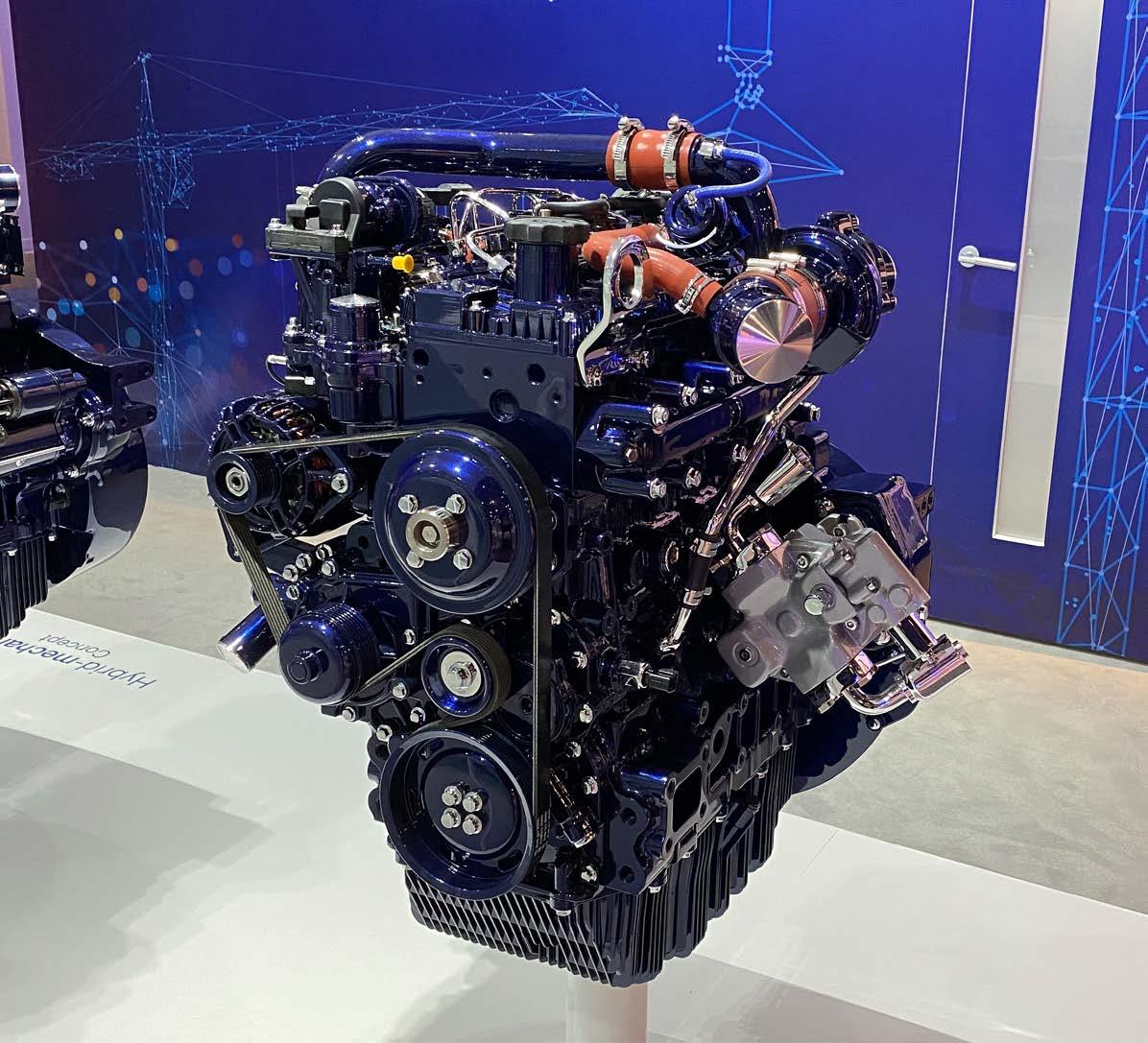
10 minute read
EXCLUSIVE Alex Woodrow, MD of Knibb, Gormezano and Partners (KGP), reviews the move to low carbon machines at this year’s IVT Expo Virtual Live Conference
IVT Expo Virtual Live saw 40 live presentations and a number of panel discussions, reviewed Construction Equipment and related non-road machinery powertrain and HMI (Human-Machine-Interfaces) technology developments. Presentations can be viewed online HERE .
Here are Alex’s notes on a cross-section of the presentations…..
Advertisement
Dockoon Yoo, Leader of Advanced Engine Development - Doosan Infracore, focussed on hybridisation opportunities in the medium power/energy segment. Doosan’s 48V mild hybrid with a 55kW engine is expected to be cost competitive with a 75kW machine, due to savings in aftertreatment cost. However, it will offer significant fuel economy improvements leading to lower CO2 emissions. Fitted in a Doosan compact wheel loader the original 3.4l engine is downsized to 2.4l in the mild hybrid, complimented with a 20kW electric machine. The mildhybrid will be one solution in Doosan’s portfolio including Natural Gas (CNG/LNG), full hybrid and fuel cell powertrains.
Ahcene Njdemi, Volvo CE Electro-Mobility Leader summarised the Volvo Group's broader de-carbonisation activities. A 100% reduction in fossil fuel consumption is one of three tiers of the Group which also include “100% safe”, and “100% more productive” machines. The initial phase of its strategy has been the launch of fully electric compact wheel loaders and mini excavators. In these segments Volvo CE has stopped development of new diesel engine models. Originally launched at Bauma in 2019 the machines are now shipping to customers, after extensive testing in Europe and the US, amongst other markets.
Volvo’s electric mini excavator has a 20kWh 48V battery powering a motor running its hydraulic pump. Four hours operation can be achieved in most end uses before recharging is required. On-board charging is complemented with a fast charging solution offering from Volvo, and the group is also likely to offer a solution for off-grid charging. Access to public 48V charging for its compact machines will however be a barrier, as most road vehicle charging will be high voltage, not 48V.
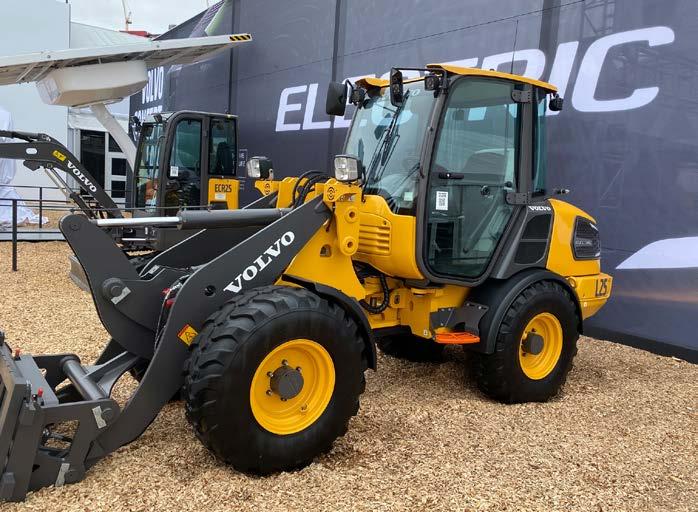
After the launch of the compact electric machines a larger EC55 all electric excavator was launched at Bauma China in November 2020. As part of the strategy Volvo’s next smallest machines will be increasingly electrified from 2022-2023, medium machines circa 2025, and the heaviest machines closer to 2030. The strategy will use both battery electric and fuel cell technologies, likely to use cells from the Group’s joint venture with Daimler AG.
Jyri Kylä-Kaila, CEO of Epec OY’s examined the development of a hybrid system for larger machines. As of part of Ponsse Group, a producer of forestry machines in Finland, Epec is a specialist system supplier. It identified four main drivers for its solutions - CO2, TCO (Total Cost of Ownership), Productivity and Safety. Its hybrid system for a 200kW machine, aimed at reducing CO2 20% through lifecycle assessment (LCA) and systems engineering. The resultant ISO14040 guided LCA estimate is that 93% of CO2 comes from machine use, 4% from materials manufacture and 3% from maintenance (hydraulic oil manufacturing). The difficulty of sharing LCA across complex companies, as in the CE sector, is a barrier to adoption. It also identified less maintenance as meaning less business for service companies – which will therefore need new a business model.
Julien Wachter – VP Research and Innovation at Manitou described its strategy. Manitou is expecting electrification to cover products wider than traditional forklift and warehouse trucks. All construction machine ranges will have zero emission options including Telehandlers and Skid-Steer Loaders. It has implemented its eco-design tool across the complete design process as part of its strategy.
The first all-electric product is its 200ATJ all-electric telehandler. It sees opportunity as the C40 Cities Construction declaration 2030 will require use of zero emission construction machinery from 2025. As part of the declaration, Manitou is providing machines for construction of a new port which will have green hydrogen production onsite. In a life cycle analysis of the project 40% of emissions from its construction are from machines, and this is aimed to be reduced by 80% by using hydrogen. 75% of batteries are expected to be reused to further reduce emissions.
Dr Niall Caldwell, Director, Digital Displacement, Danfoss Power Solutions, summarised eco-options for excavators. Its assessment of over 1m excavators estimated the global population contributes more than 80mt of CO2 per year, higher than total CO2 emissions of Denmark and Scotland combined. One solution is to make them electric but with 10x high load factors than a typical car, limited charging infrastructure and an often remote environment this is a challenge. The availability of green energy was also raised, as an estimated 105TWH of energy would be required.
Danfoss’ Digital Displacement pump enables and disables pistons in real time, using computer controlled valves. The better pump efficiency, improved system efficiency, reduced energy losses enables significant downsizing or increased machine productivity and facilitates more efficient energy recovery. A number of architectures will be available - SA1 - replaces existing pump, SA2, adding improved pump efficiency, reduced valve losses and energy recovery. Its SA1 current proof of concept – enables 15% fuel savings and 15-20% improved productivity. The SA2 currently a concept - 30% fuel savings, 20-25% productivity improvement and SA3 - 50% fuel savings, over 25% productivity improvement. Supported by UK's Advanced Propulsion Centre the solutions reduces battery size required, plus charging capacity and energy required. However policy is needed to incentivise improved system efficiency, science based targets, and infrastructure. A standard test cycle is also required, as in forklift truck market.
Calstart - Bill Van Amberg, EVP of Calstart reviewed the organisation’s progress in California. A recent programme has seen a rapid programme of technology transfer from the heavy duty on-road segment to off-road – the so called CORE - Clean Off-Road Equipment Program. Calstart, a non-profit established in 1992, has adopted five waves supporting a beachhead from transit bus through more demanding applications as technology matures, supply chain improves and cost reduces. It cited examples of BYD and Volvo, where bus hybrid and electric applications transferred into truck, marine and off-road sectors.
Supporting the programme is the Clean Off-Road Equipment Voucher Incentive Project (CVIP) funding which has included $44m for Terminal Tractors (82 vouchers up to $200,000 each, 36% of total funding), Refrigerated Trailers ($65,000 each, 17%), Railcar Movers ($500,000 and 11%), Mobile and Ground Equipment Power Units ($300,000, 6%) and Large Forklifts (Up to $200,000 each for 22 units).
Philipp Hermann, Market Segment Director, Danfoss Power Solutions presented Danfoss’ assessment that 300-400Mt of CO2 is produced by construction machinery annually. In the assessment, cost and infrastructure are considered the two main barriers. The group is focussing much of its work on excavators over 50kW, which contribute significantly to the total CO2 from construction machinery. Looked at scenarios for battery costs, €200-€400 cost, needs to be below €200 but likely to be €300 in the time frame. However combining with its Digital Displacement technology will allow closer to €400 per kwh of battery cost.
As well as offering machine technologies it has developed a concept for on-site charging and an energy storage solution. As an example, it presented a 400V input battery pack of 300kWh capable of charging machines at 300kW at 600-800VDC.
Mario Daellenbach – Project Engineer at Bucher Hydraulics examined developments in electro-hydraulics. Bucher’s advanced pumps and electronic control enables further automatic and smaller battery sizes for electric machines. Its AX Pump with lower friction, low starting torque and other performance enhancements has engineered in an electric refuse collection vehicle, reducing noise and battery size. Systems analysis showed that switching from a standard external gear pump to its new AX high performance pump allowed the battery size to be reduced from 171KWh to 125kWh, reducing weight from 856kg to 625kg, cost from 60,000 Euros to Euros 44,000 (Euro 350kWh at low volume).
In hydraulic machines Bucher’s assessment shows a reduction in battery size by 75% as advanced hydraulic pumps with variable speed drive, and energy recovery improves the number of cycles on a 20kWh battery from 150 to 625.
Romain Nicolas discussed Siemens PLM's simulation of a compact excavator assessing electrical requirements, battery sizing and validation of a new excavator concept. 34kWh energy is required for a seven hour digging cycle mission profile. 46.1kwh is required for SOC delta of 80%. With given chemistry and voltage etc. the equipment voltage size can be defined. Different chemistries can then be modelled. Allows ageing of different chemistries and profiles with different charging strategies. After 5 years the battery estimated to fall by almost 10%, but remaining above 7h run time.
Giacomo Fiocchi - Hybrid system ePower Systems Carraro presented the group’s solution for Agricultural and Construction applications. As with Doosan Infracore’s mild-hybrid the Stage V 55kW engine is coupled with a motor to provide with support in transient phase where NOx emissions are high. The Carraro configuration uses a Nickel-Metal Hydride (NiMH) battery, sized according to application. The belt driven motor generator in Carraro’s vineyard application has a 48V 1kWh battery, Permanent Magnet motor. Batteries can be sized depending on application. On inclines the hybrid system can run for two minutes at full power, with battery discharging from 80 to 20 percent SOC. When recharging from the engine the battery requires four minutes to charge fully. Carraro assessed its solution over a typical compact tractor life-cycle of 10,000. For these applications, about 55% of the total hours require power over 55kW, 25% of which is spent spraying, 15% cultivating and 15% travelling, require over 55kW. As a result the mild Hybrid performs similar to 75kW in over 95% of applications. Fuel economy savings over 18% in therefore achieved in these heavier applications, with the Adblue saving included. Fuel saving net benefit compared to additional cost of hybrid battery, harness, and other components, 10.3% CO2 saving. Improved vehicle performance. Neha Roy - Innovation lead highlighted Hyster-Yale’s concept for port handling equipment. A 36t laden container handler produces 128 tonnes of CO2 per year running for 3,000 hours and consuming 16 litres of diesel per hour. 3 applications and 3 options offer a scalable path for low, medium and high load applications with battery and fuel cell options. The fuel cell range extender option it is proposing uses its Nuvera Modular 45kW fuel cell ‘engines’. In that application four integrated hydrogen tanks allow a long operation and quick refill time, with the Lithium-ion battery for peak power demand. It Hyster’s assessment as much as 0.45kwh to 1.8kWh per cycle can be recuperated, the former braking from 23kmh/H at 80t, the latter lifting a 52t load 13m gives 1.8kWh saving. Hyster’s data collection has allowed it to model various cycles and size energy storage accordingly. Its data shows machine usage can vary widely from a minimum of 1.3 hours per day to a high of 15.7h, influencing powertrain selection and charging accordingly.
Aradex, based in Germany, has been part of the Weichai Group since 2019. The group focuses on power electronics, converters and motors for hybridization of machinery to reduce TCO and improve productivity/performance. It has worked on a full electric dozer with group company, Shantui, which will be followed by a hybrid and fuel cell version. It has also integrated systems on a full size rigid dump truck running from fuel cells. Hybrid versions of machines offer 30% fuel economy savings versus conventional machines, as well as reduced wear and tear. It identified parallel hybrid as being suitable for critical applications where the configuration offers higher reliability and redundancy in the driveline.
Manuel Kagelmann - Head of product portfolio management batteries Webasto Group started with HV heater in 2015. €43m in 2019 revenue. Standardised or customised packs for small or large OEMs. It identified high voltage critical for fast charging for larger batteries. In partnership with Danfoss it has converted a mid-sized 13T wheel loader to all electric operation. 4 Webasto standard packs are adopted, 35kWh each, totally 140kWh, at 280-400V, with energy density of 203 Wh/l and 118Wh/kg. Cycle life of over 3,000 at 1C/1C charge/discharge rates, with prismatic NMC cells. The optional 800V pack. Critically the pack is VDA compliant, offering upgrades with future cells. Webasto’s cooling technologies improve the durability and performance of the cells over the life of the machine.
The next IVT Virtual Live will take place on 21st & 22nd September 2021.
“Knibb, Gormezano and Partners (KGP) is a specialist automotive consultancy focused on powertrain technology in the Commercial Vehicle (3.5t GVW+) and Non-Road Mobile Machinery segments. Since our foundation in 1988 we have helped over 500 companies worldwide grow and globalise”. Contact Alex Woodrow via www.kgpauto.com.