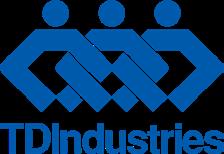

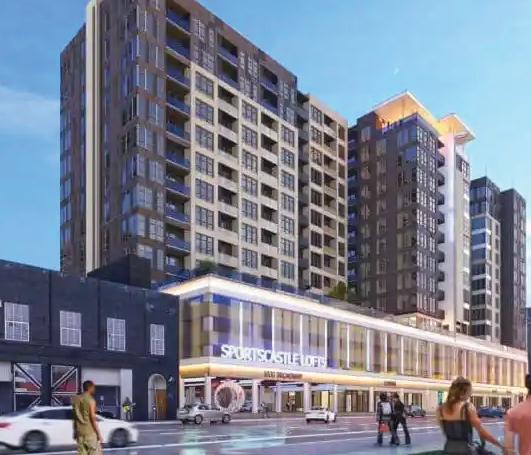
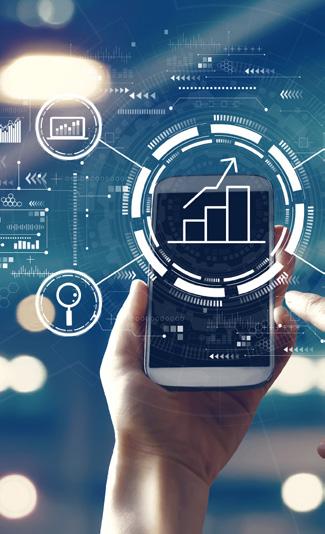

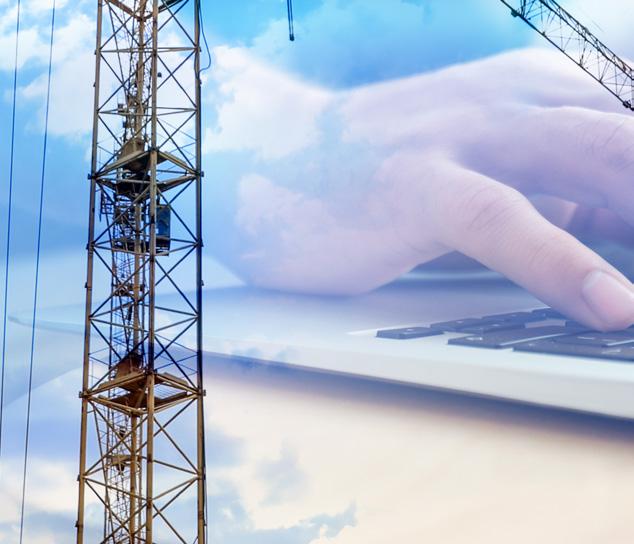
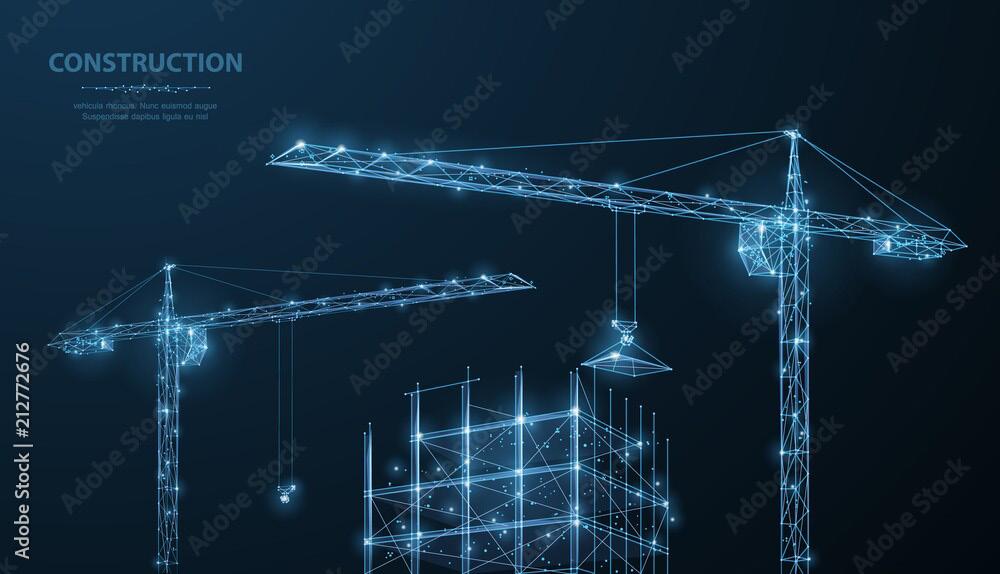
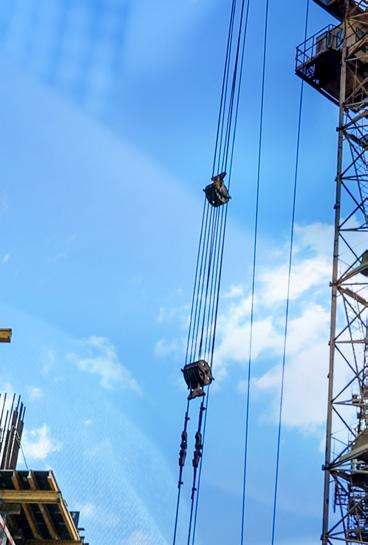
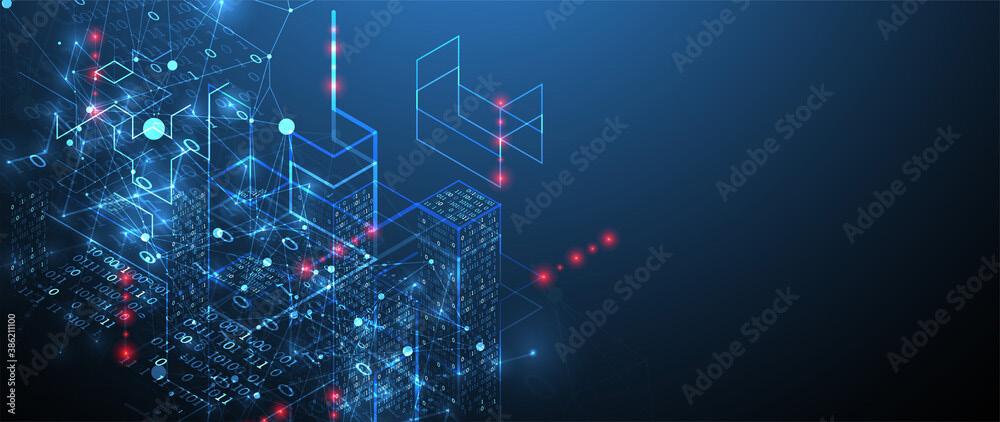
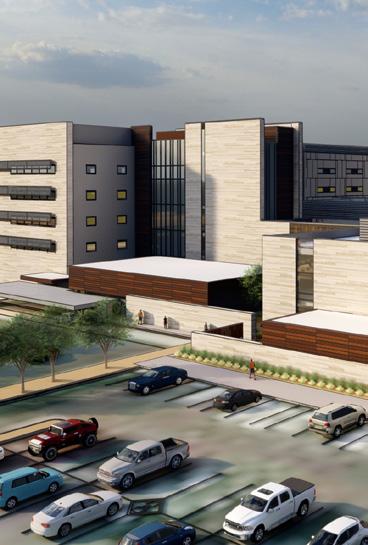

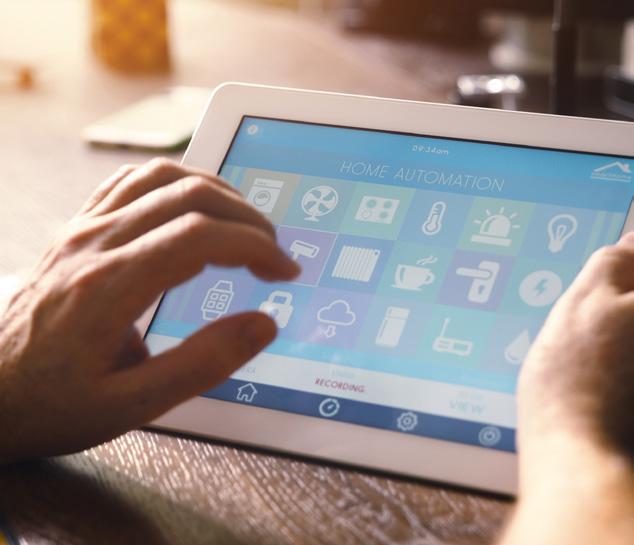
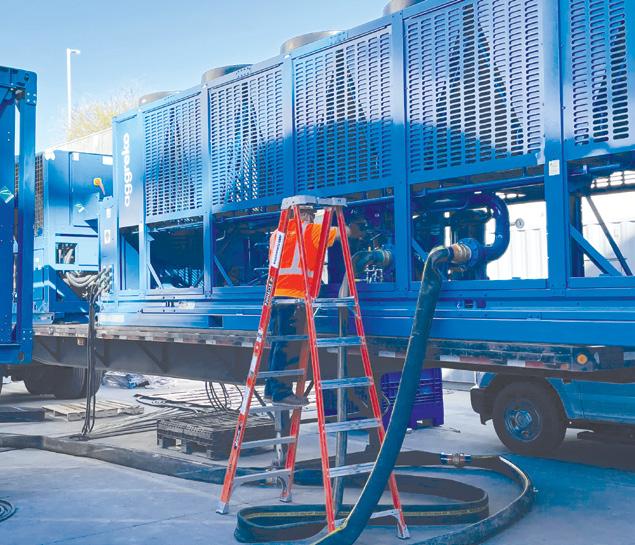
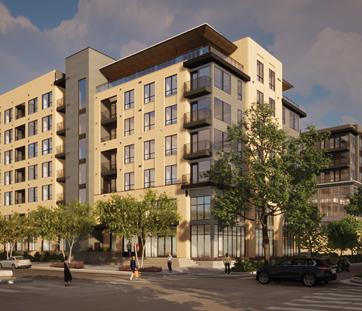
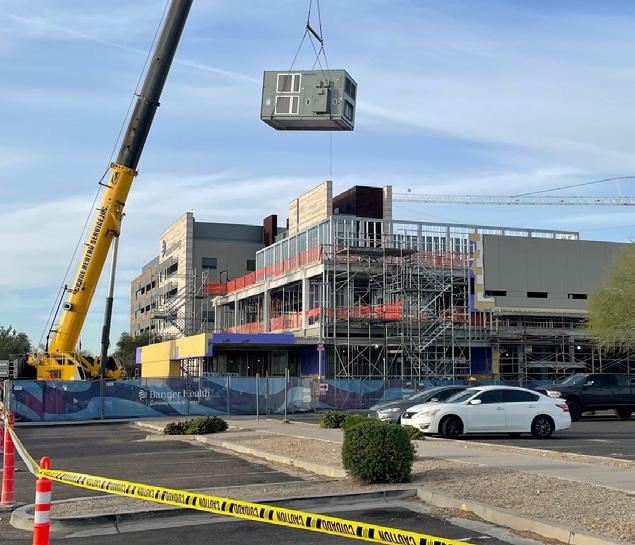
Dear Valued Customers and Partners,
When I think of all we have accomplished together in a challenging year, I am filled with hope and anticipation for our future. To quote Henry Ford, “If everyone is moving forward together, then success takes care of itself.”
We wouldn’t go far without the strong, honest relationships forged over the years of experience we’ve built with you, our customers and partners, or the strength of our dedicated team of employee-owners. Though we’ve all been involved in difficult conversations about supply chain challenges, material escalations and labor shortages, I can’t help but focus on the positive impact our collaborative work continues to have on growing and sustaining our communities.
I couldn’t be more proud or excited about the purposeful work we do to design, build and operate the buildings that bring life and economic prosperity to our cities and neighborhoods.
From multifamily housing to hospitals, schools and data centers, we use the latest tools, technology and problem-solving skills to open the door for new possibilities and a better tomorrow for us all.
I appreciate your time reading through this issue of TDSpirit and celebrating our mutual successes. In this season of gratitude, I wish you and yours all the best. I am thankful for your continued partnerships and support.
Sincerely, Harold
“If everyone is moving forward together, then success takes care of itself.”
—HENRY FORD
TDIndustries’ Multifamily division in Denver upgraded earlier this year to a combined office and shop space in Englewood, Colorado.
WATCH VIDEO
Austin officially celebrated the opening of their new office, joined by CEO Harold MacDowell and several out-of-town guests. The new one-story, 20,000-square-foot office includes 13 meeting rooms, a break area, large flexible spaces and a 15,226-square-foot warehouse to support storage and staging needs.
TD Piping Lead Kaylin Leas is not only a skilled tradeswoman but adds ‘commercial star’ to her resume.
Leading U.S. brand Justin Boots reached out to Leas, who has been with TD for four years, to ask her to be in a commercial for the Stampede Rush, a new women’s work boot.
Leas, who has been a welder for nine years, was excited for the opportunity.
“I was nervous as all get-out, but everyone was so nice,” Leas said. “I was saying, ‘Just tell me if you want me to smile, where to put my hands,’ stuff like that. They were so helpful.”
Leas said that Justin Boots wanted an actual tradeswoman to star in the commercial, and she fit the bill. Outside of her technical qualifications, she says she has some modeling experience and even auditioned to be Faith Hill’s stand-in for the movie 1883.
The commercial was filmed at a job site in Texas, with a great deal of support from General Contractor DPR Construction. The commercial will run on The Cowboy Channel, a cable network available in 42 million homes.
Leas, who has dreams of becoming a piping foreman, also enjoyed representing TD in front of the camera, something she does in her daily life.
“Any time I get the chance, I always try to plug TD’s name,” Leas says. “Whether it’s in the Empowering Women in Industry group I’m in, or wherever else I am, I always tell people about TD.”
Her job site colleagues have been very supportive about her starring role, Leas says, which is “a breath of fresh air.” And she’s even got a new nickname out of the experience: Hollywood.
Did you know that TDIndustries provides facilities management services in Arizona?
TDIndustries recently launched a five-year partnership with Northern Arizona University (NAU) in Flagstaff, Arizona. Our experienced HVAC Facilities team will be on-site year-round to support and train the in-house campus team in proactive and corrective maintenance.
TDIndustries supports NAU, and building operations teams across all industries, in conserving resources, reducing utility bills and saving money and labor on emergency maintenance.
Inflation is a real issue, and one that demands our attention if we want to deliver the most value to our customers. Every aspect of our business and every phase of the project is affected.
PRE-OPPORTUNITY: Invest time and resources in monitoring regional and global factors affecting material and equipment price escalation and supply chain bottlenecks. The more we understand, the better equipped we are to develop strategies that improve the bottom line. Knowledge is the fuel for formulating the value proposition at every project stage.
PRECONSTRUCTION: Early equipment and material procurement is a common strategy employed to reduce escalation risk. This strategy is easy to understand but can be tricky to implement. The opportunity
lies in defining and communicating the underlying assumptions. Does the entire team understand how to design the project to fit the equipment and material when design details are incomplete?
Early in the design is the time to understand opportunities for prefabrication and modularization. A contracting firm that has done its homework understands off-site labor and material efficiencies and is prepared to properly estimate cost and demonstrate value.
CONSTRUCTION: Focus on communication and planning. Follow your procedures and do not take shortcuts. Equip the project management and field leadership teams with all relevant information at this handoff.
Understand the schedule to coordinate the installation
of prefabricated assemblies at the right construction phase. Identify float in the schedule for any materials and equipment missing their target arrival dates. Approve multiple suppliers for supply chain robustness.
SERVICE AND FACILITY OPERATIONS: Periods of inflation squeeze both capital budgets and operating budgets. We owe it to our customers to articulate the benefits of extending the useful life of assets through proactive planned maintenance.
Recent market changes have placed additional responsibilities on our workforce. We must not overcommit our teams.
The market changes represent opportunity and a catalyst for positive industry change.
To read the full article, go to PHCPPros.com.
In his 43 years as an employee-owner with the company, TDIndustries Vice President of Dallas Construction JimBo Bunnell has seen and enriched all sides of the business. He’s a true servant leader who develops and supports superintendents, foremen and field trade workers in his executive field operations role.
Bunnell has decades of experience as a superintendent for projects such as the Cowboys’ AT&T Stadium, the Arizona Cardinals’ Stadium and The Ballpark in Arlington, in addition to office buildings, mission critical data centers and high-rise apartment complexes. He started at TD after high school graduation as a plumbing apprentice, moving up to a plumbing foreman, then superintendent. He’s married with two adult daughters, five grandchildren, two dogs and two horses. He enjoys riding and training horses when away from work.
Excellence in occupational safety and health is a crucial component of TD’s culture that includes our ZERO Harm safety vision of performing work that results in no Serious Injuries and Fatalities (SIF).
In 2022, our core value to fiercely protect the safety of all included optimizing current technology to record 200,000-plus electronic safety processes captured through our safety app and allow for more meaningful daily planning conversations. TD is setting the standard for innovation in safety in many areas, including safety engagement focus and safety helmets.
TD continues to optimize the use of SmartTagIt on our Safety Engagement Journey. SmartTagIt is an integrated, customizable safety app that replaces much of the paperwork needed for pre-task safety plans, inspections, work permits and safety observations, all housed in a social media style feed that’s easily accessible to the project or team for process visibility and hazard awareness.
TD is on track to record more than 200,000 safety observations this year.
Disrupting the pre-task safety planning (PTSP) process has been a worthwhile journey. Six months into the video-based planning processes, the team began to see the need for improvement in writing plans. The team worked with the app developer, and 10 safety managers scored 2,000 text-based PTSPs to teach the model how to score those written plans. Now the team is scoring and improving on two different metrics associated with pre-planning: writing great plans and leading great daily planning conversations.
Before 2019, TD captured 12,000 safety observations per year and had limited visibility to other safety processes. But with Smart-
TagIt, that number has increased to 176,000 in 2020, 189,000 in 2021, and more than 200,000 projected in 2022. With the reporting capability from the safety app, the team has been able to improve quality, at-risk safety observation percentages and more.
While observations were once separated into eight rigid categories, TD employees now have the capability to input free-form text they deem best fits their observation, and the artificial intelligence will categorize natural language and unstructured data into intelligent reporting.
With the video- and photo-based social tool, TD can measure safety risks, stay ahead of new problems that are being unveiled and move forward in the march toward ZERO Harm.
Safety helmets were introduced in the industry around 2015. While they didn’t gain much traction then, they are now quickly becoming the standard in preventing SIF-related fall injuries.
TD is introducing safety helmets to better protect against major injuries from dropped objects or falls. The traditional hard hat, now a 50-year-old technology, can come off during these events, causing unnecessary injuries and hospital visits.
TD’s safety team and key leaders began wearing safety helmets in 2021. On those helmets were QR code stickers that allowed interested employee-owners to sign up or request to be upgraded to a safety helmet.
Some of the key benefits to safety helmets include: Protection against side impacts (compared with only vertical impacts with traditional hard hats)
A chin strap, which helps keep the helmet on during a fall event
Improved design and better impact protection Improved comfort
On the safety and health team, we strive for excellence by continuously improving our safety systems and objectives. Safety is about much more than reminding someone to wear a hard hat. As safety professionals, we anticipate needs, react swiftly and help prevent injuries and incidents. At TD, we’re about continuous aggressive improvement. That’s reflected in our work and in each of us as individuals.
JAMIE DABBS, VICE PRESIDENT SAFETY, HEALTH AND ENVIRONMENTALEditor’s Note:
CyrusOne® is a registered trademark of Cyrus Networks, LLC
The CyrusOne® Data Center V, located in Texas, is a 208,000-square-foot, purpose-built facility designed to safely and securely house the computer servers of companies around the globe. Supplying the critical infrastructure to power and protect these high-value assets from damage requires significant environmental controls including temperature, humidity, ventilation, fire suppression and more.
TDIndustries won the mechanicals bid for this multi-phase project, with work starting during Phase 2 in August 2020 and ending after Phase 3 was completed in April 2021.
By the time TD’s work started, the first floor of the building was already occupied, requir-
ing substantial planning and coordination to ensure the continuity of the tenant’s operations. In addition to safeguarding the existing occupant’s equipment and protecting the safety of its personnel, TD strategically scheduled all of its crane picks on weekends when the offices were closed. And anytime a tie-in to the first floor was required, detailed Methods of Procedure were written and approved at least two weeks in advance to limit the disruption to the tenant’s business.
Due to limited on-site storage, material deliveries were meticulously scheduled for specific dates and times – then brought directly into the building and staged for installation. In the middle of Phase 3, the historic winter storm that temporarily shut down many Texas businesses further complicated matters. Lead times on some plumbing materials were extended, so TD substituted with equivalents to keep the project on schedule.
To top it all off, the COVID-19 pandemic was at its peak, slowing supply chains and compelling TD and all the site contractors to take special precautions to protect workers. Staggered work schedules, quarantine protocols and an abundance of hygiene and personal protective equipment were put into place.
TD had an opportunity to shine in problem solving after a discovery of unplanned offsets to the chilled water risers. TD’s superintendent, Charlie Miffleton, stepped in to help pull dimensions off column lines of existing pipe. Then, a VDC designer updated and revised CAD drawings used not only for this data center, but also for other CyrusOne locations around the globe.
Despite the scope of the project and the challenges that arose, TD stayed on schedule and within budget. “Proactive and transparent communication was key,” Senior Project Manager Amanda Moguel says. “Charlie [the project superintendent] and I talked every morning, setting our plans and making sure we each knew what the other was doing. We also engaged our 15-20 crew members with weekly luncheons and an on-site production board that gave work ers the rundown of the day’s activities at a glance.”
“Amanda stayed in daily contact with the General Contractor, Rogers-O’Brien Construction, to ensure our priorities were aligned. She’s also become a valued resource for CyrusOne, who reaches out to her directly when they have questions or need help solving a problem,” says VP of San Antonio Construction Greg Bailey. “Amanda embodies our culture of building and maintaining trust and the passionate pursuit of excellence,” he added.
TD is part of a team of data center contractors selected by CyrusOne that also includes Rogers-O’Brien, Walker Engineering and others. TD has worked with CyrusOne since 2014
and together, the team has completed three data centers.
Additionally, TD has become an expert in data center mechanicals, working with Stream, QTS and other owner developers. And the future looks bright with CyrusOne as TD continues to bid on its growing footprint of facilities across the Southwest.
Regardless of the many challenges, the CyrusOne Data Center V project was on schedule and completed on time. Leveraging TD’s data center expertise, best practices and processes, and our prefabrication capabilities, Phase 2 came in at 16 percent under budget and Phase 3 at 24 percent under budget.
As a bonus, CyrusOne Texas Research Park won the 2022 Building San Antonio Award for Best Industrial Project.
To
In addition to safeguarding the existing occupant’s equipment and protecting the safety of its personnel, TD strategically scheduled all of its crane picks on weekends when the offices were closed.
Construction of new semiconductor wafer fabrication facilities continues, including in Central Texas, with many current facilities expanding to better meet surging global demand.
The semiconductor industry is now established as truly essential, along with farming and oil and gas, with recent chip shortages showing how important a consistent supply is for the global economy. A recent Deloitte report notes that the semiconductor industry is expected to grow 10 percent by the end of 2022 to more than $600 billion, with continued growth in the new year.
“Chips will be even more important across all industries, driven by increasing semiconductor
content in everything from cars to appliances to factories in addition to the usual suspects — computers, data centers and phones,” the report notes.
Construction of new semiconductor wafer fabrication facilities continues, including in Central Texas, with many current facilities expanding to better meet surging global demand. Such facilities produce microcontrollers (MCUs) and microprocessors (MPUs), power management devices, RF transceivers, amplifiers and sensors and more.
TDIndustries’ unique full-scope building expertise served general contractor DPR well for a recent 1.8 million-square-foot manufacturing facility for a confidential client, projected to complete in July 2023. TD supported the project as a cross-collaboration between Process Solutions, Austin Construction, and Controls and Building Automation teams.
The largest portion of the project, which included cleanroom manufacturing space, included the design, manufacturing and prefabrication expertise of TD’s Richardson-based Process Solutions team. The process piping scope for the project includes:
Process exhaust, process piping and UHP piping installation of new cleanroom buildout within existing facility.
Preconstruction, procurement, prefabrication and installation services of various pieces of process utility equipment and PVF including:
» Compressed air, specialty process gases, ultra-high purity water, chemical drains, process exhaust and chemicals.
Materials used include:
» Various grades of stainless-steel pipe and tubing.
» PVDF, CPVC, Polypro and PFA.
» Coated stainless steel, galvanized and FRP ductwork.
For TD’s Austin construction team, the project scope includes:
The installation of an 81,000 lb. make-up air unit with a custom-built vestibule to house all the piping for the new fab space.
Piping systems installation for chilled water, chilled water glycol, heating hot water, condensate and low-pressure clean steam using materials from copper to carbon steel and stainless steel.
air unit and dry coil valve banks.
Installed controls for water systems and VAV boxes outside the clean space.
Developed a particle measuring station for the process water.
Supported specialized clean room instrumentation and complied with site component wiring requirements for stainless steel conduit.
Provided extensive commissioning support.
Built custom frames to install (83) dry cooling coils and associated carbon filters that line the perimeter of the clean space.
Semiconductor manufacturers continue to apply for incentives to further invest in Central Texas projects that could potentially create hundreds of jobs in the region.
Modern technology requires semiconductors to operate; they can be as small as 4 nanometers in size.
Piping from the new make-up air unit provides chilled water to these cooling coils which will serve the new level 100 clean fab.
Finished out existing support rooms for the level 100 clean room fab space.
TD’s Building Automation and Controls team:
Installed controls in the clean space for almost 1,000 fan filter units, the make-up
The largest portion of the project, which included cleanroom manufacturing space, included the design, manufacturing and prefabrication expertise of TD’s Richardson-based Process Solutions team.
Three decades of multifamily experience, strong owner partnerships and a new Englewood, Colorado office are setting the stage for TDIndustries’ Multifamily team to drive growth to serve our customers. Projects in the works include wrap/podium style, garden and high-rise buildings with Embrey, Brinkman Construction, Arco/Murray and more going into 2023 and beyond. Mid-rise Denver Arts District projects like Santa Fe Flats and Santa Fe Lofts are completed and already filling up with eager residents, with more luxury high-rise and design-build plans on the horizon. In addition to Denver, TD’s Multifamily team also serves the Austin and Dallas/Fort Worth markets.
Since Arvada Station in 2011, TD and Embrey have worked as design-assist partners on nine projects, with the three latest — Keene at the District, Hensley at the District, and The Finch including dual plumbing and HVAC scope.
“As we build our team and diversify our types of projects for Colorado, our close relationship with customers like Embrey will sustain our growth,” says Senior Manager of Operations Alex Shipp.
ACTIVE EMBREY PROJECTS INCLUDE:
Banner Health is one of the largest nonprofit hospital systems in the country with 30 acute-care hospitals and multiple healthcare divisions and services. With 50,000-plus employees and growing, it’s the largest private employer in Arizona and serves more than 1 million members in its provider network.
Banner Health offers access to quality care by building and expanding hospitals and health centers throughout the communities it serves. TDIndustries is pleased to support Banner Health in several of its recent Arizona projects, including the Banner Gateway Medical Center Tower expansion and renovation in Gilbert, which will be complete in early 2023.
TD’s heavy design-assist role with the project team, including the owner, general contractor McCarthy Building Companies, architect SmithGroup and others, is a strong example of the innovation, value and strong relationships TD provides for its healthcare customers.
“Our team strives to make what is right for the project, not just cost-saving engineering solutions but the right solutions,” says Ardas Sabuncuyan, P.E., TD Engineering Group Sr. Project and Healthcare Area Manager. “We listen to the perspectives of all stakeholders and believe in transparency of decision-making. We have great chemistry and communication with the project team. Our goal on this project, and every project, is to implement TD’s core values to win back-to-back work from the clients.”
Banner Gateway Medical Center is a designassist project with significant contributions from TD engineering, VDC (Virtual Design &
Construction), preconstruction and construction teams.
The five-story, 310,000-square-foot patient tower project doubles the size of the existing Banner Health campus with the capacity for about 300 new beds. The project also includes a 112,000-square-foot expansion to the diagnostics and treatment building that includes emergency, surgery, imaging, cardiopulmonary and endoscopy departments.
TD’s design-assist role for plumbing and HVAC includes:
Planning, specifications and code compliance review.
Budget guidance and constructability reviews.
Project management and engineering strategies to control budget, schedule and scope.
Drawing production with one model in mind.
Influencing the project design to take advantage of TD’s manufacturing and prefabrication capabilities.
Early design input, allowing teams to get ahead of material orders with long lead times.
Phasing concept developments during design phase to avoid existing hospital shutdown.
Ensuring all collaborators work well together.
TD’s construction role includes:
All the hydronic, plumbing, piping and HVAC for the expansion project.
Upgraded equipment for the new build and future expansion.
Central plant upgrades adding two 1,200-ton chillers, three cooling towers, two condensing water pumps and two chill water pumps.
Cost- and time-saving measures on the project include:
Prefabrication of construction elements including bathroom pods and mechanical and plumbing components.
Project delivery completed in five separate design packages, allowing construction to start before the completion of the design phase.
Simultaneous construction of building expansions on three sides of the hospital.
The project team worked together from the beginning through design, preconstruction, VDC and modeling stages, using one model to inform budget, materials and schedule. Trust is key for the coordination to work six ways between TD engineering and the owner, general contractor, engineer of record, preconstruction and construction.
“We needed to build six-way trust for success,” says Arizona Preconstruction Director Chad Halmrast. “Ardas’s expertise and review of preliminary design concepts helped resolve
The project team developed an A3 report together to determine the best way to upgrade the central unit plant for the current project and future expansion.
Our team strives to make what is right for the project, not just cost-saving engineering solutions but the right solutions.Rendering provided by McCarthy Building Companies, Inc.
At peak construction, TD had 135 employees on-site working in multiple areas concurrently.
Banner Gateway Medical Center is a design-assist project with significant contributions from TD engineering, VDC (Virtual Design & Construction), preconstruction and construction teams.
constructability issues and flagged potential healthcare HVAC code compliance conflicts before construction started, saving everyone time and expense.”
The TD team brought expertise to do the right thing in design to eliminate future issues. That included a 20 percent to 30 percent reduction of airflow volume (cfm) that helped reduce duct sizes, fans, etc. to save money in construction and in efficiencies for the life of the building.
Expedited schedule with concurrent work “The schedule was extremely aggressive—if you didn’t have a plan you were going to be in trouble,” says TD Senior Superintendent Doug Wallace.
The team worked concurrently in every space within the project, operating at a maximum manpower level of 135.
“Fortunately, we had just finished up a similar facility with McCarthy,” Wallace says. “It was a win-win because we had just teamed up and built a Dignity Health project in Chandler, Arizona, that went very well. We were able to take a lot of lessons learned and transfer it to this project.”
Meticulous pull planning and a dedicated TD technician to coordinate materials orders and just-in-time deliveries kept the work on schedule.
One key challenge in expanding an existing facility and upgrading a central plant is working through the moving parts and pieces of keeping a bed tower and operating rooms online as you’re building out the new construction.
“At one point we needed to add a piece of equipment to the central plant,” Wallace says. “We created a temporary chiller by piping in about 800 tons of temporary cooling so there were no disruptions to the facility while we installed the new equipment. We did that on a Saturday and had the facility filled back up and running that night.”
The construction team emphasized transparency and trust as a key component of project success.
“If there’s something that’s preventing us from doing what we do, it’s a very open and candid conversation to help eliminate those issues so we can all be successful,” Wallace says. “If you’ve got relationships where they trust you, they’ll listen and you’ll get things done.”
On the design front, TDIndustries’ more than 150 years of combined design and preconstruction support experience for healthcare projects help our customers mitigate risk, ensure code compliance and constructability, and consider alternative design ideas that can save the
owner expense and maintenance over the life of the building.
“TD’s vast healthcare design and preconstruction expertise improved the quality of this complex project, mitigating future risks to provide the best value,” Sabuncuyan says.
The TD team built a temporary chiller to ensure there were no disruptions to the active hospital during a major central unit plant equipment installation.
When [TD technicians] come out, we know they’re going to do their job and do it correctly.
The manufacturing sector has increased significantly the past five years in Texas, with manufacturing GDP rising 22 percent since 2016, according to the National Association of Manufacturers.
TDIndustries supports that growth with its skilled and experienced Service team, including its long-lasting relationships throughout the Southwest. One client, Allied Electronics, has been a partner with TD for more than 10 years. The relationship started with TD subcontracting on the HVAC and plumbing work for Allied’s building.
Because of TD’s expertise across the life-cycle of a building, TD supplies ongoing maintenance for those systems and provides building automation support at the facility. And when Allied needed a building expansion, TD was there to provide mechanical and plumbing work. From
start to finish, TD helped Allied scale its facility and keep its standards high, all because of the great relationship the TD team built and maintained. And that relationship is strong today, too, because of the high quality and efficiency of the technicians’ work.
“When [TD technicians] come out, we know they’re going to do their job and do it correctly. They know our system, so we don’t have to
bring someone in to train them,” Allied Electronics Facilities Maintenance Manager Rickie Fowler says. “Techs come in, they go right to the location, they communicate well. It’s just a great experience all around.”
The long-standing relationship helped in a pinch when Allied had its board in the office for a meeting and the A/C went out.
“[TD technicians] were out there within 30 minutes and had it up and running about 30 minutes later,” Fowler says. “They’re always Johnny-on-the-spot for us.”
TD also provides service to many manufacturing companies in the food and beverage sector, such as PepsiCo, Coca-Cola, Cargill, DiMare Fresh and Bimbo Bakeries USA. These companies appreciate TD’s specialized technicians who can work on complicated job sites, like those in the food and beverage industry.
For example, as a manufacturer of bread, bagels, buns and more, Bimbo Bakeries USA has specific temperature and humidity parameters it must maintain in its bakery to meet its high quality standards. The bakery has a process chiller that TD technicians have the right expertise to work on, which is critical.
“Having someone that’s here consistently and learns our system and all the little things our system does is probably the most important thing to me,” Bimbo Bakeries USA Plant Engineer Tim Conn says. “You can have the best technician, but if he doesn’t know your system, then it’s tough.”
With its chiller, Bimbo can keep its mixing equipment cool, which allows the company to produce product all day long.
And with planned maintenance also a key focus of TD’s service team, loss of production is minimized because the team addresses potential problems before failure. When equipment failure does occur, which happened recently at Bimbo, quick response times mean the least amount of lost productivity.
“The technicians arrived in the evening and worked through the night into the next day,” Conn says. “They had to beg, borrow and steal to find refrigerant. We put about 800 pounds in the system, and they stayed through the night to make sure things were still up and running.”
These companies appreciate TD’s specialized technicians who can work on complicated job sites, like those in the food and beverage industry.
Detect faults and diagnose repairs Monitor and manage energy usage Track comfort and maintenance targets Proactively address high-impact tasks Prolong the life of your equipment
BrightBlue building analytics platform plugs into existing building systems, analyzes thousands of data points and pinpoints the highest impact performance issues.
Community outreach is core to our purpose at TDIndustries. We invest in our communities every day by building, operating and maintaining hospitals, schools and universities, office buildings, data centers, stadiums, entertainment venues, multifamily homes and more – bringing jobs and critical services to local residents. But it doesn’t stop there. TD and its employeeowners, whom we call Partners, have a long history of giving back to organizations that support our communities and help our citizens thrive.
From school supplies to bus shelters to support for veterans – our shared “labors of love” help bring wellness and security to our families, friends and neighbors. At TD, helping others comes from our hearts – and we couldn’t be more proud or appreciative of the contributions of everyone involved. Check out a few of our community involvement projects in the following pages, and read more about highlighted articles at tdindustries.com/blog
Our Arizona team and their families hoofed it through Downtown Phoenix to raise $5K for the American Heart Association. The team participates in the walk every year.
TD teams up with organization to provide resources to disabled soldiers and to help end veteran suicide. Read more at tdindustries.com/blog.
In Houston, volunteers provide food and relief to the war-torn region.
Partnering with Adapt a Vet, San Antonio team members install central heat, air and repair plumbing and electrical issues in the home of a Vietnam veteran.
Houston Partners build a doghouse for a Citizens for Animal Protection fundraising auction that supports vagrant animals.
TD employee-owners donate generously to United Way and our colleagues in need through internal campaigns each year.
TDIndustries Manufacturing, in coordination with DBIA Southwest, donates materials for Glen Park neighborhood bus shelters so riders can wait comfortably with protection from the weather. Read more at tdindustries.com/blog.
TD’s Partner Resource Groups gather and donate school supplies in Uvalde, Texas, to show our care and support as students and staff prepare for the new school year.
To be a leader in today’s construction industry requires an authentic commitment to diversity and inclusion and an intentional culture shift through education and training.
TDIndustries’ training is foundational to its employee-owned, servant leadership culture, its core values and business success. The company’s diversity and inclusion training includes how to:
Encourage and listen to co-workers’ different points of view;
Have open-minded, respectful discussions in diverse groups;
Value all sources of expertise for a safer, collaborative workplace.
Retention is vital to a company’s success, especially in the construction industry where there is a skilled labor shortage. TDIndustries enjoys significantly lower turnover rates and gains a competitive edge in hiring through a culture of inclusion. Fair treatment and opportunity sound simple but do not come easily. The investment in diver-
sity. inclusion and unconscious bias training allows employees to practice diverse thinking and behaviors to emulate daily in the workplace.
What’s a bias? It’s a tendency, inclination or prejudice toward or against something or someone.
In class, we use the visual of an iceberg. The things below the water are things you wouldn’t know about someone unless you got to know them. We often use the things we see above the water line to make assumptions about things below the water line.
We encourage participants to ask questions first before making assumptions. Asking questions is a great way to encourage two-way communication.
By taking time to stop, think and behave inclusively, we learn to overcome our biases. Biases are often based on stereotypes. Whether positive or negative, such cognitive shortcuts can
result in prejudgments that lead to rash decisions or discriminatory practices.
Each of us has preferences, and each of us has biases. Acknowledging the bias and moving it from unconscious to conscious is the first step in changing behaviors and building organizational inclusivity.
TD’s organizational development/ talent management team developed the curriculum and collaborated with experts to enhance delivery of the in-person training.
“The in-person classes allowed participants to empathize and connect with each other by role playing real-life bias traps or micro-behaviors faced in everyday circumstances,” TDIndustries Director of Inclusion Mark Joseph said. “Leveraging outside expertise helped us present a safe, respectful and effective learning environment based on mutual respect and servant leadership.”
A large part of inclusion is knowing where everyone is in their journey. Collaboration and inclusion framed inclass role play. Interactive videos, group breakout discussions and “connections” questions fostered a way to get to know each other in a nonjudgmental way.
Connections questions include:
Where would you like to travel to and why?
What’s the biggest compliment you have ever received?
Where did you grow up and what is most memorable about it?
For what in life are you grateful?
“It takes a conscious thought to interrupt an unconscious bias.”
Class participants examined their biases by sharing with the group and showing acceptance of co-workers’ culture and experiences.
Of the hundreds of leaders who have completed the training so far, most agreed that examining the origins and impacts of some of their long-held beliefs helped them grow as leaders. Comments included:
“The training helped me realize that though I wasn’t judging or excluding
people, I did not fully include others in the office conversation.”
“The group activities showed how everyone’s contributions lead to open-minded discussions.”
“The facilitators’ enthusiasm, belief in the presentation and energy made it easy to stay engaged and learn.”
At the end of each class, the facilitators asked each participant, “What is one thing you are committing to do to help build a more inclusive environment within your team, department or community?”
This summer, TDIndustries hosted its largest group of interns ever, with 51 college and 39 high school students participating across offices and job sites in Texas, Arizona and Colorado.
From June to August, the interns were provided on-the-job, real-world experiences in areas such as construction, facilities, service, engineering, finance, HR and more.
“The internship at TDIndustries helps the company and the students grow in multiple ways,” says Derek Dostal, senior director of talent acquisition. “The interns are engaged full-time in supporting our teams in real-world tasks and responsibilities that
bring innovative value. Our employee-owners work with the interns daily gaining coaching experience and leadership skills to grow their own careers.”
The college internship program consists of weekly programming related to company culture, safety and industry topics, leadership coaching, as well as training on the importance of inclusion, networking and relationship building. Interns also have the opportunity to participate in one of six group research projects, with the goal of working together to help TD solve a business problem or provide added value to the company.
“I enjoyed working on-site and gaining first-hand experience
Responses to this prompt encouraged an introspective reflection that would lead to a mindset or behavioral change. When employees feel included and believe they are contributing to the company’s mission in a meaningful way, productivity and job satisfaction increase.
ABOUT: Cary Broussard, author of From Cinderella to CEO, began developing customized DE&I curriculum as an adjunct professor at New York University. Together with Dr. Faye Hall Jackson of Tuskegee University, they offer training across industries through CinderellaCEO.com
with a project team – having the opportunity to rotate around various business units – and most importantly interacting with the people who work here,” shared one intern. “Everyone was so willing to answer my questions, give advice, and share their experiences.”
The high school program allows students to gain on-thejob experience working in the trades. In some business units, such as manufacturing, teams worked with their interns to identify an area in the shop that
best suited them, while in other regions, like San Antonio, the interns rotated every two weeks between various trades to learn where students’ skill sets and aptitude shined the most.
“Our interns are the future of TD, and of our industry,” says People Program Manager Meagan Bubela, who leads the internship program. “Their research contributions each year are extraordinary, and it’s amazing how much they accomplish in just a few short months of hands-on training.”
TDIndustries President Graham Moore retired early in 2022 after 42-plus years of leadership. We’d like to share a bit of his wit and wisdom with our community.
A. From a business perspective, and this started with Jack Lowe Jr., it is to build a business plan every year. Drill down to get true objectives and action items to accomplish that plan, then have the discipline to complete the action items.
If you don’t plan your work, you’re going to lose money. No question. If you plan the work, you’re giving yourself the opportunity to make budget. If you want to set record operating incomes, go inspire your people. Give them a plan and then inspire your people, and they will knock it out of the park for you.
Q. WHAT’S BEEN THE MOST MEANINGFUL PART OF YOUR CAREER JOURNEY?
A. The way we built the Houston team is we hired pretty much right out of school. And the most rewarding thing is getting to watch those you hired develop their careers, develop their lives. Ronell [Peters] and I have worked together for 33 years, Nikki [Morgan] 24 years and Tasos [Banos] for 23 years. I got to watch them literally grow up, get married, have families, and their careers just blossomed into all of these things.
Watching all of these lives evolve in front of you is by far the most rewarding thing.
A. You can take a construction career in whatever direction you want to. You can master a craft if you want to. But you also have the opportunity to crosstrain, learn different things, or climb up that corporate ladder to be a vice president or even more.
But there’s something else. What other job is there that you can take
your kids and grandkids around a great city and tell them that you helped build these monuments that are going to be here far after we are? It’s just different. We get to participate in building the monuments of the communities we live in. How does it get any better than that?
A. The thing that I would tell everybody is to do the very best at the job you have. I have had many different jobs at TD. And I applied for one, and that was Assistant Project Manager when I walked in the door. And then my boss asked me, “Hey, would you do this or do that?” And then Harold [MacDowell] asked me, “Can you add this and that?” And so, it just evolves. When you’re excelling at what you do, the opportunities are going to come.
They may take you directions that you wouldn’t have thought. If you had told me 40 years ago, “Did you know you’ll have run Houston for 20 years and been responsible for Phoenix and then responsible for Dallas, Fort Worth, Austin and San Antonio?” I would say, “Are you crazy? What’s wrong with you? I’m the best Senior Project Manager we’ve got; I’m on the top of my game. This is it.”
And so, I tell everybody: Really make sure you’re giving the job you’ve got the very best you have. And the rest will fall into place.
Editor’s Note: TDIndustries is grateful for Graham Moore’s 42-plus years of contributions, leadership and friendship. We wish for you what you have given us — all the best! Read the full interview on LinkedIn
BrightBlue™ is TD’s automated fault detection and diagnostics solution. It optimizes commercial building systems’ reliability and performance to conserve energy and resources, ensure occupant comfort and extend equipment life. It’s backed by TD’s 75-plus years of engineering, construction, technology and building operations expertise.
The skilled labor shortage affects facility owners and operators everywhere.
TD’s Senior VP of Facilities Brian Lillard shares insights and solutions to help the industry weather the storm and inspire tomorrow’s trades leaders in IFMA’s September/October 2022 FMJ magazine.
Houston First Corp. continues to lead the charge in building sustainability as the George R. Brown Convention Center (GRB) this year achieved its first-ever LEED Gold certification from the U.S. Green Building Council. TDIndustries is proud of our 19-plus years of Service and Facilities support throughout their journey.
Editor: Donna Stokes donna.stokes@tdindustries.com
The Robert K. Greenleaf Center for Servant Leadership at Seton Hall University recognizes high-profile individuals and organizations who have demonstrated outstanding servant leadership. The inaugural 2022 Hall of Fame inductees include Jack Lowe Jr., Chairman Emeritus of TDIndustries, as a Legacy Honor, and TDIndustries as a Servant-Led Organization.
Media Contact: Phylissia Clark phylissia.clark@tdindustries.com
TDIndustries Headquarters: 13850 Diplomat Drive, Dallas, TX USA 75234-8849 • 972-888-9500