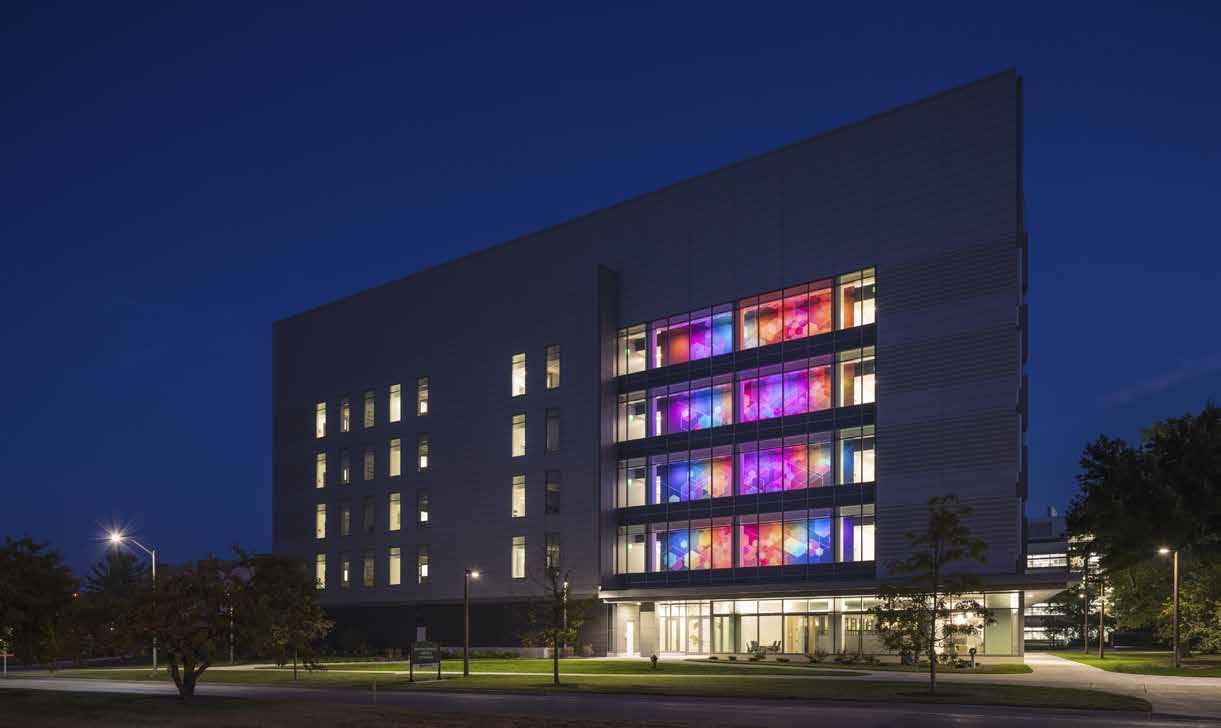
19 minute read
ESD Construction & Design Awards 2020
The recipients of the 2020 ESD Construction & Design Awards are diverse in their project focus, but singular in their expertise to use creativity, modern technology and stellar engineering teamwork to create impressive foundations for research, business, and development.
Evaluated by an impartial panel of industry judges, the Awards are among the premier recognitions awarded to members of the construction industry and their projects. These awards are unique in that they honor the three primary members of the building team—owners, designers and constructors—and recognize outstanding achievement and innovative use of technology. The awards were conceived 46 years ago to encourage elevation of the standard of practice in the construction industry.
OWNER: Michigan State University DESIGNER: SmithGroup & Ellenzweig Contributing Designer CONTRACTOR: Clark Rockford Joint Venture
The Michigan State University (MSU) Interdisciplinary Science & Technology Building (ISTB) is a biomedical research building developed by MSU to support their investment in the Global Impact Initiative (GIi) to recruit more than 100 new faculty investigators. The GIi will help accelerate finding solutions to the recognized Grand Challenges of Engineering and allow MSU to aggressively pursue big ideas, innovation, and global impact.
MSU elected to repurpose the design of the recently completed Grand Rapids Research Center (GRRC) to this site on campus. This new 165,589-ft² modern building— designed for interdisciplinary research and technology— consists of a wet bench and computational research space; research support space such as animal care and imaging; and offices, conference, and common areas to foster collaboration.
The facility is configured as a seven-story building above ground with six occupied floors and a seventh floor mechanical penthouse. The basic organization of the building was conceived with carefully zoned building blocks to support the primary goal of the project: a research block consisting of laboratory and lab support spaces in a 1:1 ratio, with a rodent animal facility on the sixth level. and a parallel office block, which includes offices for the principal investigators and administrative support staff. The two blocks are joined by a sky-lit common atrium space with horizontal and vertical connections providing natural light to the researcher write-up areas and open office administrative spaces.
The MSU, Clark Rockford. and SmithGroup teams worked collaboratively as a single team from project inception through occupancy to assure that the stated construction budget of $73 million and the target schedule were met successfully.
For MSU, speed to market was paramount, which made an aggressive schedule a major driver. This
brought the need for early collaboration and innovative delivery methods to get in the ground quickly. The first challenge was to replace the parking for the adjacent clinic operations that was being removed due to the new building. To expedite, SmithGroup worked directly with Clark Rockford for an innovative delivery approach, which culminated in providing a 3D model of the grading directly to subcontractors. Design and documentation efforts were completed in six months, compared to the 13 months required for the GRRC. The ISTB was completed on time and on budget.
The project is a model of cost efficiency. ISTB translated the successful GRRC design from a dense urban context to a major university campus with modest refinements to the ground floor in response to the academic setting and on the research floors and vivarium to address specific research requirements. The ISTB refinements have resulted in a 55% efficient building, including the atrium.
A key factor in the project was meeting energy efficiency goals. Prior to this project, Michigan State University embarked on a path to reduce its greenhouse gas (GHGs) by 45% by this year. As part of this effort. MSU has made significant progress in lowering its buildings· energy use intensity (EUI). Also. code-related (ASHRAE) and legislated (LEED) mandates required levels of energy efficiency as well.
Therefore, one of the biggest challenges for the design team was to create an energy efficient building within budget while also considering the type of building and activities occurring within the facility. Research laboratories are some of the most energy-intense facilities in the world, especially facilities with live animals. Demand ventilation, digital building controls, variable frequency drives, LED lighting and daylight harvesting, and a high-performance building envelope are strategies that helped to achieve the sustainability


goals while meeting the intended function. Equipment was considered not only for its initial costs but for life-cycle costs that have reasonable savings with long-term operations.
With these energy goals established at the forefront of the project, the design team knew that the GRRC, and therefore the ISTB, had to be highly efficient buildings with low carbon footprints, and they were tasked with reducing energy consumption to 30% better than what the code mandates. The design team knew that they had to design a system that met all energy requirements as well as the construction budget. Familiar elements had to be used in innovative ways.
Throughout the design of ISTB, the team was conscious of interior materials, choosing those that have the least impact on indoor air quality. They also maximized the ability to rely on natural light with extensive curtain wall and atrium skylights, designed to maximize light and minimize energy loss. The building’s electrical design includes sophisticated lighting controls to minimize electrical consumption. The ISTB is projected to be 72% carbon neutral.
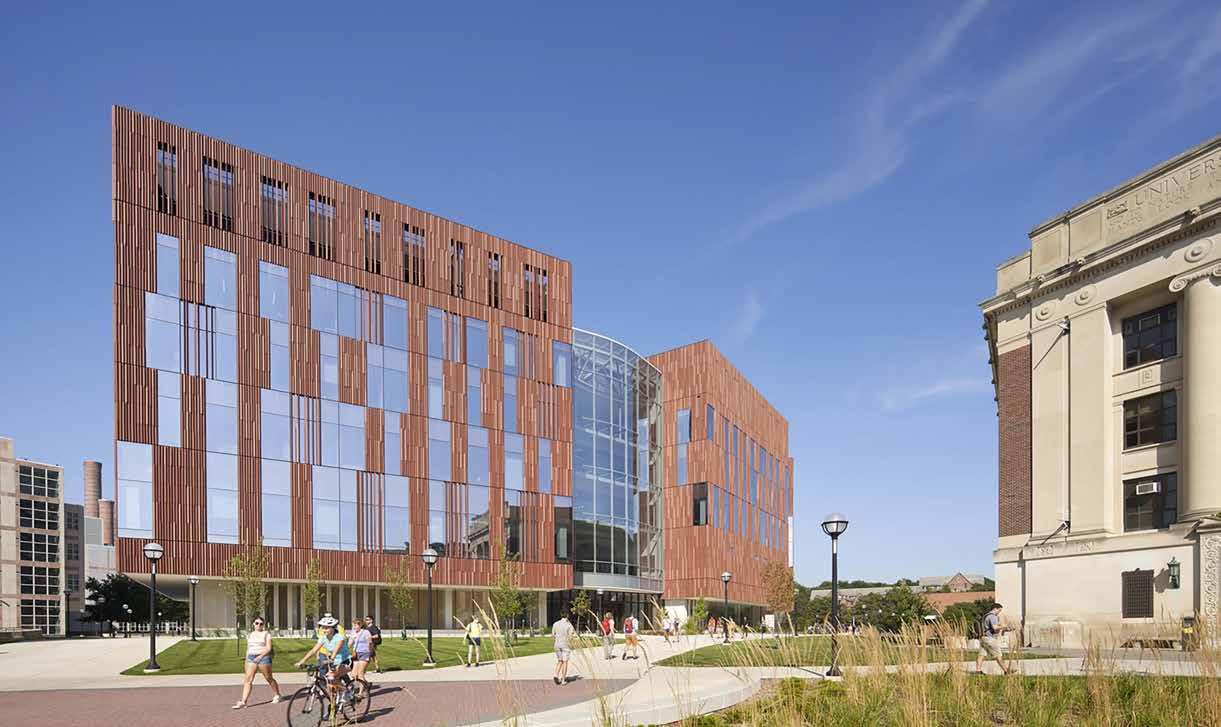
OWNER: Regents of the University of Michigan DESIGNER: SmithGroup & Ennead Architects CONTRACTOR: Barton Malow
The University of Michigan identified the need for an advanced integrated science facility. Ennead Architects developed a sophisticated and unique building exterior. SmithGroup outlined a cutting-edge interior design for research labs, classrooms, and museum space. Early on, it was evident that the details of the facade required special attention. The team developed a procurement plan that helped control costs and keep the project under budget while delivering a one-of-a-kind design.
Only three manufacturers in the world have the capability to construct the large-format curved and flat glass specified in the unique design. The curved glass was procured from Barcelona, Spain. The selected 77,000 ft² of terra cotta was sourced from Munich, Germany. Incorporating these international vendors required a high level of coordination among all team members to ensure both quality and efficiency.
Multiple cross-continental travels took place over a one-year period. Representatives from SmithGroup, Barton Malow, Ennead, and the University were present for each trip to Spain and Germany to review early samples and mock-ups for material selections and then to inspect the glass and terra cotta. Over 100 large-format glass panels of various dimensions and 38,500 individual terra cotta tile shapes were analyzed. The team made over ten trips abroad to make sure the specs were met and that no defects were present. The components were then shipped to a prefabrication facility in Indianapolis where they were inspected and approved by the same quality control team of Barton Malow, SmithGroup, and Ennead, as well as a third-party forensic facade expert. The materials were then assembled and transferred to the site for construction.
Every component arrived for installation without issue. This proactive approach to quality control and the ongoing communication among all team members ensured that the expectations for quality and schedule were met through every phase and at every location.
The BSB team faced its share of project challenges. In utilizing specialty building materials from across
the globe and incorporating complicated interior finishes amid an active college campus. it was imperative that the project team remain on the same page from project start to finish. With a cohesive approach, the team remained on schedule and under budget at $261 million and successfully completed a world-class interactive space to learn, explore, and experience science at every level.
While the facade presents the Biological Sciences Building with a unique identity on the University of Michigan’s campus, it is what’s housed inside that makes the BSB stand out among other academic facilities across the country. Within the three towers, the building’s spaces are woven together to offer its visitors a new look into the world of science. School children are welcomed by giant mastodons where they learn about the history of our world in the Natural History Museum. Undergraduate students frequent the building for classes that offer an active-learning experience. World-class researchers accompanied by graduate students conduct studies and exploration of many different disciplines from neuroscience to paleontology.
Developing the plans for BSB required executing multiple project types into one building. In addition to the highly functional wet-bench research laboratories, interactive classrooms, and museum spaces, it was important to create a visually engaging environment for all occupants and visitors.
The complexity of the building comes from the multitude of uses and the constraints that come from designing in a pre-existing campus where chilled water and steam are produced in district plants. The frog rooms were designed to operate at a room setpoint between 54 ºF and 77 ºF, which couldn’t be achieved year round with plant-chilled water. A booster chiller was required to create lower temperature water to meet the setpoint requirements of those users. For frog and aquatic rooms, controls were installed that could increase ventilation based on the need to dehumidify. Insect-proof grilles and door seals were required for rooms that house insects.


Safety during construction was a key factor. Shoehorned between other educational facilities meant workers had to be cognizant about student and pedestrian traffic. It’s estimated that 10,000 people passed near the site each day. Deliveries were also a challenge throughout the project. Noting this, the project team had to be vigilant about maintaining a safe, secure border, and it did so by working closely with U-M to implement a coordination plan to ensure student and staff safety, and minimize interruption to the surrounding campus. Internally, every worker was required to go through a 90-minute orientation that detailed the scope of the project and reinforced key safety directives prior to entering the job site.
Environmental consciousness was also important. With occasional flooding in the area and the regional stormwater detention basin below the adjacent Palmer Drive parking structures at capacity. The site goal was no increase in stormwater flow for all storms up to and including the 100-year design storm of 5.11 in., which exceeded the University’s stormwater treatment requirements. The solution addresses an increase of approximately 17% impervious surface relative to previous conditions for both water quality and water quantity. For water quantity control, new underground stormwater infiltration systems were constructed in the new courtyard north of the proposed BSB building and below the primary campus walkway south of the building. These systems consist of prefabricated chambers in a drainage aggregate base and backfill that provides approximately 26,000 ft³ of volume storage. The existing soils below the underground detention systems have high infiltration rates. allowing the increased stormwater runoff to naturally infiltrate and thereby reducing the overall runoff volume from the site by over 5,000 ft³ during a two-year rain event and over 14,000 ft³ during a 100-year rain event.
Between the energy conservation measures and many other sustainable features, the building obtained LEED Gold Certification.
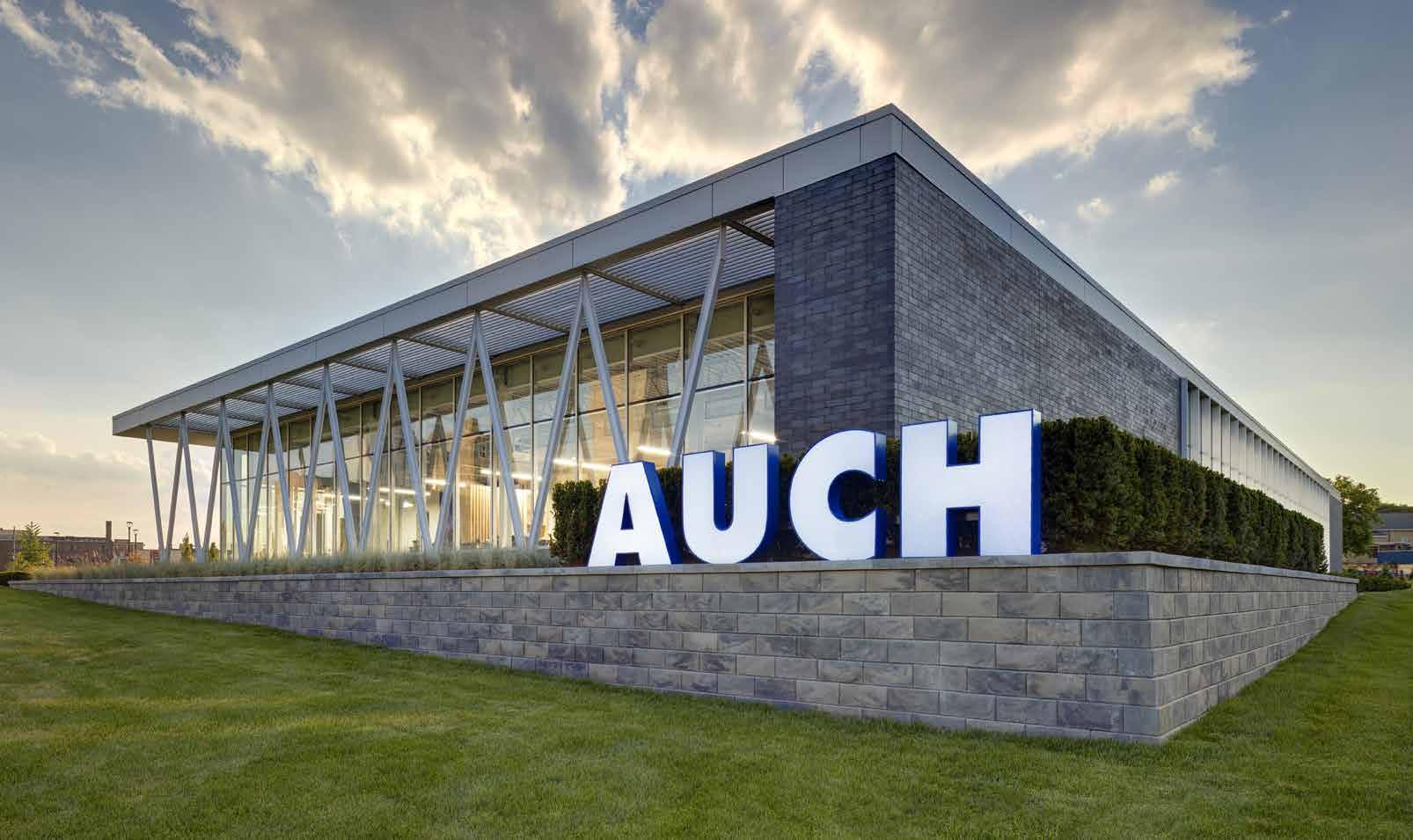
AUCH Construction New Headquarters
OWNER: AUCH Construction DESIGNER: HED CONTRACTOR: AUCH Construction
The AUCH Headquarters building project is a model of integrated project delivery. In this project, the owner, contractor, and architect worked together in seamless and continually dynamic interactions to deliver a building that, more than a headquarters, represents the aspirations of the company and community.
To kick off the project, AUCH evoked its 110-year history and its purpose and commitment to deliver a landmark building and a new kind of workplace to serve its next generation of construction leadership. As a well-known, dedicated member of the community, AUCH purchased a long vacant RACER Trust brownfield and committed itself to developing it into a prominent gateway site and catalyst for future development in the city.
The new 20,000-ft² AUCH Construction Headquarters leverages AUCH’s desire to promote a more collaborative, interactive workplace culture with their need for a new facility that contributes to the revitalization and renewal of downtown Pontiac.
The building celebrates construction and the ability of architecture to make basic materials beautiful. The raw materials of construction are on candid display throughout the building, ranging from the aggregate concrete floor in the corridors to the metal transparent scrim ceiling panels in the lobby. Construction is elevated to the level of craft and artistry at moments throughout the building, such as the development of the wood feature wall in the lobby and the sunshade and truss composition of the south facade.
AUCH believes in environmentally friendly construction and, therefore, decided to incorporate the LEED principles of building. During design it was determined that the project was to meet or exceed LEED Silver guidelines. To help achieve these guidelines the following was incorporated in the building: % Material/ trash sorting so items can be recycled % Recycled materials were specified and installed (curtain wall materials, gypsum materials, FSC woods, carpets, ceiling tiles)
Low-VOC materials were specified and installed Special glass systems (coatings were installed on surfaces 2 and 4 of the exterior glass) Energy efficient HVAC systems (VRF system with a make-up air unit was used) Lighting controls systems and daylight harvesting systems were used Energy monitoring systems were incorporated
This project was completed on budget and on schedule. Even though AUCH is a well-known builder experienced in construction schedules, the project fell into the category of “the design and construction needs to be completed ASAP.” The company needed to ensure the entire project was completed by April 2018 so they could move in May 2018, before the summer construction crunch season. Their project could not affect their clients’ needs. AUCH determined a 12-month permitting, bidding, construction, and move-in schedule was needed. The construction schedule alone was concentrated to only 10 months. This was a tall order for a 4-acre brownfield site with a 20,000-ft² building.
To ensure that the project was completed on time, activities such as pre-ordering of materials directly from the manufacturer, team-approached sequencing schedules, and manpower juggling were required.
In addition, the project team understood the importance of making safety everyone’s business. Trade workers were aware of their individual responsibilities; they were part of creating a culture of safety where people look out for one another. This approach resulted in another safe project with 0 incidents on-site, 0 days lost on-site, and a DART Rate of 0.
This project generated significant interest in the community due to its prominent location and the high

profile attention it received. AUCH’s headquarters was not to be just another construction company’s office building. It needed to tell a story through different construction techniques and products while helping serve the needs of the Pontiac community. It would be used as an educational tool for students, provide a meeting place for local professional groups, and serve as an active location for construction-related groups. AUCH employed Pontiac residents as apprentices, led building tours, and has hosted presentations to groups from various colleges, universities, and professional groups since opening.

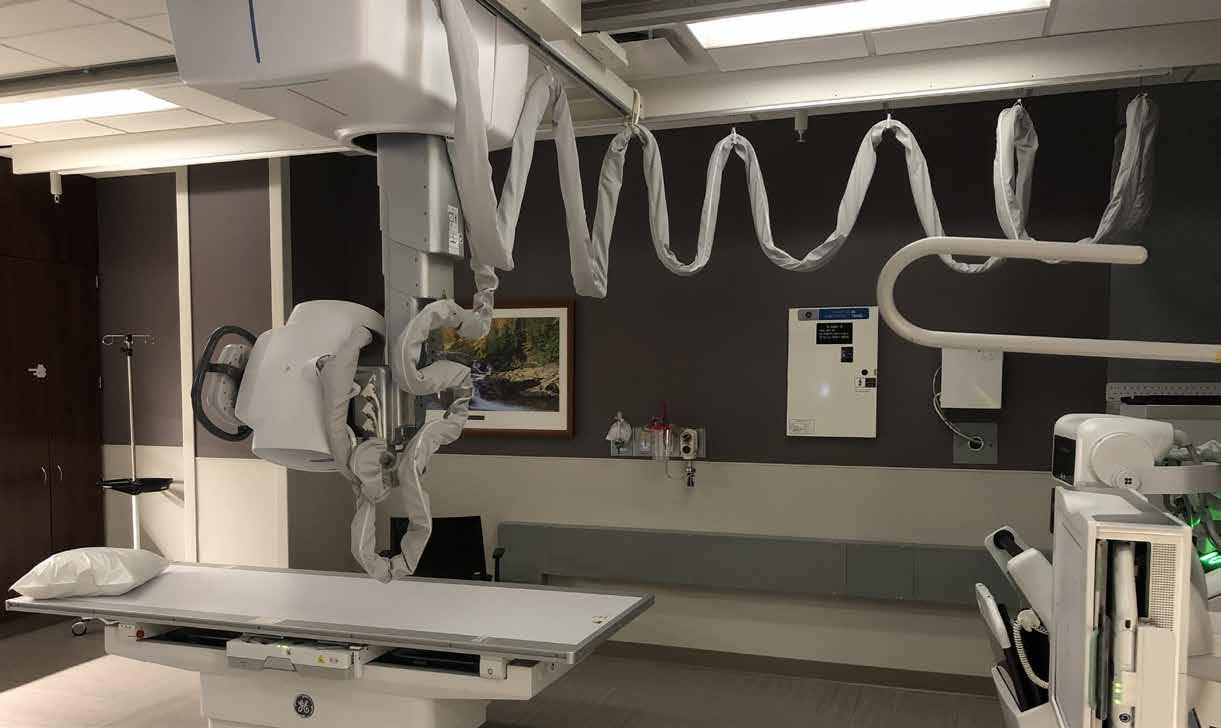
OWNER: Beaumont Health DESIGNER: FreemanWhite and HED CONTRACTOR: Barton Malow
Beaumont Hospital Royal Oak Emergency Center is the busiest Emergency Center in Michigan and one of the busiest in the country. Beaumont Health, HED, and Barton Malow developed, designed and constructed an addition and renovation of the new Emergency Center that improves the patient experience and meets growing community needs. The project was a multiphase 100,000-ft² expansion on the west side of campus with a roof-top helipad, and subsequent 50,000-ft² renovations to double the size of the existing emergency department. The project comprised three major phases.
Logistics of the project were complicated. New work involved rerouting many key underground utilities. Additionally, the new expansion area required the existing helipad to be relocated, encroached on the existing ambulance bay, and disrupted the main employee entrance. Several mini-phases were required, and a good deal of temporary work was necessary to keep the existing ED operational, the ambulance entrance accessible, and the helipad in use.
The collaborative efforts of everyone on the team culminated in a successful project that was completed on time and on budget.
The Emergency Center Expansion project was completed on budget. Early partnerships with major mechanical and electrical design assist contractors also helped in the budgeting process.
Safety was at the forefront of the project. Collaborative engagement in site logistics planning and shutdown coordination was critical to the safety and success of the project. Early on, during schematic design development, Barton Mallow provided preliminary site logistics, prior to going to bid. The team partnered with Beaumont Health to create the best plan for routing patients and staff, traffic, and parking. The City of Royal Oak was also engaged early in the process to ensure they understood the plan, particularly for ambulance traffic. Ultimately, the team maintained 15 phases of patient and staff traffic routing while building adjacent to the occupied Emergency Center and throughout phased renovations.
The Beaumont project included a pandemic suite, a group of exam rooms designed to be a large negative pressure area. In the event of an infectious disease outbreak, Beaumont can quarantine a large number of rooms in one area. This pandemic suite included a unique exhaust fan dedicated to the area, specific locking sequence for doors that are tied into the security system, and a unique sequence of controls.
The project took the environment into consideration. The team recycled scrap metal and other materials on-site throughout construction. The team altered the campus detention pond, making it deeper and flow slower to the Oakland County Drain, and planted trees around the detention pond.
In addition, with the comfort of patients and families in mind, Beaumont partnered with the Detroit Zoo to provide animal-themed artwork and photographs for the Pediatric Emergency Center, including: % Photos with different animal themes in the rooms % Fun facts about the animals % A wall print of zoo animals in the waiting room of the pediatric area

Focused on serving the community, this significant expansion and renovation project doubled the size of one of the most visited emergency centers in the country and the only level-1 Trauma Center in Oakland and Macomb Counties. Additionally, the expanded and renovated Emergency Center was recently awarded a $21 million donation to meet the continuing needs of emergency medicine at Royal Oak.



Frank Rewold and Sons Corporate Headquarters
OWNER: Frank Rewold and Son Inc. DESIGNER: Auger Klein Aller Architects Inc. CONTRACTOR: Frank Rewold and Son Inc.
Frank Rewold and Sons, Inc. (FRS), a 100-year-old Rochester-based business, found themselves in need of a new headquarters. They continued their dedication to the community of Rochester by developing four acres of downtown real estate that had remained undeveloped due to environmental contaminants from past industrial uses, geotechnical issues, ongoing third-party liability responsibilities, and land-use limitations. There, they built a new 49,000-ft² leading-edge office building overlooking the scenic Paint Creek.
Safety was the highest concern for the construction team. Strict safety procedures included additional PPE and third-party monitoring. Site specific safety included safety orientations, tool box talks, pre-task planning, and health and safety checklist reviews. An extensive Due Care Plan, third party monitoring, and inspections were all part of the rigorous safety policy. The construction team logged over 65,000 tradehours without a safety or environmental incident or MIOSHA violation on this project. The project safety plan resulted in no incidents or lost time.
The significant chlorinated-VOC contamination at the site presented the potential for vapor intrusion and inhalation by human occupants, as well as direct human contact with impacted soil. SME worked closely with the architect and owner to evaluate and design appropriate vapor intrusion controls to prevent exacerbation and potential human health exposure to pre-existing contamination. SME conducted daily field monitoring of construction activities, ambient air conditions, and other due care tasks. After evaluating multiple building design options, an open air, first floor garage concept was chosen. This concept was a strategic design aimed at significantly reducing the amount of enclosed building space and thereby reducing potential human exposure to vapors emanating from the contaminated ground.
Sustainability was a consideration throughout the project. While the building is not certified there are many sustainable LEED design features that were incorporated into the project that exemplify the teams commitment to the environment.

Ford Central Energy Plant
OWNER: DTE Energy DESIGNER: OPN CONTRACTOR: Walbridge
DTE’s Ford Central Energy Plant (CEP) was designed and built to be a significantly cleaner source than the existing infrastructure to generate electricity and distribute chilled water, hot water, and steam to serve buildings at the Ford Research and Engineering Campus. The CEP consists of a new combined heat and power plant and a chilled/hot water plant for the combined generation of power and steam.
The CEP project was completed on time. As for safety, during the 478,475 total hours worked, the total recordable incident rate was 1.26, DART Rate was 0, and the lost time incident rate was 0.
The CEP uses several environmentally conscious and sustainable components. The building envelope incorporates a vast amount of low-E, energy-efficient glazing to ensure access to natural light and views to the exterior. Increased access to natural light also reduced the demand for electrical lighting fixtures in several of the commonly occupied building areas. LED fixtures were installed where electric lighting was necessary.
Much of the building material was sourced within 500 miles of the project site, lessening the impact of shipping and transportation. The primary palette consists of highly recycled, recyclable, or sustainable materials including precast concrete, and exposed steel structure. Because the structure is exposed in many cases, less finish materials are required, resulting in a lower carbon impact.
Substantial design consideration was given to the mechanical and electrical systems, which reduced the overall energy performance by 30% from the baseline for typical buildings of this type. By adding a construction waste management plan, a construction indoor air quality plan and the use of LEED building material, the LEED Gold certification is in process.
The Ford Research and Engineering Campus will see significant benefits in air quality when the CHP is fully operational. The area will experience as much as: % 98% reduction in carbon monoxide emissions. % 66% reduction in NOx emissions. % 18% reduction in overall greenhouse gas emissions.