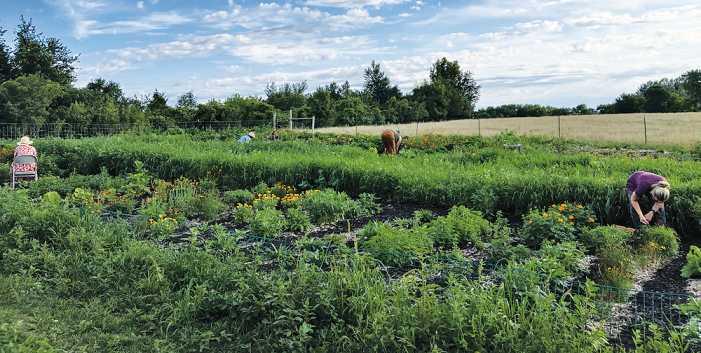
2 minute read
Small plots from many growers fuels Salt of the North Dyes
By LAURA COLE
The Land Staff Writer
Advertisement
The concept of farm to table is likely a familiar one: in basic terms, it’s buying produce locally. But there is more to the end result. It means knowing where food comes from, avoiding a more processed version of the product, and supporting communities.
Maddy Bartsch, a plant-based dye farmer and founder/owner of Salt of the North Dyes, values the idea of farm to shirt just as much as farm to table. “Textiles feel like a sister to food for me,” Bartsch said. Last year, Bartsch along with Theresa Bentz of Get Bentz Farm were approved for a grant with North Central Region –Sustainable Agriculture Research and Education (NCR-SARE) to delve deeper into larger-scale dye plant farming and lay a foundation for the makings of a farmer-owned dye plant cooperative.
Bartsch became acquainted with Theresa Bentz through Three Rivers Fibershed, a Midwest affiliate of the global Fibershed community. The organization embraces a cyclical “soil to soil” perspective to benefit the environment. Bartsch is a co-founder and the current president of Three Rivers Fibershed. Bentz is a steward member of Three Rivers Fibershed and also raises sheep and operates a wool mill.
According to SARE’s website, grants through the organization are intended to allow farmers and ranchers to “explore sustainable solutions to problems through on-farm research, demonstration, and education projects.” Last year, Bartsch and Bentz planted about 17 species of dye plants on a little less than a quarter of an acre on the Get Bentz Farm to begin their research. Now, one year into the 23-month grant, Bartsch reflected on their background, the importance of the dye plant industry, and how the grant can create a new option for Midwest farmers.
An interest in textile production blossomed while Bartsch attended college at the University of Minnesota, majoring in Sculpture and Fashion Studies. While participating in an apparel program,
Bartsch gravitated toward a more “agricultural pursuit.” Bartsch noted, “I was really interested in everything that led up to making fabric.”
Bartsch began learning more about the full “sheep to shawl” process by any avenue available: attending classes, reading books, and watching videos about spinning, weaving, and dye plants. Living in the cities, Bartsch rented a community garden plot and planted herbs and natural dye plants.
Dubbing 2014 “the year of wool,” Bartsch interned at farms learning firsthand from shepherds and also worked at a fiber mill in Hastings. Bartsch recalled dye plants were more in the background during that time, but noted that working with dye plants was something which “came natural, was enjoyable, and soothing.” A few years later, Bartsch shifted focus toward working with dye plants and began teaching classes.
Synthetic fabrics such as nylon, polyester and spandex are often made with petroleum. Bartsch pointed out that our largest and most porous organ is our skin. To use naturally-colored fabric, Bartsch stated, “is so much better for the environment and all parties involved.”
Bartsch noted that while restaurants are making a point to offer local foods on their menus and consumers may be more interested in buying clothing from local designers, concepts such as ethical fabric, fabric traceability, and understanding color origins are still relatively new.
Bartsch noted the local fashion industry is “missing the infrastructure to have yards of local fabric available.” By increasing the number of sustainable dye gardens throughout the region, Bartsch hopes to alleviate some supply chain gaps for designers, artists, and makers and allow them to have more availability of naturally dyed fabrics and yarns while also implementing ethical practices and providing more transparency about the agricultural practices used.
Bartsch’s plan also brings farmers another option to diversify. By becoming part of a cooperative, farmers with even a fraction of a spare acre can incorporate dye plants into their crop rotation. “A joint venture is the way to increase scale,” Bartsch explained.
Because of the plants’ structures, dye gardens require hands-on work. Bartsch used the French Marigold as a harvesting example. “The flowers don’t just sit on top. You have to go around the whole plant,” they said. Bartsch stated using a tractor or implement would not be practical, and while thought has been put into how certain tools could be adapted
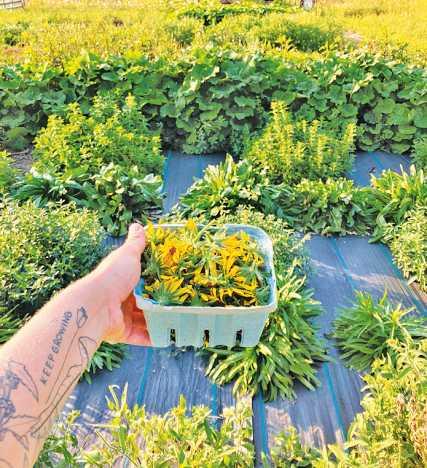