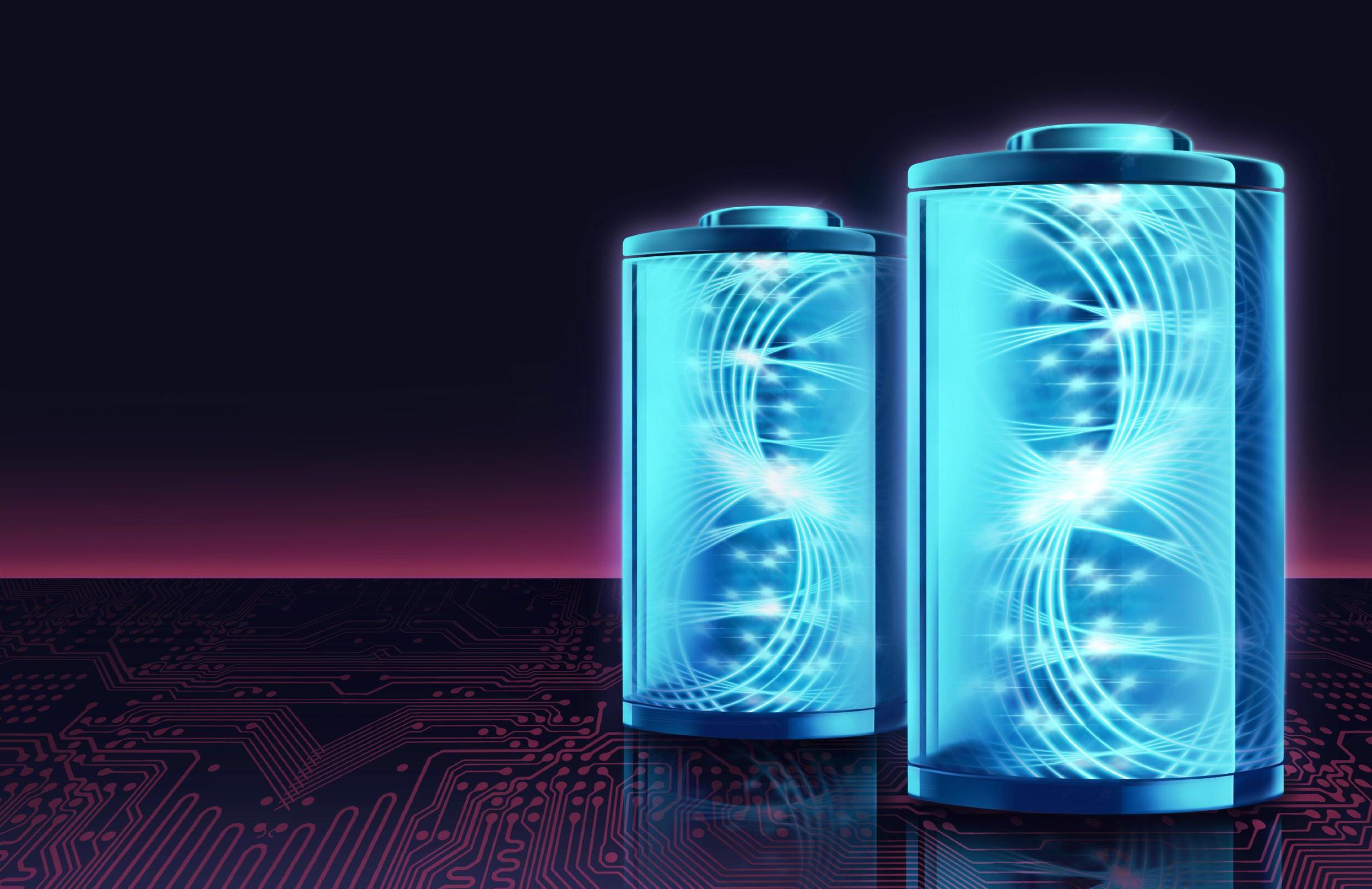
9 minute read
The Route to Alternative Energy
Continuing our series on perspectives on future fuels, Chris Sleight, managing director of Off-Highway Research and a former construction journalist, gives his thoughts on how the construction equipment industry will tackle the alternative energy challenge.
As in the on-road world, we can expect construction equipment to move away from fossil fuels to alternative energy sources. Although the off-highway industry tends to follow what happens in the on-road world, it also has some unique challenges. That means the journey for our industry won’t be a carbon (or no carbon) copy of on-highway developments.
Advertisement
Diesel v alternatives
Although alternative energy now looks like a question of ‘when’ rather than ‘if’, the timeline is hard to predict. There are many factors driving both the decline of diesel and the rise of replacement energy sources.
Cost is being added to diesel power and has been for some time. Ever-increasing regulation on emissions has meant more expensive engines with elaborate after treatment being introduced, along with more consumables like AdBlu. Although we have paused for the moment at Stage V in Europe, while the rest of the world heads towards Stage III-IV equivalents, it would be naïve to think this will be the end of diesel engine emission regulation.
The move away from fossil fuels in general, and the demonisation of diesel in particular, is likely to mean that law makers around the world will remove tax breaks and subsidies. An example of this is the change currently taking place in the UK around the permissible uses of cheap ‘red diesel’. As well as the loss of favourable treatment, doubtless taxes on fossil fuels will continue to be increased, while the oil price is always a source of uncertainty in the future.
This will all tilt the economic balance further away from diesel.
On the other side, technology around alternative fuels will improve, delivering better efficiency and greater power density, while increased scale will lower prices. That could be accelerated if governments use policy to drive this change. These may be carrots like subsidies, tax breaks or other incentives, or they may be sticks, such as the setting up of zero emission zones.
In the off-highway world, the alternative fuels focus to date has been on electrification. This is a reality today. Many companies, including major suppliers like JCB and Volvo, now have electric machines commercially available. More will follow. The greatest opportunity for electrification in construction equipment is compact machines. Depending on how this is defined, it could account for as much as two thirds of the 1.1 million units-per-year global construction equipment market. As time goes on, technical and economic feasibility will change and bigger electric equipment may become viable as batteries get cheaper, better and more compact.
Even today electrification is not limited to small machines. Liebherr, for example, now offer a 220 tonne capacity battery-powered crawler crane, and several manufacturers have shown prototype batterypowered 20 tonne excavators at exhibitions
The need to be lightweight is a burning issue in the on-road world, but it is less important in many off-highway applications. Battery weight
is always a penalty in on-road applications, but many construction machines require a counterweight, so a heavy battery is not necessarily a problem in those machine types. But in some, particularly hauling equipment, battery weight will be a headache.
There may also be operational benefits to electrification. Very little maintenance is required on a battery and electric motor. Compare that to the daily checks and regular servicing required to keep a diesel engine happy and healthy.
Things could improve further with true all-electric machines. Rather than using the electric motor to turn a hydraulic pump, the obvious next step is for electric motors and actuators to facilitate machine movement and functions. This would remove expensive hydraulic components like the pump as well as the associated maintenance and potential for downtime (no more hydraulic leaks and hose bursts!).
Greater inherent efficiency could also be expected from all-electric machines. Going straight from electrical energy to the kinetic energy of the machine removes the losses due to the conversion to hydraulic energy as the steppingstone between battery and machine movement. This does not mean electric machines will be maintenance and mishapfree, but they have the potential to be easier and cheaper to maintain than current diesel/hydraulic technologies.
Construction considerations
Arguably the bigger question around electrification in construction – and the key difference to the on-road world – is how do you charge equipment? If the machine is on an urban or fixed site, or returns to a depot every night, there may be the opportunity to charge it from the electric grid. If not, which will be the case for many machines, on-site power is likely to come from a diesel generator. Charging an electric machine in this way would spectacularly defeat the object of the exercise.
The availability of grid power could be significant in a deeper way for construction equipment. This is well-illustrated by Liebherr’s large crawler crane, which can operate ‘plugged-in’. Unlike onroad applications, where mobility and travelling long distances is everything, many construction machines move very little in a working day. Even over many months a machine may stay on the same site of a few hundred square metres. In that case, why worry about building a battery pack which can run all day on a single charge? It might be feasible to run the machine ‘plugged in’.

Battery politics
A final and perhaps vaguer societal concern on electrification is around batteries themselves. Current technology requires lithium, nickel, cobalt and other rare earth metals to manufacture batteries. These resources are finite and by definition mining them has an environmental impact. The sustainability of a battery-powered world is therefore, at best, relative. In addition, these elements are not evenly distributed around the world. Possession of the ores therefore has the potential to create geopolitical tension in the same way oil has many times throughout history.
Finally, but perhaps more solvable is the question of recycling. A quick search of YouTube will illustrate the kind of fireworks which result in a lithium ion battery being incorrectly disassembled (or hit with a hammer by an idiot teenager). Clearly this problem has to be overcome and there has to be a push on battery recycling if they are to become a more sustainable part of our future.
The un-electrifiable
There are machine types in mining and construction, such as large dump trucks and loaders, where battery power does not look feasible for the foreseeable future. There may be other ways of electrifying mining, such as overhead lines and pantographs, but there will still be many cases where a combustion engine will remain the only solution. But a combustion engine does not necessarily mean a fossil fuel. It could also mean hydrogen. This element is often discussed in terms of hydrogen fuel cells, which react hydrogen with oxygen to produce electricity, with just water as the by-product. In this context they are often seen as an alternative to batteries. We therefore think of them as being most viable for small to medium machines, although JCB has developed a prototype 20 tonne class hydrogen fuel cell excavator.
Although hydrogen fuel cells have been around for decades, it is early days in their application in construction equipment. It therefore remains to be seen where their practical and economic limits lie.
However, hydrogen can also be burnt in a combustion engine in much the same way petrol, diesel or natural gas can, and this may be the solution for much larger mobile machines, where electrification looks too expensive or just not possible.
The problem with hydrogen is that it doesn’t occur naturally in its elemental form on earth, so has to be manufactured. It is therefore only interesting if it can be manufactured with renewable energy in an environmentally sustainable process. Many current industrial processes produce CO2 or other pollutants as a by-product, but this need not be the case. Hydrogen can be produced by electrolysing water, for example, where the only by-product is oxygen.
Hydrogen may also have advantages in construction, particularly for sites without mains power, as the fuel can be trucked to where it is needed. This is not as straightforward as trucking diesel around, as hydrogen has to be transported as a high pressure gas or extremely cold liquid. But it is nevertheless transportable. Consequently hydrogen could be used to either fuel construction equipment directly or to fuel hydrogen-powered generators to charge electric equipment.
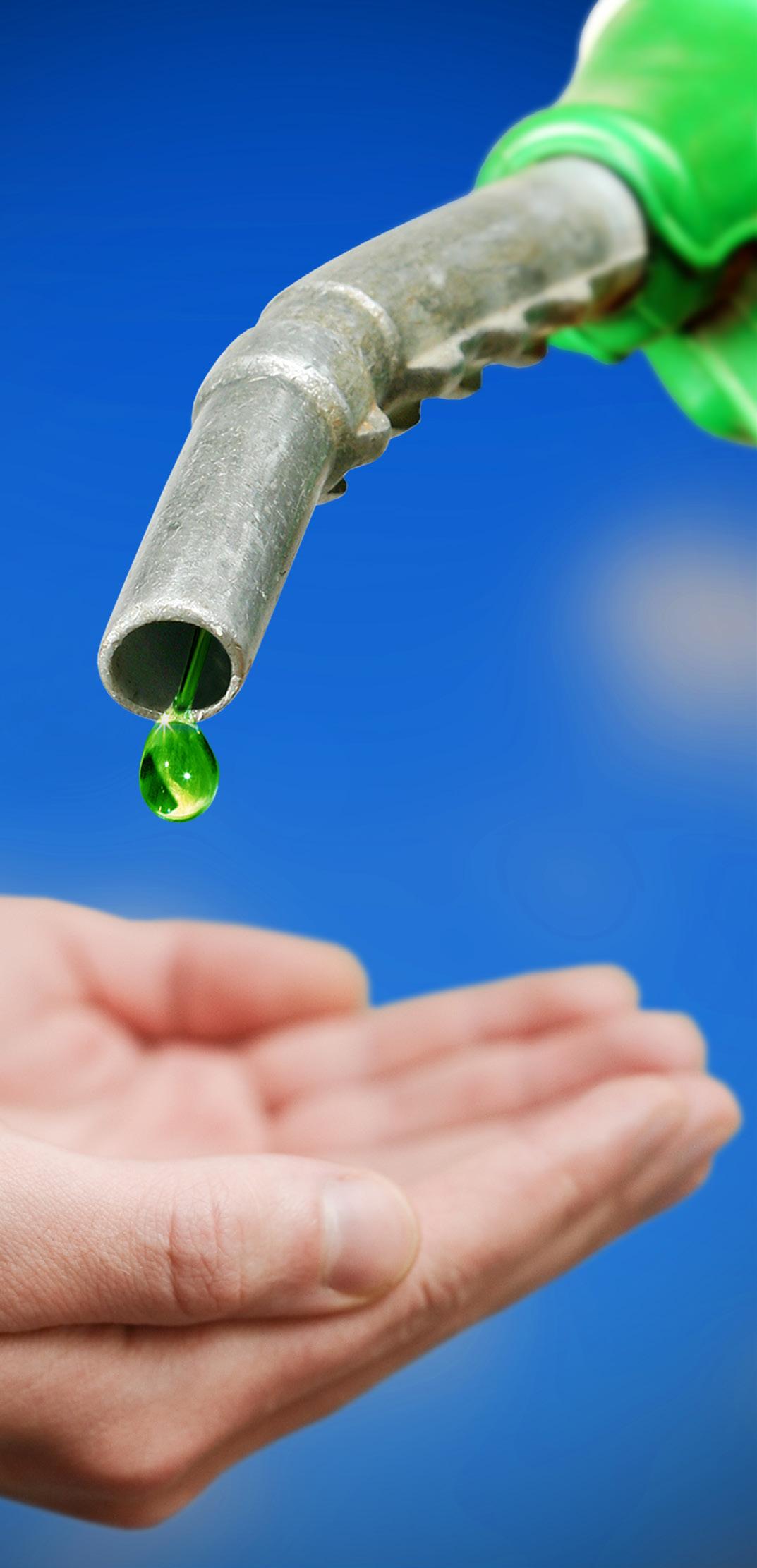
Industry adaptation
It is not often discussed, but the move to alternative fuels might be something of an existential threat to construction equipment manufacturers. These are companies which have built their products around diesel engines, hydraulics and conventional transmissions for decades. They have huge engineering expertise (and plenty of patents) in these areas and they make good machines as a result. What value does this baggage have if manufacturers have to pivot to new technologies around fuel cells, batteries, electric drives and actuators, hydrogen storage and so on? How will they cope in a world where a ‘new launch’ is a software update, rather than yellow iron?
This will be a challenge requiring fresh thinking, new talent, new suppliers and perhaps even a different approach to manufacturing and the industrial footprint. It may therefore be an opportunity for newcomers and start-ups – either to challenge the incumbents or to be acquired by them at spectacular valuations.
The potential of lower maintenance all-electric machines also challenges business models where the real margins are in wears and spares. Without diesel engines and hydraulic systems consuming oil, filters and parts, manufacturers will lose an attractive revenue stream over time.
What next?
Given that alternative energy sources should be viable in construction equipment, how will the industry get there? The diversity of the industry and the sheer span of machine sizes and applications means there will not be a single approach or technology which works universally. We are also very early in the journey, so there will be technologies and approaches which may look promising, will be tried, but which just won’t work out.
The rate of adoption will come down to economics, which is to say when the total life cost (including purchase, operation and maintenance) of alternative energy machines becomes the same price or cheaper than conventional equipment. However, also essential will be the supporting infrastructure of charging points and hydrogen availability.
At the risk of stating the obvious, the construction industry also needs alternative energy equipment to be available. Trade shows like Bauma may bristle with such machines, but there is a big difference between displaying a gold-painted prototype and having equipment in series production. There is an obvious ‘chicken and egg’ argument in the last two paragraphs. The economics will not work, and the infrastructure will not be viable, until there is large scale production and a sizeable working population of equipment. However, the machines won’t be attractive until scale makes them cheaper and there is infrastructure in the world to support them. Adoption could therefore be a slow until a critical mass is reached.
Finally, there must be a continued societal push towards renewable energy, because this is a pointless exercise if the ultimate source of energy to generate the electricity or manufacture the hydrogen is a lump of coal, pocket of natural gas or barrel of oil.