
3 minute read
Zirkonzahn - The “all in-house” culture trilogy Part 1
THE “ALL INHOUSE” CULTURE TRILOGY Part I
A TOUR THROUGH SOME OF ZIRKONZAHN’S PRODUCTION CENTRES, ALL LOCATED WITHIN THE VICINITY OF THE HEADQUARTERS IN THE ITALIAN ALPS
Advertisement
When it comes to deciding how to plan their production, companies first need to determine: in-house or outsourcing? This is an important choice, which has to be made with consideration of the biggest impacts on the company’s vision and goals. In this magazine edition, we focus on the first of a three-part “tour” of Zirkonzahn’s production sites in the Aurina Valley (South Tyrol, Italy). The dental technical company exemplifies the “all in-house” culture, owning five production sites located within the vicinity of the company’s headquarters, where all their milling units, furnaces, scanners, implant prosthetic components, dental materials, burs and tools are produced.
Together with the production centre in Gais, Molaris I & II and Caninus, Premolaris is one of the firm’s production sites. Built in 2021, it is dedicated to the assembly of milling units, furnaces, scanners as well as machine testing and customisation. The production facility reflects the company's philosophy in the clear values of accuracy, cleanliness and order – prerequisites to a precise work, which perfectly combine in the firm’s design concept of product modularity. Founded and run by dental technicians (Enrico and Julian Steger, MDT), the company understands the needs of laboratories and aims to design complex technologies to be as transparent and comprehensive as possible, based on welldefined interfaces, to guarantee the greatest freedom of choice and processing. This means that not only can the users benefit from a high level of customisation according to their necessities, but they can also avoid any waiting for service or loaner machines, saving valuable time.
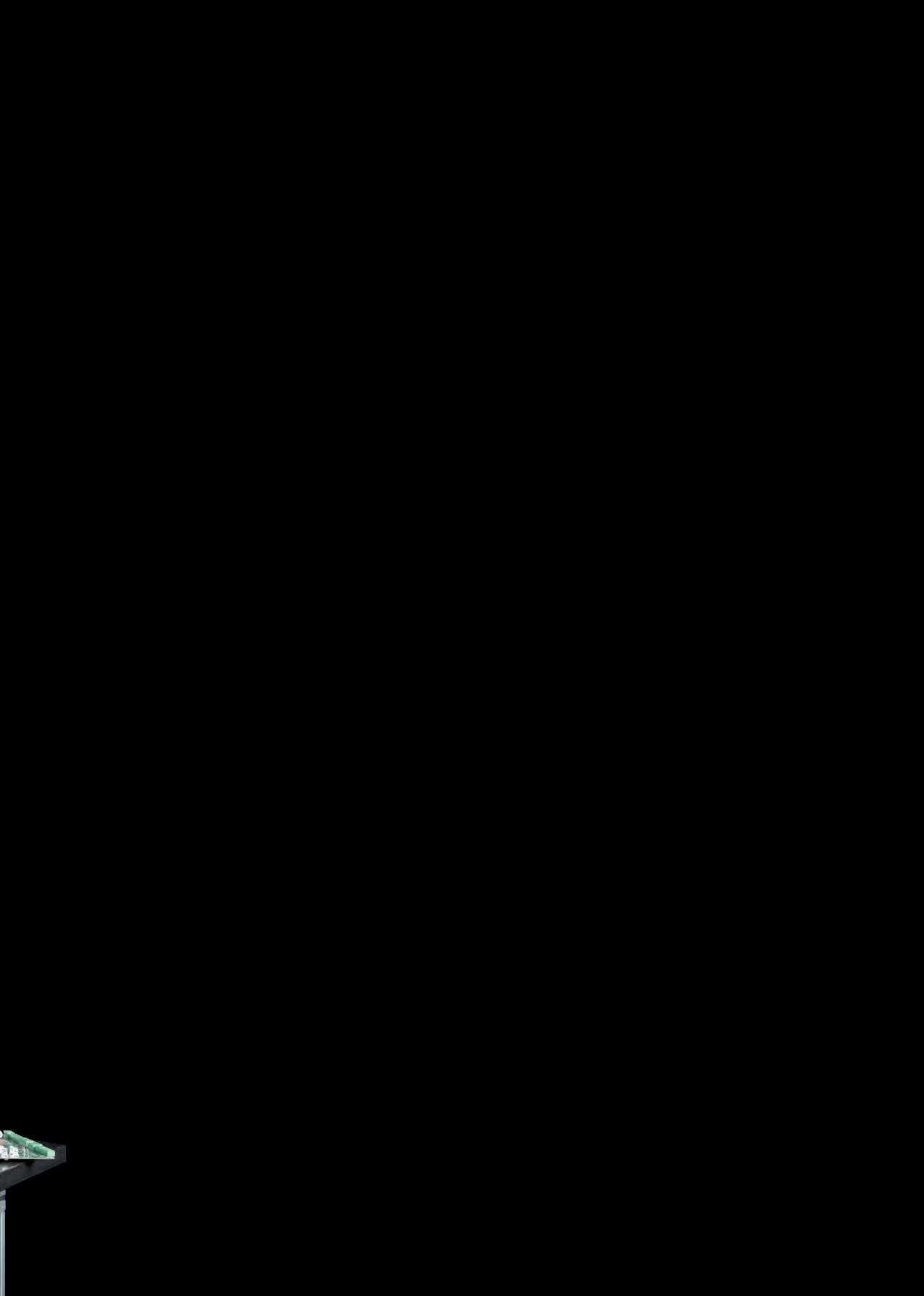
Machine components production takes place in Molaris I & II. In Premolaris, milling units, scanners and furnaces are assembled, calibrated and fine-tuned at individual stations according to standardised production processes. A new machine must pass through numerous quality stations before it reaches the final inspection and each employee is responsible for a specific assembly step, becoming an expert in what he or she does. For example, this is the place where spindles and orbits are assembled into the milling units with all hardware and software components: precision tests and measurements are carried out on each spindle before they are mounted in the machines and all data obtained is recorded and registered. Machine assembly is a very complex procedure and employees have to comply with strict checklists, which serve to coordinate the different working steps and ensure safety. An area of Premolaris is also dedicated to laser marking. Here, machines are marked with their names, and products that can be customised – such as Zirkonzahn Shade Guides – are laser-marked with the name of the clinic or the laboratory. A selection of glass cases, which the clients can choose from to personalise their equipment, is also available in this area. Premolaris is also the place where the first milling, scanning or sintering processes are performed on the new machines: only after the execution of the final checks and tests is the equipment ready to leave the production site, moving on to the on-site logistic department.
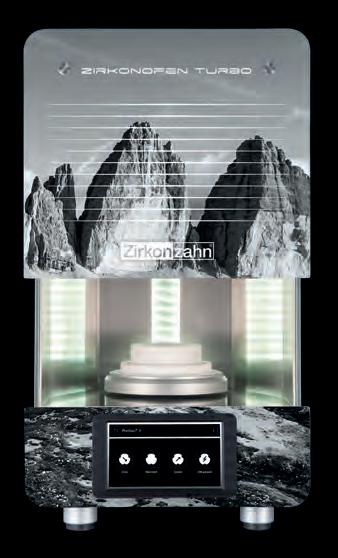
… To be continued in the next issue.
OPPOSITE PAGE: Testing the new, in-house developed electronics of the new Zirkonofen Turbo BELOW: The production site of Premolaris. ABOVE: The new Zirkonofen Turbo. The first sintering process is performed at Premolaris.
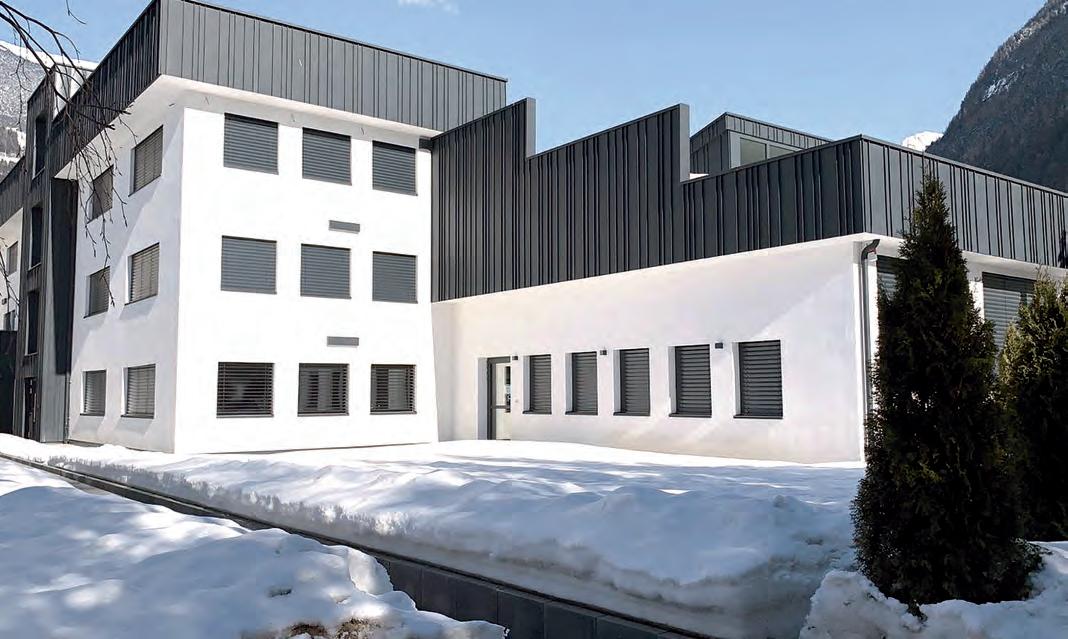