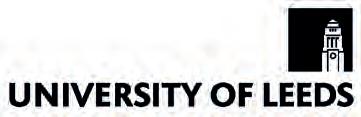
4 minute read
Can 3D printing provide a better way to make dentures? By Dr Andrew Keeling
CAN 3D PRINTING PROVIDE A BETTER WAY TO MAKE DENTURES?
By Dr Andrew Keeling
Advertisement
SUMMARY
The techniques used to make dentures are labour-intensive, expensive, inaccurate and have remained largely unchanged for decades. Recent advances in technology now make it possible to create 3D printed dentures, so Dr Andrew Keeling is finding out if this is feasible, and whether the results are acceptable to wearers and as good or better than existing dentures.
Dr Andrew Keeling
Although around six per cent of the population have lost all their teeth and require complete removable dentures, their needs are often overlooked in modern dentistry. Dentures have been around for over a century, along with the labourintensive techniques used to make them. Are 3D-printed dentures better?
3D-printed dentures have the potential to solve a lot of problems. We are investigating whether they can be made better fitting and more comfortable than conventional dentures, and will be cheaper, easier and faster to produce. At the same time, these new dentures must be acceptable to wearers.
New materials for use in 3D printing have recently received a ‘CE mark’, meaning that they’ve been certified as safe to make items such as dentures. However, there haven’t been any robust studies testing the best ways of manufacturing 3D printed dentures, or finding out how they compare with traditional versions – such as whether they fit better, are sufficiently robust for daily life, or are as well-liked by wearers.
Dentures have been around for over a century, and the techniques used to make them haven’t changed much in that time either…
In a pilot study, we collaborated with three dental centres equipped with a digital scanner used to scan dental impressions and models. We worked with them to refine the scanning software and optimise the 3D printing process, then trialled the results with users. Each participant in the study was given two sets of dentures: one made using traditional methods, and one made using 3D printing. Overall, both sets were scored about the same by wearers, confirming that the new versions are acceptable.
We wanted to find out how best to make 3D-printed dentures, and test whether they were as good as traditional dentures through clinical trials.
Now we have found the best method to scan impressions and models, and to print dentures, we will be taking this technology forward into a larger trial.
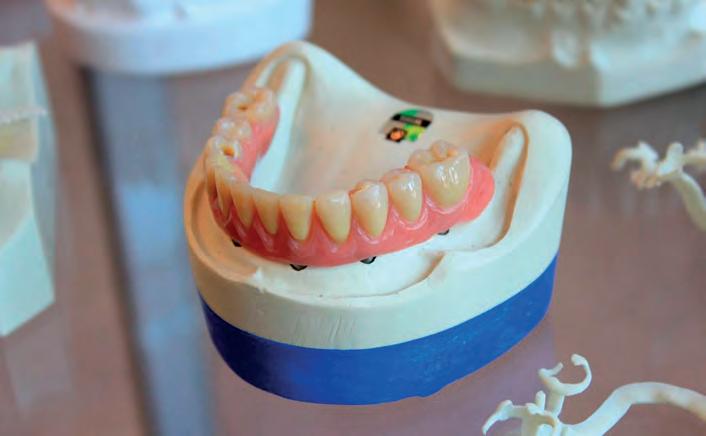
What impact could this have?
Our work will not only make a difference for people receiving their first set of dentures, but also people who lose them – a situation that occurs particularly in hospitals and care homes. Currently in the UK, the time and cost of making a new set of dentures means that people can be left without teeth for months, with knock-on effects on nutrition and confidence.
Right now, it takes several dental appointments and costs the NHS thousands of pounds to make a new set of replacement dentures in a care home setting. With 3D printing, we can use the digital scanner file to quickly print a new set to be sent out. Not only could this significantly save time and money, it also reduces the number of face-to-face visits with the dentist.
We’ve shown that 3D-printed dentures are acceptable to users. In the future, they could have the potential to be better fitting and easier to produce than conventional dentures – now that would be something to smile about!
Dentures aren’t the most glamorous aspect of dentistry, but they’re essential for millions of people in the UK – many of them older, less wealthy and often struggling with poorly fitting dentures or none at all. The one thing that stands out from our trials is how grateful the participants always are to receive their dentures. It’s really gratifying to be able to do something meaningful for a significant minority of the population who are often largely forgotten.
Currently, our work has been halted by COVID-19, but we’re hoping to get started again as soon as it’s safe. The Dunhill Medical Trust got in contact as soon as it became clear that the pandemic was affecting our research, providing support and reassurance early on when nobody knew what was going on. They were quick to react, and have been very accommodating of the changes we’ve had to make to the project.
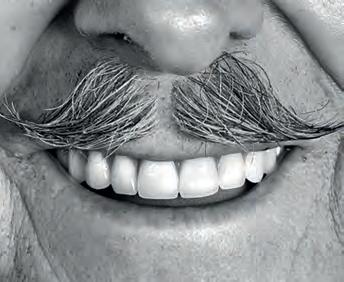
Dr Andrew Keeling
ORIGINALLY PUBLISHED HERE; https://dunhillmedical.org.uk/success-stories/can-3dprinting-provide-a-better-way-to-make-dentures/?f bclid=IwAR0xghQwxx46rVWe1K6Hc4PKKCJZ1WVL dd_ei5MDnK58JpG-iZuaRvo3elM
MORE INFORMATION
NEW! SCREWDRIVER LAB AND SCREWDRIVER HOLDER MAGPRISM
NEW SCREWDRIVERS FOR WORKING ON THE MODEL AND RELATED HOLDER FOR A SAFE STORAGE
- Screwdriver Lab is used to fi x and loosen different screws on the model (not approved for intraoral use)
- Available in different lengths and colour codings depending on the implant system
- Screw marked with the same colour of the screwdriver, for an easy identifi cation of the screwdriver and implant system
- The Screwdriver Holder MagPrism is provided with rubber pads on the underside to prevent slipping on the work surface