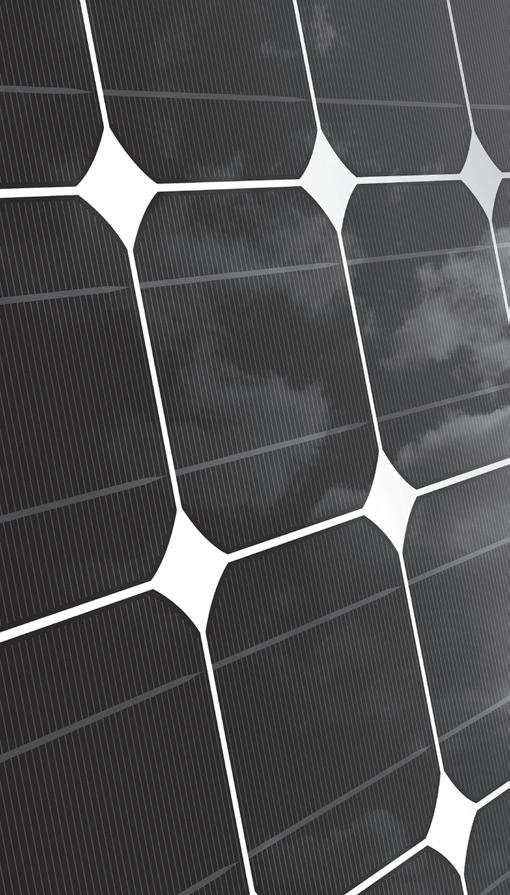
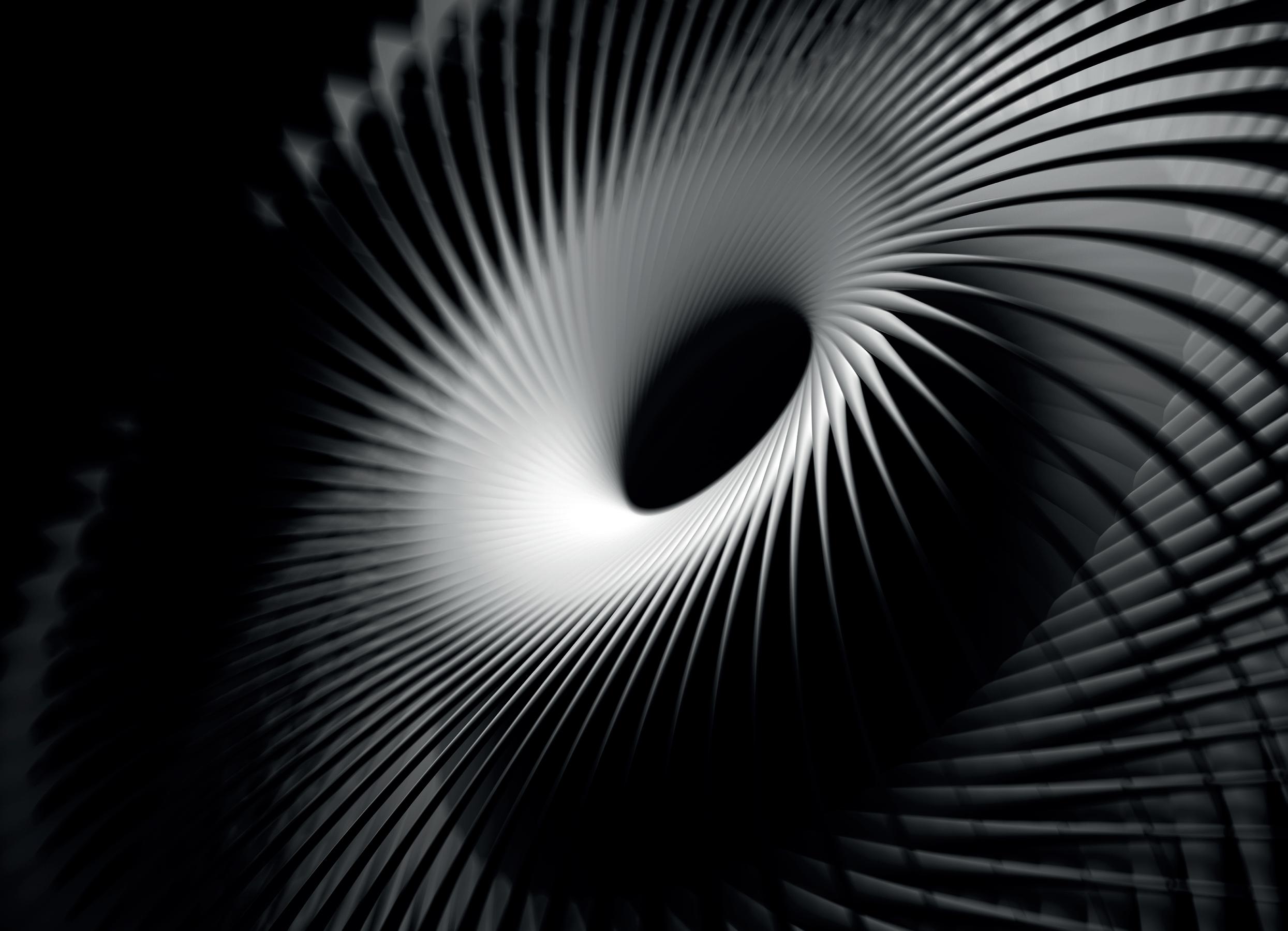
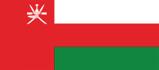
On 16 August, President Joe Biden signed the Inflation Reduction Act of 2022 (IRA), a new bill which will drive the largest expenditure in combating climate change in US history. It foresees investments in climate protection, tax credits for households to offset energy costs, investment in clean energy production, and tax credits aimed at reducing carbon emissions.
Energy-wise, it creates a new 10-year incentive for clean hydrogen production – a tax credit that would pay clean hydrogen producers up to US$3 per kg. The size of the tax credits available depends on the lifecycle greenhouse gas (GHG) emissions of each project. The basic tax credit rate for ‘qualified clean hydrogen’ is set at US$0.60/kg, with a sliding scale depending on lifecycle emissions – measured in carbon dioxide-equivalent (CO2e) – of the H2 produced. Hydrogen manufactured with less than 0.45kg of lifecycle CO2e emissions per kg of H2 would receive 100% of the credit, followed by 33.4% for 0.45-1.5kgCO2e/kgH2, 25% for 1.5-2.5kg and 20% for 2.5-4kg.
Additionally, it extends the Investment Tax Credit (a federal income tax credit for certain types of renewable and clean energy projects) for wind and solar (up to 30%) for the next ten years. The 30% applies to both business and residential projects, including projects installed in 2022, and will last until the end of 2032.
Furthermore, energy storage projects were previously ineligible for tax credits unless they were connected directly to solar power projects. The IRA removes these requirements and allows energy storage projects to receive the same 30% tax credit for the first time, even if they are stand-alone facilities.
Solar power projects eligible for the full 30% tax credit can increase their tax credit by an additional 10% – to 40% in total – by purchasing domestically produced hardware. According to the bill, 100% of steel and iron must be domestically manufactured in the US. For manufactured goods – like solar panels, inverters and electrical gear –the goods must initially be 40% US manufactured, though this percentage will increase in the future.
The IRA also aims to boost the US clean energy supply chain by incentivising the domestic production of clean energy technologies and by offering tax incentives for US companies to manufacture products like carbon capture technology and offshore wind components. Over the next ten years, the IRA will provide at least US$370bn in funding and subsidies for clean energy production and addressing climate risk. Overall, the IRA is expected to create up to 550,000 new jobs in clean energy industries; more than doubling the current clean energy workforce.
Designed and published by Energy Industries Council 89 Albert Embankment, London SE1 7TP Email info@the-eic.com
However, not everyone supports these new incentives and tax credits. Concerns have been raised by the EU and Asian countries such as Japan and South Korea, that the recent subsidy plans represent market-distorting measures that aim to convince companies to shift their production to the US. It is fair to say that the IRA attempts to reshape multiple clean energy industries in ways that will benefit America’s trade balance, as some of its subsidies, such as its aggressive solar manufacturing and hydrogen incentives, are available only to US firms that produce their goods domestically.
To address this matter, on 26 October 2022, the European Commission launched an official task force to discuss the implications of the new bill, stating that it ‘will address specific concerns raised by the EU related to the IRA’ and, a day later, the German Finance Minister, Christian Lindner, restated the considerations in a press conference. In theory, the IRA will promote new supply chains in clean energy sectors in North America and also countries that have a free-trade agreement with the US. However, under the World Trade Organization (WTO) rules, a subsidy granted by a WTO member country is prohibited if it is contingent, in law or in fact, on export performance or the use of domestic over imported goods.
The US currently has free-trade agreements with Australia, Canada and Mexico, for instance, but not with Japan, Germany or the United Kingdom, which makes these countries more susceptible to the effects of the new bill and will force them to negotiate with the US to see how they can soften the impact to their supply chains. Moreover, it should be mentioned that building barriers through subsidies will not only cause disruption to the global energy industry and supply chains of clean energy sectors, but will also trigger a domino effect by generating major shocks to the global economy. Depending on the outcome, European and Asian countries may look to roll out their own countermeasures.
This means that the IRA has the potential to trigger a trade war between the US and its trade partners, with protectionist trade measures being issued by other countries if their concerns are not addressed.
Despite its target being Chinese manufacturing, the new legislation indicates the US’s increasingly protectionist mood; which will have an unplanned negative impact on global free trade and supply chains. In this sense, the IRA may be dragging the global economy and trade into an unintended crisis. In these difficult times, this shows the importance of working with your allies to find common solutions, not against them.
Gustavo Berlie, Energy Consultant gustavo.berlie@the-eic.comThe January issue of Inside Energy opens a special year for the EIC: next month, the EIC will be 80 years old. To celebrate, every month from February onwards, Inside Energy will host a dedicated section to our oak jubilee where you will be able to discover more about us and our history of continued success, as well as read testimonials from our collaborators and stakeholders. Before that, see page 27 of this edition, where we’ve displayed our strategic objectives and core values.
The first sector analysis of 2023 has been produced by Gustavo Berlie, EIC energy consultant from the Rio office. In his article, Gustavo explores Joe Biden’s recently signed Inflation Reduction Act (IRA) and its impact on the energy supply chain worldwide.
Sandvik Materials Technology’s rebrand to Alleima is the focus of the members’ services section. The company, a manufacturer of steel products founded in 1862, is based in Sandviken, Sweden, and has a staff of over 5,500 serving customers from 90 different countries.
In spotlight on technology, readers can get to know ABB’s OPTIMAX, an energy management system specially designed for green hydrogen facilities. The software supports every aspect of a hydrogen plant’s lifecycle, from design and engineering to operation.
Stephan Ciniselli and Mauricio Pereira, global director for offshore wind and head of renewable energy respectively at Bureau Veritas, have been interviewed by our team for the one-to-one feature. Our conversation focuses on Bureau Veritas’ new offshore wind services in Brazil, the sector’s prospects worldwide, and more.
David Clark, CEO of the Vysus Group, has contributed this month’s EIC guest editorial. David’s piece delves into the challenges the international market currently faces when it comes to keeping the energy trilemma stable.
The EIC is looking forward to 2023, a year that we’re certain will be special, providing our network of readers with the usual office updates and regional market reports from the teams based in Europe, the Americas, Asia Pacific and the MENA region. Projects and business news from our associates worldwide are also included.
Léliam de Castro, Head of Marketing and Communications leliam.castro@the-eic.com
Operator: Nuclear Power Plants Authority Value: US$30bn
Doosan Enerbility has stated that it was awarded the construction of turbine islands on 10 November 2022 worth US$1.2bn. Eni is considering two development options to advance the project.
Operator: ExxonMobil Value: US$6bn Modec has been awarded the FEED contract for the Uaru FPSO. The contract is expected to lead to an EPCI award once the project is approved by the government and secured a final investment decision (FID).
Operator: Gen2 Energy Value: US$250m
Gen2 Energy is looking to develop a 100MW green hydrogen facility. The plant will produce 45 tonnes of green hydrogen per day in its first phase. Wood has been contracted to deliver the FEED studies for the plant.
For more information on these and the 12,000 other current and future projects we are tracking please visit EICDataStream
Operator: Saudi Aramco Value: US$4.5bn
Saudi Aramco and Saudi Arabia’s Ministry of Energy have signed a MoU to develop the world’s largest CCS hub in Jubail Industrial City. The project is expected to come online by 2027 and its first phase will be able to store and utilise 9mtpa of CO2
Operator: Northland Power Inc Value: US$2bn CSBC-DEME Wind Engineering (CDWE) has secured a contract worth US$300m that involves the transportation and installation of foundations, turbines and offshore substations. Pre-piling work is scheduled to commence in 2024 followed by installation of 73 turbines.
Operator: Ocean Winds Value: US$750m
Crowley has agreed to be a developer and operator of a terminal at the Port of Humboldt Bay that would be California’s first offshore wind installations hub. The Humboldt Bay Offshore Wind Heavy Lift Marine Terminal will be leased and support future tenants for operation activities.
The latest release has mapped 19,000 producing assets across 47 countries in the region. Fully interactive – search for energy facilities by location, sector and operator. Find out who you need to do business with at each facility.
Countries include: Antigua and Barbuda, Argentina, Aruba, Bahamas, Barbados, Belize, Bolivia, Brazil, Canada, Cayman Islands, Chile, Colombia, Costa Rica, Cuba, Curacao, Dominican Republic, Ecuador, El Salvador, Falkland Islands, French Guiana, Greenland, Grenada, Guadeloupe, Guatemala, Guyana, Haiti, Honduras, Jamaica, Martinique, Mexico, Nicaragua, Panama, Paraguay, Peru, Puerto Rico, Saint Lucia, St Kitts & Nevis, St Martin (Fr), St Martin (Ned), Suriname, Trinidad & Tobago, Turks & Caicos, Uruguay, USA, Venezuela, Virgin Islands (UK), Virgin Islands (US).
Alleima is a leading manufacturer of high value-added products in advanced stainless steels and special alloys as well as products for industrial heating. Its origins date back to 1862 and the foundation of the company Sandvikens Jernverk by Göran Fredrik Göransson, a pioneer in using the Bessemer method for steel production on an industrial scale.
Based on long-term customer partnerships, Alleima advances processes and applications in the most demanding industries through unique materials that are lightweight, durable, corrosion-resistant and able to withstand extremely high temperatures and pressures.
With more than 900 active alloy recipes, Alleima’s offering comprises products for several segments, mainly seamless tubes for the energy, chemical and aerospace industry, precision strip steel for white goods compressors, and air conditioners.
Sustainability is present in all aspects of its operations and is an integral part of its commercial strategy. Alleima’s product offering enables the transition to renewable energy sources, electrification of industries, innovation in the medical sector and much more.
Alleima’s fully integrated value chain, from R&D to endproduct, ensures industry-leading technology, quality, sustainability and circularity.
Alleima, with headquarters in Sandviken, Sweden, and revenues of SEK13.8bn (€1.26bn) in 2021, has more than 5,500 employees and customers in 90 countries. Local UK office: Alleima Limited Tel +44 (0)1782 228 940 Email sales.uk@alleima.com Web www.alleima.com
Email newsdesk@the-eic.com Phone +44 (0)20 7091 8600
Green hydrogen made via electrolysis – a process of using electricity from renewable sources to split water into hydrogen and oxygen – is widely considered an important energy vector for achieving a low carbon future. It does, however, pose significant challenges in the way of high production costs and energy intensive processes.
According to the Green Hydrogen Catapult, a global initiative made up of leading energy companies, to scale up production capacity to the 50 times needed, the cost to produce green hydrogen needs to drop by 50% to less than US$2/kg by 2026.
ABB’s OPTIMAX® supports this by serving every aspect of a hydrogen plant lifecycle, from simulation at design and engineering phases to real-time visualisation and monitoring when in operation.
The software measures bi-directional power flows and carbon dioxide emissions providing contextual data which operators can use to determine optimal energy consumption levels required to support plant processes and minimise waste.
The transparency offered by the solution can also be applied to increase the efficiency and safety of each electrolyser module being operated within the plant, regulating each module’s speed, and ensuring it is only used as and when required.
Incorporating intra-day planning, operators can also utilise OPTIMAX® to plan ahead to trade competitively with the grid, developing a circular energy system that is based on forecasts of renewable energy availability against demand, also considering market electricity prices.
Get in touch Any EIC members who wish to be profiled in this section please contact Léliam de Castro... Email leliam.castro@the-eic.com
Bureau Veritas talks about new offshore wind services in Brazil, the sector’s prospects worldwide, and more.
https://marine-offshore.bureauveritas.com/
As a world leader in audit and certification services, Bureau Veritas supports its 400,000 clients to be more efficient, more methodical and more trustworthy in their journey towards more sustainable business and a more sustainable world. The Group is a key player in the energy transition, present at key stages of the renewable energy production chain.
In offshore wind specifically, Bureau Veritas helps developers by mitigating the risk of their projects, therefore increasing the value of offshore wind assets. This has a secondary effect in the offshore industry as a whole; better projects increase the confidence of investors, which then makes the offshore market more resilient. Examples of services that Bureau Veritas offers include and are not limited to project development services, owners engineering, technical due diligence, asset management and project certification.
Bureau Veritas recently announced a one-stop shop service to Brazilian developers in the offshore wind sector. What does it entail?
The licensing process in Brazil is complex and requires that several public bodies (10+) are involved in the application of DIPs (declarations of prior interference, in Portuguese). Bureau Veritas reduces the burden on developers by compiling all information needed in a one-stop shop called Balcão Único. Leveraging Bureau Veritas’ previous experience in licensing, Balcão Único works as the developer’s representative to make sure all information is provided to the authorities at each step of the process.
What are the common challenges faced by offshore wind developers across the globe when it comes to a project’s permitting process?
Each market has its own particularities. While in western Europe and the US the challenge is on speeding up the permitting process so that renewable energy targets can be achieved, in offshore wind developing markets the main challenges would be on ensuring that clear guidelines are provided to stakeholders so that confidence on the local regulation is increased.
The offshore wind market has seen a rapidly increasing project pipeline across the globe. Meeting supply chain challenges is a key topic, however. What is your view?
When we talk about supply chain the initial thought is usually on component manufacturers. China, western Europe and the US are amongst the regions where most offshore wind components are currently being manufactured. Considering the number of existing offshore wind projects in the pipeline, there is an immediate need for local supply chains to be created and strengthened, otherwise projects will end up in tough competition for the same global suppliers. This increases the risk of having less than ideal quality components being installed in wind turbines or of delaying project operation.
Additional supply chain challenges that also need to be considered are related to cyber security, logistic constraints (eg undersupply of vessels and turbines getting bigger), training to overcome the lack of talents, amongst others.
Bureau Veritas can help the industry by making sure that projects access a reliable supply chain through our pool of inspectors and engineers.
Oil and gas and offshore wind present supply chain synergies. What advice would you give to companies diversifying from oil and gas to clean energy?
To partner up with an expert and to cross-train your technical workforce. Offshore wind is a fairly new industry, which everyone is trying to get to at the same time. This created a race to the bottom in terms of levelised cost of energy, which means the level of competitiveness for each project is extremely high. Partnering up with an offshore wind expert and cross training highly skilled engineers would give oil and gas players a competitive advantage as they can combine and leverage decades of offshore experience from their staff with specific wind power knowledge from partners.
Which offshore wind markets will offer the largest opportunities for Bureau Veritas in the coming years?
BV is a global company with 19 technical centres across the globe and over 400 professionals dedicated to offshore wind spread across the Americas, Europe and Asia. Historically, BV has been strongly involved in Europe, China and the US, however we are now seeing strong momentum emerging in Latin America with Brazil and Colombia, in Eastern Europe with Poland and the Baltics, and in Asia with Vietnam, Korea, Taiwan, Philippines and Australia. With a presence in 140 countries, Bureau Veritas will be able to support the industry wherever the project is located.
Get in touch Share your news and views...
Email newsdesk@the-eic.com Phone +44 (0)20 7091 8600
How is Bureau Veritas helping offshore wind developers across the globe?
Via Expressa Francisco Cleuton Lopes, 3850, Água Branca District Contagem, Minas Gerais State 32.370-485, Brazil
Contact André Dias da Mota, Business Manager andre.mota@actemium.com
Gustavo Caldeira Pyramo Rala, Business Manager gustavo.rala@actemium.com
Telephone +55 31 3399 6693 +55 31 3399 6765
Web www.actemium.com.br
Actemium is a VINCI Energies brand dedicated to industry. Focusing on a continuous optimisation of industrial performance, Actemium accompanies customers smoothly into the new industrial era.
The network, comprising of more than 400 agile and self-learning business units specialised by market segment, enables a customised approach, presenting multi-technical, multi-site and multi-country solutions.
Operating throughout the entire industrial life cycle: consultancy, engineering, procurement, construction, commissioning and maintenance, Actemium innovates in order to support the longterm development of industrial customers, in a sustainable way.
AIMS Oil and Gas Equipment Trading –Sole Proprietorship LLC
Plot 23-WR 43 ICAD III Musaffah Abu Dhabi, UAE
Contact
Zaheer Ahmed Juddy, CEO and Founder
Telephone +9712 643 6114 Email info@aimsgt.com Web https://aimsgt.com/
Analytical Instrumentation Maintenance Systems (AIMS) is a service-based company with likeminded professionals working in the Middle East with offices located around the Middle Eastern countries, providing service and process solutions to the entire market.
AIMS is an ISO 9001:2015, ISO 14001:2015 and ISO 45001:2018 certified company that specialises in providing innovative solutions in process technologies throughout refinery gas processing trains, the petrochemical industry for online analysers, process solutions, technical services, maintenance contracts and customised engineering solutions. The company is recognised for providing one-stop solutions for gas processing trains specialised in sulphur recovery units and refinery units.
The process division delivers outstanding toll production and mixing capabilities which benefits both customers and suppliers. With a designated manufacturing site in Abu Dhabi, the company helps clients to lower their costs and save time by formulating, blending and packing finished products and chemical intermediates providing a confidential toll manufacturing service to the specifications of AIM’s clients.
Get in touch Share your news and views...
Email newsdesk@the-eic.com Phone +44 (0)20 7091 8600
NEW PRIMARY MEMBER
ENTACT,
101 Old Underwood Road, Bldg J La Porte Texas 77571
US
Contact Daniel Woodward, National Account Manager dwoodward@entact.com
Bob Emerson, Account Executive remerson@entact.com
Telephone +1 281 996 9892
Web www.entact.com
ENTACT is a national provider of environmental and geotechnical construction solutions. Founded over 30 years ago on the belief that safety, technical excellence, field expertise and sound business practices are all necessary to deliver outstanding service, ENTACT is recognised today as a premier provider of remedial construction services.
The company’s talented teams implement field remediation and geotechnical solutions for a range of private industry clients at their most challenging projects, including active facilities, multiparty sites, and developmentdriven work. ENTACT is one of the largest providers of remedial contracting services to private industry in the US.
ENTACT directly self-performs field construction work, which enables it to offer efficient, accurate and timely solutions. It possesses inhouse expert personnel and stateof-the-art equipment. ENTACT’s projects often integrate several scope components and various media, including soil, sediment and groundwater.
www.the-eic.com
If so, why not refer that company to us?
If they join, you will receive four Global Digital Support packages as a thank you for your efforts. Worth over £1,000, these packages can be used alongside either online or live events and are a great way to raise the profile of your company. They include:
• Your logo with link to your landing page on the event webpage
• Your logo on screens at the event
• You will be mentioned in some of the marketing for the event
Amarinth, a world-leading, net-zero designer and manufacturer of low lifecycle cost centrifugal pumps and associated equipment, primarily for the offshore and onshore oil and gas industries; nuclear and renewable energy generation; defence; desalination; process and industrial markets, has secured an order from Yinson Production of two large API 610 OH2 pumps for use aboard the FPSO Atlanta, which has been commissioned by Enauta.
The Brazilian oil and gas company Enauta recently concluded the purchase of an FPSO for the definitive system of its operated Atlanta field located off Brazil. The FPSO, which will be capable of operating in ultra-deepwater depths of 1,500m, is being adapted by Malaysia’s Yinson Production from the existing FPSO OSX-2 through a turnkey engineering, procurement, construction and installation contract.
The project will be completed in Dubai Drydocks World and includes structural upgrades, refurbishment and enhancement of equipment. The FPSO Atlanta is scheduled to start operating in 2024 with a production capacity of 50,000 barrels/day.
Yinson has successfully used Amarinth pumps on previous FPSO builds and so was confident that Amarinth could design and manufacture the two API 610 OH2 pumps with Plan 53B seal support systems on the very aggressive 36week delivery that is required to fit with the build schedule of the FPSO.
The large crude oil transfer duplex pumps will have 570mm diameter impellers and be equipped with variable frequency drives to improve energy efficiency. All electrical items will be IECEx certified for operating in ATEX Zone 1. The pumps will also be America Bureau of Shipping witnessed and certified in line with the FPSO being operated under ABS Class.
i
For more information: www.amarinth.com
International subsea equipment rental and solutions specialist Ashtead Technology has appointed a new leader for its mechanical solutions service line to accelerate the delivery of its global growth strategy.
James Christie, who is regional director for Ashtead Technology’s Asia Pacific region, also assumes the role of head of mechanical solutions as the company looks to cement its market position as a leader in IMR and decommissioning services for the global offshore energy sector.
In his expanded role, Mr Christie will continue to be based in Singapore and will work with Ashtead Technology’s regional teams to grow the company’s capabilities and drive forward the international expansion of its mechanical solutions service line which specialises in subsea cutting, dredging, coating removal technologies and ROV tooling and associated services.
i
For more information: www.ashtead-technology.com
The Transport Intelligence Global Freight Forwarding 2022 report shows that in 2021 the global forwarding market rebounded to exceed its pre-pandemic levels. According to the findings, the global freight forwarding market grew by 11.2% in 2021 and is forecast to grow by 5.7% in 2022. Market players must take decisive action to ensure that the sector continues to grow in line the EU’s binding targets to achieve climate neutrality by 2050 and the British government’s net zero strategy.
Dmitri Krolov, Sustainable Development Manager at AsstrAAssociated Traffic AG, said: “For companies like AsstrA, at this point such initiatives are not only about environment but also economy. The recent increase in energy costs, shortages of raw materials, and desire to diversify away from Russian gas have driven more interest in environmental solutions in the design of warehouses and logistics processes.
“Greater trade volumes will be supported and business will grow as such solutions are applied over time. Process optimisation will help transport and logistics companies manage demand and efficiently adapt to the rapid changes and development. That is why we have launched our ESG strategy (environmental, social and corporate governance) to guide the framework for sustainable development at AsstrA.”
Anna Smirnova, Head of AsstrA Industrial Project Logistics in the UK, added: “The company tracks its CO2 emissions and has plans to minimise its negative impact on the environment. We aim to reduce our CO2 footprint 25% by 2025 and 50% by 2030.”
i
For more information: https://asstra.com/
Only 30 minutes from the centre of Oslo a new real estate area called Langenga, is taking shape in Asker. The area is currently transforming from a muddy construction site into a green, child-friendly suburban oasis.
The only downside is that the bedrock is very hard – requiring significant drilling to establish foundations. The solution was to call in Brødrene Myhre – a drilling contractor established in 1976 and who today is one of Norway’s largest, employing some 30 drilling experts.
We are investigating new ways of supporting and charging the electric compressors –the energy storage system ZenergiZe from Atlas Copco is one interesting option.
Håkon Myhre, CEO, Brødrene Myhre
When the company was appointed as the drilling subcontractor for the Langenga real estate project, it opted for a powerful electric compressor from Atlas Copco. Atlas Copco has long been one of the company’s suppliers and for this project the largest E-Air compressor – the V1100 – was considered best suited, both in terms of air flow but also in terms of minimal noise output.
Brødrene Myhre’s CEO, Håkon Myhre, paid close attention when he heard about the VSD (variable speed drive) functionality of Atlas Copco’s E-Air V1100 compressor. Adding the E-Air V1100 to the fleet opens new opportunities for all types of construction projects, especially in a country with some of the strictest environmental regulations in the world.
i
For more information: www.atlascopco.com
Aberdeenshire-based Blaze Manufacturing Solutions has announced major contract breakthroughs and new jobs since introducing a redefined global business strategy.
Following a major investment boost from fellow EIC members Balmoral Group in 2019 the company has secured work from the nuclear, renewables and industrial sectors as well as maintaining its presence in the traditional oil and gas field. The new work has led to the creation of 12 full time jobs with more expected to follow.
A leading provider of fire safety products and services the company’s strategy has a renewed focus on delivering greater added value while providing solutions to detect, prevent and protect high-risk assets from fire incidents.
The company says it has secured deals into the next decade ranging from multi-million pound projects in the nuclear sector to international turnkey projects in the renewables market, while supporting historic oil and gas clients with asset life extensions and downstream work.
To support recent developments the company has appointed Stuart White as operations director and refreshed its brand identity to reflect and enhance its market diversification capabilities.
Mr White, a qualified CA, comes to Blaze following a successful career in the financial services sector as well as time spent in energy logistics and construction engineering.
A new website that highlights Blaze’s capabilities, expertise and industryleading knowledge has been created and can be viewed on the URL below.
i
For more information: www.blazeman.co.uk
Hitachi Energy has delivered its grid connection solution for Qatar’s Al Kharsaah solar photovoltaic (PV) power plant – one of the world’s largest and the country’s first utility-scale solar PV park, 80km west of Doha.
Al Kharsaah has a generating capacity of around 800MW and will help Qatar progress towards its goal of reducing greenhouse gas emissions by 25% by 2030.
Leveraging its strong regional footprint and expertise in project design and execution, Hitachi Energy has provided an engineered package that collects all the power generated by the plant’s 1.8m solar modules and transfers it into the national transmission system safely and reliably.
Our expertise and long track record of supplying grid integration solutions in Qatar and the Middle East make us a partner of choice for large-scale renewable energy projects.
Niklas Persson, Managing Director, Hitachi Energy’s Grid Integration businessHitachi Energy is a market and technology leader in grid connections and power quality solutions, with more than 10,000 installations worldwide. Recently, the company launched its GrideXpand™ range of modular and prefabricated grid connection solutions that make it faster, simpler and more efficient to expand power grid capacity and accelerate the transition to a more sustainable energy system.
Leading global provider of mission critical air and gas handling products, technologies and services, Howden, has secured a contract with INOVYN – a subsidiary of INEOS. Howden will supply a lowpressure piston compressor as well as a high-pressure diaphragm compressor for INOVYN’s hydrogen production facility in Runcorn, UK.
As a global leader in hydrogen compression solutions, Howden was selected for its extensive experience and innovative technology. Delivering an efficient design-tocost approach, Howden customised its solution to fit INOVYN’s needs while also reducing the total cost of ownership of its operations.
Already Europe’s largest operator of electrolysis technology used to make clean hydrogen, INOVYN’s Runcorn site can power over 1,000 buses or 2,000 trucks with low-carbon fuel. Harnessing Howden’s state-of-theart compressor technology, INOVYN can now supply compressed fuelcell quality hydrogen to the transport and industrial sectors.
With Howden’s support, INOVYN is able to tap into the emerging hydrogen fuel-cell market in the UK and boost its revenue from coproduced hydrogen, realising the business’ mission to lead the UK to net-zero carbon emissions.
Developing highly innovative solutions for its customers, Howden optimises the availability, reliability and installation footprint to reduce the total cost of ownership of customers’ operations.
Howden is partnering with its customers to provide equipment and technology that enable emission reductions and greater sustainability.
i For more information: www.howdenprocesscompressors.com
Johnson Matthey (JM), a global leader in sustainable technologies, has begun fuel cell recycling in China. Located in Zhangjiagang, Jiangsu Province, the plant is refining and recycling the platinum group metal content from membrane electrode assemblies (MEA), a key component of an automotive fuel cell, from Unilia, one of the world’s leading providers of fuel cell stack technology.
While the volume of materials for refining will be small to begin with, JM has sufficient capacity and ability to scale up its facilities to meet demand over the coming years.
China is the biggest PGM market in terms of demand but with very limited natural resource, so recycled precious metals will be critical to meeting this challenge. On average, around 80% of the platinum group metals used by JM are sourced internally, creating a resilient supply of metal for JM as a leading global player in the automotive catalyst and fuel cell sectors.
Secondary supply of PGMs is expected to grow globally at roughly 3-5% per annum. Recycled metals cost less and have a much lower carbon footprint (up to 98% lower) than primary supply PGMs. They also provide security of supply of these scarce resources, which becomes ever more critical with global supply chain disruption.
Johnson Matthey is a global leader in sustainable technologies that enables a cleaner and healthier world. With over 200 years of sustained commitment to innovation and technological breakthroughs, it improves the performance, function and safety of its customers’ products. JM’s science has a global impact in areas such as low emission transport, energy, chemical processing and making the most efficient use of the planet’s natural resources. Today about 15,000 Johnson Matthey professionals collaborate with its network of customers and partners to make a real difference to the world around us.
i
For more information: www.matthey.com
Kent, a leading engineering company in oil and gas and hydrogen (H2) technologies, has been appointed as the FEED contractor for aspects of hydrogen supply and resilience for Cadent’s UK Hydrogen Village project. Kent has been involved in over 50 hydrogen projects worldwide and is an engineering partner at HyNet (North West England).
Progressive Energy Limited (PEL) has appointed Kent to develop a front-end engineering design (FEED) to deliver hydrogen at the correct specification and availability for Cadent’s proposed Hydrogen Village project.
The primary purpose of the Hydrogen Village project is to demonstrate how to facilitate the decarbonisation of home and commercial heating by replacing domestic natural gas supply with hydrogen using existing local gas pipes.
This win is a testament to the fantastic work we have been doing on hydrogen projects in the UK. We look forward to continuing our working relationship with PEL.
Matt Wills, Market Director, Low Carbon, and Onshore Projects,Kent
Hydrogen demonstration projects, such as the proposed programme in Whitby, Ellesmere Port, are part of the plan to reduce CO2 emissions to reach the UK’s 2050 net zero targets. Kent’s scope of work will include:
• Develop the FEED design for a hydrogen supply compound, which will handle hydrogen before it is injected into a pipeline to supply Whitby Village in Ellesmere Port.
• Provide sufficient hydrogen buffer storage to meet intraday design peak and comply with all safety regulations.
• Develop FEED design for supporting infrastructure and utilities, ensuring the required resilience of the hydrogen supply to Whitby.
i
For more information: https://kentplc.com/
Kongsberg Digital and Keystone have combined their software expertise to form an industry-first technology partnership, enabling real time wells and planning data to be combined and contextualised to power more valuable workflows leading to optimised drilling operations.
Kongsberg Digital’s partnership with Keystone will enable customers to develop more effective planning, execution and learnings in well operations. Together we will make data and insights easily available in real time for end users to use to make better decisions.
Shane McArdle, CEO, Kongsberg DigitalBusinesses across the NRL Group have joined together to sign the Social Mobility Pledge. The initiative asks organisations to make a commitment to support children and young adults from disadvantaged backgrounds, using their skills and expertise to help even the playing field and encourage them to think about their future.
Organisations who sign up to the pledge undertake social impact activity in three key areas – outreach, access and recruitment. Working with local initiatives to reach young adults, offering work experience and apprenticeship opportunities and adopting open recruitment processes that welcome people from all walks of life.
Having already supported a wide range of community initiatives in recent years, and with a strong commitment to continue to build on this important focus area, it was a natural choice for the NRL Group to sign the Social Mobility Pledge.
Specialist energy talent acquisition group Petroplan has strengthened its liquefied natural gas (LNG) service offering across North America. Petroplan is exploring a number of opportunities to support LNG development projects and operational facilities, concentrating on operations in the US Gulf Coast, Western Canada and the Mexico Pacific Coast.
The service is being driven by David Waterfield, managing director for North America, supported by newly appointed senior client development manager, Adrian Kraeger.
With almost 30 years combined experience working on LNG projects in North America, David and Adrian are experts in the field and bring unique insight into the future challenges and demands for LNG operators.
By combining both companies’ well application portfolios, Kongsberg Digital and Keystone’s partnership represents an important step change in industry standards. Well data is combined and contextualised to provide well plans using Keystone’s SmartHUB. Utilising its Industrial Work Surface, Kongsberg Digital provides a detailed picture of the real time well operation through an interoperable platform.
This increased accuracy and consistency of available data in a single open platform helps teams to leverage real-time data, the latest and most consistent information, and embedded analytics tools for well operations.
i For more information: www.kongsberg.com/digital/
NRL Group’s experts make a positive impact in society by supporting some of the most innovative global companies, the people who power them and the major Infrastructure projects they deliver.
From humble beginnings in 1983 providing NDT services at the Sellafield nuclear site, today’s diverse international Group provides a range of resourcing, outsourcing, non-destructive testing, rail contracting and consultancy services.
NRL Group helps clients to meet their future growth plans and deliver their projects with 100% compliance, knowing that this approach provides a wealth of opportunity for its candidates.
i
For more information: www.nrl.co.uk
Petroplan offers consultative services to support clients’ resourcing strategy across all areas including organisational design, compensation, staffing and hiring strategies, immigration solutions, as well as recruitment itself. As LNG access, consumption and production continues to significantly increase and there is an unprecedented demand for staff on these projects, Petroplan’s expertise provides a vital solution to clients wishing to ensure success of their LNG projects.
The Petroplan Group is a specialist global talent acquisition, mobility and workforce solutions business, servicing employers and professionals in the energy and infrastructure industries. Petroplan covers talent sourcing and talent acquisition (contract and permanent hire), global mobility solutions, payrolling and managed solutions.
i For more information: www.petroplan.com
Sherwin-Williams Protective & Marine Coatings has expanded its awardwinning intumescent passive fire protection range for structural steel with the launch of FIRETEX® FX6010.
Now available across the UK and Europe, the new intumescent coating enhances the FIRETEX FX6000 range to allow for greater versatility in application, with FX6010
able to be applied by standard single-leg spray equipment, helping applicators to embrace the FIRETEX range with existing equipment.
To enable use of a more standard application method, FX6010 also offers extended pot life and working time, offering greater flexibility in use, while still maintaining durability and quick curing qualities in as little as three hours.
Once applied in shop or on site, FX6010 can be exposed to weather after four hours, while its mechanically toughened qualities ensure reduced damage during installation.
FX6010 also offers up to 120 minutes fire protection and can be exposed to C5 high corrosive environments with correct primers and topcoats.
The qualities of FX6010 make it ideal for infrastructure projects such as sports arenas, schools, hospitals, transport hubs and office blocks.
The new coating system complements the Sherwin-Williams range of FIRETEX® intumescent coatings.
i
For more information: www.leighspaints.co.uk
With the European energy crisis and ongoing conflict in Ukraine, there is an unprecedented dependency on the global LNG market. To support the increasing demand for LNG, we will continue to strengthen our ability to support clients to resource their operations around the world, and particularly in North America.
Christopher Honeyman Brown, CEO, Petroplan
Thunder Cranes has launched operations in the Middle East and Africa. The offshore crane company had previously operated with a base in Dubai from 2009 to 2019 – now reopened – and in addition has just launched a new base of operations in Luanda to serve Angola and western Africa.
Since 1995, Thunder Cranes has been supplying its proprietary brand of API-compliant, portablemodular cranes which were developed in the US. Today, Thunder Cranes is headquartered in Malaysia and operates globally, with bases in the UAE, Thailand, Malaysia, Brunei and Angola.
Many of the older platforms are not equipped with sufficient crane capacity or coverage to support current projects, thus the need for temporary cranes that can be installed when required. Safe, efficient and cost-effective, the portable-modular crane has become essential equipment used to facilitate a diverse range of offshore projects in well intervention, P&A, construction, crane changeouts and decommissioning.
In line with its vision to become a global leader in offshore lifting solutions, Thunder Cranes has focused on customer satisfaction through reliable, safe performance – a strategy that has resulted in consistently winning long-term service contracts with oil and gas companies in Malaysia, Thailand, Brunei and Dubai, as well as securing projects in China, Vietnam, Indonesia and Angola.
In 2022 Thunder Cranes was awarded another long-term contract with an oil major in Thailand.
For more information: www.thundercranes.com
Specialist drilling waste management company, TWMA, has launched its new XLink™ solution, designed to provide oil and gas operators with increased automation, deeper insights and real time data monitoring to improve the efficiency of their wellsite drill cuttings processing system.
XLink is a new hardware and software system upgrade that provides both POB reduction through offshore automation and allows customers to monitor their drilling waste operations live from anywhere in the world.
The system links drill cuttings volume monitoring, and material conditioning, all combined through a data platform that delivers real time monitoring capability.
Following successful roll outs in the UK and Norway, the cloud-based system, which can be integrated into any existing TWMA asset operating offshore or on land, is increasingly becoming a core component of TWMA’s global solution offering.
The XLink system allows for full control of the drilling waste management handling process from one central control point on the rig. The radar level sensors fitted within the CSTs allow tank volumes to be tracked and displayed in real time via TWMA’s secure online portal, which customers can access from anywhere. i
For more information: https://twma.com/
WIKA has been certified by TÜV SÜD in accordance with the new ISO 19443:2018 quality management standard for civil nuclear projects.
The measurement technology manufacturer is the first company in Germany, and the fourth worldwide, to achieve this status. The audit was passed at the first attempt.
So far, WIKA has been certified to KTA 1401. However, this standard was primarily designed for the German market. With its processes in accordance with ISO 19443, WIKA is now focusing on global project business in the civil nuclear power generation segment. Customer audits for qualification as a supplier can thus be widely reduced.
For the measurement requirements of the industry, WIKA offers products and customer-specific solutions for the measurement parameters of pressure, temperature and level.
ABB and CCS specialist Captimise have joined forces to help industrial CO2 emitters find the most efficient and cost-effective solution to integrate CCS into their operations and eliminate the release of CO2. The UK Government’s Industrial Decarbonisation Strategy sets out the goal of reducing industrial CO2 carbon emissions by at least 90% by 2050, with CCS cited as a key tool in achieving this.
At
Captimise’s experience across Europe and the US includes over 25 live case studies with CO2 emitters from a range of different industries. Together with ABB’s depth of knowledge in the power, oil and gas, and chemicals sectors, Captimise offers support to CO2 emitters as they transition to more sustainable operations.
Through their screening study methodology, ABB and Captimise partner with operators to evaluate the alternative technologies and in the context of their wider business most cost optimised and appropriate
@TheEICEnergy EIC (Energy Industries Council)
Just over a year ago 120 world leaders converged on Glasgow for COP26, fuelled, we hoped, with a concerted realisation that time is running out on the climate change agenda. The time for talking is past; the time for acting is now.
As a result, COP26 saw some serious commitments being made towards decarbonising the energy industry. They didn’t go as far as many might have hoped, nevertheless some real milestones were set. The challenge now is to translate those commitments into real solutions and live projects.
In Scotland and across the rest of the UK, that led to an even greater focus on the need to prioritise the energy transition, to move from a dependence on hydrocarbons in favour of a more sustainable, cleaner energy mix.
On 24 February 2022, the Russian invasion of Ukraine rocked a world already turned on its head by a global pandemic. As the impact of what that meant for our energy supply and security became increasingly evident, policy underwent a U-turn, oil and gas were no longer bad words and we saw a ramping up of actions designed to not only rejuvenate, but to accelerate the production of hydrocarbons as a primary source of energy.
Short-term solutions are needed that respond to today’s immediate needs for energy security and affordability, yet ensures sustainability isn’t pushed onto the back burner and continues to be a priority with longterm strategic planning for growth.
How we address the energy market and its mix of economic demand and political pressure is a significant challenge. The headwinds that will create the uncertainty of economic growth as we continue our recovery from COVID, should not be underestimated.
In countries across the world, we are seeing different responses from governments as they try to provide a safety net and relief for consumers and businesses.
Getting the balance right will be extremely difficult with politics driving short-term decision making as opposed to more strategic, impactful medium and longer-term activity.
No one doubts that working towards real, sustainable solutions to the energy trilemma is complex. But critically this must be about longterm thinking, long-term transition, long-term implication and there will never be a quick, easy answer.
Our energy transitions from coal to hydrocarbons to something else, always brings more complexities than what has gone before. It’s about more than just a change in energy infrastructure and supply, it’s about how we consume energy, how we store it and how we move it around.
The reality of past decision-making around committing to a single solution of supply infrastructure then not following through, is part of what we’re seeing come to the fore now.
In France for example, we saw fantastic development of a nuclear feed, but they took the foot off
the pedal and are now seeing the problems it has created because they don’t have a next phase of production coming through.
There is a question too as to whether the high costs of power we are currently experiencing will help or hinder the energy transition. The reality is that we must tackle those issues together. Unpopular as it is in many quarters, the need for hydrocarbons will remain a crucial part of our energy mix for decades to come. But alongside that we must continue to press ahead with the energy transition.
From a UK Plc perspective, it’s encouraging to see positive language in the government’s messages that will change the status of the oil and gas sector from being the bad boy in the room and, as part of the industry as a whole, become more of an engaged partner which can help identify solutions for the future.
Alongside that, we must also move forward with some of the early-stage development of add on activities to oil and gas production to drive forward some of the new projects surrounding carbon storage, gas storage and critically, some of the mixed energy transition solutions.
This includes projects around the electrification and decarbonisation of production assets with the ultimate goal of newer energy solutions and how we are going to store and transport those.
World leaders gathered for COP27 in Egypt, but it will be COP28 in UAE this year that will shine a much stronger light on where we are in progressing the commitments made in Glasgow against performance.
One of the biggest questions facing us is how we meet the ambitious targets set by governments for the production of those newer energy solutions and for increasing local content through the supply chain.
The complexity of building the capacity, capability and the supply chain is enormous. Thanks to oil and gas, we already have a wealth of engineers and the project delivery muscle to deliver large-scale, multidecade projects. The UK already produces a significant proportion of the world’s fixed wind energy, but in reality our supply chain needs significant development to reach these aspirational goals.
Identifying ways to build up our supply chain and localising it to make it effective and globally competitive is a massive challenge, the solution to which lies to a large extent with the multi-billion investment that can make it happen.
There is much debate on whether we should try to do it all, against a realisation or acceptance that we simply do not have the capacity and infrastructure to make this happen if we are to meet our production targets. Our focus should perhaps be on building on what we know we do well, exporting our globally-leading skills and expertise to the wider market.
In achieving our goals, collaboration will be key and as part of that, the route to progress must be smoother, more straightforward and more co-operative. Anyone who has tried to do anything from a planning perspective knows that it can be a pretty tortuous process – and that’s just one part of the equation.
To be successful, we must take a more integrated approach to our energy creation, our energy story.
The challenge in the future is to acknowledge the overlap between agencies such as OEUK, Renewables UK, Scottish Renewables, Crown Estate and Crown Estate Scotland, various levels of government and the National Grid. They must work in tandem to realise achievement.
We have targets set through ScotWind, but how do we actually plug that in, where is the grid infrastructure and how do we build a coherent, interconnected system are all questions that must be answered.
We have the skills, the expertise developed over decades in the oil and gas sector and we now have to join the dots on the regulator picture to enable us to accelerate our transition.
It’s always going to be a challenge. Politics is a reality. We’ve seen a succession of energy ministers come and go through BEIS and its predecessors, each time a learning cycle and new engagement creating and adding to new challenges.
Sign up for the EICOnline newsletter Visit www.the-eic.com/Forms/NewsletterSignup
COP28 in UAE 2023 will shine a much stronger light on where we are in progressing the commitments made in Glasgow. That will bring the reality. That will emphasise how crucial it is that we move on from the rhetoric to real progress before we run out of time.
Vysus Group is a standalone engineering, global energy and technical consultancy formed from the former energy division of Lloyd’s Register Group in November 2020. The company offers specialist asset performance, risk management and project management expertise across major industrial, transport, manufacturing and energy assets. It supports owners and developers of energy, power and complex infrastructure – covering nuclear, oil and gas, renewables, onshore, offshore and non-hydrocarbons. Headquartered in Aberdeen, Scotland, Vysus has a global reach of more than 20 countries, with key sites in Houston, Oslo, Melbourne and Kuala Lumpur.
Vysus Group retains its entire capability and continues to offer its full suite of technical, regulatory and operational expertise globally and it is driven by its purpose to help clients manage risk and maximise performance, blending deep technical knowledge and data-driven insights with hands on expertise.
For more information visit www.vysusgroup.com
Before we look forward to 2023 we would like to look back at the year just passed. It is strange to think that 2022 started still very much in the grips of uncertainty, we clearly remember this time last year worrying what the Scottish Government were going to do and if Offshore Europe was going to be postponed. As we returned in the New Year the news very quickly came that Offshore Europe had indeed been postponed to 2024. Our next event, Wind Expo Japan, also had to once again go virtual in March 2022 as Japan’s borders were still closed. The year started looking up however, and we were delighted to once again host UK pavilions at OTC Houston, Rio Oil and Gas, Gastech in Milan, WindEnergy Hamburg, Oil and Gas Asia and we managed our first pavilion at the Hydrogen Expo in Bremen. To end the year as always we had ADIPEC, where this time we hosted 93 UK companies in the pavilion.
The show was quite frankly unbelievable. The footfall was crazy, by 10am on day one the halls were full and absolutely buzzing! We are already nearly booked up for 2023 so if you do want to exhibit with us, we would recommend getting in touch soon.
As well as our pavilions we were delighted to once again be managing the Energy Exports Conference in Aberdeen in June, which was once again inperson and attracted over 1000 delegates, 83 speakers, 5 inward delegations, 24 exhibitors and 238 one-to-one meetings.
This year looks even busier with some old and new shows. To see what we have coming up check out the website or contact one of the team, but for now here are some highlights from the year:
Firstly, I would like to take this opportunity to wish all our members a very happy, healthy and prosperous new year. We hosted 32 events in 2022 which focused on the whole energy sector from hydrogen, CCUS, nuclear, offshore wind, decommissioning, the blue economy and many more current topics and project updates.
North Sea Decarbonisation Conference
Marriott Hotel, Grosvenor Square, London
The EIC, along with international supporting partners, is delighted to be bringing you the third North Sea Decarbonisation Conference on 16 and 17 May 2023 in London. NSDC 2023 will include sessions focussed on: offshore wind, floating offshore wind, hydrogen, CCUS, marine energy, nuclear, financing net zero and electrification. Our two-day conference will explore the North Sea’s journey and how it is playing a leading role in the transition to a low carbon energy future, as well as presenting an opportunity to further connect the UK and neighbouring European markets.
At the start of last year we were thrilled to launch a two-year partnership with Mott MacDonald. This partnership was established to deliver a global platform of events for industry experts to discuss the technological, economic, environmental and social transformations needed to build a sustainable future. We were also delighted to deliver a series of energy transition masterclasses alongside Energy Transition Zone Ltd (ETZ) aimed at supporting north east Scotland energy supply chain companies transition to and capitalise on future opportunities in the UK and international low carbon energy markets. 2023 will be another exciting and busy year for the EIC UK events team. We are committed to bringing you up to date industry events across all sectors. Our aim this year is to bring you even more events, host networking opportunities and give members a platform to promote their brand and stay connected with the industry. Some highlights for 2023: 20 April 2023
The EIC 80th Anniversary Networking Dinner Dorchester Hotel, London
For the 80th anniversary EIC is looking back into our EIC history and celebrating in style, bringing back the EIC’s iconic networking dinner and dance at the Dorchester Hotel in London. Taking on a 1940’s theme the evening will provide all EIC member companies and invited guests a networking event to remember, featuring guest speakers and the odd surprise throughout the night.
5-8 September 2023
Offshore Europe Collaboration Zone P&J Live, Aberdeen EIC is delighted to be looking after the newly established Collaboration Zone at Offshore Europe 2023. There will be a series of sessions running over the four days highlighting the power of collaboration within the energy sector.
Survive and Thrive Excellence Awards
Marriott Hotel, Grosvenor Square, London
The EIC Awards are back for 2023 on 19 October at the amazing Marriott Hotel in Grosvenor Square, London for another fabulous evening of networking, entertainment and celebration. The evening will provide the opportunity to mingle with industry professionals, catch up with old friends and celebrate the amazing achievements of our EIC member companies. Widely considered the Oscars for the energy sector!
If you are interested in any of the above, please email eventsuk@the-eic.com
We look forward to seeing you all soon.
Jo Campbell Regional Director, UK & Europe
jo.campbell@the-eic.com
On behalf of everyone here in the office we would like to wish you, your respective families, and businesses a healthy, happy and prosperous 2023. Based on what we are seeing in the market, alongside several conversations that I have held with many of you over the past few months, this year is gearing up to be one of the busiest yet.
Ryan McPhersonWith COP28 taking place in the UAE towards the end of the year I am certain that this year will prove to be the start of a long awaited upturn in our industry, where the entire team is on hand to assist you wherever we can. We look forward to seeing you at our many events across the year and wish your organisations all the success for what we hope is a period of prolonged growth for you all.
Ryan McPhersonRegional Director, Middle East, Africa, Russia & CIS ryan.mcpherson@the-eic.com
Last year held a number of highlights for the team here as we fully transitioned out of the various restrictions in place. Our EIC Roundtable series was held across five different countries where we had over 100 companies participate in several pertinent topics. Our EIC Monthly Luncheon also kicked off providing a platform to network amongst your peers. UAE Re-Connect also returned in its physical guise, our first collaborative event with SPE was an overwhelming success, we celebrated our inaugural EIC Regional Awards; and once again we enjoyed a productive week hosting over 90 companies on the UK Pavilion during ADIPEC 2022.
The challenge is always to build and improve upon this for our members and this year will be no exception. We have bolstered our events team to ensure a full programme, which includes our inaugural Oman Connect event taking place on 7 February 2023 alongside UAE Connect which will return to Abu Dhabi in May 2023. We are excited to welcome McDermott to the first of our ‘Business Opportunities with’ series on 26 January 2023, which will take place across the year, and who could forget our Annual Golf Day taking place at the Els Club, Dubai on 2 March 2023. Our quarterly GCC and Africa Market and Project Update webinars will also continue, providing you with a high level of market intelligence.
This year also represents a significant milestone for EIC as we celebrate our 80th anniversary. Alongside my colleagues across the globe, we will be rolling out the red carpet where we look forward to welcoming as many of you as possible to celebrate with us.
Full details of these events can be found on our website with more to come. Anyone interested in sponsoring these events can reach out for further details to baqhtawar.shaikh@the-eic.com
Our UAE Country Report has also been launched which is free for all members to download. With UAE SupplyMap and our Qatar Country Report to be launched later on in the year we are making sure that we provide you with the required market intelligence to assist your organisation.
ADIPEC 2022 generated an estimated US$8.2bn in business for exhibiting companies, a survey conducted across the 2,200 exhibitors has revealed. The event hosted more than 40 ministers and 38 company heads, with a record attendance of more than 160,000 attendees from 164 countries, with 41% coming from abroad as it addressed critical issues facing the energy sector.
Africa could capture as much as 10% of the global green hydrogen market as demand for cleaner fuel continues to grow amid decarbonisation efforts. African hydrogen projects could create up to 3.7m jobs and add as much as US$120bn to the continent’s GDP in the next three decades. Africa’s solar and wind resources could produce 30 to 60m tonnes per annum (mtpa) of green hydrogen by 2050, about 5-10% of global demand.
Africa likely to capture 10% of global green hydrogen market by 2050
This year has been an interesting one for us at EIC APAC. We started the year amidst a pandemic, dealing with a myriad of restrictions and closed borders but things shifted quite rapidly throughout the course of the year, and we have finally gained some semblance of normality with lifted restrictions and the freedom to travel across borders. With less than two months left until the new year, I would like to reflect upon some of the major events that EIC APAC has hosted over the year.
Azman NasirIn September, we organised and managed the UK pavilion at the Oil and Gas Asia conference (OGA) in Kuala Lumpur. This month EIC APAC is collaborating with Informa Markets to organise the Race To Net Zero – The Tools Needed In Mobilising Energy Transition session at OSEA 2022. At this session, speakers from PETRONAS, Wood and GE Gas Power will share their organisation’s energy transition strategies and discuss the tools that will enable the decarbonisation of the energy sector. The event will be held on 15-17 November 2022 at Marina Bay Sands Expo & Convention Centre, Singapore. Azman Nasir, Head of Asia Pacific azman.nasir@the-eic.com
We kicked off with our annual EIC breakfast networking event in January 2022 officiated by the Deputy British High Commissioner to Malaysia, Dave Thomas. A total of 10 ASEAN member companies participated as sponsors and exhibitors, with about 200 attendees from within the energy community in KL. Although there were some -19, we were encouraged to see the large turnout. It was an indicator for us that energy players in KL were eager to attend physical events.
In February we hosted our first monthly EIC members networking session to give members in KL an opportunity to meet one another and exchange notes. We received a lot of positive feedback for this event that was attended by more than 50 members and non-members. This led us to continue hosting similar networking events within KL and beyond (once the borders opened) with the aim of engaging with existing member companies and recruiting new members within the Asia Pacific region. We ran two major series of networking events this year – the Coffee and Chill series and Meet The Energy Players (MTEP) roadshows. Locations included KL, Terengganu, Sabah and Sarawak in Malaysia, and Ho Chi Minh City in Vietnam.
In May, we organised the EIC APAC Energy Conversations 2022 which was a huge success. The event was officiated by the Deputy British High Commissioner to Malaysia, Dave Thomas. We also had in attendance the Group CEO of Sarawak Energy, Datu Sharbini Suhaili, the Vice President and Chief Sustainability Officer of PETRONAS, Charlotte Wolff-Bye, and the Country Chairman for Shell Malaysia, Ivan Tan. The event was geared to enlighten the energy community especially SMEs in the region on how the energy landscape is evolving in APAC.
EIC APAC also participated in various external events as an exhibitor this year, such as the Sabah Oil & Gas Conference & Exhibition (SOGCE) in Kota Kinabalu, in June 2022, and the Future Energy Asia 2022 Exhibition and Summit (FEA) in Bangkok, in July 2022.
Visit www.the-eic.com/Forms/NewsletterSignup
Medco Energi is going ahead with its Bronang field development on South Natuna Sea Block B offshore Indonesia and has invited companies to pre-qualify for the key EPCI prize that will involve production facilities including the Bronang gas wellhead platform, modifications to the Hang Tua mobile offshore gas production unit and the Belanak floating production, storage and offloading vessel.
Samsung Engineering is joining the group of players aiming to study the potential of supplying at least 900MW of hydro-based renewable power for the H2biscus green hydrogen/ammonia project in Sarawak, Malaysia. Samsung and South Korean compatriots Posco and Lotte Chemical are teaming up on the study with Sarawak Energy and the Sarawak Economic Development Corporation (SEDC) for the study.
membership@the-eic.com
Keeping you up to date with energy news from around the world
On behalf of all in the EIC APAC team, I would like to wish everyone reading, your families, and businesses a happy and prosperous 2023.
EIC APAC will be kicking off our events for 2023 with the EIC APAC Annual Breakfast on 10 January, to set the tone for the rest of the year. The event will be officiated by an official representative from the Department for International Trade UK to Malaysia. A total of 10 member companies will be participating as sponsors and exhibitors, with about 200 attendees from within the energy community in the region.
In March, EIC APAC will be organising our flagship Asia Pacific Energy Conversations 2023 (APEC 2023) event. APEC 2022 was a huge success. The event was officiated by the Deputy British High Commissioner to Malaysia, Dave Thomas. We also had in attendance the group CEO of Sarawak Energy, Datu Sharbini Suhaili, the vice president and chief sustainability officer of PETRONAS, Charlotte WolffBye, and the country chairman for Shell Malaysia, Ivan Tan. APEC 2023 is geared to enlighten the energy community especially SMEs in the region on how the energy landscape is evolving in APAC. The theme is focused on opportunities in decarbonisation and digitalisation as well as avenues for SMEs to diversify their businesses.
EIC APAC will be continuing our Meet the Energy Players series in not only Malaysia but also across the region, mainly in India, Australia, Japan, Philippines, Indonesia and Taiwan. We will be bringing member companies to meet energy players within these markets, including state-owned enterprises, key operators and EPC contractors. This event will also provide a platform for our member companies attending to present their latest solutions and offerings related to sustainability and energy transition. Please see the page opposite for all of our events and sponsorship opportunities this year.
We are happy to note that as of December 2022, the EIC APAC office in Kuala Lumpur has managed to recruit 43 new members since April 2021. We are hopeful that this number will keep increasing in 2023 and that we continue to provide improved value-added services to all members in the region.
Azman NasirHead of Asia Pacific azman.nasir@the-eic.com
Email newsdesk@the-eic.com Phone +44 (0)20 7091 8600
The Palaszczuk administration, Fortescue Future Industries, and Windlab plan to construct the North Queensland Super Hub with 10GW of wind and solar projects to generate industrial-scale green hydrogen. The first stage will comprise the 800MW Prairie wind farm and the 1,000MW Wongalee project, the details of which have not been disclosed. The construction of the first 1,800MW of capacity is anticipated to begin in 2025, pending approvals. Land agreements have been obtained, and by Q1 2023, an application for development approval will be submitted. Windlab will construct 100 turbines and it is expected to be operational by 2027, with production being utilised to manufacture green hydrogen and fed into the grid.
Copenhagen Infrastructure Partners (CIP) and Pacific Corporation JSC have signed a memorandum of understanding (MoU) to allow the company to work on their development projects to design and execute a solution in which Vinh Tân port could be used for construction activities and operational support during the lifecycle of offshore wind farms. The port is strategically located to support the offshore wind farm La Gan and other projects in south of Vietnam.
has partnered with Vietnamese company to fast-track
EIC APAC Annual Breakfast 16 January Kuala Lumpur, Malaysia P P P
Upstream Oil and Gas Opportunities 17 January Webinar P
Meet the Energy Players in Johor 9 February Johor, Malaysia P P P
Downstream Opportunities 15 February Webinar P
Meet the Energy Players in Terengganu 23 February Terengganu, Malaysia P P P
EIC Sports Day 25 February Kuala Lumpur, Malaysia P
Meet the Energy Players in Australia 15 – 17 March Perth, Australia P P
Doing Business in the Middle East 21 March Webinar P
3rd Regional Committee Meeting 30 March Kuala Lumpur, Malaysia
EIC APAC Iftar Networking 30 March Kuala Lumpur, Malaysia P
EIC APAC Eid-ul-Fitr Open House 9 May Kuala Lumpur, Malaysia P P P
EIC 80 – APAC Energy Conversations 10 – 11 May Kuala Lumpur, Malaysia P P P
Future Energy Asia – EIC Pavilion 17 – 19 May Bangkok, Thailand P P P
Energy Exports Conference (EEC) 6 – 7 June Aberdeen, UK P P
4th Regional Committee Meeting 8 June Sabah, Malaysia
Sabah Oil, Gas & Energy Conference 8 – 9 June Sabah, Malaysia P P P
Meet the Energy Players in Philippines 20 June Manila, Philippines P P P
Meet the Energy Players in Sarawak 12 July Miri, Sarawak P P P
Decarbonisation Opportunities 25 July Webinar P
Meet the Energy Players in Sabah 15 August Sabah, Malaysia P P P
EIC Regional Awards 24 August Kuala Lumpur, Malaysia P P
Wind Energy Opportunities 5 September Webinar P
OGA Networking – EIC Pavilion 11 – 14 September Kuala Lumpur, Malaysia P P
Meet the Energy Players in Indonesia 21 – 23 September Jakarta, Indonesia P P
Meet the Energy Players in Taiwan 19 – 21 October Taiwan P P P
Meet the Energy Players in India October India P P
Meet the Energy Players in Australia 9 November Perth, Australia P P P
APAC Energy Market Overview 16 November Webinar P
APAC Christmas/Year-End Networking 14 – 15 December Kuala Lumpur, Malaysia P P 2024
EIC APAC Annual Breakfast 10 January Kuala Lumpur, Malaysia P P P
Meet the Energy Players in Japan February Tokyo, Japan P P P Get in touch For more information contact...
Sign up for the EICOnline newsletter Visit www.the-eic.com/Forms/NewsletterSignup
Email apac-events@the-eic.microsoft.com • Email faazila.sadik@the-eic.com • Phone +603 2725 3600
The new year is here! The EIC North and Central America team wishes the EIC community a prosperous and fruitful 2023. During the holiday season, the North and Central America team made the most of the conferences taking place in our region by attending and participating in: World LNG & Gas Series: Americas Summit & Exhibition, Deepwater Operations Topsides Platforms – Hulls Conference & Exhibition, and the Reuters: Petrochemical Supply Chain and Logistics 2022 Conference. I had the pleasure of moderating the Mapping the Route Towards a Strong Hydrogen Economy in the Americas panel and speaking in the GHG Emission Reduction and Technological Innovation Across the Gas & LNG Supply Chain panel and the Supply Chain’s Impact on Sustainability panel at two of the above listed conferences. These panels included the industry experts: Paul Sullivan, VP, UMLNG; Anand Jha, global sales leader for chemical, oil and gas, ABB; Saima Yarrow, head of LNG, MIQ; Will Shimer, business development manager, projects, OGCI Investments; Abid Rizavi, global drilling procurement manager, bp; and Anita Manivani, supply chain manager, Shell.
In addition to the conference and exhibitions our team attended, during November we held an online webinar open to both EIC members, non-members, and free of charge with event partners Speedcast and Amazon Web Services (AWS) titled How Latest LEO Satellite Technology and Cloud-Based Applications are Revolutionising the Energy Industry. I moderated this event, and was joined by Sandro Delucia, commercial product director, Speedcast; and Dmitriy Tishechkin, principal partner, technical lead for energy, Amazon Web Services (AWS) to discuss how the latest LEO technologies can accelerate a company’s cloud journey without adding unwanted complexities.
In December, we welcomed Bechtel again for a second business briefing as part of our EIC member only, 20222023, North and Central America Business Briefing series. Throughout this event, EIC members had the opportunity to hear from Bechtel as they presented an updated project opportunity list, procurement process, key messages to vendors and much more. This is also a great opportunity for EIC members to network. We hope we may see new and familiar EIC members during this series and throughout our events in 2023.
Amanda Duhon Regional Director,North & Central America amanda.duhon@the-eic.com
The Department of Energy (DoE) has announced US$350m funding for upcoming long-duration energy storage (LDES) demonstration projects planned to be ultimately capable of delivering electricity for a minimum of 10 hours and for up to an entire day. The programme will finance up to 11 projects and its main goal is to reduce the cost of grid-scale energy storage in the country by 90% by 2030.
Amid climate discussions at COP27, Mexico pledged to slash its greenhouse gas emissions by 35% and to double clean energy production in the country by the end of 2030. To fulfil the promise, Mexico and the US have presented a preliminary investment plan forecasting funds of up to US$48bn to be channeled into the sector over the next eight years. Additionally, so ambitious a goal will also require the government to modify its energy policies, making efforts to unlock multiple foreign investments in the sector in the future.
Please go to page 20 to see upcoming events around the world
Did you know that the Rio office can help you with the Petrobras registration process? Petrobras’ Registry of Suppliers of Goods and Services has the purpose of allowing a prior evaluation of companies wishing to take part in the procurement process. In order to win bids, companies have to be registered. Petrobras is in the process of implementing the SAP business network (Ariba network), where goods and services fiscal documents will be transacted. When you use EIC support you will save time by letting us handle all communications with Petrobras, receive alerts when your documents are due to expire, avoid any problems with the process handover if you decide to change the local agent and use the EIC to act as your power of attorney for the registration should you not have a representative in country.
We are also proud to deliver high quality global industry events to the whole of the energy sector. If you are looking to host an event and need help reaching the right audience, EIC’s event management service is here to help. Our Event Solutions service provides and simplifies the entire event planning process, helping to support your event. EIC’s bespoke event management allows you to focus on your day-today job. We provide venue sourcing and management, event marketing, speaker recruitment, all event administration duties, agenda production and event management support on the day.
The latest report from UK-based Wood Mackenzie suggests solar energy will be the most cost-effective energy source in Latin America by as early as this year. Chile and Mexico will take on pioneering roles in this shift due to their high solar potential in the region and will be followed by Brazil, a trend that could gain momentum in other countries as costs are estimated to fall by 55% before 2050. In contrast, prices in the wind sector are likely to increase owing to supply chain constraints but will remain more affordable than gas-fired projects over the next decade.
The latest EIC market intelligence product, EIC Inform is a bespoke market intelligence service created to support businesses, government departments and nongovernmental organisations to gain a better understanding of energy industry sectors, local markets and available business opportunities. This data-driven service can be used to conduct market analysis to research possible business partners, potential competitors or to create target lists of companies who may require your products and services. Last year, the Rio office provided EIC Inform for three companies. We delivered two webinars, using our market intelligence tools and searched for representatives in Brazil.
In 2023 the EIC will have a stand at two very important conferences: Rio Pipeline Conference, in August, and OTC Brazil, in October. Companies will have the opportunity to exhibit on our stands. If you are interested in any of our services, please contact us at rio@the-eic.com
Clarisse Rocha, Director – Americas clarisse.rocha@the-eic.com
Among promises of fiscal benefits for the further advancement of renewable initiatives, be it in new wind/ solar parks or in green hydrogen schemes, Brazil’s newly elected president Lula has highlighted the role Petrobras can have in the country’s energy transition. This new role could see investment growth both in natural gas and in the downstream sector (fertilisers, biofuels and refining), harnessing the pre-salt layer and realigning oil product prices in the domestic market.
How is ThinJack Ltd. thriving?
Faced with a cocktail of internal and external challenges, niche oil and gas well services and products provider ThinJack Ltd. recognised a potential business crisis in 2018. The company’s leadership knew that it had to change its approach to business, both in terms of its solution offering and target markets.
Fast-forward to 2022, and there are promising signs that the visionary shift is working, particularly in regard to new innovations and building a network in the Middle East. Thanks to support from the EIC, Scottish Enterprise, SDI and the GlobalScot network, the company looks well set to capitalise on potential demand for its technology through a local agency agreement finalised in March 2022.
Losing an influential business development leader is always a major setback, and this is exactly what happened to ThinJack Ltd. in 2018. For an SME of less than 10 employees, the compounding series of challenges, loss of BD function, need for new products and services and bad debt prompted the company’s senior leadership to chart a new course.
Lack of product and service diversity was starting to hold it back from securing new business, a narrow focus on the domestic UK offshore market limited opportunities. Its own research showed revenue streams were primarily coming from maintaining ageing assets and, with the UK winding down oil and gas activity, ThinJack Ltd. needed
to look elsewhere. Combined with oil price volatility, energy transition acceleration and a lack of presence in major oil markets such as the Middle East, it was clear that wholesale change was needed.
Faced with potential cashflow crisis and demoralisation of the team, ThinJack Ltd. set about a complete strategic rethink, leading to a new website design in 2019 and a detailed business plan consultation devised to breathe new life into the business.
Attention turned to the research and development of new offerings as a window of opportunity was granted by the COVID-19 pandemic, which had brought various projects to a halt. The company then developed two new products, the first being BonnetBuster: designed to enable better access to valves on christmas trees, it was created following client consultation regarding a problem requiring a bespoke solution. The second, HoleGuard, a semi-permanent wellbore protector in a variety of sizes and heights which safeguards the gasket ring and protects the wellbore from potential dropped object damage.
Armed with these two new innovations as well as the ThinJack Service technology, ThinJack Ltd. identified the Middle East market as the primary target for its internationalisation strategy, forming the backbone of its forward momentum through 2021 and beyond.
The company engaged with bodies such as the EIC, SDI and the GlobalScot network for advice on entering the
(0)20
region and identifying potential local partners. After searching and scoping out numerous options, ThinJack Ltd. selected Al Yaseah OGISS as the partner of choice to enter a local agency agreement. This contract was finalised in March 2022 with the aid of an SE IRP grant for legal support.
Since then, the main priority has been generating awareness of ThinJack Ltd.’s capabilities throughout the region. This has involved attending flagship events such as ADIPEC and OWI, the Middle East’s leading well intervention conference, with solid interest being shown by several potential clients such as PDO Oman, Dragon Oil and Cameron. In May, ThinJack Ltd. attended the EIC’s ReConnect UAE event held in Abu Dhabi, with a view to an in-country technology demonstration later in 2022.
Such events and progress bode well for ThinJack Ltd. as it seeks to drive forwards with its diversification and internationalisation strategy. With its local agency agreement established and networking activities well underway, and already yielding interest, it is only a matter of time before contracts are secured and revenues start to flow from this new market.
Formed in 2005, ThinJack Ltd. supplies niche oil & gas well services and products internationally. It delivers extreme force in tight and difficult-to-access spaces, primarily for breaking apart stuck equipment. Well applications include flange separation, tree cap, and bonnet removal. Other services include flange gap, tilt measuring, gap holding, and pre-lift weighing. ThinJack Ltd. also manufacture HoleGuard, a product which is a temporary fitting over the wellbore, well spool connecting hanger and the flange sealing face. It is a barrier which minimises the likelihood of damage to the gasket ring and prevents dropped objects entering the wellbore. ThinJack Ltd. has a team which has accumulated over 39 years of technical and business experience in 30 countries.
#collaboration (main category)
#export
• Diversification and internationalisation strategy moving forward
• New possible clients already interested in doing business with ThinJack Ltd.
For industry
• Be realistic on timelines, sales and cost projections
• Maximise homework on marketability, positioning, and pricing of services
• Create initiatives to support SMEs’ activities and costs for setting up internationally e.g., Business Cluster Ventures
The company received support from Scottish Enterprise through the International Recovery Programme grant to expand into the Middle East.
ThinJack at a glance:
Key products and services: Supply of niche oil & gas well services and products.
Main industries served:
• Oil & gas – 100%
Headquarters: Westhill, UK Year established: 2005
Number of employees: 9 Revenue: £300,000
Revenue from exports: 0% (2021, 2020); 70% (before 2020)
Launched by a tightknit, passionate team just six years ago, TP-Products has carved its position as the go-to technical solutions partner for operators and developers of complex subsea installations utilising compact flanges, thanks to its specialist inhouse expertise. Between an unrivalled technical knowledge base and proven track record, the firm has found its niche and is maximising opportunities at every turn, demonstrated by a continual growth in clients and revenue year after year.
John Arnesen has been able to share a truly exceptional entrepreneurial success story for this edition of Survive & Thrive. Having previously worked for a large multinational firm, he and his colleagues had a lightbulb moment. Wanting to participate more actively in the development of an organisation and develop a brand that they could call their own, they decided to take the plunge and venture out on their own to launch TP-Products in April 2016.
Of course, starting a company from scratch is no easy task, particularly in a highly competitive compact flanges, clamp connectors and subsea valve market. Indeed, it would require extreme patience and immense industry expertise to even get off the ground.
This was proven by its start, the firm recording revenues of approximately just 1 million NOK (£85,000) in its first year. Further, it also faced several unexpected surprises after failing to account for those qualification approvals needed to meet client needs and allow the firm to trade effectively.
It was a steep hill to climb, yet its entrepreneurial founders were determined to succeed.
To turn TP-Products from a pipedream into a truly successful venture, the team set about maximising the most of what they did have – driven people and esteemed competences in key technologies.
Joining Arnesen from the outset was Sjur Lassesen, a leading global expert and engineer specialising in compact flange technology. Lassesen was a key asset, having written the initial standard for compact flanges and sitting on all key global standards committees in this space. Indeed, he remains Equinor’s go to contact when facing challenges on flanges.
Having such an individual on board was vital, providing the firm with an immediate competitive advantage. Compact flanges were invented by a small Swedish engineering company in the 1960s, then being adopted by a small Norwegian company in the late 80s. Subsequently, Statoil became interested and wanted to use this flange in its large development Snorre A and later for the FPSO at Norne. However, Statoil feared that the Norweagian firm was too vulnerable and requested they make the technology a standard, this coming to fruition in the form of NORSOK L005.
Today, after the ISO 27509 NORSOK standard took over in 2012, any company can create a L005 flange. However, having the knowledge to go beyond these standards for niche applications, unique requirements and to overcome specific challenges is a highly specialist skill – one that TPProducts could offer from the outset.
This technical capability remains the firm’s unique selling point, with Lassesen’s colleague Marc Smits – a renowned engineer in design and drawings – also having joined to
ensure the company could provide the whole package, catering to unique needs with ease and flexibility.
It has been by no means a conventional road for the firm in the six years since its launch. The initial strategy was to gain a strong foothold in the Norwegian market before gradually expanding globally, yet the company was catapulted into the international market immediately, landing its first order in New Zealand. Since then, it has steadily expanded into an undeniably successful business thanks to a proven track record in successfully delivering for its clients.
One such example comes in the work completed at Shell’s Nyhamna processing plant in Norway as its plant’s technical service provider.
Here, TP-Products was brought in to address issues with seals in compact flanges. Here, Shell was faced with leakage problems that were not only incredibly dangerous but also resulted in unforced downtime and massive revenue losses. The firm helped to re-machine its flanges and acquire more suitable seals, successfully eliminating its leakages and the subsequent lost production in a smooth and efficient manner. Resultantly, TP-Products has gone from strength to strength.
Having been targeted for acquisition in December 2020, the company completed a merger with Teknisk Produksjon – a move which has proven to be a major success. Further, its revenues have now increased dramatically to 110 million NOK (£9.4 million) in 2021, having enjoyed a tenfold increase in clients in just five short years.
Moving forward, the company plans to launch a new generation of compact flanges during 2022 and beyond, an endeavour that is possible thanks to its immense team that continue to break new boundaries.
Indeed, TP-Products is a company that’s quickly made a name for itself, and at just six years young, it is undoubtedly one to watch for the coming years.
TP was established back in 1968 as a machining company delivering its services to the mechanical industry. Through the years, the company has evolved to becoming much more than just a modern machine shop. Today, TPProducts are manufacturing highly complex mechanical components for the most demanding clients in a multitude of markets, and is also offering a product portfolio of tailor made compact connectors and subsea valves, stabs and jumpers. TP-Products’ internal value chain comprises everything from design, engineering and innovation, to manufacturing and testing of its products, all done inhouse at our modern facilities in Drammen, Norway.
Story type
#scale up (main category)
#service & solutions
Benefits
• Elimination of leakages and lost production
For industry
• Have patience, it is key before results come
For government
• Make it easier for start-ups to establish themselves in the market (eg. cutting off taxes)
Government support?
The company has not received any type of government support.
TP-Products at a glance:
Key products and services: Supply of compact flanges, clamp connectors and subsea valves.
Main industries served:
• Oil & Gas – 80%
• Offshore wind – 18%
• Hydrogen – 2%
Headquarters: Drammen, Norway
Year established: 2020 (merged)
Number of employees: 53
Revenue: £9.6m
Revenue from exports: 60%
TÜV SÜD Energietechnik, a 100% subsidiary company of TÜV SÜD, has been only offering nuclear energy services for decades. However, together with the TÜV SÜD group’s dedicated Green Energy & Sustainability business unitc, the company has been driving a desire to expand its decarbonisation activities in recent times. Energietechnik has adapted to a new business environment and changing energy landscape to offer clients expert verification, validation and certification solutions to help them achieve their environmental targets, opening a dedicated Climate Action Certification business line with services in the area of carbon management. Despite only being in operation since 2021, the new business line is already making its mark, building up a track record that will only help to secure more projects and collaborations in the future.
For any business with 150 years of history behind it, plans to change course and adapt to new dynamics can easily be confronted with a certain degree of resistance to change. Why change a winning formula? Why risk moving away from its core activities?
For TÜV SÜD, a German company in the TIC sector which started in 1866 as a voluntary inspection association, a growing urgency around climate issues has emerged over the past 15 years.
While today it still stands as a global leader in safety, sustainability and security solutions across a range of industrial cateogories, recent years have seen something of a strategic rethink. Global momentum around energy transition, coupled with Germany’s policy shift away from nuclear, has opened up the minds of its leadership to new ideas.
Get in touch Share your news and views...
Email info@the-eic.com Phone +44 (0)20 7091 8600
At the beginning of 2021, TÜV SÜD Energietechnik’s Climate Action Certification business line was officially launched. It was effectively born as a start-up with some of Energietechnik’s existing business carved into it, with employees such as Paula Maria Auer-Saupe (VP of Climate Action Certification) bringing a strong background in environmental engineering with them. Indeed, Paula has been an auditor for climate change projects for 15 years and has experience in validating and verifying these types of projects all around the globe.
There are several factors which have immediately helped to strengthen the Climate Action Certification business line’s hand. Not only is it housed in a long-established, successful and financially stable parent organisation which has access to 70 experts around the world, but its board is a strong supporter of sustainability and eager to make this venture work.
On the flipside, such is the eagerness of the company across the board to explore sustainable lines of business, the establishment process often involved large numbers of keen stakeholders with strong opinions. This made it difficult to narrow down and focus, with the onboarding process seeing a huge amount of competition.
Not surprisingly, the company already has ambitious plans in place for the Climate Action Certification business line in the years ahead. To make headway, it is focusing on countries with the highest net zero and carbon reduction ambitions, a key part of the analysis phases being the creation of specific country roadmaps, evaluation of competitors and identification of specific sectors of interest, and barriers to decarbonisation that potential clients are facing.
In the area of carbon management specifically, TÜV SÜD helps organisations meet decarbonisation and sustainability goals, providing verification and validation against regulatory requirements, offering support in three phases.
First is accounting. Here, the firm provides Certification of Green Energy spanning origin, generation, fuels, chemistry, as well as classification of biogas and biofuels. Equally, the company offers Verification of Carbon Footprint, EU Emission Trading System, Verification of F-gas Reports, and Certification of Hydrogen services, among other key solutions.
Secondly, the firm helps companies to reduce their carbon footprints through energy efficiency audits. And thirdly, it helps to compensate for footprints through climate neutrality certifications, as well as the validation, verification and certification of climate protection projects.
In addition, the firm provides complementary services relating to water desalination and treatment, recyclability of packaging, sustainable supply chains, battery passports and lifecycle assessment.
In truth, TÜV SÜD ET has developed a formidable footprint supporting all stages of the carbon management lifecycle – an impressive feat given its relatively novel shift to carbon management solutions. From enhancing corporate sustainability initiatives to enabling its clientele to better position themselves for green finance projects and funding, it is a quickly mounting a reputation that will stand it in futureproof stead for years to come.
Since 1959, TÜV SÜD Energietechnik (ET) is an independent and neutral service provider for assessment, inspection and consulting services in fields of technology which present a high-risk potential, focusing on activities related to the safety of nuclear facilities. A one-stop service provider, TÜV SÜD ET supports clients with assessment and advisory services including siting and plant concepts, independent safety assessments, certification of mechanical, electrical and I&C components, on-site inspections and control of documentation and reports. Additionally, the company offers a comprehensive range of trainings in alignment with the entire nuclear power plant lifecycle.
Story type
#sustainability (main category)
#diversification, #innovation
Benefits
• Certification enables transparency into clients’ systems.
• Customers’ carbon footprints are significantly reduced.
• Be open and flexible, taking opportunities whenever they present themselves
• Walk the talk and promote your own sustainability
• Establish a standard, harmonised regulatory framework throughout the world
The company has not received any type of government support.
TÜV SÜD Energietechnik at a glance (Climate Action Certification business line):
Key products and services: expert verification, validation and certification solutions, offering services in the area of carbon management.
Main industries served:
• Energy sector – 50%
• Heavy industries (steel, pharma, pulp, and paper) –50%
Headquarters: Munich, Germany
Year established: 2021
Number of employees: 70 Revenue: £5.1m
Revenue from exports: 40%
The world’s foremost authority on flow measurement technology to the energy sector and governments globally, TÜV SÜD National Engineering Laboratory (TÜV SÜD NEL) has continued to support its customers successfully through the pandemic period thanks to an accelerated move into digital services. With a transformed offering that is now underpinned by real-time software solutions for the monitoring and optimisation of meters, valves and other subsea pipeline equipment, the organisation has secured new drivers for further innovation and growth.
Like many companies serving the energy industry across multiple territories, the implications of the COVID-19 pandemic created immense challenges for TÜV SÜD NEL. Owing to global travel restrictions, clients could not travel to witness key equipment calibrations, the firm losing significant business as a result.
These mounting pressures were then exacerbated by both growing uncertainty in the oil and gas market and the increasing promotion of green energy technologies, accelerating the transition away from the former and towards the latter of these two markets.
The knock-on effects were significant for TÜV SÜD NEL. Not only did it begin to face operational and financial issues, but it equally struggled to retain key talent during the height of the pandemic, with many either moving into new energy or retiring.
At the height of the pandemic, there was a sense of urgency within TÜV SÜD NEL – a feeling that embodied itself as a catalyst for change.
The organisation had to respond to secure its future, this reaction beginning in mid-2020 with the development of digital packages that would be offered to clients. Indeed, it had experience in leveraging digital technologies for internal purposes. However, under the circumstances it pivoted rapidly, accelerating the development of these solutions so that they could be marketed externally and add value to client operations.
Here, the focus was on developing real-time data software packages for the remote monitoring of and optimisation of meters, valves and other subsea pipeline equipment. Not only would this provide more meaningful data for clients, but it would equally remove the need to travel offshore, enhancing convenience and reducing their operational emissions.
To achieve this the firm invested in growing the consultancy and digital teams, currently sitting at 15. Meanwhile, its key facilities in East Kilbride in Scotland provide the means of backing up its newly deployed digital solutions with physical testing, adding a much-needed additional layer of reliability to its adapted offering.
Owing to this focus on enhancing capability, the firm was able to successfully roll out a series of new technologies including computational fluid dynamics (CFD) – a form of fluid mechanics using numerical analysis and data structures to evaluate issues with fluid flows.
The results of this transition have proven invaluable. CFD modelling contributed to an overall revenue growth of £1.6 million in the digital segment between 2019-21.
There have been several key projects completed during this time, one example coming from the deployment of a virtual multi-phase meter that provides real-time data and alerts into valve and meter health and performance. Poor meter performance risks creating multi-phase issues such as the presence of either excess gas or water, which can be dangerous. Here, the technology has been deployed to address such an issue directly, allowing adjustments to be made ahead of time and preventing the need to remove/ replace valves and meters completely which can come at a heavy cost.
In addition, TÜV SÜD NEL has also completed work for a client where software was deployed for analysing the performance of a flare stack. Here, CFD modelling has been used to improve both flaring and combustion performance at the flare tip. By assessing if the methane phase is too high, adjustments can be made to burn more methane, offering significant benefits with methane being 80 times more damaging to the environment than CO2. Resultantly, the solution is saving significant costs.
Of course, there have been difficulties with such a major transition. Towards the end of 2021 the firm suffered a quiet patch while also finding it challenging to recruit staff given the skills shortages facing the industry. Yet with a new futureproofed offering and revenues from digital services growing year on year, the company has firmly enhanced and diversified its services in order to better meet clients’ needs in the long run.
As holder of the UK’s National Standards for flow and density measurement, part of the UK’s National Measurement System funded by BEIS, TÜV SÜD National Engineering Laboratory is one of the leading authorities on flow measurement issues in the world.
The company is an independent provider of calibration and testing services, in addition to consultancy services offering theoretical guidance and practical support on all aspects of flow measurement. Besides, its studies and development work is at the forefront of research into flow and density measurement at the UK, European and global level.
Story type
#digital (main category)
Benefits
• Digital revenues increased by £1.6m in two years
• Savings for client of $10m annually in flaring fines and taxation
For industry
• Collaborate, not just compete, in order to accelerate the energy transition
For government
• Don’t villainise the oil & gas industry; find a place for it in the transition
Government support?
The company has secured a number of government contracts.
TÜV SÜD NEL at a glance:
Key products and services: independent consultancy, on-site measurement, testing, R&D and training services
Main industries served:
• Oil & gas – 70%
• Hydrogen, CCUS – 30%
Customers:
• Government – 60%
• Industry – 40%
Headquarters: East Kilbride, UK
Year established: 1995
Number of employees: 80
Revenue: £12m
Revenue from exports: 5%
Tackling the problem of fugitive emissions head on
How is UCT Fluid Solutions thriving?
UCT Fluid Solutions has grasped the nettle when it comes to the bigger picture of net zero and sustainability. Recognising that leakages through valves are a major source of fugitive hydrocarbon emissions among many of its clients, the company has set about developing and upgrading its product ranges to better manage this problem. And the early signs are that the investment may be on track to pay dividends for years to come.
After a challenging 2020 caused by the oil & gas market downturn, compression fittings and valves manufacturer UCT has once again been able to increase its market share through 2021 as demand picked up again.
However, it has not all been plain sailing. As well as having to overcome various supply chain and logistical problems by leveraging its global footprint, the company is also working with its customers who are striving to become hydrocarbon free. Given that a portion of emissions leak through the very valves it produces, UCT Fluid Solutions knew that it had to be first to market with a leak-free offering (or as close to as possible) that could support net zero ambitions.
Cutting fugitive leaks has been a major priority for
companies operating in the process industries market, and given that around 60% of such leaks occur through valves, UCT decided to rise to the challenge and enter territory that no other player has explored to date.
Indeed, the strategy to upgrade and certify various product lines for leakages and emissions has been formally in place since 2019. It has involved several major areas of focus which have brought products into line with ISO 15848 certification – the standard that covers fugitive emissions.
A key part of this has been the development of a fully encapsulated valve technology designed to eliminate all fugitive emissions with secondary containment of all emissions. Incorporating the use of magnetic bearing systems, UCT has committed to introducing new production methodologies in order to produce the component at scale.
Although 2021 has seen a greater willingness from UCT’s customer base to adopt new technology after a challenging 2020, the development is still a work in progress and presents a more costly option than typical mainstream valves. However, the company is continuing to work with clients to demonstrate performance and use cases, and is also seeking to uplift specifications in refineries which will create additional demand.
For example, an Israeli oil refinery has utilised UCT’s Fluid Solutions Emission Free Valve to eliminate leak hazards (chiefly Hydrogen sulphide and Benzene) during
the process flow, as well as to conduct sampling without risking damage to the environment. Its previous valve technology had major vulnerabilities, and the customer is now able to operate a healthier workplace thanks to Fluid Solutions’ fully encapsulated shut-off valve.
This example aside, the overall numbers at this stage, appear to be promising. UCT sold several hundred in 2021, a considerable increase over 2020 – and within five years, hopes zero emissions products such as this will account for a larger portion of all product sales.
Another area of focus has revolved around smart solutions. Here, the company has developed a valve fitted with sensors which are capable of detecting emissions and thus triggering shutdowns to avoid additional leakage. A key challenge that has been overcome involved the integration of the electronics and software into a compact package, a move which saw UCT break new ground having previously only developed mechanical products.
Established in 1950, UCT Fluid Solutions is an Israelbased manufacturer of high-tech compression fittings and valves. The company’s portfolio includes tube, pipe and flare fittings, process valves, pneumatic actuators, manifolds, ultra clean valves, connectors and hoses, among other products. UCT Fluid Solutions is active in a range of industry sectors, including semiconductors, power generation, oil and gas, chemicals and petrochemicals, CNG/NGV, nuclear, pharmaceuticals and hydrogen, among other sectors. UCT Fluid Solutions is also present in the UK, USA, Singapore, Germany, and China.
The significant transitions and mindset that UCT Fluid Solutions rooted in the company were imperative to lead them to where they are today. Post-acquisition with UCT, the company is broadening technology and engineering expertise to support new designs and solutions. With this new approach, customers are exposed to a wider portfolio of advanced products and services.
#technology (main category) #innovation, #energytransition, #sustainability
• Revenue is in the early-growth stage and expected to ramp considerably soon
For industry
• Understand industry pain points and offer economically sensible solutions
• A business survives as long as it has a vision and a well-versed plan
For government
• Guidelines and tools for making statements and visions happen need to be enforced and materialised
• Emissions reduction goals need to be backed up with tangible programmes as well as support to the supply chain
Government support?
The company has not received any type of government support.
UCT Fluid Solutions at a glance: Key products and services: flow control products and solutions
Main industries served:
• Semiconductors – 60%
• Oil and gas – 20%
• Automotive/hydrogen fuels – 8%
• Power – 6%
• Analytics – 6%
Headquarters: Nazareth Illit, Israel
Year established: 1950
Number of employees: 1,050 Revenue: N/A
Revenue from exports: N/A
Having spent its first few years in operation acquiring innovative technology businesses with the potential to serve the energy market, Valor is now on the path to building out these assets, serving both traditional oil and gas markets as well as renewables.
Its innovative downhole heater, named THOR, developed and operated by Group company Cavitas Energy, is proving a particular hit within the oil sector. Following recent trials conducted in California for a local operator, some promising numbers have been provided in terms of performance and cost-saving potential. As further trials are conducted and concepts proved, the business will soon enter the realm of major growth.
As an investor-backed growth enterprise, Aberdeen-based Valor has been adding new technologies and services with a view to bringing them to market and, eventually, turning them into commercial entities.
Now, the time has come to accelerate the ‘build’ phase. Here, the company is focused on providing its newly acquired solutions to stakeholders across the energy spectrum, with key focus areas being oil and gas, energy transition and diversification into renewables such as offshore wind.
Applying its technologies and expertise to energy transition activities is a particular priority for Valor, recognising the traction being gained in this field due to decarbonisation targets being worked towards around the
world, which have been solidified in the Paris Agreement and recent COP conferences.
In response, Valor created a new entity dedicated to supporting the offshore wind sector in the form of V-TES Renewables. A service business, the company houses several specialist electrical capabilities, from HV cable terminations to switchgear maintenance, and has embarked on an extensive training programme to bring its employees up to speed and comply with offshore wind regulations.
On the technology front, a game-changing development is emerging from Cavitas Energy. THOR, its thermal enhanced oil recovery tool, is at the most exciting stage of its journey to date and in the process of being rolled out across the oil industry. Not currently facing any performance-based competition, the technology promises to revolutionise thermal applications and reduce carbon emissions related to in-situ near wellbore heating. Indeed, tests have shown it can increase heavy oil production by up to 500% and boost pump efficiency and run life by more than half. Moreover, given over 40% of the global remaining oil is heavy, which is most effectively developed by thermal operations, THORs low carbon barrels could play a key role in keeping global temperature rises under the 2°C stipulated in the Paris Agreement.
In the United States, THOR is already being deployed by an oil major looking to boost production. Having started the trial in October 2021, the company has produced some encouraging results to date, which show a three times uptick in heavy oil production, improved pump efficiency, mitigation of wax and a reduction in oil viscosity thanks to the solution’s 100-fold superior heat per foot ratio versus competitors. Meanwhile, THOR is also operating with less energy requirements than other electric or topside steam
alternatives. In terms of possible financial gains, return on investment can be made within one to two months of operation, with a revenue uplift potential of around $1 million per well per annum.
Importantly, THOR’s downhole tooling requires no maintenance across its three-to-five-year run life and can be monitored remotely, whereas more traditional methods require technicians to be on site 24 hours a day. Cavitas can fully customise THOR to suit specific well operators’ requirements.
Following a successful trial, the company has already received its first order from a Sudanese firm, a sign that Valor is ready to start realising returns on its investments made over the past four years.
Indeed, with technological innovations such as THOR at its disposable, along with in-house expertise both within AISUS, V-TES renewables and the rest of the group, Valor is starting to gain some serious momentum as its build phase journey continues. Be it traditional oil and gas or energy transition segments of the market, the company is shaping up to be capable of providing solutions and services to a sizeable portion of the energy industry.
Located in Aberdeen, Valor is a specialist growth enterprise boasting a suit of oil & gas companies collectively working towards the highest of standards within the industry. With a common purpose of increasing performance, increasing production, and providing assurance, each of the subsidiaries within Valor has been specially selected to interlink their operations in the oilfield sector. Whether it be an innovation, technology or service-based business, Valor offers and intrinsic platform to allow maximum company growth for those part of the group.
Offering flexible investment frameworks, Valor will assist current business owners to progress the company’s operations whilst reaping many benefits from the group.
Story type #technology (main category)
• Product’s successful trial paved the way for new orders and further revenue
For industry
• Develop technology and services aiming to be exceptional in your field
• Be ready to wait – get-rich-quick schemes are not real
• Control cost inflation and help new initiatives and technologies be affordable
Government support?
The company has been supported by trade missions and R&D tax credits.
Valor at a glance:
Key products and services: Investor-backed growth enterprise with buy and build strategy in new technologies and services in high-growth companies.
Main industries served:
• Oil & gas – 75%
• Renewables – 25%
Headquarters: Aberdeen, UK
Year established: 2018
Number of employees: 28
Revenue: £4.5m
Revenue from exports: 30%
How is VWS Westgarth thriving?
VWS Westgarth is on a mission to clean up the environmental impact of FPSO operations, not least in the vast volumes of plastics these activities send to landfill every year. By introducing cleanable stainless steel cartridge filters for offshore in water injection systems to the market, the company is offering a more sustainable and financially viable alternative to throwaway plastics which have been the mainstay for far too long.
The oil & gas sector has historically been more risk averse and slow to adopt change than many other industries. In the upstream water treatment space, the use of plastic cartridge filters has been the norm for many years – cheap and easy to use, it is only now that stakeholders are being presented with a viable alternative.
Veolia, through its VWS Westgarth division, is looking to shift the dial. Currently, some 1,200 MT of plastic waste from cartridge filters is sent to landfill each year, a state of play which is unsustainable – and one that Veolia is determined to reverse.
However, change will not happen overnight. Industry players need to be convinced about the financial viability of any alternative solution before it becomes widely adopted. Indeed, the traditional cartridge filter market is a lucrative one – worth around £22 million a year, with Veolia accounting for 5-10% of this business.
Indeed, the mood is changing. COP26, hosted in Glasgow, has brought sustainability to the very doorstep of the UK’s offshore industry, and Veolia’s goal is to spearhead an ecological transformation both here and across its markets around the world as part of the transition to a net zero society.
In response to the enormous waste generated by the current use of plastic cartridge filters in the upstream water treatment sector, VWS Westgarth has developed a stainless steel cartridge filter designed to offer a more sustainable choice to FPSO operators. These are cleanable offshore, and so can be used on a rotational basis.
The company is deploying a two-step approach to aid clients with the transition, leveraging its own recycling network to take away plastic cartridge filters while customers adjust to the new metal solutions.
Veolia is currently planning the pilot testing phase of its roadmap to full commercial deployment, which it hopes to achieve by the end of 2022.
A key part of the strategy, and central to its success, is convincing water treatment industry stakeholders of the business case behind the innovation, something which appears to be sound based on what we know so far. For example, while the stainless steel solution is 20-30 times the cost of plastic components, its expected lifecycle is
10-15 years – this means it can pay itself back within just two years. Factor in the lifecycle costs associated with logistics of taking plastic waste away, and the financial case looks even more compelling.
Indeed, Veolia believes it can reduce costs relating to cartridge filters by £300,000 per year per FPSO deployment. The company aims to capture around 40% of the market, which would see a huge amount of plastic waste cut from FPSO operations that currently send 870,000 plastic cartridge filters to landfill every year.
The development of a sustainable alternative is important for the FPSO sector’s sustainable credentials moving forwards. Water injection systems as we know them are here to stay, and with more FPSO deployments on the horizon, the potential to produce more plastic waste is clear for all to see. For Veolia, any short-term financial hit through phasing out its plastic solution is more than offset by its strong values and objectives around sustainability.
And while in the short-term the company knows it will be a tough sell, if trials in the coming months prove successful then the case for making the switch to stainless steel may be too difficult to ignore.
A world leader in seawater sulphate removal systems, VWS Westgarth specialises in the design, build and operation of water treatment plants for seawater injection and produced water in the upstream offshore oil and gas sector. As well as being part of Veolia Water Technologies, VWS Westgarth cooperates with other of Veolia Water Technologies’ subsidiaries around the world in Europe, Africa, the Americas, Middle East and APAC. This allows Veolia Water Technologies to cover the full scope of water treatment processes for the oil and gas industry (both upstream and downstream) and ensures they are able to satisfy local content requirements where needed by clients.
#sustainability (main category) #innovation, #serviceandsolutions
• New market size of £22m p.a.
• Potential OPEX savings of £14.4m p.a.
For industry
• In the upstream segment, evaluate business opportunities from a project’s engineering and execution to its operational lifecycle and decommissioning
For government
• Adopt a clearly defined energy transition path that recognises the role fossil fuels still play in society
Government support?
VWS Westgarth has benefited from the Apprenticeship Levy as well as R&D tax credits. The company has also received support from the Engineering Construction Industry Training Board (ECITB).
VWS Westgarth at a glance: Key products and services: design, build commissioning and operation of offshore water treatment systems
Main industries served:
• Oil and gas – 100%
Headquarters: East Kilbride, UK
Year established: 1962 Number of employees: 146 Revenue: £85m
Revenue from exports: 90%
Having successfully navigated a period of prolonged lossmaking, the impact of COVID-19 and separation from its parent company, Vysus has kicked on in its first full year as a lone entity, successfully pursuing operational diversification on multiple fronts to better align with its renewables-driven 30-30-40 vision.
In October 2020, global engineering and technology consultancy Vysus Group separated from its former parent company Lloyd’s Register to become an independent, standalone business.
Between an extensive programme of transition activities and continuing to meet its customers’ needs in the middle of a pandemic, it proved to be a challenging yet successful year.
But the company hasn’t stopped there. From this point on the firm has sought to reposition its operations in order to better navigate the complexities of energy transition. As a business that historically relied upon upstream oil and gas revenue generation across our service offerings and global footprint, the firm recognised the need to diversify to create a broader scale renewables and complex infrastructure and power business.
Indeed, with these ambitions signifying a mass shift away from its legacy footprint that dates back to the 1930s, the challenge for Vysus in 2021 was clear.
The decision to restructure came back in 2019 after a
period of loss making from 2014 as a result of the oil price crash, signifying the need for Vysus rethink its offering.
The company reshaped the business back to being profitable, decided which key expertise to retain and grow, and launched a five-year vision to position for net zero with the launch of its 30-30-40 vision (revenues derived from 30% oil and gas, 30% infrastructure and 40% renewables).
While COVID and Vysus becoming a lone entity created significant operational complexity, the firm has continued to persist with its 30-30-40 vision to great effect.
Internally, it evaluated skillsets to identify strengths and weaknesses to inform a recruitment plan that would work to plug any existing skills gaps. Revisiting the messaging and image of the firm was part of this plan – necessary in order to ensure the technical challenges and move to renewables was seen as an engaging and exciting prospect for existing team members and new starters. Here, time was spent consulting with staff members to redefine its core values and develop a new identity.
Operationally, the company also worked tirelessly to better understand how it could deliver key solutions to clients. The EICDS was used to learn more about renewables markets and client engagement was also used to identify specific needs, trends and opportunities while cultivating relationships. This included the firm’s Planit22 initiative –an external survey of 250 energy execs on their views on COP26 and what they planned to do to align towards net zero and embrace sustainability.
Such initiatives have already proven to be extremely successful. Not only has the company been able to repurpose its expertise and capabilities to focus on new
markets and evolving technologies, but it has equally begun to support existing clients through their own strategy shift and build new relationships with emerging players.
As a result, it moved from being a loss-making enterprise to making a small profit in H2 2021, capping off a promising first full year for Vysus. And in 2022, the ambitions remain similarly grand.
Plans for the year ahead are centred around more growth, diversification and performance improvement as the organisation continues to pursue its 30-30-40 vision.
By 2025, the firm expects its business mix to comprise 30% in upstream activities, 30% in infrastructure and process industries and 40% in the power, renewables and transition space – a major shift from 90% of its business being focused on the upstream sector through to mid-2020.
And the signs are promising. Indeed, five years ago, revenues secured by its Survey & GeoEngineering business were circa from 80% oil and gas and 20% from renewables. Fast forward to 2021, and this has flipped to approximately 90% from the renewables sector.
Meanwhile, Vysus’s Grid & Power Systems business in Australia is expanding; it has established a hydrogen sector of excellence within its risk management organisation; and in the US the company’s onshore survey and power engineering businesses has seen a significant increase in power and renewables related projects.
Between these endeavours and an ongoing commitment to supporting its oil and gas customers as they continue to play a key role in the energy mix, the future looks ever brighter for Vysus.
Vysus Group is a standalone engineering, global energy and technical consultancy formed from the former Energy Division of Lloyd’s Register Group in November 2020. The company offers specialist asset performance, risk management and project management expertise across major industrial, transport, manufacturing and energy assets. It supports owners and developers of energy, power and complex infrastructure – covering nuclear, oil & gas, renewable, onshore, offshore and nonhydrocarbons. Headquartered in Aberdeen, Scotland, Vysus has a global reach of more than 20 countries, with key sites in Houston, Oslo, Melbourne and Kuala Lumpur. Vysus Group retains its entire capability and continues to offer its full suite of technical, regulatory and operational expertise globally and it is driven by its purpose to help clients manage risk and maximise performance, blending deep technical knowledge and data-driven insights with hands on expertise.
#diversification (main category)
• Revenues expected to grow by 12% in 2022 from 2021.
• Don’t see the market as a “one winner takes all” environment. We all need to win.
• COVID has taught us that we can do things differently
• Make sure UK companies are competitively positioned on the world marketplace
• The supply chain is able to move its money and capabilities anywhere in the world. Work hard and earn the right to be best home for the energy supply chain.
Government support?
The company has received R&D tax credits
Vysus Group at a glance: Key products and services: global energy, engineering and technical consultancy
Main industries served:
• Oil & gas – 55%
• Power & complex industrial – 45%
Headquarters: Aberdeen, UK
Year established: 2020
Number of employees: Circa 650 Revenue: £100m+
Revenue from exports: 70%
Through its newly revitalised Klippon Engineering wing, long-standing connectivity specialist Weidmüller has been re-emphasizing its presence in the oil and gas, hydrogen and process industries over the past few years. With a newly focused sales and engineering team in place, Klippon Engineering is building up the sort of tender pipeline that saw it flourish in the UK between the 1950s and 1980s. The team and network within Weidmüller are also making some impressive strides further afield in the likes of Saudi Arabia, where contracts have established.
Weidmüller has been a household name in the connectivity solutions sphere for a very long time. Weidmüller, when founding its UK operating business all the way back in 1952, chose Klippon Ltd as the company’s name and brand. It largely dominated the the process market through to the 1990s, when it restructured and re-branded back to Weidmüller. In 2019, the decision was made to establish Klippon in the UK once again, placing additional emphasis on partnering with the process industry.
Spearheading the project is Jonathan Lane, Managing Director of Klippon Engineering, who, along with many Weidmüller managers, helped devise the strategy to target the country’s oil and gas, process and hydrogen industries with internally developed and third-party solutions.
It was immediately clear that Klippon Engineering needed, especially for the process industry, which requires a specifically focused and tailored approach, a dedicated team of experts to serve the market. The key aim was
indeed to establish Klippon Engineering as a partner that solves problems as opposed to a supplier of products. For this, Stuart Bell, Vice President of Global Sales, was brought back from his 15-year tenure in the Middle East to UK to be teamed up with Rick West, Vice President of Global Engineering, who is based in Australia.
That meant being given autonomy and developing the ability to source partners and sub-suppliers in order to present bespoke solutions that meet specific client needs, whilst venturing beyond selling Weidmüller products. Indeed, before this strategic decision was taken, the company was missing out on taking work from competing parties as its flexibility and solutions-based approach were slightly lacking.
Establishing a broader engineering capability as a global network within the business has therefore been central to the company’s revival in the UK. Several steps have been taken to this end, its experienced leadership, who know what to look for in engineers that can serve the process industries has actively recruited new colleagues for the key UK activity, established a competence centre in India, as well as achieving umbrella certifications for solutions to enable wider use of products in these solutions to cover client requirements.
Its UK-based and international team of engineers has already expanded thanks to the hiring of more than a dozen people and the company now draws on expertise from networks in the Middle East (UAE and now Saudi Arabia), Malaysia and Canada. Gaining internal buy-in from Weidmüller´s regional organizations and national entities has been critical, with the team meeting key leaders in person to explain the strategy and reassure them that the newly emerged Klippon brand custom is there to support them.
The flexibility to provide solutions which include other manufacturer´s components has already paid dividends. In the Middle East, for example, Klippon has secured first and second phase contracts worth over £1 million to engineer and supply electrical starter panels to key equipment manufacturers – the end user being the national oil company (NOC), which is in the process of upgrading well head systems across its 5000-plus well heads. Their aim is to enhance uptime, optimize production and go digital with central data visualization capabilities, something which Klippon is able to provide by utilizing third party products. Moreover, the NOC will benefit from a reduced need for engineers to carry out manual maintenance work in the desert.
This is just one of several contract wins that helped Klippon, alongside Weidmüller, to generate revenues of €110 million in 2021, up by almost 10% on 2020. What’s more, its tender pipeline is currently worth exceed that and showing even stronger growth since the new strategy has been deployed. In this way, Klippon Engineering as a global network, combining sales, engineering, production and assembly capabilities is helping Weidmüller realize more of the extensive solution opportunities by being both global and local.
By changing tact and pivoting to a solutions-based offering, Klippon has well and truly rediscovered itself in the UK market.
The Weidmüller Group gathers experienced experts to support customers and partners around the world with products, solutions and services in the industrial environment of power, signal and data. Klippon Engineering, which is headquartered in Leicester, is internationally renowned in the field of process engineering, combining over 60 years of engineering expertise with the knowledge and experience of specialists and long-established strategic partnerships in the process industry. On behalf of Weidmüller, Klippon’s offering ranges from connectivity solutions, power and signalling protection products and systems to complete solutions and technologies for communications, retrofit & migration, automation, translation, IoT and data acquisition/analysis. We partner with Asset Owners, EPCs, OEMs, manufacturers of Control Systems, Bulk Suppliers, Systems Integrators and its Hazardous Areas Solution Provider network.
Story type
#service & solutions (main category) #transformation
Benefits
• Secured contract worth over £1m
• Revenue in 2021 grew to €120m (£100m)
Government support?
The company has been supported by the Furlough scheme.
Weidmüller at a glance:
Key products and services: Industrial connectivity solutions.
Main industries served:
• Oil & gas – N/A
• Hydrogen – N/A
• Water / Waste water – N/A
Headquarters: Detmold, Germany (Weidmüller) Leicester, UK (Klippon)
Year established: 1893 (Weidmüller), 2020 (Klippon)
Number of employees: Circa 5,300 Revenue: £822m
Revenue from exports: N/A
How is Wozair
Faced with a volatile oil and gas market that had come off the back of a 2014-15 price crash and was now contracting, specialist HVAC solution manufacturer Wozair was losing revenue, resulting in underlying profitability challenges for the company. In 2016, after becoming aware of the Fit For Nuclear programme via an EIC event, the seed to diversify and transform the business was well and truly planted. Fast-forward to today and, under the stewardship of new CEO John Foley, the company has assured intentions of securing its first real major contract in the nuclear segment in more than a decade, an important step in its bold commitment to doubling its non-oil and gas market income over the next few years.
Back in 2014, Wozair was, and remains so today, a highly respected and trusted supply chain partner to the oil and gas market with highly specialised HVAC solutions catering to a broad range of extreme environment applications.
However, the company was exposed as being too reliant on custom from traditional oil and gas businesses. By the time the height of the mid-decade oil price plunge hit in 2015, it was deriving up to 90% of its income from a sector which was proving to be extremely uncertain – a pattern which has largely continued in the years since.
For Wozair’s leadership, it served as a major wake-up call. Revenues were beginning to slide (by as much as 40%) and healthy profits were turning into losses. A new impetus was needed, and 2016 proved to be a huge turning point.
The catalyst for Wozair’s strategic transformation has been Fit For Nuclear (F4N), which one of its Founders came into contact with thanks to a conversation with a nuclear industry supplier at an EIC event.
Since starting the journey with F4N, the process has transformed the way the company does business and its internal culture, not least in how it has highlighted opportunities to optimise its operations.
While agility and the ability to offer bespoke solutions to clients has been an important part of Wozair’s USP and (and still is), the company has also learned that profitable growth will rely on increased internal and external stability. The opportunity of creating that stability, from how inter-connected the Group products will be in the future, is significant, whilst serving a much broader range of end-markets. Indeed, access to F4N consultants helped to optimise its manufacturing approach, one which is now underpinned by a design for manufacture and assembly (DFMA) ethos. This has also led to the enhancement of internal processes, and development of a clear roadmap for system development, helping to attract and further develop the skills required to thrive,
and indeed using those skills to add more value across the organisation.
Wozair’s mantra and culture now revolves around continuous improvement, as a systems designer and a serious UK manufacturer of highly specialised end-to-end HVAC solutions for a mixture of markets, including nuclear.
The F4N journey lasted five years, during which time the company also boldly invested in three acquisitions to build up its capabilities further. Jet Environmental, a Midlandsbased climate control engineering firm, specialising in landside commercial and industrial applications, was acquired in 2016. Veotec, acquired in 2017, is an air intake and filtration business which has been repositioned by Wozair to also serve coalescers. The final investment was made in 2019 in Thermoplant, a specialist refrigeration and cooling business, not yet integrated within the Group.
The level of ambition and commitment shown by Wozair, now under the leadership of CEO John Foley, has been laudable. Far from being a box ticking exercise, F4N has served as a tool to impart wholesale change for the better, the company going on to venture into the renewable energy sector opportunities such as offshore wind, adopting the Fit 4 Offshore Renewables (F4OR) framework in the process.
And with a commitment to double its non-oil and gas revenues over the next three to four years in place, the momentum being gathered shows no sign of slowing down just yet, with reliance on oil and gas clients reducing from ~90% to 73% between 2015 and 2020. With much work still to do, the journey to profitable growth however is well and truly underway.
Wozair was originally established in the UK in 1986 as Waterloo Air Technology. Following a management buyout by the two partners Paul Azzopardi and Simon Collins of Waterloo-Ozonair in 1995, the name was abbreviated to Wozair in 2000. Since then, the company has expanded quickly into new sectors and internationally, with manufacturing and office facilities in the US and Singapore, and a further office in Dubai. Wozair Group now specialises in the design and manufacture of high-integrity heating, ventilating, air conditioning and refrigeration equipment for offshore oil and gas, nuclear, renewables, marine, petrochemical, pharmaceutical, process and power generation sectors. The company relies on a global reach, over 27 years of established expertise and a reputation for innovation.
#diversification (main category) #culture, #optimization, #resilience, #transformation
• Diversification of clients’ sectors
• Stability valued as part of the company’s culture, optimising processes
• Three major acquisitions
• Seek to hire the best people and empower them to do their job
• The real benefit and learning from F4N has been in the journey and not the outcome
• Support British manufacturing through local supply chain content, delivering the government’s ambitious energy transition goals
The company has been supported by the UK Apprenticeship Levy programme, trade missions and R&D tax credits.
Wozair at a glance:
Key products and services: Wozair Group designs and manufactures high integrity HVAC products and systems including Air Handling Units, Air Conditioning and Refrigeration Systems, Air Intakes, Filtration and Separation, and specialist Fire and Control Dampers.
Main industries served:
• Oil & gas
• Commercial and Industrial
• Nuclear
• Renewables
• Marine / Others
Headquarters: Gillingham, UK
Year established: 1986 Number of employees: 154 Revenue: £24m Revenue from exports: 71%