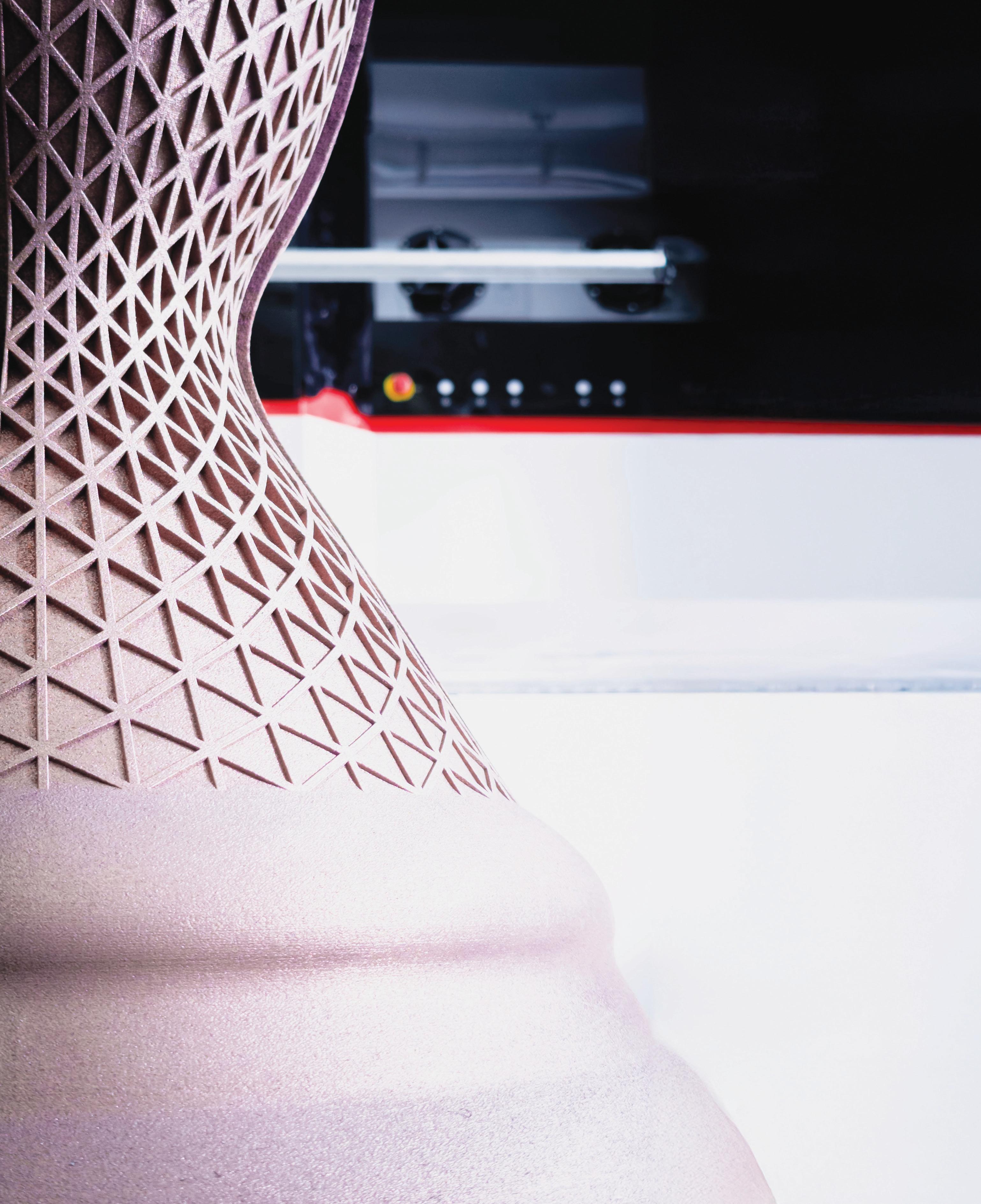

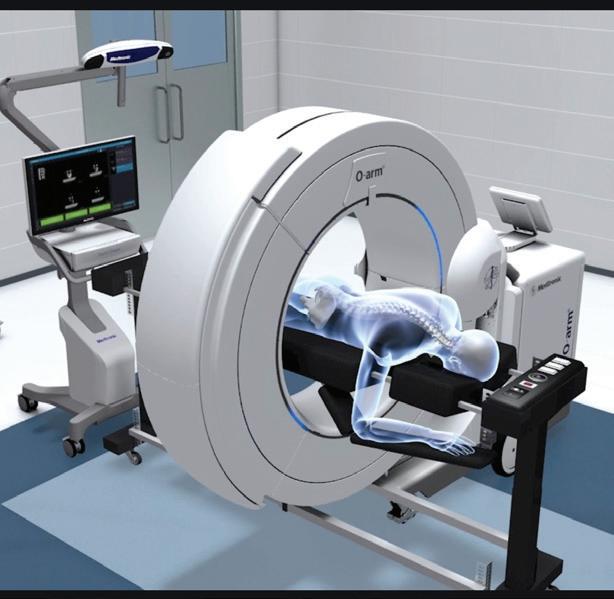
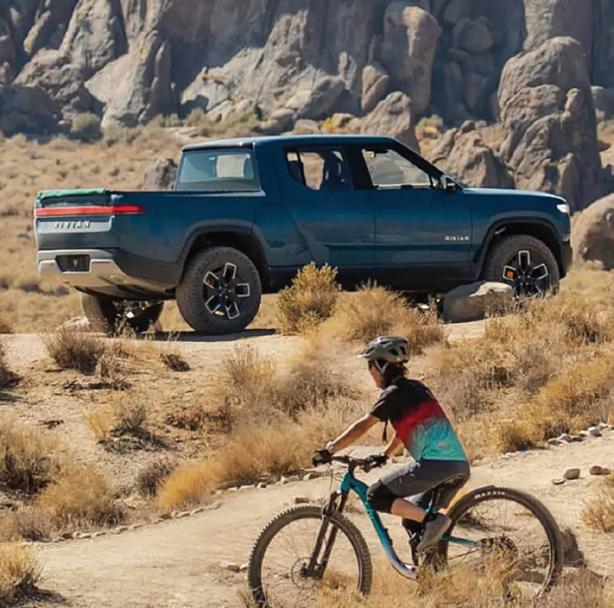
EDITORIAL
HEAD OF CONTENT
EDITORIAL
HEAD OF CONTENT
How can I sum up additive manufacturing in 2024? I’ve learned it’s not particularly wise to ask people, no matter how expert, to predict the future. Who can? I don’t like being asked to commit to plans a month in advance, let alone a year.
It was, largely, another 12 months defined by cuts and consolidation. The mostread stories on tctmagazine. com were those headlined by bankruptcy filings, noncompliance notices from the NYSE, acquisitions and job losses. Alas, it’s human nature to gravitate towards the negative but I like to think that on these pages, we do a good job of showing the positive too.
Reflecting on the list of predictions that we and our advisors made in our first issue of the year, it turns
Laura Griffiths e: laura.griffiths@rapidnews.com t: + 44 1244 952 389
GROUP CONTENT MANAGER
Samuel Davies e: samuel.davies@rapidnews.com t: + 44 1244 952 390
ADVERTISING
HEAD OF SALES TCT PORTFOLIO
Carol Cooper e: carol@rapidnews.com t: + 44 1244 952 386
PRODUCTION
Sam Hamlyn Matt Clarke
MANAGEMENT
C.E.O. / PUBLISHER
Duncan Wood
out there’s a lot we got right. An additive space boom? Well, SpaceX’s apparent use of AM for its Raptor 3 engine certainly grabbed a lot of attention. Rise of the entry-level printer? If we use CONTEXT’s figures, Creality, Bambu Lab, Anycubic and Elegoo would argue a resounding yes. The convergence of AI? We're talking about it in this very issue, so check.
There’s also plenty of other stuff, positive news, that we couldn’t have predicted. Like Manuevo rising out of the ashes of Shapeways’ bankruptcy to relaunch its AM service. Or GE Aerospace announcing a more than $150 million investment into facilities running AM equipment. Or BMW reporting it had 3D printed more than 400,000 parts worldwide in just a year.
SUBSCRIPTIONS
PUBLISHED PRICES
In a column earlier this year, TCT advisor Steve Cox wrote about playing the AM long game. If I reverse engineer his advice, take a longer view and reflect on AM in the ten years I’ve been reporting on it, the picture doesn’t seem so gloomy, or all that unique. We’ve had highs and lows, overnight successes and slow revolutions, the same as any other disruptive technology, but it has matured (though maybe not as quickly as we’d like) into a set of technologies that are undoubtedly having an impact.
The end of the year is a time for reflection, so I guess what I'm trying to say is, do so with perspective. There are plenty of reasons to be cheerful, and you’ll find many of them throughout this issue.
TCT North America Print Subscription - Qualifying Criteria US/Canada - FREE UK & Europe - $249 ROW - $249
TCT Europe Print Subscription - Qualifying Criteria UK & Europe - FREE US/Canada - £249 ROW - £249
Subscription enquiries to subscriptions@rapidnews.com
Read this and back issues for FREE on Issuuwww.issuu.com/tctmagazine
EDMMax 433W
X axis: 400mm 15.7"
Y axis: 320mm 12.6"
Z axis: 280mm 11.02"
Max. Workpiece Wt: 600kg 1320lbs Footprint: 2130 x 2000mm (84" x 79")
EDMMax 656W
X axis: 630mm 24.8"
Y axis: 500mm 19.7"
Z axis: 625mm 24.6"
Max. Workpiece Wt: 1000kg 1320lbs Footprint: 2130 x 2000mm (96" x 95")
EDMMax FC45HW
400 x 400mm build plate 500mm high Submerged Inverted Horizontal cutting
X axis: 400mm 15.7"
Y axis: 320mm 12.6"
Z axis: 410mm 16.14"
Max. Workpiece Wt: 600kg 1320lbs Footprint: 2130 x 2000mm (84" x 79") Uses pure water - no additives!
EDMMax 818W
X axis: 1000mm 39.4"
Y axis: 800mm 31.5"
Z axis: 800mm 31.5"
Max. Workpiece Wt: 2000kg 4400lbs Footprint: 2130 x 2000mm (104" x 89")
Max. Workpiece Size: 31" x 31" x 70"
X axis: 400mm 15.7"
Y axis: 320mm 12.6"
Z axis: 410mm 16.14"
Max. Workpiece Wt: 600kg 1320lbs
Footprint: 2130 x 2000mm (84" x 79")
EDMMax 1100HW (Single Axis)
X axis Clearance: 1100mm 43.3"
Y axis Stroke: 1400mm 55.1"
Z axis: 1250mm (49.2") can be increased
Max. Workpiece Wt: 3000kg 6600lbs Footprint: 3500 x 3100mm (138" x 122") ALL 4-AXIS MODELS EQUIPPED WITH
● CNC Control
● Molybdenum Wire .007" dia.
● Touch Screen
● Tapering
● Two (2) Paper Filters
● 3.5kVa Input 220/3/60
● 3-Pass Cutting Technology
● On-board CAD System
● No Chiller or Air Pressure Required
● AC & DC Cutting Power
● USB, LAN and MDI Inputes
● On-site training Included
● Prices starting at $64,500
04. THE NEXT BIG THING
AMCM provides a first look at a new machine launched at Formnext.
07. TRUE OR FALSE
Sam Davies takes a closer look at the reality of AM-enabled distributed manufacturing.
11. ALL EYES ON US
Materialise discusses its vision for ‘a movement of digital artisanship.’
12. HEAD ON
How AM enabled a sportswear equipment start-up to turn heads and minds.
15. RIDING TALL
Sam learns how Fizik is leaning on Carbon in its automated workflow for personalized bike saddles.
21. ADVANCING REFRACTORY ALLOY DEVELOPMENT
America Makes on hastening refractory alloy development to meet the demands of extreme AM applications.
19. BIG ON DATA
Interspectral CEO Isabelle Hachette discusses the growing importance of tools to visualize and analyze AM data.
22. JUST ONE THING
What is the single most important action that would help address the AM skills gap?
24. HOW AM IS HELPING TO SECURE NATIONAL INTERESTS
TCT Advisor Tali Rosman talks deploying AM to fortify supply chains.
In Starnberg, November 2024, Martin Bullemer, Managing Director at AMCM, made a commitment: “Our new M 8K system will be operational within a year. We have promised ArianeGroup the first printed combustion chambers once the machine is up and running.”
AMCM has used the time since then to further optimize the new M 8K system for the critical requirements of printing parts up to 820 x 820 x 1200 mm in challenging materials such as copper. In addition to superior laser technology, efficient cooling and optimum process gas airflow and filtration are of paramount importance.
The M 8K comes with eight 1kW lasers and is already prepared and ready for nLight AFX light sources, which AMCM uses in its M290 FLX system. The state-of-the-art scanner system is provided by the long-term partner SCANLAB. Their innovative RTC6 smart controllers provide excellent long-term stability, which is critical as part sizes and print times increase.
AMCM paid particular attention to the thermal management of the M 8K. The system will be used for high-end metal AM applications in the aerospace industry, where copper alloys are among the most used base materials. When printing copper alloys, part quality is highly dependent on the ability to keep the build platform, build chamber, and optical system consistently cool throughout the entire printing process.
For this reason, AMCM has implemented an innovative cooling system not only for the optical units, but also for the build frame, as well as a thermally decoupled optical bench. Collimator, scanner and optical bench interfaces are parallelly liquid cooled. Additionally, the cooled build platform provides ideal heat dissipation.
AMCM gives first impressions of its new large-format printer at Formnext 2024.
To avoid any loss of quality over long printing times, a uniform laminar protective gas flow which covers the powder surface must be maintained while fumes must be safely dissipated.
AMCM used metal AM extensively to manufacture the M 8K process gas system. The process gas nozzle went through several simulation and rapid prototyping cycles and is printed on AMCM’s M4K system. The same is true for the argon gas heat exchanger, which keeps the argon gas temperature below 25°C with minimal pressure drop. The heat exchanger has again been developed in collaboration with Conflux Technology, a partnership that has already yielded great results for the M 4K system. The very positive benefits of additively manufacturing this component are a dramatic reduction in its size of roughly 90% while increasing its cooling efficiency.
Any significant advance in process gas filtration technology for metal additive manufacturing will help safeguard human health and product quality while delivering value-added productivity improvements.
AMCM designed the new RFS NOVA filter unit based on proven filter technology but introduces significant advancements in powder consumption and hazardous waste management. The integrated particle separator makes a significant contribution to this. The unit recovers unused powder material from the gas stream so that it can be reused instead of being discarded.
Most importantly, AMCM introduces an innovative oxidation unit for the M 8K that eliminates the need for any external passivation medium.
With larger parts and longer print runs, process control and validation become increasingly important. All improvements in process monitoring and in-process quality assurance, will help to reduce subsequent testing effort.
AMCM has integrated 4 OT-cameras with more than 10 Gb/s data transfer rate to run SmartFusion and EOSTATE Exposure OT, which is a unique solution in the AM market that can monitor the process behavior not only during melting, but also after solidification. This enables the engineers to control the process in a closed-loop feedback manner with Smart Fusion.
The first application will be the printing of the combustion chamber of the Ariane Group’s Prometheus rocket engine. Printed in CuCr1Zr with a height of > 1,000 mm and a
“A new benchmark in terms of dimensions and quality.”
maximum diameter of 800 mm, this combustion chamber will be a benchmark in terms of dimensions and quality.
SINTAVA - ONE TO THE FIRST CUSTOMERS TO USE THE M 8K Sintavia, a Florida-based aerospace component OEM specializing in thermodynamic applications, is already an experienced operator of multiple M 4K systems and wants to build on this success with the much larger M 8K platform.
Brian Neff, Founder & CEO of Sintavia states: “We are proud to be the first in North America to utilize the larger build volume of the AMCM M 8K for our customers. Our experience with the M 4K over the past four years has been tremendously positive in terms of quality, productivity and service. We are very much looking forward to being able to take advantage of the much larger M 8K in our production.”
About AMCM GmbH
AMCM (Additive Manufacturing
Customized Machines) offers customized AM solutions based on proven EOS technology and processes that set the benchmark for metal 3D printing. The machines are built with varying degrees of customization, either designed almost from scratch or as modified and enhanced EOS systems. This involves process customization, including the use of new lasers, adapted heating concepts and different spot sizes, as well as modified build volumes. AMCM is an EOS Group company.
For more information visit amcm.com.
freeformer 750-3X
With the freeformers, fully functional components and small volume batches based on original plastic granules can be industrially additively manufactured using ARBURG Plastic Freeforming (APF), even from very soft materials (up to hardness 28 Shore A) or in hard/soft combinations. The industrial 3D printers are generally suitable for sophisticated applications in medical technology, the automotive industry and aerospace.
The high-temperature freeformer 750-3X features a build chamber which can be heated to 200°C and can plasticize high-temperature plastics at up to 450°C. This means that even the original granulate Ultem 9085, for example – which has been certified for use in aerospace applications – can be reliably processed and turned into resilient functional components. The machine has three discharge units and, from the outside, is indistinguishable from the freeformer 300-3X. Inside, however, the part carrier is around 2.5 times larger at roughly 750 cm2 and the build chamber has been enlarged significantly, measuring 330 mm x 230 mm x 230 mm.
The high-temperature freeformer 750-3X works at build chamber temperatures of up to 200°C.
In addition, data processing and the GESTICA controller, which is developed and manufactured by ARBURG in-house, have been optimized in terms of process stability, component quality and discharge speed. Improved software features and grid-shaped support structures mean that the build time can be reduced considerably. The result is significantly reduced costs per component and lower material usage. The intuitive GESTICA controller enables a clear, straightforward production process thanks to its “intelligent” assistance functions. At the push of a button, the startup sequence for material preparation runs completely automatically with no need for human intervention. The operator can see all of the relevant information regarding order status and the production sequence at a glance as required. Furthermore, the high-end machine can be used for industrial additive manufacturing of small series without any problems.
Further information: www.arburg.com
An hour into the second of three Executive Perspectives Keynote panel sessions at RAPID + TCT, there was a tap on my shoulder.
The CEO of an additive manufacturing (AM) software firm leant in, with a hushed voice, and remarked how refreshing it was to see someone staunchly express a controversial opinion.
Up on stage were five AM business leaders, providing their perspectives on a range of industry trends and talking points. Though it may be convention for the participants of such panels to be diplomatic, to be tactful and to skirt the edges, this one was different.
As DMG Mori General Manager Nils Niemeyer grappled with the realities of distributed additive manufacturing, covering the real-world challenges but emphasizing the theoretical upside, Materialise founder Fried Vancraen uttered the rarely heard phrase: “Allow me to disagree.”
“I think,” he went on to say, “that distributed manufacturing is one of the most false narratives of our industry.” Leveraging his near 40 years of
experience in the AM sector, Vancraen went on: “If you look at what has really worked in this industry, it is the bigger centers where a lot of competence is built up in a certain application, not shifting from medical implants to aerospace engines.” He was pulling no punches: “It is simply not working. It’s a different environment. It’s different post-processing. It’s a different mindset. I’ve seen every decade of this industry, entire companies betting on distributed manufacturing and going bankrupt, time after time.”
It hasn’t, though, deterred others from taking on the challenge of setting up distributed manufacturing networks in the hope of proving the exception to the rule.
There are many ways to stand up a distributed manufacturing model. A ‘flexible network’ approach, as referenced by a recent ACAM Aachen Centre for Additive Manufacturing and Boston Consulting Group report, consists of independent plants that can produce a similar product range, helping to balance capacity between sites. The ‘hub and spoke’ model sees core production steps concentrated at one or a few locations, with final production steps done closer to the point of consumption, while ‘local for local’ is essentially local production for local markets.
Each flavor of distributed manufacturing is made up of a dispersed network of facilities and promises reduced inventory, potential cost savings, resilience against supply chain disruption, and the flexibility to produce parts where it most makes sense. But more than that, according to 3YOURMIND VP, North America William
Cuervo, they give manufacturers the initiative to take control.
“Given how long lead times are and how delicate the supply chain is, the biggest advantage is not having to wait around for an update [from your suppliers],” he told TCT. “They can tap into industry-ready services and capabilities that are at their disposal, whether that be internally, through an academic institution, or through a contract manufacturer.”
When you add it all up, it is no wonder that so many companies over the years have championed the potential of distributed AM, and set up their businesses to adopt such approaches. Vancraen would suggest that most of these outfits have failed to achieve much success, but is that down to idea, execution or hype?
Dr-Ing Wilderich Heising, Partner & Associate Director at Boston Consulting Group, suggests the communication around distributed AM can’t be ignored, while Cuervo has thoughts on their implementation.
“AM is not a panacea to solve the world’s problems, and distributed manufacturing is not that miracle cure either,” Heising said.
“What we’ve seen with AM over the last ten years was a really big hype; we were exaggerating the possibilities and that might have happened with the decentralized narrative too.”
Cuervo added:
“Decentralized and distributed manufacturing could be a false pipe dream, but so can AM if you’re not doing it for the right reasons and you’re not in touch with the how and the why
you’re looking at this in the first place.”
This is the first big hurdle for manufacturers trying to implement distributed additive manufacturing networks and there are more down the track. A decentralized approach won’t get off the ground without deep thought into why and how, but even once that’s figured out, there is still the investment in capital equipment, identification of partners and suppliers, and, if you’re working in certain industries, regulatory constraints and knowledge transfer. A supply chain that revolves around one fixed production site is complex, let alone one that serves multiple facilities in multiple regions.
There are opportunities though. Markforged CEO Shai Terem wasn’t shy in making that point at RAPID + TCT (see our featured case study for more) and Replique can point to several examples. One of which is a collaboration with MAN Truck & Bus, where Replique produced several spare parts for a marine diesel engine. The original manufacturer was no longer available, but Replique was able to quickly identify a suitable production partner to fulfil the order with minimized downtime. Alstom, Miele and RehaMedPower are others that Replique has supported with a decentralized approach, noting how many customers demand the production of parts close to the point of need.
When Vancraen made his comment about companies failing to make a success of distributed AM approaches that catered for a variety of industries, companies like Replique were brought to mind. Decentralization and distribution are core to Replique’s approach, while its tagline – trusted parts for everyone, everywhere –suggests there is no industry the company won’t serve.
At a high level, they seem the kind of company at risk of suffering the same pitfalls as those Vancraen has seen rise and fall over the last four decades. But when you dig into how its process works, it reveals a company that has likely learnt from the mistakes of others. Replique has assembled a range of specialist manufacturers in various industries (250 across six continents), rather than
manufacturing sites that ‘have a lot of competence in everything,’ with its framework identifying the best partner for whatever job has presented itself. The company’s software platform also documents the digital twin and history of every part to ensure quality assurance and process stability.
“We don’t view distributed manufacturing as a simplistic approach,” Replique CEO Max Siebert said. “For us, it’s about having decentralized capacities while centralizing expertise. When done right, this approach enables companies to scale efficiently without sacrificing quality.”
This kind of set up might be where Vancraen would be willing to bend on his assessment of distributed AM. As counter points were made, he conceded there would be grey areas where companies were achieving success. And it’s a good thing too. Although Covid-19 was probably the biggest supply chain disruption of the last century, they
haven’t exactly slowed down since 2020. Blockages in the Suez Canal, Typhoons in Shanghai and ongoing international conflicts have only underscored the importance of supply chain flexibility.
Just as well then that there are promising signs from the likes of Replique.
“As product variety continues to grow and the demand for parts increases, the importance of decentralized and on-demand manufacturing will rise to maintain flexibility for diverse production needs,” Siebert finished. “While AM won’t be the only manufacturing method, it is undoubtedly becoming a go-to approach for parts where its benefits are most evident.”
For three years now, wind turbine manufacturer Vestas has been working with Markforged and Würth to build out a distributed additive manufacturing network. The company’s distributed manufacturing infrastructure includes a digital inventory of more than 5,000 Vestas parts and a fleet of Markforged machines operating across several manufacturing sites.
Previously, Vestas was relying on external suppliers to manufacture essential parts like top center marking tools and lightning tip receptors, enduring the weeks-long lead times and risking the potential for components to fail final inspection. Now, Vestas has brought the production of these parts in-house, allowing any individual with the right permissions to scan a part code or search the ERP system and send print files to the most suitable Markforged machine. Control is centralized, but manufacturing is decentralized.
“Distributed manufacturing is already starting to happen,” Markforged CEO Shai Terem said at RAPID + TCT. “Point
of need production, when you can, is great, and when you cannot, you have a centralized location. Vestas has 8,000 tools required to [manufacture] these big wind turbines, and 5,000 of them are on a digital library now, printed at the point of need. Printers are being controlled from some central place, they control the library, control the process of how to certify, how to upload them to the digital library, and then they’re printed where needed by the most efficient way to do it.”
The TruPrint 3000 is our versatile medium-format machine. Benefit from increased productivity thanks to the cooled build plate, the De-focus function, and full 700watt laser power – perfect for processing specialty alloys and reducing your part costs The new powder handling station, designed for easy sieving and conveying of metal powder within just 1 m², ensures consistently high powder quality
www.trumpf.com/s/TruPrint-3000
WORDS: LAURA GRIFFITHS
SHOWN: Impressio eyewear
When Materialise unveiled its latest eyewear collaboration with Impressio in Paris, the frames, distinguished by their bold water-inspired silhouette, and opaque, acetate-like finish, were poised to represent not only the possibilities of modern manufacture, but the epitome of what the Belgian additive manufacturing (AM) company describes as ‘a movement of digital artisanship.’
The eyewear sector has embraced AM over the last decade. Modelled by companies like Hoet and Yuniku, which have brought novel customization experiences to consumers at retail, and luxury brands like Porsche and McLaren who have leveraged the technology for celebratory collections, Materialise has produced several hundred thousand frames for around 80 different brands. Championing the potential for mass personalization, eyewear products have been largely enabled by laser sintering, augmented by new materials developments across metals and polymers, including those designed to reduce its carbon footprint. But over the last five years, the team has been exploring different processes and materials to deliver eyewear that more closely resembles the look and feel of traditional frames, with all the benefits
that a digital supply chain and design for AM can afford.
“It’s about learning about each other’s realities,” Alireza Parandian, Head of Global Business Strategy, Wearables at Materialise explained of Materialise’s latest ‘co-creation’ with Luxembourgbased Impressio. “Impressio came with multiple design ideas to help us not only bring about a product that looks beautiful and extends the idea of something wearable to something that is sculptural, but also, in the process, kind of cover up for imperfections or thicknesses that are required in order to make sure you have mechanical stability. In these co-creations, you have to put all of those things on the table. It requires a lot of experience on our side and courage on the side of our partner.”
“This innovation is based on a novel material that transitions from an opaque to a translucent finish, revealing all the curves and volumes in the light, with shades of ocean blue, bottle green, or ruby red,” Guillaume Boisson, co-founder of the Impressio Collection told TCT. “This perfect marriage of cutting-edge technology and creative freedom promises to redefine design standards in the world of eyewear.”
‘Be like water’ was the concept. The volumetric design mimics the movement of water falling and bursting onto a surface, brought to life with transparency
and three vibrant colorways. To get there, the team began working with DLP, benchmarking almost 50 different materials against mechanical stability, thermal stability, and crucially, medical regulations.
“That’s exactly where deep knowledge in 3D printing comes in – engineering knowledge, being solution-minded, trying out different things and not accepting a ‘no’, which is a culture here at Materialise,” Parandian explained. “This was truly a sculptural piece. We needed to take that and look at how engineering could support this. It wasn’t easy.”
With unique design freedoms come unique challenges. While AM allowed the team to create a lightweight, seamless product, married with the more traditional aspects of eyewearmaking, the use of resin-based technology meant considerations around support removal and postprocessing had to be made to achieve a glossy, retail-standard finish.
“Software is the unsung hero of 3D printing,” Parandian said. “If you really are looking for the moon shots, you have to think about freedom of design to its highest degree, where personalization and customization is bringing so much added value that it can have transformational effect.”
With the frames as its showpiece at this year’s Parisian optical event SILMO, Materialise is signaling to the industry, where it has spent the last ten years optimizing and investing, it is open for collaboration.
“We want to be the innovator you can count on,” Parandian said. “It’s really important to give room and freedom to our partners to come up with ideas, and what we’re trying to do and assess every time, together with our partners, is where is the market fit? Is it feasible in terms of economic aspects? Is it viable in terms of all their requirements? Our vision with this was, we wanted to come and show what differentiating possibilities 3D printing can offer to the industry. And that was not just [about] translucency but to go beyond what acetate makes possible –to go beyond what is possible.”
In any good story, nothing worth fighting for is ever easy. For BATS-TOI, Inc., a New York-based developer of contact sports equipment, it could have been the supply chain challenges that assailed even the most robust manufacturers during the pandemic that forced it to hang up its headgear and quit. It could have been when the National Federation of High Schools (NFHS) came knocking and demanded it stop selling its product, which had already been embraced by hundreds of student athletes across the United States. But for Mario Mercado, founder and CEO of BATSTOI, which takes its name from the French to “fight to overcome any obstacle,” a new form of headgear that would better protect the health and careers of athletes, was absolutely worth the battle.
It started as a graduate school project, first at NYU and then at Columbia University. Mercado had been a wrestling coach at NYU and also Deputy Commissioner for the New York State Athletic Commission, assisting in the regulation of professional boxing and mixed martial arts. That experience led to the realization that, while high-profile sports like football and hockey are synonymous with protective headgear, wrestling, a sport which requires consistent, intense grappling between opponents, endures greater risk to concussions and head injuries than any other. It gave Mercado the motivation to design a new form of headgear that focused not only on ear protection, as industrystandard wrestling headwear traditionally has, but also reduced the risk of concussion.
Armed with this idea, he started knocking on the doors of NYU’s Mechanical and Aerospace Engineering Department where Dr. Nikhil Gupta introduced him to the lab’s additive manufacturing capabilities. A first prototype, made using FDM, planted the seed around 3D printing’s potential, but this wouldn’t be an overnight AM success story. Instead, the start-up went ahead with the traditional route of injection molding, manufacturing its first headgear in Italy and in Asia. It wasn’t cheap, and against the backdrop of the pandemic, where global
travel restrictions made in-person quality control impossible, Mercado realized, it simply wasn’t going to work.
“The cost of that as a startup was just crazy,” Mercado told TCT. “That really sparked my interest of going back and revisiting additive manufacturing.”
Mercado spent a year working with different service providers until Dr. Gupta directed him to a place on Manhattan’s Fifth Avenue where he could take a look at HP’s Multi Jet Fusion. There, he met another hurdle – there was no 3D printer to be found. Deflated, he sat in the waiting room, scrolling through LinkedIn and hastily connecting with anyone related to HP’s 3D printing division. The following day, a flurry of messages appeared in his inbox, and Mercado quickly began working with Akash Valavala from HP’s Professional Services team. In just seven weeks, the headgear was converted into an AM-optimised design and printed using MJF.
“I believe that first MJF helmet was the point when we realised this could really work on MJF,” says Brian Ingold, Head of GTM Solutions at HP. “There have been many iterations and design enhancements throughout the years but getting that first helmet to work was a pretty big “aha” moment for the team.”
Mercado was finally getting somewhere. AM, suddenly, appeared to be a viable production method.
“Could it be done with injection molding?” Mercado reflects. “Yes, but not economically.”
Still, the AM economics didn’t come immediately – initially, Mercado recalls being quoted $800 to print a single helmet. With ambitions to scale to 1020,000 units as a minimum, this pushed him to figure out a way to use AM to his advantage and simultaneously get costs down. Today, a single helmet, known as the Mercado III, retails for less than $100.
“We’ve lowered the part costs through this journey as we’ve designed for nesting while keeping function,” Ingold continued. “I think the key to production is finding that right part cost. It’s been really impressive to see the iterations of the helmets as a new idea comes out, but also how quickly we can turn that around into a product that can get into the market. It’s something you would never be able to do with the traditional methods of manufacturing.”
In wrestling, there is no ‘one size fits all’ and to withstand grabs and takedowns, headgear must fit like a glove. The Mercado is geared to provide coverage to the athlete’s head and ears and is fitted with an adjustable chin strap. In one early pre-AM iteration, made in Italy, BATS-TOI planned to integrate the strap, but wildy
WORDS: LAURA GRIFFITHS
“We can be responsive to that person in real time.”
up, left Mercado manually fixing hundreds with duct tape and wire cutters. For a new company, the costs of starting over with injection molding were prohibitive, but AM allowed Mercado to iterate quickly.
“[HP’s] design team has a ton of experience in working with commercial products that have been scaled in the millions of units,” Mercado said. “The great thing about engineers is what really excites them and pushes them is how to solve a problem that people think is almost impossible to solve.”
Mercado worked with HP’s design team to determine the structure of the headgear – which parts needed to be stiffer, more flexible, how thick or thin it should be? – and develop a product that could effectively scale for serial manufacture with minimal human interaction and assembly. BATS-TOI took scans from several athletes to get the right form factor and determine five that would fit the greatest range of shapes and sizes. The designs were developed using the HP Lattice Design Engine and printed in TPU via HP’s Digital Manufacturing Network.
“With additive, we’re able to have four styles without having to invest that large amount of money that would normally be required for injection molding,” Mercado explained. “We went through that process by modifying the CAD. If there was a problem at a wrestling competition on a Saturday, someone would tell us about it either on a Sunday or Monday, we would
address it that week, look at the CAD, and then print a new one the following week. We’ve had a customer receive multiple iterations of our headgear within a month.
“We are standing behind our pact to give their daughter or son something that actually works. But then also it shows that the beauty of additive in this application is that we can be responsive to that person in real time without having to start from scratch, and then continue to move forward and make that progress.”
While the final products are said to be lighter than the mass of foam and deliver greater energy absorption, it’s not just about performance and durability on the mat. Throughout the headgear’s many iterations, BATS-TOI has worked with athletes to learn where it needed to adjust, understand their psychology, their needs. When athletes fed back that it was too hot to have headgear pressing hair against their necks, for example, they adapted, creating a ponytail hole, first for comfort, but also to allow wrestlers to show their personal style.
“Designing a product, particularly in sports, you have to understand what is the anticipated behavior of, in this case, the wrestler,” Mercado said. “They’re not just going to put it on and take it off. There’s an emotion behind it when they’re winning or they’re losing.”
Like any start-up, Mercado had taken many risks. The biggest, perhaps was going straight onto the market and selling, bypassing the old guard of the National Collegiate Athletics Association (NCAA). This was an entirely new product and Mercado knew it would require a change in mindset. Within three months, BATS-TOI had sold around 1,500 units before a cease and desist arrived from the NFHS, the body that writes the rules for high school sports in the United States, instructing the company stop selling and leaving BATS-TOI almost bankrupt. It was a fight Mercado
was prepared to take on, and the company went head-to-head with the NCAA to get the product accepted. In a fortuitus case of timing, shortly after, new rules from the state associations started to come into play, stating that if an athlete were to get three concussions within a season, they would be out. Now, both the athletes and the associations that looked after the sport understood that this product was a necessity, and pretty soon, BATS-TOI was getting letters from athletes praising the Mercado for saving their season. Now, BATS-TOI is recognised as an Official Wrestling Headgear Partner of the NFHS.
“It was never a problem about product market fit. It was really about the timing,” Mercado said. “We started to see more of a grassroots adoption of the headgear and we realized that we had struck a nerve. And that’s what allowed us to improve on the headgear, even to the same athlete with multiple iterations, because they knew the value of our product towards their athletic career and their athletic goals.”
We’ve worked with Naval Sea Systems (NAVSEA) to achieve compliance for one of Maritime's most common materials.
• Produce metal parts that are antimicrobial and antifouling.
• Excellent wear and corrosion resistance properties.
• Galvanically compatible with steel and iron.
Manufacture and post-process Nickel Aluminum Bronze (NAB) parts in less than 24 hours with our Expeditionary Manufacturing Unit (EMU) capability. EMU combines our patented XSPEE3D cold spray metal 3D printing technology, and post-processing SPEE3Dcell unit, enabling you to make reliable, dense metal parts faster than ever thought possible.
Sam Davies explores the automated AM workflow behind Fizik’s personalized One to One bike saddles.
SHOWN: Fizik One to One saddles feature 3D printed padding
In 2019, the coverage of a 3D printingenabled bike saddle had a reporter pondering.
Carbon and Fizik had just unveiled the latest success story to come out of Carbon’s Lattice Engine: The Adaptive bike saddle with 3D printed padding, where the energy return properties of Carbon’s EPU 41 material and zonal cushioning characteristics of a lattice structure combined to provide greater comfort to cyclists.
It barely had a chance to prove out its promise when attention was turning to the future.
“Eventually,” a CyclingNews article read, “an in-store system could collect consumers’ pressure-mapping. This data can then be fed back to the 3D printers at the Fizik factory before a completed unit is shipped direct-to-consumer.”
When 3D printing applications hit the press, the imagination tends to stretch its legs, picturing all kinds of digitally automated workflows, processes and practices for the development and production of, for example, personalized goods. What CyclingNews projected back in 2019 has long been one of additive manufacturing’s
“3D printed saddles are the saddles that we sell the most.”
biggest promises. Most of us have been around these parts long enough to know that they aren’t always fulfilled. But this one was.
Five years on from the launch of the Adaptive bike saddle, Fizik has introduced the One to One saddle – a customized seat engineered to suit the rider’s shape and style. This latest product iteration still leans on Carbon’s 3D printing offering – Fizik operates a Carbon L1 printer – but has added gebioMized, a leader in pressure map data, to the equation too.
The process now sees a pressure sensor mat capture 64 data points pertaining to the rider’s shape, positioning and riding style, with the information being transferred to Carbon through an API in less than an hour. The Carbon Custom Production Software –inclusive of Carbon’s Design Engine – then
kicks into gear, gathering the input data and generating a 3D printable file that is sent directly to the print queue of the Carbon L1 machine sitting in Fizik’s factory. Each step of this process – down to the serial number and part tracking – occurs sequentially without the need for operator input.
What arrives with the consumer is a saddle unique to them.
“All of these One to One Fizik saddles have the same volume,” Andrew Sink, an Application Engineer at Carbon, tells TCT. “What we’re doing is we’re modulating the density in different areas, specifically for riders based on that pressure map feedback. There is a very high level of customization in each saddle based on where you want that zonal density.”
The lattice structure used for Fizik saddles is also unique to this particular project, with the design based on the characteristics of the EPU 41 material.
Carbon’s Design Engine software uses this structure as a baseline, with the pressure map dictating where modulations are made to ensure the latticed saddle padding offers different responses in different zones.
This is important since a soft saddle using the same foam from the nose to the back is counter intuitive. What will likely happen is the rider’s ischial tuberosities (sit bones) will sink through the soft padding, hit the shell and pinch, causing discomfort.
“There are body parts touching the saddle that need different kind of support,” explains Alex Locatelli, Product Manager at Fizik. “If you are sitting on the ischial bones, then the bones can support more pressure without even noticing. But if you rotate your pelvis on the saddle, and then your soft tissues are squeezing on the saddle, then you can feel pain, numbness,
SHOWN:
Pressure mapping data informs the lattice structure
The process developed in partnership with Carbon and gebioMized is working to address these issues. Using gebioMized’s sensor mapping technology has allowed Fizik to measure how cyclists generate pressure on the saddle, where that pressure is being generated and how intense the pressure is. That then informs the exact shape and density of the lattice structure that will be incorporated into the saddle’s padding.
“On the ischial bones, the padding is much firmer; you need more stability,” Locatelli says. “But while rotating on the saddle, the padding has become much softer, so you don’t have numbness. The general comfort of the saddle is much better. With this technology, we can be so precise. You can find the right spot where there’s a little bit of unnecessary pressure and then we can compensate for that with the technology.”
Not only can Fizik be precise, but it can also be flexible, quicker and, in theory, hit bigger scales. As far as Fizik can tell, it is the only saddle manufacturer that has access to an in-house 3D printer capable of printing multiple products in a single build, with post-processing carried out overnight and custom products turned around in a couple of weeks.
The success is owed to the upfront work carried out by the automated workflow, which serves to reduce design iterations, validate lattice shapes, and go from printing multiple parts per rider to deliver a repeatable process per saddle.
As Sink explains: “The way this process works is once we have the saddle geometry, and this is the lattice structure that performs a specific way according to some baseline, we have a lattice that we understand and characterize. When we go through the scaffolding and apply the transformations for the custom lattice, the printability of the file doesn’t change. There’s no second iteration required, there’s no print testing, or anything like that. The lattice has been validated, so your custom saddle and my custom
saddle, if you look at them, you’d be able to see that they’re different, but when you look very carefully at the lattice structure, you won’t see any defects or broken struts because we’ve already validated the lattice itself.”
What we’re left with is a lighthouse application for Carbon and a dream come true for Fizik. Since work started on 3D printing saddles, the end goal has been to deliver customized products at a price point that won’t deter consumers.
In 2019, one of Locatelli’s first tasks as a member of the Fizik team was to explore the feasibility of 3D printing for bike saddles, procure material and lattice samples from Carbon, and spend a couple of weeks in California to immerse himself in the technology. Five years on, the experts in making saddles and the experts in making lattices have pooled their know-how to turn 3D printing’s promise into a reality.
The Fizik One to One saddle is available for consumers to buy from 25 dealers around the world. And they’re doing so. And they’re coming back for a second. And a third. It is good going for a company just five years into its additive manufacturing journey.
“Back then, it was a bet because the technology was expensive and even if the saddle costs between 300-400 Euros, our margin is basically not as good as the margin we make on standard saddles,” Locatelli says. “But we wanted to test the market and see if the riders would react to this new technology. And we were surprised because the feedback from the market was very, very positive. Some customers order the custom saddle and after a couple of weeks they want another one for another bicycle. Nowadays, 3D printed saddles are the saddles that we sell the most because of the comfort that the technology can provide.”
April 8-10, 2025 | Huntington Place | Detroit, MI
Four world-class manufacturing events, together in one location
SME is bringing together these four events, providing access to more than 600 manufacturers while showcasing advanced manufacturing, smart technologies and mobility advancements. Combined Audiences, Magnified Impact!
At RAPID + TCT 2025, you’re under the same roof with SME’s AeroDef Manufacturing; SAE’s trademark mobility event, the World Congress Experience (WCX); and America Makes’ project success showcase, Technical Review & Exchange (TRX).
Claim your complimentary Expo Pass!
Use promo code TCT when registering
WORDS: LAURA GRIFFITHS
Additive manufacturing is an inherently digital process, and if you ask Isabelle Hachette, CEO at Interspectral, a Swedish technology company specializing in 3D visualization
and data fusion, ‘there is no lack of data’ from AM – just a lack of tools to fully utilize it.
Here, Hachette discusses why now, more than ever, quality assurance technologies are playing a crucial role as AM continues its path to production.
TCT: Tell us about Interspectral, where did it all start?
IH: We are actually entering from a neighboring industry, scientific visualization. We entered the additive manufacturing industry because we saw that there was a high demand for our technology, specifically to enable serial production, and [through a] research project and industrial cooperation that we had in Sweden, we discovered that there was a lot of data that was measured and acquired in the production process. We also discovered that there was no standardized way of handling the data in an efficient way, and many times the data could consist of several terabytes and that made it difficult to use the technology in a larger scale. So we think that we can take a lead in developing the market to efficiently read and visualize and draw conclusions [from] this big data.
TCT: What is Interspectral bringing to the market that’s different to current quality assurance and process monitoring solutions on the market today?
IH: We provide a unique value to quality assurance and process monitoring because we have developed our proprietary algorithms, and they were developed even before we entered into this market. These proprietary algorithms can read, visualize and analyze big and complex data in a very efficient way.
We can read data from any machine. We can actually handle any data format independent of the type or the dimension, and when acquiring the data during the build process, there are several different data formats,
point clouds, volumes, 2D measurements. We can gather all this different data into one single digital twin. That makes it easy for the end user to have a holistic view of all the data that has been gathered during the build process, from the design file to the data that is gathered during the printing process and also, during the post-inspection, for example, with CT scans and so on.
TCT: We hear a lot about ‘AI-driven’ technologies. How is AI being leveraged here?
IH: The proprietary technology of Interspectral from the beginning was very much about handling large data, visualizing large data in an efficient way. Now we are complementing that technology with AIdriven technologies. The AI component that we are developing is actually for optimizing
the error detection in the build job, for example, so that we can automate, and make it easier for the end user to use the additive manufacturing in production. We are optimizing the way to get the right answers in the right time.
TCT: What unique challenges does AM present for manufacturers in terms of quality assurance?
IH: Specifically for the parts that are produced with AM, they are [often]times more complex and they have more complex interiors. Then it’s also more challenging for traditional QA methods. So there needs to be development of more sophisticated QA processes, required for this type of quality assurance. At the same time, additive manufacturing, and specifically LPBF and EBF, are fully digital processes and the process parameters are monitored during the full production process. A lot of data is created, up to several terabytes per build job, and I think that the challenge in terms of quality assurance in this industry is very much about how to, in an efficient way, handle this large amount of data that is being measured during the process, and then also to understand and be able to draw the conclusions from that data.
TCT: Are users doing enough with their data?
IH: As we say and experience every day at Interspectral, there is no lack of data. There is a lack of good tools to visualize, understand, and gain insights from the data that has been generated during the full process - pre-process, during the process and after the process. We believe that there is still a lot to discover within the data that has been measured, and we are providing the tools for this discovery and the big data handling, the standardization, and producing efficient workflows.
Editor’s note: This interview has been edited for brevity and clarity.
Hastening refractory alloy development for additive manufacturing (AM) to meet the demands of extreme applications is critical for AM advancement. This development would significantly increase the application’s operating temperature, leading to improved energy efficiency, enhanced performance in power generation systems, and reduced costs. However, expediting research and development efforts within current approaches carries risks, expenses, and time-to-market barriers.
Nonetheless, the promise of accelerating new material development remains significant enough to draw on the broader industry for innovative solutions with America Makes and Ames National Laboratory, a U.S. Department of Energy (DOE) national laboratory and renowned leader in material development, leading the efforts.
Drawing on evidence from its 2021 America Makes AM Alloy Development Workshop, material systems were identified across aviation, space, medical, energy, oil and gas, nuclear, and defense applications.
“The quest to develop metal alloys suited for AM continues to unfold.”
WORDS: Eartha Hopkins, America Makes
Leveraging this knowledge in tandem with academic research is poised to create a step change in feedstock manufacturing technology and feedstock cost alongside AM product performance and price.
Historically, traditional manufacturing materials have been developed based on accessibility and compatibility with a particular manufacturing process. However, this is not the case for AM. Instead, materials used in AM fusionbased processes like laser powder bed fusion (LPBF) have heavily relied on their compatibility across welding processes. To address these technological gaps, additive research primarily sought incremental improvements to alloy development to validate and examine material properties.
Along these same lines, material processability emerged as another roadblock. Considering a material’s surface condition and chemical composition can significantly impact its performance, material development and qualification may require an indepth analysis of mechanical properties, including oxidation, wear, fatigue crack growth, and creep/stress rupture, emphasizing statistical analysis.
Today, the quest to develop metal alloys ideally suited for AM continues to unfold, but now with an even greater focus on high-temperature applications. Therefore, the acceleration of refractory alloy development for AM has become an even more critical research endeavor.
“Refractory alloys are becoming increasingly important due to their exceptional ability to resist heat and wear,” said Dr. Ryan Ott, Deputy Director of Material Science and Engineering at Ames.
One of the key opportunity areas to achieve this, according to Ott, is through gas atomization for metal additive powdered alloys. This method creates metal powders specifically for 3D printing, by breaking molten metal into tiny droplets that solidify into spherical particles. It has proven to enhance performance,
reliability, and versatility while reducing costs and enabling new material and design exploration. However, challenges persist. “Due to their reactivity and quick solidification, creating powders with extremely high melting temperatures is not easy. Gas atomization is a standard method, but generating small particles suitable for many AM technologies remains challenging,” Ott asserted.
Beyond these technological challenges, the U.S.’ current supply chain vulnerabilities in raw material acquisition, combined with limited domestic technological capacity, are also concerning. Restrictions in feedstock availability and high unit costs for specific materials can significantly hinder development timelines and budgets.
Further investment to fast-track refractory alloy development offers a compelling opportunity to elevate the U.S. industrial base and enhance competitiveness across critical applications. This dynamic partnership holds the potential to significantly expedite alloy development timelines, paving the way for more successful outcomes. Furthermore, America Makes has identified a pressing need for comprehensive training to harness AM’s potential fully. The focus is not only on pioneering new alloys but also on refining the effectiveness of existing ones and establishing a more robust processing ecosystem for future alloys.
“We envision these efforts will yield not only successful demonstrations of improved material performance, but also deliver statistically-based material datasets, process specifications, postprocessing specifications, material specifications, techno-economic analysis, pilot scale manufacturing demonstrations, and education and workforce development opportunities,” said Brandon Ribic, Ph.D., Technology Director at America Makes.
If the findings from the first two TCT UK User Group meetings are any sort of indicator, no matter where a conversation about additive manufacturing (AM) challenges may begin, it typically always leads to a discussion about skills.
From classrooms to apprenticeships and industrial strategies, there are many ways to tackle the gap in AM skills. We asked those across industry, academia and research: What is the single most important action that would help address the AM skills gap? Here’s what they had to say.
COURTNEY
PUHL |
EWD Senior Project Engineer | America Makes
“Addressing the skills gap is critical to growing the additive manufacturing industry. At America Makes, the National Additive Manufacturing Innovation Institute, we collaborate with our members from industry, academia, and government to create comprehensive education
and training programs that align closely with industry needs. Institute-developed awareness and inspiration programs are designed to widen the funnel, expose learners to career opportunities, and encourage individuals to enter programming that will bring them into the industry. Through career exploration tools and microlearning modules, the AM industry is made accessible to all learners regardless of age or circumstance. Learners inspired to pursue the next step of a career in AM can continue to more in-depth institute programs. By offering hands-on experience with cutting-edge tools, certifications, and clear career pathways, these programs can equip the workforce with the specialized skills required for the rapidly evolving field of additive manufacturing.”
DR CANDICE MAJEWSKI
| Senior Lecturer | School of Mechanical, Aerospace and Civil Engineering | The University of Sheffield
“I think there’s a danger that, when we talk about skills, we focus quite narrowly on the technical aspects of additive manufacturing. And while technical capabilities are without a doubt hugely important, we mustn’t let them obscure the need for a broader range of skills. For our industry to advance to meet its full potential we need ongoing innovation; for that we need new
MELISSA ORME | Vice President of Boeing Additive Manufacturing
“There is a recognized gap in the skilled workforce for additive manufacturing that is due in part to erroneous perceptions that AM, and all manufacturing for that matter, lacks career advancement and is not interesting or meaningful. Hence to address the AM skills gap, we need to change the perception that it is not interesting. The truth that needs to be conveyed is that AM is a high-tech capability that is based on digital integration. It uses modeling, simulation, big data analytics, machine learning, and AI. Engineers implementing AM are free to unleash their creativity and imaginations in ways that were never before possible in manufacturing. It is a capability that combines material science, structural mechanics, dynamics and data analytics.
Hence, the first step is to interest the workforce in AM roles by promoting the allure of innovation and cuttingedge technologies that comprise the AM workstream. Once the motivated and energetic workforce begin to fill the workforce gaps, the second step is to train and upskill them at the same pace as the rapidly changing technology.”
ideas, new perspectives and perhaps completely new mindsets. So the biggest question becomes, how do we attract a broader range of people? For me that means we need to be getting out there and speaking to the people we don’t normally reach. This might be as simple as spreading the word via events, magazines, and podcasts in new areas, but could also include AM-focused events targeting new audiences. If we can reach new people with accessible, easy to digest, information, we can hopefully get the influx of new people that will help transform the industry.”
LINUS TILLMANN | Education
“AM education is already addressed quite well at the university level, and we are seeing better AM-educated engineers graduating and entering the market. However, a skill gap persists throughout the industry, preventing AM from breaking through as a universally adopted production technology with its own design and production rules. Standardized training programs would provide
PROFESSOR KATE
BLACK | CEO & Founder at Atomik AM
“We need to implement targeted education and training programs that integrate AM into the broader manufacturing landscape. For too long, we
a common language, framework, and skill set, making it easier to acquire the necessary skills and for employers to identify qualified personnel. Numerous training systems already exist, offered by various market players and institutes, some of which provide certifications for specific roles within the AM supply chain. Implementing standardized training programs at a higher level would improve transparency and comparability across training offerings, certifications, and the qualifications of trained personnel.”
have viewed AM as either a replacement for, or an alternative to, traditional methods, when it should be seen as a complementary tool, one that works synergistically with existing manufacturing. The goal should not be to replace traditional manufacturing but to enhance and augment it through AM, creating a more versatile and adaptive manufacturing ecosystem. This means training programs must emphasize how AM can coexist with and enhance established techniques,
equipping workers with the knowledge to leverage both sets of skills effectively. For this, fostering better communication and collaboration between academia and industry is required. Industry needs to provide guidance on the specific skills required, while educational institutions must adapt their curriculum accordingly. This way we can ensure the future workforce is equipped with the right mix of competencies to thrive in a manufacturing environment.”
WAI YEE YEONG
| Professor and Chair of School of Mechanical & Aerospace Engineering at NTU Singapore
“AM involves engineering principles in a holistic manner, covering different aspects including designprocess-material and product development. The key is the ability to identify unique advantages of using AM to achieve better final performance of the intended application. It is important to develop hands-on workshops or laboratory-based design and fabrication modules that allow learners to experience the entire process flow of AM from design to print. As a result, learners will be able to map the key values of using AM technology for the specific industry or application.”
WORDS: TALI ROSMAN
Recent global disruptions and conflicts, from Covid-19 to the situation in the Ukraine, have underscored the critical importance of robust manufacturing capabilities and resilient supply chains. The ability to rapidly produce essential equipment (military and civilian), especially in times of conflict, can be the decisive factor in determining the outcome of a war. Specifically, these events exposed a concerning weakness in the United States: a significant decline in manufacturing capacity coupled with an alarming dependence on foreign suppliers, including China, for critical civilian and defense components alike. Amidst these challenges, additive manufacturing, once confined to prototyping and niche applications, has emerged as a powerful force, enabling the rapid production of complex components and enhancing supply chain flexibility. AM has been put to the test in the last year and has been growing in importance when it comes to re-building the USA manufacturing base and fortifying the supply chain.
The US has recognized the strategic significance of AM and is investing heavily in its potential to revolutionize defence production. AM’s agility and speed offer a distinct advantage in a world where conflicts are increasingly characterized by rapid technological advancements and evolving battlefield dynamics.
• Drones: AM is playing a pivotal role in revolutionizing drone technology, which is increasingly crucial in modern warfare. Companies like Firestorm are leveraging AM to produce entire drone airframes, consisting of 44 printed parts, showcasing the speed and flexibility that AM brings to drone manufacturing. The US Air Force is also actively supporting startups like RapidFlight, which was awarded a contract to develop advanced, 3D printed drones with a focus on autonomous capabilities.
• High-Performance Aerospace Components: Honeywell is reducing production time and costs by using AM to print ceramic molds to fabricate turbine blades for their jet engines. Similarly,
Pratt & Whitney is leveraging AM to completely redesign its TJ150 turbojet engine. This redesign, enabled by AM’s design freedom, has drastically reduced the engine’s part count, leading to faster production and potentially lower costs.
• Large-Scale Manufacturing: The US Army is pushing the boundaries of AM with the “world’s largest 3D printer,” developed by MELD Manufacturing. This massive system is being used to produce parts for the Apache attack helicopter, demonstrating the scalability of AM to meet the demands of large-scale military hardware production.
The true strength of AM lies not only in its ability to produce diverse military equipment but also in its unparalleled speed and agility. Task Force 99, a specialized Air Force unit, has showcased the potential of AM by designing and printing a functional drone in under 48 hours. This rapid prototyping and production capability provides a significant advantage in adapting to changing battlefield conditions and countering emerging threats, outpacing the limitations of traditional manufacturing processes.
More broadly, there is a focus on quick production of cost-effective solutions that can be readily deployed, where AM has an inherent advantage.
The drive to reshore manufacturing and reduce reliance on foreign suppliers is a central theme in the US’s embrace of AM. In a significant move that underscores the strategic importance of AM, the US Department of Commerce has recently imposed export controls on metal AM equipment. This action, driven by national security concerns, restricts the flow of sensitive AM technology to potentially adversarial nations, highlighting AM’s potential to shift global power dynamics.
While the transformative potential of AM in reshaping the future of warfare is undeniable, challenges remain. Scaling up production to meet the demands of largescale military operations, establishing industry-wide standards for quality control, and advancing materials science to expand the range of printable materials are all critical areas that require further development.
As AM technologies continue to evolve and integrate into mainstream manufacturing, their role in re-building the USA manufacturing base and enhancing national security becomes increasingly pivotal. By bolstering the United States’ manufacturing autonomy and resilience, AM not only addresses current supply chain vulnerabilities but also prepares the nation for future challenges in an uncertain global landscape.
“AM has been put to the test in the last year.”
Gain practical knowledge through proactive participation and handson experience
n Become more productive through AMUG’s community of problem solvers
n Learn and share expertise, best practices, challenges, and application developments
Impactful networking without any agendas
n Embrace the camaraderie and enjoy effortless networking
n Form meaningful connections through casual conversations
Get the most value of any conference with an ALL-INCLUSIVE program
n 4-day conference
n Hands-on workshops
n Technical competition
n AMUGexpo
n Meals and entertainment throughout
We Convene...
The most brilliant minds from industry and academia
We Coordinate... Transformative technical and workforce data
We Catalyze... High-value, high-impact collaborative projects
America Makes is the leading collaborative partner for additive manufacturing and 3D printing technology research, discovery, and innovation in the U.S. Structured as a public-private partnership, we innovate and accelerate AM/3DP to increase global manufacturing competitiveness.
Focused on additive manufacturing, America Makes is the first institute of the Manufacturing USA® network. ®
Learn more at www.AmericaMakes.us