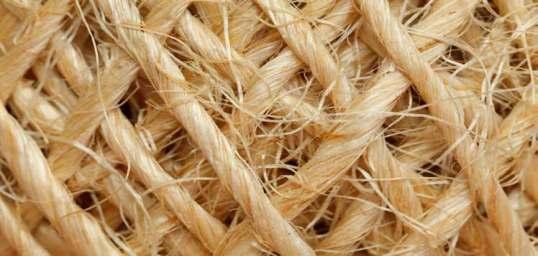
9 minute read
Wet spinning
MS. MANALI BHANUSHALI
INTERN AT TEXTILE VALUE CHAIN
Advertisement
SISAL FIBRE SPINNING
Highlight of the article
Sisal fiber obtained from the plant Agave Sisalana, yields a stiff fibre, traditionally used in making twine, rope and also dartboards. Today Brazil is major world producer of sisal. The first commercial plantings in Brazil were made in late 1930’s and the first sisal fibre exports from there were made in 1946. Sisal plants consists of a rosette of sword-shaped leaves about 1.5 to 2 meters long. Young leaves may have a few minute thin along their margins, but lose them as they mature. The sisal plant has a 7-10 years life time and typically produces 200-250 commercially usable leaves. Traditionally, sisal has been the leading material for agricultural twin (binder twin and baler twin) because of its strength, durability to stretches, affinity for certain dyestuffs, and resistance to deteriorstion in salt water.
But the importance of this traditional use is diminishing with competition from polypropylene and the development of other haymaking techniques, while new higher-valued sisal has been developed.
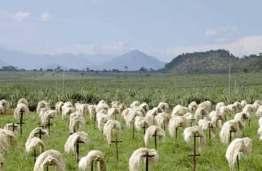
Natural fibres are fibres that are produced by plants, animals, and geological processes. One of the most widely used natural fibers is Sisal fiber. It is also very easily cultivated. You can obtain Sisal fiber from Sisal plant. The plant, was formally known as Agave Sisalana. These plants produce rosettes of sword-shaped leaves which start out toothed, and gradually lose their teeth with maturity. Decortication is a process in which every leaf loses its long, straight fibers. During decortication, the leaves are beaten down to remove the pulp and plant material, leaving the tough fibers behind. Sisal fiber is a high renewable source of energy , also it is fully biodegradable. Green composites were fabricated with soy protein resin which were modified with gelatin. Sisal fiber, modified soy protein resins, and composites were characterized for their mechanical and thermal properties. Sisal fibre is low maintenance with minimal wear and tear, and exceptionally durable. It is not suitable for a smooth wall finish and also not recommended for wet areas, because it is too tough for textiles and fabrics. The texture of sisal is fine because of which it takes dyes easily and offers the largest range of dyed colours of all natural fibres. Sisal agriculture uses zero pesticides or chemical fertilizers. It is traditionally used in making twine, rope and also dartboards because of its stiff fiber. The sisal plant has vascular tissue from which sisal fiber is manufactured (Agavesisalana). It is used in automotive friction parts (brakes, clutches), where it imparts green strength to performs, and for enhancing texture in coatings application. Sisal fibre is derived from the leaves of the plant. After harvest, the freshly harvested leaves of the agave plant are pressed in machines to separate out the fibers. Subsequently, the separated fibers are washed, dried in the sun, bleached, and combed with rotating brushes. The dried fibre represents only 4% of the total weight of the leaf. The length and diameter of sisal fibre is 80 to 120 cm in length and 0.2 to 0.4 mm respectively. Sisal fibre is made from the process of Decortication, leaves are crushed and beaten by a rotating wheel set with blunt knives, so that only fibres remain. The other parts of the leaf are washed away by water. Decorticated fibres are washed before drying the sun or by hot air. The fibers can then be spun into thread for twine and textile production, or pulped to make paper products. The fibre quality depends upon moisture content so proper drying is important. To get better grades of fibre artificial drying has been found in place of sun drying. Dry fibres are machine combed and sorted into various grades, largely on the basis of the previous in-field separation of leaves into size groups.
A sisal fibre in cross-section is built up of about 100 fibre cells. The cell walls consist of several layers of fibrillar. In the primary wall, the fibrillae have a reticulated structure. In the outer secondary wall (S1), which is located inside the primary wall, the fibrillae are arranged in spirals with a spiral angle of 40° (for sisal fibre) in relation to the longitudinal axis of the cell. The fibrillae in the inner secondary wall (S2) of sisal fibres have a sharper slope, 18° to 25°. The thin, innermost, tertiary wall has a parallel fibrillar structure and encloses the lumen. The fibrillae are, in turn, built up of micro-fibrillae with a thickness of about 20µm. The microfibrillae are composed of
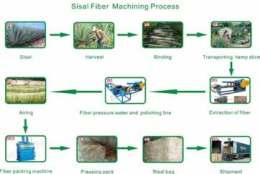
cellulose molecular chains with a thickness of 0.7µm and a length of a few µm.
The spinning process of sisal fiber starts with these following basic steps:
1. After extracting sisal fiber from sisal leaf by using automatic decorticator, after cleaning and drying, it is sent to sisal yarn factory.
2. The fiber must be sprayed with certain moisture and sesame oil before using in order to make sure the process goes smoothly.
3. Sisal combing machine is used to comb fiber and make the sisal sliver to be in average size and be straight.
4.after the combing process is done ,the fiber is sent to the drawing machine for drawing processing where the sisal sliver are passed through a series of rollers, thus straightening the individual fibres and making them more parallel.
5. The fibers are then sent to the spinning machine for making yarn.
6. After the above process , the yarns are rolled out of the spinning machine. And the process is complete. Uses and Applications : Sisal is broadly categorized under three grades and applied in various industries according to the grades.
Low-grade: cellulose and hemicellulose portion are mainly used for-
Paper industry
Cordage industry
Medium-grade: used in making of binder twine, ropes, bales-
Agriculture
Marine
General industrial purpose
MS. VASAVI MEHTA
INTERN - TEXTILE VALUE CHAIN
WET SPINNING

Highlight of the article
Wet spinning is the oldest process. - It is used for fiber-forming substances that have been dissolved in a solvent. - The spinnerets are submerged in a chemical bath and as the filaments emerge they precipitate from solution and solidify. - It is called “Wet spinning” since the solution is extruded directly into the precipitating liquid. - Examples: Rayon, Aramid, Acrylic, etc.
The first monetarily effective strategy for the production of synthetic fiber was the wet turning of the cellulosic fiber, rayon. This technique is as yet utilized today. Basically, the procedure includes the utilization of a proper fluid arrangement, which is siphoned through a little spout, which is known as a spinneret, into a synthetic shower that coagulates the expelled arrangement of unlimited strands of fibers. These coagulated persistent filaments are drawn out of the shower, cleansed by washing, dried and afterward twisted onto spools. The development of the spinneret might be shifted by the ideal outcomes. On the off chance that the spinneret has one expulsion gap, at that point a monofilament yarn will be created. In the event that the spinneret has numerous gaps, at that point a multifilament yarn will be created. The size and number of the openings of spinneret might be fluctuated. In this manner, the number and size of the fibers of which it is developed decide the thickness, or denier of the yarn. Likewise, the measure of turn given the prepared yarn will influence its surface and quality.
On the off chance that we talk in detail, Wet turning is the most mind boggling of the turning procedures. Some wet turning forms require the polymer answer for be kept above or beneath surrounding temperature and subsequently a warmth exchanger is utilized. The spinnerets are drenched in tanks containing the coagulation into which the fibers are expelled. The expulsion course is variable from vertically upwards to flat. The spinnerets utilized in wet-turning can have up to 2,000 gaps for business applications. In any case, ordinary wet turning is the slowest of the chief procedures having windup rates to roughly 150 m/min.
This procedure depends on precipitation just, without substance recovery. The dissolvable diffuses out of the extrudate into the shower, and a non-dissolvable diffuses from the shower into the extrudate. The polymer encourages as a gel at first at the extrudate-coagulant interface however logically all through the extrudate. The coagulation rate affects the gel structure and the last fiber properties. The preparing factors are fixation and temperature of the turning arrangement, structure, focus and temperature of the turn shower; and the stretch applied during turning. These conditions bring down the turn shower temperature, and lower stretch during turning. These conditions lead to more noteworthy homogeneity and higher orientability in a resulting extending or attracting procedure and subsequently to better malleable properties. The turn shower and turning arrangements may incorporate limited quantities of altering specialists that will in general improve homogeneity of the spun yarn. The coagulated fibers ignore a manual for driven rollers. The means succeeding coagulation differ as indicated by the item however ordinarily incorporate washing, extending, finish application, drying, creasing, controlled unwinding for a tow, in addition to cutting for a staple fiber item.
Wet turning is applied to polymers which don’t soften and disintegrate just in non-unpredictable or thermally temperamental solvents. In this procedure, the polymer is disintegrated in a reasonable dissolvable, and the arrangement is expelled through a spinneret to a fluid shower containing low sub-atomic weight synthetics. This substance is a non dissolvable to the polymer yet is uninhibitedly miscible with the dissolvable used to plan polymer dope
In this procedure, the strategy for arrangement readiness, filtration and expulsion i.e., polymer dope planning is fundamentally the same as those utilized for dry turning. Be that as it may, increasingly weaken polymer arrangement is utilized for entangled hardening process. Polymer content fluctuates between (5 % to25 %) it 20 to 5000 balance thickness. For expulsion, a similar general standards are utilized for the plan of the spinnerets. In any case, the separating of the gaps in the wet turning is nearer than the dry turning in light of the fact that the polymer stream he moves in a fluid medium after expulsion. Nearness of fluid confines t blending of the fibers during hardening. The turn square is anything but a compacted one like that of liquefy turning and dry turning due to the nearness of exceptional turn shower with synthetic compounds. Rather, the spinnerets are lowered in turn shower and associated with the turn obstruct by move e of funnels. Likewise, the spinneret pack present in turn synthetically inactive material. The cementing procedure of the polymer arrangement comprises of extraction of the dissolvable by the synthetic compounds present in the turn shower.