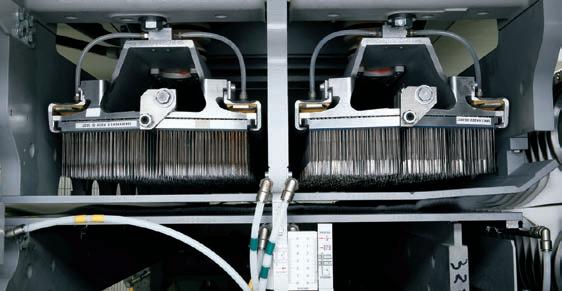
15 minute read
What’s New
Recycling fibers from garment waste into technical textiles
Pureko to install a new Andritz eXcelle needle-punching line for the recycling of garments. Founded in 2009, Pureko is one of the most important producers of nonwovens in Poland. The company’s nonwoven products are mainly used for wadding; they are free of chemicals, do not involve any health hazards, and are hypoallergenic. Pureko’s products carry top certificates such as INTERTEK, FIRA, OEKO-TEX, and the National Institute of Hygiene.
Advertisement
The final products will have fabric weights ranging from 300-500 gsm, and production capacity will be up to 750 kg/h. Installation and start-up are scheduled for the third quarter of 2021. This is the second ANDRITZ line to be supplied to Pureko, thus demonstrating the strong partnership between both companies. Three years ago, Pureko invested in a new, modern plant supplied by ANDRITZ Asselin-Thibeau to produce soft nonwovens in the furniture, textile, and clothing industries. The new line will enable Pureko to continue its ongoing growth.
Grand Textile specializes in functional fabrics and knits for sportswear, outdoor, and baselayers presented a nylon & spandex fabric combining different yarns and treated with the patented "Color Max" finish. Due to the different yarns on the face side, the color is absorbed differently during the dyeing process. The result is a unique pattern and color combination. The Color Max finish is currently manufactured exclusively in Taiwan.
The fabric was awarded the best product for fall/winter 2021/22 at the ISPO Textrends in the category of street sports. Besides, Grand Textile focuses on sustainability: for example, the company expands the share of recycled polyester yarns, and all chemicals are bluesign approved. In 2020, approximately 7.5 million meters of recycled poly fabrics were produced, an increase of 80 percent compared to the previous year.
The introduced functional fabric is made by a special dyeing process, with a unique pattern, and can be applied to any material, maintaining the fabric's original soft hand.
Color Max won the best product for ISPO 2021/22 sports category

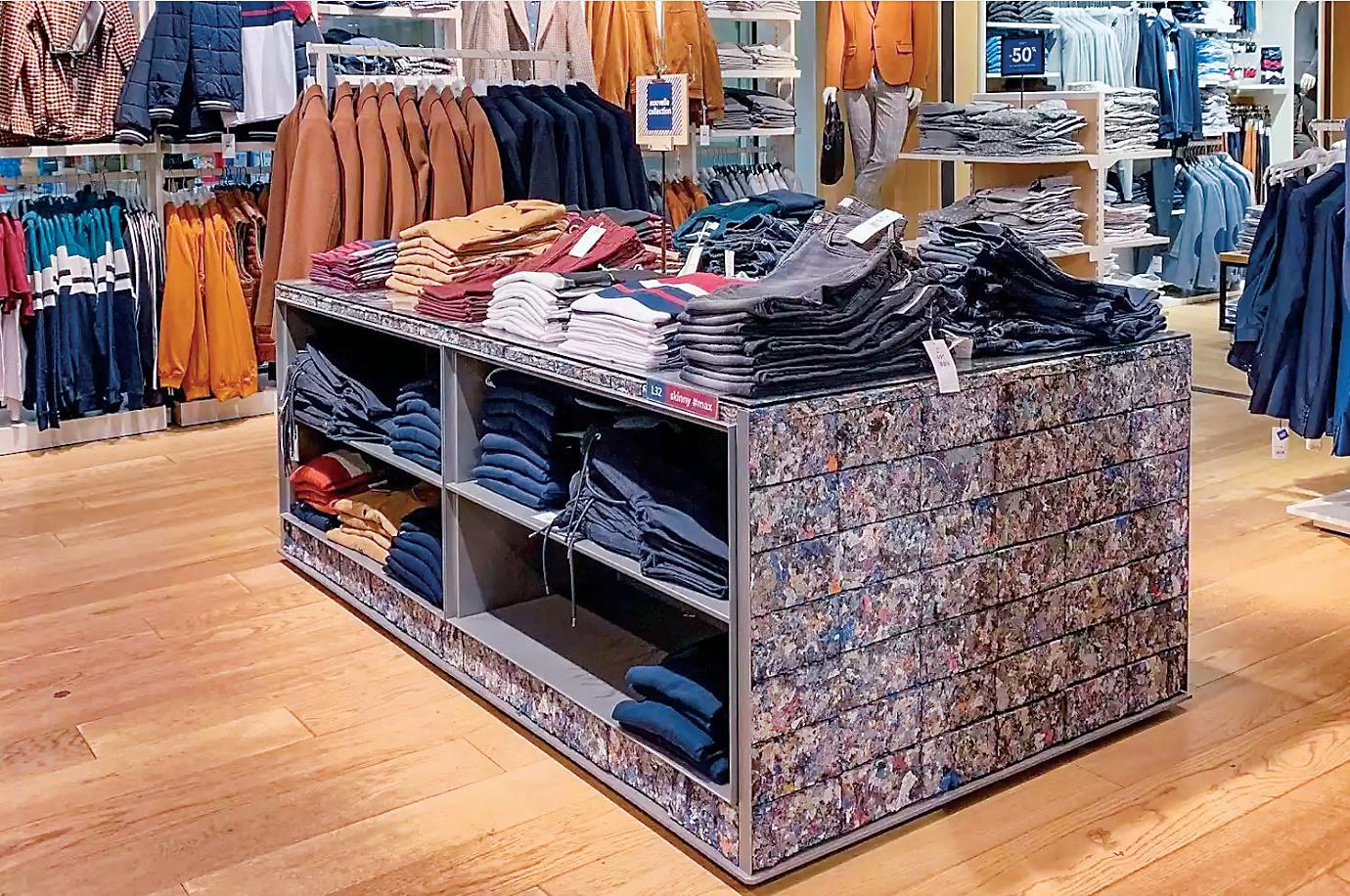
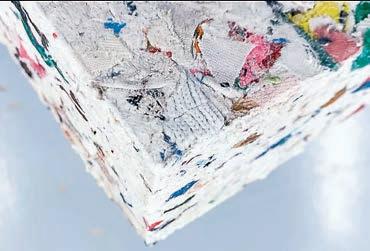
FabBRICK: An innovative company converting textile waste into beautiful bricks
Textile waste is a big problem around the globe. In France, it's estimated to be around 4 million tons, and that's just a fraction of what gets tossed globally; it was 17 million tons in the United States three years ago. Very little of that discarded clothing is collected for reuse or recycling, less than a third in France, and half of that (15%) in the U.S.
Clarisse Merlet, a French architecture, came up with the idea for FabBRICK, her award-winning company that makes decorative and insulative bricks out of old clothes. The basic component of the bricks is shredded clothing, which Merlet purchases pre-ground from a supplier in Normandy. Each brick uses the equivalent of two to three T-shirts' worth of material and, any kind can be used, including cotton, polyester, elastane, PVC, etc. The scraps are mixed with an ecological glue that Merlet developed herself, then pressed into a brick mold. This mold uses mechanical compression to form the bricks, so it requires no energy beyond what a human worker needs to press it down. The wet bricks are removed from the mold and set out to dry for two weeks before using.
At FabBRICK all creations are thought out and handcrafted in workshop in the heart of Paris. Since the creation at the end of 2018, the company had already designed more than 40,000 bricks which represent 12 tons of recycled textiles. Three machines have been developed to make the project bigger. The latest version has been duplicated five times, to be able to increase the production capacity. The next step is to industrialize the manufacturing process so that we will be able to recycle even more textile waste.
Royal DSM has announced mass-balanced bio-based Arnitel ® for lower carbon footprint to boosting its sustainability campaign. In this new range, a thermoplastic elastomer has been mixed with Sympatex Technologies. DSM’s bio-based Arnitel is manufactured with bio-based feedstock using a mass-balance approach*. The end product contains more than 25% bio-based content by weight.
Sympatex uses Arnitel to manufacture its waterproof, windproof, and breathable membranes for sports applications. The transition to bio-based feedstock will maintain the unique functional properties of Arnitel and will enable Sympatex to easily shift to a more sustainable solution with a lower carbon footprint without having to requalify materials.
Shruti Singhal, President DSM Engineering Materials, said: “I’m very proud that DSM is helping lead the transition to a circular economy by offering an increasing range of bio-based alternatives to our portfolio. This builds on our extensive experience developing sustainable solutions, in line with our purpose of creating brighter lives for all. And, by working with our partners across the value chain, we’ll keep driving sustainability in our industry to new levels and contribute to delivering a better future.”
After a very successful first Kickstarter campaign, Polygiene's partner Nordifakt is back on Kickstarter, and this time, they are bringing their efforts into the bedroom. They have created bacteria-free bedding using Polygiene Biostatic technology that inhibits the growth of odorcausing bacteria and will enable you to use more, wash less and save time.
Nordifakt says that bedding is treated with Polygiene®. It is one of the most advanced and sustainable silver fabric treatments available. The treatment consists of a low concentration of recycled silver salt (silver chloride), which is naturally found in both water and soil, effectively getting rid of bacteria, fungi, and other microbes. The treatment is applied at the finishing stages of the textile production, and field and lab tests show that it lasts the entire life-cycle of your bedding. There is no interference with bacteria naturally occurring on the skin - the technology is active only on the material's surface. It does not interfere with bacteria naturally found on the skin. There is no identified risk from dermal and oral contact with silver treatments. Polygiene® is not a nanosilver.
Nordifakt's Christianshavn bedding is made in 100% organic cotton, and OEKO-TEX® certified. Our technology partner Polygiene® is both OEKO-TEX® and Bluesign® certified. Nordifakt knows that eco-friendly and technology can go hand in hand. Eco-friendly does not mean we need to go back to horse-drawn carriage technologies to protect the environment. Instead, Nordifakt is finding ways to use technology positively, to improve and make the home textiles we surround ourselves with healthier, more efficient, and smarter. Nordifakt uses eco-technology to create products that help the environment by the concept; use more, wash less -saving both water and CO2.
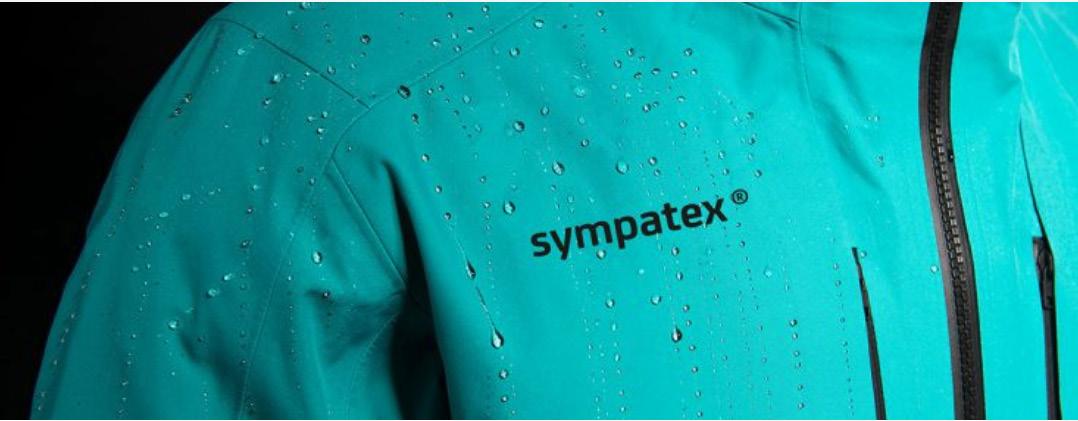
New antimicrobial bed clothing with Polygiene's technology
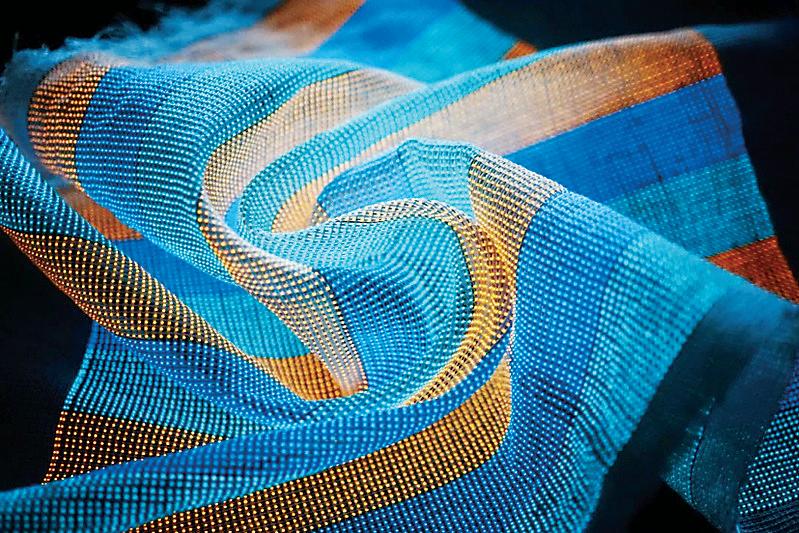
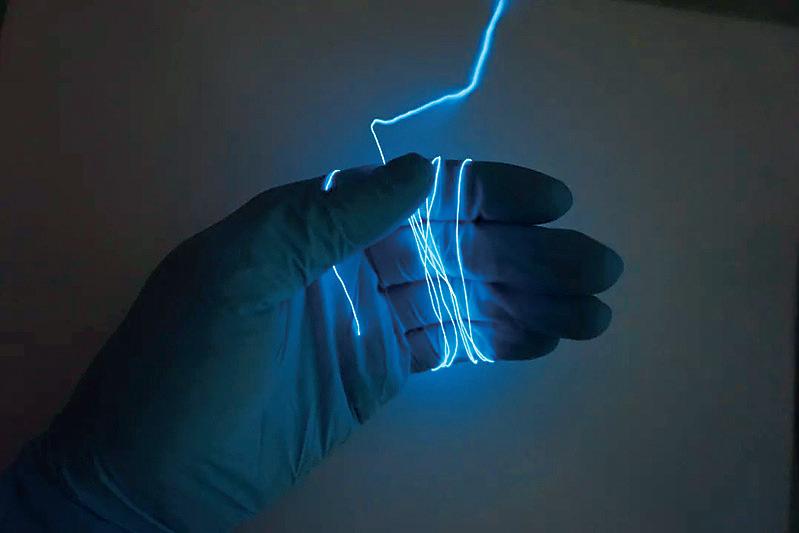
Researchers at Fudan University, China, have developed flexible, breathable, and durable textile material. According to Professor Huisheng Peng of Fudan's Department of Macromolecular Engineering, the new material is ideal for practical uses.
Weaving conductive weft and luminescent warp fibers forms micrometer-scale electroluminescent units at the weft–warp contact points. The brightness between electroluminescent units deviates by less than 8 percent and remains stable even when the textile is bent, stretched, or pressed. As the light-emitting fibers' diameter can be precisely adjusted between 0.2 mm and 0.5 mm, clothing woven with it can be ultra-fine and ultra-flexible. Fabrics will fit the human body's irregular contours and can be as light and breathable as ordinary fabric.
The researchers incorporated a touch-sensitive 16-button fabric keyboard, solar-energy-harvesting threads, and battery fibers into their textile to add interactivity and a power supply. They added electronics to wirelessly link it to a smartphone via a Bluetooth connection so users could send and receive messages on their sleeves and see real-time locations on a map. After 1,000 cycles of bending, stretching, and pressing, the vast majority of electroluminescent units' performance remained stable. Besides, the brightness of the electroluminescent units remained stable after 100 cycles of washing and drying.
Electronic textiles capable of communicating, sensing, and supplying electricity have been reported previously. However, textiles with functional, large-area displays have not yet been achieved because it is challenging to obtain small illuminating units that are both durable and easy to assemble over a wide area.
Professor Peng said that "With the integration of more functionality, we expect these smart textiles to shape the next generation of electronic communication tools. We have shown that an integrated textile system consisting of a display, keyboard, and power supply can serve as a communication tool, demonstrating the system's potential within the 'internet of things in various areas, including healthcare. Our approach unifies the fabrication and function of electronic devices with textiles."

M&S set high sustainability standards in denim
M&S introduces a new sustainability standard for denim that centers on better sourcing cotton, finishing, and dyeing. The action plan falls in line with Plan A, the company’s framework for a safer and more inclusive workforce, better products, and reduced impact on the environment.
According to the standards, all cotton used for all M&S clothing will be responsibly sourced. Through the Better Cotton Initiative (BCI), the majority helps farmers reduce their water usage and increase their profits. In the wash process, M&S is reducing its water intake by using technologies by sustainable finishing tech firm Jeanologia. M&S is also committed to switching out standard indigo dyes for cleaner alternatives that are safer for people and the planet and require less water and chemicals to produce. Monique Leeuwenburgh, head of product technology for M&S clothing and home, said, “Denim is a wardrobe staple for our customers, but we know now more than ever they want style where sustainability is built in as standard. By taking collaborative action with our denim suppliers, we can give our customers the confidence that every pair of M&S jeans they buy for the family are not only stylish, great quality, and fantastic value, but have been responsibly made too.”
M&S has started switching all denim to more sustainable indigo dyes, including nearly 50 percent of the new range, which also uses 86 percent less water than the industry average for denim finishing and 100 percent responsibly sourced cotton. M&S has brought the new sustainability features to life in its Spring/Summer marketing campaign.
Protective nonwovens for maximum safety amid COVID-19
Piana Group has introduced their patented fiber treatment technology to provide maximum protection regarding viruses and microbes. The innovative Piana Protection technology enables any textile or porous surface to be protected with a durable antiviral and antibacterial treatment.
The solution relies upon advanced silver chemistry and patented Piana fiber treatment processes that ensure efficacy within minutes of contact. Independent laboratory tests have shown a 99.8% reduction in viral activity in the first 30 minutes and 99.995% viral reduction after one hour. This new technology is highly versatile and will soon be integrated into a host of other consumer products including pillows, mattress toppers, filtration and seating applications. The proprietary antiviral and antimicrobial solution is
pending approval by the U.S. Environmental Protection Agency.
Piana Group products are manufactured using patented, ecologically sound manufacturing processes and are 100% recyclable, minimizing and reusing waste through its highly transparent, eco-friendly operations in Cartersville, GA, and San Luis, AZ. Piana Group is the 439-year-old textile company known for breakthrough chemical treatment innovations for fiber and nonwoven textiles in automotive, appliance and bedding markets.
Piana Protection fiber technology is currently specified for use in face masks which are pending final approval by the U.S. Food and Drug Administration and will be available in the market in Spring 2021.
Naveena Denim, Karachi, Pakistan, has an exclusive agreement to develop denim fabrics featuring the new bio-based Dyneema. By adding a small percentage, less than 10% of Dyneema to fabrics, the abrasion resistance by 100%, when compared with 100% cotton denim fabrics.
Dyneema is an ultra High-molecular-weight polyethylene (UHMWPE) that is many times stronger than steel and its ability to replace steel has, for example, resulted in ropes that have 75% less weight, with all of the advantages that brings in terms of towing, mooring, anchoring etc. In addition, ropes made from the fiber have ten times the working life of steel equivalents.
In traditional Dyneema production, the polymer is dissolved in a solvent and then spun through spinnerets in a proprietary process. Successively, the spun solution is solidified by cooling, which fixes a molecular structure which contains a very low entanglement density of molecular chains. This structure gives an extremely high draw ratio and results in the fiber’s extremely high strength. The solidified fiber has a gel-like appearance and contains an almost 100% crystalline structure with perfectly arranged molecules, which promotes its extremely high strength, modulus, and other properties.
Rashid Iqbal, executive director at Naveena Denim, said, “We have been partners with DSM since 2015 and together we have produced some of the most durable and strong denims for workwear groups and motorcyclists in Europe and the USA. We share common values when it comes to sustainability and sustainability starts with the enhanced durability of the denim.”
Peto Verdaasdonk, application development specialist at DSM, said, “We are in a unique position because we are the only ultra-high molecular weight polyethylene fiber produced in the world that is backward integrated. This means we have been able to work with our raw material suppliers and arranged that they replace oil-based materials with renewable feedstock. This further enhances the carbon footprint of the fiber.”
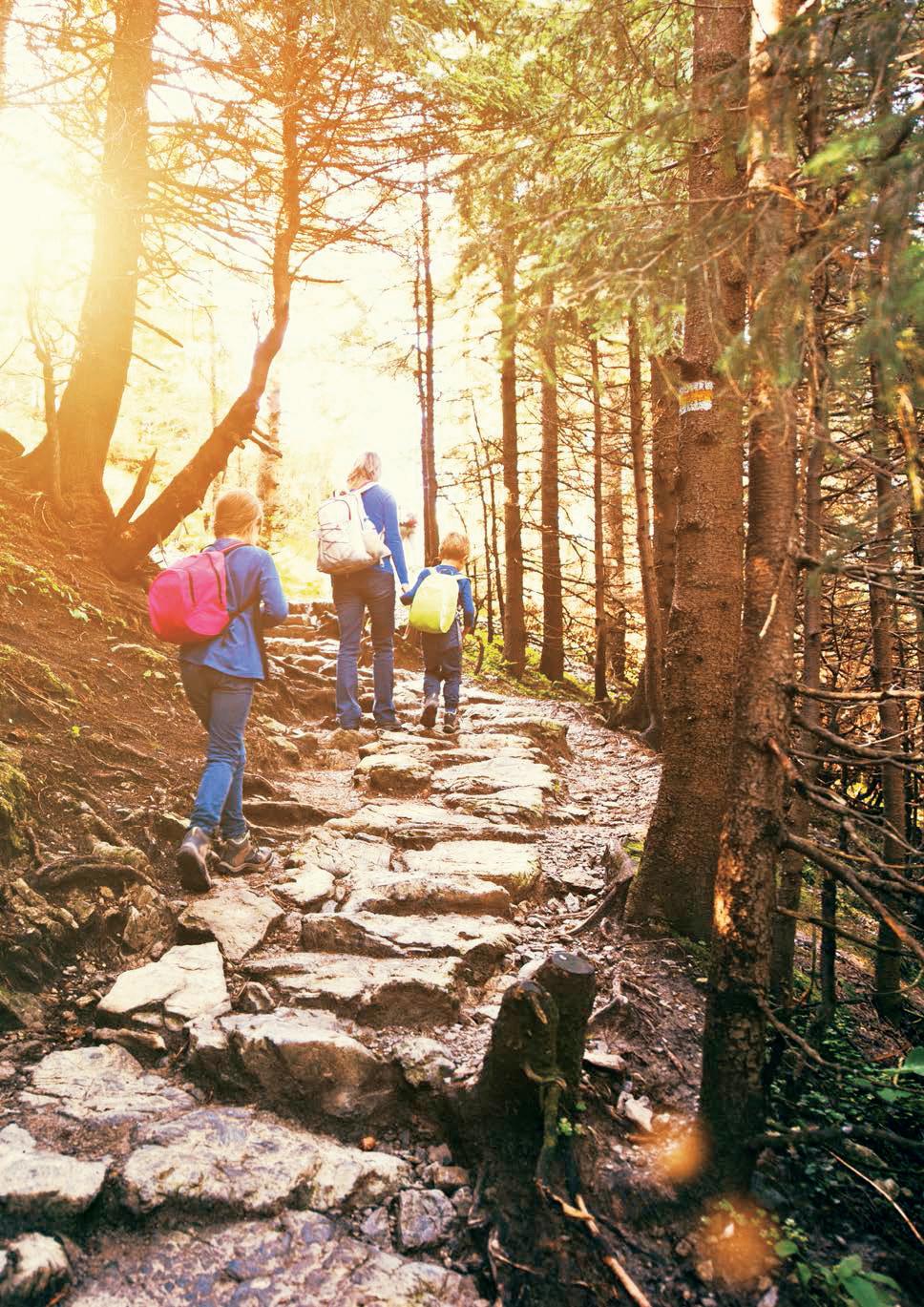
Purissimo: A natural allergen control technology for textiles
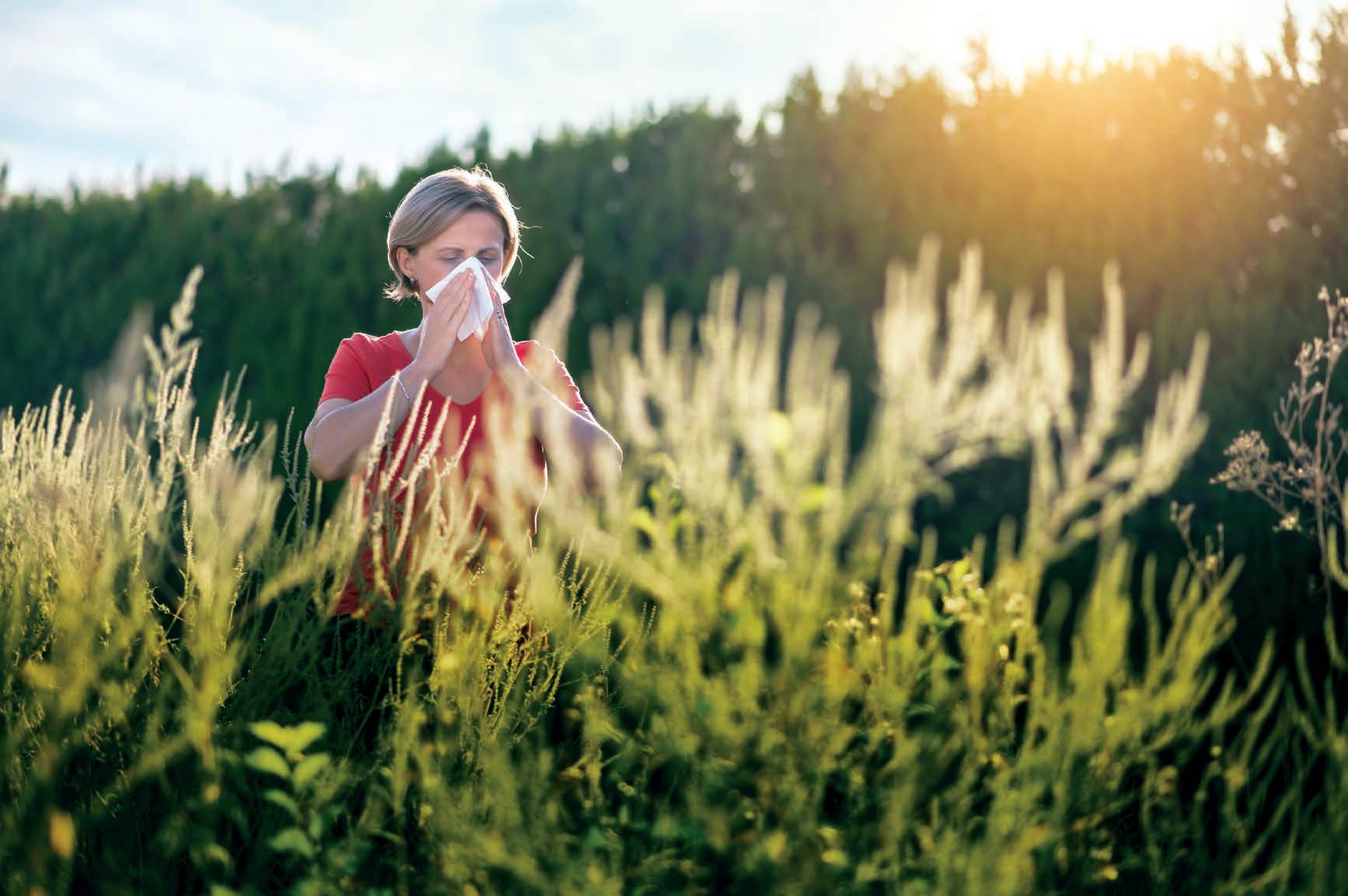
Purissimo is allergen control technology produced by Devan of Ronse Belgium. The new finish has been found effective against allergens from pollen. The technology had already been proven to significantly reduce the number of allergens from house dust mites and pets. Inactive probiotics as spores are encapsulated and integrated into the textiles. Friction opens the microcapsules and releases the spores which absorb humidity and self-activate and are then transformed into probiotic bacteria that start to consume the allergens.
Pollen is one of the most common causes of allergies in the United States. Pollen is a very fine powder produced by trees, flowers, grasses, and weeds to fertilize other plants of the same species. Many people have an adverse immune response when they breathe in pollen.
The immune system normally defends the body against harmful invaders, such as viruses and bacteria, to ward off illnesses. In people with pollen allergies, the immune system mistakenly identifies the harmless pollen as a dangerous intruder. It begins to produce chemicals to fight against the pollen. This is known as an allergic reaction, and the specific type of pollen that causes it is known as an allergen.
Sofie Depluverez, PhD researcher at Devan, said, “Allergens are small protein molecules, which can cause allergic reactions and asthma. All allergy sufferers are different when it comes to their sensitivity to allergens, but few people are only allergic to a single allergen and the effects of multiple allergens can add up. The key to reducing and even eliminating symptoms is to reduce your exposure to the allergens themselves. As time goes by, the various allergens start to build up inside the house, certainly when ventilation is limited. As the allergen concentration increases – especially in combination with seasonal allergens such as pollen, the allergy threshold may be reached if no allergen reduction measures are in place. As the probiotics consume the allergens, exposure is gradually reduced to below threshold levels. Therefore, individuals with respiratory allergies will be exposed to fewer attacks.”
Recycling breakthrough: Researchers have successfully converted cotton into Spandex and Nylon
So far, recycling cotton means converting into other cotton products. What if we could recycle cotton into Nylon and Spandex? Is it possible? The answer is a big YES! Researchers from Sweden’s Lund University have found a way to convert cotton into sugar, which in turn can be made into spandex, nylon, or ethanol.
Edvin Ruuth is working at the Department of Chemical Engineering in Lund. There is a great deal of information about using micro-organisms and enzymes to transform the “tougher” carbohydrates in biomass into simpler molecules. This means that everything from biological waste and black liquor to straw and wood chips can become bioethanol, biogas and chemicals. In the new research, scientists have succeeded in breaking down the plant fiber in cotton, the cellulose, into smaller components. However, no micro-organisms or enzymes are involved. Instead, the process involves soaking the fabrics in sulphuric acid. The result is a clear, dark, amber-colored sugar solution.
The researchers started making glucose out of fabrics a year ago, the return was a paltry three to four per cent. Now he and his colleagues have reached as much as 90 per cent. Once the recipe formulation is complete, it will be both relatively simple and cheap to use. However, for the process to become a reality, the logistics must work. There is currently no established way of managing and sorting various textiles that are not sent to ordinary clothing donation points.
Fortunately, a recycling center unlike any other in the world is currently under construction in Malmö, where clothing is sorted automatically using a sensor. Some clothing will be donated, rags can be used in industry and textiles with sufficiently coarse fibers can become new fabrics. The rest will go to district heating.
Hopefully, the proportion of fabrics going to district heating will be significantly smaller once the technology from Lund is in place. From a normal sheet, they extract five liters of sugar solution, with each liter containing the equivalent of 33 sugar cubes. However, you couldn’t turn the liquid into a soft drink as it also contains corrosive sulphuric acid.
Ruuth said, “What makes cotton unique is that its cellulose has a high crystallinity. This makes it difficult to break down the chemicals and reuse their components. In addition, there are a lot of surface treatment substances, dyes and other pollutants which must be removed. And structurally, a terrycloth towel and an old pair of jeans are very different. Thus it is a very delicate process to find the right concentration of acid, the right number of treatment stages and temperature.”
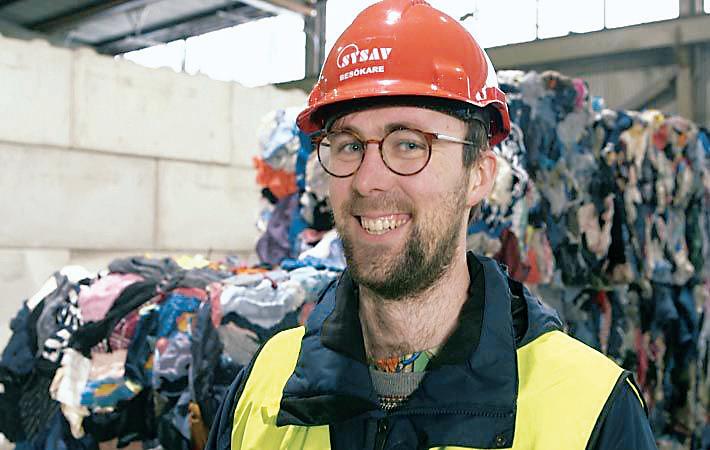