
4 minute read
Influence Of Modified Yarn Path With Mechanical Compacting System To Improve Spinning Efficiency
Influence of Modified Yarn Path with Mechanical Compacting System to im- prove Spinning Efficiency
Padmanaban.P SENIOR PARTNER
Advertisement
TEXCOMS TEXTILE SOLUTIONS
Abstract One of the Major factors contributing to Spinning efficiency is Strength of yarn and if we able to improve this parameter, the nett result will be a much better working of the ring spinning machines. The experiment stated below proves that yarn breaks during spinning is much lower when we are able to align the maximum number of fibers along the yarn axis and allow the twist flow up to the nip of the front roller. The fiber fleece is firmly bonded immediately after coming out of the front roller nip and thus the effort in reduction of spinning triangle is paying back. Introduction Yarn Strength is the foremost property of yarn which affects the efficiency of spinning, yarn finishing, weaving, fabric finishing, and wear ability of clothes. The factors affecting yarn strength include the physical and mechanical properties of fibres constituting the yarn as well as the spinning method and technology. Therefore, in the textile industry, yarn strength is the parameter most extensively studied to reduce Yarn Strength is the foremost property of yarn which affects the efficiency of spinning, yarn finishing, weaving, fabric finishing, and wear ability of clothes.
the end breaks and improve the spinning efficiency in Ring Spinning Frames. In this chapter, we will discuss about the influence of modified yarn path compare to traditional yarn path when we employ mechanical compacting system. Our study confirms that this out of the box thinking is working well with short stretch model Ring Frames like Zinser, Toyota and any Chinese models. Experiment To determine how the yarn path will effectively influence the twist flow up to the nip of front roll delivery and bind the fiber firmly to improve strength and reduce the hairiness further with mechanical compacting system like RoCos. How this reduction in hairiness will improve the Quality of a yarn further. 30s Ne 100 % Cotton Combed Hosiery was selected and a controlled study was conducted to compare. Twist direction: Z twist Experiment no.1 We have conducted the trials inZinser-321-E Ring Frame with RoCos premium mechanical compacting system and allow the yarn to run in straight yarn path (regular) and Right diagonal (cross) yarn path (fig.1)
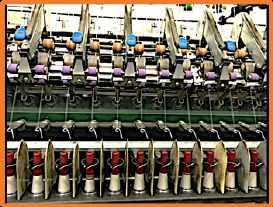
(Fig. 1) Experiment no.2 We have also conducted trials in Rieter G32 Ring Frame with RoCos premium mechanical compacting system and allow the yarn to run in straight yarn path (regular) and Right diagonal (cross) yarn path (fig.2)
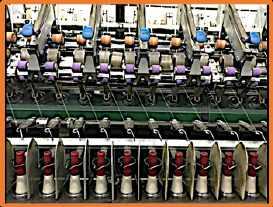
We have collected the samples from both type of Ring Frame at same stage and tested for quality parameters like U%, CVm, IPI/km, HSF/km, Single yarn strength(cN), and Tenacity (cN/Tex). Data were compared and analysed to understand the improvements. We have collected the samples from both type of Ring Frame at same stage and tested for quality parameters like U%, CVm, IPI/km, HSF/km, Single yarn strength(cN), and Tenacity (cN/Tex). Data were compared and analysed to understand the improvements. Results and Discussions A detailed comparative test results table is given below (fig. 3) In the RoCos premium mechanical compacting system the spinning triangle is reduced with the help of a guide placed in between main front top roll and a delivery top roll (20mm). However, the spinning triangle is formed on the front delivery top rubber roll (20mm)
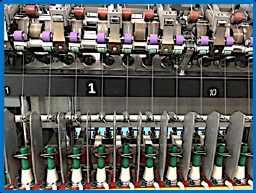
The front delivery top roll in this compacting system is placed in such a way that it is disturbing the yarn path and the untwisted fleece is not fully free to receive the twist immediately after it emerges from the front top delivery roller nip (fig. 4-(i))

The full benefit of twist flowing to the closest possible point with reduced triangle formed in this compacting system is obstructed because the spinning triangle is formed on front top rubber roll and
angle of delivery.
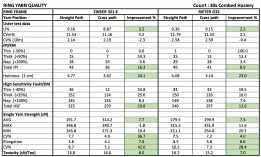
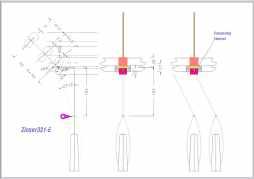
The Right diagonal (cross) yarn path as shown in Fig 4-(ii) is better in allowing the twist to flow easily closer to the nip of the front top delivery roll due to increase in free spinning length and reducing the friction between fiber and front top delivery rubber roll. (See in enlarged area of fig. 5) Once the protruding fibers are twisted together, the yarn evenness and IPI level will improve automatically along with yarn strength. The improvement in yarn quality
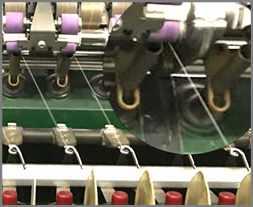
will reduce the ends down and allow spinners to run the Ring Frame more efficiently. Benefits • Production and Productivity improvements up to 15% • Pneumafil waste reduction from 2.5 to 1.75% • Machine cleaning and housekeeping improvements. • Manpower improvements. • Yarn waste reduction in Autoconer due to a smaller number of clearer cuts • Autoconer efficiency improvements. Conclusion With the Right diagonal (cross) yarn path arrangement, there is an increased concentration of fibers in the right-hand side of spinning triangle due to the increased pretwisting of fibers. As a result, the pre-twisting effectively binds the fibers into the bulk of the yarn structure, thus reducing yarn hairiness. Right diagonal yarn path is effective in reducing hairiness for a Z-twist yarn while Left diagonal deteriorates hairiness results. Yarn quality improvements and performance of the machine will enhance the performance of the operations and reduce the cost of manufacturing.