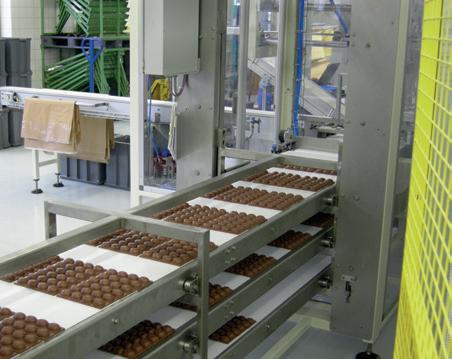
1 minute read
Efficiency enhancement systems for snack packaging lines
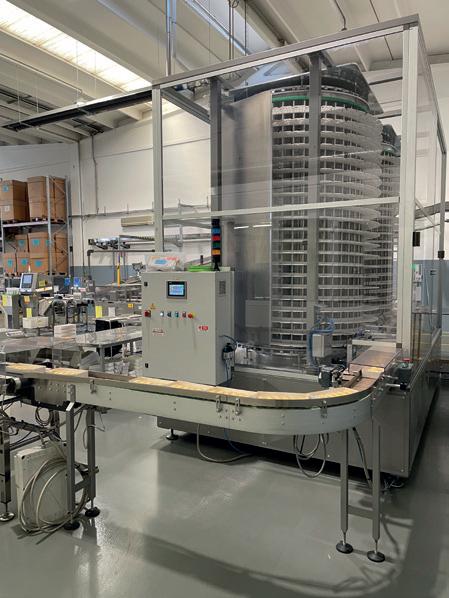
Accumulation technologies for the confectionery sector proposed by M.H
Advertisement
When designing accumulation systems in a packaging line, the first objective is obviously to improve efficiency. In order to also achieve cost savings, we might be tempted to insert a single accumulation system, upstream of the primary packaging line, to manage all downstream machines with it. Normally this would be a valid solution, but in the case of particularly fast lines, as is the case in the production of snacks, it would expose us to the risk of not achieving the expected results, or even making the situation worse.
The typical snack line, downstream of the process, consists of a rank distribution line with the products arranged in multiple rows, a number of flowpack machines, one or more tray packers followed by other over-wrapping flowpack machines, casepackers and, finally, the palletiser. A considerable number of packing levels. If we used a single buffer placed on the rank line, this would have to handle all the idle stops of the downstream machines and would therefore be particularly stressed. Not only that, when the machine restarts, all the nodes in the chain of production that are located before it would have to go into recovery speed (usually 10 to 20% higher than the nominal line speed), which in turn would be more stressed and therefore subject to the risk of further stoppages.
In light of these considerations, it is advisable to divide the accumulation tasks into two different zones of the line. The buffer arranged on the rank line remains valid, for which M.H. proposes a FIFO system with multi-level belts, which will intervene in the event of stops of the flowpacks or the tray packers; we will then go on to manage the trays, which at this point are already a secondary containing multiples of product, with decidedly lower line speeds. In this case we will further exploit the vertical space with a HELIFLEX double spiral buffer, with LIFO operation. This second buffer is capable of handling stops of the multipack, the case packer and also the palletiser, which in any case can also afford a few metres of accumulation with pressure, given that the risk of damage to the boxes is decidedly reduced. The line configured in this way is decidedly less stressed and makes it much easier to manage production fluctuations and imbalances that may occur between one machine and another. The higher initial investment is amply repaid by the lower maintenance and better overall efficiency of the line.
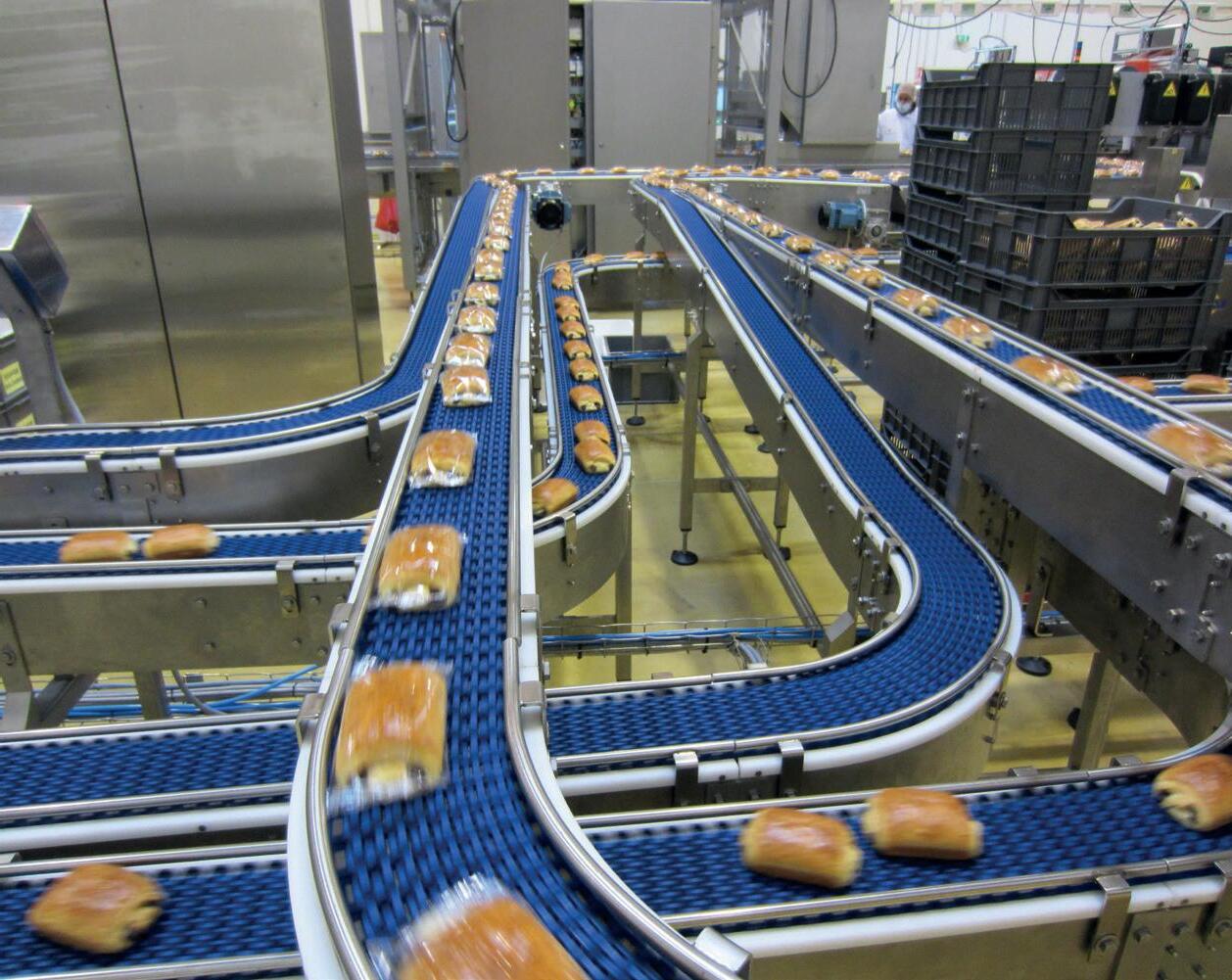

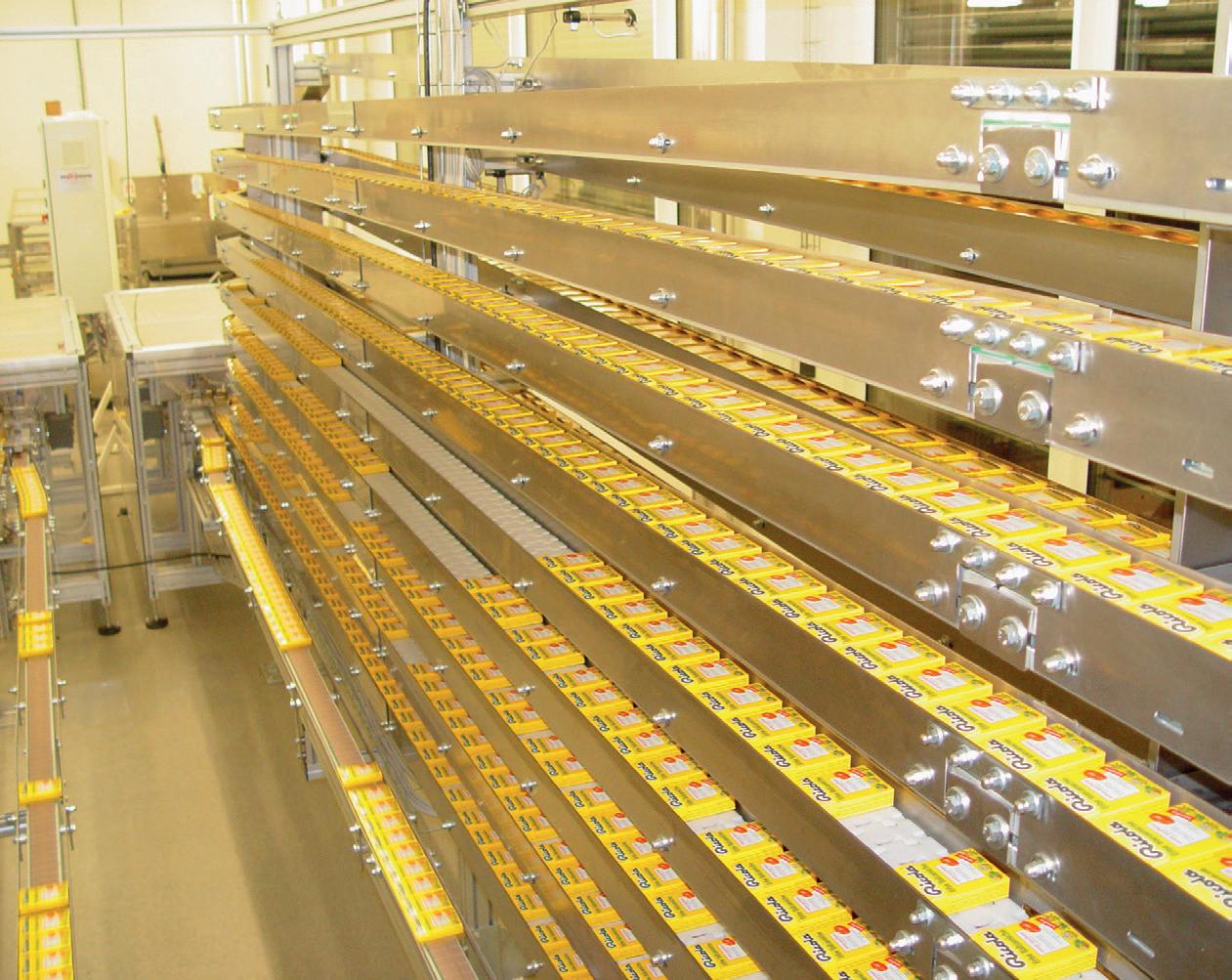
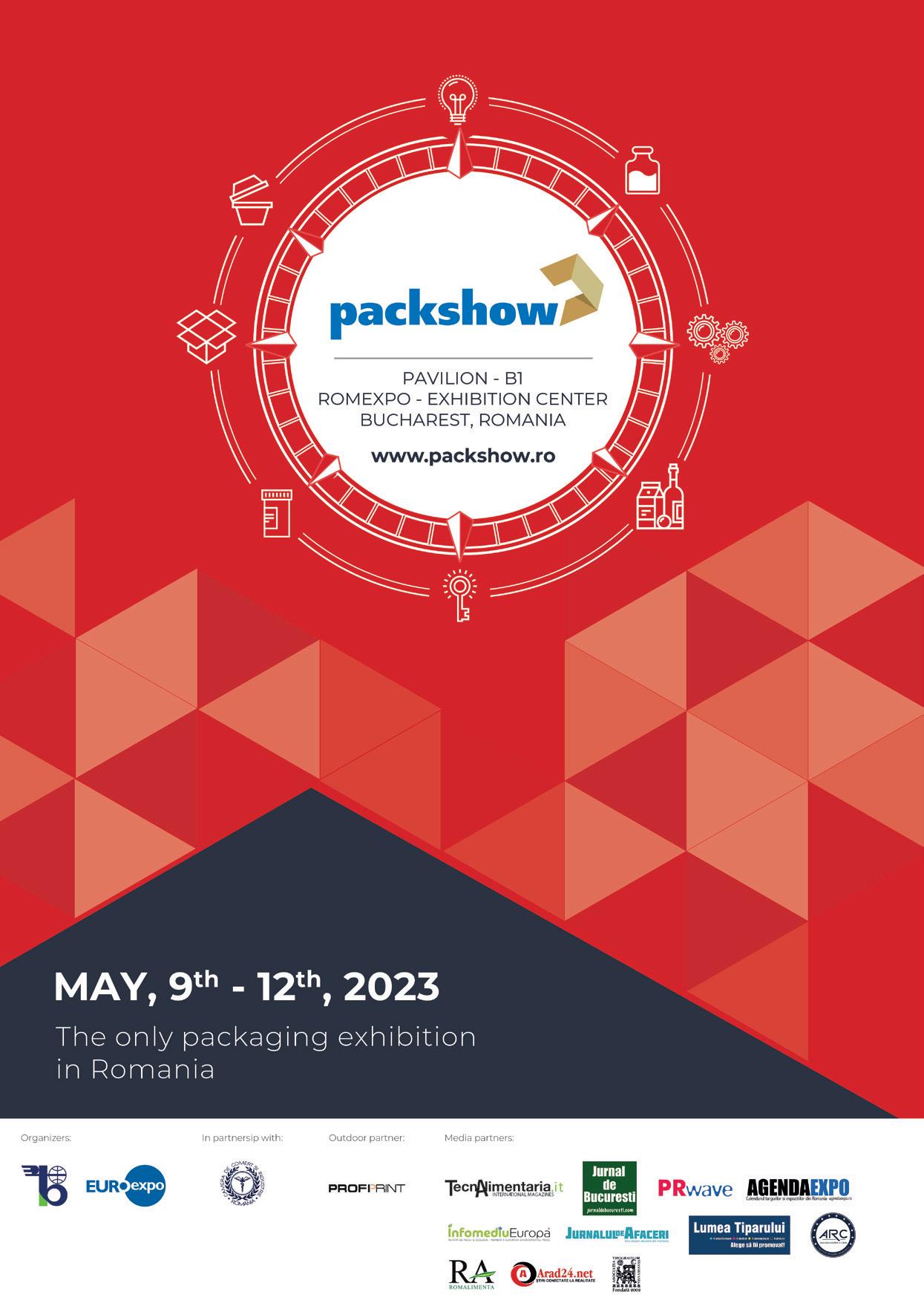
