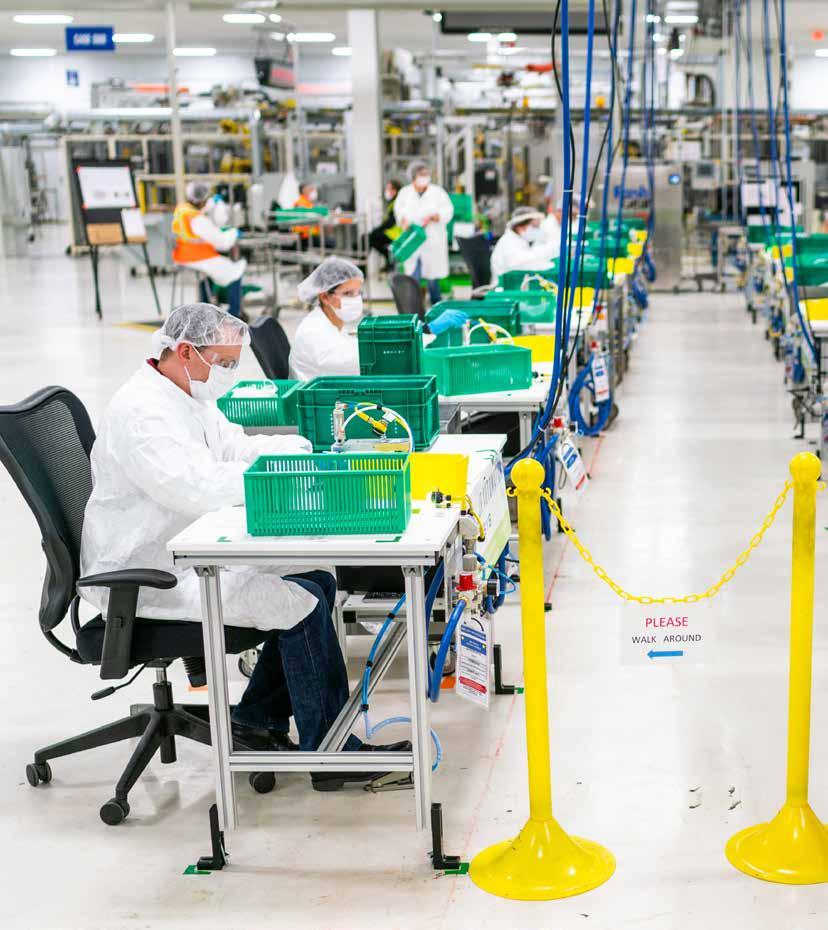
5 minute read
FROM VEHICLES TO VENTILATORS
Ford, GM gear up to manufacture medical equipment to combat COVID-19
BY RUTH NICOLAUS
Production at Ford and General Motors plants across the nation has shifted from cars and trucks to medical equipment, to combat COVID-19.
While automotive sales have tanked since the pandemic hit the U.S. in mid-March, Ford and GM are still up and running.
But they’re not making cars and trucks. They’re manufacturing ventilators, medical face shields, PAPRs (powered air-purifying respirators), re-usable hospital gowns, and face masks.

Face masks are being produced at the General Motors manufacturing plant in Warren, Mich. Between 50,000 and 100,000 masks are produced a day. Photo by John F. Martin for General Motors.
For Ford, the “a-ha” moment came when president and CEO Jim Hackett was talking to White House staff about the impact of the pandemic on the auto industry. As they discussed the shortage of ventilators, he blurted out, “Maybe Ford should help make ventilators.”
Ford is partnering with GE Healthcare and Airon, a Florida-based company that makes pneumatic life support products. GM has teamed up with Ventec, located in Washington State, a company that has developed a portable personal ventilator.
The transition from autos to ventilators took a bit of doing. Assembly lines with robotic welding machines and power drills morphed into work benches with hand tools.
And workers needed training, too. “You’ve got to bring 1,200 people up to speed on processes they’ve not ever done before,” Gerald Johnson, GM’s global manufacturing chief, told the Wall Street Journal.
The automakers had to secure inventory as well. No single contractor makes all ventilator pieces; they are made by different subcontractors, so aligning inventory for each piece required some time and effort.
At GM’s idled plant in Kokomo, Ind., a facility that made electronic components for engine controls and air bags, hundreds of workers set up to make the Ventic Life Systems V+Pro critical care ventilator.
GM has partnered with Ventec Life Systems to mass produce ventilators. Ventilators weren’t designed for highvolume production, so it took a bit to get the assembly lines going for the big auto makers to produce the device.
In Ypsilanti, Mich., Ford workers are assembling their parts of the ventilator in a building that used to see production of oil pumps and hybrid-car batteries, and in Flat Rock, Mich., workers are assembling PAPRs.
Medical device assembly requires oversight by the FDA, who ensures quality. Ventilators are made to sustain life; they cannot be poor quality. “There’s a tracking system you have to meet (when ventilators are assembled), and you have to take the time to do a documentation for a ventilator,” Pamela Fry, vice-president of Airon Corp., told Forbes magazine. Assembling a ventilator requires precision. “There’s been a lot of talk about building ventilators overnight,” Chris Brooks, Chief Strategy Officer for Ventec, told Forbes magazine, “but a ventilator is much more than moving air in and out. If you’re giving the patient too much air and you’re overinflating the lungs, it can cause harm or death. And if you’re underinflating the lungs, you can cause harm or death.”
The automakers brought their own unique skill set to manufacturing. Hackett, Ford’s CEO, pointed out that they are exceptional at gathering inventory and manufacturing in a short time frame. “How do you get disparate pieces to be assembled and moved out? Automotive has perfected doing this, so you’re not sitting on billions of dollars of inventory.”
Henry Ford designed the assembly line 107 years ago, and that is a help to making ventilators and other devices more quickly. Ventilators weren’t designed for high-volume production, and ventilator companies have limited supply chains because the machines are produced in small numbers.
Hackett explained what Ford is capable of. “With our supply chain, we build an F150 every 52 seconds. This is a machine with a price of $70,000 to $100,000 per copy, so it’s more complex than a ventilator.”
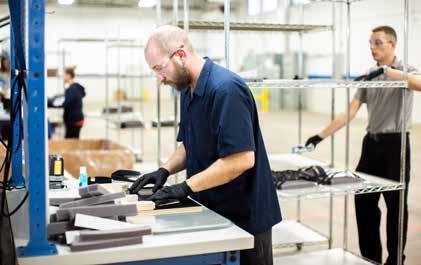
Operators and assemblers assemble medical face shields. Ford, along with other automotive giants, is using its proficiency at assembly and production to ramp up the manufacture of medical devices.
Ventec’s Brooks understood what GM had to offer his company, in terms of manufacturing ventilators. “It was immediately understood that they could bring a lot to the table, as far as helping us with the supply chain, and bringing new suppliers to source more quickly. GM understands mass production.” Production of ventilators has been a small-scale process, but not with GM and Ford helping out. “We immediately started thinking outside the box: how can we ramp up production?”
Ford is doing more than making ventilators. In mid-April, they began producing face shields at their Plymouth, Mich. factory, PAPRs, face masks and re-usable gowns for health care workers.
The gowns, made of silicone-coated nylon, can be washed and reused up to fifty times. The material for the gowns is supplied by one of Ford’s airbag suppliers, with 1.3 million of them cut and sewn by early July. The face masks will be certified for medical use.
Ford is also providing manufacturing expertise to Thermo Fisher Scientific, a company in Massachusetts that makes scientific instruments and consumables for the healthcare and laboratory industry, allowing them to quickly expand production of COVID-19 collection kits to test for the virus.
Ford experts in manufacturing, purchasing and supply chain have been working with 3M manufacturers to help increase production of other medical supplies needed for the pandemic.
Ford and GM are not profiting from sales of the medical devices. Both companies hope to have their costs covered. “We’re not looking for a contract,” Hackett said. “We have a verbal agreement that will be transparent and ethical about the cost, and we really don’t want to profit from this. It’s just not the time for profit. We’ve just put our head down, and we’re building.”
The auto makers are ensuring their own workers are safe from the virus. They are stationed at least six feet apart and will wear medical grade face masks. Even with the risk of infection, more than 500 volunteered to work at Ford’s Dearborn, Mich. location.
It isn’t the first time U.S. automakers have volunteered to help in the face of national emergencies. During World War II, GM built tanks and ammunition while Ford made B-24 Liberator bombs. In the 1940s, Ford developed an “iron lung” for polio patients.
The companies are putting “the pedal to the metal” in getting devices built. More than 100,000 face shields per week, starting in mid-April, were produced by Ford. Alongside Airon, Ford plans on producing 50,000 ventilators by July 4, and GM, with Ventec’s help, has a goal of producing 10,000 ventilator units a month. GM also has a contract to deliver 30,000 ventilators for the national stockpile by the end of August. Ford is making 100,000 medical gowns a week, and as of mid-April, had already made more than three million face shields.
The automotive giants were happy to join up to help those fighting COVID-19.
“We knew that to play our part helping combat coronavirus, we had to go like hell and join forces with experts like 3M to expand production of urgently needed medical equipment and supplies,” said Jim Baumbick, vice president of Ford Enterprise Product Line Management. “We’ve unleashed our world-class manufacturing, purchasing and design talent to get a scrappy start making personal protection equipment and help increase the availability and production of ventilators.”