
2 minute read
Zirkonzahn - The “all in-house” culture trilogy Part 2
THE “ALL INHOUSE” CULTURE TRILOGY Part 2
THE HEAVY METAL SIDE OF ZIRKONZAHN: PRODUCTION OF METAL BLANKS, MACHINE PARTS, MILLING BURS AND MORE THAN 5000 IMPLANT PROSTHETICS COMPONENTS
Advertisement
In the previous magazine edition, we started a three-session journey through Zirkonzahn’s production sites, exploring the firm’s concept of in-house production that was carefully constructed to align with their work philosophy. After Premolaris, the place where machine assembly takes place, we will concentrate in this issue on the Molaris I & II production sites, located nearby the company’s headquarters in the Aurina Valley (South Tyrol).
Molaris I & II host the high tech necessary to produce all burs, machines parts, implant prosthetics components and metal blanks. The company’s values of rigor, precision and quality are clearly reflected in this location. By means of the latest turning, milling and grinding techniques, the company’s range of manufactured implant prosthetics components achieves a particularly high accuracy, and for the implant-supported components a high-quality medical titanium alloy is used (Ti 6Al 4V ELI according to ASTM F136 and DIN EN ISO 5832-3). The range is in constant expansion and is currently comprised of more than 5000 components available for more than 140 implant systems. All components are fabricated to meet the strictest quality criteria, and to reinforce this the company assumes the responsibility by granting voluntarily up to a 30-year warranty on all Zirkonzahn implant abutments used and the corresponding screws. The warranty also includes implants from other manufacturers used in combination with Zirkonzahn’s implant abutments.
In Molaris I & II, the company also manufactures all milling and grinding tools for their milling systems with no involvement of third parties, creating any tool geometry and making quick and flexible adjustments in close collaboration with the in-house R&D department. Surface coating, electroplating and diamond coating procedures are also performed in this facility, along with the production of the company’s range of 200 milling burs – with different geometries and shank diameters (3 and 6 mm) – milling units parts and colouring liquids. The company’s blanks of Sinternit, the firm’s sinter metal, are also produced in this location, where injection moulding machines are used to inject more than 10 different types of resins into discs and to provide them with different colours or colour gradients. To ensure safety and prevent breakdowns, the same task is performed by two machines, and measurement equipment as well as technical testing (e.g. optical and tactile 3D measuring, hardness and roughness measuring, microscopic analysis, etc.) are used to guarantee quality and precision.
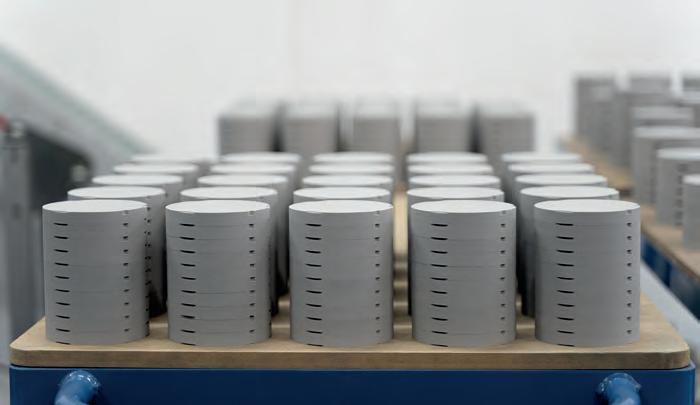
...Continues in the next issue
For more information or to arrange a company tour, visit www.zirkonzahn.com or contact Carmen Ausserhofer Tel: +39 0474 066 662 or email carmen.ausserhofer@zirkonzahn.com
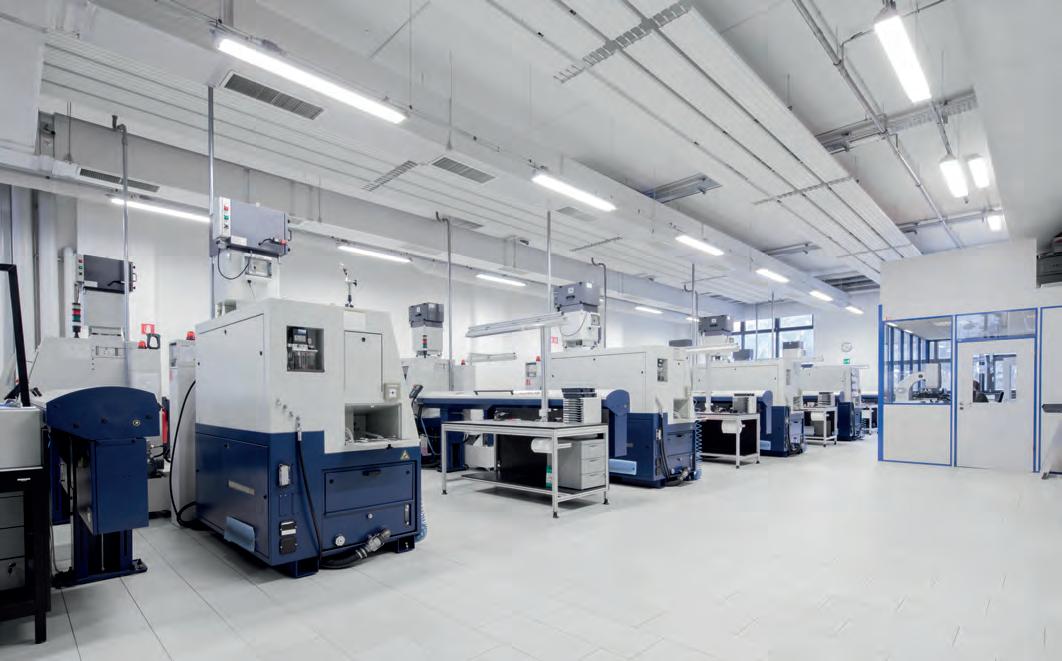
THIS PHOTO: One of the company's three production halls dedicated to implant prosthetics components. OPPOSITE PAGE: Measurement equipment guarantees quality and precision ABOVE: Sinternit blanks, the company’s sinter metal.