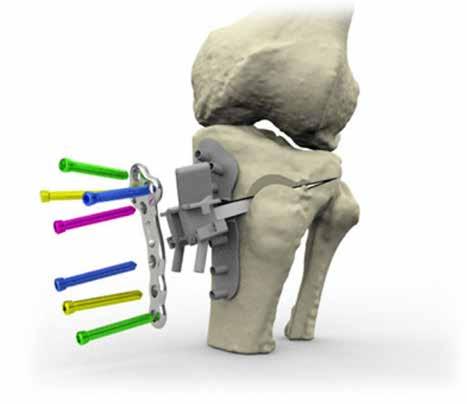
2 minute read
Customised knee implant pioneered by TOKA®, Accelerate and Cardiff University Biomechanics Research Facility
Osteoarthritis is a highly prevalent disease affecting nearly nine million people in the UK causing pain and mobility issues. Bath based med tech company 3DMP and its subsidiary based at Cardiff Medicentre specialise in developing surgical planning software and digital healthcare applications.
3DMP have pioneered a revolutionary customised surgical implant technique to deliver a novel solution for knee osteoarthritis. The TOKA® device combines 3D printing and data-imaging technologies to create a customised knee implant device. TOKA® is a precision engineered, patient specific device for High Tibial Osteotomy (HTO) surgery. HTO is a common ‘knee preserving’ surgery particularly indicated for younger (40 to 65 years) patients as alternative to partial or total knee replacement.
A new Accelerate funded project is enabling Cardiff University Musculoskeletal Biomechanics Research facility to apply its unique research equipment and expertise to better understand the individual requirements of each patient and create a more personalised implant. Currently TOKA® offers device personalisation based on individual patient anatomy, matching their geometry (shape). Patient outcomes are still dependent on the accuracy of the procedure, and the current solution is a onesize-fits-all approach. HTO surgery is successful if it can preserve the knee joint by re-aligning the tibia bone and redistributing the painful high-pressure regions within the knee. The precision of each device can be improved by also meeting the individual biomechanical loading requirements of each patient. The Accelerate funded research collaboration with Cardiff University is addressing this problem by providing new biomechanical data to inform TOKA®’s bespoke surgical planning tool. The research team are collaborating to collect biomechanical and knee joint imaging data both pre- and post-surgery from patient volunteers scheduled for HTO surgery at Cardiff and Vale Orthopaedic Centre (Cardiff & Vale University Health Board). The resulting data will be used to alter existing surgical planning software, create custom-made devices and improve 3D planning tools for surgeons. Ultimately the collaboration will support the surgeon and offer the patient a much better surgical outcome and a faster recovery time.
The Musculoskeletal Biomechanics and Bioengineering facility (MSKBRF) based in Cardiff University School of Engineering is a world class, integrated, state of the art human movement research centre focussed on biomechanics and musculoskeletal disease. The facility is one of only a few locations globally with bi-plane fluoroscopy equipment able to create highspeed 2D video X-ray images. These images in combination with 3D models created from 3D imaging (CT or MRI) can directly measure the position and orientation of bones during different activities. This information is invaluable to be able to understand the effects of disease and determine the efficacy of surgical interventions.
The Accelerate support programme was established to facilitate and speed up the translational pipeline from the identification of healthcare needs, through to the delivery of evidence-based innovation. Accelerate is part funded by the European Regional Development Fund through the Welsh Government and focuses on the delivery of innovative healthcare solutions driven by expert collaborations between clinicians, industry, academia and the third sector. The Cardiff University Innovation Accelerator is one of four key partners, the others being the Life Sciences Hub, the Assistive Technology Innovation Centre ATiC (University of Wales, Trinity St David) and the Healthcare Technology Centre (Swansea University). The resources at the MSKBRF are available to clinicians, sports teams and businesses requiring biomechanical, clinical or physiological data. Please get in touch to view or book the facility.