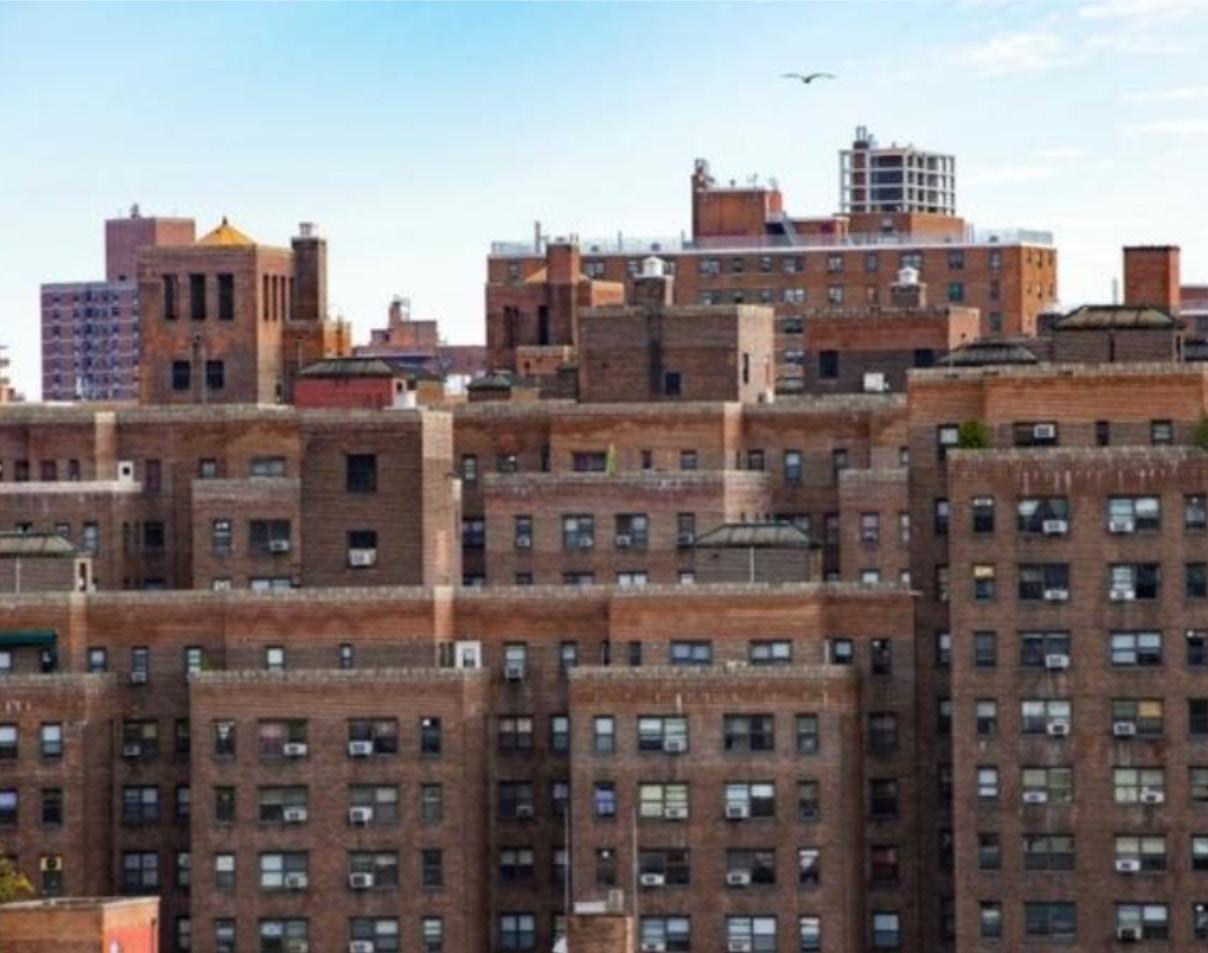
9 minute read
Affordable housing set to collapse like ‘house of cards’ warns RSA
tion extends the eviction moratorium for residential tenants based on the submission of a simple declaration of financial hardship without proving such hardship caused by COVID-related job loss or income reduction,” said Strasburg.
“With no requirement of proof that the COVID-19 pandemic negatively affected their income, and no income limitation to qualify for eviction protection, a tenant whose household income went from a half-million dollars to $250,000 would qualify for eviction protection by declaring that their income has been ‘significantly reduced,’” Strasburg said.
Advertisement
“Technically, it has – but they clearly could afford to continue paying their rent and should not be protected by an eviction moratorium.
“This law should have the same scrutiny and eligibility review as Section 8, senior citizen rent increase exemption, and other government-sponsored assistance. Anything less, what impetus would there be for any tenant to pay rent, even if they are still employed – including thousands working from the apartments they will be withholding rent payments?” Strasburg added.
Strasburg said the legislation is in stark contrast to California’s legislative approach in their eviction law (AB3088), which requires tenants earning $100,000 on 30 percent of AMI to provide documentation supporting their hardship claims.
“A cap on the amount of the rent level would ensure that the benefits of this legislation would reach those that need it. This legislation does not make a serious effort to require tenants to take advantage of available rent relief – such as the DHCR rent relief program, the federal rental assistance program, or the city’s HRA one-shot program. Lawmakers should be directing their constituents to these programs, whose funds are critical to landlords in maintaining and keeping their buildings safe and to paying their real property taxes – the latter vital to keeping the city and essential services afloat,” Strasburg said.
“The tsunami of evictions is not occurring; in fact, a minimal number of evictions have been executed since March 7 –and those cases pre-dated March 7. Tenants have been protected by the Governor’s eviction moratorium executive orders and the Safe Harbor Act,” Strasburg said.
The Senate Democratic Majority today passed the COVID-19 Emergency Eviction and Foreclosure Prevention Act.
RSA President Joseph Strasburg warned that a blanket eviction moratorium without the requirement of proving economic hardship effectively encourages thousands of employed tenants – many using their apartments as their workplace – not to pay rent, and will push the city off the cliff of bankruptcy and take down the affordable rental housing infrastructure like a house of cards.
“Owners recognize and support the need to help tenants without sufficient financial resources to pay rent due to job loss or health circumstances. However, this state legisla-
Considered the strongest bill in the nation to block eviction proceedings from going forward, it allows renters and homeowners to stay in their homes if they are facing hardships due to the pandemic for at least 60 days.
Car maker Aston Martin designing NYC apartments, throwing in free car
Luxury car manufacturer, Aston Martin is getting into the apartment business.
The company is partnering with architect Sir David Adjaye and real estate company, Lightstone, to create a collection of five homes at 130 William in the Financial District.

Aston Martin is also creating a special edition car for exclusively for the apartment owners.
Special Edition Aston Martin DBX
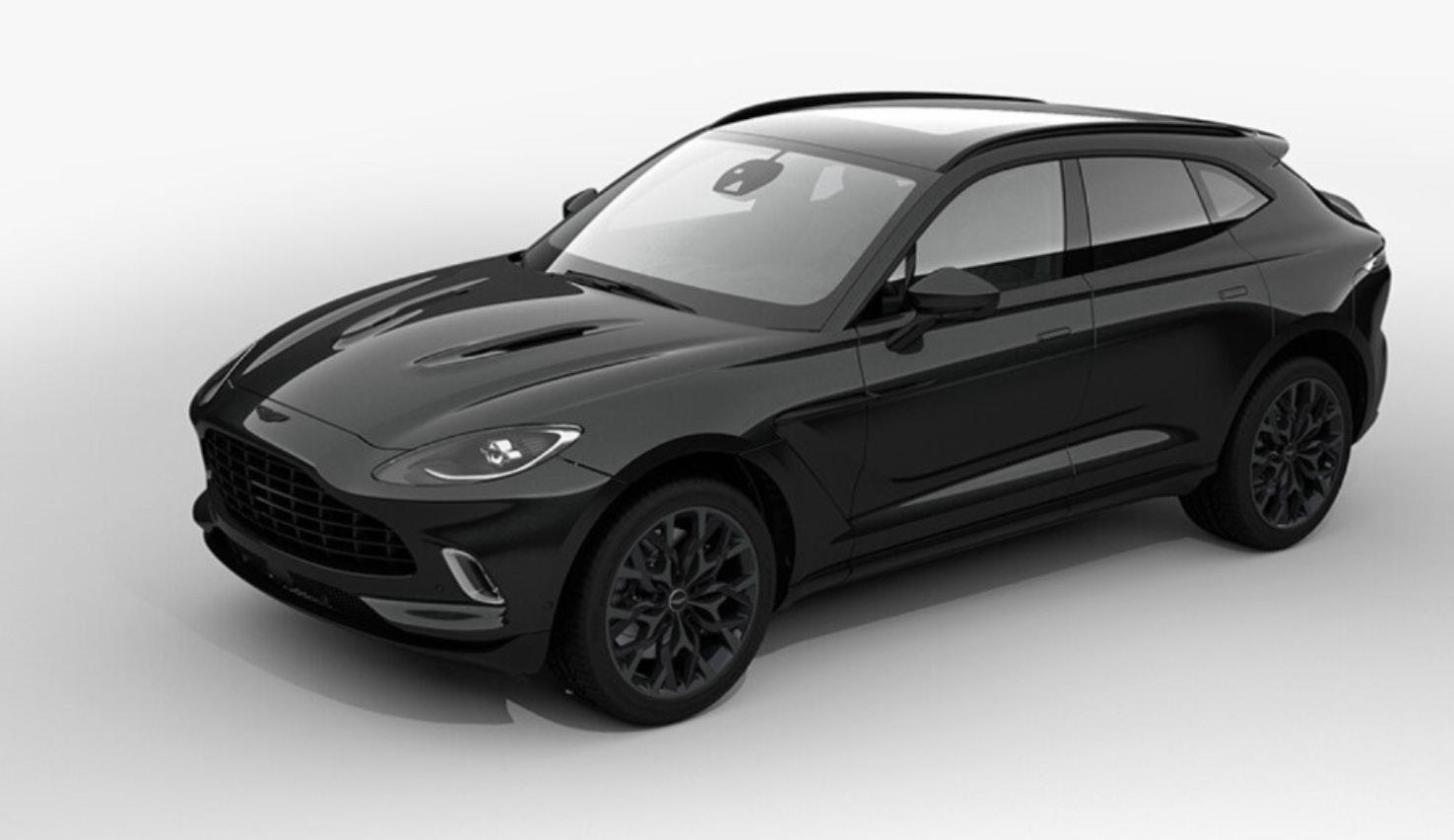
Aston Martin Chief Creative Officer, Marek Reichman said: “This is a fascinating project for the Aston Martin design team to work on and a great opportunity to collaborate with Sir David.
“It is our first real estate project in New York City but our second collaboration in real estate design after the Aston Martin Residences in Miami.
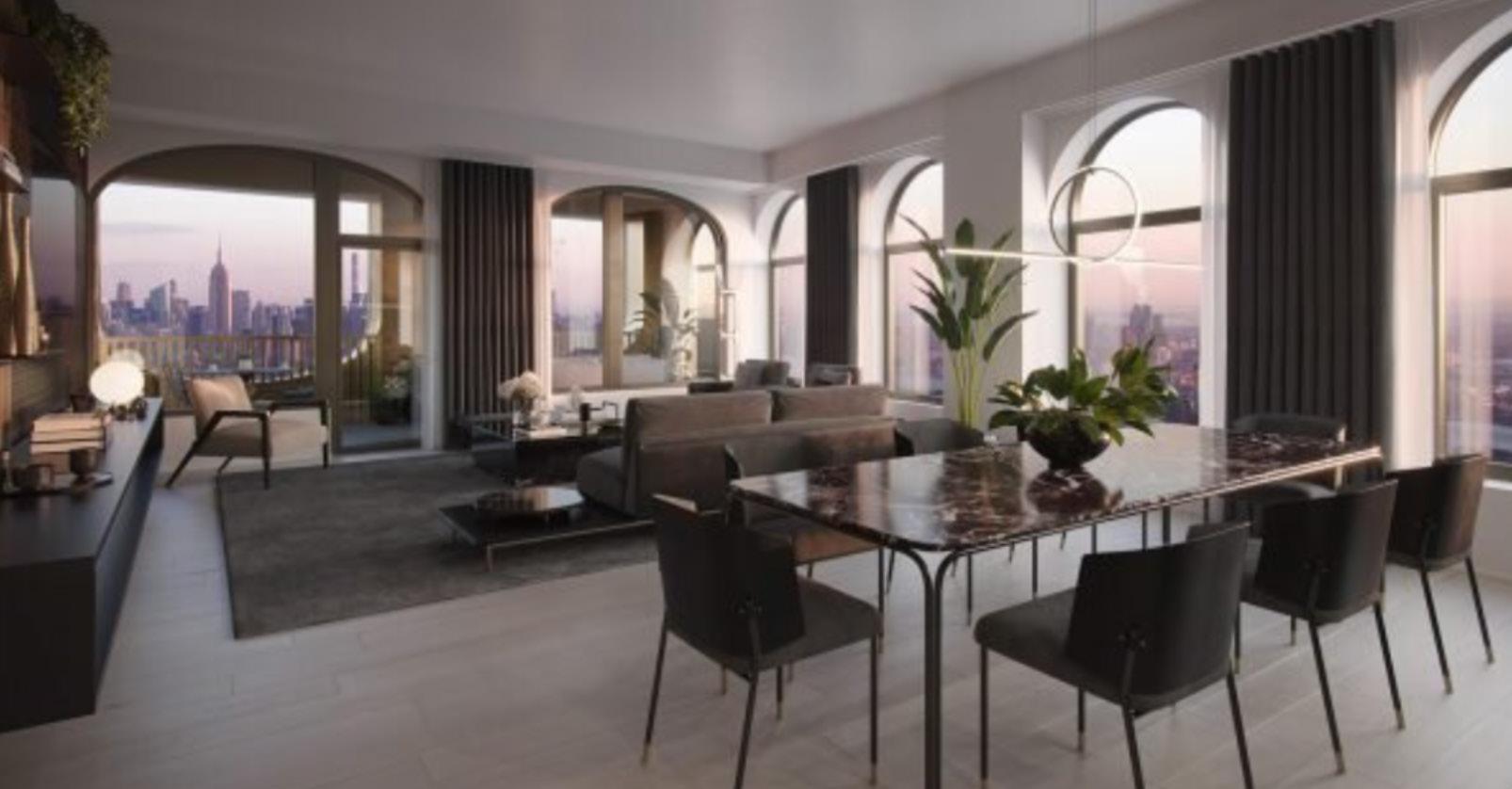
“We can apply what we have learnt in Miami and also bring our unique automotive design skills to these beautiful luxury homes.”
Adjaye is responsible for the vision of 130 William, designing its exterior architecture, as well as all of the building’s interiors which includes 242 residences, over 20,000 s/f of amenities, and a new plaza park.
The building stands 800 ft. and 66 stories. It features a custom hand-cast façade with bronze detailing, contemporary stonework and large-scale arched windows.
Living dining room, 130 William
Sir David Adjaye, said: “It was exciting to find an opportunity to collaborate with the Aston Martin team. The 130
William Aston Martin homes have been touched in a very particular way that merges our design sensibilities. Together with the limited edition SUVs that come with these units, we’ve created a truly unique signature that blends our two disciplines.”
Scott J. Avram, senior vice president of development, Lightstone, added, “130 William is an architectural triumph and in developing this collaboration, we knew we had to offer something truly unique.
“The partnership between David Adjaye, Aston Martin and Lightstone, will bring to market homes unlike anything seen before in New York City.
“The addition of the 130 William Adjaye Special Edition Aston Martin DBX is truly noteworthy and a must have for any true automobile enthusiast.”
Aston Martin Homes at 130 William include five fully furnished units located on the 59th and 60th floors.
Each home has a private outdoor loggia spanning the entire length of residence and screens dividing the balconies into a series of zones for dining and relaxing.
The residences are fully furnished, with hand-crafted materials and textiles and furniture from the Aston Martin Home Collection by the Italian manufacturer Formitalia. Interior design elements feature Aston Martin’s signature crosshatch pattern in a bronze finish. A smoked glass mirror created by Aston Martin Design reflects the skyline view in an arched form.
Each home features a grand living and dining room, with furnishings, textiles and fittings curated by Marek Reichman and Sir David Adjaye.
Located adjacent to the dining room is an open plan kitchen with textured blackened oak Italian cabinetry, Gaggenau appliances, marble countertops from the Apuan Alps in Tuscany, Italy and a cantilevered Nero Marquina marble top, which provides additional bar seating.
As well as a custom cashmere headbard, the master bedrooms have walk-in closets, a Flos light track system and a lounge chair by Hans Wegner.
Buyers have the option of customizing one of the rooms, in the two-and three-bedroom homes, into a racing simulator, an office and library space, or a bedroom.
Aston Martin Design collaborated with Curv Racing Simulators, a new British technology company founded by Darren Turner, a three-time class winner of the 24 Hours of Le Mans for Aston Martin to create the ultimate in luxury home racing simulators.
Aston Martin racing simulator
The 130 William Adjaye Special Edition Aston Martin DBX marks the first time that Aston Martin has collaborated with an architect on the custom fit out of one of their signature vehicles. The DBX is the first SUV to be created by the luxury British manufacturer.
The five homes include two penthouses, priced at $11.5 and $10.5 million. Corcoran Sunshine is handling sales and marketing.
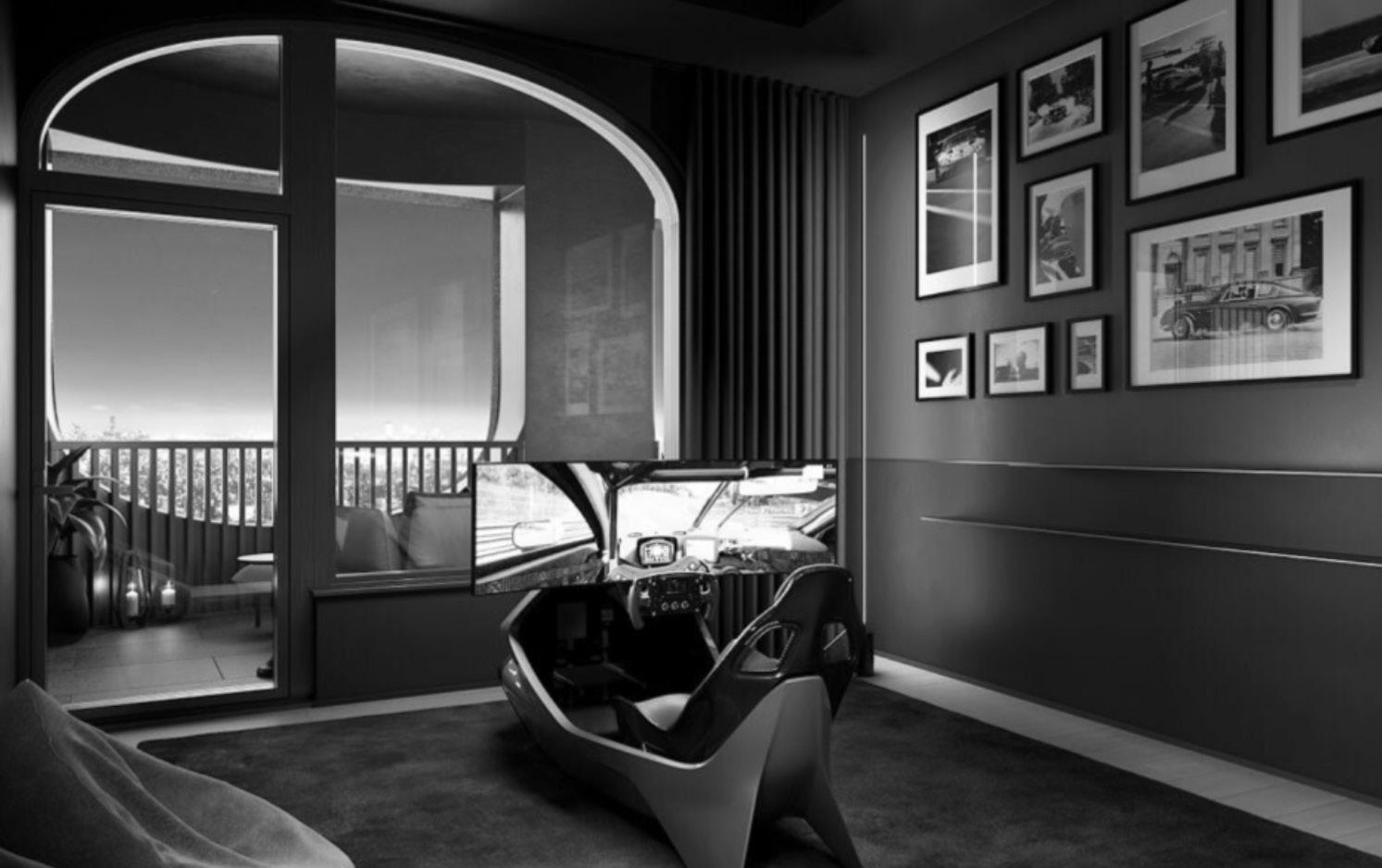
The factory, designed by Rogers Partners Architects + Urban Designers, will house research and development operations as well as production and design by the company’s artificial intelligence researchers, computer scientists, chemists and physicists.
“The Brooklyn Navy Yard has a history of serving New Yorkers in times of crisis, and it proved its worth once again at the height of the COVID-19 pandemic. Today, it has an important role to play in our city’s recovery – by building a sustainable and high-tech manufacturing base in the heart of New York City,” said Mayor Bill de Blasio. “From creating hundreds of jobs to nurturing the next generation of STEM talent, Nanotronics and the Navy Yard are helping build a recovery for all of us, and I’m proud to support their extraordinary efforts.”
De Blasio was joined by executives from the Brooklyn Navy Yard Development Corporation (BNYDC), Nanotronics, Empire State Development (ESD) and CUNY’s Medgar Evers College for the ribbon-cutting ceremony to celebrate the opening of the center in the Navy Yard’s historic Building 20, a 150-year-old former shipbuilding factory.
The project was primarily funded through $3.25 million from the City of New York and a $2.25 million Regional Economic Development Council capital grant through ESD in exchange for a commitment of 190 jobs.
Nanotronics expects to recruit talent locally through New York institutions including the Navy Yard’s Employment Center and STEAM Center (the Yard’s on-site vocational high school), the City University of New York (CUNY), Cornell Tech, New York University and Columbia University. The company has already has partnered with CUNY Medgar Evers College to host nearly 30 interns in the last three years as part of Empire State Development’s STARTUP-NY program.
Mayor opens 45,000 s/f Nanotronics hub at Brooklyn Navy Yard
Mayor de Blasio has officially opened the 45,000 s/f Nanotronics manufacturing center at the Brooklyn Navy Yard.
Nanotronics, a science technology company that combines AI, automation and sophisticated imaging to manufacture hardware and software capable of working on a nanometer scale, will use the building as its headquarters.
“We wanted to create a modern-day Edison Lab,” said Matthew Putman, CEO and cofounder of Nanotronics. “That vision of building in a way that was never done before, with the same hope and possibilities of better jobs, local products, and leading the world in invention seemed like a real possibility in the Brooklyn Navy Yard. We are thrilled to advance manufacturing with the perspective of seeing our past, looking out of our windows at the city where so much of our present is on view, and build an intelligent factory where robotics, AI, and humans can work together to create a sustainable future.” that received an EAU from the FDA. In just 90 days, Nanotronics team conceived, designed, built, and received Emergency Use Authorization from the FDA for its non-invasive respiratory relief product, nHale, to treat COVID-19 in private hospitals, homes, and large converted spaces. nHale was one of the first and most cost-effective products to fill the much-needed gap in the NIH treatment guidelines for a phased respiratory approach to COVID treatment.
Nanotronics expanded its New York presence into the Brooklyn Navy Yard in 2016. As the first and largest tenant of New Lab, the company grew its Research and Development workforce three-fold. By 2018, the company needed to expand manufacturing operations both for redundant manufacturing and to rapidly scale new products. The foundational roots within the former manufacturing hub created an ideal location with waterfront access. The hub’s location in the Navy Yard also provides space for partner firms in the life sciences, semiconductor, aerospace, automobile, additive manufacturing and quantum computing sectors to grow alongside Nanotronics.

BNYDC played an integral role at the outset of the COVID-19 pandemic last spring, serving as a central PPE production hub for the City as it faced shortages in face shields, medical gowns and ventilators, among other equipment. Ultimately BNYDC spearheaded the production of roughly a dozen products by Yard tenants, including nearly 10 million units of PPE and more than 26,000 gallons of hand sanitizer.
The opening of Building 20 comes as the Navy Yard is undergoing its largest expansion since World War II, which will increase the Yard’s job total from 12,000 to 20,000 in the coming years. The expansion includes the $187 million renovation of Building 77 to provide space to vertically integrated design and manufacturing companies and the ground-floor Food Manufacturing Market; the Green Manufacturing Center, which houses New Lab, Crye Precision, and Bednark; and an expanded Steiner Studios, the largest film and television production studio outside Hollywood in the United States. BNYDC also recently announced a $2.5 billion master plan to create 10,000 additional jobs housed in vertical manufacturing buildings, which would bring the total number of jobs at the Yard to 30,000 in the coming decades.
Building 20 was constructed in 1865 and housed the production for the Navy’s first iron-plated wooden warships. Rogers Partners collaborated with Nanotronics to turn the warehouse into a vertically integrated advanced manufacturing headquarters for the company. Few advanced manufacturing facilities seamlessly integrate the entire process; bringing together R&D and manufacturing under one roof. Initially coined as New York City’s first “smart factory,” Rogers Partners designed the building to be cleaner and more efficient than traditional factories. The adaptive re-use on legacy infrastructure along with the design, greatly reduces carbon footprint. This work helped the project win an Architect’s Newspaper Best of Design award in 2019.
Nanotronics played a critical role in COVID-19 response efforts as well. BNYDC helped Nanotronics open half of Building 20 at the start of the pandemic to enable the implementation of Intelligent Factory Control (IFC) –a first step to building the tools that sequenced the virus’ genome, necessary for diagnosing SARS-CoV-2, identifying variants, validating the first vaccines, and the production of the vaccine itself.
In July 2020, ESD restructured the disbursement schedule for Nanotronics’ $2.25 million capital grant to assist with COVID-19 response efforts and frontloaded the funding to help the company accelerate production of nHale, a BIPAP machine it created for patients suffering from COVID-19
The new building is also a model for sustainable development. While the construction of the main shell for a similarly sized facility would result in approximately 1,971 metric tons of embodied CO2, the newly constructed portion of the project is estimated at approximately 425 metric tons. The building is one of the first Commercial Cross Laminated Timber (CLT) projects built in New York City – using CLT for the interior to act as a carbon sink. Altogether, the CLT stores an estimated value of 411.2 metric tons of CO2, effectively offsetting the new construction’s emissions and resulting in a carbon neutral project.
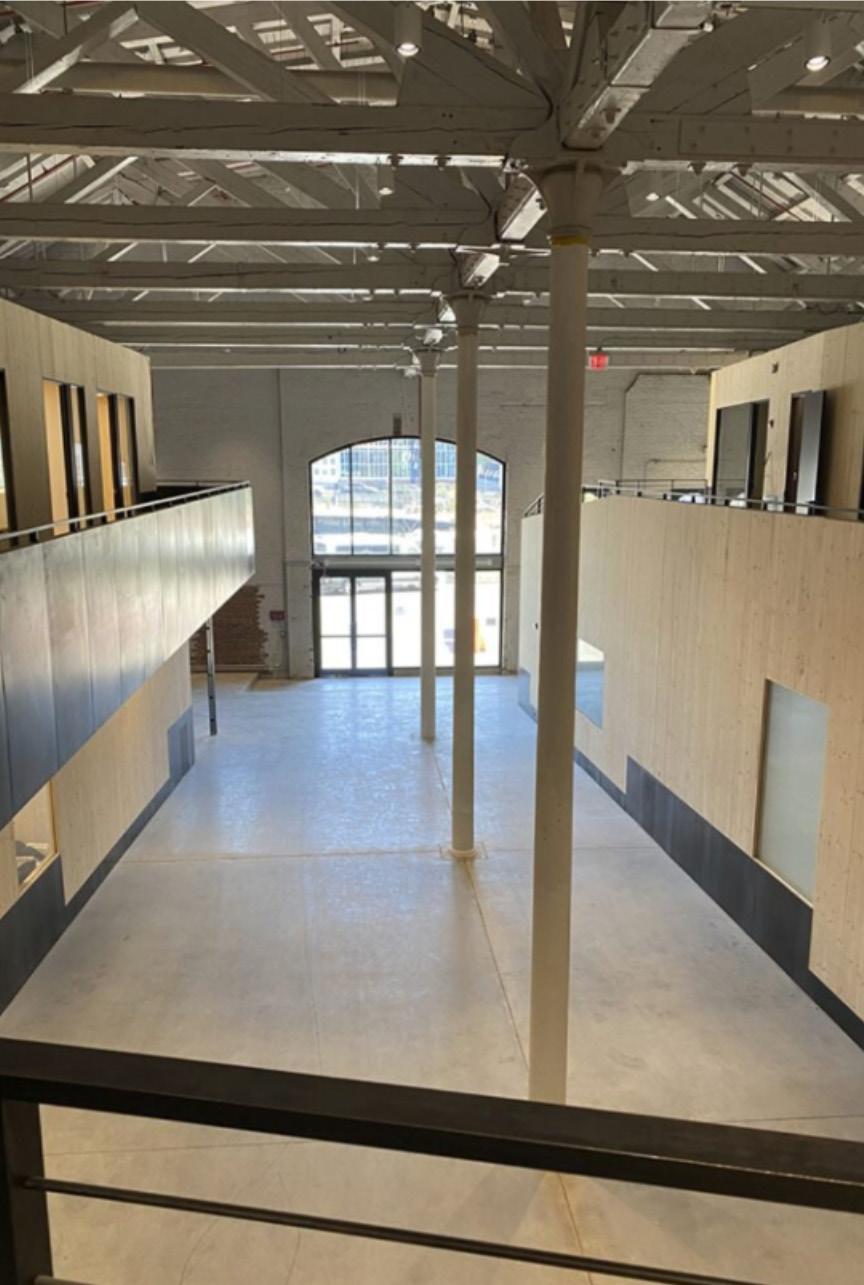