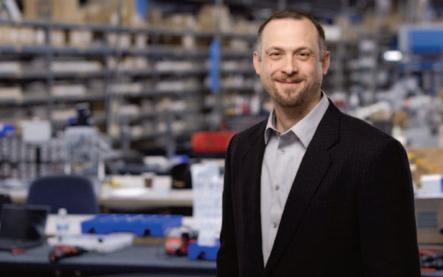
1 minute read
Seeking closure the Kwik Lok way
by The Grower
Karen Davidson
The Kwik Lok bag closure is ubiquitous. In 1954, Floyd Paxton engineered a better way to keep Washington State apples safe and fresh. And the changes, while subtle, have kept coming over the years for not only the produce industry but the bakery industry too.
Headquartered in Yakima, Washington, the company has kept up with the environmental movement. Ryan Towry, vice president of engineering and innovation, explains that two new closures reflect the evolution of materials.
Launched in 2019, the EcoLok feels like traditional plastic but includes renewable plantbased starches from potatoes and corn which lessens the amount of petroleum-based product by up to 20 per cent. It’s best suited to the produce sector which needs to protect heavy-weight packages such as apples and potatoes as well as products in a wet environment.

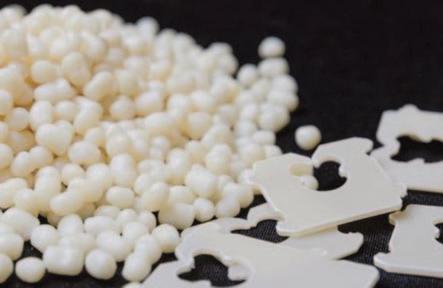
Fibre-Lok, the second sustainable option recently launched by Kwik Lok, looks and feels different because it’s made from cellulose which comes from fibres such as wood and cotton. The cellulose-based material can be used for packaging product that isn’t stored or displayed in a wet environment. Printable and reusable, this zero-plastic product is being tested in Canada.
“We’re making sure that the closures work in the current machines,” explains Towry. “We take very seriously the importance of reliability of our machines. The closures have to fulfill the brand promise of being reclosable and keeping produce safe.”
The cost of Kwik Lok closures depends on a variety of criteria including the sizes and openings explains Karen Reed, director, global marketing communications.
“The closure is the least costly part of the packaging, but every penny adds up,” she says. “For us, meeting sustainability goals and the bottom line are both important.”
Early adopters are using EcoLok and Fibre-Lok as part of their sustainability goals without having to invest in new machines.
Materials scientists have a delicate balance to achieve, searching for options with strength, flexibility and are recyclable or compostable.
“It’s a tightrope walk to determine what materials will break down quickly and will also hold up through the life of the product,” says Reed.
While companies such as Kwik Lok are innovating in the materials space, consumers are looking to their solid waste providers for innovative ways to manage the sorting process so more materials are recyclable.
Some consumers may ask for compostable solutions. It’s great if a material is compostable but if there isn’t a composting facility in the area, then compostable materials have no place to go at the end of their life and must go to the landfill.

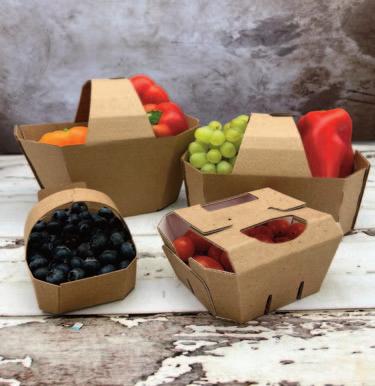
“Our goal is to have products that are high quality, reliable, reusable, compostable or recyclable in order to be part of the circular economy,” says Towry.
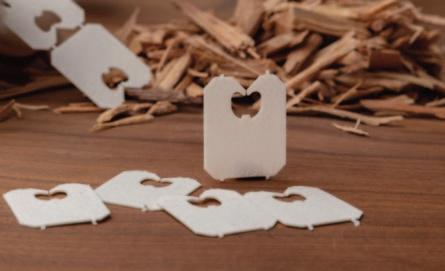