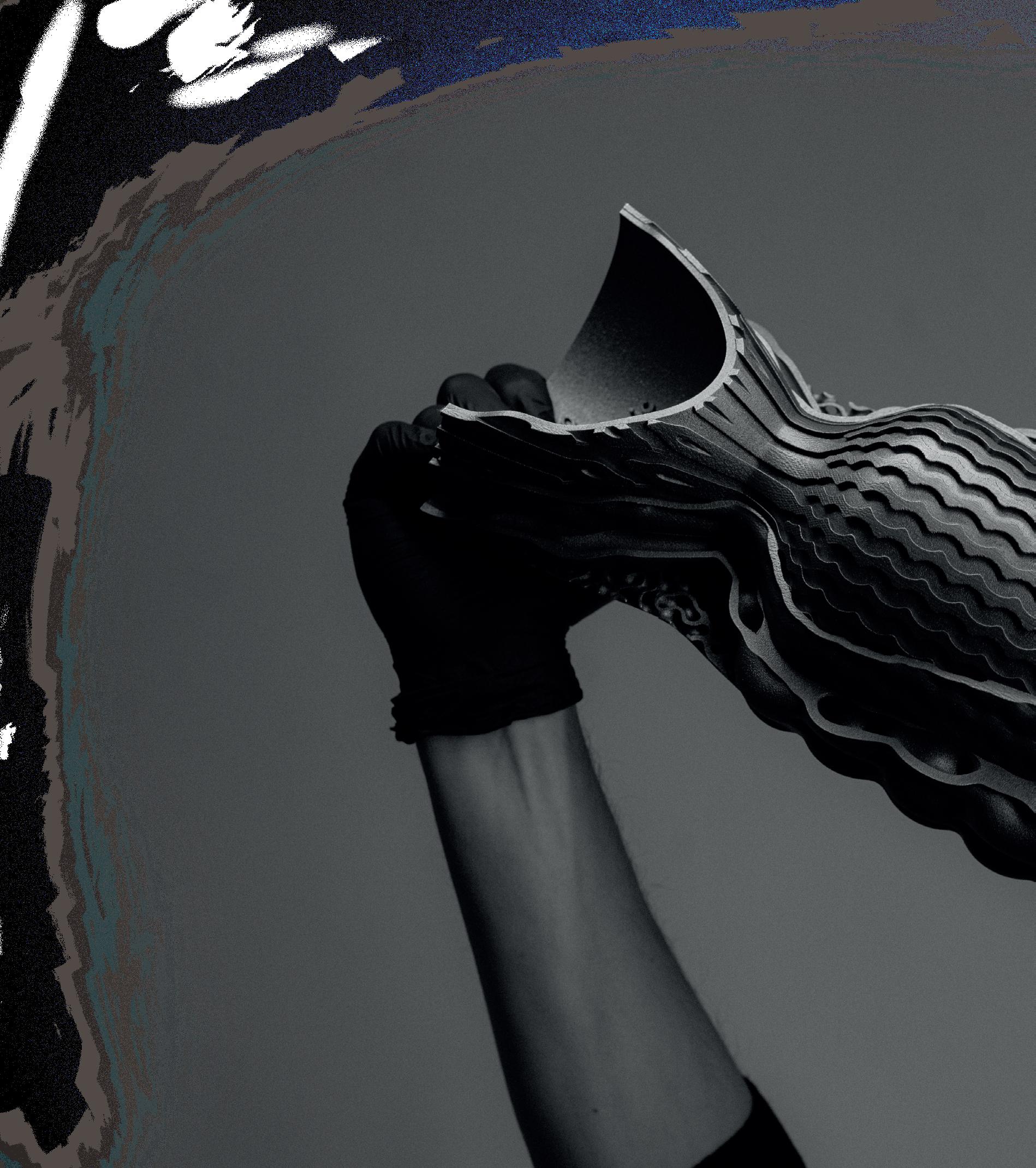
6 minute read
FINDING A ‘RITHM
There are many places in which you could pick up the story of Hyperganic CEO Lin Kayser. There’s the child inspired by technology, the entrepreneurial teenager, the successful businessperson rubbing shoulders with Hollywood actors and now the spearhead of a team that talks seriously of a ‘paradigm shift’ in design.
That kind of chat followed Kayser’s purchase of a 3D printer in 2012. For someone who thinks of software as an ‘amazing technology that can create anything,’ having a 3D printer fabricate some of those things physically saw Kayser hooked immediately. While at that time many in the industry were positing the idea that a 3D printer would be in every home, one of the technology’s hobbyist users was captivated by its potential to ‘transform’ the way we manufacture. Not long after, he handed his notice in at his then-employer Adobe, set up a new start-up in his hometown of Munich and is still motivated by that very thought nearly ten years on.
“The key thing for us is to dramatically accelerate innovation,” Kayser begins. “We believe that innovation of physical objects has not been progressing very fast. And we believe that we have a lot of challenges as humanity that we need to solve through physical objects. Think about last year, we shut the entire world down, essentially, and it had how much impact on carbon emission? It had one, but we didn’t have enough impact to make a dent in climate change, for example. The technical solutions that we have need to change in order to address [these issues].”
FUNDAMENTAL FRUSTRATIONS
Hyperganic’s contribution to that is the Core 2.0 and Print Framework 2.0 software it is launching formally in the coming months, after years’ operating in stealth and even more time carrying out R&D. As Kayser saw 3D printing’s potential to alter the way things are made, he also observed that ‘maybe we should also change the way we design things and engineer things.’ He believes that 3D printers are not so much limited by their technology as they are by the designs that are fed into them. And so, Hyperganic has set about developing tools that not only aim to change how parts are designed, but in doing so, take full advantage of 3D printing’s capabilities.
From the outset, Kayser and the company’s CTO Michael Gallo believed they would not be able to enable the paradigm shift they think is necessary with traditional CAD software that ‘work very nicely for simple shapes, but terribly for complex things.’ In one conversation, Gallo is said to have suggested creating a model where ‘we basically store every atom, every molecule in an
SHOWN:
ROCKET ENGINE APPLICATION DEVELOPED WITH HYPERGANIC’S PLATFORM
WORDS: SAM DAVIES 'RITHM
object and then we can design anything the printer can print.’ “Of course,” Kayser recalls, “we had a good laugh and said, ‘this is ridiculous.’ But then a couple of days later, Michael calls me and says, ‘hey Lin, why don’t we try this?’”
Building the high voxel engine that would enable Hyperganic to do this took three to four years. But now, Kayser and co are confident their platform can ‘represent any object that a 3D printer can theoretically output.’ That opens them up to objects of such extremely high complexity that the development of the parts, Kayser says, need to be automated.
“This is where we end up in AI-based engineering, where you can use genetic algorithms and use neural nets to find out interesting patterns and structures that work well,” Kayser explains. “And why is that so interesting to me? That has its roots in a fundamental frustration. Take a modern car and strip away all the plastic decoration that they put on, it doesn’t look that different from a car from the 1980s or 1990s. And you ask yourself, why has innovation not happened faster? Because we need it urgently, we have a lot of global challenges that we need to solve and we’re kind of running out of time. And the problem is that the paradigms that we use to engineer objects are derived from the way the Greeks and the Romans designed objects. The smart guy or smart girl sitting in front of a computer and drawing stuff on the screen and it always depends on the intelligence and experience of the designer and engineer to know what comes out of it.”
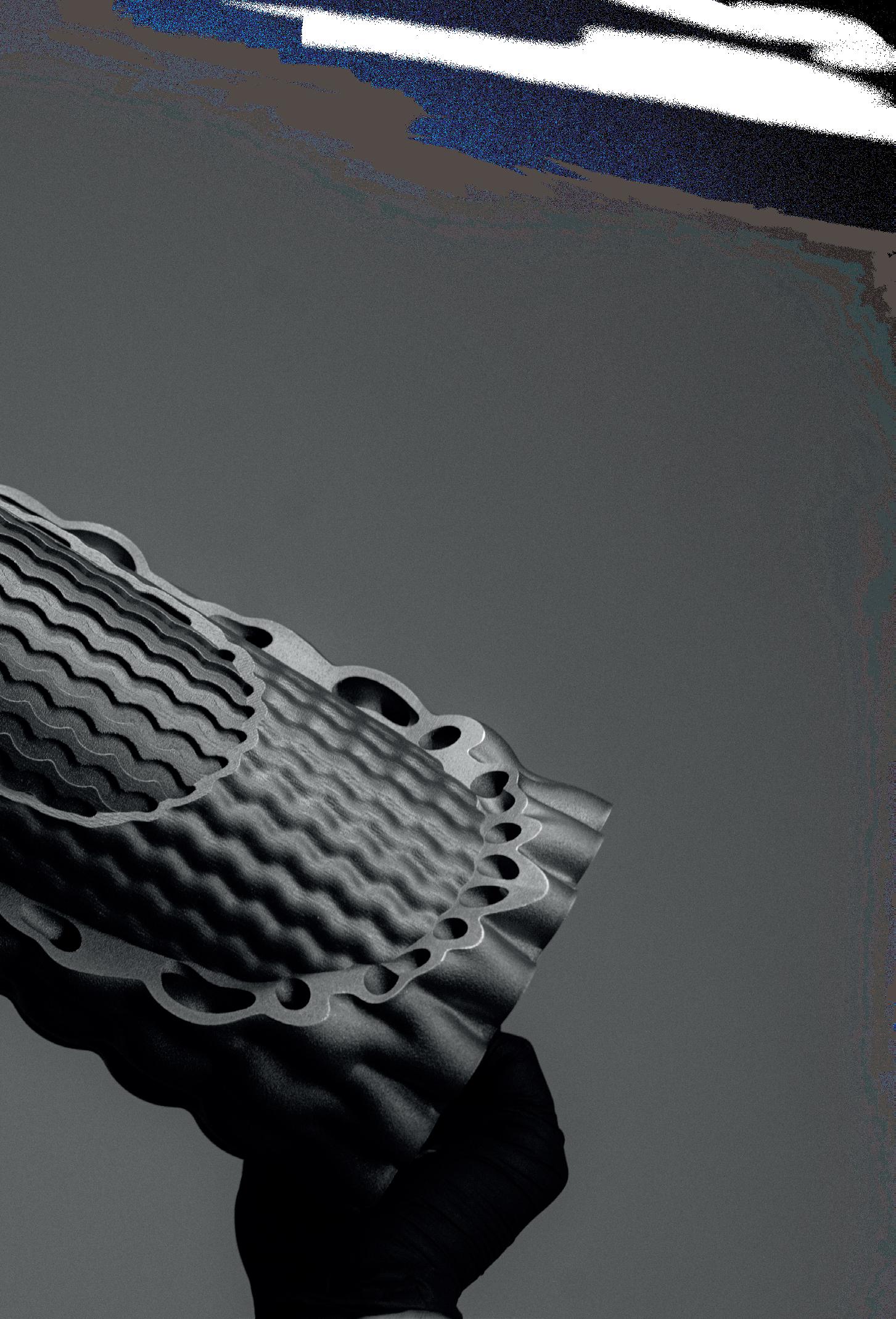
Hyperganic’s idea is to develop algorithms within its Core 2.0 offering, input a description of the part and allow the artificial intelligence to take care of the design of that component. It leans on some of the principles of generative design tools, building optimized designs from scratch and then allowing the user to harness the intelligence generated for other products. Hyperganic refers to this as ‘defining a way to design’, rather than simply designing with sketches and CAD drawings. This idea has been adopted in the computer hardware space where initially microchips had been sketched, and then later designed in a CAD programme, but once they got so complex, they had to change the approach.
“Instead of doing computeraided design, you have to do computer-generated design,”
Kayser explains. “If today you design a microchip, you’re not doing it geometrically, you’re doing it algorithmically. You’re describing what the algorithm should do and the algorithm comes up with the geometry. That’s what we want to do for the rest of the world.”
EARLY APPLICATIONS
Since Hyperganic first engineered its software a few years back – before Kayser had even incorporated the company in 2017 – the company has been working with customers to develop concept applications by combining its Core offering with 3D printing technology via Print Framework’s mesh repair, slicing, support generation and stacking tools. One of those applications is a customized bicycle helmet that was derived from the scan data of a triathlete’s head and statistical crash data procured from research into how cyclists fall when they come off their bike. This information was factored into the Hyperganic algorithm and output thousands of design possibilities, with the selected one looking like a slimline cap, with room for ventilation at the top of the helmet and a less porous structure around the sides to protect the user’s fall.
“This is the power of mass customization,” Kayser told the All Digital Additive Manufacturing YouTube channel in January. “First, it fits the right person, and second, you can take new information into account and in the next production run, immediately there is a better product. This can only happen if you have algorithms creating these things because no human ever has the time to adapt everything all of the time.”
Another application the company has been working on is a heat sink additively manufactured in copper that looks more like the bristles of a brush or a coral in the ocean than a typical heat sink. Its surface area has been maximized to allow it to dissipate as much heat as possible, while the funnelling of air to the bottom of the component has also been optimized. This is considered to be an incredibly complex design to tackle, per Kayser, but because it was developed with an algorithm, it’s not a complexity that Hyperganic needs to address again and again.
“When you implement it once, you can reuse it everywhere and sometimes it’s really surprising where you end up,” he says. “For example, the heat exchanger, because of the algorithm it uses, it generates structures that are very stable, so you can stand on it. We’ve now been using that in completely different applications where you need something that distributes the weight evenly. It’s so interesting because we actually just wanted to radiate a lot of heat and be aerodynamically optimized so that the air flows and takes the heat out.”
Read the second part of this interview, where Kayser goes on to discuss some of the company’s biggest challenges in bringing its products to market, at: mytct.co/HyperganicInterview