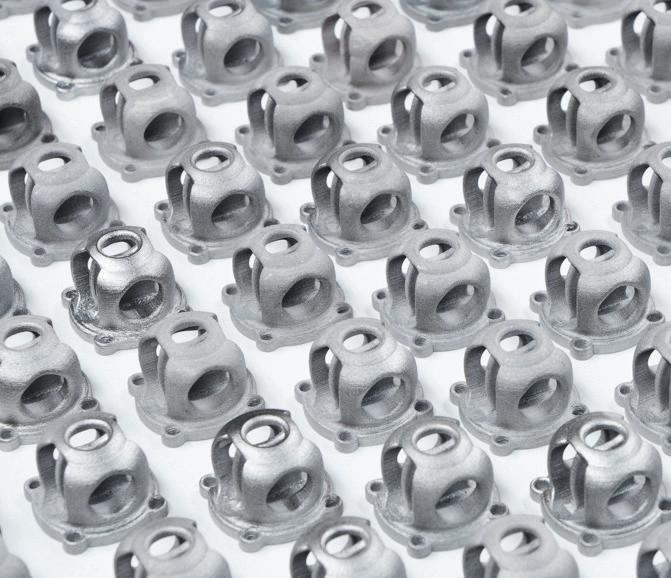
5 minute read
THIS IS AM 2.0
When Desktop Metal was featured on the cover of this very magazine last year and declared “bases loaded”, not even a global pandemic could curb the additive manufacturing (AM) company’s ambition.
First came the installations of its newly introduced Shop System, then a public listing on the New York Stock Exchange in a deal with Trine Acquisition Corp, and shortly after, the first of a series of bold acquisitions.
In January, Desktop Metal brought EnvisionTEC into the fold in a milestone $300 million acquisition, and with it, nearly 20 years of experience in polymer AM as the originator of DLP technology. For those looking on, the foray into polymers may have seemed surprising, but if you ask Desktop Metal CEO and Co-founder Ric Fulop, the opportunities outside of metal have always been clear.
“I've always believed there's a huge opportunity in composites and polymers,” Fulop told TCT. “We're in this segment of additive manufacturing that’s growing very fast and it's not tooling or prototyping - that's what's been done yesterday. It’s now all about mass production, competing with conventional manufacturing and changing the way people make things.”
Fulop and team have labelled this new era of manufacturing, “Additive Manufacturing 2.0”, the next generation in 3D printing that’s about leveraging the power of AM at scale for mass production. Shattering the belief that AM only works for specialized, low volume applications, AM 2.0 promises to innovate on product, process and materials.
Desktop Metal’s growth strategy, which revolves around these three central pillars - printers, materials, and parts, is to offer a broad set of economic AM technologies that enable the company to compete cost-effectively with conventional manufacturing across a range of applications. The focus being on performance across material properties, surface finish, tolerances, and most critically, speed and cost.
While Desktop Metal has continued to push hard on R&D internally by bringing more tweaks and materials to its own metal and composite platforms – most recently the addition of 316L stainless steel and dental-focused chrome cobalt material on its popular binder jet Shop System and also 316L SS, 4140 low-alloy steel, 420 SS and nickel alloy IN625 on the Production System platform – the company has sought inorganic opportunities to grow with the acquisition of multi-material 3D printing firm Aerosint and the Phonograft platform enabled through Beacon Bio, the latter of which came from its Desktop Health business line that's dedicated

SHOWN:
PARTS PRINTED ON THE DESKTOP METAL PRODUCTION SYSTEM
SHOWN:
FORUST AUTOMOTIVE LUXURY WOODEN INTERIOR
AM 2.0
Desktop Metal on additive’s next level.
on investment and can actually make money with this equipment. That's really what will enable broad adoption of this technology.”
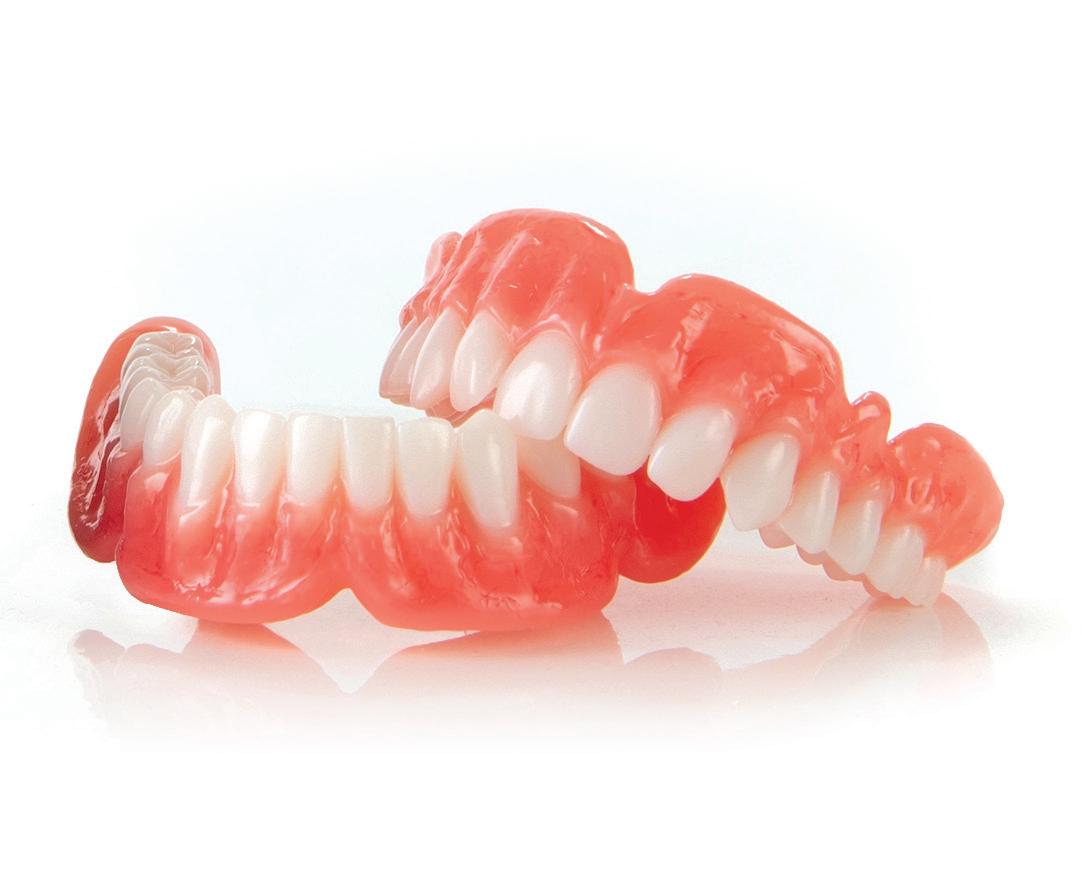
SHOWN:
DENTURES MADE WITH FLEXCERA
to the dental, orthodontic and otolaryngology markets. Most recently, the company announced a defi nitive agreement to acquire binder jet leader ExOne and 3D printed hydraulics manufacturer Aidro, both AM pioneers in their own right. There was also the launch of its new Forust process focused on delivering sustainable 3D printing with upcycled wood waste. These expansions mean Desktop Metal now has more than 225 qualifi ed materials across metals, composites, polymers, elastomers, ceramics, wood, sand and biocompatible materials.
“That is a huge enabler,” Fulop said. “We have elastomers that are best in the world through our acquisition of Adaptive3D. We have wood, which is a ground-breaking new material made from upcycled wood waste, and we've been completely astounded by the demand for that product. We have a very good project on photopolymers and what's changed in that world in the last couple years is the ability to have epoxies or resins that basically use heat to improve the mechanical properties of the part or ring-opening chemistry.
“On the metals side, what's exciting is that now with powder metallurgy, we’re able to achieve better material properties than wrought in many cases. We've launched titanium Ti64 for our Studio System recently and we’re able to get 17% elongation and better than wrought strength - that's unheard of. That's the type of result that gives confi dence to engineers to produce parts with this process for volume.”
Some of the best examples of these high production volumes can be found in dental, a market which Fulop describes as the “highlight of our sector,” thanks to the 1,000+ dental customers using EnvisionTEC printers and validated materials as well as the need for customized products. Emphasizing this demand, the company announced FDA clearance for Flexcera Base and CE Mark Certifi cation of its Flexcera resins, proprietary resins used in 3D fabrication of high-quality dental prosthetics. This was followed shortly by the launch of a turnkey metal solution based on its Shop System alongside a new chrome cobalt material option that will enable printing of custom dental products and surgical guides such as 32 partials in less than four hours.
“I think where we go next is to compete with conventional manufacturing,” Fulop said, noting the production volumes now possible. “We're trying to enable the adoption of additive at scale for production of end-use parts. I'm proud of the fact that some of our customers are small businesses, and they get a return
Companies like FreeFORM Technologies, one of the fi rst service bureaus to off er metal binder jet AM, are already seeing that return on investment with Desktop Metal’s binder jetting solutions. Because it eliminates the need for tooling, the Production System P-1 has helped FreeFORM realize cost savings - and perhaps even more signifi cantly, reduce lead times. In one example, FreeFORM was able to produce a medical “wrist” part in quantities of 1,000 or more at a per-part cost of $6.50 and deliver fi nished parts to customers in just over two weeks. Producing that same part via MIM would require an upfront investment in tooling of more than $40,000 and as much as three months before a single part was produced.
As Desktop Metal looks to 2022 and the future beyond that, the company will continue to prioritize developing solutions that integrate hardware, software, and materials to make it cost-eff ective to deploy AM at large scales. And for some of those applications, Desktop Metal may go so far as to actually be a supplier of parts themselves - where it makes sense and where it's margin accretive to the business.
With the breadth of new technologies now under one roof, when asked how the company will remain focused, Fulop confi dently states: “You could ask the same question of a company like Amazon, which has grown very fast and they're able to succeed. We keep the team small, give people high accountability and push the decision making to the edges. We bring in great people and give them all the tools they need to succeed, and then we also have good managers. That is how we are able to scale.”
If last year was “bases loaded”, this year they’re hitting a grand slam.