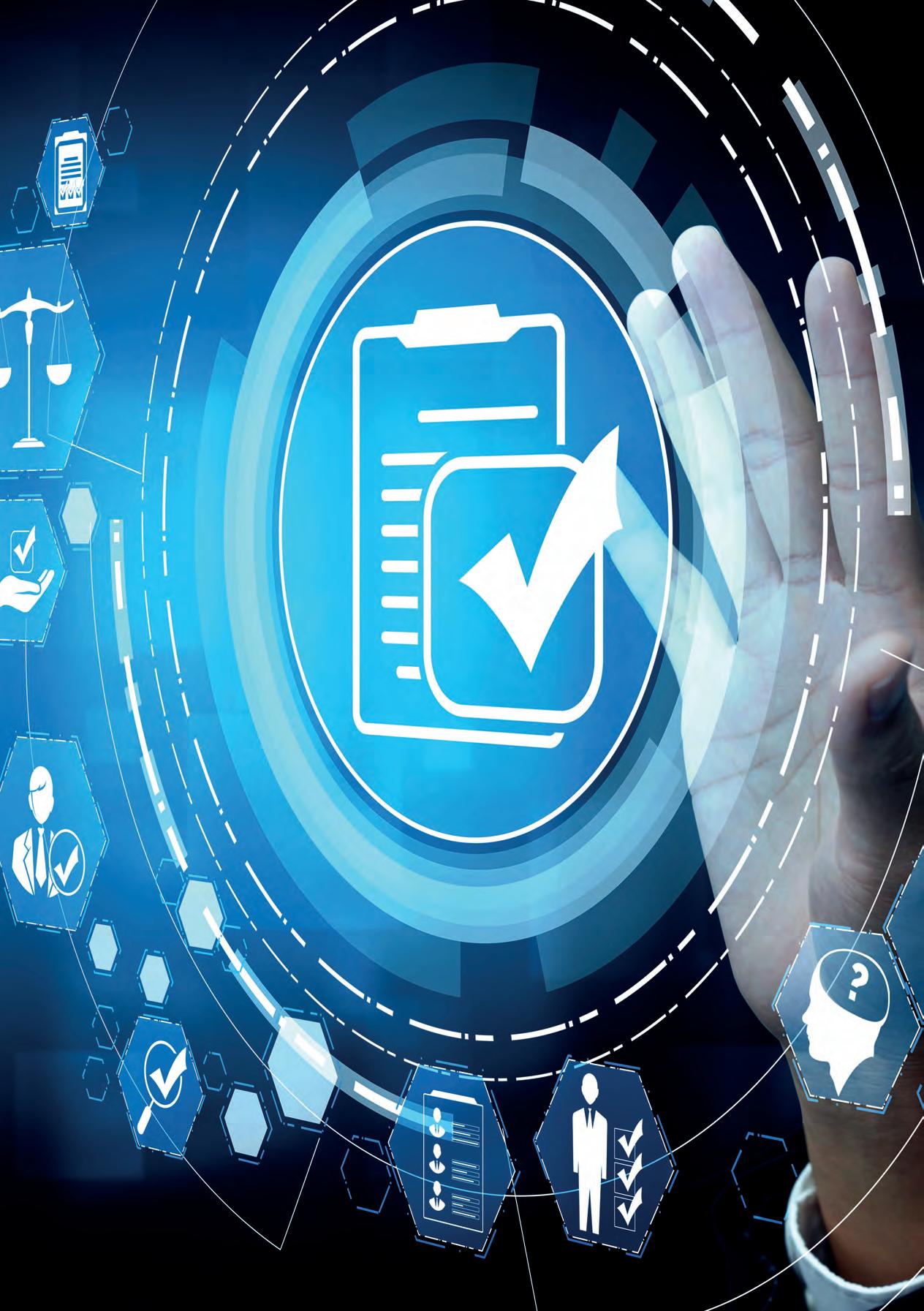
9 minute read
A Step by step guide on how to create and implement a Quality Management System, Part 1. By Peter J Natt
A STEP BY STEP GUIDE ON HOW TO CREATE AND IMPLEMENT A QUALITY MANAGEMENT SYSTEM FOR A DENTAL LABORATORY - PART 1
By Peter J Natt
Advertisement
This is a 2 part step by step guide that will run over to the August 2021 issue of The Dental Technician Magazine. The first part will prepare you to begin implementing a Quality Management System (QMS). Part 2 will go through the practical aspects and help you physically implement your QMS.
THE MEDICAL DEVICES REGULATIONS AND TRACEABILITY OF DEVICES The Medical Devices Regulations were implemented as a result of the concerns caused by the breast implant scandal where implants containing dangerous substances had been implanted within patient’s bodies.
The Medical Devices Regulation EU MDR 2017 superseded the Medical Devices Directive EU MDD 1993 because of Brexit. As from January 2021 Great Britain (England Scotland and Wales) will be following the existing UK MDR 2002 which was amended at the end of 2020 to incorporate the EU changes.
Northern Ireland will still follow the EU implementation requirements from 26 May 2021 and will have to comply with the EU MDR 2017. This is due to the Northern Ireland Protocol Agreement.
The Medical Devices Regulations has an enhanced Traceability element contained within it so as to ensure that a record is kept of the materials that a device is constructed from so that if there is a concern in the future about a specific material that it contains that it is possible to identify the Devices containing the suspect material and the Patients can then be contacted and alerted to the issue.
Another big advantage of Traceability to the Dental Team and Patients is that for instance the manufacturers of Devices (i.e The Dental Laboratory) have to keep detailed records of the materials and components that they use within a Device. So for instance a Device containing pre-manufactured implant components would mean that the following details would be required (i.e. manufacturers name, the brand, type, size and product identity code). The same also applies to the artificial teeth used on dentures as details of the artificial teeth such as the manufacturers name the brand, mould and shade of the teeth should be recorded.
This means that it will be possible to determine from the records which implants or teeth where used on a specific device, which make it far easier for them to be repaired, altered (i.e additions), serviced or re-made. The Patient will have the details of the manufacturer of their Device on their ‘Statement’ so it will be easy for them to then request the details from the manufacturer of the Device as to which materials and components were incorporated within their Device.
The Dental Laboratory industry needs to be seen to be ‘Whiter than White’ in its compliance with the Medical Devices Regulations if the public are to have confidence in it so it is important that every Dental Laboratory complies with the Medical Devices Regulations.
LEGAL OBLIGATIONS Whether you manufacture 1 or 1,000,000 Custom Made Medical Devices per year you must comply with the Medical Devices Regulations. This is a legal requirement and there are absolutely no exceptions.
Failure to comply with all the requirements of the Medical Devices Regulations means that you are manufacturing Medical Devices illegally.
This could have serious consequences for you as you could receive a large fine or even a prison sentence, and also be reported to the GDC and referred to their ‘Fitness to Practice’ committee.
In addition, your product liability and third-party liability insurance policy may be invalidated if you are operating illegally.
As a result of being found not to be complying with the Medical Devices Regulations you may find yourself at the receiving end of legal action and suffer the financial consequences not forgetting the anguish caused to you and your family in having to deal with the consequences.
SUB-CONTRACTING WORK It is important to ensure that any Devices that are sub-contracted to another Dental Laboratory or Milling Centre are manufactured by someone that is fully compliant with the Medical Devices Regulations so always check that they are registered with the MHRA and that they have an audited Quality Management System such as DAMAS in place. Keep their details (i.e a copy of their current Quality Management Certificate such as DAMAS) recorded in the ‘Approved Suppliers’ section of your Quality Management System Manual and always ensure that it is updated each year.
WHAT YOU MUST DO TO COMPLY WITH THE MEDICAL DEVICES REGULATIONS Manufactures of Custom Made Medical Devices must comply with the Medical Devices Regulations and to do this they must:
1. Be Registered with the MHRA and have a MHRA Registration Number (Anyone having a Registration Number beginning with CA must Re-Register immediately on the new MHRA online DORS Portal – see my article ‘A Step to Step Guide on how to Register with the MHRA’ in the March 2021 Issue of The Dental Technician Magazine.
This is the link to check to see if you are registered with the MHRA:
https://aic.mhra.gov.uk/era/pdr.nsf/ name?openpage&start=1&count=200
or search: ‘MHRA Register of Custom Made Devices.’ Also check that your address is correct and that all the Devices and Products you manufacture are listed.
2. Have a documented Quality Management System in place. u
WHAT IS A QUALITY MANAGEMENT SYSTEM? A Quality Management System is a formalized procedure that documents the policies, procedures, documentation requirements and processes that manufacturers use to ensure that their products are both safe and effective for the end user. The MHRA (Medical Health Products Regulatory Agency) mandates that all Medical Device companies that market product in the U.K maintain a Quality Management System.
THIS QUALITY MANAGEMENT SYSTEM The Quality Management System that I shall describe compiles with both the requirements of the Medical Devices Regulations and DAMAS so if Dental Laboratories wish to be third party audited to DAMAS then this Quality Management System will form the basis for doing so.
ADVANTAGE OF HAVING A THIRDPARTY ACCREDITED QUALITY MANAGEMENT SYSTEM The advantage of having a third-party accredited Quality Manuel System is that you can provide your clients and anyone that sub-contracts work to you with a copy of your current Quality Management Certificate (such as DAMAS) which will demonstrate your compliance with the Medical Devices Regulations.
QUALITY MANAGEMENT SYSTEMS AND THE CARE QUALITY COMMISSION (CQC) If your clients are inspected by the Care Quality Commission (CQC), who regularly inspect Dental Practices (be they NHS or Private) then it is easy for your clients to demonstrate that the suppliers of their Medical Devices are compliant with the Medical Devices Regulations by showing the auditor a copy of their Dental Laboratories Quality Management System Certificate (DAMAS).
HOW TO CREATE YOUR QUALITY MANAGEMENT SYSTEM I would suggest using a word processing software and creating a Folder specifically for all your Quality Management Files and also save each page as a different file. This will also make it easy when carrying out your ‘Internal Audit’ prior to your annual review and audit. In addition, any updates to the system as a result of changes to the Medical Devices Directive can be easily carried out. This will also make it easy for you to print out the pages for your various files.
SUGGESTED LIST OF WHAT YOU WILL REQUIRE TO CREATE YOUR QUALITY MANUAL SYSTEM: • Your MHRA Registration Number • The Name of the Quality Management
System you wish to comply with • 10 X Lever Arch Files of Foolscap (A4+) Size • 4 X A-Z Indexes for Lever Arch Files • 2 X 1-15 Indexes for Lever Arch File • A Desk Top or Lap Top Computer using the
Microsoft 10 Operating System • A word processing Software such as
Microsoft 365 Software which includes
Microsoft Word to produce the pages of your Quality Management System. • A Computer Printer (Laser or Ink Jet) - Even better a Printer/Copier/Scanner • Spare Ink Cartridges or refills for your printer • A4 White Paper • A Paper Punch • Two separate computer data Back-Up Systems to ensure that if your computer is corrupted there is always an up to date backup available. i.e a separate hard drive and a separate system for backing up to the cloud. • A Laminating Machine capable of laminating A4 size sheets of paper • Glass Clear Laminating Pouches (A 4 Size - 2 X 125 um Thick) • Velcro Stick On Loops Male • Velcro Stick On Loops Female
FILES AND THEIR CONTENTS • Lever Arch File 1 Quality Management
System Manuel (Insert a 1-15 Index) • Lever Arch File 2 All Correspondence
Relating to the MHRA • Lever Arch File 3 Equipment Instructions (Insert an A-Z Index) • Lever Arch File 4 Material Instructions (Insert an A-Z Index) • Lever Arch File 5 Staff Training and Staff
Qualification Records (Insert an A-Z) Index • Lever Arch File 6 Cleaning Records • Lever Arch File 7 Maintenance and Servicing
Records (Insert an A-Z Index) • Lever Arch File 8 Current Orders • Lever Arch File 9 Completed Orders • Lever Arch File 10 Superseded Documents (Insert a 1-15 Index)
HOUSEKEEPING AND CONVENTIONS Create a folder within Microsoft Word Documents called QMS to keep all your individual files within it so that they are accessible and easy to find. At the bottom of each page of each document put the name of the file and the date it was created. i.e 10.06.2021 i.e c:documents/qms/compliance.001 TO START OFF YOU NEED TO DOWNLOAD A PRINTED VERSION OF: • A Copy of the Medical Devices Regulations. www.legislation.gov.uk (In the search title field type Medical Devices Legislation and in the Type field select All Legislation (including originating from the EU). • A Copy of the requirements of your Quality
Management System (i.e DAMAS). www.damas.co.uk Click on Downloads Then Click on DAMAS Specifications Issue 8.
FIRST TWO THINGS TO DO IN YOUR DENTAL LABORATORY If you manufacture new or repair worn dentures, carry out additions or relines to worn dentures then you need to ensure that you have two completely separate polishing lathes, pumice baths and polishing baths so that cross-contamination cannot occur between worn and new dentures as pumice will allow micro-organisms to survive and grow within it.
You also need to have a documented system which shows you regularly clean out and renew the pumice in your polishing lathes and keep separate grinding stones and burs for new and repaired dentures.
Also ensure that you have a disinfectant bath for all devices leaving the laboratory and again have a documented system that shows you regularly clean out the bath and change the disinfectant.
To reduce the risk of cross-contamination have a separate disinfectant bath for worn appliances/restorations and another one for new appliances/restorations. Mark them as to what they are so that there can be no doubt or mistakes.
THE SECOND PART TO THIS ARTICLE, WHICH WILL GUIDE YOU THROUGH THE CREATION OF THE QMS WILL BE PUBLISHED IN THE AUGUST 2021 EDITION OF THE DENTAL TECHNICIAN MAGAZINE.
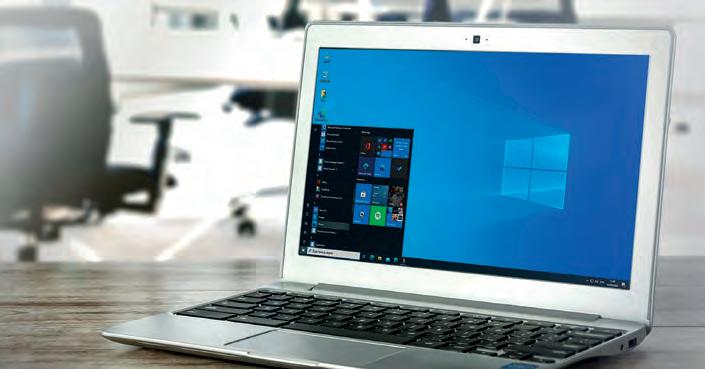