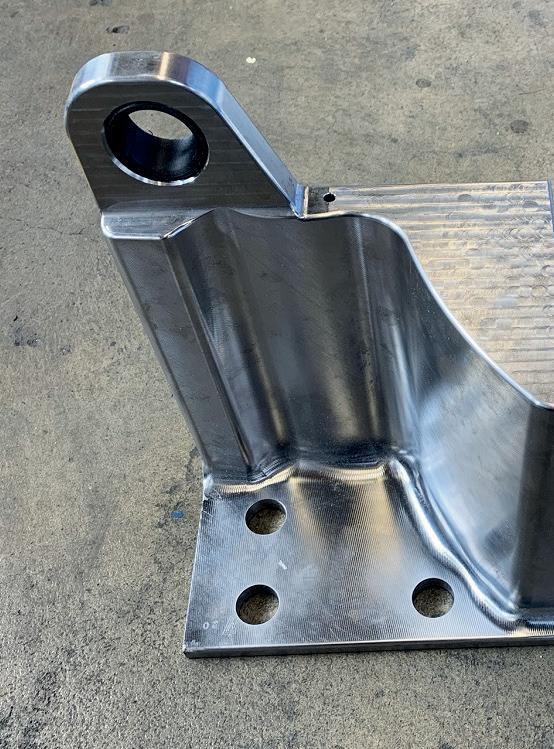
7 minute read
THE INSIDE TRACK
Stefanie Brickwede, Head of Additive Manufacturing at Deutsche Bahn and Managing Director of Mobility goes Additive (MGA) talks to Laura Griffiths about 3D printing in the rail industry, why sustainability needs to be taken seriously and how the pandemic pressured companies to innovate.
TCT: Last time we caught up you
were on a MakerBot roundtable talking about the use of 3D printing during the pandemic. Deutsche Bahn had already been using AM for a long time, but can you give us your take on how AM adoption was ramped up during that time?
SB: It's not just the pandemic. We have to cope with such interruptions of supply chains nearly every month. And what really helped during the pandemic, those companies are more minded to consider alternative ways of production. Many companies say they are much more open to additive manufacturing than before. That’s one of the reasons. Others are that they were under economic pressure, they have to move. The need to think about innovation is much bigger than two years ago.
TCT: During that panel, the question
was asked of whether this open mindset was really going to stick with us postpandemic. And as you've just said, it's not just about a pandemic. What are your thoughts now?
SB: So many companies have discovered that they can use the technology for parts, spare parts, whatever you can think of. You can see a lot of it in tooling. For tooling, you don't need any certification so those are the low hanging fruits. In the railway sector, also far beyond in the automotive sector, they’ve used AM for a very long time for prototyping and now more and more for tooling. They have printers on their premises, in their maintenance workshops or production halls, and the logic just to have an idea, produce it overnight and use it the next day is really great. This is something we are now experiencing also within Deutsche Bahn and other railway companies. Within the network, we have eight European railway companies. The others are thinking and considering exactly the same.
What you can also experience is that you have a lot of younger and even older people who have a printer at home and bring the idea to the job. If you ask people ‘who is interested in joining in a 3D printing project or department?’, you will always find people who are really waiting for someone to ask them.
4RIGHT:
HANDRAIL SIGN WITH BRAILLE (SOURCE:
DEUTSCHE BAHN AG / OLIVER LANG)
6BELOW:
STEFANIE BRICKWEDE
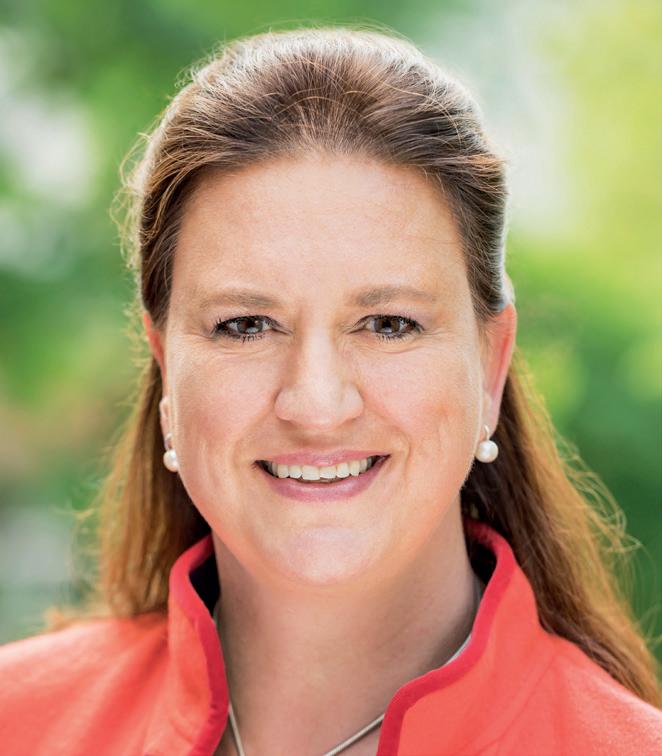
TCT: You mentioned it's not just
Deutsche Bahn, there are lots of other rail companies using AM. As more companies turned to AM throughout the pandemic, did you already feel ahead of the curve?
SB: In the railway sector, Deutsche Bahn and French SNCF, they are leading by far. But the others are very open to that. We have a working group, which is called RAILiability, they're working on rail and liability and the exchange in that working group is so open.
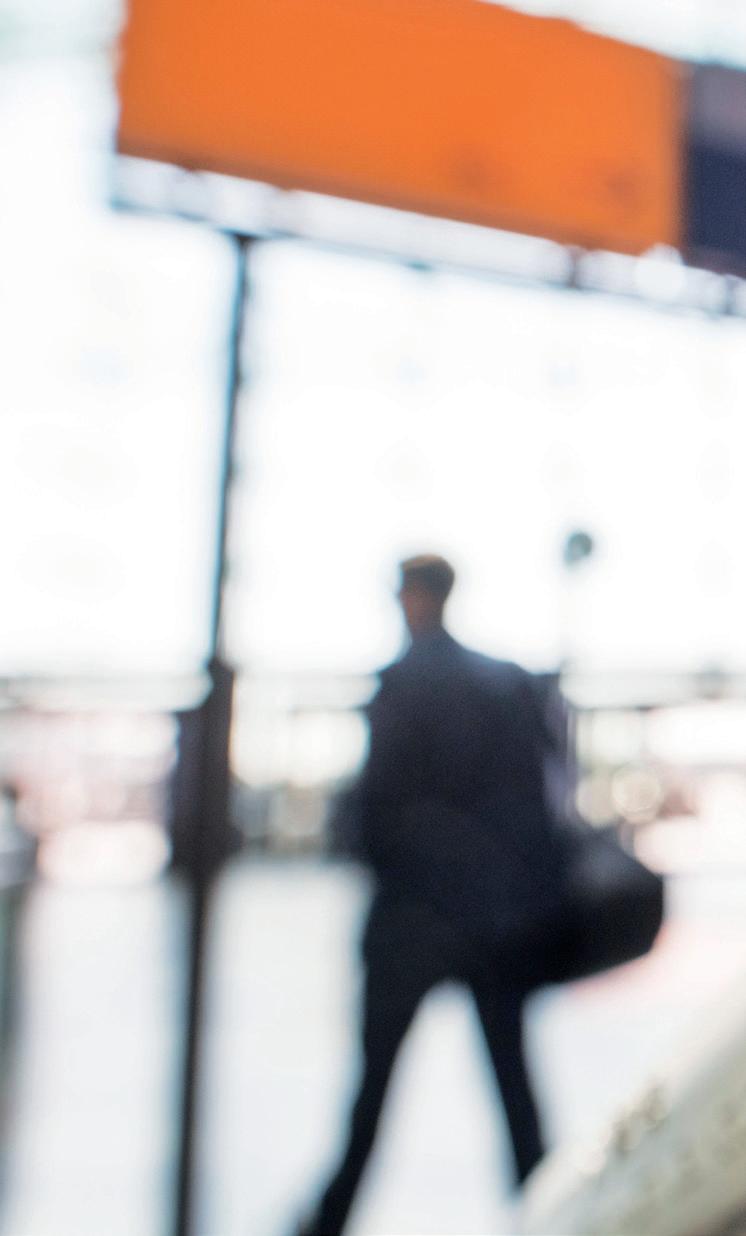
SHOWN:
SECONDARY RAIL STOP (SOURCE: DEUTSCHE BAHN)
TRACK
What you can also see is that, we all know that the automotive sector is really dealing with big change management projects, they have to focus on e-mobility so they really have to change the mind of the people. The suppliers also suff er from that crisis in automotive and it's really astonishing that not only one, but quite a few already considered producing AM parts for the medical sector. Three years ago, no one would have ever had the idea as an automotive supplier to produce parts for medical, that would have been too far. Now you can really experience that because they have to change, they have to be open minded, they have to focus on other markets. Medical defi nitely is a great market for AM and for us, it's great because within the [MGA] network, we already cover both mobility and medical. When we started with medical three years ago, I was asked by my board, ‘why do we do medical? We come from the railway.’ I said, okay, let's give it a try and if it doesn't work within the next two years, then we’ll stop it again. After the pandemic, no one would ever ask such a question again.
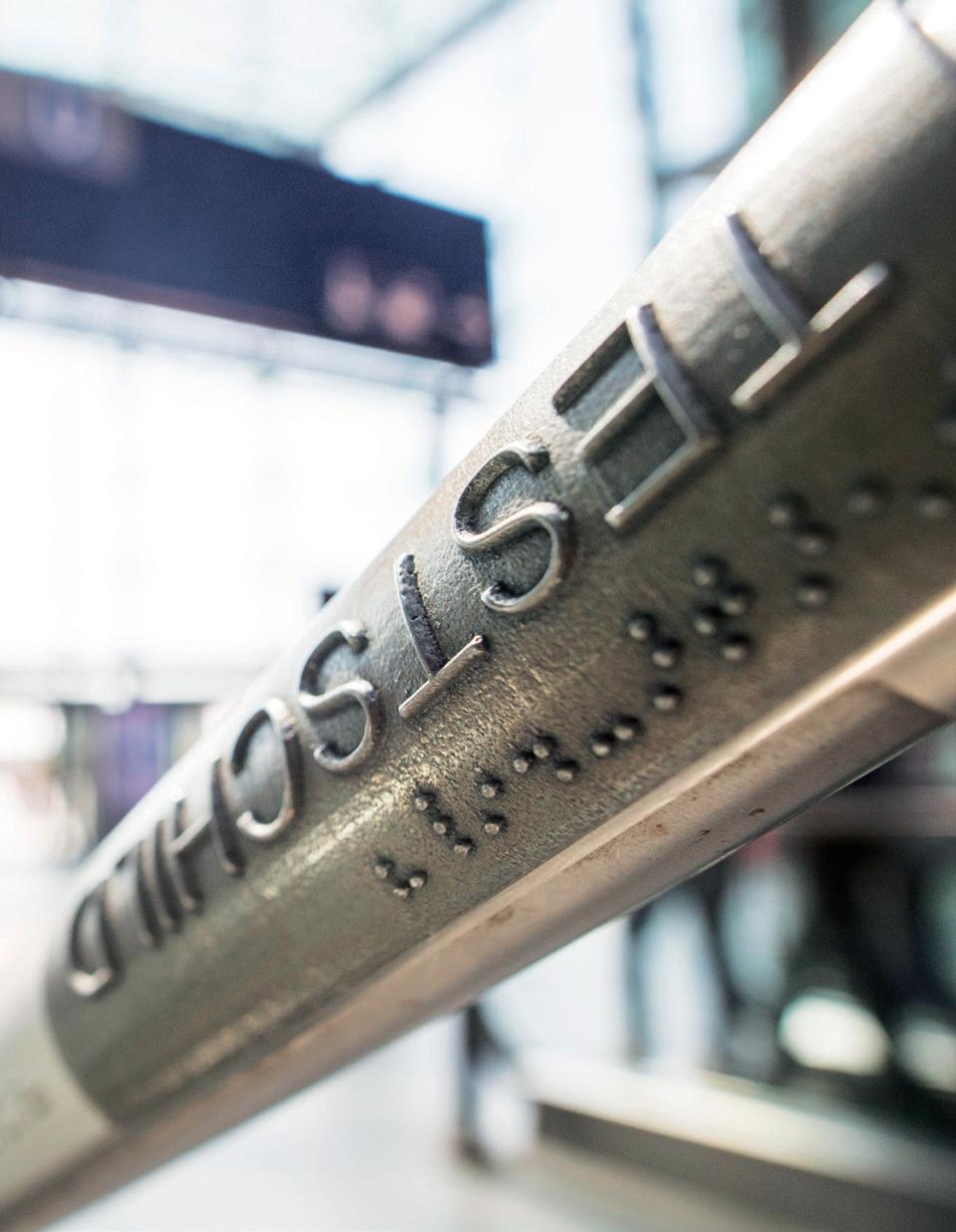
TCT: For rail applications, are we
talking mainly about polymers or metals?
SB: Metals as well. What you can see is that two thirds in the railway sector is polymers and about one third is metals. So, if it comes to tooling cases or smaller parts within the interior of trains, we are often talking about polymer parts. There we have to meet high levels concerning fl ame retardancy, which are even higher than aerospace. If you want to print parts to prevent the standstill of trains, we are often talking about metals. The metals are, of course, much more expensive and certifi cation is more crucial. What I fi nd really interesting is that we are now working on the fi rst use cases of concrete for the stations, for instance. I am absolutely sure that there's huge potential but you can compare it to printing spare parts fi ve years ago, the printing of concrete is quite new. They have to work on the certifi cation but also on materials and [fi nding] the right use cases.
We are also now working on elastomer printing and I'm not talking about prototyping elastomers. TPUs for prototyping existed for quite a long time but now we are talking about spare parts and those spare parts have to go on the trains for at least fi ve to six years, being in contact with oil and dirt and whatever you can consider.
TCT: Can you give us a sense of what
Deutsche Bahn’s in-house AM capacity looks like?
SB: We have a great team and we don't have that many printers because we still rely, I would say to 85%, at least, on printing service bureaus. We don't want to focus on the buying, if machines are suitable or not because we want to focus more on the solutions for use cases. And we're not a producing company. We're just a maintainer. For us, it's more important to cover a very broad variety of diff erent materials, technologies and use cases, and to know exactly what is the matching technology for the use case and also to be very open to new technologies. [...] We want to focus on not just on dealing with one or two or three machines. We now have now more than 60 desktop printers within the company. Those are mainly for training, tooling and giving people the opportunity to materialize their ideas.
TCT: Does that involve a lot of
redesign or is it better to repurpose current designs for AM?
SB: In maintaining sectors in general, you would always stick to the full fi t function of the previous part. So you would not re-design or do bionic design. That is something companies can do who are really constructing and then of course you get the full potential, but if you have to stick to certifi cation processes, you would not change that much because, of course, we are still in a phase that many authorities have to learn about AM. First they have to trust the technology and this is much easier to prove if you stick to the former designs. From month to month, it's getting more open.
TCT: One of the mission points for
Mobility goes Additive is ecological sustainability. Can you touch on how AM contributes to that?
SB: Most of the companies in the AM sector are either quite new start-ups or small, midsize companies. So usually, we have to give them a wake up call to focus more on ecological sustainability and not just greenwashing. We have to focus more on the ecological sustainability of materials, the whole production supply chain, how we can improve that, and it's not suffi cient just to say that we don't need as much material as other technologies, we also have to talk about energy consumption, we have to talk about how that material is produced. And we have to talk about great use cases.
This is why we started a study within MGA in cooperation with AMPOWER to have a logic where you can bring in, this is metal focused, some data concerning your part, material technology and so on and they will give you some indication of how sustainable that is. Of course, this is not on an individualized lifecycle assessment basis, but [...] this is what we really have to work on. Otherwise, the technology will lose its unique selling proposition.
We all have to focus more on virtual warehouses. [...] We did an analysis within Deutsche Bahn and after six years, you have to throw away all the elastomeric parts you have on stock, whether you use them or not. [...] That's a brilliant case for AM.