
9 minute read
COVER STORY: CCS PACKAGING INSTALLS RYOBI RMGT 970 7 COLOUR OFFSET PRESS FROM CYBER
CCS Packaging installs Ryobi RMGT 970 7 colour offset press from Cyber
CCS Packaging CEO Gerry van Happen believes the new Ryobi RMGT 970 and its larger sheet size, will provide the business with a greater ability to service customers
Waiting two decades for a sale requires patience and persistence, but this is precisely what Bernard Cheong from Cyber had to do to confirm his sale of a Ryobi RMGT 970 7 colour offset press with coater to CCS Packaging.
“I first visited Kevin from CCS Packaging over 20 years ago,” Cheong remembers.
“I was joined two decades ago for the first meeting at CCS Packaging with my colleague George Williams who unfortunately didn’t live to see the final sale.
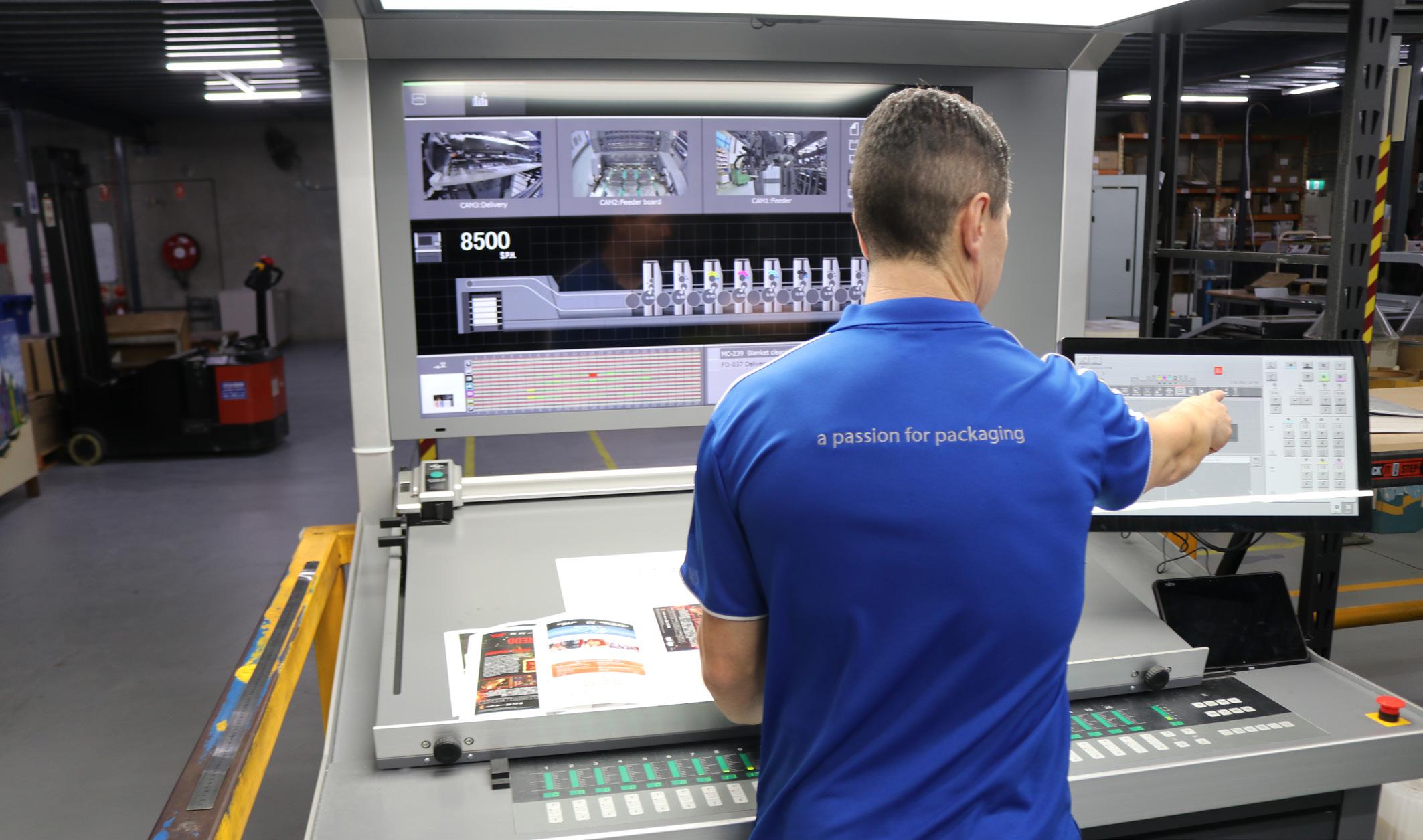
“We were unsuccessful on that occasion and since then Kevin has bought six offset presses from another company, so we feel very fortunate to have confirmed lucky number seven.
“We welcome CCS Packaging to the Cyber family and they join over 200 other RMGT 970 presses sold globally and the second RMGT 970 in Australia,” Cheong said.
Kevin Wilson from CCS Packaging purchased the machine almost a year before it was delivered and installed within his factory located at Silverwater in Western Sydney.
“As our business evolved we told ourselves that we needed a packaging press that was customised for use in the packaging industry. Previously we were using a commercial press for packaging production. Now that we have a customised machine, this is a serious packaging press that is built for purpose. We now have the ammunition to make a serious investment into the packaging category – whereas before we were merely just assessing the segments in the packaging landscape. We expect this will provide substantial benefits and really open up opportunities for our business,” Wilson said.
The Ryobi RMGT 970 machine purchased by CCS Packaging has been customised with a Skeleton Transfer System and this is the second press in the world with this system – the only other machine is in Korea.
“This does an equally good job as a RMGT 10 Series, and will integrate perfectly into their workflow,” Cheong said.
“For packaging printers, versatility is key. The 7 color Ryobi 970 configuration with the skeletal transfer system will provide the versatility required to allow CCS packaging to take the company to the next level.
Packaging diversification
CCS Packaging CEO Gerry van Happen says the business has historically serviced the music and media industries, but is now diversifying into other categories.
“CCS built its reputation over 37 years in the very exciting media business producing packaging for vinyl, CD, DVD, Blu-ray and games categories. These industry segments have declined in the last seven years, but they are still a vital contribution to the business with CCS being the market leader for media packaging in Australia. Interestingly, over the last five years vinyl has been rediscovered and is now worth more than CDs in dollar terms. Vinyl is now a luxury product with high specifications representing both international and local artists.
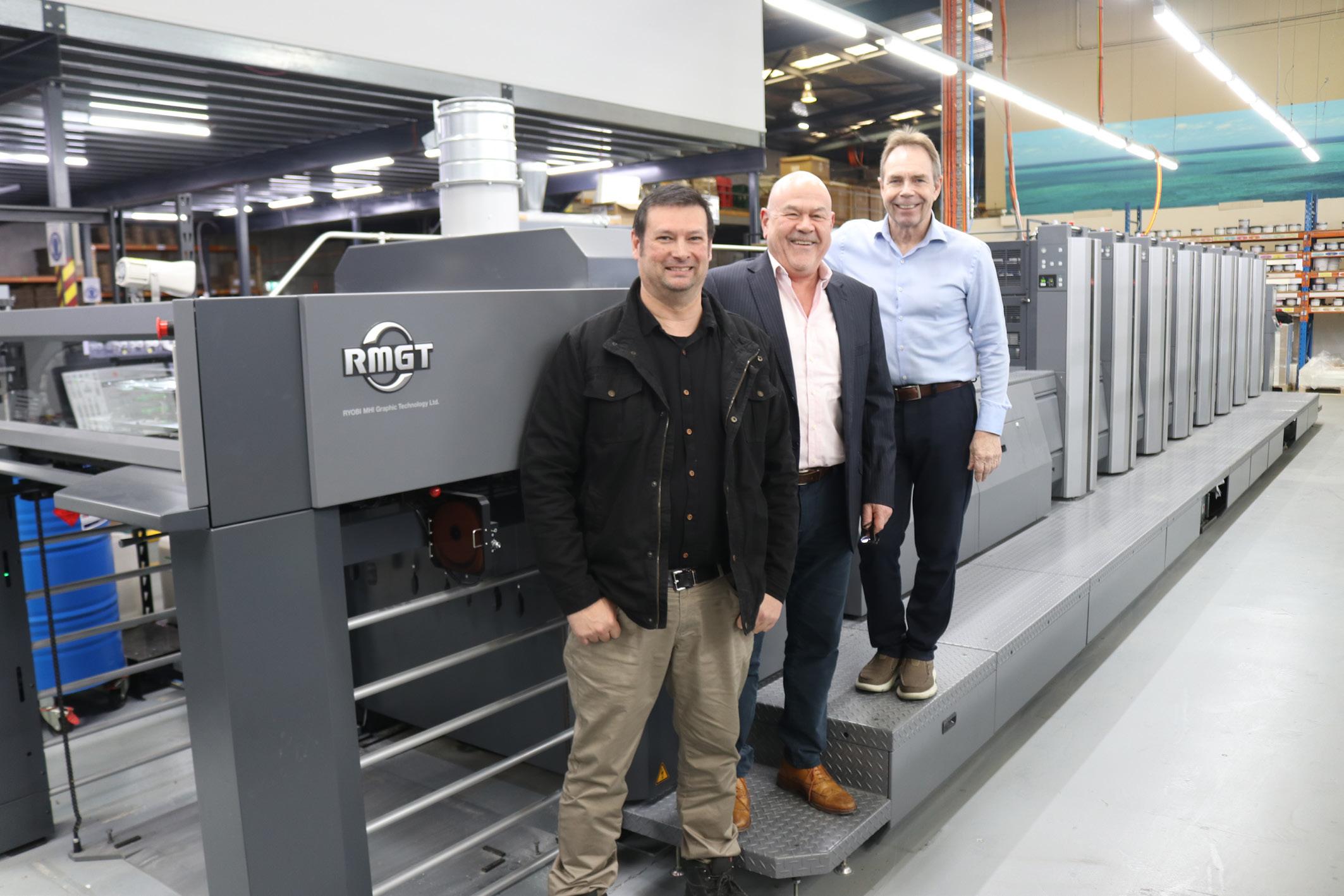
“Our largest packaging segment is now represented by the cosmetic, personal health and loyalty card businesses. Our experience in producing high quality products on short lead times has allowed us to grow this area. With in-house coating, rigid box, hard cover and finishing equipment we able to produce the vast majority of products without any outside operations. Further investments this year have also enhanced our position and we are always looking at ways we can offer our customers value options.
“CCS built its business on fast turn arounds and high quality. We have translated this knowhow into the packaging segment. The new Ryobi with its larger sheet size, will sit very nicely against our current eight colour with coater press. We have great fire power, superb finishing and complimentary equipment to offer to our customers,” van Happen said.
Shifting clients to onshore
CCS Packaging works closely with its current and potential customers to encourage them to consider the benefits of onshoring their packaging work.
“Even before the recent epidemic we were asking our potential customers ‘what is the real cost of producing offshore?’. We found that by equating the cost of tying up capital in large order quantities we could offer faster deliveries more often. There is more to the real cost than just a cheaper off shore quote,” van Happen said.
CCS Packaging Operations Manager, Simon Studdert, is also very passionate about the benefits of keeping work in Australia and explaining the numerous benefits this presents for customers and plans to compete directly with overseas printers rather than local businesses.
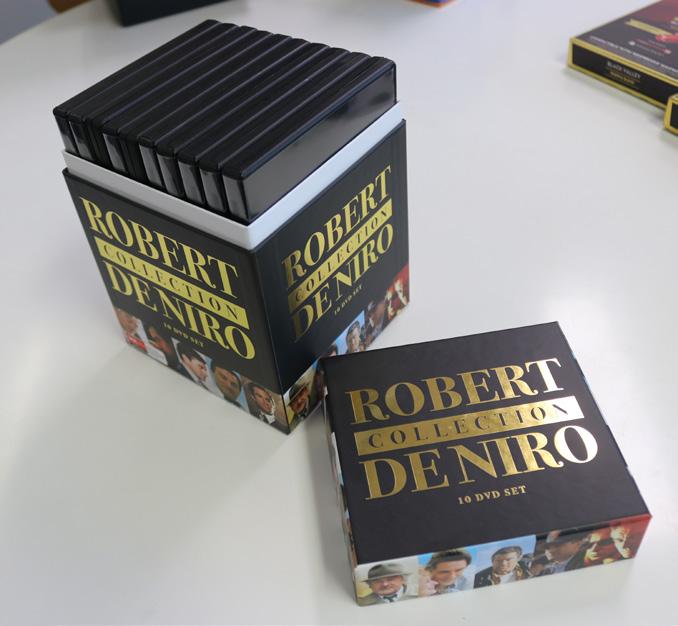
“We have had success changing the views of several customers who can see the benefits by looking at the entire job as well as the advantages of printing onshore –and not just the unit price. We have taken our hard earned media knowledge to challenge the mindsets of potential customers regarding offshore print and packaging procurement. Are customers really getting a better price offshore compared to onshore? Sure, the unit price may be better, but what about shipping cost and warehousing.
“With higher minimum quantities required for overseas printing, we have seen a number of customers run into problems after a large run when there is a change that needs to be made – particularly with ingredients for food packaging or out of date content for pharmaceutical packaging. All of that stock that has been brought in from overseas that is no longer usable needs to be destroyed. By offering a local solution with a faster turnaround time – customers also don’t need to order as many which can also be very beneficial to cashflow as well as the costs associated with storing a large amount of packaging. Real estate is also very expensive when used to store out of date packaging.”
Purchasing the Ryobi RMGT 970
As part of the extensive research leading up to the purchase of the machine, a trip to Japan was organised by Cyber NSW Account Manager Giorgio Rossi to test the Ryobi RMGT 970.
“Before we purchased the machine, we had a great experience travelling with Giorgio to Ryobi in Japan and we were very well looked after,” Studdert said.
“The professionalism of the team at Ryobi was brilliant and they couldn’t be any more accommodating. We went through the entire assembly plant as well as some of the other parts of the business including the die-casting facilities for the automotive industry.
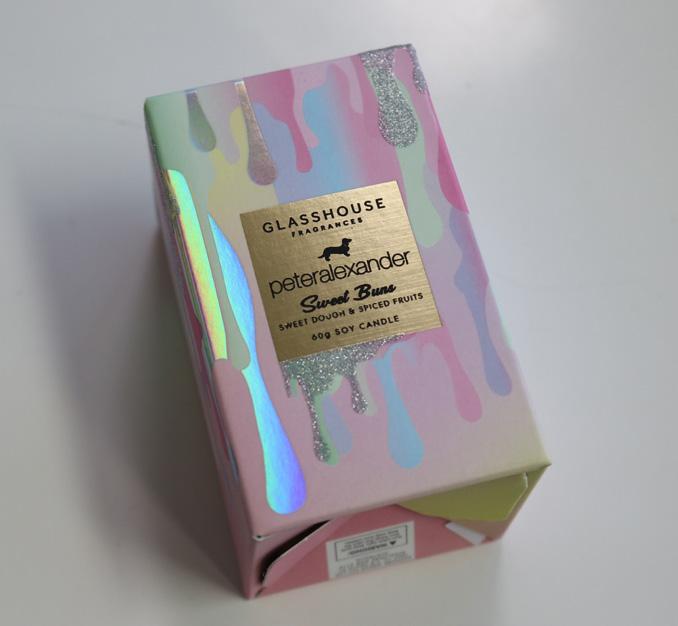
“To test the machine, we trialled several technically difficult print jobs within the demonstration centre. We tried to push the machine past its limits with work printers have nightmares about. However, the Ryobi RMGT 970 passed with flying colours. We tested thin stock with very heavy ink coverage and fine reverse out type, followed by maximum thickness board at high speed with full solids. The press delivered mark free print with very clean screens. Metallics and fluoros with fine reverse out text remained open with no evidence of roller, gear marks or emulsification.
“During the testing, Ryobi RMGT 970 were very accommodating with their press time and access to the finer mechanical details of the machine. From the research I did, I was quietly confident that the machine would pass the tests, but I expected it to have some trouble with setting up – but that wasn’t the case – it went from one substrate to another with ease.
“Giorgio from Cyber was very helpful with providing us with specifications, configurations and information on all the machine’s systems answering any questions I had about the machine during the research process.”
Skeleton Transfer System
This press features the Skeleton Transfer System which allows the wet side of the sheet to travel the length of the press without any contact. This also eliminates the need for regular IPC film cleaning and replacement. The new Ryobi RMGT 970 with a sheet size of 970mm x 650mm complements the existing B2 eight colour press within CCS Packaging.

“This is the first installation in the southern hemisphere for this particular machine which is a 0.8mm spec machine that allows the printing of stock up to 800 micrometre boxboard.
“The Skeleton Transfer System means there is no IPC film that always needs to be cleaned by the operator. There is no build-up and then after a certain amount of impressions the cylinder on that film goes blind, so you have to replace it as it is a consumable. All of these issues are eliminated with this set-up – there is no marking and most importantly it creates better quality results. The side-lay on this machine is a new design – it is not just a pull side-lay, it also has a push from the opposite side that gives a more positive registration,” Rossi said.
“Purchasing this machine brings us into a different space in the market. It is also ready for us to embark on using the seven colours to produce the many special colour variants required in packaging. There will also be further technical opportunities that the Ryobi will be asked to achieve for our business and our customers.”
Installation and training
The installation of the Ryobi RMGT 970 was conducted by Cyber demonstrator John McCallum.
“John is based in Sydney and has worked with Cyber’s Ryobi machines for over 20 years. He has full factory training and is always on site when machines are installed,” Rossi said.
“Our installer and demonstrator John McCallum has been fantastic to work with,” said Studdert.
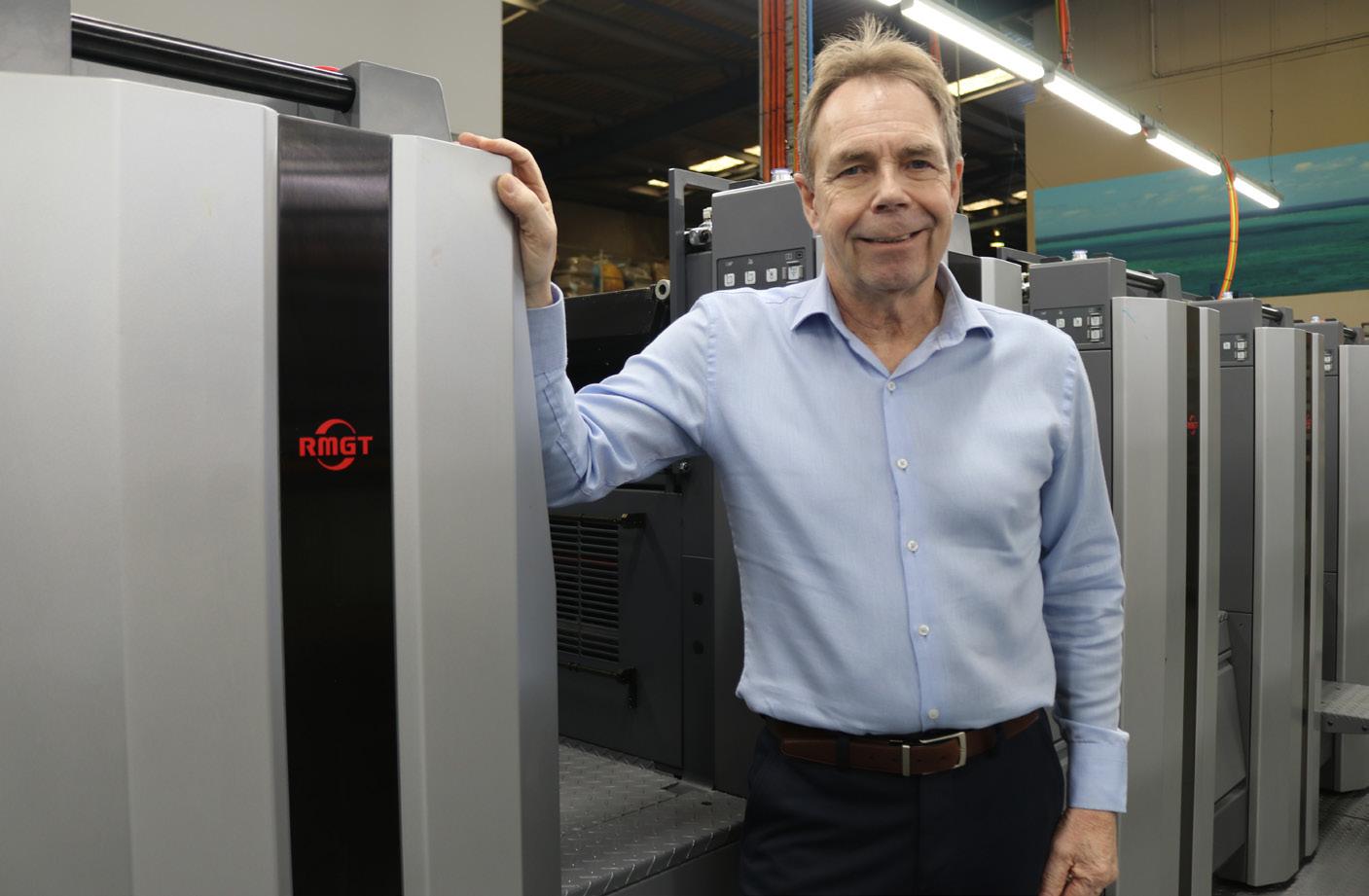
“His knowledge and experience was very thorough. John would stay back for hours each day to ensure the machine was 100 per cent and our operators had the support during the training stage. His enthusiasm and passion for what he does, shows in his work.”
Studdert said the graphical user interface (GUI) on the Ryobi RMGT 970 has been one of the key elements that has helped staff make the transition to the new machine during the training and installation process.
“Having mainly operated German presses, we found the iconology and operating system of the Ryobi to be very intuitive. This was also important, as it makes the transition from one press manufacturer to another a lot easier for our staff.”