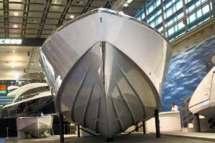
9 minute read
Jute fibre spinning process
Nozzle drawing- The glass fed in is melted in a heated melt tub at 1250–1400oC. Then, it emerges at the bottom of the melt tub from nozzle holes of 1–25 mm diameter and it is taken off and drawn. The filaments solidify and are finished and wound. One can find them in the shops as various kinds of “glass silk”.Nozzle blowing- The same as with nozzle-drawing, glass balls are melted in the tub. The melt emerging from the nozzle holes is then taken by pressed air, which draws the liquid glass so as to make fibres of 6–10 um diameter. A fluttering effect is caused by the flow of pressed air, which results in fibres of lengths from 50 to 300 mm. A lubricant is put on and the fibres are laid down on a sieve drum which sucks them in. The dry web received is held together by the long fibres, the short ones lying in between them as a filling material. Then, the slivers of glass fibre material are cut. Rod drawing- By means of a burner, bundles of glass rods are melted at their bottom ends. This results in drops which, as they fall down, draw filaments after them. The filaments are taken by a rotating drum, a squeegee laying them down onto a perforated belt. Thus, a dry web is received which can be wound as glass fibre slivers. Machine performance being limited by the number of glass rods fed in, the rotating drum may be combined with nozzle-drawing, which results in drum-drawing. This multiplies machine performance. The dry web is again laid down onto a perforated belt and solidified or, after winding it so as to receive slivers, cut for further processing on machines producing wet laid nonwovens. Using and processing glass fibres is not without any problems. For example, fine pieces of broken fibres may disturb if the work place is not well prepared for the purpose. Using the nonwovens to manufacture glass-fibre reinforced plastics, it is important the surface of the plastic material is fully even. Ends of fibre looking out may be pulled out or loosened by outward stress (temperature, gases, liquids), which may influence material characteristics. In some cases, it is advisable to cover up such layers of glass fibre with suitable chemical fibres.
PROPERTIES:
Advertisement
1.
Mechanical strength: Fibreglass has a specific resistance greater than steel. So, it is used to make high-performance fabrics 2. Electrical characteristics: Fibreglass is a good electrical insulator even at low thickness. 3. Incombustibility: Since fibreglass is a mineral material, it is naturally incombustible. It does not propagate or support a flame. It does not emit smoke or toxic products when exposed to heat.
4. Dimensional stability: Fibreglass is not sensitive to variations in temperature. It has a low coefficient of linear expansion.
5.
Compatibility with organic matters: Fibreglass can have varying sizes and has the ability to combine with many synthetic resins and certain mineral matrices like cement. 6. Non-rotting: Fibreglass does not rot and remains unaffected by the action of rodents and insects.
7.
Thermal conductivity: Fibreglass has low thermal conductivity making it highly useful in the building industry. 8. Dielectric permeability: This property of fibreglass makes it suitable for electromagnetic windows.
BLENDS: 1. Glass-reinforced plastic (GRP) is a composite material or fibre-reinforced plastic made of a plastic reinforced by fine glass commonly referred to as fibreglass.
2. Reinforced concrete: Glass fibre concretes are mainly used in exterior building façade panels and as architectural precast concrete.
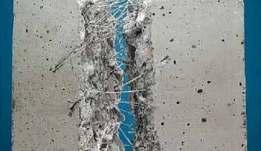


3. Aramid-Glass: The high impact resistance and strength of aramid fibre combines with the good compressive and tensile strength of glass. The aramid glass laminate has also im
proved delaminating resistance.
MS. HETAL MISTRY
INTERN - TEXTILE VALUE CHAIN

Highlight of the article
The jute fibre is a natural fibre. The fibre which is obtained from the bast layer of the plants Corchorus capsularis and Corchorus olitorius is called jute. It is one kind of cellulosic fibre.
Spinning is the first steps of textile product processing. The process of making yarn from the textile fibre is called spinning. zThere are two types of jute spinning process. They are:
1. Sliver spinning 2. Roving spinning
The jute fibre is a natural fibre. The fibre which is obtained from the bast layer of the plants Corchorus capsularis and Corchorus olitorius is called jute. It is one kind of cellulosic fibre. Jute is also called as “Golden Fibre”. Jute fibre is used for sacking, burlap, and twine as a backing material for tufted carpets. Spinning is the first steps of textile product processing. The process of making yarn from the textile fibre is called spinning. There are various types of spinning methods for producing various types of yarns. If we notice, we will see that the Jute Fibres are converted into fine yarn, hessian yarn, carpet yarn, sacking yarn and jute blended yarn depending on the end use of the yarn. For producing this type of jute yarn different spinning methods/process are used. There are two types of jute spinning process. They are: 1. Sliver spinning 2. Roving spinning 1. Sliver Spinning: In sliver spinning, yarn is produced from the sliver of finisher drawing frame. Sliver spinning is used for majority of jute yarn. 2. Roving Spinning: In roving spinning, yarn is produced from roving sliver of roving frame. By this spinning process finer and superior quality jute yarn can be produced. In this spinning process after passing through three drawing frame, sliver are converted into rove by a roving frame and after that a spinning frame is used to produce yarn.

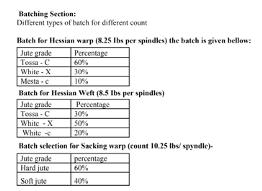

Fig.: Jute Spinning
Jute yarn manufacturing process flowchart: Jute spinning can be classified in five divisions. They are: Batching, Carding, Drawing, Spinning, Winding. They are the main process, either there are sub process to manufacture jute yarn. There are two types of yarn are produced from jute spinning; sacking yarn and hessian yarn. The manufacturing process of raw jute are mentioned below. Flow Chart of Raw Jute Spinning Process Fig.: Flow Chart of Raw Jute Spinning Process Emulsion Section: What is emulsion: Emulsion is a mixture of some lubricating agents which is applied on jute fibre to make the fibre soften and flexible for spinning; prepared for spun. An emulsion is an intimate mixture of two immiscible liquids where one is dispersed in small globules on the other and addition of a third substance brings stability. Emulsion is made by splitting up oil into minute drops which are prevented from reuniting in water. Basic ingredients of an emulsion : Water
Mineral oil and Emulsifier The reasons why emulsion is used are given below:- To make the jute fibre soft. To increase flexibility. To reduce fibre stiffness and brittleness. To increase cohesiveness of fibre. Recipe for Emulsion:- Oil 27.67% Water 72.28% Emulsifier 0.05% Fig. Emulsion Making Procedure: Emulsifier and equal quantity of mineral oil are placed in the mixing tang. Adding remaining oil then add water and mixed for a period of time. Then transferring to the reserve tank to supply next machine Softening Section: After preparing emulsion it is applied on the fibre by softener or spreader machine. The discussion is here about softener machine. The figure and function of softener machine are given belowFunction: The long jute fibres are fed on the machine by feed rollers. Gripping and beating the fibres by spirally fluted rollers. Emulsion is sprayed after passing one third portion of the fluted roller zone. The fibres are delivered through delivery roller and delivery sheet. Function: The long jute fibres are fed on the machine by feed rollers. Gripping and beating the fibres by spirally fluted rollers. Emulsion is sprayed after passing one third portion of the fluted roller zone. The fibres are delivered through delivery roller and delivery sheet.
Deeping System: Why it is used? It is a system developed by the authority of BJM by means of which the cuttings portion of the long jute fibre are slightly sink into the emulsion before feeding the fibres in softener machine so that a large amount of emulsion can be applied to the cuttings
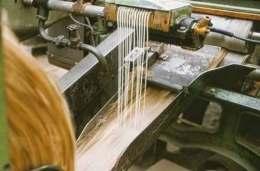
portion of the fibre and make it more flexible. Fig.: Deeping System
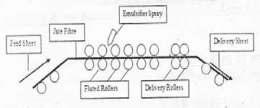

Pilling Section: Definition of Pilling: It is the process by which emulsion applied long jute fibres are kept under a thick fabric for a certain time as a result fibre become soft and flexible. Depending on fibre quality the pilling time is varied. Assumption of pilling assembly:- 19 ft*5.5 ft*6 ft
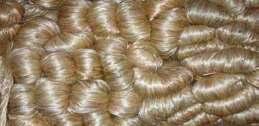
Fig.: Pilling Carding Section: Carding is the process by which long strikes of jute fibres, while passing through high speed
pinned rollers, are broken down into an entangled mass and delivered in roll form of uniform weight per unit length.
Breaker Card: Fig.: Breaker Card Machine Information: Delivery rate=600 kg /hr Dollop weight =34 lbs , Clock length=13 yards , Clock rotation=360 degree , Draft=6 , Sliver weight /100 yards=18 lbs, Surface speed of different rollers, Surface speed of cylinder =3935 ft/minute, Surface speed of pin feed roller =22.5 ft/min, Surface speed of worker =70.61 ft/min, Surface speed of stripper =81.7 ft/min, Surface of doffer =192 ft/minute, Surface of Delivery roller =268.13 ft/minute Finisher Card: Fig.: Finisher Card Machine Information: Doubling=11:1 Draft=10.6, Delivery=400-450 kg/h

Finisher roll weight /100 yards=16 lbs, Surface speed of different rollers, SS of stripper=398.48 ft/min SS of worker=54.39 ft/min, SS of doffer=103.389 ft/min SS of cylinder=2388.6 ft/ min, SS of feed stripper=34.33 ft/min, SS of top drawing roller=117.20 ft/min, SS of bottom drawing roller=123.21 ft/min, SS of
front delivery roller=128.85 ft/min Drawing Section: After above these process drawing & doubling is done. JUTE Ring Spinning Frame: Finally we get jute yarn from spinning frame.

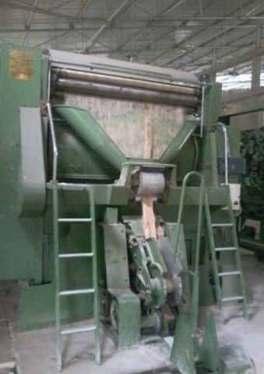
Fig.: Jute Yarn
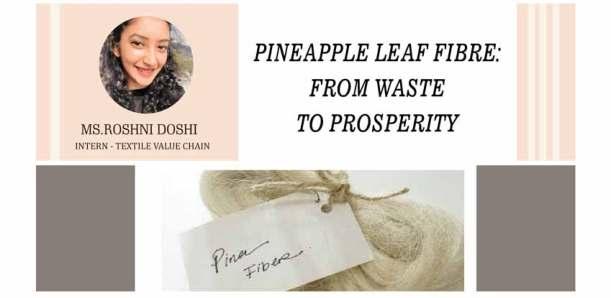
Highlight of the article
Every year tones of Pineapple leaf fibre are being produced but very small portions are being used. Pina is a traditional Philippine fibre made from pineapple leaves. The name Pina ia a Spanish word, meaning Pineapple. The fibres derived from pineapple leaves are long, strong, white, silky with one of the best fineness indexes among vegetal fibres, which make them suitable for many industrial applications. The fibres are detached from the leaves by the hand scraping method (coconut husk are good for this). Fibre from Pineapple leaves for long has been used by Philippine handicraft artisans to produce cloth. Up to 15-18 pieces of white, creamy lustrous fibre, about 60 cm long each can be provided by a kilo of leaves and it easily retains dyes. The Pina fibre is softer, and has a high lustre, and is usually white or ivory in colour. As the making process of Pina fabric is tedious, time consuming and labour intensive, it becomes quiet expensive. Pineapple fibres, primarily used in hand weaving are divided into two groups- the linuan or fine fibres and bastos or coarse fibres.

C
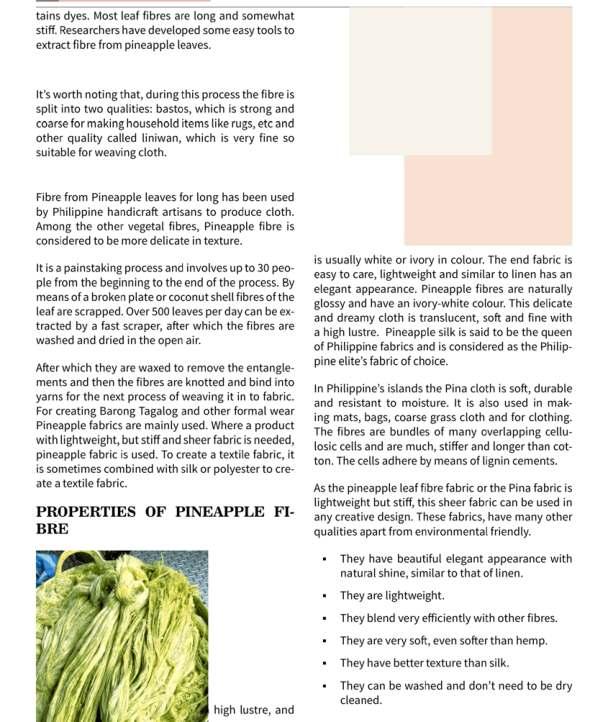
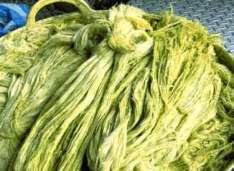