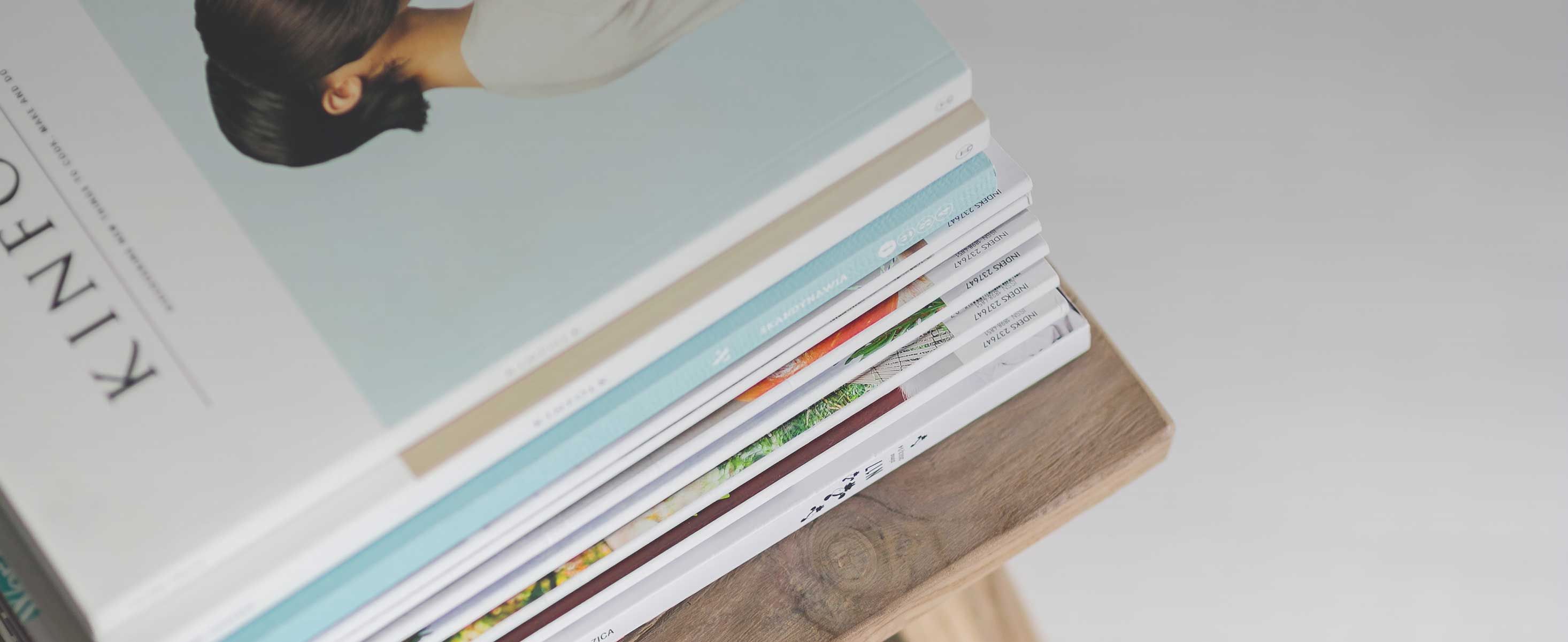
8 minute read
Surat Report
The onslaught of cheap imports of Nylon yarn wounded local yarn spinners The members of the Nylon Spinners Association said that the Indian nylon filament yarn industry is suffering due to the onslaught of cheap imports. The imports of nylon yarn from China have increased from avg 23 mt/ month in the year 2016 to 1,250 mt/ month by the year 2019, the rise of almost 5180%. An extreme surge of imported yarn at different prices is affecting the local yarn spinning industry. In a press release, the association has stated that against the onslaught of cheap imports of the nylon yarn, the spinners had applied to impose Anti Dumping Duty. DGTR authorities conducted a detailed investigation of facts and figures of application and the DGTR office has concluded that there is a genuine injury to local yarn spinners. DGTR office has issued its “Disclosure Report” on nylon filament yarn anti-dumping petition on 4th February 2020. However, after the issue of disclosure report, vicious propaganda against this Anti Dumping Duty started by importers lobby by a few individuals with vested interests. The allegations issued by this lobby is baseless. Nylon accounts for only 2% in MMF, rest is Polyester, Viscose, and other fibers. Out of the 2% segment of Nylon weavers, 80-85% weavers uses Nylon yarn manufactured by India spinners. During 10 years of Anti DumpingDuty(2007-2017), the consumption of domestic produced Nylon yarn increased from 3000 mt/ month to 10,000 mt/month. This indicates the kind of support and cooperation among weavers, knitters, and domestic spinners. So, the allegation that if Anti Dumping Duty is imposed, weaving and Knitting industry will close and about 1 to 1.5 lac workers will be unemployed is meaningless. The prices of Nylon yarn are majorly dependent on international raw material prices as well on supply-demand. The domestic industry itself is having un-unutilized surplus capacities to the extent of 28-30% as against 18-20 imports. The argument that after implementation of Anti Dumping Duty, spinners will rig the prices of nylon yarn with ann increase of Rs 100/ kg is a blatant lie. The association has stated that power loom is being replaced to Rapier, Water jet and Air jet looms to reduce the cost of production, mainly with the help of the TUF scheme, capital & interest subsidy incentives by the state government. During the last two years, there was no Anti Dumping Duty. So, the allegation of around 1.5 lac power looms are scrapped in the last 2 years is vague to create fear in weavers. Indian made Nylon yarn is continuously being exported to Turkey, Bangladesh, Brazil, Italy, Egypt, Morocco, Algeria, Sri Lanka, etc. This itself proves that Indian made Nylon yarn is of international grade. Domestic spinning Industry is having an investment of about 3,000 crores and annually contributing approx 350 crores of GST with about 10,000 direct employment. The industry has exposure to 50,000 by way of dependent families, support services and logistic providers. If cheap imports continue, the local spinning industry has to shut down operations and the very spirit of Make in India will also Die. Price of textile chemical increased up to 17%, fabrics job charges may rise by 5-7 percent
The variety of colors and chemicals used in textile processing mills has received an increase in prices. The chemicals and dye manufacturers in south Gujarat have been importing raw material from China in bulk quantities. Manufacturing of color dye raw material has been affected after the outbreak of coronavirus in China. The prices of textile chemicals rose by 6 to 17 percent. The short supply
Advertisement
February 2020 www.textilevaluechain.com in many quality has also given the rise in chemical prices. The prices of dyes Scarlett BR has risen 17%. Along with this, Rubein BL price increased by 12%, Blue GSL 8%, and Orange RL Prices have increased by 6.5% per kg. The price of Red CF Chemical, useful for printing in the mill, has risen by 70%. Before some time, the rate of this chemical was Rs 436 per kg, which has increased to 745. The availability of many colorchemicals is low. Supply against the demand of Pink SB Chemical is limited. Similarly, the supply of Red F3BL, Red YFBL, and Yellow NGL Chemical are less. The increase in the price of the color chemical has been implemented from 14 February. There are about 350 textile dyeing and printing mills in Sachin, Palsana, Pandesara, and Kadodara. About three crore meters of fabrics are processed in dyeing and printing mills per day. The textile processors said, if the chemical supply cycle is not regularized, the chemical price may further go up in the coming time. The recent rise in dye and chemical prices has increased the production cost of textile processors in the city. The association of textile processors has called a meeting in the next few days to decide on a hike in fabrics job charges. They may increase job charges by 5-7%. SGCCI TO ORGANIZE A TEXTILE EXHIBITION IN BANGLADESH The Southern Gujarat Chamber of Commerce and Industry(SGCCI) will organize a textile exhibition from 2 to 4 April 2020 in Dhaka, Bangladesh. This event will encourage the Trade and Industry of South Gujarat and will help to promote the ‘Brand Surat’. In more than 100 stalls, various categories of textile yarn, fabrics, and machinery will be presented in this three days event. This expo will help local manufacturers, dealers and suppliers to showcase their product. This event will encourage local yarn and fabric producers to export their
goods in foreign markets. This three days event will focus on new trends and quality fabrics and textile machinery, types of equipment, technology, and accessories. Cotton-viscose fabrics production improved : Orders for modern textile machinery increased During last few months, the demand for cotton & viscose fabrics increased in textile city. The exporters have received good orders. The installation of high-speed Air-jet machines used to produce cotton-viscose fabrics has also increased. The deadly Coronavirus spread in China has affected the overall production. Many industries have shut down their operation. However, the Surat textile industry has benefited. Surat is the largest producers of polyester-synthetic fabrics in india. Local textile entrepreneurs have increased production capacity over the past decade by investing in waterjet-airjet machines to capture export quality products. Most of the polyester fabrics are sold indoors and the demand for cotton, viscose and other fabrics are more in export market. The modern airjet machine is the most flexible to meet the global demand for glaze cotton, rayon, denim. Airtel machines have been installed in Surat for the past decade. For textiles product, including cotton, glaze cotton various countries rely on China, Vietnam, Bangladesh, Cambodia and India. Because of high production cost in India, various comapnies of world, make their major purchases from China. China accounts for over 33% of the world’s textile market. India’s textile industry has benefited from China-US trade war. The domestic textile companies are able to meet the need of textiles for ready-made garments of countries of the world. Surat is rapidly emerging in this direction. According to sources, large orders are being received for companies that manufacture textiles on AirJet machines. There are more orders for Glaze Cotton, Rayon, Denim. There are around 3,000 AirJet machines installed in the city and production from these machine accounts for 20 percent. The production in China has almost stalled due to the coronavirus. India has the best supply to meet the needs of the world’s countries. Most of the Asian countries that used to order China are now giving orders to India. Orders from Malaysia, Bangladesh, Sri Lanka have been diverted to India. The future of the AirJet machine in India is bright. The industrialists of the city are eager to invest in modern machinery. The production of pure silk has declined and cotton-viscose can take place instead of pure silk. China recently vacated the $ 2.4 billion apparel market from the United States, the Export Promotion Council said in a statement. This market has been emptied after the US-China trade war. Indian companies are capable of capturing a market of $ 237 million. “It is the first time, and most probably, the last time that H&M is selling sarees because of our collaboration with an Indian designer. The idea is to surprise consumers and we will have to see what response we get and how it fits the future,” said H&M’s India CEO Janne Einola at RAI Retail Leadership Summit. Mumbai : Swedish fast-fashion retailer Hennes & Mauritz (H&M) said it will launch sarees in India by midApril as part of its partnership with designer Sabyasachi Mukherjee, the first-ever instance of any ethnic product being launched by the world’s second-largest clothing firm globally. The Stockholm-based H&M stocks fast fashion items created in-house and teams up with designers for onetime collections, but has restricted its merchandise to western wear. “It is the first time, and most probably, the last time that H&M is selling sarees because of our collaboration with an Indian designer. The idea is to surprise consumers and we will have to see what response we get and how it fits the future,” said H&M’s India CEO Janne Einola at RAI Retail Leadership Summit. Sabyasachi, who has dressed celebrities including Deepika Padukone, Nita Ambani and Oprah Winfrey among others, sells products for Rs 2 lakh and upwards on an average. However, H&M said their collection in collaboration will the designer would be completely mass-priced as an effort to democratise fashion. In India, ethnic wear is the single biggest category in women’s wear accounting for over 70% of the segment with saree controlling a third of the market with its market size of Rs 39,350 crore, according to Technopak. Last year, Japanese rival Uniqlo, had launched special collection of Kurta during its Indian entry after partnering Delhi-based designer Rina Singh. Nearly two years ago, Tataowned Titan, too, launched its saree brand Taneira. “H&M’s strategy will help increase curiosity among consumers and sarees would like a collectors item. H&M is also trying to create interest for the new collection with merchandise going beyond its conventional western wear,” Subrata Siddhanta, CEO at Texperts, a fashion specialist firm. H&M has opened a store a month in India on average so far since its entry in India in October 2015. The retailer has 47 doors and is the second-largest fast fashion brand after Zara. The retailer follows a December-November financial year, and reported sales growth of 45% to Rs 1,491 crore in 2019. With China, COME APRIL, YOU WILL GET TO WEAR A SAREE FROM H&M. NEWS