
8 minute read
Clinical trial monitoring goes mobile to help with COVID-19
Clinical trial monitoring goes mobile to help with COVID-19
Quick-thinking engineers at Vaisala have enabled a US-based drug manufacturer to conduct clinical trials in mobile units, which had been almost unthinkable before COVID-19.
In summer 2020, a drug manufacturer initiated an innovative project to conduct clinical trials on potential treatments for elderly COVID-19 patients. Long-term care facilities have been especially vulnerable to COVID-19 outbreaks since the beginning of the pandemic, with some sources estimating that up to 40 per cent of novel coronavirus-related deaths in the US occur in those facilities.
To respond to this situation and ensure that elderly people living in long-term care were included in research into treating the virus, a team of clinical development, clinical supply and engineering experts came up with the idea of converting recreational vehicles (RVs) into mobile research units. Along with the mobile units, trailer trucks were customised to transport clinical research supplies. Clinical trials are one of the most complex and challenging ventures in science, and the data they produce must be painstakingly collected and protected, otherwise crucial research can be lost. Laboratories that contain samples and other high-value research assets require storage environments that are carefully maintained in specified conditions. Records of those conditions must be complete and accurate.
The drug manufacturer conducting this clinical trial was already using Vaisala’s viewLinc system to monitor temperature, humidity and other parameters in several cGMP environments at their facility. The question was: could the viewLinc system’s data loggers be used in the new mobile research units to send monitoring data back to their existing viewLinc system and send alerts for excursions? And more importantly, could Vaisala provide such a solution quickly? Mobilising a monitoring system The drug manufacturer contacted Vaisala. They needed monitoring in the refrigerators and freezers mounted inside the RVs which had been newly outfitted as mobile research units. The RVs would be travelling the country to perform clinical
Conducting clinical trials in mobile units was almost unthinkable before COVID-19. But with the help of the VaiNet wireless monitoring technology and Vaisala’s quickthinking project engineers, the drug manufacturer was able to put its mobile research units on the road within 30 days.
trials in long-term care and nursing home facilities. However, due to the pandemic and the vulnerability of the residents, the implementation timeline for the monitoring system in the mobile research units was only a few weeks.
Because the fridges and freezers would be opened twenty times per day or more, it was critical to record temperatures inside the fridges and freezers every few minutes to ensure proper conditions were maintained. The temperature data history also needed to be automated, accurate, complete and easily reportable. Ideally, the data would reside in their existing viewLinc monitoring system, which was validated. Most importantly, if any temperature excursions occurred, remote staff had to be alerted immediately by email or text message.
Leveraging modern communication technology Vaisala project engineers used simple, off-the-shelf modems to enable several VaiNet AP10 network access devices to communicate from the mobile laboratories. This was achieved without a VPN to connect the access points in the RVs to the viewLinc server. This method requires only a modem and the inherent communication capabilities of the AP10.
The wireless RFL100 temperature and humidity data loggers use Vaisala’s proprietary VaiNet wireless technology. The modulation technique used by VaiNet is based on LoRa chirp spread spectrum. LoRa (Long Range) is a low-power, wide-area network (LPWAN) protocol.
VaiNet’s indoor signal range typically exceeds 100 m (300 ft) and can easily penetrate walls and other barriers. Outdoors, the signal range is much higher. For instance, if the research staff were to take the RFL 100 data loggers outside the mobile labs, they could go several hundred feet from the RV and maintain connectivity to the AP10 network device. The AP10 access point functions as a base station for the VaiNet wireless data loggers.
Low power, simple and fast In the application, the RFL100 temperature probes were placed inside fridges and freezers. The AP10 was connected by Ethernet cable that included Power over Ethernet (PoE) to a network switch inside the RV. A typical PoE network switch provides roughly 48 to 50 volts along with network connectivity. This eliminated the need for DC power adapters for the AP10 network access devices. A 4G modem, which was also PoE-capable, was used. This allowed only one outlet to power the monitoring system; the network switch uses a power outlet and provides power to both the AP10 and the modem via PoE. However, all devices are equipped with power adapters, and if needed, the AP10 could connect directly to the modem.
The modem was used for communicating with the AP10, but also provided local internet access at a computer workstation inside the RV. The advantage to using a 3G/4G modem with the AP10 is that the AP10 uses an extremely low amount of data bandwidth. Although each AP10 can host up to 32 RFL100 data loggers, there is only a small amount of data going through the wireless modem, using very little bandwidth. Since cellular modem charges are based upon usage, this was a cost-effective solution. The modem communicates to a cell tower and allows the data to be sent over the Internet to the validated viewLinc server.
Stronger together The mobile research units created in 2020 are currently deployed to COVID-19 outbreaks at facilities across the US. This clinical trial was the first of its kind and a steep learning curve for the many scientists, project managers and engineers who worked to implement it. In a time when so many are isolated, few are as isolated or vulnerable as people living in nursing homes and long-term care. Vaisala was proud to provide a solution for a research organisation endeavouring to help in an urgent situation.
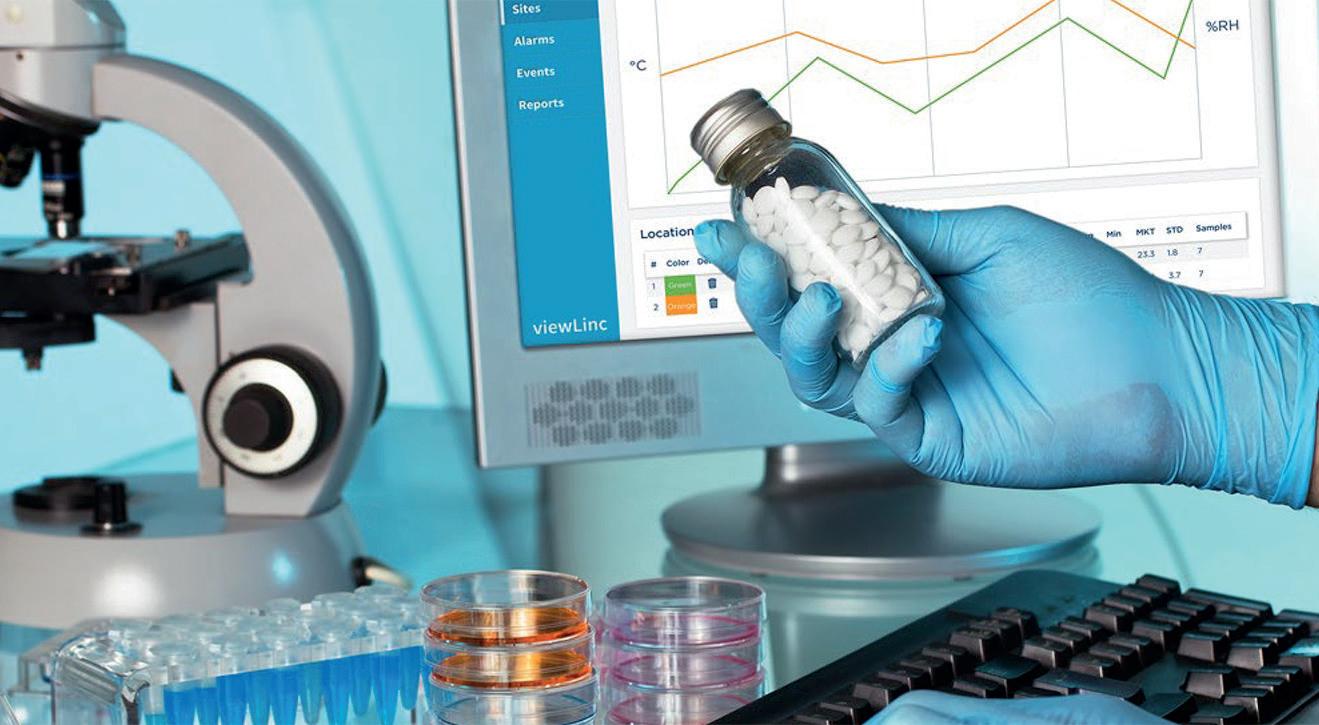
Medilink UK has launched an International Resource service to help companies identify international markets, grow their export capabilities and de-risk international expansion.
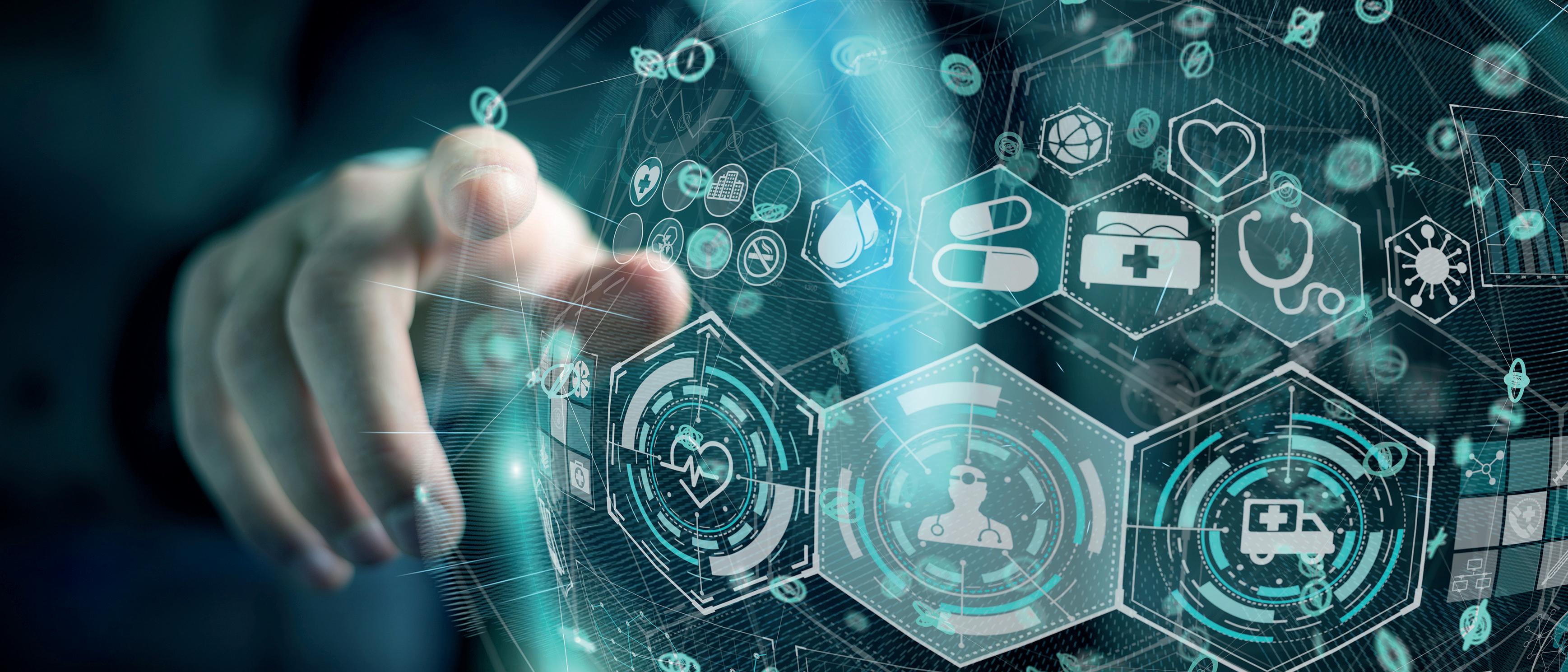
Their team of international specialists can work with you to understand the challenges that your business faces and help complement your export team and strategy. This costeffective and low-risk additional resource can be used for projects ranging in size and scope, or for more long-term cover and additional capacity, for example maternity, absence or sickness cover.
Typical projects may include:
l Market identification and research l Distributor assessment l International marketing review l Exhibition participation support l Board or investment strategy l International trade training l Sales and partnership agreements Medilink’s International Advisors have over 50 years’ experience working with healthcare technology and life science businesses and have supported a huge variety of companies over the years. They have an extensive network of professionals from across the world, with specific expertise in Europe, Africa and the Middle East. The team will use their overseas market knowledge and expertise, supplemented by refined research techniques, to assist your organisation’s international trade goals whether you are a new or experienced exporter.
There is currently regional funding spread throughout the UK for international development, and as such your project with Medilink’s International Team could be subsidised by up to 60 per cent.
To discuss your company’s needs and requirements, and any potential funding routes as part of a free and personalised project-scoping exercise, please contact the team on the details below.
Medilink also has an extensive international healthcare event calendar, supporting UK companies to reach their exporting goals in markets including the Middle East, Germany, the US, Thailand and South Africa. They offer cost-effective exhibition stand packages and a range of services designed to help you get the most out of your exhibiting experience.
For further information, get in touch with the team on: Email: international@medilink.co.uk Tel: 0114 232 9272
PHARMASEAL’s Engility platform selected by US medical device company
PHARMASEAL, a provider of clinical trial management and governance solutions, has secured its first Medical Device customer – an award-winning US-based company providing ultrasound technology, which selected PHARMASEAL’s Engility Trial Management Platform following review of several clinical trial management systems (CTMS).
Engility provides users with a higher level of productivity by allowing clinical teams to operate with one single system. Ultimately it saves time on setup, implementation, user training and validation. This allows better, more integrated workflows and a consistent user experience across both capabilities.
The platform simplifies the management and control of clinical trials for biopharmaceutical, clinical research organisations and medical device companies. It has a combined CTMS and eTMF capability offering a simplified, cost-effective process for managing, tracking and storing documents within one system. For customers who have not invested in CTMS or eTMF technology, or are unhappy with their incumbent technology, this development eliminates the need for investing in two separate systems and having to integrate them, which can be complex. The platform utilises advanced engineering, offering enterprise management with rapid deployment, has a simple intuitive user interface and integrates easily with other eClinical applications to optimise clinical governance and trial oversight.
PHARMASEAL wants to give customers increased control of their clinical trials and product development. The company has applied industry expertise, innovative thinking and advanced automation to build and operate an integrated enterprise platform which allows biopharmaceutical and medical device companies to manage all of their clinical trials effectively. They share a vision with innovative companies to simplify and unify clinical trial governance.
BresMed’s new global HQ at Steel City House in Sheffield is the heart of the company’s worldwide operation. Commenting on the move, CEO Nic Brereton said: “I am so proud to be expanding BresMed to these premium “This news is a great start to the year for premises in the city. The building very much PHARMASEAL. We are delighted that Engility fits with our brand – it’s iconic with a quirky has been selected and licensed to support feel and, like us, it dares to be different.” its first medical device customer to improve The company has come a long way since Nic moved into a one-person office in the city many years ago, adding: “Actually, it was more a cupboard! However, it helped me launch the business.” the management and control of their device trials. Furthermore, this will allow us to work with more global medical device companies who have expressed an interest in Engility, allowing for smarter management and execution of medical device clinical trials.
We have the vision to create smarter technologies for the improvement of human health and we are excited to see what possibilities emerge from this collaboration for transforming the future of healthcare.”
Daljit Cheema
Founder and CEO
PHARMASEAL
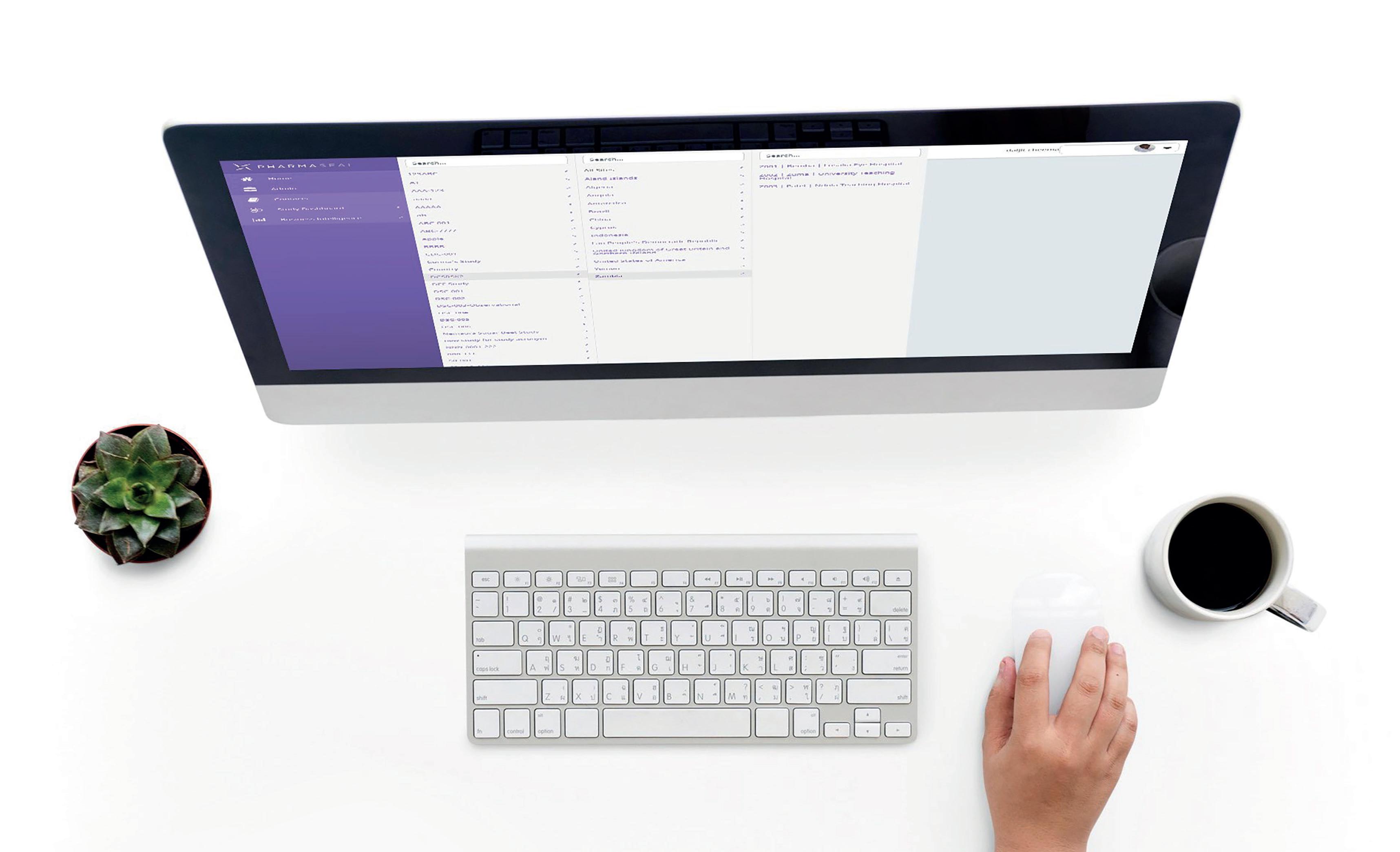