
9 minute read
COVER STORY: INNOVATIONS IN PRINTING AND PACKAGING MACHINERY
Heidelberg drupa 2024: Innovations in printing and packaging machinery
Heidelberg’s new generation of machines feature many innovative functions that contribute to cost reduction, alleviate skill shortages, enhance the sustainability of printing companies, and improve their speed to market
The demand for packaging is increasing worldwide.
Simultaneously, consumers are seeking sustainable packaging that minimises environmental and climate impact. Legal requirements related to the environmental aspects of packaging are also on the rise.
In a survey conducted in 2022 involving 5,000 consumers from five European countries, Pro Carton: Choosing Cartons for a Sustainable Future, participants identified climate change as one of the most urgent issues of our time.
Consumers place the most trust in paper and cardboard packaging from an environmental compliance perspective.
This is partly because effective recycling systems are already well-established at a high level.
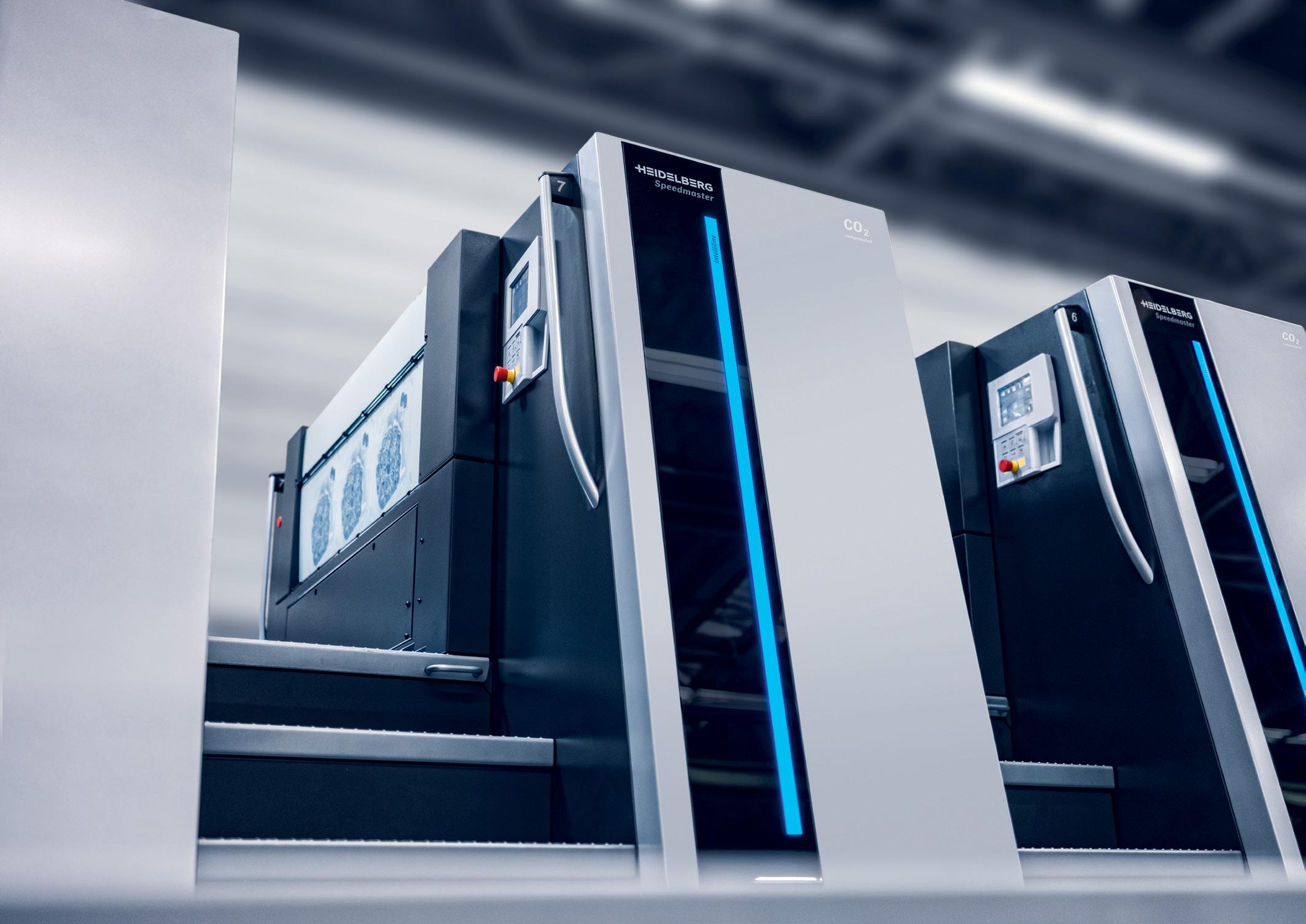
For example, in Germany, the recycling rate for wastepaper exceeds 95 per cent of total paper consumption. Across Europe, 82.5 per cent of paper and cardboard are recycled.
It is estimated that the added value in global folding carton production will increase from the current €68 billion ($110.27 billion) to €76 billion ($123.24 billion) by 2027, showing an annual growth rate of approximately 2.3 per cent.
Packaging and labels are increasingly important to the strategic future of the printing industry, with annual sales now worth more than half a trillion dollars, according to research firm Smithers.
In its The Future of Package Printing to 2029 study, Smithers showed that in 2024, the total global value in the sector will reach US$504.9 billion ($750.7 billion). This will see 14.31 trillion A4 print equivalents of labels, corrugated board, folding cartons, flexible paper and plastics, rigid plastic and metal packaging printed this year, consuming 1.54 million tons of ink.
In the printing market, there are several significant challenges, including rising material and energy costs, and a shortage of skilled labour. Print shops worldwide must address these issues while meeting demand and maintaining their competitiveness.
Heidelberg’s new generation of machines feature many innovative functions that contribute to cost reduction, alleviate skill shortages, and enhance the sustainability of printing companies.
Autonomous printing in folding carton production
Today, more than half of the sheetfed offset presses that Heidelberg sells and installs worldwide are for packaging customers. This underlines the company’s market leadership in this crucial growth segment.
At drupa 2024, Heidelberg introduced the new Peak Performance generation of the Speedmaster XL 106, featuring numerous innovations specifically for packaging production.
This new press generation, which incorporates autonomous Push to Stop operations in packaging printing, increases net output by up to 20 per cent compared to the previous generation and reduces drying energy consumption by up to 30 per cent with the new DryStar Combination Eco.

With a production capacity of up to 21,000 sheets per hour, the new generation of machines addresses major challenges in the folding carton segment, particularly cost pressure, sustainable production, and the shortage of skilled labour.
The new generation of machines also introduces autonomous Push to Stop production in packaging printing, reducing the cost per printed sheet. The main levers are increased digitisation and automation, as well as the expanded use of artificial intelligence in many assistance systems.
Another standout feature is the new Push to Stop coating unit, which integrates highly automated control systems into the Prinect Press Center XL 4. The changeover process for coating plates, anilox rollers and coating is automatically initiated at the control station via Intellistart 3 software. The necessary information is provided by the job parameters in the job queue.
Reaching a new benchmark of 100 million sheets annually
The new Peak Performance generation of the Speedmaster XL 106 can print up to 21,000 sheets per hour. With enhanced Push to Stop concepts, autonomous printing is now possible even in packaging production.
“Further automated processes promote high overall system efficiency,” Heidelberg chief technology and sales officer Dr. David Schmedding said.
“We expect to quickly reach a benchmark of 100 million sheets per year for a packaging printer with high production volumes. That means up to 20 per cent more than the current industry leaders with 85 million sheets.”
Mike Günther, managing director of German print shop colordruck Baiersbronn, a pilot customer for the new Speedmaster XL 106, said, “We expect a significant reduction in makeready, setup and general downtimes in order to improve cost-effectiveness in printing thanks to lower costs per job”.
Reducing setup waste and increasing net output
The Speedmaster XL 106 offers the optional AI-supported Hycolor Assistant. Combined with the new Hycolor XL ink/ dampening unit, this system is particularly effective for demanding print forms.
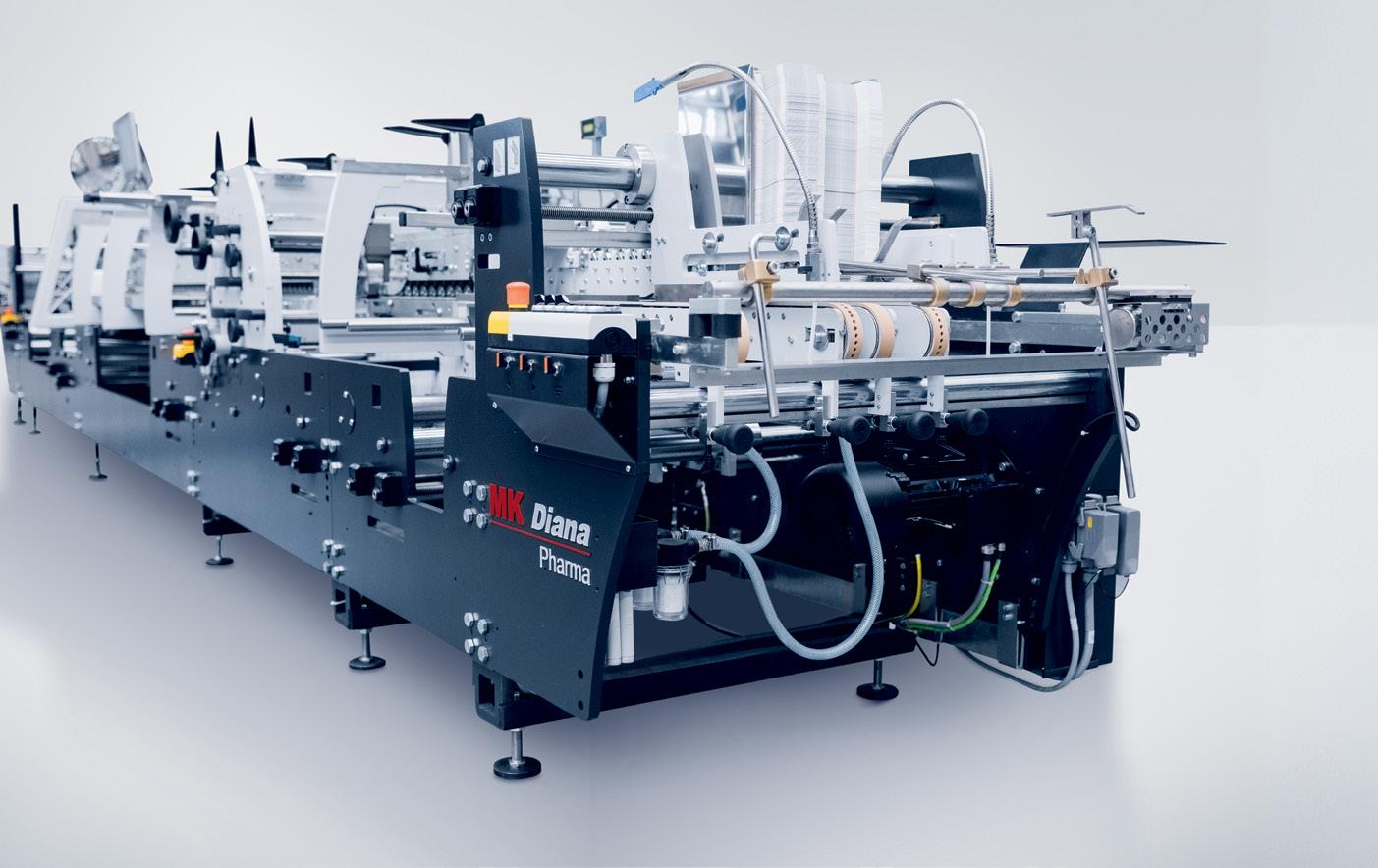
Before the first sheet enters the press, the Hycolor Assistant fully automates the optimisation of ink/dampening unit settings, including ink distribution and the Vario function. The Hycolor XL ink/ dampening unit achieves excellent results in print forms with reverse text elements in solid areas, conditions that are difficult to control with manual adjustments.
Production output is achieved much faster, and waste is reduced by up to 25 per cent, compared to using the Hycolor Assistant and Hycolor XL ink/dampening unit.
“Folding carton producers benefit, in particular, from the combination of our innovations in mechanics on the one hand and AI-supported software on the other,” Dr. Schmedding said.
“They make huge savings in material, personnel, energy and machine time. The new Peak Performance generation of the Speedmaster XL 106 is a huge step forward in terms of increasing competitiveness.”
New DryStar Combination Eco –Saving up to 30 per cent energy
For the new generation of the Speedmaster XL 106, Heidelberg offers a new dryer technology, the DryStar Combination Eco, available on request. Cantilever insulation, crossflow heat exchangers, and an improved dryer cassette design enable up to 30 per cent energy savings compared to the previous generation. This energyefficient dryer is particularly interesting for markets with high energy prices.
In Europe, where energy prices are very high, investments in the DryStar Combination Eco typically pay off within about two years. Furthermore, the faster the printing speed, the lower the energy usage per 1,000 sheets.
For example, increasing the printing speed from 18,000 to 21,000 sheets reduces energy consumption by approximately 4.5 per cent. This energy saving feature is expected to bring print shops cost savings in A/NZ as well.
“Given the rising energy prices, we expect this new drying technology to help reduce energy consumption pressures,” said Stefan Leonhardt, president of WEIG Packaging, a pilot customer of the new generation.
“The new press also automates key processes in folding carton production, resulting in improved efficiency, reduced make-ready times, and increased uptime.”
Special configurations for packaging printing
Heidelberg has long been a leader in special configurations of Speedmaster presses, and this expertise is in high demand in the market. Users of these systems are primarily folding carton and label printers, who particularly value the extensive finishing options and flexibility for producing high-quality packaging.
For example, last year, a major international packaging printing company with locations worldwide installed the longest Speedmaster XL 106 sheetfed offset press to date, featuring 20 units and a total length of 42 metres. This world-record press is operating at a facility in Poland. Another 19-unit press was delivered to a site in Germany.
“The high investment willingness of our customers in Heidelberg’s packaging technology underscores the trust our company enjoys among market players, especially in this demanding market segment. Through our global sales and service network, we strive daily to remain the partner of choice now and in the future,” Dr. Schmedding added.
Efficient printing demands efficient post-press processes
In today’s fast-paced packaging industry, the importance of efficiency extends beyond just the printing process. As we continue to push the boundaries of speed and precision in printing, it’s critical to ensure that our postpress processes evolve in tandem.
This end-to-end approach to production is what enables Heidelberg to deliver exceptional results to its customers, from start to finish.
Together with its trusted partner, MK Masterwork, they stand as ’Your Partner in Packaging’, ensuring the highest productivity throughout the entire production chain.
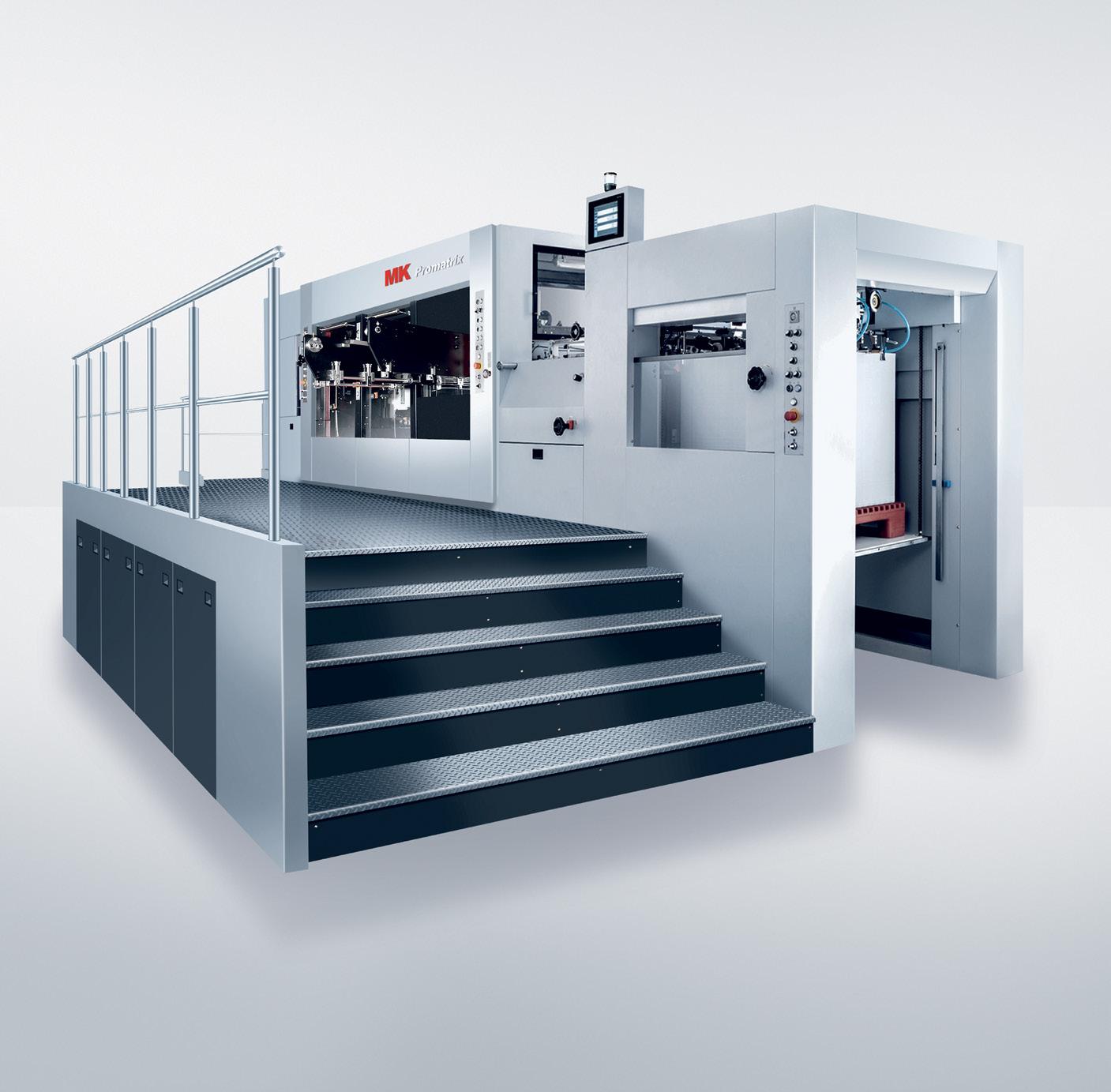
At the heart of Heidelberg’s post-press solutions are the Mastermatrix die-cutting and Diana folding carton gluing machines, engineered to transform printed sheets into perfect folding cartons.
These machines represent the pinnacle of post-press technology, where innovation meets reliability to meet the highest standards in the packaging industry.
Both the Mastermatrix and Diana machines follow a shared philosophy: automation that empowers operators, optimises production efficiency, and reduces manual touchpoints. This philosophy is embedded in every aspect of the design, from shortening make-ready times to ensuring seamless operation.
By streamlining these critical processes, Heidelberg helps its customers enhance productivity, reduce downtime, and maintain consistent quality across every job.
Its Diana Pharma 85 folding carton gluing machine shown at drupa was especially developed to meet the requirements of the pharmaceutical industry. In addition to its compact design, the machine is characterised by exact folding and gluing, precise and powerful embossing and fast and uncomplicated changeovers.
At just 12 metres, the Diana Pharma achieves a running speed of up to 250m/ min and, with the integrated Diana Braille module, provides up to 60,000 packages and more per hour with Braille.
With Heidelberg’s post-press equipment, the company takes pride in not only meeting the demands of today’s packaging market but in setting new benchmarks for efficiency and automation.
“When choosing Heidelberg, you choose a partner that is as committed to your success and driving the future of packaging forward, one perfectly folded carton at a time,” Dr. David Schmedding said.