
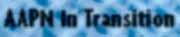


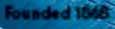
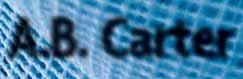

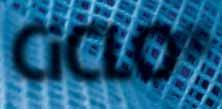


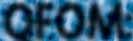



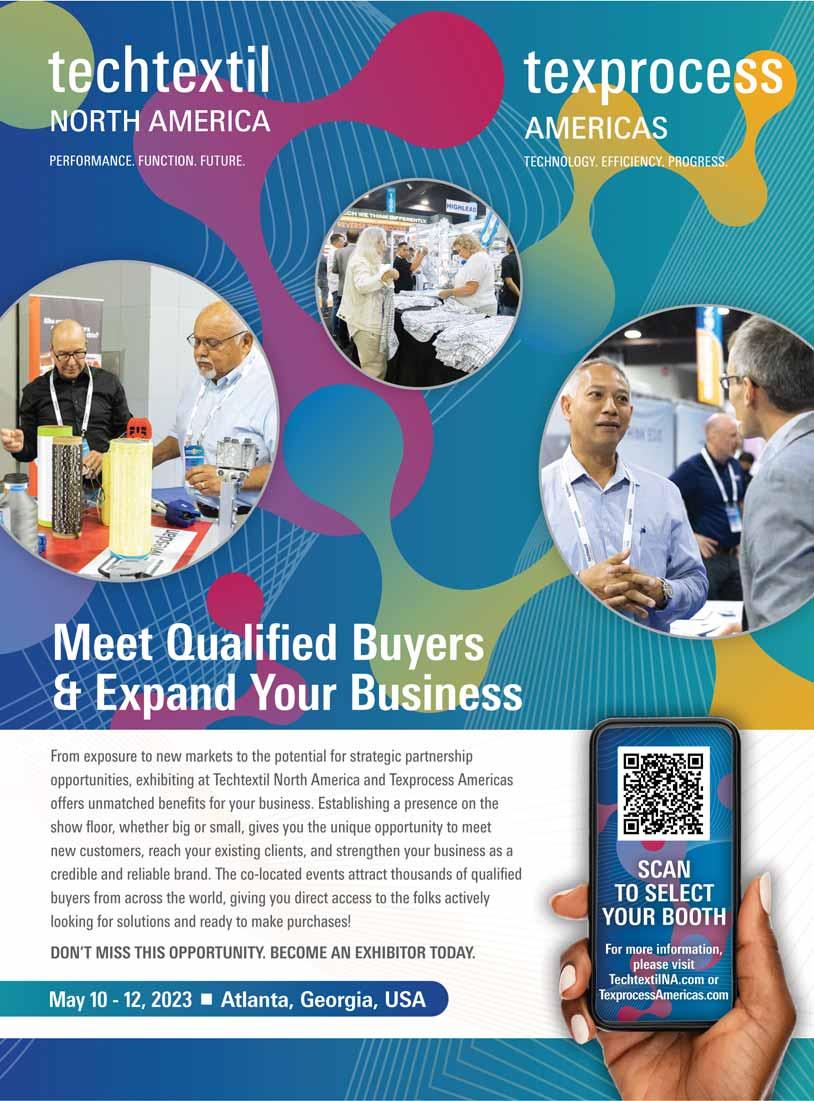
10 Executive Forum: Andrea Ferris Co-founder and CEO of Intrinsic Advanced Materials and Co-inventor of CiCLO® technology
14 From Traveling Traveler Salesman To Traveler Expert Driven to innovate and exceed customers’ expectations, A.B. Carter recently celebrated 100 years in business.
32 Three Ways Digitalization Can Streamline Textile Production Digital color management programs simplify the color approval process and ensure accuracy in the supply chain.
34 Automation: A Key To Successful Textile Production Stäubli Textile offers automation solutions for today’s modern weaving mills including the SAFIR automatic drawing-in machines.
ON THE COVER:
Junes designs reusable bags that are “cute, foldable and affordable” with sustainabilty in mind. Its signature fabric, branded as bio-knit®, is made from recycled plastic bottles and CiCLO® Technology to reduce the persistence of man-made microfiber pollution.
4
6
35
36
37
38
17 50 Years Of SYFA
A preview of the upcoming fall conference and anniversary event
18 A Time For Celebration: 50 Years Of Leadership In Synthetic Fibers
From its beginnings as TYAA in 1972, SYFAhas adapted to weather industry downturns and is celebrating its 50th anniversary this year.
Philippa Grogan, a consultant with Eco-Age, discusses greenwashing and best practices for communicating sustainability claims.
AAPN recently announced Lynsey Jones as transition advisor
28 News
29 New Method Can Remove Dyes From Wastewater
Recent research focused on using polymer to clear dyes from wastewater
30 It’s Time To Bring Fashion And Textile Production Home Sustainable, on-demand production provides opportunity for reshoring operations
VOL. 172, No. 5 / TEXTILE WORLD (ISSN 0040-5213) is published bimonthly by Textile Industries Media Group, LLC, PO Box 683155, Marietta, GA 30068, and incorporates Modern Textiles, Textile Industries, Fiber World and Knitting/Apparel magazines, which remain the property of Textile Industries Media Group, LLC. Copyright 2022, Textile Industries Media Group, LLC Title registered with the U.S. Patent Office. All rights, including translation into other languages, reserved. Subscription rates for one year are: $65 (US); $85 (Canada and Mexico); $130 (Other International). Single copy rates are: $15 per copy. All prices are in U.S. dollars and all orders must be prepaid. Questions may be submitted to jdavis@textileworld.com. To obtain electronic copies of print articles, please contact ProQuest at www.proquest.com. To obtain microform copies, please contact NA Publishing at www.napubco.com.
POSTMASTERsend address changes to: Textile Industries Media Group, LLC, PO Box 683155, Marietta, GA 30068. Send Canadian address changes to: Textile World, c/o The Mail Group, P.O. Box 25542, London, ON N6C 6B2, Canada. Customer #7007632 Publications Agreement #40612608.
IInthis issue of Textile World ,the cover story,“CiCLO®: Just One Arrow In The Microfiber Pollution Solution Quiver” highlights three impressive points.
It is refreshing to see the U.S.textile industry acknowledge,address and invest in solving serious environmental challenges.
Environmental issues facing the industry have always been taken seriously,but on some level the industry has had a contentious relationship with environmental regulators.
There is a strong history of progress on improving the relationship and impact of textile manufacturing on the environment — who doesn’t want clean air,clean water and efficient use of clean power?
In truth,the relationship between textile manufacturing and the environment really has moved to the next level.
Now,in some cases,effluent leaving the plant is cleaner than the water entering the plant.Technological improvements in textile dyeing,printing and finishing have reduced both consumption and waste of water,dyes and chemicals.Digital printing,new indigo technology,waterless dyeing,and improved foam and spray application of finishes are perfect examples.
The next level of improvement is focused on embracing sustainability and the full life cycle of products the industry creates.
Recycling technologies have moved from a fringe group of manufacturers to the mainstream with recycled polyester in common use.Apparel brands have been supportive and demanded sustainable solutions for their products which has encouraged manufactures to invest and innovate with new technologies.
Acknowledging the man-made microfiber pollution challenge — the impact fiber and plastic five millimeters in length loose in the environment — goes a long way to developing serious solutions.
The CiCLO story is a prime example of developing a serious solution.As Co-founder and CEO of Intrinsic Advanced Materials and Co-inventor of CiCLO technology
Andrea Ferris explained:“CiCLO technology gets blended with conventional or recycled polyester and nylon during melt extrusion at the very beginning of the fiber manufacturing process.It becomes permanently embedded in the fiber,so it never washes out.”
CiCLO provides nutrients that encourages microbes to biodegrade the polyester or nylon within which the CiCLO is embedded. One can only imagine the breadth of environmental impact this technology will have and the proof is in the partnership.
In 2018,Intrinsic Textiles Group LLC and Parkdale Advanced Materials — the fibers and yarns innovation division of Parkdale Inc., Gastonia,N.C.— formed a joint venture named Intrinsic Advanced Materials.
Ferris stated:“As the largest spun yarn manufacturer in the Western Hemisphere, Parkdale’s production of polyester-containing yarns exceeds 500 million pounds per year.It has taken a leadership position in delivering sustainable solutions for the textile industry and CiCLO is the proven technology to mitigate microfiber pollution generated by man-made textiles.”
It is that kind of leadership — acknowledging,addressing and investing in solving serious environmental challenges that takes the textile industry’s relationship with the environment to the next level — and into the future.
James M. BornemanJames M. Borneman
Rachael S. Davis
Dr. Lisa Parillo Chapman, Dr. Peter J. Hauser, Dr. Trevor J. Little, Dr. William Oxenham, Dr. Behnam Pourdeyhimi, Dr. Abdel-Fattah Seyam, Dr. Andre West
Robert S. Reichard
YARN MARKET EDITOR
Jim Phillips
CONTRIBUTING EDITORS
Jim Kaufmann
Stephen M. Warner
INTERNET CONTENT EDITOR
Rachael S. Davis
Julie K. Brown-Davis
ADVERTISING BUSINESS MANAGER
Denise Buchalter
ART DIRECTOR & PRODUCTION MANAGER
Julie K. Brown-Davis
UNITED STATES & CANADA
Turner Marketing &Media, LLC
Telephone +864-594-0921 Fax +864-439-5070 E-mail: sturner@textileworld.com
EUROPE (except ITALY)
Sabine Dussey Telephone +49-171-5473990 E-mail: sabine.dussey@dussey.de
Ferruccio &Filippo Silvera Telephone +39-022-846716 Fax +39-022-8938496 E-mail: info@silvera.it
James M. Borneman Telephone +678-483-6102 E-mail: jborneman@textileworld.com
MEXICO, CENTRAL & SOUTH AMERICA
Virgilio L. Gonzalez Telephone +58-412-622-2648 Fax +58-212-985-7921 E-mail: vlgonzalezp@gmail.com
CLASSIFIEDS & INTERNET
Julie Davis
Telephone +678-522-0404 E-mail: jdavis@textileworld.com
PO Box 683155
Marietta, Georgia 30068, USA Telephone +678-483-6102
BIOPHIL Natural Fibers,a hemp stalk processor with a processing facility in Pennsylvania,has announced plans to invest more than $10.9 million in a new operation in Lumberton,N.C. The company produces fiber and hurd from the stalks,which can be used in a variety of applications from construction to paper and nonwovens and woven textiles.The new 90,829square-foot facility will have decortication equipment as well as parallel processing lines to further clean,refine,and cut hurd and fiber to customer specifications.The operation also will house research and development for mycelium load-bearing structural composites by Okom Wrks Labs,as well as prototyping and eventually manufacturing for hurd-based construction materials and other hemp-based products.
Biophil will hire 41 associates for the new facility including production,administrative and managerial roles with an average starting salary of more than $40,000.
Milliken & Company recently announced it has expanded its domestic yarn spinning capacity with the acquisition of a plant —
previously known as Frontier Spinning Plant #3 and located in Mayodan, N.C.— from Montrealbased Gildan Activewear Inc.The open-end spinning facility will make yarn for Milliken’s protective fabrics, workwear,government and defense,industrial, and napery businesses. Milliken will rename the plant Two Rivers Plant. “Investing in this plant enhances the agility of Milliken’s Textile Business and shores up our supply chain in the U.S.to benefit our customers,”stated Halsey Cook,president and CEO.“Guided by integrity and excellence in all we do,this move bolsters our supply chains to enhance customer service.”
The board of directors of the American Floorcovering Alliance Inc.(AFA) recently voted to dissolve the floor covering advocacy organization.Pandemic-related revenue shortfalls and event cancellations were factored into the decision. The board agreed to donate a cash balance of $135,000 that remained to Georgia Northwestern Technical College (GNTC) to support flooring industry education programs.GNTC — which added a Flooring Production program in 2019 comprising of a Flooring Production Operator and Flooring Production Technician certificate
The Washington-based National Council ofTextile Organizations (NCTO) recently hosted two roundtables — one with Representative Greg Murphy (R-N.C.) and a second with Congresswoman Kathy Manning (D-N.C.) — and both featuring textile executives from the fiber,yarn,fabric and finished textile product sectors.The meetings were designed to highlight the importance of the industry and urge the lawmakers to back policies that support the competitiveness of the U.S.textile industry.
The event with Representative Murphy was hosted by East Carolina University in Greenville, N.C.;while Unifi Inc. hosted the roundtable with Representative Manning at its headquarters in Greensboro,N.C.
Executives spoke about the innovative and sustainable production practices, as well as the industry’s contribution to the state of North Carolina.According to U.S.government data, textile jobs employ more than 36,000 people in the state and support a further 108,000 jobs.The state also leads the nation with its $2.7 billion in textilerelated exports.Executives also raised priority issues
program — was selected to receive the funds based on its essential role in workforce development for the floor covering industry.
for the industry in Washington such as maintaining the yarn forward rules of origin in the Dominican Republic-Central America Free Trade Agreement (CAFTA-DR),advancing the Miscellaneous Tariff Bill,and upholding buy American and Berry Amendment procurement policies,among other issues,
“As the proud representative for North Carolina on the Ways and Means Committee,it’s an honor to work alongside NCTO to promote American jobs, grow our state economy, and protect domestic manufacturing,”Representative Manning stated.
“I am thrilled to engage with industry leaders in my district,as we discuss ways to grow the U.S. textile industry and the critical role that textile manufacturers play in our local,state,and national economy,”Congresswoman Manning said.
NCTO President and CEO Kim Glas expressed her sincere appreciation to both lawmakers for participating in the meetings.“It is imperative that we have sound trade and government procurement policies that help the U.S.industry continue to grow jobs and contribute to the overall U.S economy,”Glas noted.
“Upon the dissolution of AFA,we determined that the balance of cash after liquidation would be best used by local colleges
to assist in training and recruiting students to help fill the employment gap and provide skilled talent to the industry,”said Stephanie Manis,owner of Capital Contract Services and former executive director of AFA.
A memorandum of understanding (MOU) recently was signed between North Carolina State University,Gaston College and Catawba Valley Community College, and Honduras-based Central American Technological University (UNITEC) in an effort to educate and train a next-generation textile workforce using training and certificate programs as well as undergraduate and graduate degree programs.An increase in nearshoring and onshoring in Honduras,Central America and the United States is leaving the industry with a shortage of trained workers.
With almost $1 billion of textile and apparel investment in the United States and Central America anticipated this year,employee growth projections over the next five years suggest more than 10,000 new skilled workers will be needed to meet the demands of the industry in Honduras alone.
The MOU,backed by the U.S.Department of State,also creates an educational pathway to economic opportunity in Honduras and the region.
A signing ceremony was held at Gaston College in Dallas,N.C. Both U.S.and Honduran government officials — including Jose W.Fernandez, under secretary of state for Economic Growth,Energy and the Environment; Jennifer Knight,deputy assistant secretary for Textiles,Consumer Goods and Materials at the U.S. Department of Commerce; and Hector Zelaya,private secretary to Honduran President Xiomara Castro — participated in the signing,as well as a roundtable discussion that followed.In addition, the government officials toured two of Gildan Activewear’s yarn spinning facilities in Salisbury,N.C.
Radians is expanding its Memphis,Tenn.,campus with a new building.The manufacturer of a wide variety of personal protective equipment required additional space for its growing warehouse operation.The addition will allow the company to have more inventory in-house and grow its supply chain capabilities.Additionally, the new facility will process orders for some big box retailers and large industrial customers.
“The increase in space is significant because the expansion represents a 20 percent increase in Radians’overall square footage,bringing our Memphis campus footprint to approximately eight acres under roof,”said Radians CEO Mike Tutor. TW
AAfter a string of months in which demand for U.Smade yarns remained remarkably high, especially considering inflation rates and a slowing economy, the past few weeks have seen a slight-to-moderate drop in inquiries and orders for a number of spinners.
“I think we’re in a lull — a temporary one, I hope — because the market is currently saturated,” said one source. Added another, “The retail pipeline looks to be full at the moment. Store shelves are generally well stocked, and our customers are hesitant to place new orders until they see how the economy goes. Fingers are crossed at this point that we can avoid a recession, but the odds of that seem to be decreasing day by day. Consumers have already begun to tighten up their pocketbooks.”
In fact, The Expectations Index, part of the Consumer Confidence Index published by The Conference Board®, although recovered slightly in August from July’s nineyear low, still remains below a reading of 80, suggesting recession risks continue. Consumer concern about inflation remains elevated, but has retreated from the high of previous months.
Spot quotations for the base quality of cotton (color 41, leaf 4, staple 34, mike 35-36 and 43-49, strength 27.0-28.9, and uniformity 81.0-81.9) in the seven designated markets measured by the USDA averaged 108.53 cents per pound for the week ending September 15, 2022. The weekly average was up from 90.71 cents reported for the corresponding period a year ago. Daily average quotations ranged from a high of 111.07 cents Monday, September 12 to a low of 106.10 cents Thursday, September 15. Spot transactions reported in the Daily Spot Cotton Quotations for the week ended September 15 totaled 7,467 bales. This compares to 7,613 spot transactions reported the corresponding week a year ago. Total spot transactions for the season were 20,447 bales compared to 24,772 bales during the same period a year ago. The ICE October settlement price ended the week at 105.24 cents.
In other cotton news, Cotton Incorporated, as part of the USDA Partnership for Climate-Smart Commodities pilot project, is collaborating
with industry leaders to focus on increasing the adoption of climate-smart agriculture practices. The project will build markets for climate-smart cotton and provide technical and financial assistance to more than 1,000 U.S. cotton farmers to advance adoption of climate-smart practices on more than one million acres. This will allow the production of more than four million bales of climatesmart cotton over five years.
“The climate-smart cotton program brings together USDA with private industry resources to increase the production and demand for climate-smart cotton that will help the U.S. cotton industry meet the ten-year sustainability goals,” noted Dr. Jesse Daystar, vice president and chief sustainability officer for Cotton Incorporated.
Eastman, maker of Naia™ Renew sustainable fibers and yarns, is collaborating with Patagonia® to offer a limited run of T-shirts made with Naia Renew ES — Eastman’s latest fiber offering made with increased recycled content.
Named for its enhanced
sustainability, Naia Renew ES is made with 60 percent recycled content. Unlike other cellulose-based yarns and fibers, this option requires fewer virgin materials to make an environmentally friendly product. Naia Renew ES is made from a combination of 40 percent molecularly recycled waste material, 20 percent recycled cellulose, and 40 percent renewable wood pulp.
The 20 percent recycled cellulose comes from waste materials, textiles waste and non-forest-derived cellulose waste. This innovation is made possible through Eastman’s continuous efforts to collaborate with eco-conscious partners throughout the value chain. For example, the Naia team has partnered with GP Cellulose, a pulp supplier with a focus on sustainability, to integrate renewable forest fibers and non-forest fiber solutions into its feedstock.
The remaining 40 percent recycled content comes from Eastman’s molecular recycling technology that breaks down hard-to-recycle waste materials like plastic packaging and old carpet into fundamental building blocks to produce the acetic acid used to make cellulose acetate yarn and fiber. TW
COTTON FIBER (BASE GRADE)
CARDED COTTON
COMBED COTTON
POLYESTER/ CARDED COTTON
CURRENT6 MO. AGO1 YR. AGO Spot Market, ¢/lb.108.53117.8786.31
Ring-Spun 100% Carded Cotton
YARN TYPECURRENT6 MO. AGO1 YR. AGO 10/13.203.102.04 18/13.333.132.07 24/13.413.312.24 30/13.423.332.25 12/23.773.682.61 20/23.903.802.69
Ring-Spun 100% Combed Cotton
YARN TYPECURRENT6 MO. AGO1 YR. AGO 18/14.204.022.79 26/14.374.192.87 30/14.704.523.16 38/14.774.593.23
Open-End Spun 100% Carded Cotton
YARN TYPECURRENT6 MO. AGO1 YR. AGO 4/12.972.961.22 10/13.133.031.27 16/13.193.091.32 18/13.253.151.38 20/13.353.241.47
Ring-Spun 50/50% Polyester/Combed Cotton
YARN TYPECURRENT6 MO. AGO1 YR. AGO 20/13.422.482.33 30/13.512.572.39
ACRYLIC & RAYON
Ring-Spun 50/50% Polyester/Carded Cotton Open-End Spun 50/50% Polyester/Carded Cotton
YARN TYPECURRENT6 MO. AGO1 YR. AGO 20/13.203.092.19 30/13.353.252.26
YARN TYPECURRENT6 MO. AGO1 YR. AGO 12/12.702.551.14 14/12.822.681.27 18/12.832.691.47 24/12.962.821.51 28/12.972.831.55
Open-End Spun 100% Acrylic (worsted count)
YARN TYPECURRENT6 MO. AGO1 YR. AGO 1/123.303.103.10 1/183.353.153.15 1/243.423.223.22 1/283.473.273.27 1/323.683.483.48
Ring-Spun 100% Polyester (whites only)
SPUN POLYESTER
YARN TYPECURRENT6 MO. AGO1 YR. AGO 8/12.072.002.24 16/12.692.622.36 20/12.822.752.49 22/12.922.852.59 30/13.233.232.97
Open-End Spun 100% 1.2 Denier Rayon
YARN TYPECURRENT6 MO. AGO1 YR. AGO 20/14.564.564.56 30/14.794.794.79
MAN-MADE FIBERS/ FILAMENTS
Ring-Spun 100% Polyester (dyed)
YARN TYPECURRENT6 MO. AGO1 YR. AGO 8/13.673.673.42 16/13.883.883.63 20/13.963.963.69 22/14.0140.13.77 30/14.394.394.14
Filament Polyester Partially Oriented Yarn (POY)Textured Nylon
YARN TYPECURRENT6 MO. AGO1 YR. AGO 70/23.453.453.45 100/23.583.583.58
Textured Polyester (knits)
YARN TYPECURRENT6 MO. AGO1 YR. AGO 70 denier2.202.202.20 100 denier2.142.142.14 150 denier2.082.082.08
Man-Made Staple Fiber
YARN TYPE
CURRENT6 MO. AGO1 YR. AGO 70 denier (dyeable)2.212.212.01 70 denier (whites)2.252.251.93 100 denier 1.921.921.72 (dyeable
den. (dyeable)1.871.871.67 150 den. (whites)1.851.851.65
YARN TYPE CURRENT6 MO. AGO1 YR. AGO Polyester (1.5 denier) 2.22-2.362.22-2.362.22-2.36 Acrylic (3.0
2.08-2.242.08-2.242.08-2.24
All yarn prices in U.S. dollars per pound & asking prices only. Prices compiled from 9/20/22 See TextileWorld.com for archived Yarn Market data.
Intrinsic Advanced Materials — a joint venture between Intrinsic Textiles Group and Parkdale Advanced Materials — offers a solution to man-made microfiber pollution with its CiCLO®technology.
TW Special ReportMMicroplastics
— defined by the U.S. National Oceanic and Atmospheric Administration as any piece of plastic less than 5 millimeters in length — are harmful to marine and aquatic life,and,like it or not,textiles have been found to be a contributor to microplastics in the environment in the form of microfibers.Such particles are too small to feasibly recover and once in the environment,they persist because they do not biodegrade naturally.The full extent of the problem is still being studied,but between the millions of tons of apparel and other textile products sent to landfills each year,as well as fiber shedding from textiles during use and laundering, much work is to be done to reduce the impact of textile fibers in the environment.
Realistically,there is no “one-size-fits-all”solution
and companies are tackling the problem in a variety of ways — from developing new recycling technologies that can handle mixed waste streams to recover and recycle plastic an almost infinite number of times, to encouraging circular economies and textile reuse.
Another strategy employed by Intrinsic Textiles Group LLC focused on making man-made textile fibers biodegradable. It is impossible to ensure that no microfibers end up in the environment,so what if such tiny fibers could biodegrade in nature and reduce their environmental impact? That was the question asked by Andrea Ferris and partner Alan McIntosh when they founded Intrinsic Textiles Group and set to developing a technology they named CiCLO® Ferris notes on the CiCLO website that,“CiCLO fibers were invented from a conviction that‘built to
last’shouldn’t mean ‘here forever.’”
The pair’s business and burgeoning technology eventually caught the eye of Parkdale Advanced Materials —the fibers and yarns innovation division of Parkdale Inc.,Gastonia,N.C. In 2018,the two companies decided to collaborate and a joint venture company — Intrinsic Advanced Materials — was formed.
Textile World recently had the chance to discuss CiCLO’s progress with Ferris,co-founder and CEO of Intrinsic Advanced Materials and co-inventor of CiCLO technology,to learn more about the company’s beginnings,how the technology works and the product’s commercialization.
TW : Circling back to the beginning,it’s unusual for a textile technology to get its start in Silicon Valley! What was the drive behind the technology?
Ferris: CiCLO technology was the brainchild of Intrinsic Textiles Group, a textile technology start-up that spun out of a uniforms and branded merchandise agency in Silicon Valley serving hi-tech clients as well as fast casual restaurant chains.We initially invented the technology to solve our own problem.But,over years of research and development,we discovered that we’d created such an important solution to help reduce plastic pollution that it made sense to build an infrastructure to make it available to the rest of the world too.
TW : How was the concept initially conceived?
Ferris: The story goes like this.Way back in 2012, we had the realization that the large uniforms programs we were supplying were emitting massive amounts of microplastic pollution in the form of man-made fibers into the
Co-founder and CEO of Intrinsic Advanced Materials and Co-inventor of CiCLO technology Andrea Ferris (left) and Cheryl Smyre, director, Advanced Materials, Parkdale, are teammates leading the Intrinsic Advanced Materials joint venture.environment.We were already using recycled polyester (rPET) as a raw material,but had a crisis of conscience when considering the unavoidable pollution the products we supplied were causing.So, we set out to make a better polyester — one that would still be durable and high performance during the useful life of finished products,but one that would eventually biodegrade when it ends up in the environment as a pollutant.We knew that biodegradable plastics existed,so it sounded easy enough at the time!
More than 60 percent of the world’s textiles are made with man-mades like polyester and nylon,which fall into the category of plastics.“Plastics”have a bad rap,but polyester and nylon play an important role in our lives — delivering high performance characteristics — they comfort and protect us — durability —they last virtually forever so we can use longer and buy less — easy care —less washing and drying is required — and global availability at affordable costs.But almost all fabrics shed fibers during manufacture,use and care. The fibers,referred to as microfibers or fiber fragments,are so small that they leak into the environment. Once fugitive,they cannot be recaptured.It’s common knowledge that most plastics,including polyester and nylon,are not inherently biodegradable and persist indefinitely in the environment.Considering all this,
it’s not shocking that research shows that manmade textiles are a contributor to microplastic pollution
While source reduction, 100-percent prevention of plastic pollution and completely closed loops are ideal goals,the idea for the CiCLO solution was grounded in current reality. The goal in developing CiCLO technology was to ensure that fiber fragments shed from man-made fabrics using the technology won’t persist in the environment forever the way other man-mades do.
TW : Parkdale is known for its cotton processing expertise.What about the CiCLO technology was attractive to Parkdale,and how does it complement Parkdale’s traditional business?
Ferris: As the largest spun yarn manufacturer in the Western Hemisphere, Parkdale’s production of polyester-containing yarns exceeds 500 million pounds per year.It has taken a leadership position in delivering sustainable solutions for the textile industry and CiCLOis the proven technology to mitigate microfiber pollution generated by man-made textiles.Parkdale is committed to being part of the solution by creating a path for a cleaner planet,and that is transformational for the textiles industry.
TW : What did the development process look like,and how did Parkdale’s involvement contribute to a commercial product?
Ferris: The development process was long and comprehensive,starting with an investigation into existing biodegradable technologies and biopolymers.We found that while there were some innovativematerials in the market,there was nothing designed specifically for
evaluation,and a sizable — and ongoing — financial investment in third-party lab testing for performance and biodegradation.
The joint venture with Parkdale has been instrumental in scaling CiCLO technology,from contributing its expertise to optimizing the formulation
Tiny fibers can have big impact: Pelagic crabs are shown shackled by fugitive man-made microfibers in this image captured by the Moore Institute for Plastic Pollution Research.
the requirements of high-performance textiles. By that,I mean we needed a technology with safe ingredients that could be blended homogeneously, spun efficiently with conventional and recycled polyester using existing equipment,dyed and finished conventionally, with no loss of mechanical characteristics or durability … but that also eventually biodegraded at greatly accelerated rates when fugitive as a pollutant in the environment.The technology didn’t exist,so we made it! It took four years of trial and error, relationship building,raw materials sourcing and
for spinning to transforming the company from a startup with limited resources and reach to a meaningful textile technology business.Parkdale’s size,textile industry relationships and sincere commitment to innovative solutions that improve lives and sustain the planet make it the perfect company to help CiCLO polyester become the new industry standard globally.
TW : For readers not familiar with CiCLO technology,what is it and how does it work? What types of man-made fibers are compatible with the technology?
Ferris: CiCLO technology gets blended with conventional or recycled polyester and nylon during melt extrusion at the very beginning of the fiber manufacturing process. It becomes permanently embedded in the fiber,so it never washes out.In the simplest of terms,it provides nutrients that attract and act as a food source for microbes,allowing microbes to breakdown and digest — or biodegrade — the active ingredients as well as the surrounding polymer.
The process can be likened to how other natural and inherently biodegradable materials break down in the natural uncontrolled environments.Just like a wool sweater won’t biodegrade during manufacturing,use, care,or in the closet,neither will CiCLO polyester or nylon.Biodegradation of any biodegradable materials requires the presence of moisture and microbes over extended periods of time.
TW : The technology is “scientifically proven.” How is the technology tested for biodegradation and what sort of data supports those claims?
Ferris: The efficacy of CiCLO technology has been scientifically proven by long term biodegradation studies conducted by third-party labs,including Intertek and Bureau Veritas among others,using inter-
nationally recognized ASTM Test Methods that simulate environments where man-made fibers are prolific pollutants — wastewater treatment plant sludge,natural soil, anaerobic digester landfill conditions and sea water.
ture,among other factors.
Australia-based lifestyle and technical clothing brand Billabong has adopted CiCLO®and currently offers boardshorts and wetsuits featuring the technology.
Biodegradation is a complex topic,as is the testing.We often give long presentations on these topics alone.We share comparative long-term data to prove greatly accelerated biodegradation, but no claims can or should be made about “how fast” a biodegradable material will biodegrade in natural, uncontrolled environments.
Think about it … every drop of seawater,square foot of landfill,and field of soil varies greatly — from nutrients to moisture to diversity and density of microbes,absence or presence of oxygen,tempera-
If I could leave readers with two takeaways on the topic of biodegradation it would be that first the length of time it takes anything that is biodegradable —think wool,cotton or paper,for example — to biodegrade will vary based on many factors including the material properties and external factors; and second,years of third-party testing proves that CiCLO polyester and nylon biodegrade at greatly accelerated rates versus to comparable nonCiCLO polyester and nylon in wastewater treatment plant sludge,natural soil,anaerobic digester landfill conditions and sea water.
TW : During development,what were the challenges and were there any roadblocks?
Ferris: We had some bumps in the road along the way when it came to biodegradation testing. We do not extrapolate data, and full biodegradation studies can take a few years.We went to market using one primary lab but quickly realized that brands and retailers wanted to see triangulated data from multiple labs. There aren’t a lot of labs that offer biodegradation testing,and the test environments can be challenging to manage because they are living systems.
Even the most reputable labs sometimes have systems die and need to restart experiments,adding to the already long time frames.Over the past four years,we have invested heavily in building relationshipswith third-party lab resources and conducting additional long-term studies to corroborate data. Ongoing testing is a top priority.Our research and development team always has multiple studies in the works,and we’re committed to spot testing materials in the market.
TW : Have companies been quick to adopt the technology?
Ferris: My semi-joking answer is that “quick”and “textile development”seem to be competing concepts. CiCLO technology may break the world record for most highly vetted textile technology ever to be commercialized!
My serious answer is that we find it can take two to three years from the time a brand shows interest in CiCLO fibers to when its CiCLO-branded products stock shelves. Coming from a textile background,we understand this process and appreciate the due diligence on our clients’part.We launched in 2017 and are now seeing new products coming to market every week from brands we have been working with for years. There’s truth to the statement that the day you plant the seed isn’t the day you eat the fruit.
TW : Who has adopted and are any brands currently featuring the technology in consumer products? Is the product branded and marketed to consumers using hangtag programs?
Ferris: Products made with CiCLO fiber have been available at retail since early 2020.It’s used widely in apparel and home textiles like bedding. Some adopters include Girlfriend Collective, Billabong,Definite Articles, Oakley,Aeropostale, Junes Bags,Lucky Brand, Kindthread,DCK Boardshorts,Sheets & Giggles, Finisterre,and Nimble. CiCLO branded products can be found at Target, Macy’s,Bed Bath & Beyond,Urban Outfitters, Madewell,Free People, and many more retailers.
We offer CiCLO hangtags upon request,which is tied into our traceability program,that many brands utilize.Some choose to create tags using their
brand voice and aesthetic, but that are also in line with CiCLO brand guidelines about how to communicate biodegradable plastics to consumers.
TW : Is it requested by brands or are textile manufacturers opting to use the technology to attract customers to their textile products?
Ferris: Both,and the source of interest has evolved over time.As a new company and technology,we initially had to prove ourselves and the product to fiber and fabric manufacturers.We couldn’t sell the product to brands until we were also able to offer CiCLO fiber availability globally.Then, we tirelessly presented the concept to brands and helped align them with our reputable fiber suppliers. Brand awareness of CiCLO technology has grown so significantly that today we get daily inquiries from
both brands wanting to adopt and manufacturers wanting to supply.
TW : Is the product certified by any thirdparty organizations?
Ferris: The chemistry used to create CiCLO technology is ECO PASSPORT Certified by OEKO-TEX® All components are also REACH compliant.
TW : Does CiCLO technology extend beyond textiles?
Ferris: We are solely focused on pollution caused by textiles today, and very intentionally avoid applications for unnecessary single-use plastics like straws.Our position is that biodegradation of plastics makes sense when the material unavoidably leaks into the environment and cannot be recovered or recycled.
In addition to designing with CiCLO polyester and nylon,we encourage brands and manufacturers to pursue ways to lessen shedding,filter fibers, recycle,reduce use of man-made fibers,utilize natural fibers and all the other ways the industry can work to mitigate pollution caused by textiles. CiCLO technology is just one arrow in the quiver!
TW : So,after 10 long years,you’ve proven the science,built a global infrastructure for traceability and availability, developed meaningful and responsible marketing, and adoptions are growing daily.What challenges do
you face today and what keeps you up at night?
Ferris: Every business has challenges,and I’ll share our top two.
First,brands and retailers are facing real and difficult supply chain disruptions, which delays adoptions of any new technology.We’re patient,understand these issues and are here for the long haul,so this is temporary and we’re already overcoming this.
Second,there is understated confusion on the complex topic of biodegradation — how fast, in what environments and how does it work? Unfortunately,we’ve seen some bad actors doing things like having a very specific fiber,or fibers,certified compostable,then marketing a “biodegradable”yarn for textiles.BPI,a certifying body for compostability, will only certify products and materials related to food packaging and yard waste.Additionally, finished products —not just raw materials — need to be certified to qualify as compostable.Commercial compost is not an end-oflife solution for textiles. We see it as our job to educate the industry, which we’re doing.It will continue to take time and becomes more challenging as other companies and manufacturers propose well branded — and I’d like to think well meaning — but irresponsible, unproven solutions to synthetic microfiber pollution.That’s what keeps me up at night!
TW
Lucky Brand is opting to use hangtags on its products featuring CiCLO®to educate consumers about the technology.A.B. Carter offers years of experience in rings and ring travelers and can help customers optimize their spinning processes.
Driven to innovate and exceed customers’ expectations, A.B. Carter recently celebrated its centennial.
TW Special Report
are always special, but a 100-year anniversary is a significant milestone especially worth celebrating. Through innovation, quality production and exceptional customer service — all performed with a global outlook — A.B. Carter Inc., Gastonia, N.C., has reached that centennial. Established in 1922, the company has weathered the ups and downs of the U.S. textile industry and finds itself in a great position today and is ready to take on the next 100 years.
A.B. Carter bills itself as a company grounded in American heritage, yet driven to innovate. It aims to meet and exceed its customers’ expectations, and is committed to excellence in products and service.
A.B. Carter was founded in 1922 by Arthur Bynum Carter. A selfeducated fellow, Carter began his career as a ring traveler sales representative working with spinning mills. It was during this time that Carter was introduced to the Boyce Weavers Knotter. Finding the technology interesting, Carter bought the patent and struck out on his own. He began manufacturing the knotter, modifying and tweaking the design until it was the finest weaver’s knotter sold all over the world — loved, in part, because of its simplicity.
Carter then began to expand his offerings and using his interest and prior expertise in ring spinning and
ring travelers, began manufacturing metal travelers. Carter Traveler Co. soon began to supply high-quality ring travelers to customers in the United States and beyond. The company later added yarn spinning rings and nylon travelers to its portfolio.
“Our steel and nylon travelers have grown and evolved to be the global standard in all types of spinning and twisting applications,” said Henderson Wise, president and CEO, A.B. Carter.
“Mr. Carter worked his way up the ladder of success by the sweat of his brow,” Wise noted. “His passion and fortitude for the textile industry laid the foundation for our company.”
Today, in addition to its travelers and rings the company’s diverse product portfolio includes bobbins, belts and accessories, splicing and knotting equipment, lab testing equipment, and some accessories for carpet yarn production.
The diversity of the business has been a positive for the company as the industry has changed over the years. “Through acquisitions and partnerships, we have added lines to complement our knowledge and work in all types of spinning and twisting applications,” Wise said. “We must continue to innovate as we move forward in this ever-changing industry.”
A.B. Carter operates a vertical manufacturing structure to ensure high-quality products with flexibility and customization in mind. The company maintains complete control over the manufacturing process for its steel travelers. The Carter Wire Co., a division of A.B. Carter, produces the highest-quality wire that is drawn to size, annealed and shaped. The formed travelers then are heat treated and finished to exact customer specifications. Quality is assured by the company’s advanced metallurgical lab and innovation center staff who conduct extensive tests on the company’s products.
A company’s longevity and continued success is determined by many other factors, but long-standing relationships with valued customers undoubtedly plays a significant role.
“Mr. Carter believed then, as we still believe today, that our customers are our partners, and we should always go above and beyond to serve them,” Wise said.
Customers depend on A.B. Carter’s technical assistance in the spinning process. “Our technical engineers have many years of experience to help optimize the spinning process along with our rings and ring travelers in all types of applications,” Wise said. “We value this relationship as we work to make our customers successful.”
A.B. Carter also relies on its customers to be partners in innovation. “We have stuck to our roots with continued innovation,” Wise offered. “Our research and development and engineering teams have worked diligently as the demands of spinning mills increase. Innovations are paramount as we partner with our customers to optimize the spinning process, and our partnerships are valuable because they propel us to improve and innovate.” The company currently is excited about a new
traveler series that is showing excellent improvements in traveler life and yarn quality parameters in production conditions.
A company’s success surely also is aided by a team of knowledgeable and loyal employees. Henderson says one of A.B. Carter’s greatest strengths and assets is its employees. “Many of our employees have been here for many years,” Wise said. “We have always had an open-door policy as this extended communication and genuine interest in all our employees makes everyone feel like they are an important member of the team.”
Henderson Wise, A.B Carter president and CEO A.B. Carter employees, friends and family recently gathered for a centennial celebration.A.B. Carter is founded by Arthur Bynum Carter and production begins on the company’s first product, the Boyce Weavers Knotter.
A.B.Carter expands, moving to a larger plant in Gastonia, N.C., on Highway 321 South.
Metal traveler business is established.
The company buys first molding machine for the production of nylon travelers.
A.B. Carter Inc. enters into the wire manufacturing business, establishing Carter Wire Co. This business makes wire for internal traveler needs as well as wire for filtration, broom and brush, automotive, and other industries.
The company enters the spindle tape and transmission belt market. Growth over the years includes stainless steel belts and counter bands used on carpet heat-setting equipment.
A.B. Carter acquires Whitinsville Spinning Ring Corp.
A.B. Carter becomes a certified ISO9001 manufacturing facilty, meeting international standards for quality assurance.
A.B. Carter establishes A.B. Carter India Pvt. Ltd. to provide traveler and ring products specifically for the India, Bangladesh and Sri Lanka markets.
A DIVISION OF A.B. CARTER, INC.
Dary-Victor Ring Traveler Co. is acquired and relocated to the Gastonia facility from Massachusetts.
The company acquires U.S. Ring Traveler Co.
Dynacast Molded Traveler Co. is acquired.
A.B. Carter purchases an equity position in DayStrong Rubber Products LLC in Mauldin, S.C., a producer of rubber-based accessories for the carpet industry, amont other industries.
The company partners with Germanybased Saurer Components GmbH to sell and distribute cots, aprons and metal parts (accessories) to the textile industry in the United States and Canada.
Spinning is a global enterprise, and in order to grow and remain successful, A.B. Carter is committed to doing business on the international stage, keeping up what Mr. Carter started all those years ago. “Spinning optimization is critical to mill profitability, and spinning mills today compete in a global market,” Wise said.
To support the company’s positive and growing global demand, in 2006, A.B. Carter opened a subsidiary in India —A.B. Carter India Pvt. Ltd. — to supply travelers and ring products to customers in India, Bangladesh and Sri Lanka. “The team at A.B. Carter India does a great job in covering the markets in India and Bangladesh,” Wise said. “The spinning mills in those areas are very technical and run some of the highest spindle speeds worldwide. We have seen our market share increase there as recent innovations have allowed our customers to improve their processes and yarn quality.”
The company’s full global network also includes employees and offices in Hong Kong, Shanghai; Sao Paulo, Brazil; and Istanbul, Turkey; as well as 45 agents located throughout the world.
A.B. Carter recently held a company-wide celebration at its Gastonia headquarters that included employees past and present, the board of directors, shareholders, and friends. “A.B. Carter Inc. has a long and storied past and a great future as a global supplier in the textile industry,” Wise remarked. “I am extremely proud of our company and all our employees for achieving this great accomplishment.
“Our customer service and continued innovation are commitments that began 100 years ago with Mr. Carter’s drive and passion,” Wise continued. “We look forward to continuing our next chapter as we move forward in the ever-changing textile industry.”
TW
TThehistory of the Synthetic Yarn and Fabric Association (SYFA) is an interesting one (See “A Time For Celebration: 50 Years Of Leadership In Synthetic Fibers,” TW , this issue). Established in the 1970s with the dawn of draw texturing as the Textured Yarn Association of America Inc. (TYAA), the organization is celebrating its 50th anniversary this year.
Today’s SYFA comprises more than 265 individual and corporate members affiliated with the manmade fiber, yarn and fabric industry. Its mission “is to support the production and continued advancement of synthetic yarns and fabrics through technology and education and to promote both existing and new uses for these quality materials. Through our conferences and other events, SYFA provides members with a valuable forum for networking, discussion and presentations related to the development of synthetic yarns and fabrics and their downstream applications, as well as to explore current trade issues to find new solutions to the challenges that face our industry.”
SYFA’s fall conference, to be held November 3-4, 2022, at the Sheraton
TW Special ReportCharlotte Airport Hotel, will celebrate the milestone anniversary with some special features.
As usual, the conference will feature a slate of speakers with presentations from Consultant Jeff Dugan; Julie Rader, director, U.S. Manufacturing and Sourcing, Walmart; a speaker from the Wilson College of Textiles, NC State University; Laura Murphy, research director, Fibres, Wood Mackenzie; Nello Masciarelli, director of Energy, Gildan; and Alasdair Carmichael, program director, NAPCOR.
In addition, a panel featuring six of the textile industry’s top leaders — Leib Oehmig, CEO Glen Raven Inc.; Cameron Hamrick, CEO, Hamrick
Mills; Jeff Price, executive vice president of Strategic Initiatives, Milliken & Company; Charles Heilig, president and CEO, Parkdale Mills; Eddie Ingle, CEO and director, Unifi Inc.; and Amy Bircher, CEO and founder, MMI Textiles — will sit together and share their thoughts on the “Past, Present and Future” — the theme for this anniversary event.
Several past TYAA and SYFA presidents will be in attendance as the association looks back over its 50 years.
At the end of Thursday’s session, all attendees will gather for a cocktail reception at 5:30 p.m. followed by a sit-down dinner at 6:30 p.m. During dinner, Kim Glas, president and CEO, National Council of Textile Organizations, will deliver a keynote address.
Mark your calendars to come network and reminisce with SYFA members past and present this November as the association celebrates its 50th anniversary. TW
For more information about the SYFA’s fall 2022 conference and to register for the event, please visit thesyfa.org.
The Synthetic Yarn and Fabric Association (SYFA) will celebrate its 50th anniversary during its fall conference with an enhanced schedule.
Source: Fiber Organon
From its beginnings as the TYAA in 1972, SYFAhas adapted to weather downturns in the industry and is celebrating its 50th anniversary this year.
TTheSynthetic Yarn & Fabric Association (SYFA) and its predecessor organization the Textured Yarn Association of America (TYAA) is celebrating 50 years of operation in 2022. The TYAA was first formed in 1971 and held its inaugural meeting in 1972.
producing a staple fiber to either complement cotton in blended yarn or to compete with cotton. Filament polyester remained a smaller volume than polyester staple globally until 1993, but by 2020 had grown to be more than double the size of staple.
By Alasdair CarmichaelThis time period was the dawn of draw texturing and the commercial arrival of polyester textile filament as a feed yarn for draw texturing. Prior to the beginning of the 70s, nylon was the main textured fiber using fully drawn yarn as the supply.
Polyester was developed in the 1940s, and the initial focus was on
The growth of texturing and particularly polyester brought a number of new producers into the U.S. market and resulted in industry leaders, led by Norman Cohen of Goulston Technologies Inc., Monroe, N.C., deciding that the sector was large enough, and unique enough, to warrant its own technical trade association. The author of this article joined
the U.S. texturing industry in spring 1972 and had the privilege to attend the second full meeting of the TYAA in summer 1973.
A major driver of the growth in texturing in the United States and elsewhere was the development of draw texturing which took four process steps and combined them into two steps, as well as increasing productivity and producing a larger, better package of yarn for direct knitting or weaving.
There was no shortage of technical developments to be discussed at the TYAA conferences!
In the mid to late 1970s, there were approximately 115 companies in the United States withtexturing or draw texturing machines. At this time, the structure of the industry was driven by growth. There were a number of large fabric companies that diversified their production to include texturing. Additionally, some of the large polyester fiber producers also invested in texturing. There also were many specialized yarn companies with texturing operations. The double knit industry provided an apparently insatiable appetite for more and more textured polyester, until the inevitable happened and demand collapsed.
Figure 1 shows data from the American Fiber Manufacturing Association (AFMA) publication Fiber Organon. Polyester textile filament capacity in the United States grew from 316 million pounds in 1970 to 1.7 billion pounds by 1979, with the growth driven mainly by demand for textured polyester. The 1979 peak was the highest level the U.S. industry ever achieved. The 1980s were a time of consolidation and closures within the industry, as well as a time for product development and production technology improvements which resulted in a good recovery in the 1990s.
However, the good times for the domestic industry came to an end as the calendar turned into the 21st
century and global supply chains became the prevalent business model. Many sectors of the textile industry were hit very hard by global sourcing and the textured yarn industry was no exception. The chart tracks the downturn very clearly.
The TYAA was faced with a rapidly declining pool of membership. From approximately 115 companies with texturing machines in the late 1970s, by 2006 there were only 17 companies remaining.
Norman Cohen, George A. Goulston David Petree, Burlington Industries Richard Whisenant, Burke Knit Peter Cook, Wamsutta Mills
Allen Booth, Duplan Corp
Frank Gaddy Jr, Burke Yarns Doug Blanchard , Blanchard Yarns John McKinnon, Duplan Corp William Rush, Hoechst Fibers
The first meeting of the TYAA was held at the Holiday Inn Four Seasons in Greensboro, N.C., in 1972 and resulted in 355 individual members from 160 companies.
The association faced three options:
• Close down completely;
• Merge with another group; or
• Increase the scope of membership by rebranding and appeal to a wider range of membership.
Following tough discussions, the board decided to take the most difficult of the alternatives and rebranded in 2006 as the Synthetic Yarn and Fiber Association (SYFA), a name that was later changed to Synthetic Yarn and Fabric Association.
The rebranding has been a success with both membership and attendance at conferences seeing significant growth in the years following the decision.
Two association milestones stand
out. The first is an awareness of the importance of sustainability to the industry and, from the beginning of the association’s rebranding process, it has made a conscious effort to include presentations on sustainability at all its meetings. The most successful meeting in association history was the 2008 Winter Conference when the entire program was devoted to sustainability under the theme “Sustainable is Attainable.” That meeting saw a record attendance of more than 300 people.
The second milestone is more recent, and that was the ability to come through the COVID-19 pandemic and be in position to look ahead to a bright future.
The association is celebrating 34 years as TYAA and 16 years as SYFA for a total of 50 years of serving the U.S. synthetic textiles industry. Please join SYFA in celebrating this milestone at the fall conference to be held November 3-4, 2022, in Charlotte, N.C. For more information about this special event, please see, “50 Years Of SYFA,” TW, this issue. TW
Editor’s Note: Alasdair Carmichael is vice president of the Synthetic Yarn and Fabrics Association (SYFA)
Fruit of the Loom, Bowling Green, Ky., has partnered with Recover Textile Systems S.L. to launch a collection of unisex T-shirts featuring Recover™ — a recycled cotton fiber. According to the company, Recover is one of the lowest-impact fibers available in the market, which reduces the carbon and water footprint of apparel produced using the fiber. Each T-shirt is made using 20-percent Recover, and the limited-edition collection is available in eight colors.
seminars and event content for those not able to attend the openhouse in person. The theme for the event is “Open Up The Future.”
Shima reports it is sending a strong message on this anniversary “in an effort to accelerate the widespread use of virtual samples to reduce waste throughout the supply chain to ensure a sustainable future for the fashion industry and for the planet as a whole.”
Stockholm Essity reports it has finalized the purchases of Canadabased Knix Wear Inc. and Australiabased Modibodi. The two companies are providers of leakproof apparel for periods and incontinence — a fast growing segment in the intimate hygiene sector.
Greensboro, N.C.-based Cone Denim® is expanding its partnership with hemp processor BastCore LLC. The two companies will continue to collaborate to offer sustainable denim offerings while supporting American agriculture.
Cone recently introduced its U.S. Hemp Collection featuring BastCore U.S.-grown hemp as well as natural indigo and U.S. cotton. The fabric range includes classic 3x1 weaves, comfort stretch and modern workwear constructions.
BastCore manufactures hemp fiber in Montgomery, Ala., that is USDA biopreferred and OEKOTEX® Standard 100 certified.
“This collection is the latest way Fruit of the Loom is producing more sustainable products across the entire business,” said Mercedes Lopez, vice president of Corporate Social Responsibility at Fruit of the Loom. “As one of the world’s largest manufacturers and marketers of casualwear, we are committed to reducing our environmental impact across the total value chain.”
Shima Seiki Turns 60
Japan-based Shima Seiki Mfg. Ltd. is celebrating its 60th anniversary. To mark the milestone, the company will host a three-month-long openhouse event at its headquarters in Wakayama, Japan, that will feature a virtual fashion show, machine and sample exhibits, and a presentation of the latest DX design technology; as well as a special website that offers
Knix has a strong presence in the United States and Canada; while Modibodi has a presence in Australia, New Zealand and the United Kingdom. Essity acquired 80 percent of Knix, while Founder and CEO Joanna Griffiths holds the remaining 20 percent share. She will remain as president of the company.
Apparel company Duluth Trading Co., Belleville, Wis., announced plans to locate a new distribution and fulfillment facility in Adairsville, Ga. The $53 million investment will create 300 new jobs.
“We are excited to welcome an iconic brand in Duluth Trading Company to the Peach State,” said Governor Brian Kemp. “We are confident this new facility will begin a prosperous relationship with the people of Bartow County as Duluth expands to meet the distribution needs of our modern economy. Georgia’s prime location and robust infrastructure allows companies
“Cone is extremely proud to work closely with an industry-recognized company like BastCore as we advance our commitment to provide more sustainable, alternative fiber options to our denim community,” said Cone Denim President Steve Maggard. “With a shared goal of pushing new sustainability levels, our partnership with BastCore is creating exciting opportunities that support U.S. agriculture and its use of world-class practices and responsibly sourced products.”
to distribute products to 80 percent of the U.S. market in less than two days of drive time or two hours by plane.”
“We are thrilled to open Duluth Trading’s first-ever automated fulfillment center in Adairsville, Georgia,” said Sam Sato, president and CEO, Duluth Trading. “With an expanded fulfillment network and state-ofthe-art robotics, this new facility positions us to better serve our customers nationwide all while adding hundreds of new jobs to the Bartow County community.” TW
Cone Denim®, BastCore Continue Partnership Fruit of the Loom T-shirts featuring Recover™ fiber.Eco-Age helps brands develop sustainable business strategies beginning with responsible practices that lower a company’s impact on people and the planet. Eco-Age’s team — comprised of technical, strategy, communications and digital media content specialists and consultants — also helps its clients effectively communicate their journey in a transparent and tangible manner. The end-to-end agency reports it has collaborated with non-governmental organizations, governments and changemakers across industries over the past 10 years working to effect change in corporate responsibility.
Current and past clients related to the textile industry include The Woolmark Company; fiber producer Aquafil; denim manufacturer Candiani; British retailer Marks & Spencer; and fashion brands Diesel, UGG and Stella McCartney, to name just a few companies. Eco-Age also has established the Green Carpet Challenge® and the Green Carpet Fashion Awards to bring attention to sustainable fashion brands while pairing “glamour with ethics.”
In the age of sustainable manufacturing, the term greenwashing is heard more often than ever before. A take on the term “whitewash,” greenwashing is defined by MerriamWebster dictionary as “the act or practice of making a product, policy,
TW Special Reportactivity, etc. appear to be more environmentally friendly or less environmentally damaging than it really is.”
T e x t i l e W o r l d recently had the chance to speak with Philippa Grogan, a sustainability consultant in Policy, Fashion and Textiles at EcoAge, about greenwashing and sustainability in the fashion industry. She has two Masters degrees in fashion sustainability and enjoys working with her clients to help “mitigate their environmental impact through innovative, alternative and regenerative material selection.”
Textile World : Current news suggests some brands have been greenwashing. What does the fashion industry need to do to mitigate continued greenwashing?
Grogan : The fashion industry should share focus between outward-facing sustainability narratives and inward-facing better business strategies. So many brands are determined to appear sustainable in the public eye that meaningful sustain-
ability strategies are falling by the wayside. Sustainability communications should evolve against a backdrop of continual and holistic sustainability progress. The industry needs to acknowledge imperfection and be ready to communicate about learnings as well as wins. Nobody is perfect, and we are all navigating this space together. Companies should be more forthcoming with the things they are working on, rather than the things they have already achieved.
TW : From an Eco-Age perspective, what do you view as the dangers of brands utilizing incorrect data to verify sustainability claims?
Grogan : Brands need to think twice about using generalized lifecycle assessment (LCA) data to communicate sustainability to consumers. Generalized data can be aggregated and reworked from industry, global, or national databases and is often not as accurate as primary data — first-hand data collected from a company’s own operations. LCA data can be useful for guiding business decisions behind the scenes, but there is a risk of greenwash if this data crosses the threshold to the consumer and used as a marketing tool in sustainability claims.
Incomplete, unrepresentative, or inaccurate sustainability data can do more damage than good. Company or consumer, when faced with weak sustainability data, you cannot make
Philippa Grogan, a consultant with Eco-Age, discusses greenwashing and best practices for communicating sustainability claims.
an informed choice. This means that brands and designers could inadvertently create products with more impactful materials and consumers could be misinformed at point of purchase. The proliferation of shaky sustainability data in marketing and communications stands to exacerbate consumer confusion, jeopardize responsible purchasing, and derail public trust of overall sustainability performance.
TW : How do you think brands can better communicate a product’s total impact without greenwashing?
Grogan: Many brands are, inadvertently or otherwise, misleading consumers when sustainability claims focus only on the upstream phases of a product. Of course, the production and manufacturing phases have an impact, but so do other touchpoints in a lifecycle — such as the active-use phase and the end-of-use phase. Product-level sustainability communications and claims should, as best possible, focus on the whole lifecycle of the product, otherwise they should be called “production-level” claims.
Instead of relying on tenuous terms and meaningless buzzwords, sustainability communications
should detail why the product might have a lower impact and disclose how it has been produced.
Beyond this, products are company output. A “sustainable” product sold by a wholly irresponsible company can never be truly “sustainable.” Sustainability claims and company performance should look beyond the commodity and holistically assess all factors of the business.
TW : Moving forward, what recommendations can you offer to brands?
Grogan : For sustainability communications to be free from greenwash, they should not rely on vague, ambiguous buzzwords such as “eco,” “green,” or “planet-friendly” — these terms largely are meaningless without scientific substantiation.
Another common greenwashing tactic the industry should avoid, is cherry picking favorable sustainability elements without detailing overall sustainability performance. For example, championing the use of recycled materials whilst being unable to trace supply chains, pay a living wage or reduce emissions.
It’s ok to be imperfect, but not ok to pretend something is perfect. Be humble about sustainability performance and be brave enough to share learnings as well as wins. This level of transparency is commendable and can demonstrate an ongoing journey rather than a light switch moment of “boom, now we’re sustainable.”
TW : How important is it to consider socio-economic impact when addressing sustainability?
Grogan: Sustainability is about so much more than the environment. The social impact of a product, company or service is a crucial and inextricable metric for sustainability. This notion is a core focus of the amazing work of Donut Economics and Future Fit Business Benchmark. To approach sustainability, brands need to apply a future-focused and systemic lens. It is vital they think beyond existing sources and materi-
als and also focus on innovations that can reduce the world’s overreliance on existing materials in the markets such as cotton.
TW : What challenges and opportunities have you encountered when dealing with LCAs, products and brands?
Grogan : The idea of LCAs and LCA-based systems is to crystallize complex concepts into digestible, consumer-facing information that can demystify the science for the average member of the public. However, the methodology, the boundaries, and the input data must be sound in order for the results to have a hope of being accurate.
LCAs can be really useful for guiding business decisions behind the scenes. However, once they cross the consumer threshold and make their way into public-facing sustainability claims, we should exercise extreme caution, even more so if it is from aggregated data from industry averages.
Best practice sustainability communications are accurate, substantiated, measurable, demonstrable, and above all, transparent. Issues arise when initiatives are used as a transparency exercise, but the methodology, boundaries, and input data are behind a paywall.
T W : What are some key issues with the fashion industry’s overall sustainability performance?
Grogan : Some of the most concerning issues linked to the fashion industry largely stem from overproduction, overextraction, and overconsumption of resources and materials. The fashion industry as a whole must seriously rethink its relationship with the natural world, specifically its resource overuse which is not only leading to natural capital depletion, but also exponential volumes of unmanageable and polluting waste. Most fast fashion clothing is produced with planned and perceived obsolescence in mind, meaning that thanks to fleeting trends and poor-
Philippa Grogan is a sustainability consultant in Policy, Fashion and Textiles at Eco-Agequality materials, they are prematurely disposed of to make way for new trendy garments. Many of today’s production and consumption patterns have become detached from earth’s natural systems. If we are to secure a sustainable future, we need to depart form linear take-make-dispose models to technically and biologically circular models where materials can biodegrade or be recycled at the end of use.
Another key issue faced by the fashion industry is the human rights and remuneration of those working in upstream supply chains, such as manufacturers and producers. Fashion’s long, complex, and globalized supply chains result in traceability issues, and it is challenging to monitor conditions, let alone ensure everyone is treated fairly and paid a living wage. This needs to be put firmly on fashion’s agenda.
TW : What is the role of market regulators and policymakers in the fight against greenwash?
Grogan: Greenwashing is everywhere. We have seen a recent shift in market regulator scrutiny of sustainability claims, with many nations’ advertising watchdogs screening brand’s sustainability claims and outlining proposed sanctions for those found greenwashing. It is now so widespread and wields such damaging potential, the only way of combatting it, sadly, is through legislation and regulation on claims.
TW: Is there a need for standardized rules for using sustainable terms in the fashion industry?
Grogan : We can no longer rely on company’s self-improvement initiatives. Government-led sustainability claim regulations are instrumental for unifying global sustainability language and driving real industry change. If earth’s declining ecological health is not incentive enough for our industry to produce sustainably and communicate ethically, then we must involve legal and financial incentives. TW
AAPN’s 2019 pro:Americas Annual Conference held at the Faena Forum in Miami Beach, Fla., attracted more than 200 attendees.
growing, and the demands quickly became more than one person could handle alone.
The future AAPN Managing Director Mike Todaro attended his first AACA meeting in 1994 in Perdido Beach, Ala. At the time, he worked for Manhattan Associates. In 1995, Todaro joined AACA staff in charge of marketing and technology.
AAPN’s ability to leverage the latest technology at a pinnacle of technological change — the advent of the internet was significant.
TW Special ReportFFirstestablished in 1981 as the the American Apparel Contractors Association (AACA) by Don Strickland in Atlanta, today’s Americas Apparel Producers’ Network (AAPN) has adapted and innovated to become a significant network of diverse members that make up the apparel supply chain. Throughout its history, AAPN’s leadership has acknowledged, adapted and led change initiatives facilitating the effectiveness of its members.
The evolution of AAPN, was, and is, largely driven by emerging technology, the changing structure of the industry, and the needs of its members. Technology was an early driver of AAPN’s innovations.
“When I joined the association in 1987, there was a personal computer in the officewithout a hard drive, but we did have a really big floppy disk —
about 8 inches square,” said AAPN Executive Director Sue C. Strickland. “When someone called needing to know if we could give them the names of factories that made T-shirts, we fired up the computer, put the floppy diskinto the A drive, typed in a lot of undecipherable characters in code form and we hada list!
“It wasn’t too long before we could use another monumental breakthrough intechnology — and actually fax this list to the caller."
Later in 1994, AACA members were listed on a dial-up database established in cooperation with Clemson University. That spring, Strickland started the “Fax On Demand Sourcing Hotline.”
When AACA founder Don passed away unexpectedly in 1990, his wife Sue took over as the sole staff member. The organization was rapidly
In 1996, all AACA Members were listed on an internet-based network, which was an industry first, according to AAPN. “It gave customers immediate access,” the association reported. “The internet was becoming as pervasive as the fax machine, at a much lower cost. E-mail began to gain acceptance, but it wasa while before we could communicate with the entire membership using email, but wemade it clear that technology was a part of the AAPN.”
In 1997, AACA changed its name to the American Apparel Producers Network (AAPN). Membership had dropped from 350 to 150 in two years largely because of the implementation of the North America Free Trade Agreement (NAFTA). According to AAPN, the name change was driven by committing to the internet, and taking hold of the word “network.” It also felt the word “producer” was much stronger than “contractor.” It meant factories, mills, spinning, trim and much more, including both brands and private label.
“We dropped ‘contractors association’ replacing it with the much more accurate and exclusive phrase ‘producers‘ network,’” Todaro noted.
AAPN recently announced Lynsey Jones as transition advisor to assist Executive Director Sue C. Strickland and Managing Director Mike Todaro chart a course forward.AAPN needed to addressthe scope of change driven by evolving trade agreements and policy. In 2001, AAPN expanded its membership to include NAFTA, Caribbean Basin Initiative (CBI) and Americas producers.
According to AAPN: “We went regional. AAPN changed its mission from primarily ‘sourcing’ to ‘networking’ and extended full membership throughout the Americas to reshape the sourcing infrastructure of the hemisphere.”
The early 2000s were prime time for developing meetings, roundtables and trips abroad. AAPN was holding meetings in Central America and the United States.
According to AAPN, by 2005, “AAPN became the first true global supply chain network. AAPN reached critical mass with one or more global players in every step and stage in the apparel supply chain ‘from the dirt to the shirt.’”
In 2013, AAPN becameAmericas Apparel Producers’ Network, acknowledging the ties that had been built through the years throughout the Americas.Regional conferences, in addition to the annual meeting, grew in demand.
In 2018, the association launched the AAPN Carolina Mill Tour. Designed as a learning tour for brands and retailers, participants visit five Carolinas-based textile manufacturers over the course of a week to see the manufacturing processes up close and get some in-person education. “In April, we held our first ever AAPN Carolina Mill Tour in a packed bus,” Todaro said. “The tour started and spent the day at Contempora Fabrics. Other stops included UNIFI, Parkdale, CCW [Carolina Cotton Works] and A&E. It was a spectacular success. We had several dozen staffers from a dozen brands and retailers.”
The program continues to help demonstrate to brands and retailers a viable domestic apparel supply chain
Right (left to right): Jacobo Kattan, PROTEXSA; Jesus Canahauti, Elcatex; Mike Todaro and Sue Strickland, AAPN; Mario Canahauti, AHM; Joe Cuervo, Kohl’s; and Juan Zighelboim, TexOps, at the 2018 Apparel Summit of the Americas in Honduras.
and the level of technology and investment domestic suppliers have made and continue to make.
The onset of the COVID impacted the industry tremendously. What was an essential worker, which businesses could stay open, and which needed to furlough workers? It was a confusing time. However, the country needed personal protective equipment (PPE) and textile companies wanted to help. AAPN wanted to help too, and launched an online Sourcing Center on March 22, 2020, available to its members. Within 10 minutes the center had its first post. By April 3, more than 10,000 users had viewed the center, with 3,500plus registered users and almost 500 posts. AAPN opened its network to
members and non-members alike to assist insourcing PPE and PPE materials. Users were from every corner of the industry including members of other organizations serving the uniform, industrial fabric, nonwovens and equipment sectors, among other associations.
“In turn, word of mouth from AAPN members to their customers, articles posted in journals, and blogs and websites across the industry brought people into the exchange,” Todaro reported. “Fortunately, AAPN was able to share a network that was already active with 200 industry organizations and some 1,600 people.”
Todaro noted that the experience was one of the most ground-breaking validations of the power of trustthough-networking in the nearly 40-year history of the AAPN.
Above: AAPN 2019 Carolina Mill Tour group in the lobby at Milliken’s headquartersAAPN adapted to the COVID and post-COVID environment — experimenting with virtual networking solutions and eventually organizing face-to-face meetings once again — and AAPN leaders Strickland and Todaro wondered what is next? They have decided this is an opportune time to chart a course forward for future AAPN leadership.
Finding the right person for the leadership role was no easy task. “AAPN is a unique ‘no rules, no hours, no supervisor’ radical business model,” Todaro said. “We [Sue and Mike] are the staff. During our 28 years together, every project/event/ meeting/execution fell fully into our laps. So, we had to find someone tough, flexible, independent, always ‘on’, driven and passionate.
“Just as importantly, we needed a proven, respected, high profile industry veteran, with C-Suite experience, industry connections, a global perspective, supply chain savvy and street smarts — in other words, someone smarter than us. We made a dream sheet list of potential candidates — all AAPN members of course — and began vetting them. We knew that the ‘sum of the parts’ of the two of us was unique, but we were also acutely aware neither of us
had ever worked in the industry, had never ‘walked the walk’ of sourcing and production.”
After this extensive search, AAPN was proud to announce that Lynsey Jones is AAPN’s new transition advisor. She eventually will become the executive director of AAPN. “As Lynsey wound down her career at Carter’s, taking time to transition out of Hong Kong and back on staff at Carter’s with big plans and projects, we began to discuss her eventually replacing Sue and me,” Todaro said. “The details quickly fell into place.”
Jones has had an extensive apparel career building on a formal education in textiles achieving a Bachelor of Science in Textile Technology & Apparel Management from NC State University. Jones also achieved a Master of Science in Textiles and became an ITT fellow.
Her career began at Abercrombie & Fitch, followed by 10 years in various positions at VF Corp. Jones’ most recent assignment was as vice president, Global Sourcing Strategy & Transformation at Atlanta-based Carters Inc.
A planned transition of two years will be supported by Strickland and Todaro who are excited to explore Jones’ vision of membership growth, new unique value-add services, innovative programs, potential acquisitions and so much more.
"I am so humbled that Sue and Mike chose me to hand over the reinsof their 30 years of hard work and dedication,” Jones said. “Ever since I lived in Panama and concentrated on Western Hemisphere sourcing, I knew that it was a passion of mine to make the region a success. As a long-term member, I know that AAPN is the group that can make it happen because I’ve seen it time and time again! I am excited to blend my passion and vast experience to drive value for our membership."
“AAPN is not a job. It has been my life’s mission for the past 32 years and I have been constantly amazed by our members’ability to roll with the punches and think about the good of the industry above all else,” Strickland said.“Mike and I are beyond excited to have Lynsey coming behind us to continue our work. She brings new energy, expertise and some pretty exciting ideas with her. I can't wait to see what the future holds!” TW
Add
Subscribe to Textile World for complete coverage of the U.S. and global textile manufacturing industry — the latest technologies, applications, regulations and trends.
Now you can receive your Textile World magazine anywhere you go.
Print advertisers receive additional reach and linking with free inclusion in Digital Editions.
read / share / engage TextileWorld.com
Green Theme Technologies Inc. (GTT),Rio Rancho,N.M.,has granted a license to The Haartz Corp.,Acton,Mass.,for its patented EMPEL™ textile finishing platform. EMPEL is per- and polyfluoralkyl substances (PFAS)-free,and uses “clean chemistry”in a waterless process to add treatments such as durable water repellents,antiwicking and durable stain releases to a variety of textile substrates. The platform applies a nontoxic hydrocarbon monomer solution to a fabric that is then polymerized to wrap each individual yarn with a high-performance,durable finish.
“Haartz is the perfect partner for GTT,”said Martin Flora,vice president of Business Development for GTT.“They are world leaders in scaling finished fabric technologies through world-class manufacturing and testing facilities.With their various product categories,including apparel,furniture and automotive, our partnership brings textile innovation to North America and helps drive a positive and sizable environmental impact.”
Italy-based Tonello S.r.l.recently introduced the Evolution 3,a new generation of washing and dyeing machines.The technology was developed with reduced water and energy consumption,increased productivity, and lower maintenance costs in mind.According to the company, the updates result in energy savings of up to 20 percent compared to previous generation machines.
Improvements include: high efficiency motors; an optimized transmission with high-efficiency belts for improved durability; a more compact design; new inverters for
motor control to reduce stress and vibration; and electronic boards designed to withstand even the most harsh laundry and dyeing plant conditions.The machines are constructed using premium materials, such as AISI 316L stainless steel; and quality construction methods, such as drum welds created by highprecision anthropomorphic robots.
The Evolution 3 range is designed to handle future technology updates, and is compatible with accessories and kits,and the Metro and Mago Site Manager software programs.
Microban®Introduces DuraTech™Antimicrobial DuraTech™ by Microban® is a new antimicrobial additive for cotton applications from Microban International,Huntersville,N.C.According to the company,the product “helps to prevent the growth of odor-causing bacteria up to 99.99 percent after 75 home launderings.”It also continues to reduce odors up to 99 percent once home launderings surpass 75.
The product is non-heavy metal, binder-free,non-ionic and fully water soluble.DuraTech may be applied using traditional padding processes. Microban reports the additive also does not impact the appearance or feel of the cotton fabric.The technology — available to customers in the United States and Asia — is suitable for sheets and towels used in home textiles and hospitality applications.
TAU Investment Management LLC,with locations in New York City and Hong Kong,reports it has made investments in two waterless dyeing companies.The company will acquire significant stakes in and join the board of directors at DyeCoo Textile Systems BV and CleanDye Holding BV through a
Switzerland-based Archroma, a portfolio company of private investment firm SK Capital Partners,reports it has entered into a definitive agreement to acquire the Textile Effects business of Huntsman Corp.,Salt Lake City.The transaction is subject to customary conditions and approvals,and is expected to close in the first half of 2023.
“I am thrilled to see the combination of Huntsman Textile Effects and Archroma”, said Barry Siadat,co-founder of SK Capital Partners and chairman of Archroma.“Finally,we have achieved a dream of combining the technologies,products and capabilities of the legacy pioneers of the textile industry,namely Ciba,Sandoz,Hoechst and BASF, into a modern and cohesive enterprise that is focused on delivering innovative and sustainable systems and solutions to serve the evolving needs of today’s textile industry.”
special purpose vehicle formed and managed by TAU.DyeCoo is the creator of a waterless and chemicalfree dyeing technology named DyeOx.CleanDye is the first dyeing facility built to use DyeOx technology exclusively.The investments are part of TAU’s strategy to invest in sustainable and responsible supply chains,and TAU joins other companies — including Ingka Investments and Nike — who have already invested in the technology.
“This is a unique opportunity to support two organizations bringing a new facet of sustainability to the garment industry,”said TAU CEO Oliver Niedermaier.“We look forward to further application opportunities for the technology in other sectors, such as automotive and beverages.” TW
NNorthCarolina State University researchers have demonstrated that a synthetic polymer can remove certain dyes from water, and that the polymer can be recovered and reused. The findings offer a new potential method for cleaning wastewater after use by textiles, cosmetics or other industries.
“Dyes are used everywhere, including in the textile industry, as well as in pharmaceuticals, cosmetics, paper, leather and even in medicines,” said Januka Budhathoki-Uprety, lead author of a paper on the work and an assistant professor of textile engineering, chemistry and science at NC State, Raleigh, N.C. “If these contaminants aren’t properly removed from wastewater after dyeing and finishing, they can be a significant source of environmental pollution and pose risks for human health.”
In the study, published in ACS Applied Polymer Materials, researchers made a synthetic polymer called polycarbodiimide. The researchers then tested the material’s
ability to clean wastewater first by dissolving it in a solvent, and then mixing it with water contaminated with dyes. They tested the polymer solution against a series of 20 anionic dyes, also called acid dyes, which are usedin the textile industry. For initial assessments, the researchers did a visual test with the naked eye to see if the polymer worked. The researchers later quantified how well the polymer removed the colorant using ultraviolet-visible (UV-Vis) spectroscopy.
“We mixed the polymer solution and dye-contaminated water so the polymer in the solution can grab on to the dye,” Budhathoki-Uprety said. “This is a two-phase solution, just like oil and water. The polymer part of the solution grabs onto the dyes. Then we were able to easily separate the clean water from the contaminated solution mixture by draining it out, similar to separation of water from a mixture of oil and water.”
The polymer solution removed all but four of the 20 acid dyes they
The left vial shows dye solution in water (blue) and the right vial shows clear water after the dye was removed from the solution by the polymer.
tested. In addition, they found it was easy to recover the polymer within minutes. They found characteristics of the dyes — related to their molecular structures — that contributed to whether the polymer worked or not.
“We found that the polymer solution can remove dyes from contaminated water, and we can recover the polymer and use it to remove dye from contaminated water again,” Budhathoki-Uprety said.
In future studies, researchers are planning to develop a library of polymers that would have the potential to work with more types of dyes. In addition, they want to develop a more practical mechanism for using polycarbodiimide to clean wastewater.
“We are working to develop materials that can do the same work without having to use the polymer in the solution phase,” Budhathoki-Uprety said. “If you have dye spill, you don’t want to have to use a flammable solution — you want a solid material that is easier to handle.”
The study, “Polycarbodiimide for Textile Dye Removal from Contaminated Water,” was published online in ACS Applied Polymer Materials on July 22, 2022. Co-authors included Meghan Lord, graduate student in Fiber and Polymer Science Program, and Graham Neve and Mike Keating, undergraduate students in the Textile Engineering, Chemistry and Science Department at NC State. The study was funded by the Textile Engineering, Chemistry and Science Department at NC State. Individual researchers were also supported by the Office of Undergraduate Research Federal Work Study Research Assistant Program at NC State. TW
Editor’s Note: Laura Oleniacz is Public Communications Specialist at NC State News Services.
(Photo: Januka Budhathoki-Uprety)Arecent Bloomberg article, “American Factories Are Making Stuff Again as CEOs Take Production Out of China,” observes the trend of bringing major manufacturing operations back to the United States, briefly seen as a stopgap measure to mitigate complications arising from the pandemic economy. This now appears to be
part of a broader strategy for longterm operational viability, resiliency and value.
Per the article, “… the construction of new manufacturing facilities in the U.S. has soared 116 percent over the past year,” while a survey suggests many U.S.-based corporate executives see fit to move production out of China, with many such opera-
tions expected to return to the United States or Mexico. While high labor costs have long been used to justify offshore production, volatile supply chains, shipping complications and costs, tariffs, perceived sociopolitical instability, and other factors — including the proliferation of automation technologies that necessitate fewer laborers to operate in general — have made reshoring to North America a practical, profitable, and safer proposition.
While this development may come as news to some, here in the fashion and textile worlds this trend has been witnessed up close and personal. Indeed, the economics of bringing production closer to the end consumer — immediately delivery that negates the need for vast and vulnerable supply chains, the ability to react to demand in real time, the eco-friendly aspect of a streamlined process, and the mitigation of troublesome external factors in general — underlies the KornitX Global Fulfillment Network, which effectively nearshores production for every market.
Many of Kornit’s partners and customers are founding or adapting their businesses on the basis of localizing their operations, even in highly regulated and high-cost regions that would not, on their face, appear to be logical production sites. Yet, efficient, on-demand production technologies make these models highly profitable.
Consider Charlotte, N.C.-based Printful, a successful practitioner of on-demand digital direct-to-garment (DTG) fulfillment this past decade, which has thrived by localizing its operations across many regions, including several locations within the United States — including high-cost Los Angeles.
Also consider FABRIC, a so-called “fashion incubator” based in Tempe, Ariz., created to empower independent fashion designers to bring their creations to life, without significant up-front investment or commitment. Using Kornit’s sustainable, versatile, on-demand direct-to-fabric production capabilities, it is working to make Arizona a hotbed of fashion production.
Consider countless small businesses like Little Cocalico, Reinholds, Pa., where proprietor Jon Boll invested in Kornit’s sustainable, ondemand Kornit Presto S direct-tofabric system because “people are realizing it’s not more expensive, and you can get better quality giving fellow Americans jobs and bringing production back to the United States, and bring sustainability and quality to their businesses.”
One of the greatest attributes of localized, on-demand fashion and textile production models is that the strategy is entirely modular; it can be replicated to mitigate risk, foster operational agility and versatility, and deliver profitability anywhere. Perhaps no Kornit partner exemplifies this proposition better than London-based Fashion-Enter, which employs both Kornit DTG and direct-to-fabric production systems to educate, empower, and fulfill the
Right: Kornit’s Atlas MAX Poly system is a direct-to-garment solution for vibrant designs on polyester and poly blends.
needs of aspiring fashion designers in the United Kingdom. That it can successfully do so within the city of London, the high-cost cradle of the Industrial Revolution itself, demonstrates how “Make It British” can also mean “make it sustainably, make it with superior quality, make it in any quantity, make it without limitations, make it brilliant — and make it cost-effectively every time.”
Regardless of the challenges we face, game-changing technologies have provided a solution in times of need. In the past 40 years, technological advancements have made considerable gains in areas of alleviating poverty, improving healthcare and wellness, revolutionizing the ways we communicate and shop, increasing our quality of life, and far more. Where simple economics once drove manufacturers to solve problems by simply moving operations to far-flung locations where
both labor and space were cheap and plentiful, those committed to developing sustainable, efficient, highly automated, and versatile production technologies have made it more profitable than ever to bring those operations back home. What’s more, unpredictable global market dynamics, like any number of risks and complications we’ve seen these past few years, have compelled business leaders to embrace the wisdom of doing so.
In the Bloomberg piece, GE Appliances CEO Kevin Nolan summed up the situation succinctly: “I’ve always said, this is just economics, people are going to realize that the savings they thought they had (from offshoring operations) aren’t real, and it’s going to be better and cheaper to make them here.” TW
Editor’s Note: Jecka Glasman is chief commercial officer at Kornit Digital.
Above: Designer Love Hero demonstrates the power of on-demand sustainable textile and fashion production at Kornit Fashion Week London. (Photo: Haydon Perrior)BBrandsmust continue to keep up with production and react to trends despite ongoing global events causing shifts in the textile industry. Disruptions to the supply chain, material shortages, changing sourcing strategies, evolving job roles, shifting government policy, and public demand for sustainable practices are causing uncertainty across all industries, but color professionals can rely on digital color management technology to minimize at least some of the impact.
A well-implemented color management program not only reduces waste, but saves time on color submissions, assists with efficient communication across the supply chain, and keeps business moving while meeting the color quality expectations of consumers.
Because the apparel industry is, by nature, constantly in flux from the ebb and flow of trends —regardless of world events — designers and
By Lisa Beckcolor managers will sometimes say a color is visually “close enough” to get a collection to market quickly. The downside of this tactic? Quality and color accuracy may be sacrificed and that can end up damaging the brand’s reputation.
Color can be tough when you don’t have the right tools. Human color perception is subjective — meaning we all see color differently — and therefore, relying on our eyes alone to assess color is a fallible process. Although using a lightbox to evaluate fabric can certainly be part of a color control program, a more objective means of color evaluation is needed to avoid the effects of colorimetric phenomena like metamerism.
For example, lab dips for a matching separates collection looked perfectly matched when compared to the fabrics in the lightbox, but when the finished collection arrives at the retail store — where the lighting differs from what was used to evaluate the samples — consumers may notice those “matching” separates are different by a shade or two.
Digital color management tools, like spectrophotometers paired with the right software, help bring objectivity to the color assessment and approval process. When color can be communicated digitally across the supply chain in seconds, consistently accurate color measurement is ensured, and that reduces instances of miscommunication and minimizes the occurrence of potentially avoidable — and costly — color mistakes.
With a digital color management program in place, the process for color managers becomes simpler and
Digital color management programs simplify the color approval process and ensure accuracy in the supply chain.Spectrophotometers paired with color management software help provide objectivity, ensuring consistency and reducing mistakes during production.
more efficient. After the design or trend team chooses their color palette and fabric choices, it becomes the color manager’s job to decide if those choices are feasible in the desired combinations and to communicate the information to the textile mills, dye houses and other vendors.
Knowing that color is subjective, how does a color manager make sure suppliers are seeing, interpreting and understanding colors correctly?
To avoid miscommunication and delays caused by subjective color assessment and to speed up approval times, color should be communicated via QTX files containing reflectance measurements of the colors in a palette. Every color has its own unique reflectance curve so the chances of receiving the wrong color from a mill are extremely low if the staff is properly trained.
A color program assessment service can verify supplier color capabilities and their ability to meet quality expectations, as well as test the knowledgeability of staff. Such an assessment can expose areas where suppliers have room for improvement when it comes to color. Knowing what a supply chain is — or is not — capable of, allows color managers to make strategic partnership decisions, build trust with suppliers, and eventually empower their vendors, further streamlining movement through the supply chain.
In addition to better supplier relations and a higher percentage of firstshot matches, the use of digital color communication diminishes the need to ship physical lab dips — sometimes across the world — to gain approval, therefore saving companies time, money, and resources. For brands using only visual assessment, color approval could take months, but with digital color communication, the turnaround time for color approvals can be reduced to just a few weeks. If it turns out that adjustments do need to be made, that can be quickly achieved with very little back and forth.
Overall, digital color management creates a smoother color approval process that allows brands
not only the agility to keep up with demand and evolving trends, but also stay ahead of their production cycle. Now, color managers can spend less time going in circles with color approvals and perhaps focus more on the new responsibilities that are starting to fall into their hands.
Demand from consumers and government bodies for higher sustainability standards and more sourcing transparency in the textile and apparel industry is a drum that is steadily beating louder. Generation Z tends to have strong preferences for brands that are outspoken and honest about their commitment to reducing waste, recycling, lowering their impact on the environment, and refusing to work with suppliers known for or suspected of using forced labor. In addition, bills have been introduced in the United States and Europe that would force some companies to map their supply chains and install verifiable sustainability measures.
For example, a state senator in New York recently introduced the Fashion Sustainability and Social Accountability Act that is pending in the state Senate, and brands are watching closely. This bill would require retailers and manufacturers who sell their products in New York state and do more than $100 million in business globally to disclose the environmental and social impact of
their business activities. These companies would also have to provide supply chain mapping proving their use of ethically sourced labor and materials. If passed, this legislation would affect thousands of brands.
What new responsibilities will color managers potentially take on as a result of policies like this? Some are being tasked with sustainability targets in their departments, such as reducing overall waste, reducing the number of color approvals, and making sure the suppliers they contract with are using sustainable and ethical practices.
With a solid digital color management program in place and by working with suppliers that have been verified via an assessment service, color managers can easily work towards these goals.
It is undeniable that the future of apparel production is increasingly moving towards digitalization. World events, fashion trends, and government policy will continue to reshape the industry, and brands need to be agile enough to react and pivot. When you have a robust digital color management program in place to streamline the production cycle, you can insulate your brand from some of these disruptions and keep product moving from designer concept to final consumer.
TW
Datacolor’s SpectraVision benchtop spectrophotometer was designed for multi-colored, textured, small or irregularly shaped samples. Editor’s Note: Lisa Beck is product manager, Datacolor, Lawrenceville, N.J.TTo succeed in today’s ever-more competitive textile industry, weaving mills must meet a challenging range of essential requirements, including optimized production workflow, high-quality output, cost-efficient operation and on-time delivery. Mills must examine every step of their production process to identify and exploit their optimization potential. Automation along the entire process chain is central in this effort. Switzerland-based Stäubli Group is a competent global partner for mills that want to increase their productivity, delivering automation solutions for weaving preparation, weaving all sorts of fabrics, and mastering new application challenges.
SAFIR automatic drawing-in machines enable the mill’s drawingin department to supply the required amount of completely drawn-in warp beams to the weaving department. The weaving harness and reed are
prepared to perfection, according to Stäubli, with no crossed threads, no multiple threads in heddle, and no drop-wire or repeat errors. This improves the ratio of weaving machines per operator. It also reduces downtime, thereby boosting the efficiency and productivity of each weaving machine. The use of automatic instead of manual drawing-in typically improves the mill’s overall weaving efficiency by 1 to 4 percent or more, which over a year can amount to several hundred thousand meters of fabric, depending on the size of the mill.
The trend toward higher-quality fabrics and the use of increasingly finer and more specific yarns increases the number and complexity of warp threads to be drawn in. If the mill relies on manual drawing in, more workers will be required. But finding and keeping suitable workers in this field is becoming
increasingly difficult. The willingness to do such work is disappearing, and the organizational effort required for manual drawing in is significant. Another drawback of manual drawing in is that human error creeps in as the thousands of warp threads are drawn into the shafts, heddles, reed and drop wires pinned onto the weaving machine.
When it comes to warp changes, Stäubli Textile provides a complete range of warp-tying solutions that can handle the entire spectrum of fibers and filaments, from the finest silk to coarse polypropylene tape. These high-precision machines are reliable workhorses that can be easily integrated into the workflow of any weaving mill. They feature many state-of-the-art technologies like automatic docking to the warp and a unique auto-reverse function that repeats the yarn separation without operator intervention when a double end is detected.
Stäubli Textile division collaborates with the Stäubli Group’s Robotics division to develop new automation solutions for the textile industry. Synergies and intensive know-how exchange among the 600 research and development specialists and application engineers in the Stäubli Group have led to new automation examples like pick and pack bobbin handling, and solutions for loading yarn bobbins on preparation creels for both direct or sectional beaming. Stäubli robots can be designed for any application in any industry where speed, precision, and reliability are required. The comprehensive range of robots — including industrial, collaborative, mobile, and AGV — are all Industry 4.0 compliant to support industry transformation. Textile industrials can count on the Stäubli Group to support their efficient production with proven automation solutions today and new leadingedge solutions tomorrow. TW
TW Special Report Stäubli Textile offers automation solutions for today’s modern weaving mills including the SAFIR automatic drawing-in machines.Jim Kearns, executive director and CFO of Alsco Uniforms, recently was elected chair of the board of directors of TRSA – the organization Strengthening the Linen, Uniform and Facility Services Industry.
Teijin Holdings USA President Jane Thomas has again been appointed to the Investment Advisory Council of the U.S. Department of Commerce. She will serve until 2024.
Spartanburg, S.C.-based Milliken & Company has promoted David Smith to executive vice president and president of Milliken’s Textile Business. He replaces Chad McAllister who has left the company.
Ulrich Reifenhäuser, chief sales officer of the Germany-based Reifenhäuser Group, recently was awarded the 2022 Georg Menges Prize at the 31st International Colloquium on Plastics Technology. The award recognizes those who have contributed outstanding service to the transfer of research results into industrial practice.
Web Industires Inc., Marlborough, Mass., has promoted Kathrin Doyle Arena to vice president of human resources.
Matt O’Sickey has joined the Association of the Nonwovens Fabrics Industry (INDA), Cary, N.C., as director of Education and Technical Affairs. INDA also recently named Ryan Ragan director of Membership and Industry Relations.
Kraig Biocraft Laboratories Inc., Ann Arbor, Mich., has contracted Jeff Dorton to help the company develop innovative yarns and fabrics using its Dragon Silk™ spider silk fiber. Initial developments will be used by Spydasilk Enterprises, the company’s Singapore-based joint venture apparel brand.
Mayzo Inc., a specialty chemicals company based in Suwanee, Ga., has named Doug Hartman director of sales and customer care. He replaces Eduardo Padilla who was promoted to president of the company last year.
Elin Wengström has joined Coloreel, Stockholm, as vice president of marketing.
Cambridge, England-based Global Inkjet Systems Ltd. (GIS), a Nano Dimension division, has announced that GIS Co-founder Nick Geddes has joined the executive team at Nano Dimension as senior chief technology officer. Steve Williamson has been promoted to GIS general manager.
The New York City-based American Down and Feather Council (ADFC), a division of the Home Fashion Products Association (HFPA), has named Brett Rife chair. Rife is vice president of sales for Keeco LLC and succeeds former Chair Travis Stier.
Advanced Functional Fabrics of America Inc. (AFFOA), Cambridge, Mass., has announced the promotion of Michelle Farrington to chief technology officer. She will lead AFFOA’s integrated technology development team and is responsible for developing AFFOA’s technical strategy.
Steven Bethell of Bank and Vogue has joined the board of directors at AcceleratingCircularity.
Search the People archive on-line at TextileWorld.com.
Conover, N.C.-based Nufabrx® has named former W.L. Gore & Associates CEO Dr. Jason Field board member; and Elise Donahue, former CEO of Airborne, South Beach Diet and co-founder of Prestige Brands, advisory board member.
Unifi Inc., Greensboro, N.C., has elected Frank Blake to its board of directors.
Dearborn, Mich.-based Carhartt has appointed Susan Hennike chief brand officer. She reports to President and CEO Linda Hubbard.
Chico’s FAS Inc., Fort Myers, Fla., has named Leana Less senior vice president of marketing.
Tommy Bruno has joined Culp Inc., High Point, N.C., as executive vice president of Culp Home Fashions. He replaces long-time employee Sandy Brown who is retiring at the end of the year. The company also named Teresa Huffman chief human resources officer; and promoted Forrest Buck to vice president of Information Technology.
Emilie Arel, president and CEO of Casper Sleep, has joined the board of directors at Macy’s Inc., New York City. TW
Smith Farrington Ragan Blake O’SickeyCalhoun,Ga.-based Mannington Commercial recently joined the Drawdown Georgia Business Compact,a consortium of Georgia businesses that are working together to address climate issues in the state with the shared goal of transitioning Georgia to net zero carbon emissions by 2050.
Pakistan-based Gadoon Textile Mills Ltd.,a member of the Yunus Brothers Group,has joined the Zurich-based International Textile Manufacturers Federation (ITMF) as a corporate member.
Atlanta-based sublimation paper manufacturer Beaver Paper has announced price increases of up to 12 percent across all its paper grades.The increase goes into effect for all deliveries after October 1,2022.
Atlas Copco recently introduced a new generation of variable speed drive compressor named the GA VSDS.
Germany-based Freudenberg Performance Materials was recently awarded the EcoVadis Silver Medal for U.K.-based facilities in Ebbw Vale and Littleborough that manufacture advance wound care and ostomy products.The silver medal recognizes the company’s performance in environment,ethics,labor and human rights,and sustainable procurement categories; and ranks the company in the top 25 percent of companies rated by EcoVadis.The company also recently established the Apparel Technical Solution Center - Asia at its Nantong,China, factory,to expand innovation capabilities.
New York City-based Carnegie Fabrics has expanded its Xorel® biobased fabric with four new patterns — Ashford,Windsor, Dover and Galway.
New York City-based Schumacher has opened its first concept showroom in Nashville,Tenn.Located at 609 Merritt Ave.in the Wedgewood-Houston neighborhood,the space features a to-the-trade showroom exclusively for interior designers and also a luxury boutique for consumers interested in smaller items.
Epson,Los Alamitos, Calif.,has introduced its first Epson-built spectrophotometer,the SD-10.
Finland-based companies Marimekko and Spinnova have collaborated on a capsule clothing collection that features Marimekko’s iconic Unikko poppy print on a blended SPINNOVA® fiber/organic cotton/cotton fabric.
Matouk reports it received STeP by OEKO-TEX® certification for sustainable and responsible textile production practices at the company’s Fall River, Mass.,facilities. Pendleton Woolen Mills also recently announced both its centuryold mills in Washougal, Wash.,are now STeP by OEKO-TEX certified.
Suominen,Helsinki, has announced general surcharges on all its products in North America as a result of increases in raw materials,energy and freight costs.
Regel™ recycled acrylic fiber from Thai Acrylic Fibre Co.,a member of the Aditya Birla Group,is now bluesign® Approved.
Boston Scientific Solutions Inc.,Woburn,Mass., has launched the NatronSilTexAS Series of screen printing silicone inks for socks and gloves.
Finotex,Miami,recently launched a new website located at finotex.com. The site was redesigned with the user experience in mind and includes all the information as well as a geolocation feature to help customers with their specific branding needs.
Gildan Activewear Inc., Montreal,recently published its 18th Environmental,Social and Governance (ESG) Report.
Santa Clara,Calif.-based Avery Dennison and the San Francisco 49ers recently announced an exclusive partnership naming Avery Dennison the official cutting-edge embellishment partner of the football team.Avery Dennison will provide smart embellishments and digital labels for select 49ers Fanatics merchandise to introduce digital connectivity into the products.
Alpharetta,Ga.-based Datatex TIS Inc. reports Parkdale Inc. selected NOW as its next generation enterprise resource planning (ERP) solution replacing an older Datatex TIM ERP system. Parkdale also will implement the solution at its U.S.Cotton business. TW
A garment from Marimekko and Spinnova’s collaboration. Atlas Copco’s GA1-4 :Fiber and Filament Extrusion Fundamentals,organized by the Nonwovens Institute (NWI) and the Association of the Nonwoven Fabrics Industry (INDA),NC State University, Raleigh,N.C.Visit inda.org.
3-4 :Synthetic Yarn and Fabric Association (SYFA) Fall Conference —celebrating 50 years —Sheraton Charlotte Airport Hotel,Charlotte,N.C.Visit the syfa.org.
11-12 :Marine Fabricators Association (MFA) Southwest Regional Workshop, organized by the Advanced Textiles Associ-
ation (ATA),SewLong Custom Covers, South Salt Lake City,and SugarHouse Awning Industries,Midvale,Utah.Visit marine.textiles.org/marineworkshops.
14-17 :Hygienix™ 2022,organized by INDA,the Roosevelt New Orleans Hotel,New Orleans.Visit hygienix.org.
16-18 :Upholstery & Trim Annual Convention 2022,organized by ATA, Westgate Las Vegas Resort and Casino, Las Vegas.Visit textiles.org/utac.
20-24 :ITMAAsia + CITME2022, National Exhibition and Convention Center,Shanghai,China.Visit itmaasia.com.
6 :Southern Textile Association (STA) Southern Division fall meeting,upstate South Carolina,venue TBD.Visit southerntextile.org.
6-9 :Nonwoven Product Development And Innovation,organized by NWIand INDA, NWI headquarters,NC State University, Raleigh,N.C.Visit inda.org.
7-8 :Driving Digital Textile Transformation … Go! conference,sponsored by the American Association ofTextile Chemists and Colorists and Printing United Alliance, Sheraton Imperial Hotel,Durham,N.C. Visit aatcc.org/aatcc-events/printing2022. TW
SC Mngt, Finance, Businss (w/ IT) or rel +3 yrs exp work’g in apparel, intimates & swimwr; negotiat’g agrmnts rel to SC & import of textiles; perfrm’g systs integratn us’g 3D prototyp’g & dvlpmt (us’g 3D model’g sftwr such as Browzwear, Clo & TukaTech); & B2B sales. Apply atsusiek@brandix.com
With athlete performance and sustainability in mind, Nike’s Forward platform focuses on needlepunching for apparel creation.
Go online to TextileWorld.com for archived Quality Fabric articles.
The garments feature raw cut pockets with no closures or embellishments to make it easier to recycle at the end of its useful life.
are a relatively new textile material compared to woven and knit constructions that are thousands of years old. The nonwovens process allows a wide variety of fabric types with unique properties to be produced depending on production parameters. This adaptability has led to an extensive portfolio of products used in automotive, construction, filtration, and medical applications, to name just a few markets.
There is still lots of potential to unlock in nonwovens production, especially as it relates to apparel and fashion applications. Although applications are broad, the properties of a nonwoven fabric typically do not have the aesthetics or performance characteristics sought in a non-disposable apparel fabric. However, Beaverton, Ore.-based Nike Inc. is looking to change that notion.
The company recently introduced Nike Forward — a platform used to produce a sustainable nonwoven that the company believes can be used in place of traditional fleece fabrics in athletic applications. The motivation behind the platform was to help solve problems for athletes with environmental concerns top-of-mind.
Nike saw the potential of nonwoven manufacturing techniques to reduce the number of steps required to produce a fabric compared to traditional knit or woven fabrics and set about “hacking” a needlepunching machine in a research and development process that took more than five years.
Fewer processing steps — as with all nonwovens, the process goes from fiber directly to fabric — results in less energy consumption, which Nike reports translates into an average of 75-percent reduction in the carbon footprint compared to the traditional knit fleece fabrics it currently uses.
A diverse range of fibers can be incorporated into the layers from pre- and post-consumer waste as well as industrial waste; and the garments feature 70-percent recycled content by weight. No water is used to dye or finish the fabric, and garments initially will be available in only one color — gray. The garments also feature raw cut pockets and no embellishments such as trims, zippers or other closures. These design details result in a garment that is easier to recycle at the end of its useful life.
The initial introduction of Nike Forward includes a crew and hoodie style made using 100-percent polyester in a five-layer construction. This lightweight material, which will break in over time, is warm and meets Nike’s Therma-FIT ADV technology standards for warmth without the weight.
Nike does admit piling is possible and provides specific care directions to mitigate the issue.
“As part of our commitment to serve athletes by offering more sustainable options and meeting our bold, sciencebased impact targets, we’re introducing a material innovation that can be adapted to different lifestyle and performance purposes,” says Seana Hannah, vice president, Sustainable Innovation, Nike.
“We believe this platform has the potential to reset the way we think about material and apparel,” said Aaron Heiser, vice president, Global Apparel Product Merchandising, Nike. “This is the biggest Nike apparel innovation since Dri-Fit 30 years ago and has huge potential to transform the industry in the way that Air and Flyknit did for Nike footwear.”
According to Nike: “Today Nike Forward shows up as a hoodie — the uniform of sport and a style around the globe. Tomorrow it could be anything.” TW
website / magazine / e-newsletter
Subscribe to Textile World for complete coverage of the U.S. and global textile manufacturing industry — the latest technologies, applications, regulations and trends.
Website, eNewsletter, Magazine, and now in Digital Editions available.
Print advertisers receive additional reach and linking with free inclusion in Digital Editions.
read / share / engage TextileWorld.com
Comfier. Lighter. Smarter. Stronger. Make sure your footwear designs check all the boxes with advanced materials from DuPont.
Our versatile Hytrel® and Zytel® solutions present innovative opportunities across footwear elements. Propel performance with outstanding properties in flexibility and strength. Streamline your production with easy processing. Our team of experts is ready to help you put your best foot forward. dupont.com/mobility-materials/consumer/sporting-goods/footwear.html
Visit us at the K Show – Hall 6, Stand C43 – to learn more.