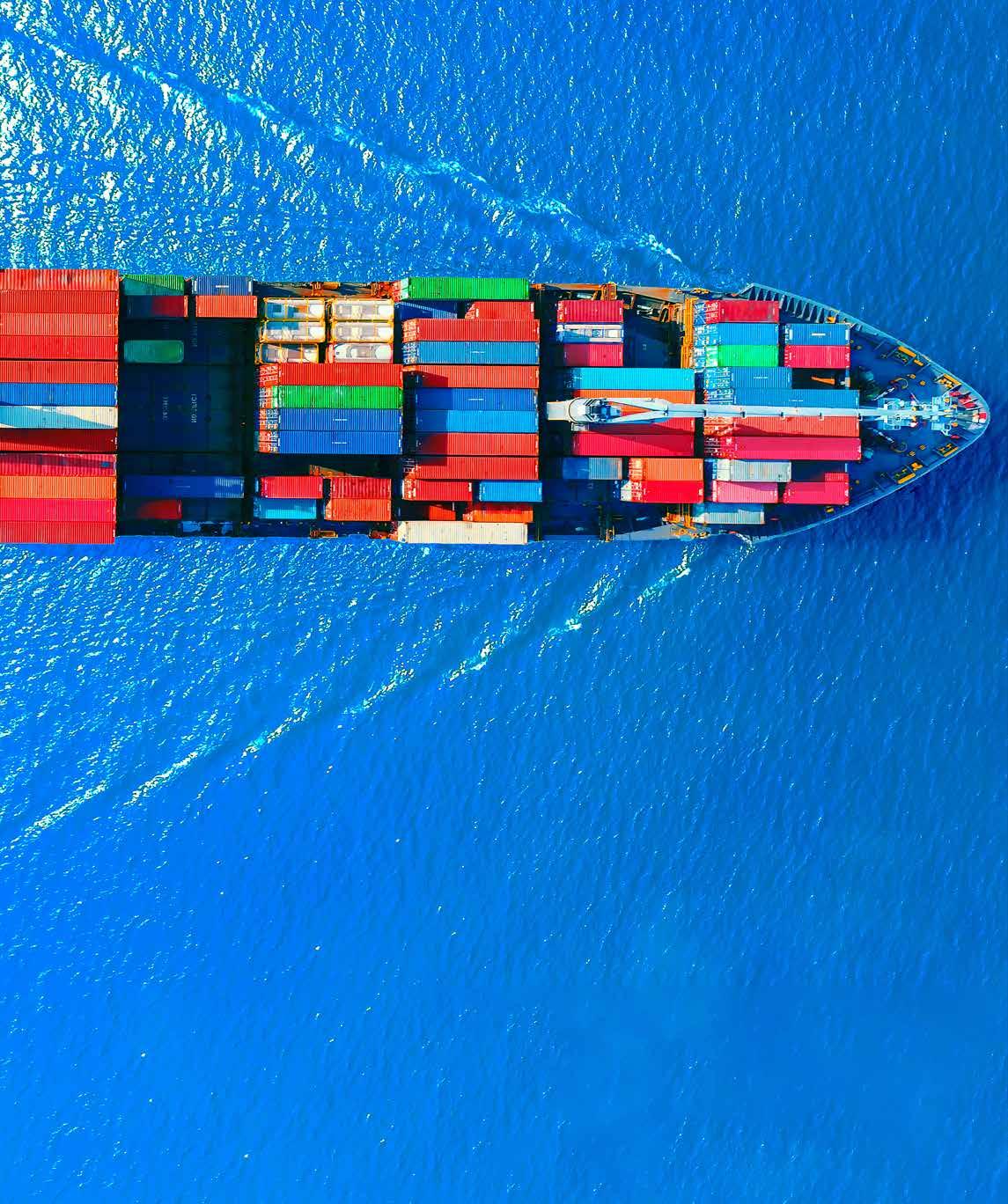
12 minute read
SHIP SHAPE
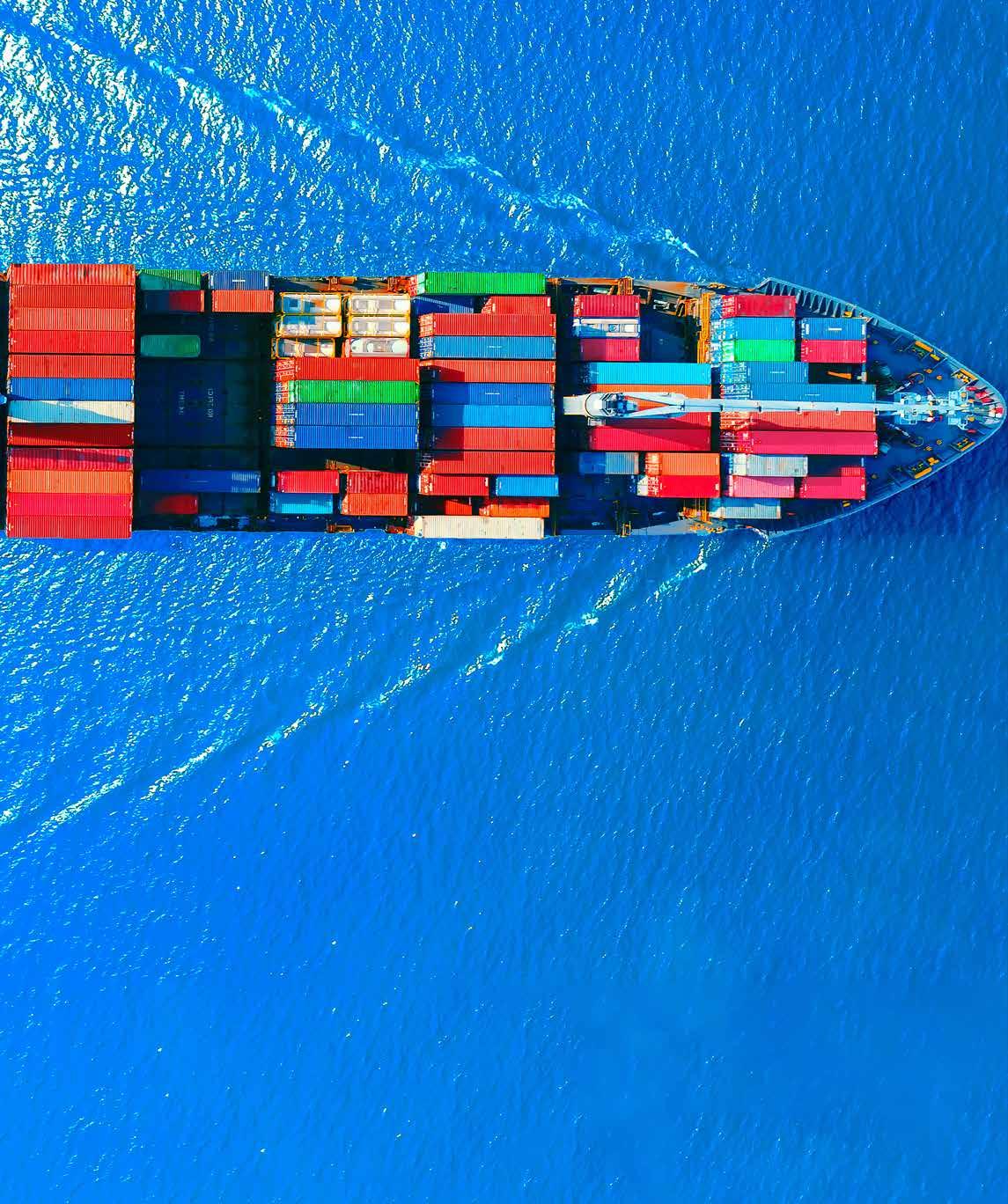
JULY/AUGUST 2021 LIGHTING JOURNAL 25
Maritime lighting
The maritime industry is responsible for transporting around 90% of items around the world and is a key cog in the global economy. Yet many ports’ operators still have not ‘got it’ when it comes to understanding the benefits of modernising to LED. Ports can also present technical challenges for lighting around weather, wind and temperature
By Simon Newcombe

For many years now, LED lighting has been recognised as the world’s main source of lighting, superseding HPS and LPS in efficiency and application.
A longer lifespan, solid-state fast-switching, high CRI, superior energy efficiencies and lower maintenance requirements have all assured its popularity amongst street lighting engineers and councils.
Yet, despite this, some of the world’s largest industries are still yet to realise the full potential of upgrading their lighting solutions to take advantage of these benefits and the relatively quick return on investment.
The operators of large-scale, multifaceted operations like those in the maritime industry are one such industry, being still by and large in the early stages of investing in LED lighting. Equally, selecting the expertise necessary to ensure that luminaires perform as expected in demanding and often extreme environments is essential to a successful outcome.
MANAGING CHALLENGING CONDITIONS
The maritime industry is responsible for transporting around 90% of items around the world, underpinning the global economy. How critical it is to keeping the world’s economic cogs turning was brought into sharp relief earlier this year when the massive container ship the Ever Given blocked the Suez Canal for six days in March.
We therefore depend on it being efficient, safe and cost-effective. However, many ports and terminals are still using lighting solutions that fail to achieve their full operational, economic and environmental potential.
Another complicating factor is that ports can face extreme and varying weather conditions. For example, temperatures in Dubai’s Port of Jebel Ali can reach highs of 45 °C whereas CentrePort Wellington in New Zealand is notorious for its high winds.
So, environmental factors must be considered when investing in LED lighting in this sector. In challenging environments, where lighting is fundamental to the continuation of operations, one solution does not fit all, and every single part of the product specification must be considered.
At Midstream Lighting we very much advocate the importance of taking a holistic expert approach that factors in such challenges. Ports and terminals are typically wet and saline-heavy environments. Therefore, necessary precautions to mitigate potential damage and reduce maintenance caused by these harsh environmental factors are essential. For example, we would recommend to clients to consider as standard:
• Powder-coated marine 316-grade stainless steel and marine-grade aluminium to resist corrosion • Vibration-resistance measurement of 100,000 cycles at 6G to inform durability and reliability • Reducing the fittings’ weight and susceptibility to wind loading • TM21-rated equipment to ensure longterm reliability and reduced downtime • Designed-in glare and light spill control • Long warranty
With no one port layout the same, flexibility from a wide range of optics is also key. By using the optimum choice of optics tailored to a specific location, port and terminal owners and operators can simultaneously control lux and uniformity ratios whilst reducing glare.
HIGH-HEAT ENVIRONMENTS
Failing to factor unique environmental elements, such as temperature, into purchase decisions can result in costly downtime, dangerous working conditions and a failure to comply with regulation later down the line.
The cheapest option is not always the most cost-effective, considering the lifespan of a project. Considering the differing extremes in temperatures in ports around the world, lighting must be built with the appropriate features, like an extruded heatsink, to allow highly efficient heat dissipation, amongst other unique specifications.
This keeps lumen degradation to a minimum, extending life and performance – without this specially designed heatsink LED lights can simply burn out and fail.
Furthermore, with global temperatures set to rise due to the impact of climate change, this level of detail is vital to ensure port and terminal owners are making reliable long-term investments.
UNDERSTANDING ‘DIRTY’ POWER
Similarly, ‘dirty’ power, which can include low power, voltage variations, frequency variations and surges can cause significant disruption to maritime operations.
This is partly due to the amount of energy required to power sprawling infrastructure and equipment at ports and terminals. A critical element in all ports and terminals, lighting must be protected from potential surges to avoid costly downtime.
LED lighting should therefore contain elements, such as an integrated two-step surge protection feature, to safeguard the luminaire against potential power surges, and enable more reliability and longer performance.
This type of construction is vital to ensure the structural integrity and guaranteed lifespan of the product and as well as to protect the commercial reputation of the port or terminal.
As engineers and lighting professionals, we recognise that it is our role to help change perspectives. There is a necessary education role to support sectors such as the maritime industry to understand that purely commodity-based purchasing decisions to lighting are overlooking essential value-added benefits, such as improved durability, efficiency and sustainability.
PROVING THE BENEFITS
The energy-saving potential of LED lighting in ports and terminals is verified and tangible. Let’s illustrate this by looking in more detail at a number of recent projects that we have been involved in.
Midstream recently contributed to a modelling exercise at the Port of Tyne, as well as a long-term analysis of its electricity network. This saw the port successfully reduce its energy use by 2.3 million kWh, eliminating more than 1,500 tonnes of CO2.
As part of its clean strategy, we designed
Maritime lighting
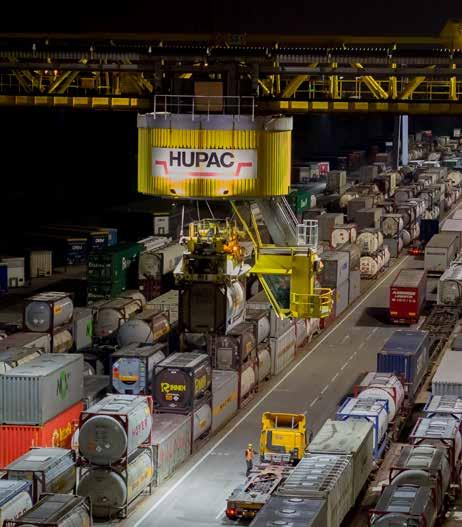
The Hupac Terminal in Italy. Outdated metal-halide lighting has been upgraded to LED, improving light quality, safety, energy use and employee wellbeing
and provided a unique high-mast lighting solution that turned only four of the floodlights on at dusk. The six remaining floodlights could be turned on with a push button on the mast, to provide the higher lux values when required.
Our Titan 420 series of LED floodlights enabled not only huge energy savings but a 50% increase in light levels.
In the same way, we secured a 65% energy saving for Hupac Terminal, Italy by upgrading the outdated metal-halide lighting systems on its cranes with 120 of our ‘Docker’ 350 and 150 luminaires.
The Docker series was the most effective upgrade for the terminal’s 1,000kW and 400W floodlights, which were proving costly to maintain. This was mainly due to the moving parts in the metal-halide lamps being easily damaged by the vibrations of the moving cranes.
The quality of lighting is also a key element of enabling safe and secure operations, whilst ensuring employee wellbeing.
Another area we have been involved in is intermodal terminals, or terminals that combine the movement of goods from rail to other forms of transport, such as street or highway.
Like most intermodal terminals, the Intermodal Terminal of Trieste in Italy operates 24/7, which means lighting is critical to its operations and the wellbeing of its workers. Yet, at the time, it was using old-fashioned high-pressure sodium lighting systems.
We replaced 1,000W sodium projectors with 455W LED technology, with the number of lighting units cut from 60 to 47. The result was 73% energy savings and high uniform light levels across the whole yard – without any light pollution for the neighbours.
Likewise, a ‘one-size-fits-all approach’ is not the most effective option for port and terminal owners and operators with unique requirements.
Total Terminals International (TTI), Pier T at the Port of Long Beach, California, was designed for maximum efficiency and productivity and therefore required lighting to support its seamless operations.
We were tasked with replacing the 1,400 high-mast 1,000W metal-halide lighting fixtures to cut energy, operational, and maintenance costs, while keeping the exact number of luminaires.
It was this project that saw the creation of our versatile ‘Atlas’ series. These madefor-purpose 330W and 660W lighting fixtures were designed to be robust enough to cope with the hostile conditions and be highly efficient at the time.
By combining them on a single pole, they were able to deliver the required illumination at the lowest possible energy consumption – around 500W. Once installed, the increase in colour of the light made the port a much safer place to work, as well as increasing energy savings by 60%.
SUMMARY
The maritime industry is currently navigating a period of unprecedented change and addressing major challenges, such as decarbonising operations, and exploring advanced technologies to revolutionise the terminals of tomorrow. Therefore, increasing the sophistication of lighting systems is unlikely to be at the top of the agenda for many busy operators.
Yet, by taking a consultative approach, we have been steadily helping to build awareness in the industry that there are very real and accessible advantages in making incremental operational changes, such as upgrading lighting.
These can be, broadly speaking, a highly transformative process and delivered quickly with minimal disruption. These types of initiative are not only creating significant cost-savings and improving health and safety they are also paving the way for performance gains in other areas of port operations.
Investing in lighting, now, illuminates the pathway for other aspects of improvement and raises the bar for sustainability and performance tweaks in overlooked operational aspects of the maritime industry.
Moreover, this is not unique to the maritime industry. This is why we believe it is important that, as a lighting industry leader, we remain passionate about highlighting the benefits of modernising lighting solutions and helping lighting systems to be viewed as a key strategic asset.
Simon Newcombe is head of specification at Midstream Lighting
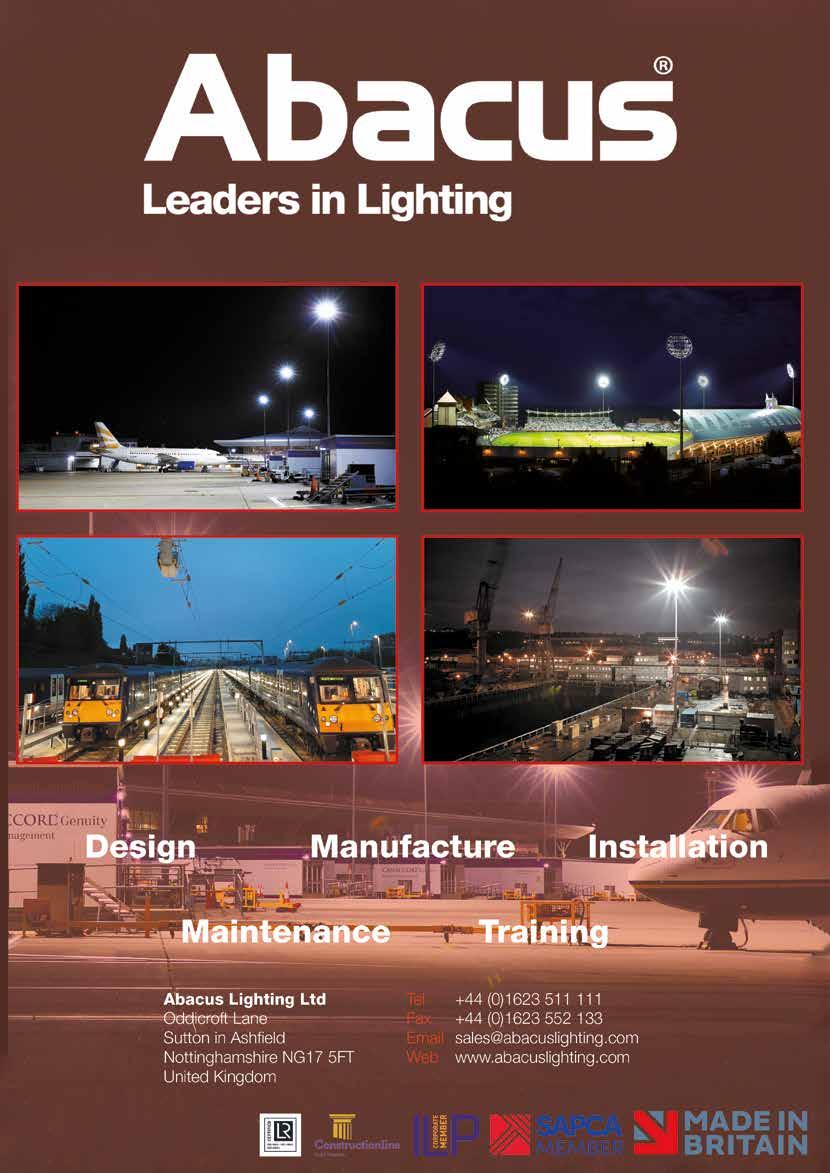
A series of eye-catching sailing mast-style 19m-high wooden lighting columns are at the heart of the regeneration of Ostend’s old fishing harbour in Belgium

By Nic Paton
The port city of Ostend is Belgium’s largest coastal outpost and a beautiful example of Flemish architecture. For the past few years, the city’s previously rundown old fishing harbour has been undergoing regeneration, with the creation of a new residential and retail district called Baelskaai as part of what is known as the Oosteroever masterplan.
Lighting, naturally, has played a key part in this transformation, not least a series of 11 eye-catching bespoke, sailing mast-style 19m wooden columns, complete with 6m-8m aluminium bracket arms.
The project has been led by architects Ateliers JEOL, with the columns supplied by Valmont and manufactured by Tehomet, a subsidiary of Valmont.
‘The original columns were outdated functional concrete and rusty steel columns; the new poles have created a massive change,’ explains Anish Samani, EMEA decorative structures and marketing manager at Valmont Structures (UK), the UK arm of the company, to Lighting Journal .
‘The project really proves how it is possible to create something that acts as a feature within an urban environment, a placemaker for the city,’ agrees Brecht Warlop, Benelux sales manager for Valmont. ‘Ostend is one of the nicest Belgium seacoast port cities; it is a beautiful project. It has been very much about combining the architectural with the functional.’
JULY/AUGUST 2021 LIGHTING JOURNAL 29
Public realm lighting
STRUCTURALLY CHALLENGING
The project began in 2015 and the new columns were installed on site in 2018. This is the first phase of the project, with a further ten smaller wooden columns to be installed within the surrounding streets from this summer onwards. Versions of the column are also to be installed at the city’s railway station.
Because of the height and the length of the bracket arms, structurally the columns posed a challenge. ‘For me, in my 15 years at Valmont, I have never experienced Valmont produce a product of this scale with that length of arm, in steel, never mind in wood,’ highlights Anish. ‘I have people asking, for example, “does the column have a steel core?’, that is a very common question, with the answer, no, this is an engineered product and is also constructed with a hole in the middle.’
‘Standard lengths of poles are 12-13m, however these are 19m; it was necessary to design a method to connect them together from two pieces. Usually there would be a visible steel joint in the middle. In this case, we could conceal it inside the pole and so we constructed it into the arm connection, so the join could be concealed behind the connection plates; nobody can see there is any kind of joint in the pole,’ adds Sami Hämäläinen, sales manager at Tehomet.
CROSS-COUNTRY COLLABORATION
The complex engineering process involved a lot of cross-country collaboration and co-ordination, with the aluminium bracket arms being constructed by Valmont France and the rest of the column in Finland, as Joonas Innanen, product development and engineering manager at Tehomet, explains.
‘With the arms, they were quite challenging. Valmont France produced the aluminium arms and the wooden shaft and the column was designed and manufactured in our factories in Finland. It was very much a Valmont team effort. The biggest challenge was to combine these things together to meet all the requirements from the lighting design and architectural point of views. So, it needed very close co-operation between our sites and the architects,’ he says.
‘Structurally, the length of the bracket arms was the biggest challenge. Valmont France carried out extensive calculations to ensure the steel wires were of the strength required, so that we could be sure they could handle the loads from the length of the arm. After that we made a combined calculation model to take into account all the variables, including the exposed location, strong winds across the harbour and squalls and storms of course.
‘Everything was calculated, we also tested it extensively physically of course, especially the most stressed connection, the arm and the wooden section. Considering the columns were being produced in different parts of Europe and then assembled, we all had to work together closely with quite precise models and share those between the different sites so that all the dimensional details came together precisely,’ Joonas adds.
‘It is a great example of what, technically, can be achieved, how it is possible to push the limits of engineering,’ agrees Anish. ‘The scale of it, when you are standing in front of it, is amazing.’
‘Sometimes with this type of project it is difficult to rhyme the technical with the architectural, but I do feel this is a great example where the two have come together really well,’ adds Brecht.
FIND OUT MORE
For those who are interested, a video of the test installation (carried out on a snowy day in Finland) is available to watch on YouTube, at www.youtube. com/watch?v=th_gOR8Lfp4
CREDITS
Architect: Ateliers JEOL Contractor: Claesen Outdoor Lighting (Valmont Belgium) Column manufacturer: Tehomet (a Valmont company)