EIC Inside
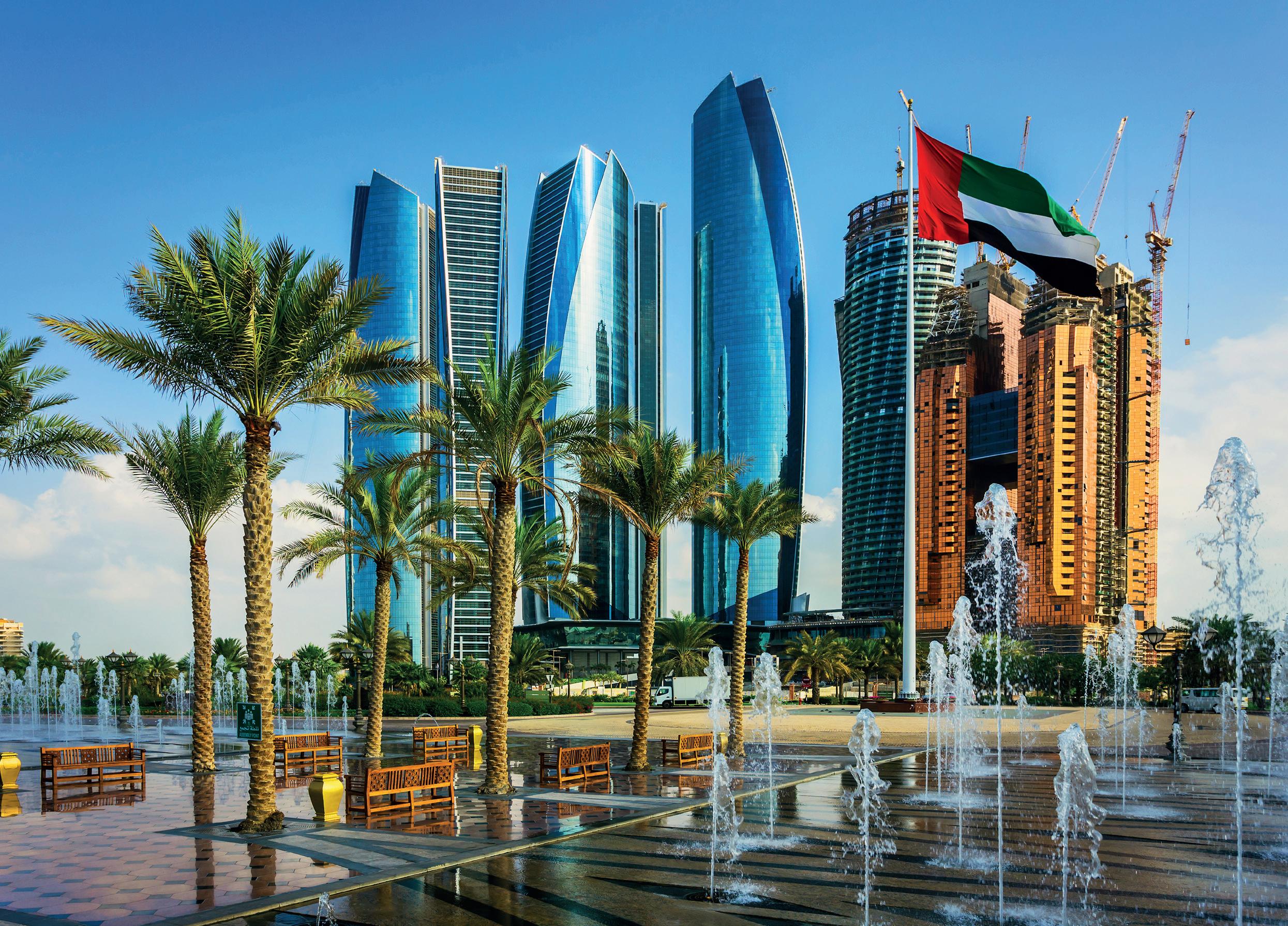
Monthly news for EIC members Special issue
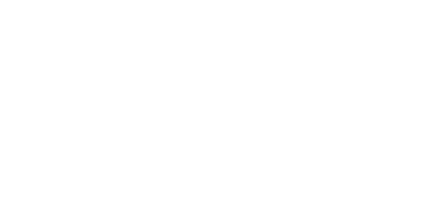
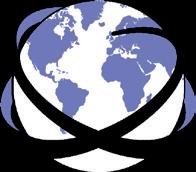


Once a thermal power plant has reached its maximum operational service life, operators will usually have to decide whether to modernise or decommission the facility. Ideally, modernising an aging power plant is more cost-effective and environmentally-friendly than adding new capacity to meet the consumer’s energy demands. A thermal power plant is designed to operate for 30-40 years and usually undergoes two types of aging: physical and technological. Physical aging occurs when equipment wears out over time because of high temperatures and pressures. Technological aging occurs when newer, better equipment renders older equipment less efficient and more costly to operate. Based on data within EICAssetMap, there are currently 466 operational thermal power plants in the Middle East. More than half of these operating thermal power plants (358) have been operating for 20 years or less while the remaining 90 have been operating for more than 30 years.
Outdated thermal power plants would usually face equipment degradation, unsustainable power losses and insufficient system automation. To ensure reliable and efficient operations, modernisation of thermal power plants is strongly recommended for aging thermal power plants. Power plant modernisation could also extend the operational lifespan and enhance the overall performance. In the context of coal power plants, modernisation can also play a crucial role in reducing emissions associated with coal combustion. By incorporating advanced technologies and optimising processes, it is possible to minimise environmental impact while maintaining power generation capacity.
To reduce environmental impact and improve air quality, countries like the United Arab Emirates, Saudi Arabia, Iraq and Iran have adopted several regulations on air quality and emissions to mitigate environmental issues caused by thermal power plants. We need to note that some of these aging thermal power plants ran on heavy oil and this type of power plant will require modernisation in order to improve environmental performance, according to the regulations set by governments. 20% of the thermal power plants operating in the Middle East are oil-fired and a third of these oil-fired power plants have been operating for more than 30 years. Operators will need to decide if an upgrade is economically feasible or if it is more economical to cease operations. We can take the Israeli Reading oil power plant as an example of a power plant which was initially built as an oil-fired plant but was then converted into a gas-fired plant to reduce the amount of pollution emitted by the plant. Recently, the Israeli Ministry of Energy announced that the plant will cease operations and will be converted into a reception site for subsea electricity cable and energy storage facilities.
Typically, a residual life assessment study will be done after 20 years of operations to assess the overall performance of the plant and future plans for the power plants are discussed based on the outcome of the assessment. Modernisation can be done in two ways: either a one-time, complete renovation that temporarily halts operations, or in multiple phases conducted during scheduled shutdowns. The process usually involves upgrading the turbines and boilers, installing advanced control systems and improving air pollution control systems. Many aging power plant units are equipped with ineffective turbines and boilers that can not keep up with the current energy demands. Installation of modern equipment would enhance the efficiency and reduce maintenance requirements. As technology advances, digitalisation and automation are rapidly adopted into power plant control systems to optimise plant operations and performance. This adoption into the control system enables operators to make a data-driven decision as this approach provides a realtime analysis on the overall performance of the power plant.
To see how a thermal power plant conducts its modernisation process, the Al-Mussaib thermal power plant would be a good example for a case study. The plant began operations in 1987 with a generating capacity of 1,200MW from four units. Electricity generation in the state peaked in the 1990’s but then declined significantly in the 2000’s from 9,000MW to less than 4,000MW causing nationwide power outages. Iraq’s National Development Strategy 2005-2007 outlined a plan to rehabilitate its power plants to restore their electricity generating capacity. Siemens was responsible for supplying the control and instrumentation systems, equipment and spare parts for steam turbine generators in the Al-Mussaib thermal power plant. As soon as the rehabilitation was completed in 2014, the plant underwent equipment upgrades for two of its four existing units. The capacity increased to 240MW and 200MW respectively after the upgrade. After the upgrades, maintenance works were conducted in a timely manner to ensure the operations ran without a hitch. The plant has been in operation for 37 years and through a scheduled maintenance programme, it is anticipated that its operational lifespan can be extended by up to 10 years.
EICAssetMap provides valuable information for those involved in the power industry. By offering data on production start dates, capacity and decommissioning status, it helps users make informed decisions about modernising or retiring aging power plants. The platform is a useful resource for anyone looking to stay up to date in the power generation landscape.
Aqilah Shahruddin, Energy Analyst – Operational Assets & Decommissioning aqilah.shahruddin@the-eic.com
Building on 40 years of energy leadership, ADIPEC 2024 returns under the theme Innovation, Action, Impact and once again, the EIC is proud to manage the UK Pavilion at what is arguably the world’s largest and most prestigious energy event.
Over the course of four days, ADIPEC will bring together more than 184,000 attendees from around the globe, including the world’s largest energy producers, governments, contractors and the critical supply chain, all focused on advancing innovative solutions across the entire energy landscape.
Since 2000, our International Trade team has been supporting UK companies at ADIPEC, which has grown from a biennial event to our largest pavilion worldwide, known for delivering tangible returns on investment. This year is particularly special as we celebrate the 20th anniversary of our UAE office, which continues to thrive while supporting our expanding membership across the region.
We are excited to have a presence in Halls 8, 12 and 14, proudly showcasing over 100 companies, including dedicated pavilions from Scottish Development International (SDI) and the Welsh Government. With several contractor briefings and a range of topical panel sessions, the UK Pavilion is once again primed to be a hive of activity.
This is an exciting time for the energy sector, especially in the Middle East, as the region leads innovation in both traditional and renewable energy. With global energy transitions accelerating, new technologies like hydrogen, digitalisation and decarbonisation are creating unprecedented opportunities for growth, collaboration and sustainability across the industry.
Our recently published Middle East OPEX Report highlights an abundance of opportunities across the region.
Whether it’s your first time at ADIPEC or you’re a seasoned veteran, we hope you enjoy the read. Be sure to stop by and visit the EIC team – we’d be delighted to welcome you.
Ryan McPherson
Regional Director, Middle East, Africa, Russia & CIS ryan.mcpherson@the-eic.com
The Abu Dhabi International Petroleum Exhibition & Conference (ADIPEC) takes place from 4-7 November in Abu Dhabi.
The EIC has been managing UK pavilions at ADIPEC for over 20 years, which has enabled us to witness its growth into one of the world’s most influential energy events as well as seeing how UK companies are leading the way by offering innovative products and services renowned worldwide for adding real value to projects and the local supply chain.
There are over 656 energy projects across all sectors under development in the Middle East region from 20242030 with an estimated CAPEX worth over US$1,008bn; ensuring that the Middle East continues to be a key area of focus for companies as we seek to maintain the UK supply chain’s position as a trusted and proven partner in the Gulf region.
We are delighted to announce that 2024 will see UK pavilions in three halls: Hall 8, Hall 12 and Hall 14, spread over 1,500 sq m of floorspace – the largest UK pavilion to date.
We are also thrilled to be welcoming back the Scotland Pavilion and Wales Pavilion in Hall 8 – hosting 26 and 13 co-exhibitors, respectively.
Located in a prime position at the centre of the exhibition halls, the pavilion is a constant hive of activity. The EIC invites its extensive network of contacts to the pavilion to develop bi-lateral trade through the following opportunities:
• VIP Pavilion tours with NOCs and IOCs, in previous years these have included ADNOC, ARAMCO, PDO and SABIC.
• Panel sessions on key topics across the energy sector including ‘Powering Up: Leveraging Digital Transformation and Artificial Intelligence to Achieve Energy Efficiency’ and ‘Clearing the Path: How to Unlock Critical Energy Infrastructure Projects’.
• One-to-one meetings between exhibitors and EPC contractors.
• Contractor presentations from the likes of Kent, McDermott, NMDC, Petrofac and Wood.
• An exclusive networking reception at the ALOFT Hotel, ensuring industry influencers and buyers from across the GCC can network with the UK Pavilion exhibitors in an informal setting.
With thanks to our Pavilion Sponsors:
UK Lounge Platinum
UK Lounge Gold
UK Lounge Silver
UK Lounge Bronze
UK Networking Reception Platinum
UK Networking Reception Gold
UK Networking Reception Bronze
UK Presentation Area Bronze
by Alice Kirker EIC Energy Researcher
Projects announced up until September 2024 have indicated an upward momentum and are on track to catch up with the number of projects announced in 2023
1: New project announcements since 2019 in all sectors in the GCC. Source: EICDataStream
According to EICDataStream the projects announced in the GCC saw a large decline in 2020 compared to 2019, this is due to the impact of the COVID 19 pandemic and the concurrent decline of oil prices. The market recovery in 2021 indicates resilience and adaptability within the region. High oil prices have led to significant profit for national energy companies, providing additional support to the economy resulting in plenty of project investment from government bodies and corporate entities. The increase in energy transition and renewable projects announced since 2019 highlights the regions forward looking approach to clean energy and the energy transition.
The total CAPEX for projects in the GCC expected to come online by 2030 is US$644bn. Upstream projects claim the largest share at 26.76% of the CAPEX share while the lowest is energy storage projects with 0.18% CAPEX share.
Oil and gas projects dominate the landscape in the GCC with 66.52% of the total CAPEX, followed by 9.52% from power projects, 2.65% are transmission and distribution projects, 8.75% are renewable energy projects and 12.55% are energy transition projects.
Energy market overview (2024-2030)
Figure 3: Energy market overview (2024-2030) in the GCC in terms of potential CAPEX spend. Source: EICDataStream
Figure 3 shows that Saudi Arabia, UAE and Qatar each have economies that are highly reliant on the oil and gas sector. Therefore, despite the global energy transition, oil and gas will remain a crucial part of the global energy mix for many years to come.
The growing investment in renewable hydrogen and other emerging clean technologies shows that while this region relies heavily on oil and gas for its economy and energy security, the need to transition to lower carbon economies is also well understood.
Figure 4: Opportunities for oil and gas projects to come online by 2030. Source: EICDataStream
The total estimated CAPEX for the oil and gas sector in the GCC is US$424bn with 248 projects to come online by 2030. These projects are currently progressing through early development phases, consisting of the conceptual design phase, feasibility phase, pre-FEED phase and FEED phase. Meanwhile, over US$282.39bn worth of projects are already advancing through the EPC stage, with US$47.92bn still in the tendering and bidding phase.
Figure 6: Renewable energy capacities (GW) in the GCC (2024-2030). Source: EICDataStream
The total capacity of renewable energy projects to come online between 2024-2030 in EICDataStream is 55.46GW, with 92% of this from solar projects. Saudi is leading with 30.4GW capacity, 54.8% of the total GCC capacity, supporting its target to transition to 50% renewable energy mix in domestic electricity by 2030. However, the current share is only at 3.2% so significant progression will be needed to reach this ambitious target. Oman is currently in a good position to reach its 2030 target of 30% renewable energy, requiring an extra 3GW of capacity which is within reach with the current capacity of announced projects.
Figure 5: Project updates in the oil and gas sector in the GCC. Source: EICDataStream
Jafurah Field Development Phase 4: Aramco is currently tendering an EPC contract for the Jafurah Phase 4 project. The work scope for the EPC contract is said to be similar to Jafurah Phase 3, which involves gas compression facilities. Ruwais LNG Liquefaction Plant: NMDC Group has been awarded the US$200m contract for marine dredging, involving removal of 15m3 of materials across a 15km channel with a width of 145m. ADNOC signed a 15-year long term Heads of Agreement with Indian Oil Corporation Ltd for the supply of 1mmtpa of LNG from Ruwais LNG Liquefaction Plant. Brownfield Development Long Term Agreement Programme: Saipem has been awarded two offshore contracts as part of its ongoing long-term agreement with Saudi Aramco. The combined value of these contracts is around US$1bn.
Figure 7: Power and renewables recent project updates in the GCC. Source: EICDataStream
NEOM Hasma Solar PV Plant: The project will have a capacity of 1.5GW and EPC is expected in March 2025.
Al Khairan IWPP Phase 1: The bids for the EPC package are currently being evaluated, bidders including: Sumitomo Corporation, JV; ACWA Power; GIC, Nebras Power, JV; AH Alsagar & Bros; TAQA; JERA and JV; Abdul aziz Al Ajlan Sons Co; China Power International New Energy Holding Ltd; Malakoff Corporation.
Al Sadawi PV Solar IPP – NTP Round 5: It is understood that the bidders have submitted their respective bids for the project. However, the list of bidders was not disclosed.
Figure 8: Current planned clean tech projects (20242030) in the GCC. Source: EICDataStream
The UAE leads with 19 new clean tech projects, Oman follows with 18 projects and Saudi with 8. In the GCC there are currently 31 hydrogen projects with 71% green hydrogen. Saudi has the most ambitious hydrogen target of 2.9mtpa by 2030, increasing to 4mtpa by 2035 and it is only third in terms of number of hydrogen projects under development. However, NEOM is the largest hydrogen project globally aiming to produce 650 tonnes of green hydrogen per day, making Saudi’s target achievable. Oman’s target of 1mtpa by 2030 is attainable with 14 announced projects. UAE has a target of 1.4mtpa by 2030 followed by a significant rise to 15mtpa by 2040, with 12 projects under development and online by 2030 this should be within reach.
Saudi plans to capture 44mtpa of CO2 by 2035. Jubail Industrial City CCS Hub will extract and store 9mtpa CO2 increasing to 44mtpa in the second phase and should be online by 2027, making Saudi likely to reach its target. Qatar targets 11mtpa by 2035. The Ras Laffan Carbon Capture project and Mesaieed QAFCO 7 Carbon Capture storage project will capture 4.3mtpa and 1.4mtpa respectively. Therefore, to reach the 11mtpa target more projects will need to be announced to be online by 2035. The UAE is likely to reach its target of 10mtpa of CO2 by 2030 with 5 projects expected to be online by 2030.
Jubail Industrial City CCS Hub: It is understood that three bidders have submitted their bids for the EPC contract for the project. The bidders are Saipem, Tecnimont and Larsen & Toubro. The technical bids are currently under evaluation.
Blue Horizons Hydrogen and Ammonia Project: KBR has been awarded the contract to supply blue ammonia synthesis loop technology for the project. The project will have a capacity of 3,000 metric tpd of ammonia. Wood has been awarded the pre-FEED contract.
Dhofar Green Hydrogen Plant – Actis and Fortescue: Hydrom signed agreement for the development of two green hydrogen projects located in Dhofar that are worth US$11bn. The first green hydrogen project will be developed by the consortium of EDF Renewables, J-POWER and Yamna. The project has moved to pre-FEED stage.
EICDataStream is the EIC’s leading project tracking database, containing information on energy projects from the inception stage all the way through to completion. Updated daily by expert analysts in London, Dubai, Kuala Lumpur, Houston and Rio de Janeiro, EICDataStream holds data on over 15,000 active and future CAPEX projects in all energy sectors across the world.
Operator: Wagner Sustainable Fuels Value: US$200m
Wagner Sustainable Fuels is developing a renewable liquid refinery in Brisbane, scheduled to begin construction in 2026. The facility will use LanzaJet’s Alcoholto-Jet (ATJ) technology and LanzaTech’s carbon recycling process. It is expected to produce 0.08 mtpa of SAF and 0.01 mtpa of renewable diesel (RD).
For information on these and more than 15,000 other current and future projects we are tracking please visit EICDataStream
Operator: Hokchi Energy Value: US$1.1bn
Hokchi Energy has received approval from Mexico’s CNH to develop the field in the shallow waters of the Salina Basin. The field development will require an investment of US$1.1bn and is expected online in 2028. The development of the area will entail the drilling of up to 15 development wells that will be connected to four fixed production platforms that will be linked to a FPSO.
Operator: Conexion Energia Value: US$2bn
The developer has secured US$480m in funding for the project. The funds were obtained through agreements with HSBC Hong Kong, Transelec and ISA Inversiones. The financing includes three loans of US$160m each.
Operator: RepAir Carbon Value: US$500m
RepAir Carbon and C-Questra have entered a partnership to develop a Direct Air Capture and Storage (DACS) project in Grandpuits. The facility will entail RepAir’s proprietary DAC technology which relies only on electricity and consumes 70% less energy compared to other DAC methods.
Operator: ExxonMobil Value: US$22.4bn
The project has entered the FEED stage which is expected to last 16 months. Two consortia are undertaking a competitive FEED, Technip Energies with JGC; and Saipem, CPECC and McDermott. One of the consortia will secure the EPC contract following completion of the FEED studies.
Operator: ACWA Power Value: US$1.2bn
ACWA Power has signed financing agreements for three solar PV projects Haden, Muwayh and Al Khushaybi located in the Makkah and Qassim Provinces, with production capacities of 2,000MW, 2,000MW and 1,500MW respectively. The agreements were signed with Buraiq Renewable Energy, Moya Renewable Energy Co and Nabah Renewable Energy Co.
Are you up to date on the latest project developments in the energy market? The EIC’s leading market intelligence database – EICDataStream – contains information on energy projects and associated contracting activity from the inception stage all the way through to construction and commissioning.
• Access details on over 14,000 CAPEX projects across all energy sectors
• Identify business opportunities and inform your business development strategies
• Explore a truly global database, updated daily by an international team of analysts
• Stay up to date with project developments, including information on tenders and awards
• Get insights into what your existing clients are doing and identify potential new clients
• Have a direct interface with analysts for local knowledge and insights
• Access insight and country reports with in-depth data on specific sectors and markets
EICSupplyMap maps the capabilities of supply chain companies that operate across all energy industries.
• These industries cover renewables, oil and gas, power, nuclear and energy transition technologies like energy storage, carbon capture and hydrogen.
• Identify the supply chain local to your region, giving you the opportunity to engage with potential new clients.
• Find the supply chain capability in eight regions, now covering the UK, Germany, UAE, Saudi Arabia, Malaysia, Singapore, US (Texas and Louisiana) and Brazil.
• An in-depth look at profiles of more than 8,800 energy sector supply chain companies.
• Make smarter decisions by targeting your offering to international developers/operators and contractors matching your capability with international energy projects.
To learn more about EICSupplyMap visit www.the-eic.com/MarketIntelligence/EICSupplyMap
with Diveena Danabalan Head of EIC Consult
For over 80 years, EIC has delivered excellence in market intelligence through its award-winning databases: EICDataStream, EICAssetMap and EICSupplyMap. But you can take it a step further with EIC Consult, unlocking deeper, tailored insights into key markets and sectors that fit your business needs. Diveena, Head of EIC Consult, shares how EIC’s newest offering can drive success for your organisation.
Diveena, for those who aren’t aware of EIC Consult, or are new to EIC, tell us what the service offers for our members?
EIC Consult offers bespoke market intelligence, research and consulting services to the entire global energy supply chain. Staying true to EIC’s energy-agnostic approach, we work across all sectors – from oil and gas to renewables, nuclear and hydrogen. Our team of experts has a global reach operating in key energy hubs in Dubai, London, Kuala Lumpur, Houston and Rio de Janeiro.
As an EIC member, you can enjoy significant discounts on our services, including a free day of Consult to help jumpstart your partnership with us. Plus, for a limited time, we’re offering an exclusive discounted week of Consult work for just £1000 – an unbeatable offer to meet your strategic needs.
We also partner with a wide range of non-member companies – from government bodies to SMEs –delivering insights that serve as a powerful tool for navigating the everevolving energy landscape.
What are Consult’s core offerings?
Here’s a quick look at what EIC Consult brings to the table:
1 Market Insights: get the inside track on global energy trends, opportunities and challenges with our deep-dive market intelligence.
2 Custom Research: tailored to your needs – whether it’s project data, market forecasts, or competitor analysis, we deliver research that’s specific to your business.
3 Consulting Services: strategic advice at your fingertips, from market entry and supply chain opportunities to navigating complex regulations.
4 Global Reach: from Europe to the Americas to SE Asia, we provide regional insights that give you a truly global perspective.
5 Real Opportunities: stay ahead of the game with early leads on key contracts and project movements. Our confidence ranking and certainty analysis cuts through the noise, so you don’t have to. We do the heavy lifting – sorting through the data to deliver only what matters most.
Our real advantage? It’s all backed by our in-house data and expert team.
And why should companies choose to work with Consult?
Companies should partner with Consult because we’re driven by one goal: helping you uncover real business opportunities. Our track record speaks for itself – whether it’s guiding companies to successfully set up offices abroad, spotting untapped opportunities in new sectors, or providing neutral, expert insight for strategic planning. We’re here to fuel your success.
Can you give us an example of work that you’ve provided for a client and the outcome from it? You mentioned that there have been successes?
Absolutely. One of our top success stories this year features a global technology provider headquartered in Europe. The company turned to us for a comprehensive look at CAPEX and OPEX opportunities in the nuclear, CCUS and hydrogen sectors across the US and Canada, a clear view of their competitors, market entry requirements, local partners and marketing channels. Our tailored reports validated North America as the perfect market for them, leading to the exciting outcome of opening a new US office – a milestone we’re thrilled to have contributed to.
RMI clinic opens in Guyana capital to support offshore industry and local community
RMI, which specialises in saving lives and protecting the health and wellbeing of workers on remote and diverse sites across the world, has officially opened a new clinic providing medical services to offshore and onshore workers in Guyana.
The fully stocked clinic, opened in the capital city of Georgetown, is acting as a central in-country medical solution to the country’s rapidly expanding petroleum, construction and manufacturing industries.
Owned, managed and staffed by local Guyanese nationals, RMI’s clinic boasts a dedicated medical team comprising onsite doctors, nurses and medics. This team delivers tailored solutions to meet the demands of RMI’s offshore client’s and can offer a range of services including acute care, OEUK medicals, Liberian medicals, drug and alcohol testing, physical agility testing and more.
With RMI’s expertise, the centre will run to the highest clinical standards, employing 20 Guyanese medical professionals who are eager and determined to provide substantial care to the region.
The opening of this new clinic is a great step forward in providing essential medical services that will support Guyana’s growing industries.
Long transit times between the shore and clinical locations has put great strains on the operational continuity of these industries but we are confident that this new clinic will be a much welcome solution.
With our highly skilled staff in operation, the clinic will become a vital asset to organisations across Guyana, providing health and fitness screening solutions and working as a convenient triage centre in an ideal location close to industrial activity. This clinic will bring a vital service to the people of Guyana while simultaneously supporting the economic potential of the country.
Jules Rawles, Vice President Business Development, RMI
Founded in 2003 as a medical training company, RMI has become a bespoke solutions partner managing risk through medical, security and HSE services in complex environments around the world. The company has been providing medical services globally since 2006.
Saudi Arabia has a strategy to reach net zero by 2060 and is relying on modern, highly efficient gas-fired power plants in combination with CO2 capture and storage, to significantly reduce its emissions. Siemens Energy is supplying key power plant technologies that will provide almost 4GW to the Kingdom, and in addition has also entered a longterm maintenance contract for 25 years for the two power plants, with a total value of approximately US$1.5bn.
Taiba 2 and Qassim 2, two of the world’s largest, modern and efficient combined-cycle power plants, will be built in the western and central regions of Saudi Arabia over the next few years. Siemens Energy’s gas turbines (HL-class), in combination with steam turbines and generators, will generate approximately 2,000MW of electricity at each site. EPC and contracting partner for Siemens Energy is China Energy International Group.
The new power plants will provide additional energy for the country’s growing population and booming economy and replace parts of Saudi Arabia’s existing aging power plant fleet, some of which rely on oil as an energy source. The new plants will save up to 60% of CO2 compared with oil-fuelled power plants.
They will also be compatible with the Kingdoms’ energy strategy which calls for the construction of CO2 capture and storage facilities in the medium term, to enable a carbon-neutral energy supply.
Taiba 2 and Qassim 2 will initially be connected to the grid in simple cycle mode in 2026 and will be permanently operated as a combined cycle power plant one year later.
Siemens Energy is one of the world’s leading energy technology companies. The company works with its customers and partners on energy systems for the future, thus supporting the transition to a more sustainable world. With its portfolio of products, solutions and services, Siemens Energy covers almost the entire energy value chain – from power and heat generation and transmission to storage. The portfolio includes conventional and renewable energy technology, such as gas and steam turbines, hybrid power plants operated with hydrogen and power generators and transformers. An estimated one-sixth of the electricity generated worldwide is based on technologies from Siemens Energy. Siemens Energy employs around 99,000 people worldwide in more than 90 countries and generated revenue of €31bn (US$33.6bn) in fiscal year 2023.
NEW PRIMARY MEMBER
Apave
Apave TIV, 105 Al Rawabeh Building
Sheikh Zayed Road Al Quoz 1 PO Box 282229 Dubai, UAE
Contact Aubrey Alba, Communication Correspondent for Middle East & India, Apave Group
Telephone +971 4 330 6116
Email meenquiry.bue@apave.com
Web https://middle-east.apave.com/
Apave is present in the Middle East in over 6 countries, with more than 10 offices. With its inspection activities (regulatory and non-regulatory), training, consultancy and technical support, certification and testing and measurement, Apave covers all its customers’ risk management needs. This presence enables the company to mobilise the appropriate skills throughout the Middle East. Wherever you are, Apave is ready to meet your needs with tailor-made solutions.
NEW PRIMARY MEMBER
Atlas Copco
Technology House
Hemel Hempstead Industrial Estate Hemel Hempstead HP2 7DF UK
Contact
Stuart Breadon, Oil and Gas Sales Manager
Telephone 0800 181 085
stuart.breadon@atlascopco.com
Web www.atlascopco.com/en-uk/ compressors
Atlas Copco Compressors
With over 150 years of experience in compressed air and industrial gas solutions, Atlas Copco’s products meet the applications, process needs and specific requirements of the energy sector.
In addition to its range of air compressors, air dryers, N2/O2 generators, N2 boosters, coolers/ chillers, the company is also able to offer a range of CO2 screw, piston and centrifugal compressors with CO2 dryers for CCS applications and also for the oil and gas onshore/ offshore sectors.
Atlas Copco supplies containerised hydrogen compressors using piston and hydraulic booster technology to meet the mobility, refuelling and process/chemical industries.
Busch
Hortonwood 30
Telford
Shropshire TF1 7YB UK
Contact
Craig Johnston, Head of Market Management –Energy & Environmental
Telephone +44 (0)1952 677 432
Email craig.johnston@busch.co.uk
Web
www.buschvacuum.com/global/en/
Busch Vacuum Solutions is recognised as the market leader in industrial vacuum pump and overpressure solutions for the energy and environmental market segments.
Busch has extensive knowledge and experience in supplying innovative vacuum solutions into markets such as oil and gas, chemical, power, hydrogen, waste water, carbon capture and renewables.
Together with Pfeiffer under the umbrella of the Busch Group, Busch manufactures the widest range of vacuum and overpressure technologies, as well as leak detectors, for a wide variety of applications. Busch’s innovative solutions are tailored to meet client-specific requirements and industry standards.
43 New Street Port of Spain
100921
Trinidad and Tobago
Contact Sean Patience, Managing Director
Telephone +868 223 7447
Email sean.patience@cargotrinidad.com
Web https://cargotrinidad.com/
Cargo Consolidators Agency Ltd (CCA) has developed into a full service freight forwarding, logistics and consolidation company with three other members under its umbrella:
CCA Guyana Inc, Guyana. Fast Flow Inc, Miami, US. Action Worldwide Services, Houston, US.
22/2 Pakorn Songkhraorat Road
Tambon Map Ta Phut Amphur Muang Rayong Rayong 21150 Thailand
Contact Ekkapop Phienlumlert, Division Manager, Project Marketing & Business Development
Telephone +66 (0)3897 7800
Email ekkapop.p@pttgcgroup.com
Web https://gcme.co.th/
GC Maintenance and Engineering Company Limited (GCME) is a Thailand-based enterprise specialising in the provision of engineering and maintenance services, with a particular focus on project execution within the oil and gas, petrochemical and energy sectors. The company offers an extensive array of engineering solutions, including: conceptual design; front end engineering design (FEED); engineering, procurement, construction and commissioning (EPC); EPC management services (EPCm); project management consultancy (PMC); plant engineering services and manpower supply.
GCME also has expertise in plant inspection and maintenance, employing a team of highly skilled engineers who have consistently delivered excellence to esteemed clients across diverse industries. The company’s experience spans refineries, aromatics, olefins, gas processing, phenol, vinyl chloride monomer (VCM), polyvinyl chloride (PVC) and polylactic acid (PLA) facilities.
GCME’s unwavering commitment to professional excellence and industry-specific knowledge has established it as a distinguished leader in the engineering and maintenance sector.
Lot 6073 & 6074
1st & 2nd floor, Block 11
Kuala Baram Land District
Jalan Tudan, Bandar Baru Permyjaya
98000 Miri, Sarawak
Malaysia
Contact Kenny R Ngalin, Managing Director
Telephone 085 491 780
Email kenny@ovgroups.com
Web www.ovbhd.com
Ocean Vantage (OV) is a leading publicly listed Malaysian (Sarawakbased) energy and oil and gas services company, with a diverse portfolio spanning several key industry segments and expanding internationally.
OV, through its subsidiaries, provides comprehensive integrated solutions that address the varied needs of its clients from manpower supply, engineering, procurement, construction and commissioning, inspection testing, rope access services, renewable energy, habitat supply to production solutions.
Ocean Vantage is dedicated to delivering innovative, high-quality services that drive value and sustainability in the energy sector and beyond.
AIS, a global supplier of advanced manufacturing solutions, has announced the acquisition of GAP Plastics, a UK-based specialist in custom plastic injection moulding.
GAP Plastics serves a diverse range of industries including energy, cosmetics, glazing and textiles, and is known for its dedication to producing highprecision plastic components.
The acquisition of GAP Plastics marks a significant milestone for AIS as we continue to broaden our capabilities and market reach.
Andrew Bennion, CEO, AIS
Through this acquisition, AIS will integrate GAP Plastics’ advanced manufacturing technologies and processes into its existing operations. The combined expertise will allow AIS to provide an even broader range of solutions, while maintaining the high standards of quality and precision that both companies are known for.
GAP Plastics will continue to operate under its established brand name, with its current leadership and workforce remaining in place to ensure a seamless transition and continuity of service for its customers.
AIS is a global leader in the engineering and manufacture of a range of innovative protection products for the energy industry. The company serves a global clientele across a range of industries, with solutions that perform in the world’s most challenging environments.
UK-headquartered logistics and materials management company, ASCO, has completed a six-figure contract with Onslow Marine Support Base (OMSB) in Western Australia, supporting the offshore decommissioning sector, in particular utilising its radiation expertise.
As part of the contract, ASCO mobilised two radiation safety officers (RSOs) as well as NORM (Naturally Occurring Radioactive Material) and mercury monitoring and analysis equipment to the OMSB site.
The RSOs delivered onsite training for NORM awareness, and monitoring for various hazards such as benzene, H2S (hydrogen sulphide) with a particular focus on NORM and mercury.
The project was led by senior RSOs John Davidson and Robin Small, who together boast 25 years of expertise in the field. The RSOs helped to optimise the site, ensuring that supervised areas were set up correctly and any contaminated materials were properly managed and contained. The team enhanced OMSB’s management plans and risk assessments, ensuring top-tier radiation management and site safety operations.
Our work in the North Sea has the way in global decommissioning activity for a number of years now and we’re excited to bring that experience Western Australia.
ASCO has had a presence in Australia for more than 13 years, in Perth, Darwin and Dongara, but this contract represents the first time it has delivered NORM services in the southern hemisphere. The project demonstrates ASCO’s capability and establishes credibility in this segment, enabling ASCO to confidently invest to deliver further large-scale projects of this nature in Australia.
ASCO is predicting continued growth in the region as it maximises the opportunities of decommissioning Australia’s aging oil and gas infrastructure.
led decommissioning and experience to
DNV, the independent energy expert and assurance provider, has announced the conclusion of the first phase of DNV’s HVDC Standards joint industry project (JIP). The JIP was convened to identify deficiencies in standards for High Voltage Direct Current (HVDC) transmission systems.
Because of the expected growth of electricity demand as data centres expand and transportation and buildings electrify, paired with the influx of new renewable generation, the US electric grid requires expansion and modernisation. Implementing HVDC transmission is a viable method to increase the capacity, reliability and resilience of the system, but, as it has not been widely adopted, there is a lack of relevant standards.
In the first stage of the joint industry project a high-level survey was conducted to identify the standards and codes needed to implement HVDC transmission systems in the US. Four types of standards emerged as priorities: performance/grid code; manuals for regional transmission organisation (RTO) and independent system operators (ISO); utility interconnection manuals; and offshore design requirements. Some functionalities, such as active power control, reactive power control, fault ride-through, dynamic voltage control and frequency control, have been at least partially addressed in the existing US Grid Code (eg IEEE 2800-2022, FERC LGIA, NERC RSBES and relevant OATT). However, several other functionalities, including control modes, islanded operation and adaptive control are not covered. Even for those functionalities that are included in the US Grid Code, there remain significant gaps.
Over the next three years DNV and JIP partners, which include Atlantic Shores Offshore Wind, EDF Renewables, Equinor, Invenergy, National Grid Ventures, Ocean
Winds, PPL TransLink WindGrid, RWE, Shell and TotalEnergies, will delve deeper into the identified gaps, focusing primarily on the first three types of standards. These standards focus on setting formal electrical standards or rule makings for RTOs and utilities. This work will consist of three distinct phases, each roughly a year in length. During the first year, DNV, JIP participants, and an advisory committee will conduct a granular HVDC standards gap analysis and prioritise the relative importance of the identified gaps. In 2025 and 2026, study participants will establish and implement a plan to address the identified gaps. These recommendations will likely include proposals to initiate NERC SAR or IEEE PAR proceedings and updates to RTO rules and offshore wind solicitation requirements.
i
For more information: www.dnv.com
ICR Group, a global leader in maintenance and integrity solutions, together with its regional partners, has secured US$3.5m in contracts in the Middle East over the past six months.
ICR’s flagship brand, Technowrap, has been instrumental in driving growth in the Middle East. The increasing interest highlights the commitment to extending the lifespan of critical assets without the need to shut down.
Technowrap provides a long-term alternative to traditional steel replacement, often with a design life of up to 20 years. The quick application can significantly reduce downtime, leading to cost savings, while offering up to a 66% reduction in carbon emissions.
Technowrap is valued for its versatility and efficiency as it can be used to repair a wide range of infrastructure, including pipelines, pipework, tanks, vessels and structural components, both onshore and offshore.
ICR’s operations are supported by its Abu Dhabi office and strategic partner agreements, enabling local service delivery of the product range across the Middle East.
Recent projects in the Middle East have included work on offshore and onshore installations for operators and engineering contractors repairing pipelines, pressure systems and structures.
Notably, Technowrap has been used in a critical subsea repair project on a 48-inch pipeline, where its ability to withstand harsh conditions and extend the life of infrastructure is crucial. ICR also supports similar onshore pipeline repairs and is developing new products for 2025 to further enhance its offerings.
The proven reliability of our products and services positions ICR to enhance operational efficiency and protect critical infrastructure, all while minimising environmental impact.
Jim Beveridge, CEO, ICR
To further complement the Technowrap range, ICR also offers non-destructive composite inspection technique called INSONO. It has been developed to validate the condition and integrity of composite repairs, giving operators and regulators confidence in the application and long-term performance. The technology can detect anomalies in the bond line and interlaminar dis-bonds within composite repair material, supporting life extension.
Quickflange, permanent flange-topipe connectors, from 2” to 14”, is another core offering that addresses scenarios where traditional welding solutions are impractical due to hot work constraints or time limitations.
ICR is exhibiting at ADIPEC this year (4-7 November) stand 6210.
John Crane, a global leader in mission-critical flow-control technologies and a business of Smiths Group Plc, has been awarded a substantial, multi-year Gas Seal Management Programme (GSMP) contract from SK Advanced, a major producer and seller of propylene, located in Ulsan, South Korea.
John Crane already provides SK Advanced with its entire installed base of dry gas seals. These mechanical seals are critical pieces of machinery embedded within the heart of a wide variety of industrial processes, ensuring the safe and efficient flow of gas and preventing contamination.
The latest GSMP contract is to provide maintenance and refurbishment of these seals. Maintaining dry gas seals in the field can be difficult due to the harsh environments in which industrial processes operate. John Crane’s maintenance programmes help preserve and extend the life of equipment, increase reliability and avoid unscheduled down time, leading to better productivity.
The maintenance programme is gearing up to two significant turnaround events for SK Advanced. These are scheduled events where a process unit of the industrial plant is taken offline for maintenance, inspection and upgrades. For SK Advanced, 10 of its dry gas seals are scheduled for turnaround in 2024, and another 10 four years later, in 2028.
Propylene is an organic compound used widely in the packaging, consumer products and automotive industries. The global demand for propylene is expected to grow in the coming period driven by demand in key markets including the US, China and India.
With the changes proposed in the NSTA’s consultation on the draft OGA Plan to reduce UKCS GHG emissions, there is a strong case for the societal cost of carbon and potentially an individual asset marginal abatement cost to form part of the project economics for decarbonisation projects.
Graham Filsell, Asset Decarbonisation Lead, Kent
Kent and the Energy Institute have announced a new collaborative effort to create comprehensive guidelines for decarbonisation economics in greenhouse gas (GHG) emission reduction projects in the upstream oil and gas industries. This report will provide clear, actionable guidance to help the sector achieve its environmental goals.
The guidelines, prepared under the expert guidance of Graham Filsell, Kent’s asset decarbonisation lead, will focus on demystifying the economics of decarbonisation.
The scope of this study focuses on the UK North Sea upstream sector but is intended to serve as a basis for future research globally. The guidelines will address the following key objectives:
Demystifying decarbonisation economics: Provide clarity for energy professionals with limited exposure to project economics, such as environmental or sustainability managers.
Understanding carbon costs: Offer insights into how carbon costs are calculated and influenced by market forces, including societal costs.
Alternative metrics: Recommend non-standard metrics beyond NPV to ensure that decarbonisation goals are met, delivered as a technical note to the industry.
Justification of metrics: Articulate and justify the choice of both standard and non-standard metrics used.
Upstream O&G value chain: Focus on the upstream sector of the O&G value chain affected by decarbonisation and assess the potential to broaden the scope to the full value chain.
The interdisciplinary process to develop these guidelines will involve the collaboration of Kent’s environmental team, asset decarbonisation team and energy environment economic (E3) modelling and communications team:
Environmental team: Providing guidance on the UK Carbon Budget and other GHG regulations through comprehensive review and evaluation of regulatory risk levels.
Asset decarbonisation team: Maintaining up-to-date knowledge of industry legislation and best practices for decarbonisation, developing marginal abatement curves and incorporating regulatory risk to calculate the unavoidable abatement greenhouse value (UAGV).
E3 modelling and communications team: Guiding the valuation of GHG emissions and demystifying decarbonisation economics by estimating metrics to benchmark the UAGV.
This collaboration marks a significant step toward achieving the environmental objectives of the North Sea Transition Deal and ensuring that the UK North Sea upstream oil and gas sector can continue to operate with the lowest possible environmental impact.
i For more information: https://kentplc.com/
Mott MacDonald, the global engineering, management and development consultancy, has supported Holtec Britain to complete the first step of the generic design assessment (GDA) for its small modular reactor SMR-300 in record time.
The GDA is a voluntary process adopted by technology vendors to de-risk new nuclear reactor designs for future project stages. The process allows UK independent nuclear regulators – the Office for Nuclear Regulation, the Environment Agency and Natural Resources Wales – to assess the safety, security and environmental implications of new reactor designs and to provide the confidence that designs will meet the UK’s statutory regulatory requirements.
Mott MacDonald supported Holtec Britain throughout the GDA process to complete in 10 months – 15% faster than anticipated and as much as 65% faster than any previous GDA. Having previously supported Holtec Britain to secure a matchfunded £60m grant funding from the UK government’s Future Nuclear Enabling Fund for the GDA, Mott MacDonald has been providing safety, engineering, environmental and
regulatory support to Holtec Britain throughout the GDA process. The fully integrated team has participated in more than 200 engagements with the UK regulators to date.
The SMR-300 design will now enter the second step of the GDA process, which involves fundamental technical assessment by the UK regulators. This is the first ever two-step GDA, marking a major milestone towards Holtec Britain’s ambition of deploying a fleet of SMRs in the UK by 2050 to bring reliable and affordable electricity and heat to UK households, businesses and industrial users, with first operation planned for the early 2030s.
SMRs are nuclear fission reactors designed to be built at a smaller size, but in larger numbers than the world’s current nuclear fleet. They are cost competitive and considered to be more versatile, scalable, sustainable, financeable and efficient. With wider-ranging applications such as generation of industrial heat and hydrogen production, SMRs are well placed to help the UK government achieve its ambition of generating 24GWe of nuclear capacity by 2050.
Roughly the size of two football fields, with production capacity of 300MWe per unit, Holtec’s SMR-300 is a first-of-its-kind advanced SMR, offering safe, reliable and economical carbon-free power.
For more information: www.mottmac.com
NRL’s recruitment teams across the UK and internationally are celebrating being shortlisted for two Global Recruiter Awards.
Celebrating over four decades in the recruitment industry, NRL’s engineering solutions captured the attention of the judges to secure nominations for Best UK Overseas Operation and Best Large Recruitment Business.
Within the award submissions, NRL reflected on its commitment to compliance in the heavily regulated engineering sectors, as well as the innovative recruitment and mobilisation solutions it develops for clients across the UK and internationally. With 33% of colleagues across the NRL Group having worked within the business for more than a decade, the industry expertise accumulated and company ethos to never be complacent helps NRL to deliver large-scale recruitment campaigns for clients and tackle complex global compliance challenges.
With 17 award categories in total, the winners for each will be revealed at the industry awards ceremony on Wednesday 20 November at The Steel Yard, London.
For more information: www.nrl.co.uk
This is a huge stride forward. One of the reasons for the successful completion of the Step 1 GDA in record time is down to the team’s dedication and meticulous preparation. Mott MacDonald’s significant experience from previous GDAs and understanding of the UK context and regulatory expectation made this possible.
In 1979, Dr Michael R Oliver embarked on a journey that would redefine the landscape of valve manufacturing. Founded in a modest garage, Oliver Valves began with a vision to innovate and excel in engineering. Dr Oliver, a graduate mechanical and production engineer, developed the company’s inaugural range of needle valves, laying the cornerstone of what would become a global leader in the industry.
Over the past four and a half decades, Oliver Valves has transformed significantly, evolving from its humble beginnings to operate from four state-of-the-art facilities in Knutsford, Cheshire. The company’s footprint now extends across the globe, serving clients in approximately 50 countries and shipping its products worldwide.
Key milestones punctuate Oliver Valves’ journey of growth and achievement. In 1982, the British Gas Corporation’s approval of Oliver needle valves for gas transmission systems marked a significant endorsement of the company’s quality and reliability.
Subsequent milestones, such as the development of high-pressure instrument ball valves in 1985 and the establishment of international offices in Aberdeen, Houston, Kuala Lumpur, Singapore and Dubai in 1990, solidified Oliver Valves’ position as a global player.
A pivotal moment arrived in 2004 with the launch of Oliver Valves India, strategically enhancing the company’s supply chain capabilities and bolstering its presence in emerging markets. This expansion underscored Oliver Valves’ commitment to meeting global demand while maintaining the highest standards of engineering excellence.
Central to Oliver Valves’ success is its relentless pursuit of innovation. The company’s commitment to research and development has yielded groundbreaking products such as the Double Block and Bleed valves and the Twinsafe valve series, setting benchmarks for safety and performance in the industry.
Throughout its history, Oliver Valves has forged enduring partnerships that have contributed to its success. Partnerships with longstanding distributors such as AWC in the US and suppliers like Dupont have been integral to supporting Oliver Valves’ global operations and ensuring the delivery of high-quality products to customers worldwide.
Oliver Valves’ journey has been defined by innovation and excellence. As we commemorate 45 years, we look forward to building on our legacy and shaping the future of our industry.
Dr Michael R Oliver, Chairman, Oliver Valves
Under the stewardship of Dr Michael R Oliver, chairman and founder, Oliver Valves has cultivated a culture of integrity, customer focus and continuous improvement. His leadership has been instrumental in navigating the company through dynamic market landscapes and technological advancements, ensuring Oliver Valves remains at the forefront of innovation.
Looking ahead, Oliver Valves remains steadfast in its commitment to driving innovation and delivering exceptional value to its global clientele. As the company celebrates 45 years of achievements, it embraces new opportunities for growth and expansion, while staying true to its founding principles of quality, reliability and customer satisfaction.
OPITO, the global safety and skills organisation for the energy industry, has launched a new standard to ensure increased competency and safety around helideck activity, benefiting the global offshore workforce reliant on safe transfers to energy installations in an open sea environment.
The new Helicopter Administrator Workplace Competence Assessment standard complies with the best practice and requirements for helicopter administrators as detailed in the Civil Aviation Authority’s Civil Aviation Publication CAP 437: Standards for offshore helicopter landing areas (CAP 437).
It assesses the candidates’ knowledge and skills in providing administrative support required to safely operate the helideck and manage helicopter movements within their role in the workplace. The Helicopter Administrator Workplace Competence Assessment will be undertaken in the candidates’ workplace and consists of five units.
Created in conjunction with Offshore Energies UK (OEUK) and wider industry in response to a previous amendment to CAP 437, this standard follows the introduction of OPITO’s Helicopter Administrator Training standard, launched in March 2023.
During development of the new standard, OPITO and OEUK engaged closely with industry stakeholders, including Spirit Energy, Harbour Energy, HCA, bp, Repsol Resources UK, TAQA and TotalEnergies, to ensure employer needs were met.
Operating for over 50 years, OPITO is an industry-owned organisation that works with governments and industry worldwide. i
OsecoElfab’s new LoKr rupture disc represents the next generation of design and engineering in pressure relief technology. The innovative design enables a higher relief capacity across all sizes compared to other reverse acting discs. This maximises pressure relieving performance and safety without having to adapt piping.
The disk’s architecture has been refined and optimised to improve performance in three key areas: keeping pressure drops in relief lines to an absolute minimum, providing enhanced reliability and accuracy and being suitable for the widest range of pressures, temperatures and line sizes possible.
The reverse-buckling disk combines a dimple on the disk with an innovative knuckle on the holder to offer full-bore opening with exceptionally accurate burst ratings. This enables a higher flow rate on burst than previously possible. This higher free flow area allows plant managers to upgrade their pressure safety equipment with minimal disruption as there is no need to increase line sizes.
Since its initial launch in the US in 2022, the LoKr rupture disc has proven popular and is now improving plant performance in hundreds of installations across the country. With receiving the CE mark, the LoKr is certified under both the US ASME Code and European Pressure Equipment Directive, demonstrating its suitability for global installation.
Global cable and pipe seal manufacturer Roxtec is bolstering its industry and infrastructure team with the appointment of George Light as Data Centre Market Manager for the United Kingdom.
George joins Greater Manchesterbased Roxtec Ltd after spending the past 15 years running his own business in the international data centre industry. George brings a wealth of experience within the IT infrastructure, design and installation sphere. A strong communicator, he has closely collaborated with mechanical and electrical contractors and appreciates the time pressures and build phases that often require swift action to overcome any pressing issues.
We’re delighted to welcome George to Roxtec to drive growth in one of our key sectors. We’ve seen significant demand in data centres over the last 10 years and that is being supercharged by AI. As a result we’re already working with some of the biggest tech firms in the world across multiple projects in the UK and Ireland which George will be supporting.
Clive Sharp, Managing Director, Roxtec Ltd
In his new role, George will be responsible for expanding Roxtec’s product offering while working closely with design houses, mechanical and electrical engineers and data centre owners. The role will also involve identifying ambitious new business opportunities within larger scale data centres, where Roxtec’s products can be seamlessly integrated as part of the IT infrastructure. Additionally, he will nurture existing relationships and provide advice and support to ensure Roxtec’s clients continue to receive the highest levels of service for their project needs.
Roxtec’s cable and pipe seals have achieved a two-hour fire rating certification for use with Euroclad panels. They also offer bespoke solutions for underground pits and roof top entry points which provide users with the guarantee that they are protected from multiple hazards.
Roxtec was founded in Sweden in 1990 and is active in more than 80 markets worldwide.
Sonihull has announced the successful installation of its ATEX and IECEx approved ultrasonic antifouling systems on New Fortress Energy’s FSRU, the Energos Winter, in Brazil. Over the past six months, Sonihull worked closely with New Fortress Energy and provided them with a turnkey solution to protect the ship’s main circulating seawater system, seawater pipeline, filters, heat exchangers and turbo generator condensers from bio-fouling, scaling and build-up.
The company utilised 20 of its advanced Agitate Pro systems and for the regasification chambers, its ATEX and IECEx approved transducers were installed in hazardous zones, with control panels mounted within Ex d enclosures for optimal protection.
Sonihull is a pioneer in achieving ATEX and IECEx approval for ultrasonic antifouling systems, with over 220 certified transducers in operation globally. Its systems effectively prevent marine growth and scaling in various industrial applications, including heat exchangers, condensers, pumps, filters, pipes and cooling systems.
Sonihull looks forward to seeing the enhanced performance of the Energos Winter and continuing its collaboration with New Fortress Energy. i For
Testing front and backsheets according to IEC 62788-2-1:2023-08 can take a very long time. Some long-term tests involve 5,000 test hours and run for up to 30 weeks. There is currently an oversupply of PV modules on the market. To avoid bottlenecks in the future, it is crucial for manufacturers to understand and comply with this new standard and to have the front and back sheets tested early in the project.
Roman
Brück, Solar and Testing Expert, TÜV Rheinland
Since October 2023, photovoltaic (PV) modules need to meet new safety requirements in accordance with the revised IEC 61730-1 and -2 standards. The changes include electrical safety and fire safety under mechanical and environmental stress. One significant change is the use of front and backsheets. These are the covers of a PV module that protect the module from environmental influences such as moisture, dirt or mechanical stress, thus reducing the risk of short circuits or fires.
For module certification, it is now necessary to qualify the front and backsheets used in accordance with the IEC 62788-2-1:2023-08 safety standard. However, many front and backsheet manufacturers still have some catching up to do, which is delaying the overall certification of PV modules to the new standard.
WIKA supports the digitalisation of gas-insulated switchgear with the new model GD-20-W gas density sensor. The wireless device with integrated battery and radio module allows for easy integration into IIoT environments. The sensor communicates the values measured for gas density, temperature and pressure via the LoRaWAN® network protocol. The device also features an alarm function for the three parameters as well as for the battery status that signals, independent of the preset transmission cycle, that a limit value has been reached.
As a compact wireless device, the model GD-20-W is particularly suitable for retrofitting existing installations operated with SF6 gas or alternative insulating gases.
The installation and maintenance effort is low. The battery life is over ten years, depending on the measuring and transmission rate.
The sensor calculates gas density from the pressure and temperature values. It measures the pressure at 20°C with an accuracy of ± 0.2%. The device monitors gas density continuously and thus allows demand-driven asset maintenance.
i
Wood, a global leader in consulting and engineering, is advancing three carbon capture and storage (CCS) projects on the Norwegian Continental Shelf.
The company has successfully assessed the technical feasibility of the Trudvang, Luna and Havstjerne CCS projects, which combined can store up to 21m tonnes of CO2 annually, the equivalent of nearly half of Norway’s total CO2 emissions in 2023 (46.6m tonnes).
Wood’s comprehensive technoeconomic assessments – the method for evaluating the economic performance of technology – have laid the groundwork for sustainable CO2 transportation solutions, enabling the projects to progress to the next stage of development. The assessment included cutting-edge flow assurance simulations, development of CO2 specifications, specialised subsea field layouts and innovative marine loading and offloading solutions.
The CCS licenses are owned by Sval, Storegga and Vår Energi (Trudvang), Wintershall Dea and Total (Luna) and Wintershall Dea and Altera (Havstjerne). Wood’s technical experts from Stavanger, Sandefjord, Galway, Aberdeen and Reading are working together to deliver these scopes.
i For more information: www.woodplc.com
We want to use every opportunity to connect with our members, so please follow us on Twitter (@TheEICEnergy) and connect with us on LinkedIn –EIC (Energy Industries Council)
Below you’ll find a selection of some of the exciting EIC activities and useful industry information we’ve shared through our social media channels.
AEG Power Solutions (AEG PS), global provider of power systems and solutions for all types of critical and sustainable applications, has introduced a new range of uninterruptible power supply (UPS) systems, which feature a full IGBT architecture and industrial-grade build quality to provide a safe power backup to protect refining and petrochemical industries, transportation infrastructures, manufacturing and other critical businesses against all power disturbances.
EIC (Energy Industries Council)
The EIC Country Report: Kingdom of Saudi Arabia (KSA) offers a detailed analysis of market trends and opportunities in Saudi Arabia. Read the full report here https://lnkd.in/eTBksbGh
Protect 8 PLUS supports a standard three-phase input and is available as single-phase or three-phase output from 10 to 40 kVA, with 216 Vdc or 384 Vdc battery voltage. By the end of the year, it will also support 60 to 120 kVA in both configurations.
EIC (Energy Industries Council)
The new Middle East OPEX report shows that the region is set to invest US$75.63bn in renewable energy projects over the next five years. Visit https://lnkd.in/eTBksbGh
Thanks to its IGBT rectifier, the system offers a high input power factor of up to 0,99 and very low harmonic current rejection on the input side (THDi) which makes it a perfect fit in situations where the UPS is supplied by a generator set or to avoid harmonic perturbations of loads connected to the upstream busbar.
EIC (Energy Industries Council)
Bankable Energies is the must-attend event for 2025! Join us to explore the urgent shift needed to attract capital and accelerate projects. Register here https://lnkd.in/e6mnq3em
This results in substantial savings on the sizing of the upstream network. The bi-directional rectifier also enables several battery capacity tests feeding back into the grid without using the bypass line, requiring additional load banks or affecting the load.
With the Protect 8 PLUS, AEG Power
Moving into the winter months the Global Events and Campaigns team has been working on developing new events to support our members.
Following the success of our first European webinar at the beginning of October, focusing on hydrogen opportunities in the Netherlands with insights from RWE and proudly sponsored by Serimax, we move on to our upcoming Opportunities in Oil and Gas in Norway on 14 November and Opportunities in Offshore Wind in Germany on 6 February 2025. Members have free access to these webinars and can be booked online. Partnership packages are also available from £2,000+VAT. Please contact louise.donald@the-eic.com
Looking forward to the new year, we are delighted to announce some of the first speakers for the inaugural Bankable Energies that is taking place on the 26-27 February 2025. You can find the agenda as it stands online and you can join us as we bring together the global investment community, key project developers, policymakers and regulators to discuss the global shift needed to attract investment and drive projects forward. If you are interested in partnering with us for this event, get in touch to discuss how your company can get involved, with packages available from as little as £1,200+VAT. Visit our website for more details.
Energy Exports Conference is also moving forward with exhibition and sponsorship opportunities going fast.
Jo Campbell
We are looking forward to welcoming Bureau Veritas as our strategic partner for the 2025 edition of the conference. If you would like to find out more about how to take your company from local to global we have opportunities to suit every budget. This event will bring together projects from across the globe to showcase the opportunities to the UK supply chain.
If you are interested on any of our partnerships for any of our events get in touch with the team, global.events@the-eic.com to find out more.
Jo Campbell
Director of Global Events and Campaigns jo.campbell@the-eic.com
As we approach the end of another remarkable year, it was a privilege to showcase the energy supply chain’s finest at our recent EIC Regional Awards, honouring winners of the World Energy Supply Chain Awards (WESCAs) across 12 categories. Congratulations to all 33 finalists, particularly the night’s winners. The event ranks among the best in my 14 years here, and I extend my thanks to all who attended.
However, with oil prices dipping below US$70 for the first time since 2021 and OPEC+ revising its demand forecasts for 2024 and 2025, we stand at a crossroads. As renewable energy gains traction, the question remains: are we witnessing a pivotal shift toward more sustainable energy solutions or just a temporary market fluctuation?
Ryan McPherson
Regional Director, Middle East, Africa, Russia & CIS ryan.mcpherson@the-eic.com
Applications will open soon for Survive & Thrive IX, watch this space for more information.
As ADIPEC 2024 approaches, we are excited to host over 125 exhibitors in the UK pavilion. Across four action-packed days, we’ll feature industry panel sessions, contractor briefings and our first-ever welcome breakfast on 4 November, setting the tone for an exciting week at the world’s premier energy event.
Looking ahead, our Christmas cracker golf day is set for 12 December at the Abu Dhabi City Golf Club, promising a fantastic day of sport, networking and festive fun. Spaces are filling up fast, so don’t wait –secure your spot today.
Early next year, we’ll bring back our KSA and UAE Connect events, along with sessions in Kuwait, Oman and Qatar to keep you updated on regional developments.
Additionally, March 2025 will feature a trade delegation to Namibia and South Africa. The programme will identify current and future project opportunities, providing the chance to meet with key players and engage with prospective local partners and supporting organisations. For further details please contact internationaltrade@the-eic.com
Our GCC, CIS and Africa webinars will also be back early in the new year. Should you be unable to attend on the day, don’t worry as these are available to view on EICTV not long after the event. In addition, our EIC roundtables will continue, where I am always interested to hear about any topics that you may feel are worthy of wider discussion.
The recently published EIC Middle East OPEX report highlights that the region will see around US$1.2tn of CAPEX across the energy sectors between now and 2030 which gives a clear indication of the size of the opportunities. Although the region is seeing significant growth in the cleantech sector it should be recognised that 70% of the projected CAPEX will be seen in the oil and gas sectors.
ADNOC is acquiring a 35% stake in ExxonMobil’s planned blue hydrogen and ammonia facility in Texas, expected to be the world’s largest. Producing 1bn cubic feet of hydrogen daily and 1m tonnes of ammonia annually, it will cut carbon emissions by 98%. With final investment decisions by 2025 and operations starting in 2029, ammonia from the plant will be shipped to Europe and Northeast Asia, targeting markets focused on decarbonisation. This marks ADNOC’s growing role in hydrogen and carbon capture investments.
The UAE achieved just under 28% of clean energy in its energy mix in 2023, aiming for 30% by 2030. Major investments in solar and nuclear power, including the fully operational Barakah plant, have contributed to this progress. Renewable energy capacity grew 70%, reaching 6.1GW and further growth is expected, supported by projects like the Mohammed bin Rashid Al Maktoum solar park. The UAE’s strategy includes carbon capture and a national hydrogen strategy, with plans to invest Dh150-200bn by 2030, aiming for net zero emissions by 2050.
October 2024 was a significant month for EIC APAC, marked by our involvement in Clean Energy Transition Asia (CETA) 2024, held as part of the International Greentech & Eco Products Exhibition & Conference Malaysia (IGEM). CETA 2024 aimed to unite both public and private sector decisionmakers to propel milestones in the clean energy transition across the region. This platform facilitated dialogues between stakeholders in both the clean energy and hydrocarbons sectors, promoting a transition bridge strategy – a vision that advocates for a balanced, just and secure energy transition. The collaboration between EIC APAC and CETA was designed to generate meaningful progress and drive innovation, helping shape the future of energy across Asia through an inclusive and holistic approach.
Rounding off the month, the EIC APAC Regional Awards Gala Night 2024 will take place on Friday 29 November. Set against the backdrop of a Bollywood-themed evening, this highly anticipated event will bring together EIC members and supporters to celebrate the achievements of the year in a festive and elegant setting. Guests are invited to don their finest Bollywood attire and enjoy a night filled with entertainment, including live bands, an informal networking session, an awards ceremony, performances, a lucky draw and themed games. The highlight of the night will be the announcement of the EIC Regional Awards winners, recognising excellence within the industry.
Azman Nasir, Head of Asia Pacific azman.nasir@the-eic.com
Additionally, on 8 October 2024, EIC APAC hosted an informative webinar titled Offshore Wind in Asia Pacific: Insights into Japan’s Wind Market. The session featured presentations by Hazwani Izzati and Lim Xiao Shuen, both energy analysts at EIC APAC, who offered a deep dive into the current offshore wind energy market in the Asia Pacific region. Special emphasis was placed on the Japanese wind market, with the webinar serving as a platform to generate interest and momentum in the lead-up to Wind Expo Japan 2025, Japan’s largest wind energy trade show. The event will provide participants with key insights into the latest developments in wind energy technologies and market trends, while also underscoring Japan’s growing role in the offshore wind sector. Wind Expo has long been recognised as a vital hub for industry leaders, showcasing the latest innovations and fostering partnerships that drive the growth and development of the wind energy sector in Japan and beyond.
In November 2024, EIC APAC will be hosting two prominent events: the EIC APAC Networking Cocktail at the Offshore South East Asia Exhibition & Conference (OSEA) and the EIC APAC Regional Awards Gala Night 2024.
The EIC APAC Networking Cocktail is scheduled for the third week of November, coinciding with OSEA, which runs from 19 to 21 November 2024 at the iconic Marina Bay Sands in Singapore. With nearly five decades of history, OSEA is recognised as one of Asia’s largest and most influential offshore and marine showcases. EIC APAC’s Networking Cocktail aims to connect key stakeholders in the energy sector, offering a valuable platform for attendees to foster new partnerships, explore collaborative ventures and enhance business opportunities in the everevolving energy landscape.
Indonesia has awarded three oil and gas blocks in the first round of auctions this year. The Melati block, which includes both onshore and offshore fields with estimated resources of 4.7 Tcf of gas and 850 Mbbl of oil, was awarded to a consortium of Pertamina Hulu Energi, Sinopec and KUFPEC. The Central Andaman block was awarded to a consortium of Harbour Energy and Mubadala Energy. This block is estimated to hold 100 Mbbl of oil and 500 Bcf of gas. Additionally, the Amanah block with estimated resources of 50 Mbbl of oil and 450 Bcf of gas, was awarded to a consortium of Medco Energi and KUFPEC.
SK Earthon has been awarded the rights to explore and operate the Ketapu Cluster, an oil field located off the Sarawak coast by the Malaysian government. Under the agreement, SK Earthon will hold an 85% stake in the Ketapu Cluster as the operator, while PETROS will retain the remaining 15%. SK Earthon expects to commence crude oil and natural gas production from the Ketapu Cluster by 2031, following exploration and appraisal drilling to assess its commercial viability.
Now heading into November, as a reminder to all, the region has a great line-up of in-person and online events scheduled for members and non-members to attend. On 5 November 2024, the EIC will be welcoming its team of analysts to provide a virtual presentation covering the US Gulf of Mexico Decommissioning Market – if you or your team have yet to register for this event, do so today! In addition, in-person events are not the only events open to sponsorship. If you or your company are interested in profile raising opportunities such as promotional marketing opportunities, please click here and become an EIC Global Digital Supporter.
On 12 November the EIC will be joining Petrofac in-person at its offices as it provides a business briefing presentation. This event is only open to EIC members and has a very limited number of seats. If you are having issues with your registration, or have any inquiries, please contact adriana.romo@the-eic.com
If you are a non-member and would like to attend this event, please contact our membership team to learn how membership may benefit you and your company in addition to granting you access to events in our Business Briefing series navied.sadeghi@the-eic.com or madison.omalley@the-eic.com
Lastly, if you are not already part of our regional mailing lists and would like to stay updated on all thing’s regional events and regional energy news, please contact houston@the-eic.com for support. Members and nonmembers on our mailing lists are the first informed about new and upcoming events. Join us.
Amanda Duhon
VP & Regional Director, North & Central America amanda.duhon@the-eic.com
Market Update: US GoM Decommissioning Tuesday 5 November 2024
Business Briefing: Petrofac Tuesday 12 November 2024
North & Central America 9th Annual Clay Tournament Wednesday 19 February 2025
In the first multi-state offshore wind auction in the US, up to 2.8GW of wind power were selected from three projects off states of the New England area, in the country’s northeast coast. Massachusetts awarded 2.6GW of energy: 1GW from the SouthCoast Wind project, developed by Ocean Winds; 791MW from Avangrid’s New England Wind 1, also known as Park City offshore wind; and up to 800MW from Vineyard Wind 2, managed by Copenhagen Infrastructure Partners (CIP). Additionally, Rhode Island selected the remaining 200MW output from SouthCoast Wind. This collaboration is part of a broader regional effort between Connecticut, Massachusetts and Rhode Island for co-ordinated offshore wind energy procurement and the selected bidders will begin contract negotiations with the respective utilities.
The US Department of Energy (US DoE) has launched up to US$435m in incentive payments to help repair and upgrade several aging hydropower plants across the country. Nearly 300 stations are to be contemplated by the funding, which is part of the entity’s Maintaining and Enhancing Hydroelectricity Incentives programme. Despite not adding significant generation capacity to the grid, the campaign will help enhance dam safety and improve efficiency of a sector that accounts for 27% of the country’s renewable generation. The states of California (39) and New York (35) lead the way in absolute number of assets awarded funding.
Please go to page 32 to see upcoming events around the world
Join us on 7 November for the most prestigious event of the year: EIC South America Regional Awards 2024. EIC members and nonmembers will get together for a gala dinner to network and develop new business, as well as to celebrate and honour the amazing achievements of our industry, especially the participating companies in Survive & Thrive 2024. The finalists for the region are Equipesea, LHR Brasil, RelyOn Nutec (US) and Vaz e Dias for Culture & Collaboration; Induscabos, MetalCoating, RelyOn Nutec (US) and VWS West Veolia for Innovation & Digital; Induscabos, LHR Brasil, Oceanica and One Nature for Diversifications & Export; MetalCoating, Pix Force and VWS West Veolia for Technology & Sustainability; Equipsea, High Supply Energy and MetalCoating for People and Service & Solutions; Hausthene Poly, LHR Brasil and Oceanica for Resilience; AIS (UK) and LHR Brasil for Scale Up and Equipsea, AIS (UK) and RelyOn Nutec (US) for Transformation.
We have confirmed our third Luncheon for Women of Energy with Sylvia dos Anjos, Petrobras E&P Director as speaker sharing insights on leadership, on 7 November. Next month, from 3-6 December, the EIC will be hosting a trade mission to Guyana.
The Uruguayan government has announced plans to auction four sites for offshore green hydrogen production along the continental shelf through state oil company ANCAP. These sites, located about 50km off the coast, will each have the capacity to produce approximately 200,000 tonnes of green hydrogen via water electrolysis. The auction will take place in two phases: the first, a 10-year evaluation period, will allow developers to conduct feasibility studies and potentially initiate pilot projects. The second phase, lasting 30 years, will focus on large-scale development and production, including the construction of offshore wind facilities and co-located electrolysers. Although a specific auction date has not been provided as of the time of writing, it is expected to occur in the near future.
Later in December, EIC will host another of our successful Breakfasts in Rio, focused on Opportunities on FPSOs with Petrobras. Lourenço Fróes, Petrobras’ new FPSOs Program Co-ordinator, will speak about their new plans, which will create significant opportunities for companies in the supply chain, particularly in FPSO technologies, subsea systems and services, as well as sustainable energy solutions.
In September we welcomed Trident Energy and SBM Offshore for our Breakfast in Rio. Isnard Carvalho, Project Procurement Lead from SBM Offshore, Viviane Selleiro, Supply Chain and Bruno Barros, Supply Chain Manager from Trident Energy, shared their knowledge and updated us on the trends and possibilities of a sector that is constantly evolving. Among the many highlights of the event, SBM talked about the priority needs of increasing local content and the importance of equipment like modules, skids, valves, mooring (single source) and pumps.
Clarisse Rocha, Director – Americas clarisse.rocha@the-eic.com
The Brazilian Fuel of the Future bill will likely be sanctioned by President Lula after securing approval from both houses of Congress. The bill will further accelerate the production of biofuels in the country by placing higher mixture mandates for ethanol, biodiesel and biomethane into fossil fuels – gasoline, diesel and natural gas, respectively. The law will also stimulate a year-on-year growing blend of sustainable aviation fuel (SAF) into fossil aviation kerosene to reach a 10% mixture in 2037. The text also serves as a foundational regulatory framework for CO2 capture and storage activities, helping to unlock synergic opportunities in Brazil’s thriving ethanol business.
W I N N E R S
COLLABORATION ECITB
DIGITAL TURNER & TOWNSEND
ENERGY TRANSITION SCHNEIDER ELECTRIC
EXPORT TENZOR GEO
CULTURE REFLEX MARINE
DIVERSIFICATION PROEON SYSTEMS
ENVIRONMENTAL SUSTAINABILITY CLARIANT
INNOVATION OCEANEERING
The EIC gathered over 400 industry leaders and innovators for a night of celebration at the EIC National Awards Dinner 2024. The event, now in its 70th year, honours outstanding achievements in the energy supply chain across the entire energy sector. The winners were judged by a panel of more than 90 experts from across the global industry. Each category winner was the result of an in depth interview conducted as part of EIC’s Survive & Thrive Insight Report 2024. Seventeen World Energy Supply Chain Awards #WESCAs were presented to outstanding supply chain companies and the winners are presented here. A special thanks to Richard E Grant and our sponsors and partners.
In its 8th year, EIC’s Survive & Thrive initiative continues to research the 15 most popular growth strategies used by the world’s energy supply chain in challenging market conditions. Each year reveals new and important findings, such as the conundrum of record growth, with 96% of companies forecasting record revenues in 2024, offset by clear and worrying growing geopolitical and policy uncertainties, resulting in more cautious decision-making by energy bosses, which hampers investment.
The report features success stories and insights from 134 member companies and underscores the need for clearer policies and trade agreements to support market expansion. It reflects that leaders are now more committed than ever to pursuing the energy transition, with or without total policy clarity, but just not on pace with 2050 net zero timelines.
Exporting to new markets remains the least used growth strategy due to excessive risks, cost and time to market. Companies call for more government support and funding with market access. The #1 growth strategy is to develop client-facing solutions and services, with 82% of these companies now working directly with operators, increasingly side-stepping the Tier 1 EPC contractors.
Please see our success stories overleaf or visit the EIC website to view the complete report www.the-eic.com/MediaCentre/Publications/SurviveandThrive
The World Energy Supply Chain Awards aim to recognise excellence from all companies and organisations across the energy industries globally. In their business cases featured in the Survive & Thrive report, EIC member companies can demonstrate how they faced a specific challenge and introduced a new business solution or any initiative that drove successful results. See the 2024 winners on page 40.
AWARD CATEGORIES
Collaboration
Culture
Digital
Diversification
Energy Transition
Environmental Sustainability
Export
Innovation
Optimisation
People & Competency
Resilience
Scale Up
Service & Solutions
Technology
Transformation
Interviews for the 2025 Survive & Thrive Insight Report will start in January 2025
Tapping into the opportunities presented by regulatory changes
How is FireDos thriving?
Frank Preiss CEO
Beside promoting a new technology, FireDos is working to capitalise on the opportunities which new regulations that demand the use of fluorine-free firefighting foam have brought about, placing its unique technologies at the forefront of installer and end-user minds. With the launch of a next generation product with advanced properties and through significant investments in its marketing activities, continually innovating its product offering, and actively leveraging its network, the company has managed to achieve double-digit growth rates after several years of flat sales figures.
The challenge - Founded in 1979, FireDos has developed to a globally renowned manufacturer of high-quality foam proportioners and fire monitors that are specifically designed to enhance the efficiency of fire extinguishing systems. With more than 120 employees across its headquarters in Wolfsheim, Germany, and two additional production facilities, the firm has successfully completed more than 15,000 installations during the last three decades.
As a firefighting solutions specialist, the company supports the industry in several sectors – from fire brigades and aviation firms to warehouses, recycling facilities and energy industry specialists spanning a variety of verticals. However, the way in which it has supported this broad clientele base has changed and advanced over time.
Having introduced its original technology in 1994, several bold enhancements have been made in recent times to align with higher viscosity foam agents that are become standard after the implementation of legislative changes. However, putting these improvements on the map of end users has been an ongoing challenge for the firm – particularly given that the main customers of its components are fire system installers that often seek the most cost effective and easiest sales of systems among end users.
The solution - For FireDos to bridge this gap and enhance end user awareness of the benefits of its products, it has had to make a radical change in relation to its approach to marketing. Indeed, legislative advances have now made this easier. New regulations that demand the use of fluorine-free firefighting foam have
prompted end users to rethink their firefighting techniques, considering how different technologies and solutions may be best suited to their unique needs.
FireDos has worked to capitalise on this. Recognising that its products are optimally positioned to support the use of novel and innovative foaming agents, the company has been offering consulting packages for retrofitting fluorine contaminated fire extinguishing systems by use of its proprietary water motor driven piston pump solution, complete with a foam return option for testing of the proportioning rate without the creation of premix or discharge of foam.
Adapting to make the most of these opportunities hasn’t been straightforward. Indeed, the company has had to fine tune its product offering and more actively leverage its existing network as it has sought to grow within tough market conditions.
However, with a technology that offers many benefits, end users are beginning to see the merits of leveraging such solutions. Not only do FireDos’ technologies enable the use of the new fluorine free firefighting foams that other technologies have problems handling due to the increased viscosities. Equally, the initial cost of installation can be compensated within two to three years thanks to the regular savings associated with avoided disposal costs due to the recirculating of foam back into the storage tanks.
From an environmental aspect, customers benefit from the firm’s technology, which allows its end users to test the proportioning rate without having to create premix or foam, which, when using other technologies dispose of foam after it has been created. In essence, this reduction in foam concentrate consumption helps to cut disposal costs and is significantly better for the environment.
After starting to phase out its older technologies in 2021, FireDos is now seeing the merits of enhancing its offering and aligning more closely with new market needs. One focus is the introduction of a remote monitoring system for their systems. This will allow real time visualisation of all operating functions and early troubleshooting through predictive maintenance. Indeed, after several years of flat sales
Story type
#technology (main category) #environmental sustainability
▸ FireDos’ new technology has proven to be efficient, cost effective, and is helping companies to protect their people and assets.
For industry
▸ Don’t look at employees as just numbers, but someone whose work and contributions can make a difference.
▸ Every individual is an essential part to a company and the loss of any employee due to a bad company culture can be the start of a decline.
For government
▸ Once rules are made and implemented, the continued adherence must be followed up.
Key products and services: development and production of innovative products and systems for the firefighting industry.
Main industries served:
▸ Oil and gas – 15%
▸ Others (non-energy): energy and wate, aviation, fire brigades, chemical, automative – 85%
Headquarters: Hesse, Germany
Year established: 1979
Number of employees: 130
Revenue: N/A
Revenue from exports: 70%
figures, annual double digit growth rates have recently been achieved.
With its products endorsed by insurers, FM-Approved, and increasingly being used by major oil and gas operators, awareness of the benefits that it can offer will only continue to build as it strives to uphold its impressive growth figures in the years ahead.
Seizing the opportunity to provide secondary steel to renewable industries
Mike Smith Operations Manager
How is Forsyths thriving?
After reaching a pivotal juncture, metalworking specialist Forsyths took the fateful decision to diversify away from the oil and gas sector and position its steel working services towards clients operating in the renewables space. It is an ongoing process, but one which has already yielded work and promises to form a key part of the company’s rapid growth journey in the years ahead.
The challenge - Any company which survives more than 130 years will have navigate its fair share of obstacles. For Scottish firm Forsyths, the ability to adapt and innovate while retaining its grassroots traditions and hallmark of metalworking quality has been key to its longevity.
Until the 1980s, a large proportion of the company’s income was generated from producing copper pot stills and condensers for the Scotch whisky industry. However, following a slump in production, the last few decades have seen the firm diversify successfully into the world of oil and gas and petrochemicals. With formidable expertise and excellent load out facilities at its dockside facility in Buckie and dedicated clean room facilities in Rothes, Forsyths is well placed to design, produce and supply equipment such as pressurised tanks, vessels, skids, and other fabrications to these sectors.
Nevertheless, akin to the decline in whisky production experienced in the 1980s, the company finds itself at another critical juncture with the ongoing energy transition gradually phasing out oil and gas projects.
The solution - Forsyths and its leadership knew it had to open a new line of business to futureproof the organisation.
It chose to pursue the opportunity in offshore renewables, and after engaging with government agencies, academic institutions, and trusted information sources from the private sector (including the EIC), this new course was charted.
The decision to pivot was taken around 2017, and embedding into the sector has been a continuous process ever since. For example, the company has finished and been granted the Fit 4 Offshore Renewables (F4OR) pro-
gramme and engaged expert partners such as Orlo Energy Ltd to help support its transition. These actions have proven crucial, not least because they have provided Forsyths with valuable insight into the sector, as well as confirming its confidence in the scale of the fabrication projects that would be required in the future.
From here, the company’s strategy has been to hire sector specific advisors, look for an additional quayside facility, and build up a track record of delivery for clients. Indeed, among its early contracts was a project in Wick for Repsol. The work involved the fabrication of frames to attach a boat landing to a platform which houses wind farm transformers.
Opportunities are also being explored through collaborations. Forsyths has struck up fruitful partnerships with 360Energy and Dron & Dickson and submitted multiple joint bids for work with a Tier 1 contractor. Meanwhile, the company is also extending its network through exhibiting at renewable energy events, and has received a grant to take part in an expert hydrogen course which could uncover potential synergies with its skillsets. Given the firm has already received enquiries in relation to green hydrogen projects, this is a timely move.
Activity in the clean energy space is building steadily as Forsyths seeks to transition away from its reliance on the oil and gas market. Indeed, based on the level of interest it is receiving in the form of invitations to tender and requests for quotes, it is clear that the market for secondary steel in the renewable space is an exciting one.
Such is the company’s confidence, plans are in the pipeline for a new quayside facility to accommodate projected growth. Revenue has already grown around 50% from £54m to £74.5m between 2021 and 2023, with the company forecasting a doubling in turnover in the not-too-distant future. And with almost a third of new enquiries being related to renewables, this new avenue of business will be a key a contributor to Forsyths future.
Story type
#diversification (main category)
#collaboration, #energy transition
▸ Forsyths’ successful strategy to diversify promoted revenue growth.
▸ Almost a third of the company’s Invitation to tender on new projects are related to renewables.
For industry
▸ Now is a time of transitioning into renewables and there are huge opportunities for entrepreneurs and young engineers with funding available for up skilling resources required.
For government
▸ Enforce a high percentage of local content and incentives for overseas investors.
Key products and services: manufacture of machinery and equipment for industrial sector.
Main industries served:
▸ Oil and gas – 55%
▸ Nuclear power – 5%
▸ Others (energy) – 5%
▸ Others (non-energy: distillation) –35%
Headquarters: Rothes, UK
Year established: 1890
Number of employees: 520
Revenue: £60m
Revenue from exports: 22%
A fourfold transformation to turbocharge its growth journey
Owen Gibbons
Commercial Director
Fulkrum has seen a strong growth trajectory after enacting a four-pronged strategy designed to better accommodate changing client priorities in the energy sector. With a near 50% revenue growth in 2023, this momentum continues to build.
The challenge - Fulkrum has been steadily growing as a provider of quality control and quality assurance services to the global energy sector.
By 2023, Fulkrum’s leadership devised a strategy designed to maintain the company’s growth trajectory and reach its goals. Sector and service diversification would ensure it remains competitive, but only if it was also able to stay true to its core values and retain its bespoke, personalised service approach with clients.
The solution - Last year was a momentous period for Fulkrum. The company’s internal headcount increased by 50%, while it opened two new offices, one in Italy and one in Qatar, bringing the total number of offices to 14. Additionally, Fulkrum surpassed its operational targets, with its technical personnel performing over 100,000 quality and inspection-related visits on behalf of its clients across various projects.
Meanwhile, from a structural perspective, the company separated the business into five operating regions (North America, South America, Europe and Africa, APAC, and the Middle East), a process which created new job and growth opportunities for internal teams.
To maintain this growth trajectory, Fulkrum recognised the need for a clearer long-term strategy for the business. The firm held its first global strategy workshop in London, where the entire global leadership team assembled for the first time. This workshop provided an environment to analyse Fulkrum’s position in the markets it operates, assess its qualities against competitors, identify forward opportunities on a global scale, and collectively agree on short, medium, and long-term priorities. The workshop also allowed the international team to strengthen bonds and foster an even stronger rapport with their colleagues.
A four-pronged set of priorities were identified to take the company through 2024 and beyond.
Firstly, the company aims to invest in its people by implementing a comprehensive “People-First”, plan focused on learning and development, training and mentoring. This approach aims to maintain high retention rates, attract top talent, and provide an environment for team members to thrive and progress within the company. The hiring of Paulina Panus as the new Head of HR was the first step toward implementing this initiative.
Secondly, Fulkrum will continue to emphasise operational excellence by expanding its ISO IMS (9001, 14001, and 14001) and ISO 17020 accreditation to additional offices. This ensures that all Fulkrum offices adhere to stringent standards for operational excellence, impartiality and industry-leading levels of customer service.
Thirdly, geographic expansion remains a priority. With the recent incorporation of Fulkrum-Iraq in Basra, Fulkrum now has a presence in 15 countries to support clients globally. The company is currently exploring five additional countries for potential local presence to support client interests and contribute to local economies through job creation and knowledge transfer.
Finally, Fulkrum aims to introduce new complementary service offerings to support its strategic evolution as a rapidly growing business. Building upon its success as an industry leader in second and third-party inspection services, the company plans to expand its additional service offerings, previously available only to local clients in specific territories, to its global client portfolio. This move will bring its standards of excellence to currently underserviced procurement and HR scopes of work.
Alongside these internal changes, Fulkrum continues to build up its impressive track record of execution for clients, often partnering with customers in long-term arrangements.
A good example comes from the Gulf of Mexico. Here, Fulkrum was engaged by a leading EPCi client to enhance quality and procurement processes for their involvement in the Shell Whale Project, a US$2 billion deepwater development which is estimated to yield over 100,000 barrels of oil equivalent daily. Beginning in 2022 and escalating through 2023,
Story type
#scale up (main category)
▸ Revenue growth, 50% rise on the turnover recorded in 2022.
▸ Geographical expansion, now Fulkrum is present in 15 countries to support clients globally.
For industry
▸ There’s no such thing as ‘failure’ –you either win or you learn!
For government
▸ Provide greater assistance to SMEs as they face the challenge of start-up and scaling.
Key products and services: leading provider of expert quality control and quality assurance services to the global energy industry.
Main industries served:
▸ Oil and gas – 80%
▸ Offshore renewable energy – 12%
▸ Hydrogen – 3%
▸ Nuclear power – 3%
▸ Onshore renewable energy – 2%
Headquarters: London, UK
Year established: 2011
Revenue: £41m
Revenue from exports: 70%
Fulkrum’s inspection and quality consulting services have been integral to the ongoing installation and project start-up and is scheduled to continue into 2024. Fulkrum delivered four pivotal services: vendor surveillance, client representation, fabrication QA/QC, and installation QA/QC. These services were executed seamlessly across more than 30 locations in North and Central America, Europe, and Asia, culminating in the ongoing installation at Alaminos Canyon Block 773.
Fulkrum’s 2023 revenue of £41m represents an almost 50% rise on the £28m turnover recorded in 2022. With its four-pillar strategy firmly in place, Fulkrum has the foundations from which it can continue along its impressive growth journey.
Facing up to energy transition challenges and doing something different
Story type
#energy transition (main category)
#collaboration, #environmental sustainability, #transformation
Benefits
Helen Coleman Managing Director
For any consultancy firm, no matter the industry it operates in, the ability to understand and find answers to customers’ challenges is paramount to success.
Genesis, a company with a successful track record spanning three-decades, recognised it had to do something different when clients began seeking long-term, sustainable strategies that align with energy transition targets and net zero ambitions. Through a mix of hiring and retaining key talent, evolving internal processes and close collaboration with clients, a new and innovative Genesis has emerged.
The challenge - The global energy industry is undergoing a significant transformation, presenting both exciting opportunities and uncertainties. Indeed, the energy transition shift has created immense potential for diversification, innovation, and blue-sky thinking to drive growth in nascent markets.
For Genesis, a leading consultancy services provider to the sector for 35 years, the need to evolve and diversify to support its clients’ transitions has been recognised and undergoing implementation for some time. Previously, environmental and emissions reporting, as well as impact reductions, were viewed as necessary regulatory requirements and reporting. However, following the Paris Agreement in 2016, emission reductions have taken centre stage within our client’s agenda. Genesis’s clients are now implementing real improvements before it is mandated, embracing sustainable practices across the entire energy industry value chain, from production to consumption, to achieve net-zero emissions.
The company has also witnessed a shift in its traditional clients, which have diversified and included renewable energy sources and energy storage in their portfolios and focussed on energy efficiency and the use of new technologies.
The solution - To better support clients during these journeys, Genesis has continually evolved its own offering.
It has enhanced its base of existing and transferable skills, retrained key people, brought in new talent, and leveraged its parent company’s experience in renewables and hydrogen. Moreover, the firm has developed new tools such as
GenCAT (for carbon assessment) and is also developing a platform of tools, Gen-Clarity, to assess environmental impacts.
Alongside this, Genesis refined its internal processes and the ‘Genesis Way’ of working, which is transferable to all its services. In doing so, the company has been able to improve the efficiency and effectiveness with which it delivers projects for clients.
Clients have also been closely consulted throughout the process, a key part of the Genesis evolution centring around collaborating with customers to find innovative solutions to their challenges. Off the back of these conversations, the company’s overarching mission was updated – now, Genesis supports clients in their journeys to a more sustainable future. Its services support them in realising their net-zero ambitions, ensuring they have all the information required to make sound investment decisions.
This strategic realignment has paid dividends over recent years. Today, the company has a whole new portfolio of customers in sustainable energies that traverse many industries, with successes spanning metals and mining to waste-to-energy developments.
Since 2017, Genesis has witnessed a resurgence of CCUS. The company has been involved in almost all CCUS clusters in the UK and was recently selected as the Northern Endurance Partnership contractors and awarded the Viking CCUS project. Indeed, its expertise in this area has positioned Genesis as a market leader in CO2.
Meanwhile, six years ago, Genesis worked on its first hydrogen project, its clients seeking to understand the feasibility of such developments and how they could contribute to their net-zero strategy. Since then, the company has performed over 70 studies in hydrogen, including the Doggerbank Green Hydrogen and Pamelia Hydrogen projects in Western Australia. Genesis has also developed expertise and tools to evaluate the different pathways of Power to X, including supporting Breakthrough Energy in its due diligence for E-fuel investments.
Because of its embrace of a ‘dare to do something different’ culture, Genesis is now better positioned to handle future changes and challenges as the energy market continues
▸ Genesis’ diversification strategy was successful as company today has a completely different portfolio.
▸ Experience in CCUS has enabled projects and awards win.
For industry
▸ Create new solutions, be adaptable. Collaborate to tackle complex challenges and drive innovation.
▸ Working with the public to gain support and build trust is crucial for maintaining a positive reputation and ensuring long-term success.
For government
▸ Prioritise joined-up policy making throughout the value chain, including off takers, infrastructure, and other key.
Key products and services: advisory and technical consulting services for the energy sector.
Main industries served:
▸ Oil and gas – 50%
▸ Conventional power – 5%
▸ Offshore renewable energy – 5%
▸ Onshore renewable energy – 5%
▸ Hydrogen – 5%
▸ Carbon capture – 15%
▸ Others (energy): downstream – 15%
Headquarters: London, UK
Year established: 1988
Number of employees: +500
Revenue from exports: 90%
Carving a reputation as a go-to advisor for navigating the energy transition
GHD is excelling thanks to an unwavering commitment to its ‘Make it Real’ strategy. Implemented in 2020 to help both GHD and its clients meet the demands of a rapidly changing world, GHD has gone on to record revenues in 2023, excelling in areas such as energy transition, business resilience and sustainability.
The challenge - With 11,000 employees generating US$1.86bn in revenue across more than 160 offices worldwide, GHD has established itself as a leading professional services company. Specialising in advisory, digital, engineering, architecture, environmental and construction solutions, GHD is dedicated to enhancing the sustainability of water, energy and communities for future generations.
Indeed, GHD’s forward looking approach has shaped its overall strategy in recent years.
In 2020, the company introduced a five-year plan titled ‘Make it Real’, recognising the need for its clients to adapt to radical changes, disruptive technologies and new business norms largely driven by the energy transition.
The challenge of shifting the global economy to net zero is immense, requiring the involvement of every company in every sector across every country. With the energy sector at the forefront of this transition, GHD’s clients are experiencing an unprecedented pace of change in market sentiment. Customers, investors and regulators are all demanding genuine corporate commitments to decarbonisation and sustainability, ensuring that no one is left behind.
To align with these evolving demands and support its clients in their energy transition journeys, GHD launched a transformational investment programme focused on recruitment, reskilling and upskilling staff. As part of this initiative, the company created new specialist roles and appointed new leadership to manage the largest enterprise-led strategic growth initiative in its history – ‘Future Energy’.
Underpinning these efforts is a clear goal: to grow and pivot its business focus so that by 2027, 25% of all net revenue – equivalent to US$1bn per year – will be generated from energy transition value propositions.
The solution - The launch of GHD Advisory in
2016, to address clients’ business challenges and opportunities driven by global megatrends, laid the foundations from which the company’s strategy could succeed. Indeed, through the advisory group, the firm was able to swiftly develop its global strategy, redefining GHD’s vision for sustainable water, energy and communities for future generations.
Resultantly, the ‘Make it Real’ strategy was implemented in 2020, this being shaped by extensive client and broader market engagements. Leveraging innovative thinking, deep infrastructure expertise, solid business acumen, and a commitment to practical solutions, GHD is now instrumental in driving efficiency, growth, and support for clients adapting to change. As trusted advisors, GHD is specifically working with its clients to tackle three key future energy challenges:
#1 – Energy transition: GHD provides strategic advice and transformational pathways, identifying short- and long-term roadmaps for energy transition. By understanding clients’ progress, GHD develops strategies that protect financial performance, drive impact, and create competitive advantages.
#2 – Business resilience: Recognising that resilient businesses and projects attract investment by meeting ESG criteria, GHD helps clients to futureproof their operations. The firm offers methodologies and strategies to address, manage, and mitigate change, enhancing value and growth.
#3 – Sustainability: Taking a holistic approach, GHD identifies potential points of failure in clients’ sustainability efforts. The firm assists in formulating and executing success strategies, ensuring clients meet their sustainability goals.
Through these efforts, the firm’s new strategy has been key in driving impressive growth and strong shareholder returns in recent times. Indeed, in 2023, GHD achieved record revenues of US$1.86bn – up 17% versus the US$1.59bn recorded in 2022.
The EMEA region, a key strategic area, experienced particularly strong growth through several key projects. In the UAE, for example, GHD is supporting the National Hydrogen Strategy, positioning the country as a global leader in hydrogen development. This includes delivering a comprehensive National
#energy transition (main category)
▸ Record revenues of US$1.86bn in 2023, 17% up from 2022.
▸ On track to have at least 25% of revenues coming from energy transition by 2027.
For industry
▸ Test more and carry out extensive scenario planning, this is a volatile market. Do more front-end analysis.
▸ Be clear about your company culture to stimulate career ambition.
For government
▸ Have clearer goals and set outcomes beyond the term of current governments. We need long-term commitment.
▸ Provide more subsidy support.
Key products and services: multidisciplinary professional services for integrated solutions.
Main industries served:
▸ Oil and gas
▸ Renewables
▸ Energy storage
▸ Hydrogen
▸ Carbon Capture
▸ Conventional power
Headquarters: Sydney, Australia
Year established: 1928
Number of employees: 11,000
Revenue: £1.86bn
Revenue from exports: N/A
Hydrogen Strategy to the Ministry of Energy and Infrastructure (MOEI), aligning with the UAE’s vision to become a leading low-carbon hydrogen producer by its 60th anniversary in 2031.
With GHD’s brand strength growing in all markets, and clients increasingly viewing GHD as the go-to trusted advisor for navigating the energy transition, it is well positioned to achieve its goal of generating at least 25% of its revenue from energy transition activities by 2027.
Building momentum in energy transition with new
foundations
Scott Martin CEO
Glacier Energy now has the financial backing it needs to fully exploit the traction it has been gaining in the renewables arena. With Averroes Capital acquiring the business, rapid growth is on the horizon through a mix of acquisitions, innovations and collaborations with stakeholders across the energy transition ecosystem. Alongside this, its reputation for solving complex problems is strengthening all the time thanks to the completion of highly bespoke projects for clients.
The challenge - For well over a decade, Glacier Energy has been helping to solve clients’ challenges with highly innovative, specialist solutions covering heat transfer and pressure vessels, onsite machining, NDT and inspection services, and welding.
Until recently, much of its business had been derived from asset operators, Tier 1 EPCs, OEMs and other large manufacturing enterprises serving the oil and gas sector. However, the past few years have seen a shift in focus to deepen its involvement in the renewables and energy transition space, especially wind, hydrogen, energy storage and carbon capture.
Indeed, the company already had a good track record in the renewables space. However, the aftermath of the pandemic posed a significant challenge to fully capitalize on new opportunities. Glacier Energy found itself constrained by limited capital, hindering its ability to invest in new strategies.
Consequently, the company was compelled to explore alternative avenues to lay the groundwork for its next phase of development.
The solution - A pivotal development came with the entry of London based Private Equity firm, Averroes Capital, finalising its acquisition of Glacier Energy in January of this year.
The move will allow the firm to capitalise on significant market momentum, with the additional funding being used to acquire and innovate new solutions, channel business development efforts into renewable markets, and secure projects with both new and existing clients.
Alongside this, the company is actively partnering with universities and spin out innovators, with new facilities and high-volume manufacturing capabilities also being explored. Acquisitions, meanwhile, could add another 50% to Glacier Energy’s revenue base over the next two to three years.
Key to forging its reputation in the energy transition arena will be successful delivery of projects and the cultivation of a track record that potential clients will find difficult to ignore.
This is already well in motion, with several success stories emerging from the renewables sector in recent months. An ongoing project, for example, for a Wind Farm operator involves the assessment of the integrity of tower flanges and shell joints on multiple windfarm sites across Europe. To date, Glacier Energy has mobilised several multi-disciplined inspection teams to various European locations to carry out conventional, advanced and visual inspections on the assets as required by the client. Downtime has been kept to minimum and tight deadlines continue to be met, helping to save the client time and money.
Another project, delivered in 2023, involved the delivery of a post-compression high pressure hydrogen cooler for a containerised electrolyser kit, which is used for charging vehicles such as lorries and cars. A highly bespoke requirement, Glacier Energy had to work outside of typical industry standards to innovate and build the hydrogen cooler, a feat it managed to pull off by combining various technologies and different types of heat exchangers.
These success stories are translating into tangible positive trends in numerical terms. Total company revenue has grown from around £21m in 2020/2021 to £35m in 2023/2024, with renewables accounting for more than a third of turnover. This financial year, Glacier Energy expects renewables to generate 40% of income, not far behind oil and gas which is set to account for roughly half of its revenue.
Given that the split was 90% and 5% in 2015, a huge amount of progress has been made in less than 10 years.
#diversification (main category)
#energy transition, #export, #resilience
▸ Successful bespoke approach resulting in revenue growth.
▸ Significant increase in renewable energy, highlighting company’s diversification strategy.
For industry
▸ Think big, work hard, choose good mentors and have a clear strategy.
▸ Listen to your customers, ac with integrity at all times and be easygoing.
▸ Develop a stable tax environment to encourage investments.
Glacier
at a glance:
Key products and services: services for renewable and conventional energy markets.
Main industries served:
▸ Oil and gas – 55%
▸ Offshore renewable energy (offshore wind) – 30%
▸ Onshore renewable energy (onshore wind) – 5%
▸ Hydrogen – 1%
▸ Others (non-energy): industrial – 9%
Headquarters: Aberdeen, UK
Year established: 2011
Number of employees: 220
Revenue: £35m
Revenue from exports: 40%
Transforming to champion cradle-to-grave off shore projects
Ekkehard Stade COO
With a renewed business strategy centred around widening the scope of its services, marine, offshore and engineering consultancy Global Maritime is looking to build on a highly successful 2023.
Having doubled its sales pipeline throughout the course of last year, the company is now seeking to provide fully integrated solutions for cradle-to-grave offshore projects and has already secured its first full scope contract in 2024.
The challenge - In 2023, the focus for Global Maritime was optimisation and transformation. Ironing out the creases of an internal process overhaul that occurred three years ago, the firm was seeking to enhance its headcount and grow its services in all offshore energy markets.
Building on that success, the company is now moving into the next phase of its journey, aiming to deliver cradle-to-grave services to the offshore industry – something that had been out of its reach prior to 2024.
In an effort to expand capability and reduce skills gaps to support those ambitions, Global Maritime had previously recruited as many as 40 people. However, more than recruiting has been required to make the overall transition a success.
The solution - Critically, this latest phase of Global Maritime’s transformation efforts was split into four key categories.
First, Global Maritime focused on bolstering its geoscience team – endeavours that have proven successful. With just one member of the company employed in this domain previously, the division now stands at 34 strong. This is despite significant skills shortages in this area, the company secondly having become more proactive in collaborating with recruitment consultants to onboard young, talented professionals and train them for key roles.
Third, in the engineering and software business stream, Global Maritime has leaned more heavily into technology, moving away from a fragmented digital solutions strategy through the establishment of an engineering and software team that focuses on developing existing projects to tailor them to client
needs. As part of this, AI-backed solutions are now in the planning phase – something that the company is hotly anticipating.
And fourthly, the organisation has created a new marketing team to establish brand presence in key target markets and verticals, efforts that have been undertaken alongside building capacity in the business development and sales teams. Not only has this served to enhance Global Maritime’s position, but it also provides a coherent strategic mechanism through which the company can easily communicate its one-stop shop and go-to-services offerings to clients.
Of course, transformation on this scale doesn’t come easy, and challenges have been encountered along the way. Yet each significant hurdle has gradually and effectively been overcome.
Where funding and investment was previously a barrier, this is no longer an issue thanks to a change in ownership. Previously owned by a private equity company until the beginning of 2024, the firm is now in the hands of a financial investor with a long-term view who is more open to providing capital to accelerate growth efforts.
Likewise, while skills shortages remain a prevalent, industry-wide issue, attracting talent has become much easier with a trusted recruitment consultant that prioritises the company’s focus on recruiting for value and culture, not just skill. This, combined with expanded capacity in the HR team, has paid dividends.
Now, with a clear, enhanced offering, and powerful management team driving a culture of unconditional trust, Global Maritime is excelling again. Thanks to its renewed structure and offering, not only did the firm’s headcount increase 20% in 2023, but its sales pipeline also doubled.
Critically, the firm has also been growing the percentage of the business that is wider in scope, rather than fragmented projects. To this end, it secured its first 100% scope project in 2024 – a bearing replacement contract for HyWind Scotland which Global Maritime’s internal skillset complements significantly. Scheduled from April to August, it will involve works across the company’s business streams.
#service & solutions (main category)
#culture, #scale up
▸ Sales pipeline doubled.
▸ 20% headcount increase.
▸ First 100% scope project secured in 2024.
▸ Build a culture in company that allows to attract and retain talent, not lose it – don’t limit activity to just oil and gas for your talent pool.
▸ Be keen and curious to learn.
▸ Develop a stable and consistent energy policy and regulation –remuneration models for offshore wind are a mess globally.
Global Maritime at a glance:
Key products and services: specialised offshore consultancy for whole value chain services, traditional energy and renewables and infrastructure projects.
Main industries served:
▸ Oil and gas – 50%
▸ Offshore renewable energy – 40%
▸ Others (non-energy): infrastructure – 10%
Headquarters: Stavanger, Norway
Year established: 1979
Number of employees: 303
Revenue: £45m
Revenue from exports: 65%
With such a significant milestone achieved so early in the year, it’s likely that Global Maritime will only continue to stride from one success to another. Indeed, it is likely that the firm’s cradle-to-grave offering will continue to gain major traction through the coming months.
Proving that patience is a virtue
How is Hausthene thriving?
Paulo Tezza CEO
Hausthene is making the most of its newfound footing in the oil and gas industry after a long wait. Having competed with long-established sector players in the development of bend-stiffeners, it has now proved the value of its products.
The challenge - Hausthene has been operating in various industrial sectors for over 40 years, providing a variety of business-critical elastomeric parts and coatings to its clients.
Dominant in the polyurethane industry, the company has gradually yet consistently faced stiff competition from new entrants. With the 2008 financial crisis cooling the market significantly, the enterprise recognised the need to diversify.
With the economy picking up between 2012 and 2014, Hausthene began to eye the oil and gas market. However, despite all its expertise, the company was unsure of how to establish a presence. Being a family-owned company and, consequently, “non-traditional” in supplying parts of such high technology and responsibility appeared to be a significant barrier to entry.
Hausthene studied the industry meticulously, building expertise in the production of bend-stiffeners (BS) - protectors of umbilical or flexible cables vital in many oil and gas projects. When it comes to such important item, suppliers prefer to lean on established enterprises. Hausthene persisted, fabricating its first BS in 2017 and offering a prototype to industry players.
However, this was never tested. The company recognised that the first major barrier it had to overcome was the dynamic testing of its BS in a simulator with Petrobras’ approval. At that very moment, one of the company’s partners – an umbilical supplier – opened the doors for it to homologate its bend-stiffeners. The test would be carried out on one of its umbilicals, and then there would be the possibility of using its BS.
It was a great opportunity with several challenges. Hausthene would have to produce the bend-stiffener within one month at yearend, meaning partners and suppliers needed to work during a holiday period.
The solution - Although Hausthene’s polyurethane injection machine was suitable for the requested size, its furnace measured only six metres while the BS needed seven. The company turned to its partners and suppliers for mould accessories and the renovation of the furnace.
Further challenges arose. While Hausthene’s overhead crane was suitable for the weight of the BS, its height limited the company in terms of its assembly and movement. To ensure total safety in the process, a crane-truck also had to be rented and positioned next to the furnace to produce the part. The BS was then ready to be assembled with the umbilical and sent to the test site.
After investing in mould, engineering, technology, and studies, the test did not occur. At that time, the partner company was also homologating a new umbilical cable supplier, and its client – Petrobras – chose not to include the bend-stiffener amid risk-based reservations.
Hausthene didn’t give up. Having gone through the process of producing two good quality BS, the firm knew its products just needed to be evaluated – another step in what had already been a long journey.
The company obtained approvals for various parts in the oil and gas market, enhanced its processes, honed its technologies, bolstered its knowledge base and began to establish a reputation within the sector.
Come 2020, the very same partner approached Hausthene to secure a new testing and homologation opportunity for its new BS.
With the scope of work formally agreed upon, the firm’s BS would be tested alongside its partner’s umbilicals – finally, the firm achieved the long-awaited homologation.
It was still a new entrant. However, it now had the documentation and track record proving that the quality of its products matched that of traditional players.
Following this, an increasing number of doors have opened for Hausthene. Not only did the company increase its supply to this initial client, whose demand for its BS tripled in just one year, but it also managed to close deals with two more clients in 2023.
Story type
#resilience (main category)
▸ Orders for 20 more products in place.
▸ Two extra clients secured in 2023.
For industry
▸ Focus on long-term results to withstand the inevitable fatigue that you will have to face along the way.
▸ When starting a company, be willing to do the work of multiple people until the business becomes more robust.
For government
▸ Stimulate small-sized, employing companies in the industry.
Key products and services: provision of high-quality polyurethane parts.
Main industries served:
▸ Oil and gas – 50%
▸ Others (non-energy): mining, steel, packaging, glass and fibre – 50%
Headquarters: Mauá, Brazil
Year established: 1982
Number of employees: 40
Revenue: £3.1m
Revenue from exports: 1%
Looking ahead, the firm now has orders for 20 more products in its pipeline, these alone representing 10% of its revenue. And as the brand becomes increasingly recognised in the sector, it finally looks set to advance towards establishing a presence in oil and gas.
An entrepreneurial success story with international ambition
How is High Supply thriving?
Bastos CEO
After proposals for an innovative explosion-proof electric panel rental model were rebuffed by his former employer, Alexandre Bastos set out on his own to fill a significant gap he identified in the Brazilian oil and gas market.
15 years on and High Supply has sustained consistent annual growth of 30-40%, the company now gearing up to use its proven success domestically as a springboard for international growth in the years to come.
The challenge - At EIC, we’re proud to be able to share the varied, successful and inspiring entrepreneurial stories of our members. Alexandre Bastos, Founder and CEO of High Supply fits well within that category.
Back in 2009, Bastos went to his employers with an idea that he believed would capitalise on the demand for high quality, cost-effective and safe explosion-proof electric panels found throughout the Brazilian oil and gas market. He put his proposals forward, but was met with resistance as they were rejected.
Maintaining belief in his idea, Bastos set out on his own, founding High Supply with the intention of reaching out to prospective clients and providing them with the high-quality explosion-proof electric panels that they needed.
The solution - Today, High Supply specialises in renting explosion-proof electric panels. The company operates primarily in the oil and gas industry, providing comprehensive services and products to support offshore oil and gas operations throughout Brazil.
However, like any great entrepreneurial story, it wasn’t an easy journey to get here. For Bastos, it quickly became clear that the company had to excel on several fronts to gain traction and establish presence.
Critically, the firm’s unique selling proposition lies in its rental model, enabling its clients to purchase and leverage high quality equipment at a fraction of the cost of purchasing. The company doesn’t simply excel on price, however. Equally, it places quality and safety at the heart of its offering, providing state-of-the-art
equipment to its clients in order to deliver market-leading services and solutions.
There have been several hurdles encountered along the way. Indeed, Bastos found he had to design his own explosion-proof electric panels after facing issues with fragile products sourced from other suppliers. However, in overcoming each challenge that has presented itself, High Supply has continued to excel in the market for a period of 15 years.
During that time, the company has sustained annual growth of 30-40% while focusing on profitability and maintaining a well-structured organisation. This consistent expansion has seen the enterprise grow to a point where 33 employees are now book, the firm now also supporting key industry operators including Ocyan, Wood and Mota Engil.
While High Supply currently only operates on a domestic basis in its home country of Brazil, with headquarters in Rio das Ostras – a twohour drive east from Rio de Janeiro – it is now actively working towards establishing itself in key international markets. Specifically, the company is exploring the potential of creating a regional division of High Supply out of Houston, Texas, as well as establishing a warehouse and fabrication unit.
Looking ahead, further growth and expansion is now the priority. While this will not be rushed through, with Alexandre key to get the right staff in place with the skills needed to ensure the firm’s next chapter is a successful one, everything points to High Supply going from strength to strength moving forward.
Having identified a gap and carved out a unique niche in the market that has facilitated high growth for 15 years now, there is nothing to suggest that High Supply won’t succeed in bringing its solution to new markets and customers.
Story type
#service & solutions (main category)
Benefits
▸ Annual revenue growth of 30–40%.
▸ High Supply plans to open a warehouse and fabrication unit in Texas.
Key findings
For industry
▸ Perseverance over discouragement. Emphasise honesty, ethics and courage as keys to success.
High Supply at a glance:
Key products and services: oil and gas equipment and installations.
Main industries served:
▸ Oil and gas – 100%
Headquarters: Rio das Ostras, Brazil
Year established: 2009
Number of employees: 33
Embedding ESG principles to offer a fresh approach to asset repairs
#environmental sustainability (main category)
#culture, #technology
▸ Company on track to increase turnover by around 20% for the second year in a row.
ICR Group is driven by a singular vision: to revolutionise the way assets and critical infrastructure are repaired, inspected and maintained. The company specialises in preserving vital, yet often aging, infrastructure across multiple industries — from oil and gas to renewable energy, defence, nuclear and telecommunications.
The challenge - The business emerged strongly out of the COVID-19 pandemic and enjoyed an acceleration in growth. Specifically, it had three priorities to address: reducing reliance on the UK and North Sea market by expanding overseas; curbing its dependence on oil and gas by diversifying; and becoming more relevant to the net zero agenda.
The solution - This journey has involved key product developments, aimed at reducing costs and time as well as supporting client carbon footprint objectives. In addition, there has been an increase in headcount – more than 80 in the past two years. ICR has put a greater focus on sustainability and increased its partner network with additional locations. This strategy carries sustainability advantages, which are the focus for CEO Jim Beveridge, who joined ICR in April 2022, bringing with him a determination to embed ESG principles into the company from the ground up. Action has been decisive, with the firm now operating with its own ESG committee and achieving silver status with ECOVADIS at its first attempt. Gold is the next target, with sustainability reports also being published to demonstrate how ESG strategies have been properly embedded into the broader business strategy.
It’s the technology that helps ICR stand out in the market. Technowrap is an innovative ICR structural, pipework, pipeline repair and rehabilitation technology designed to provide significant benefits to clients in terms of cost and time savings, as well as sustainability.
This composite repair technology rehabilitates aging infrastructure without the extensive costs and delays associated with conventional replacements, allowing for operations to continue uninterrupted and avoiding costly shutdowns.
The application extends beyond pipelines to include tanks, vessels, and even underwater structures, showcasing its versatility and effectiveness across various repair scenarios.
Jim Beveridge Gemma Neal CEO Head of Marketing and Communications
Sustainability is at the heart of Technowrap. By minimising the need for new materials and reducing waste, it presents an eco-friendly alternative to traditional repair methods. Its capacity to reduce carbon emissions by 66% compared to conventional replacements underscores its role in promoting sound environmental stewardship.
Technowrap’s efficacy is underpinned by the use of glass or carbon fibre cloths combined with epoxy resins, offering durable repairs that can last for more than 20 years. Its global endorsement and compliance with industry standards (ISO 24817, ASME PCC-2 401, and certifications from Lloyd’s Register, ABS, and DNV) attest to its reliability and capability to withstand extreme conditions.
INSONO is a cutting-edge, non-destructive testing technique designed for inspecting composite repairs applied to metallic components. INSONO has been developed to ensure the condition and integrity of composite repairs. It offers operators and regulators in installation, long-term performance, and provides evidence supporting the life extension of the repair.
Quickflange is a revolutionary approach to flange-to-pipe connections, offering a weldless, permanent and cold work alternative that significantly deviates from conventional welding methods. This innovative system employs a modified standard flange equipped with patented internal grooves, designed for a seamless slide-over installation on the pipe end.
The Quickflange technology facilitates rapid and safe installations, eliminating the need for ‘hot work’ and, thereby, reducing associated risks and costs. Suitable for a variety of pipe sizes, pressure classes, and materials, Quickflange not only offers up to 80%-time savings but also achieves a remarkable 57% reduction in greenhouse gas emissions compared to traditional methods. This efficiency, coupled with its versatility, positions Quickflange as an environmentally friendly and cost-effective solution for industry needs.
Sky-Futures is a leader in the Unmanned Aerial Systems (UAS) industry. With a focus on safety and efficiency, Sky-Futures’ drones conduct thorough inspections and emissions monitoring, significantly reducing the need for hazardous human entry. Revenues have followed a similar pattern,
▸ Successful diversification process across regions and sectors.
For industry
▸ Be a solution-provider, not just a service-provider.
▸ The industry needs to collaborate to realistically address net zero –there are many opportunities.
For government
▸ Approach the net zero challenge honestly; set realistic roadmap – one that’s achievable from a transition and commercial point of view.
Key products and services: specialist maintenance, inspection, repair of energy assets and critical infrastructure.
Main industries served:
▸ Oil and gas
▸ Renewables
▸ Conventional power
▸ Others (non-energy): defence, process industries, utilities & infrastructure
Headquarters: Aberdeen, UK
Year established: 1992 (ICR since 2011)
Number of employees: 268
Revenue: £50m
providing confidence that the company’s diversification plan is working. In 2023, 40% of revenues were derived from international business outside of the UK, with 15% originating away from the traditional core client base within oil and gas. The firm has grown its turnover from £42m to £50m this year, with a 50-50 split between UK and overseas work, and an 80-20 split between oil and gas and diversified verticals.
Achieving greater customer alignment through Growth Hub
Story type
#innovation (main category) #collaboration, #diversification
Benefits
▸ Growth Hub brought over £40m in new revenue in 2023.
Yogini Pekarskis Growth Hub Manager
Transforming the culture and operations of a large company is never a simple task. With intricate structures in place and a natural resistance to change, the process can be daunting, especially when supporting tens of thousands of employees.
IMI’s story, therefore, is immensely impressive. Recognising the shortcomings of its traditional market approach, the company boldly implemented a highly effective growth hub strategy to better cater to customer needs. Having seen several new products developed that are now driving tens of millions of pounds in new revenue, IMI stands as a true success story.
The challenge - With an annual revenue surpassing £2 billion, a workforce of nearly 11,000 employees, and an installed base of 180,000 severe service valves supporting critical industrial plants and processes worldwide, IMI commands great respect in the energy sector.
Specialising in flow control solutions for vital industries including oil and gas, power generation, petrochemical, marine, pharmaceutical, and other heavy industries, IMI has built a reputation for delivering dependable and efficient flow control systems, ensuring smooth and safe operations even in the most demanding industrial environments.
In many ways, the company eliminates the unique challenges of others. However, this is not to say that it hasn’t been immune to its own obstacles.
Traditionally entrenched in the oil and gas sector and conventional power plants, the company has been compelled to pivot its business in response to the global push for decarbonisation, assisting its clients in reducing their carbon footprint.
This strategic shift, aimed at mitigating the environmental impact of traditional energy processes and facilitating the transition towards renewable energy sources, posed both significant challenges and opportunities for IMI. Moreover, the company’s decision to embrace transformation coincided with a period of profound global political instability, heightening energy security concerns and necessitating greater agility and adaptability.
Internally, however, fostering agility and adaptability has been a formidable hurdle for IMI. Historically, the company has experienced a siloed approach to product development, with engineers working in individual teams and generating ideas internally rather than those driven by market needs. And by the company’s own admission, this approach has hindered market insight and led to unrealised development potential.
The solution - To overcome these issues, the company opted to establish a new internal Growth Hub in 2018, designed to foster innovation, insights, and agile methodologies.
The pivotal change brought about by the Growth Hub was a shift in perspective, moving from an inward focus to actively engaging with customer insights, ensuring alignment with customer demand, and placing customers at the core of operations.
Under the Growth Hub initiative, IMI teams worldwide are tasked with returning to their respective regions to identify customer pain points and validate them. Embracing a sprint mentality, teams work in intensive two-week cycles over three months. The process involves testing ideas in the first week and learning from these tests to refine minimal viable propositions in the second week, with regular check-in calls being an integral part of the process. At the end of each three-month cycle, ideas are presented to consultants and IMI’s leadership for evaluation.
In the inaugural year of the Growth Hub, only one idea received backing, leading other teams to pivot or abandon their concepts. This endorsed idea, however, subsequently launched as EroSolve Wet Steam, emerged as one of IMI’s fastest-growing products. Specifically, EroSolve Wet Steam upgrades the valve plugs, stem assembly, cage, and seat ring allowing steam valves in power plants to better deal with more frequent cycling of the plant – a consequence of more renewable energy sources feeding into the power networks. The solution engineers sealing surfaces that optimise droplet impingement angles to reduce their impact. Its use of special, erosion-resistant hard-facing materials also enhances trim life in a solution that can be easily implemented in any make of control valves for steam applications in power plants.
▸ Mindshift promoted in the business.
Key products and services: flow control solutions for vital industries.
Main industries served:
▸ Oil and gas
▸ Conventional power
▸ Nuclear power
▸ Hydrogen
▸ Carbon capture
▸ Others (non-energy): marine, pharma, iron and steel
Headquarters: Birmingham, UK
Year established: 1862
Number of employees: 10,900
Revenue: £2.1bn
Revenue from exports: N/A
More recently, Growth Hub has also led to the development of Retrofit3D, which focuses on the engineering of bespoke drop-in replacement internal components, including disk stacks and valve trims (inclusive of seat and plugs), ensuring the body of the valve can remain in situ throughout the process. Through these product developments, the programme has been incredibly successful, driving over £35m in revenue in 2023.
It’s not just the numbers that indicate the company’s success, however. Indeed, Growth Hub has changed the mindset of the entire business, driving a culture of customer-focused innovation. With such feeling now also being adopted in other functions such as sales and operations, the firm has fundamentally improved the way in which it does business.
the pandemic just months after opening for business
Irfan Fadzalisham Technical Sales Engineer
How is Impressive Logging Services thriving?
By focusing on delivery, investing in technology and dedicating time to networking, Impressive Logging Services has been able to overcome a huge testing beginning to its existence. Now, with a growing contract pipeline and expanding team, the company can look ahead to the future as a steady service partner for well operators.
The challenge - The oil and gas sector relies on an extraordinary variety of niche and highly specialised services to function on a daily basis.
For well operators, one of those is cased hole logging, a technique used evaluate the condition of a well after it has been cased and cemented. It involves lowering specialised logging tools into the cased well to gather data about the formation, cement bond, casing integrity and other crucial information.
It is particularly useful for detecting potential problems, such as casing corrosion, cement channelling, or formation fluid movement behind the casing. This information helps operators make informed decisions about well remediation, stimulation, or abandonment, ultimately enhancing the safety and productivity of oil and gas wells.
This has been the domain of Malaysia’s Impressive Logging Services since it started in December 2019. However, despite knowing it could add value to the market and being fuelled with optimism as it set out, little did the company’s leadership know that the Covid pandemic would arrive a matter of weeks later.
The solution - Indeed, the arrival of Covid-19 in early 2020 almost derailed Impressive Logging Services’ plans due to the travel restrictions imposed by the Malaysian government.
As the pandemic spread, the company noticed potential customers were cutting costs and were therefore reluctant to invest in new technology. Meanwhile, those that did utilise Impressive Logging Services’ products during the Covid period later experienced cash flow problems and began delaying payments.
These issues posed a huge challenge for the fledgling company, but it was not to be deterred.
Within a few months, it managed to secure its first contract despite the pandemic restrictions. Following the successful execution of that initial project, the company secured five more contracts and achieved a 20% increase in the number of wells serviced.
In these early days, the firm’s strategy was to ensure jobs were completed on time, within stipulated costs, and that customers were satisfied with the results. Doing so, its leadership believed, would lead customers to recommend Impressive Logging Services to other players operating in the Malaysian oil and gas industry.
Another strategy employed by the company involved the introduction of new products inspired by the latest technological innovations. For example, in 2021, it launched a new Cement Scanner, enabling operators to achieve significant reductions in costs and job completion times. Thanks to this product, Impressive Logging Services secured an additional 13 wells through the course of the year.
A third prong of the firm’s strategy has centred around marketing and enhancing visibility around its products and capabilities. Here, Impressive Logging Services decided to present at an SPE Conference in Bali, where most Southeast Asian operators were present. Off the back of this event, the company received a number of enquiries from operators in across the region, including organisations in Brunei, Thailand, Indonesia, Sabah and Sarawak.
The Impressive Logging Services pipeline grew steadily throughout 2023, with six new contracts added and another existing agreement extended by three years. Alongside this, the company’s headcount is also increasing as work volumes ramp up. Starting out in 2019 with just three colleagues on the books, the firm now has a team of 25 employees with plans to expand this further. This will help to drive up revenues, which are forecast to
#resilience (main category)
#technology
▸ Six new contracts and existing agreement extended by three years.
▸ Revenue growth and forecast to reach RM20m in 2024.
For
▸ To the young engineers, opportunities don’t come twice. Whenever we see a chance for us to thrive, take it because we don’t know if the opportunity may come back or not.
▸ Always prepare back up plans from plan B, Plan C and etc. Scenario simulation is the key in preparing ourselves for any hurdle in front. With that we able to manoeuvre business strategies according to any situation at that point in time. The key here is to be creative.
▸ Our story is closely related to the Covid -19 happening back in 2020. We appreciate the government efforts in ensuring the disease is contained. In the future, if another virus outbreak happening, we hope to see a better planning on containing the outbreak and assist small business owner to be back on their feet again.
Key products and services: logging services from well intervention to plug and abandonment phase.
Main industries served:
▸ Oil and gas – 100%
Headquarters: Kuala Lumpur, Malaysia
Year established: 2019
Number of employees: +25
reach RM20m in 2024 after the organisation turned over 15m last year and 5m in 2022.
After starting out in the most trying of circumstances, Impressive Logging Services has emerged as a growing enterprise which is ably serving the region’s oil and gas sector.
Commercial Manager for Power Utilities and Renewables
How is Induscabos Condutores Elétricos thriving?
From navigating Brazil’s hyperinflationary period to navigating ambitions to enter export markets, Induscabos Condutores Elétricos has consistently adapted, evolved and innovated to find new, fruitful opportunities. With a focus on operational expansion, technological advancements, and unwavering commitment to client satisfaction, the company stands as a beacon of quality and innovation within the Brazilian industry.
The challenge - For nearly five decades, Induscabos has proudly held its position as one of Brazil’s foremost manufacturers of high, medium, and low voltage electrical wires and cables. Located in the bustling city of Poá, São Paulo, the firm operates out of an impressive 80,000 square meter industrial complex, housing four production units and two stateof-the-art laboratory facilities.
From this innovative hub, Induscabos continually enriches its extensive product range, meticulously crafting solutions tailored to the exacting standards of professionals across various sectors. What began as a modest team of entrepreneurs crafting components for household appliances like refrigerators and stoves has evolved in step with Brazil’s dynamic market demands. Today, the company serves as a vital partner to key industries, spanning power utilities, transmission and distribution, oil and gas, mining, steel, paper, and renewables.
Throughout its history, Induscabos has faced a range of challenges, both externally and internally. The memory of Brazil’s hyperinflationary era circa 1990 lingers, prompting a strategic pivot towards more lucrative ventures, particularly within the energy and construction sectors. Similarly, in 2010, the company embarked on a significant venture into medium-voltage cable production, necessitating substantial investments in infrastructure and certifications. Additionally, the firm has also had to overcome hurdles associated with its forays into export markets. Having begun with a focus on Latin America and since expanding into other regions including the US, the firm recognised that it needed to strike up key strategic partnerships in order to be more successful.
The solution - Indeed, while challenging, each of these strategic shifts has proven not only
prudent but also immensely rewarding for the company. Faced with critical junctures, Induscabos has consistently turned in the right direction, adapting in an informed manner in line with market demands and opportunities.
The decision to invest in medium-voltage cables in 2010 exemplifies this approach, emphasising quality, industrial capacity, and technical prowess. Recognising the unique demands of this niche, the company embarked on a targeted strategy, investing in specialised infrastructure and laboratories to meet the specific demands of selected clients.
This strategic choice finds its roots in the company’s overarching philosophy, which prioritises quality over quantity. Resultantly, Induscabos has consciously opted to prioritise relationships with a select number of clients who closely match its own ideals and standards. In doing so, it ensures that its resources and efforts are directed towards serving those customers that will benefit most from its offerings.
Focusing specifically on the medium voltage and high voltage range, a segment then occupied by a mere three companies at Brazilian market, the firm seized the opportunity to differentiate itself through innovative cable designs with heightened protective features. This marked a pivotal shift from conventional construction-grade cables to technologically advanced solutions, catering to the needs of wind and solar parks that have proven crucial to the firm’s current success.
Today, this segment commands a notable 30 to 35% share of the company’s operations, a testament to the efficacy of this strategic direction. Further, success in this domain has been further bolstered by the company’s partnership with US firm Southwire.
Critically, this collaboration has served to significantly increase Induscabos’ export volumes, these now accounting for 20% of total sales, with more than a quarter of them directed to the US market. Leveraging this partnership has also proven instrumental in surmounting challenges such as recent aluminum shortages that emerged as a result of geopolitical factors.
Anchored in a commitment to continual innovation, Induscabos is constantly expanding its product portfolio, tailoring solutions to the evolving needs of the medium voltage and concessionaire market.
Story type
#innovation (main category)
#exports
▸ Induscabos’ strategy to focus on the medium and high voltage range paid off as this now represents 15% to 25% of company’s operations.
▸ Partnership with the US firm Southwire increased Induscabos’ exports volume, reaching 20% of total sales.
For industry
▸ Start studying again. Technology has evolved a lot since our university times.
▸ Previously, there would be, in one university for reference, 400 engineers graduating every year, now there are 80. Soon we will face a lack of skilled labour in the younger generation.
For government
▸ Legislation is good but bureaucratic, government should simplify processes.
Induscabos Condutores Elétricos at a glance:
Key products and services: manufacturing of electrical wires and cables.
Main industries served:
▸ Distribution and consumption: 35%
▸ Power generation: 35%
▸ Exports: 20%
▸ Others (energy): 10%
Headquarters: Poá, Brazil
Year established: 1976
Number of employees: 400
Revenue from exports: 20%
Maintaining a steadfast commitment to leadership and excellence, the company remains poised to embrace new opportunities moving forward, be it through operational expansion, facility upgrades, product development, or the acquisition of cutting-edge technologies, all in service of sustaining competitiveness and propelling growth.
Countering COVID-19 with a solutions-based exporting strategy
Martin Hess
CEO
How is INTERTEC-Hess thriving?
INTERTEC-Hess embarked on a transformative initiative, culminating in the development of PERI SHELTER, an innovative outdoor cabinet solution built to streamline operations and minimise design costs. By embracing a solutions-focused approach and diversifying its offerings, the company has experienced remarkable growth, with order intake almost doubling between 2021 and 2023.
The challenge - Established in 1965, INTERTEC-Hess has cultivated a workforce of 350 specialists renowned for providing unique solutions for the reliable protection of highly sensitive field instrumentation. Over one million of these enclosures have been sold.
Headquartered in Germany, much of its business has historically been derived from its home nation and other European states such as the UK and Netherlands, alongside several territories in the Middle East. However, it is the firm’s North American subsidiary that forms much of the focus of its survive and thrive story.
With a 45-year presence in the region, INTERTEC-Hess had already established its presence, but fully capitalising on the growth potential in key global markets such as the US and Canada presented a new challenge.
To bolster its market appeal, the company embarked on a strategic initiative to reevaluate its product offerings and concepts, seeking opportunities to optimise its solutions for field equipment protection. By identifying and addressing customer pain points, INTERTEC-Hess aimed to enhance its support for clients while positioning itself for sustained growth in dynamic markets.
The solution - Through extensive research and development, the company identified a significant market gap for compact yet robust protective cabinets designed for easy operation in harsh environmental conditions and climates.
Critically, the firm quickly encountered the common challenge of securing advanced protection solutions for complex automation systems, with stringent space constraints and demanding climatic conditions being a combination that typically caused problems for clients.
To address this, it conceived a complete solution known as PERI SHELTER – an innovative outdoor cabinet solution tailored to house field instrumentation and process control systems such as satellite instrument houses (SIH) or remote instrument enclosures (RIE).
This solution, characterised by its accessibility from the outside, streamlines operations by eliminating the need for internal access points, control panels, and corridors, thus minimising space requirements and associated design costs.
The IP65-certified cabinet, constructed from durable GRP material, ensures safe operation even in hazardous environments, with interior pressurisation preventing the ingress of corrosive chemicals. Indeed, the firm’s GRP material in itself is also extremely resistant to highly corrosive atmospheres.
Previously, customers would typically procure enclosures alongside instruments, but INTERTEC-Hess has evolved beyond this model, offering integrated equipment and products tailored to meet diverse client needs.
This strategic shift from being a single-product manufacturer to providing complex, bespoke solutions has propelled the company’s growth significantly. Order intake has surged from £24.8m in 2021 to £41.3m, reflecting the success of this approach.
With no other organisations embracing the firm’s solutions-focused approach, INTERTEC-Hess is well-positioned to further leverage market opportunities and achieve significant sales growth in the future.
Moreover, the company is proactively planning to capitalise on emerging opportunities in promising green markets in the UK, including the burgeoning hydrogen sector. While acknowledging the challenges inherent in new industries, INTERTEC-Hess remains committed to seizing competitive advantages as a successful first mover in these innovative sectors.
Story type
#services & solutions (main category)
#innovation, #optimisation
▸ Order intake growth from £24.8m to £41.3m.
▸ Optimistic hope for the future and plans to capitalise on green markets in the UK.
▸ Have a broad education – don’t limit yourself to one industry, have a practical education and theorybased education.
▸ Make something that works in the market in the future, as government funding may not be there.
▸ Free trade agreements to make trade easier across boarders –Brexit has meant we have lost access to some markets.
INTERTEC-Hess at a glance:
Key products and services: portfolio of solutions for the protection of instruments and analysers for any location.
Main industries served:
▸ Others (energy: natural gas, LNG, electrical, e-houses, battery storage and smart grid) – 30%
▸ Oil and gas – 15%
▸ Carbon capture – 15%
▸ Hydrogen – 10%
▸ Others (non-energy) – 30%
Headquarters: Neustadt/Donau, Germany
Year established: 1965
Number of employees: 350 Order Entry: £41.3m
Revenue from exports: 80%