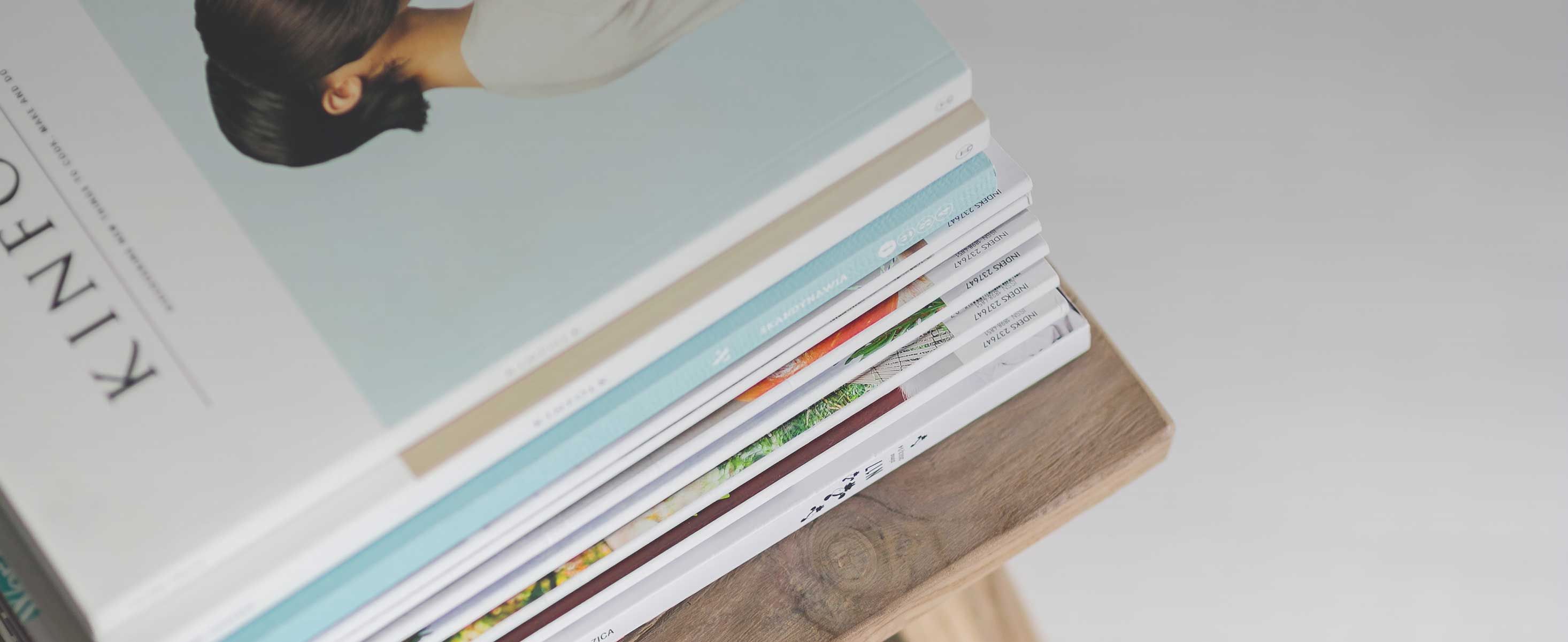
4 minute read
HARMONY IN BALANCE
from THE CRUST - ISSUE #5
by THE CRUST

When talking about monodon, Malaysia can be an interesting case study from which we can all learn. While their shrimp industry primarily relies on the vannamei species, Malaysia’s shrimp industry still has a significant percentage of monodon production. Over the last three years (2019-2021), monodon has contributed around 27-31% of the total shrimp aquaculture production in Malaysia, which equates to roughly 13-18 thousand tonnes out of their 48-56 thousand tonnes production. Furthermore, their production doesn’t rely on just the export market but is also supported by their local consumption. Malaysia is one example of a country able to create a sustainable industry by balancing its production and market demand.
As a native species in Malaysia, monodon has been cultured as early as the 1930s. In the early days, monodon was grown in traditional ponds relying on high tide for water exchange and using seed from wild stocks. Monodon was popular due to the availability of specific pathogen-free (SPF) post-larvae and its lucrative economic returns. However, this continued up to 2003, when production decreased due to disease outbreaks and inconsistent supply of SPF post-larvae. Then, producers started to shift to vanna- mei due to its shorter culture period and the lifting of the ban on its production by the Malaysian government. Despite this, monodon has yet to be entirely replaced by vannamei.
One company that has successfully balanced its production to include monodon and vannamei in its operation is Blue Archipelago (BA). BA is an integrated shrimp business that has been simultaneously producing monodon and vannamei in the same area for more than ten years. Having two production sites in Kedah (iKERPAN) and Terengganu (iSHARP) with an area of 405 and 971 hectares respectively, BA tries to balance its production between monodon and vannamei according to current conditions. The CEO of Blue Archipelago, Wan Nadhri, says the production comparison between monodon and vannamei in Kedah dan Terengganu is 20:80 and 30:70 respectively.
Since its establishment in 2007, BA has started producing monodon (2008) at the Kedah site, which was acquired from another company. The Kedah site itself is comprised of large earthen ponds suitable for monodon cultivation. “After BA refurbished the farm in 2010 into fully lined ponds, iKERPAN gradually switched to a Vannamei and Monodon mix. iSHARP, being a fully lined pond setup, started operating in 2011 with a vannamei-monodon mix from the start.” Nadhri explained.
Adapting to market trends
With a production capacity of 6,000 tonnes per annum combined with its own processing plant, the composition of vannamei and monodon production at BA is more flexible, depending on the latest supply-demand conditions. Moreover, according to Nadhri, the company’s status as a volume producer, with over 400 ponds and a processing plant, allows them to adjust their stocking plans to align with prevailing cultural trends in Malaysia.
“For example, if we sense that other producers are having a good vannamei season, BA will add more monodon ponds so that we do not overflood the market with our vannamei. Beyond that, other factors would be market demand especially for the export of monodon, disease trend, and availability of monodon PLs,” he says.
In terms of market targets, Nadhri explains that vannamei and monodon have distinct consumer segments. Vannamei is typically marketed towards a mass market due to its affordability. On the other hand, monodon is considered a niche market with a higher price, averaging RM 7-8/kg more than vannamei. BA distributes its products in both local and international markets, including China, Japan, and France.
Meanwhile, the profitability between the two species varies depending on the producer’s objectives. It largely depends on whether the farmers prioritize the number of cycles per year, volume per hectare, or the margin per kilogram of shrimp. For producers like BA, who operate their own processing plant, the processing costs can also impact their on-farm revenue.
Production system
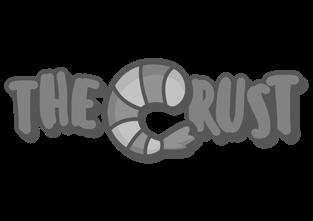
What BA is doing in producing monodon may surprise us. The company with the brand Pelagos cultivates the monodon at a relatively high density, ranging from 35 to 55 shrimps per square meter, with an average of 40 shrimps per square meter. Meanwhile, for vannamei, the density is 65 to 150 shrimps per square meter, with an average of 90 shrimps per square meter. With this kind of density, their monodon’s productivity per cycle can be quite impressive, reaching 8 to 12 tons per hectare, comparable to their vannamei’s 8 to 14 tons per hectare. This means that both productivities are quite similar. However, vannamei can go through 2.4 to 4 cycles per annum, whereas monodon can only be stocked 2 to 2.5 times per annum. In detail, Nadhri explains some of the standard operating procedures implemented by BA. These include the application of semi-floc and plankton-based preparation, using 10-30 ppm of chlorine gas for disinfection, and utilizing a combination of paddlewheel aerators totaling at 12-16 HP for each pool as needed. Additionally, BA uses large ponds sized from 0.5 - 0.8 hectares, as well as circular tanks with a volume of 200 tons.
“For our circular tanks, root blowers and paddlewheels are utilized. All ponds are fully HDPE lined and supported by auto-feeders and central discharge. Probiotics are also used to control vibrio depending on the month of the year. We do not use functional feed or additives,” Nadhri adds.
Beyond that, BA implements a modular layout with each module supported by its own sub-supply canal, sub-discharge canal, and treatment ponds. This system is designed to cater to both traditional ponds and circular tanks. It provides the BA’s production planners with a high degree of flexibility when choosing between vannamei and monodon, as well as responding to external factors such as seasonal changes.
Another thing that is going well is the new concept of pond shape and size. Nadhri thinks that smaller and circular ponds will be the future of aquaculture and will revolutionize this industry. “By going smaller, we can achieve easier control, faster turnaround, more flexibility, and better mitigation,” he concludes.