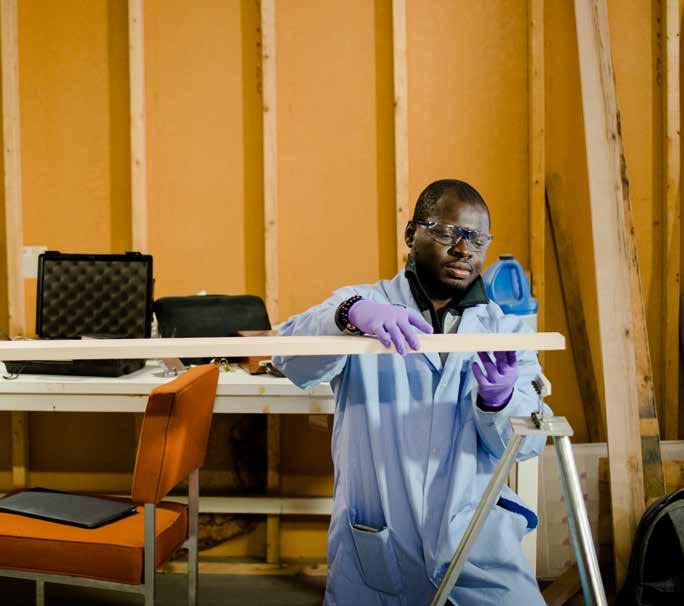
23 minute read
Why Wood? And Other Biophilic Construction Questions
Why Wood?
AND OTHER BIOPHILIC CONSTRUCTION QUESTIONS
BY ALLISON MILLS
Like farm-to-fork for the local foods movement, forest-to-frame is a new way to think about using wood for construction and building stronger regional bioeconomies. Rather than going back to hand-hewn cabins, the future of sustainable construction for skyscrapers, cars, classrooms, and homes relies on mass timber and innovative wood products.
One such material is hardwood cross-laminated timber (CLT). It’s an oldie, but a goody: Crossed grains in boat hulls—pinned in place with dowels—sailed the world for hundreds of years. Modern CLT panels are pressed boards of low-grade pulpwood that fit together like toy building blocks and can be custommade, cutting down on waste, and the material has become a prime choice for earthquake safety. Currently, only softwoods like pine and other conifers are included in building codes for CLT, but hardwoods like maple and poplar may have equal or even better chemical and mechanical properties.
In Michigan, with more than 19 million acres of timberland and more maple than you can shake a stick at, that makes hardwood CLT a major untapped market.
“It’s easy to sell high-value veneer and timber logs, but the challenge is what to do with lower-value pulp logs,” says Mark Rudnicki, professor of practice in forest biomaterials and the coordinator of industrial research, innovation, and commercialization at Michigan Technological University. Rudnicki points out that Michigan already grew a forest economy with logging, lumber, paper, pallets, furniture making, maple syrup, and tourism. But as the pandemic’s timber prices illustrate, supply and demand is subject to change—and grocery coupons, pancakes, and Adirondack chairs alone cannot seed future forests’ potential.
“Softwoods—which we really mean are conifers instead of angiosperms—are graded for construction, while hardwoods—which have a lot more variety in material behavior—are graded for appearance,” Rudnicki says. “It’s not rocket science, but someone has to do all the detailed tests to make hardwood CLT accepted for construction.”
Michigan Tech, West Virginia University, and Virginia Tech are leading U.S. testing for hardwood CLT. Rudnicki works alongside Xinfeng Xie, associate professor of forest biomaterials at Michigan Tech, and Munkaila Musah,a Michigan Tech doctoral graduate now at Auburn University. When they talk about hardwood CLT, they get a handful of common questions.
DO WE HAVE ENOUGH TREES?
When forests are managed properly, trees can be renewable and grow as WOOD BENEFITS
WoodWorks, part of the Wood Products Council, and Think Wood, funded by the Softwood Lumber Council, gather data on CLT, mass timber, and other wood construction. In Europe, wood and natural construction are called biophilic designs. Here are their main selling points: % wood buildings can cost less and earn more % carbon dioxide emissions can be reduced 15% to 20% % rapid on-site assembly is easy with modular units % reduced weight means smaller foundations % wood’s vibration properties improve earthquake and wind safety % heavy beams may improve structural integrity and fuel contribution during fires and softwood CLT panels hold up to International
Building Code (IBC) standards
fast as they’re harvested, which means 1% to 2% of our forests each year. But most people hear “logging” and picture the clear-cut landscapes of yore. Rudnicki replies, “That’s not forestry; forestry came after. That wasn’t forest management, that was denuding the landscape.”
Landscapes today in Michigan have thicker forest stands with more dead and downed trees, which pose wildfire hazards. Selectively harvesting prime logs and clearing some of the spindly competition is a more sustainable way to fell trees and this mix of wood is what interests Rudnicki, Xie, and Musah. The pulp wood slated for pallets and paper could also be used for the modular CLT construction blocks first developed in Austria in the early 2000s.
Munkaila Musah is a postdoc at Auburn University who studied wood biomaterials and cross-laminated timber (CLT) at Michigan Tech while earning his PhD.
PHOTO: SARAH ATKINSON, MICHIGAN TECH
“CLT, currently famous in Europe and North America, is made by gluing together and pressing kiln-dried dimensional lumber in perpendicular layers. The layering is repeated to the desired thickness, typically three, five, or seven layers to produce an engineered product that is strong, stable, and overcomes the inconsistencies inherent in unmodified wood,” Musah explains, adding that the panels can be assembled into custom-made modules, fabricated with precise dimensions and openings for doors, windows, and vents. “This quickens construction with a cleaner site than traditional building as CLT panels are hoisted into position and bolted together with metal brackets to build up the structure floor by floor.”
Less waste also means the original trees are used more wisely, and as demand decreases for Michigan’s paper pulp and other low-grade wood, hardwood CLT offers an additional market when harvesting for timber and veneer wood. This diversity of markets is critical as only a small percentage of trees in any given stand is the highest veneer grade: Most are pulp grade and without markets for these lower value trees it can be difficult for logging to be profitable and cut wood might go to waste.
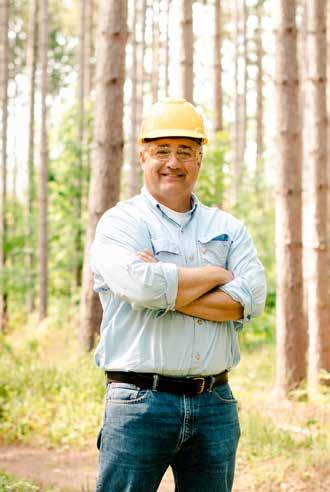
Mark Rudnicki Xinfeng Xie WHAT IF THE GUY DOWNSTAIRS IS A SMOKER?

With today’s building codes, that’s probably a bigger health concern than a fire hazard. But whether people worry about candles, Christmas trees, old wiring, or curious pyromaniac children, fires do happen and a material’s job is to slow its spread.
Fortunately, wood burns predictably. That means it’s easier to engineer how thick to make a wall, floor, or ceiling so that it will not fail for three hours or more. This predictability makes wood safer for residents and for the firefighters who need to know how much time they have.
“Wood has the components and structures that we want and are currently making using non-renewable resources,” says Xie, who studies many wood products—including hardwood decking for Army trailers in the tropics, carbon-polymer composites for car bodies, and fuels and chemicals made from waste lignocellulosic biomass. Wood overall makes a good building material but Xie says there are distinct benefits to hardwood CLT compared to softwood CLT.
“On the chemical side, processing hardwoods generates much less VOCs (volatile organic compounds) than processing softwoods. It is more environmentally friendly as VOCs
pollute the air,” Xie says. “Mechanically, hardwoods are often stronger than softwoods. Our studies showed that 3-inch-thick, 3-layer maple CLT was five times stronger than 4.5-inchthick, 3-layer softwood. That means you would have more living space in a house using hardwood CLT instead of softwood CLT.”
BUT WOOD IS OLD-SCHOOL. WHAT’S SO INNOVATIVE NOW?
Because the Chicago Fire of 1871 still wants its wood buildings back, right?
Good thing it’s 2021 and, in addition to improvements in studying and designing for fire resistance, wood has come a long way as a construction material. Many of us stay visually stuck on the traditional stick construction undergirding McMansion mushrooming, but mass timber takes many forms. As Musah points out, products in the mass timber family includes cross-laminated timber (CLT), nail-laminated timber (NLT), dowel-laminated timber (DLT), glue-laminated timber (glulam, or GLT when used as panels), and structural composites such as laminated veneer lumber (LVL) and laminated strand lumber (LSL). Advances in better adhesives make CLT possible and the Lego-like panels and blocks could change construction entirely.
Right now, the world’s tallest wood building is in Norway, reaching 18 stories tall. But Milwaukee is about to lead the world with its 25-story mass timber tower currently under construction and Chicago is entertaining an 80-story tower. Grand Rapids is planning two mass timber buildings on the Michigan State University campus and Michigan Tech is looking at hardwood designs for its new health sciences facility.
As global markets call for more carbon-neutral and carbon-negative construction, research continues to return to wood as the easiest and best option for storing carbon in a buildings’ bones. That skeleton is also crucial for withstanding earthquakes; wood has exceptional vibration muffling properties, which is also great for acoustics. Plus, psychology and health science studies show that natural, beautiful spaces enhance mental health, productivity, and well-being in schools, offices, and medical facilities.
Hardwoods CLT is specifically innovative because of the variety of chemical and mechanical properties that can enhance other mass timber qualities and provide even more customizable construction. Returning to the concept of forestto-frame, hardwood CLT also offers Michigan and other states a way to strengthen regional economies and provide more consistent and affordable supply.
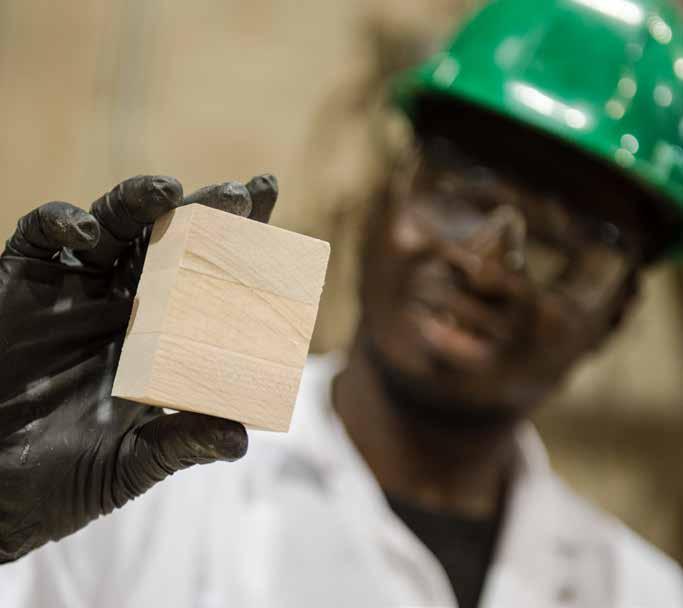
Hardwood cross-laminated timber (CLT) is made of many layers of pressed wood from species like maple, beech, or poplar
PHOTO: SARAH ATKINSON, MICHIGAN TECH
SO, WHAT WILL IT COST?
Nobody has a good estimate on the price of a panel of hardwood CLT yet. That’s because rigorous testing is still needed to ensure hardwood CLT meets building codes. Right now, there is no manufacturing of hardwood CLT and it’s not included in ANSI/APA PRG 320, the standard for performancerated CLT. Before that testing can be done, researchers need the right tools and the right collaborations.
“We need to test full-size hardwood CLT panels of more hardwood species, and we hope these tests will help get hardwoods into the standard,” Xie says. He and Rudnicki lead efforts to make those full-size panels a reality: a $120,000 specialized CLT press. But it’s the kind of equipment that’s exceptionally hard to write into a normal research grant, so they’re collaborating with regional industry partners to purchase the equipment, move from bench-scale to industry specs, and start chemical and mechanical testing for Michiganmade products.
For Michigan to grow into a leader in sustainable construction, hardwood CLT offers potential—and the sky(scraper) is the limit. Because CLT testing in the US is 20 years behind Europe and a decade behind Canada, the true cost of hardwood CLT could be missing the opportunity.
Allison Mills is the associate director of Research News at Michigan Technological University.
ESD CONSTRUCTION & DESIGN AWARDS 2021
Despite an unusual year of stops and starts, the business of building construction and design continued during 2020-21 in great form. The recipients of the 2021 Engineering Society of Detroit Construction & Design Awards—diverse in their project focus—weathered the challenges with creativity, modern technology and stellar engineering teamwork.
Evaluated by a panel of industry judges, the awards are among the premier recognitions presented to members of the construction industry and their projects. The awards are unique in that they honor the three primary members of the building team—owners, designers and constructors— and recognize outstanding achievement and innovative use of technology. The awards were conceived 47 years ago to elevate the standard of practice in the construction industry.

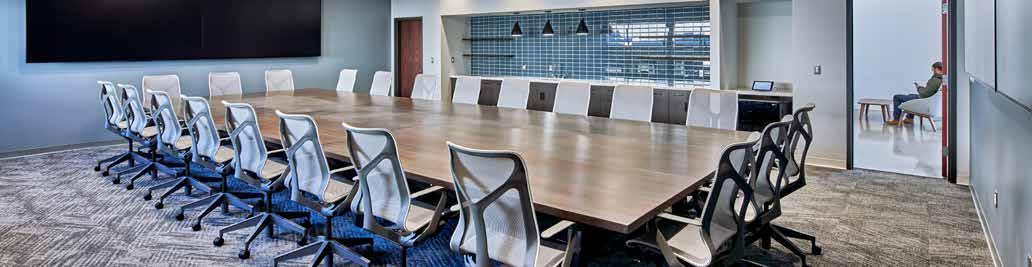
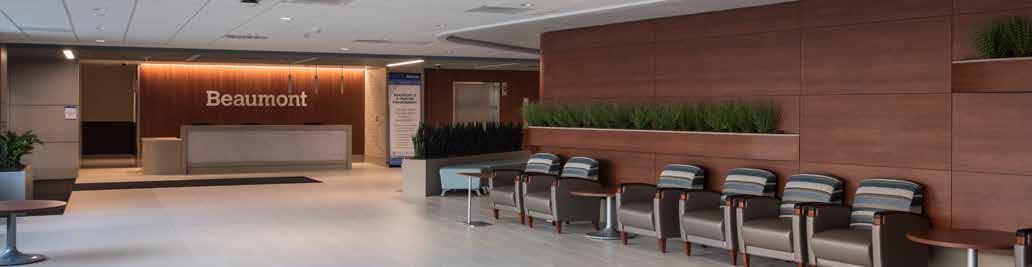

Ford Motor Company Driving Dynamics Lab
OWNER: Ford Land DESIGNER: Albert Kahn Associates, Inc.
CONTRACTOR: Walbridge
Ford Motor Company’s Driving Dynamics Lab (DDL) is a multi-functional building housing an array of vehicle test labs and collaborative spaces designed to improve communication and efficiency between product development teams. Traditionally, vehicle performance, durability, and acoustics, are scattered across a vast campus. Now, DDL houses trackside operations and engineering functions within one building, creating unity and cohesion between product engineers and test technicians. This cohesion and collaboration improves the test process flow and reduces product development timelines.
The 218,000 square foot facility is located at Ford’s Dearborn Research and Engineering Center and Proving Ground and is a LEED Gold-designed building serving multiple departments and programs.
DDL was constructed in two phases: DDL East and DDL West. The East side of the building is three stories, with the first floor including a vehicle garage, acoustics test lab, and shop space to support trackside operations. The second floor includes labs, fabrication shops, storage lockers, food service facilities and equipment rooms. The third floor includes engineering offices and test track observation areas. The West side is a single-story building featuring a tire laboratory with space-saving storage racks, shipping and receiving, durability laboratory and storage, Driver Autonomous Technology (DAT) laboratory, vehicle circulation areas, outdoor patio area, facility entry, and core support areas.
BUDGET EFFICIENCY
Ford, Kahn, and Walbridge utilized VA/VE methods to maintain the budget while optimizing the building program to fit the limited site footprint. 3D Revit modeling identified possible infrastructure issues early in the complex project, accommodating future construction to the West and South. The design team found ways to do more with less, such as installing floor-mounted vehicle lifts
and fiber-reinforced concrete slabs instead of costly alternatives to stay within budget. Special features such as a mobile tire/wheel storage racks satisfied the high demand for tire and wheel storage in a reduced footprint. Ventilation and cooling equipment were roof-mounted, taking advantage of the building’s expansive roof area and reducing the need for enclosed equipment rooms.
With the site’s location trackside at the Dearborn Proving Ground, the project demanded the utmost care in planning, scheduling, phasing, and construction sequencing to have minimal impact on Ford operations. Construction was staged and phased to mitigate impact to trackside operations while maintaining primary access for Ford shareholders to conduct normal business.
SAFETY
Safety was a huge focus with a primary challenge being the continuous use of trackside facilities by Ford employees and test vehicles throughout the phased project. Buffer zones were implemented for the safety of all personnel onsite as different phases of the project were completed. In addition, pedestrian routes were adjusted, and temporary overhead platforms were erected to ensure safety between construction and the public.
TEAMWORK
The DDL was a true partnership. As the project started, BIM 3D Modeling was utilized and completed ahead of time, allowing areas to be locked for fabrication. Each BIM contractor exceeded expectations with modeling and followthrough throughout the project.
While constructing DDL in two phases, East and West, the siding contractor completed the façade with seamless construction transition from partition walls to screen walls, maintaining continuous appearance while complementing the adjacent buildings. On part of the exterior, the team employed a robot team member. “SAM,” the semi-automatic mason, laid sections of the brick for the façade of the east side of the building.
SAM was able to increase masonry productivity and reduced the negative impact to the health and safety of the workers. Inside, a two-tier stairwell design in DDL West was a challenge as the exterior and interior glass material had to be released for fabrication before final field measurements could be taken. Utilizing the 3D modeling gave the team an increased level of accuracy and detail, which was the direct result of collaboration and teamwork from the steel contractor, glass contractor, Kahn, and Walbridge.
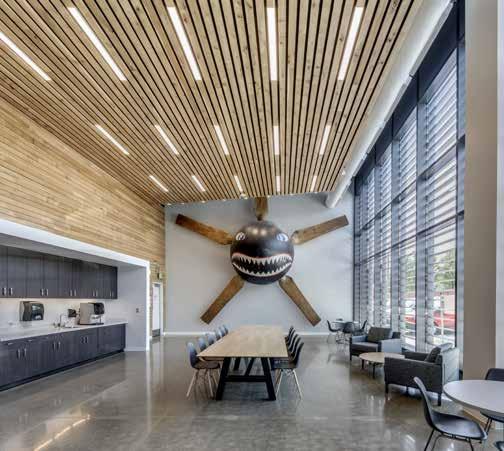
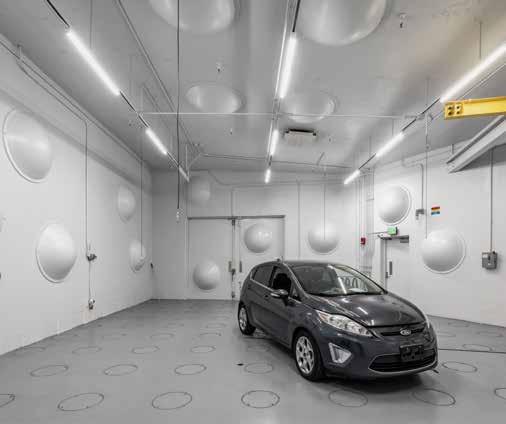
SUSTAINABILITY
The DDL was designed and constructed to achieve LEED Gold, with final certification pending. Achieving Gold level certification proved challenging in a facility where high amounts of energy is consumed by the owner’s test systems. Ford showed its commitment to sustainability by purchasing high-efficiency electric motors in not only building systems but also process testing equipment. They also purchased green power and established additional employee shuttle routes.
IMPACT
Headquartered in Dearborn, Ford has long supported the city and surrounding communities. By choosing to remain in Dearborn, Ford has made a huge impact on the city, investing not only in their corporate campuses, but also creating opportunities for additional housing, restaurant, and retail space in the city. Pledging to commit funding and resources over a ten-year period, Ford has ensured the viability of the city for the long term.

OWNER: Ford Motor Company DESIGNER: Ghafari Associates, LLC/Jacobs CONTRACTOR: Stenco Construction
Ford Motor Company’s Vehicle Performance and Electrification Center (VPEC) is a revolutionary research and testing facility situated on a 14-acre campus in Allen Park, where the automaker tests passenger and motorsports vehicles to achieve even greater fuel efficiency and performance. This 210,000 square foot facility includes three attached buildings featuring the most technologically advanced wind tunnel of its kind: capable of speeds of up to 200 mph. It also includes a state of-the-art rolling road system, a traversing measurement system, a cutting-edge frontal area measurement system, and a variety of battery cyclers and environmental chambers, as well as multiple offices and work areas.
TEAMWORK
A critical part of this collaboration was developing the plans for the wind tunnel portion of VPEC. This structure required incredibly tight tolerances – no simple feat for a building constructed out of concrete with a 28-foot-tall octagon box-out for the future fan and two double-curved contraction walls at 43 and 47 feet tall.
The project team utilized a design-build approach to control the budget and also utilized BIM modeling to eliminate issues in the model environment ahead of construction. Early on in the project, the scope expanded from an original 25,000 square foot wind tunnel facility to include a 185,000 square foot battery lab, other support facilities, new functionalities, and potential future facilities. This scope expansion impacted the original schedule. However, the Stenco design-build team worked closely with Ford Motor Company and the design partners to develop a new set of updated project plans.
Lean construction practices were implemented for the project, including onsite preassembly, strategic laydown areas, detailed logistics plans, and just-in-time delivery. These tactics allowed the project to run as efficiently as possible, conserving both time and money.
SAFETY
The project even received an NMAPC Zero Injury Safety Award in 2018, thanks in part to Stenco’s use of Safety Trained Supervisor Construction certified employees, a fully engaged and multi-discipline safety committee, a high level of collaboration across teams, and interactive planning processes.
The intensity of the safety program increased when the jobsite re-opened after a brief shutdown for the COVID-19 pandemic. Stenco quickly revised their safety plan and procedures to incorporate daily health screenings, mandatory temperature checks, social distancing, and increase sanitation of common areas.
TECHNOLOGY
A number of innovative construction techniques were used across the wind tunnel, battery lab, and other structures, including: 3D Scanning and Modeling technology to provide highly detailed, 3D as-builts of the project to provide better quality project layouts, more accurate jobsite surveys, and higher tolerance compliance.
Depending on the application, these models are accurate up to within a 16th of an inch and provided more accurate data for field measurement and verification.
The project utilized GPS controlled equipment, including an excavator and bulldozer, to ensure all excavation and earth-moving tasks were executed with an accuracy of within a hundredth of an inch. This technology helps reduce time and material by only moving the required amount of material, minimizing material overruns, fuel usage, and trucking costs for import and disposal charges. With the GPS-controlled equipment, teams were able to input the project blueprint into the onboard machine telematics, including design surfaces, grades, and precise location of infrastructure and building coordinates.
To improve the energy efficiency of the wind tunnel, Jacobs located the tunnel heat exchanger diagonally across Corner 3. This innovative solution increases the surface area of the heat exchanger compared to more traditional heat exchangers designed in the cross legs of the tunnel. Jacobs’ engineers used Computational Fluid Dynamics (CFD) to design the turning vane shapes both upstream and downstream of the heat exchanger to optimize the flow performance, estimating that installing the heat exchanger in Corner 3 saves Ford 155 KW of fan power at tunnel top speed and 44 tons of cooling capacity.
SUSTAINABILITY
Every aspect of the building was designed with sustainable principles in mind. While not LEED certified, sustainable objectives were set for the design of the facility. Considerations for energy, air, water, soil / habitat, material use and employee wellness are all given attention during the design process. The use of windows and glass in office and lab areas for natural daylighting, outdoor patio space for employee breaks, and car charging spaces are just a few of the sustainable environment details included in this facility.
IMPACT
Continuing their work developing technologies to reduce vehicle energy consumption, the ability to test vehicles in the upgraded labs will provide a more accurate picture of what to expect when vehicles hit the road for testing and production. This facility will have a lasting impact on the surrounding community not only through the creation of more jobs, but also because it was designed to allow for future flexibility. Currently there is a planned 85,000 square foot addition to the building which will open the opportunity for future growth.

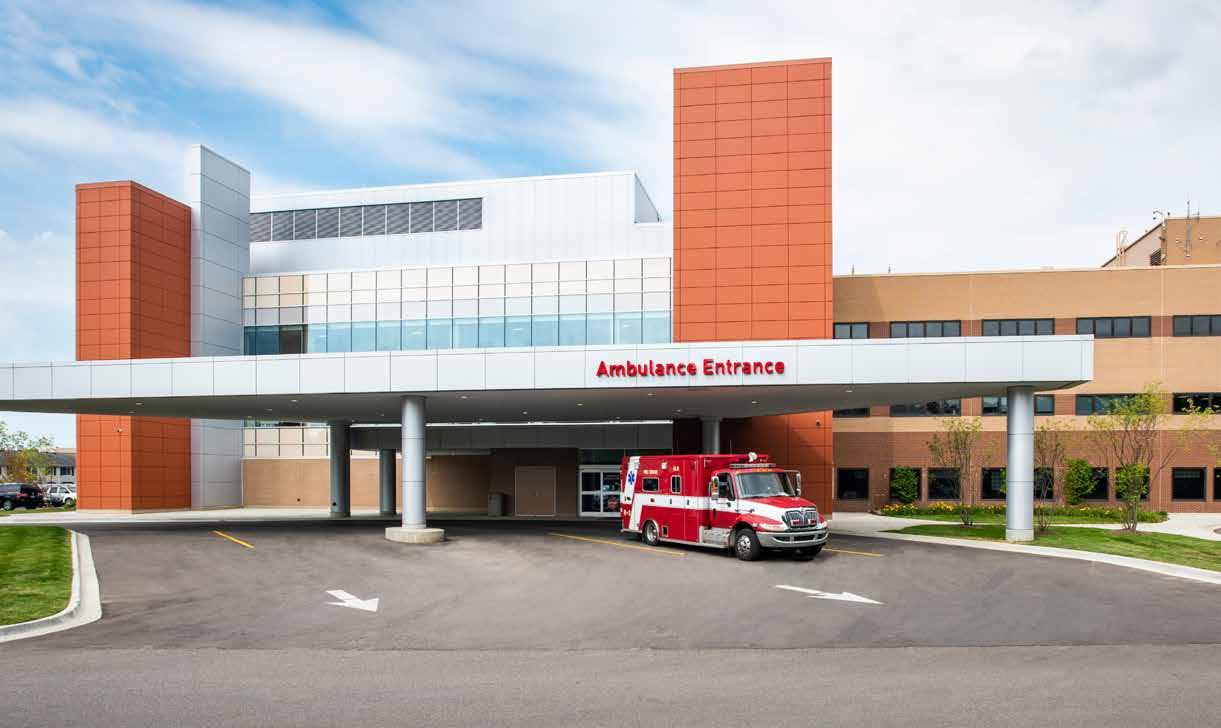
Beaumont Farmington Hills – Master Plan Implementation
OWNER: Beaumont Health
DESIGNER: HKS CONTRACTOR: Barton Malow/AIMS
With sights set on creating a quality and high-functioning healthcare campus for the surrounding community, the team broke ground on the Master Plan in October 2015. The significant impact and that these new additions and renovations had were never more apparent than in its final year of construction in 2020. The upgraded and expanded Emergency Department, brand new intensive care unit, private patient rooms, and additional space were imperative as the world faced (and continues to face) a global pandemic.
The nearly 200,000 square foot Master Plan project included: the East Tower emergency department expansion and renovation with 58 treatment and evaluation bays; a 17-bay observation unit; larger surgical services department with nine new operating rooms; a 20-bed critical care unit with private rooms; and an expanded family lounge.
The new South Tower includes 40 private patient rooms, dedicated units for orthopedic, oncology and respiratory care patients, and a new main entrance/ reception area for the entire hospital.
Additionally, the team completed a 20,000 square foot Central Energy Plant addition that is 30 percent more energy efficient than the previous plant as well as a 473-car parking structure, new helipad, and over ten acres of site work.
TEAMWORK
The Master Plan project was completed on time and the team used a variety of methods to maintain the schedule. The many components of the project were meticulously scheduled and mapped. Design and construction phases began with full-phase pull planning sessions that continued during construction and focused on the look-ahead schedule.
These collaborative sessions with the trade contractors included them in the development of work sequenc-
ing and created buy-in and accountability for all involved. The logistics plan considered every element of hospital operation to ensure minimal impact on day-to-day hospital activities. Almost every portion of the existing 10-acre site was upgraded and to mitigate the impacts, a 3D campus model was developed for each phase of construction. All stakeholders could view the campus, effects of construction, and traffic flow on any given time frame of the schedule all in 3D.
PATIENT CARE
Primary design and construction considerations for the expansion were to improve staff efficiency, promote patient privacy, decrease stress, and improve overall care and patient healing. A notable enhancement included the significant changes to the Emergency Department. Not only did the change in size increase the capacity for patient care, but the expansion also allowed for the inclusion of more patient privacy and separation. While beds were previously divided by curtains, the upgrade to sliding glass and drywall partitions has become especially beneficial during the past year. Additionally, these upgraded patient exam rooms in the Emergency Department were created with flexibility in mind to accommodate a fluctuating intake of patients. These pod spaces now have the capability to expand and contract dependent on patient needs.
SUSTAINABILITY
The new Central Energy Plant addition includes new emergency generators, 40 KV DTE incoming service lines to improve power reliability, medium voltage switchgear, a new electrical substation, and new chillers. Work also included relocation of the existing O2 farm while the hospital remained active and roughly 2,000 LF of new duct bank. COMMUNITY
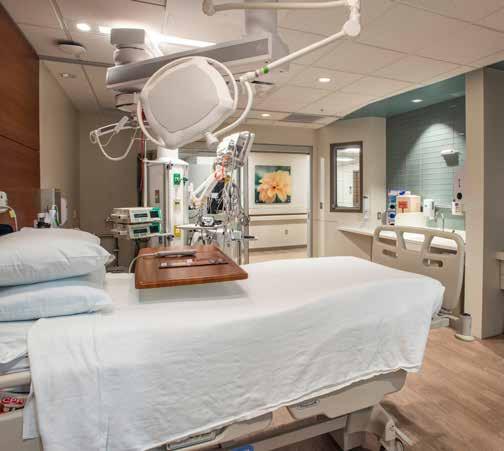
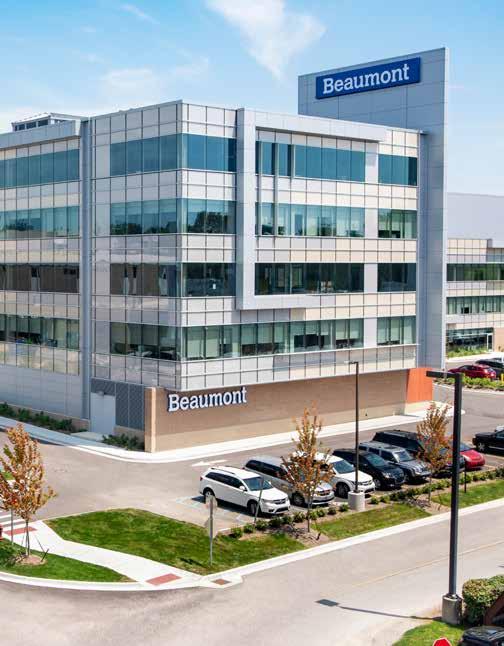
To adapt to the constantly changing healthcare landscape, Oakwood Healthcare and Botsford Hospital merged under Beaumont Health to form Beaumont Farmington Hills (formerly Botsford General Hospital). The goals of the merger and changes were to maintain quality and safety while increasing efficiencies, improving utilization and reducing avoidable costs.
As the number of patients who turn to Beaumont, Farmington Hills continues to grow, the expansion and renovations have created a safer, more healing environment designed to meet the needs of the surrounding communities. The Emergency Center at Beaumont Hospital, Farmington Hills is staffed and equipped to handle severe illnesses and injuries, as well as the bumps and scrapes that also need medical attention.
Today, the hospital is a Level II trauma status. It is a major osteopathic teaching facility with residency and fellowship programs and is the base teaching hospital for Michigan State University College of Osteopathic Medicine. The major upgrades improve patient care, reduce costs, increase efficiencies, and streamline operations. A safer, more secure environment has been created and great care is taken to prevent the spread of infection which has been especially important over the past year.
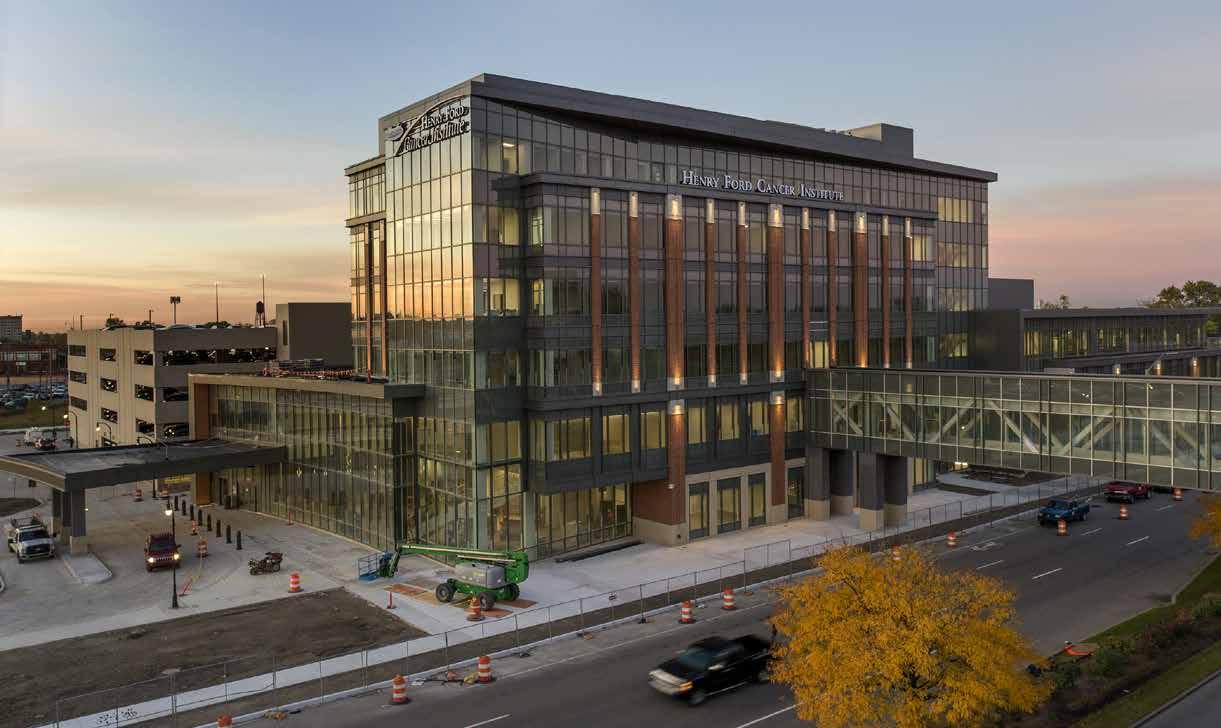
Henry Ford Health System Cancer Institute Brigitte Harris Cancer Pavilion
OWNER: Henry Ford Health System DESIGNER: SmithGroup CONTRACTOR: Turner Construction Company
The Henry Ford Brigitte Harris Cancer Pavilion opened its doors for patients on January 20, 2021. The new facility, named after Detroit businessman and philanthropist Mort Harris’ late wife who passed away from pancreatic cancer in 2016, offers treatment options for 14 different types of cancer through ambulatory cancer treatment, precision medicine, clinical trials, and supportive services.
The building’s design was guided with input from cancer patients, survivors, and families, and includes floorto-ceiling windows that bathe the interior in natural light; a multi-level attached parking deck; a third-floor terrace; quiet meditation areas; and gathering places for support groups, yoga classes, music and art therapy.
BIM made it possible to have a well-coordinated design for a large pedestrian bridge extending overtop the busy, four lanes of West Grand Boulevard. Because design could be so precise, it was possible to prefabricate the bridge offsite and deliver it in sections for safe on-site assembly. In addition, the power distribution system was designed to provide high reliability, efficiency, and to allow for future growth. The electrical infrastructure supports a variety of medical equipment which aids in cancer diagnostics and treatment, including CT scanners, MRIs, and linear accelerators. Switchboards, conduit pathways, and the indoor unit substation have been designed to allow for future vertical expansion of the west half of the building.

Zeiss Michigan Quality Excellence Center
OWNER: Zeiss DESIGNER: SmithGroup CONTRACTOR: The Christman Company
Zeiss, a 172-year-old German-based company that make high end optics, measuring devices, and medical scanning equipment, approached SmithGroup to develop an energyconscious regional headquarters and sales center that enhances both their capabilities and clients’ experience.
Since the machines Zeiss produces measure to such small tolerances, SmithGroup went to great lengths to mitigate potential temperature swings that influence how the machines measure. This approach is controlled not only by the dedicated mechanical systems, but through internal programmatic strategies that help block unwanted solar gain.
Throughout the project, the design team created a custom dynamo script to aid with the Zeiss metrology equipment MEP coordination. The custom script automatically placed, named, and assigned electrical information to the MEP connectors based on owner inputs. This automated workflow and increased efficiency during design.
Reducing consumption of fossil fuels was an important aspect of the project. A broad approximately 496 kW photovoltaic array is located on the roof, which will offset approximately 67% of the electricity consumption. Sensitive land use was also key. A series of four above-ground detention ponds manage stormwater from rain events. The design is a result of coordination between the civil engineer and landscape architect to create a display to visually demonstrate the management of rain events.