
7 minute read
SPOTLIGHT•K5600
A TORCH FOR QUALITY
By Iain Blair
“When I started this company 30 years ago, there were about ten manufacturers worldwide of HMIs, making professional lighting for the movie industry. Now there’s about 200 manufacturers, and you’ve probably never heard of half of them,” says Marc Galerne, cofounder of K5600.
But, what you will have heard of is K5600’s Joker, an HMI fixture with a parabolic reflector and set of lenses which broke into the market in 1992.
“The Joker was really a game-changer,” says Galerne. “We sold thousands and thousands of them. It made a difference, because it was the first time an HMI light was packaged in a kit, with a lot of accessories such as the Soft tube to make it like a long fluorescent lighting device. There was the ability to plug into the wall and still have a big amount of light, and a one-man-band could do everything. It was such a success that we only ever made one version update over the past 30 years.”
The Joker2 was a complete redesign, including improved strain-relief and braking systems, quickchange lamp access, and numerous ballast features, including high-speed, dimming and wireless control.
The Joker range was joined by the Bug-Lite, a 400W daylight HMI system without optics to take full advantage of Lightbanks, and K5600 subsequently combined the two to form the Joker-Bug HMI Par System. The latter saw action on location globally for TV dramas such as CSI and 24, as well as on films such as 007 Skyfall and Defiance, and deployment by Haris Zambarloukos BSC GSC on Cinderella. Then when the BBC’s Casualty series moved from Bristol to Cardiff, the team led by DP Jaz Castleton selected a package of more than 60 K5600 fixtures.
“They went 100% K5600 on that show,” recalls Galerne. “By obligation with the council they had to be green and save money, and we provided all the lights. It’s been going for over ten years now, and it’s still PKE in Manchester renting the equipment. They have probably introduced some LEDs there now, for colour effects, but I know they’re still using the HMIs. We also had some big numbers like this on another TV series in France.”
Sales of the Joker remain strong and stable. The early 200W version is no longer made, but Galerne reports that the higher the output of the Joker, the better the sales these days.
“The 400 is still selling, but not as much as we used to, the 800 is still the same, but the 1600 is definitely picking-up,” he says. “I think it really depends on the kind of film you’re doing.”
The K5600 HMI range now also includes the Alpha line of Fresnel fixtures, ranging from 200W up to the 18kW Alpha 18K, claimed to be two-thirds of the size of other 18Ks on the market. It features a custom-made reflector to increase output by nearly 15%, moulded out of quartz composite material that allows the lamp to be placed much closer to the reflector, therefore reducing the physical size.
“Robert Richardson ASC is always taking K5600 18K Alphas on shoots for Tarantino – on The Hateful Eight they had four 18Ks in the snow,” says Galerne. “Wherever they were shooting, he and his gaffer were
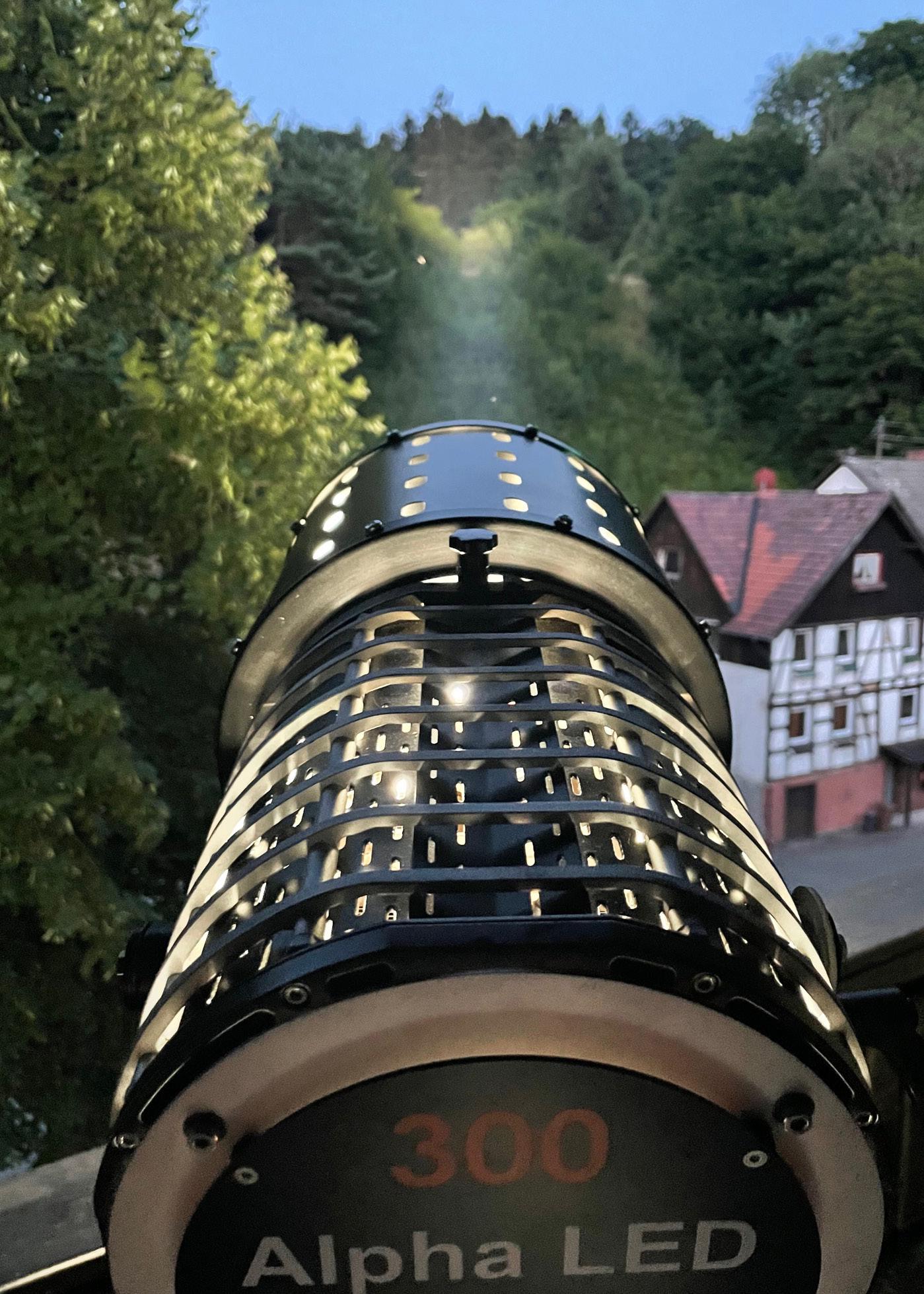



This page: Alpha 18K on The Martian, where the ability for fixture to be used pointing straight-down was a natural choice for the shot; Marc Gallerne with DP Jaz Castleton who convinced the BBC to go all-K5600 HMIs for Casualty; gaffer Julian White holding a Joker 800 in a Chinese ball on Cinderella; and testing a Joker 400 with a Softube on Casualty.
Opposite: Spacebeams in action!
asking to import Alphas from anywhere else in the world; they really insisted on them. Roger Deakins CBE BSC ASC also uses the Alphas.”
NEW LIGHT
Its maybe not surprising then that K5600 took a long run-up before entering the LED market.
“We were waiting for the right COB (chip-onboard),” says Galerne. “We felt there were so many panels around that we needed to come in with something which was much more of a directional light.
We wanted to create real shadows with a real Fresnel. The Fresnel specification has a very bright centre and a nice fall-off to the edge, and we found that had not yet been achieved when we got into the market.
“Our reputation has always been to make products which are not too heavy for end users, but very sturdy for rental companies – there are fixtures that we sold 30 years ago, which are still being rented. So, we didn’t want to go down the plastic route; we checked out building aluminium products, something really reliable, which will live longer than the actual LEDs themselves.
“It took a while to get the right combination, where we would have a COB with a size small enough to make it work with a Fresnel, which was going to be too big,” he continues. “If you want to have a real Fresnel, you need to have a very small source. So it’s a compromise between the optical quality, and also the heat dispersion. With an HMI you can go to up to 450°C at the lamp base, while for LED, an average 100° is already pushing it.
“We really wanted to be on the safe side,” he adds. “So we tested our units in our California office, where it was pretty hot and we set it to 80°C to ensure a long life of the LED, but without a quality loss and without an output loss, which is usually what happens with
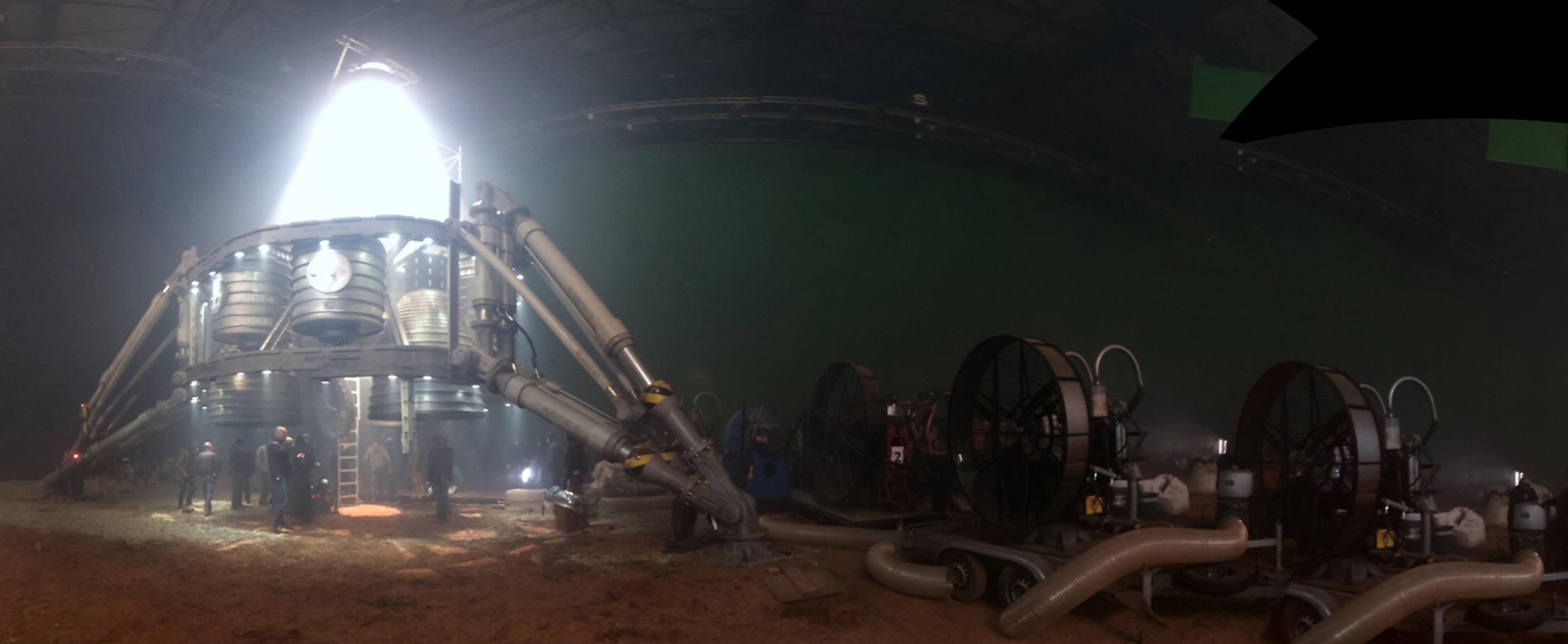
overheating elements. It took a while to do that, but we came up with a Fresnel unit, the Alpha 300W, a Joker Bug with all the accessories.”
Capable of being powered by a 300W or 1200W LED Ballast, the Joker 300 is colour tuneable from 2700K to 6500K and accurately dimmable from 1-100%. As well as several light shapers, the Joker 300 LED includes a Beamer (a par reflector of the same diameter as the Joker 400 HMI), lens and a focal spot adapter for a ‘Jo-Leko’ effect.
“It was important to us to be very versatile on the power supply,” Galerne continues. “You can plug-in up to four 300W units on 1200W ballast, which you can control independently from regular DMX or wireless. We added a range of panels, which is something we didn’t want to do in the beginning. We came into a world that we were totally new to, and basically created a system, more than just one light.
Unfortunately, we came out with it when Covid started, and then it was difficult to get components.”
K5600 has had more than its fair share of hardship and setbacks in the past 30 years, but this has built resilience that served the company well during the pandemic lockdowns.
“I was so much more prepared, because of what I’ve been through before. I had to sell my car to pay salaries one month,” Galerne says. “But you just have to do it and not think too much about it.”
“As a manufacturer, we’ve always felt that we need to have stock, and since we started we have never stopped having stock,” he adds. “When Covid came we did a lot of sales because we were able to deliver.”
As he prepares to hand over the running of the company at the end of next year, to his son, Kenny, the third generation of the family to be involved in the business, Galerne reveals that K5600 will branch into sub-rental, renting kit to rental houses.
“Let’s say the rental company has a request for four 18Ks and they only have two Alphas,” he says. “We’ll be able to sub-rent to them for a period, whether it’s a couple of days or a couple of months. The idea is to make the product available and give people what they ask for.
“We’re going to change a few things. We’re going to add some new products, whether that’s a light itself or accessories,” he adds. “There are six of us here in Paris, and six of us in the States, and we like to keep it that way. My colleagues and I want to be proud of what we’re doing and to create long-lasting quality products. We want to be able to respond to suggestions and be able to change something on a product. That is something we can do. You can’t do that when you make 10,000 units at a time.”
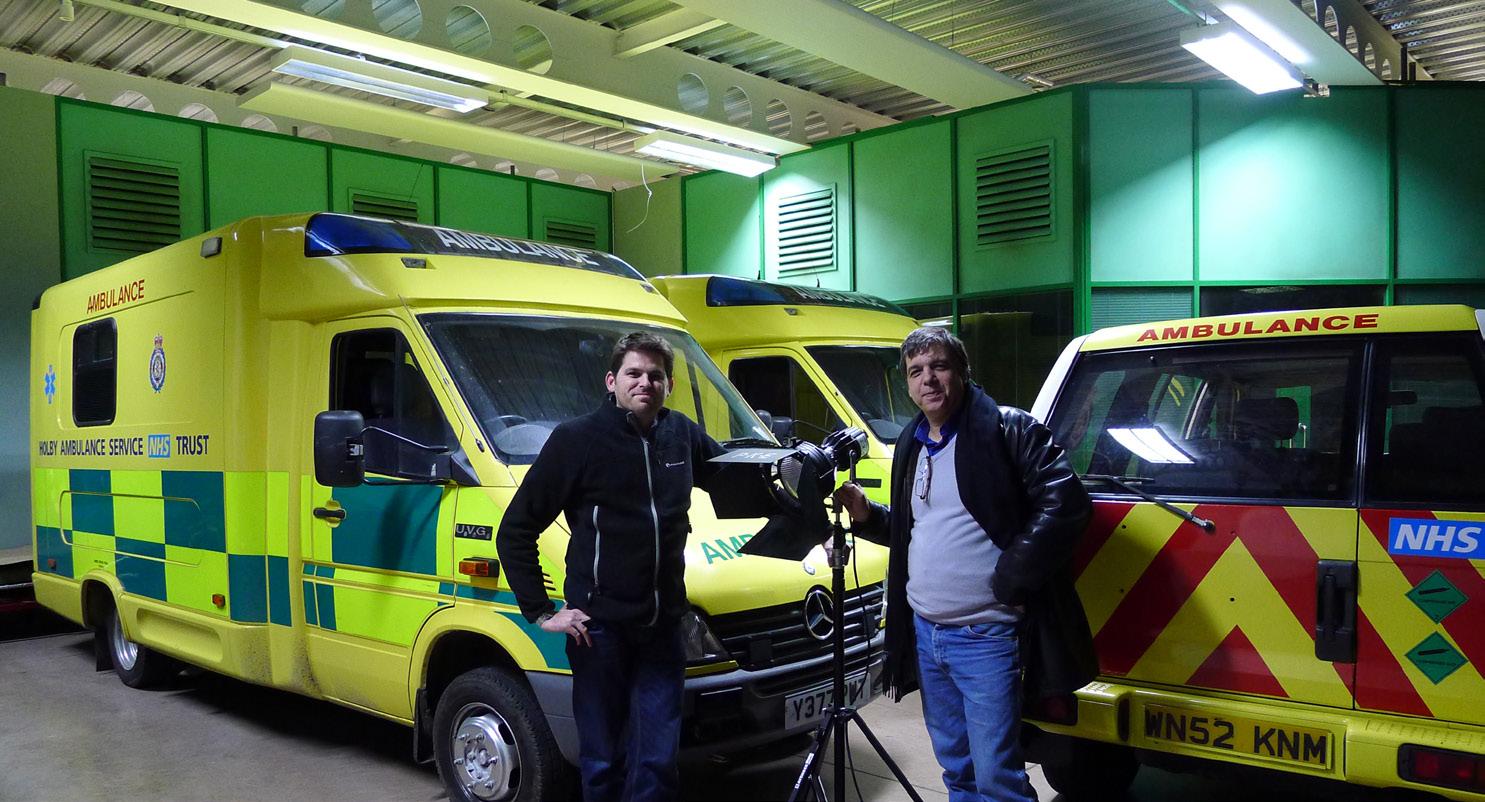
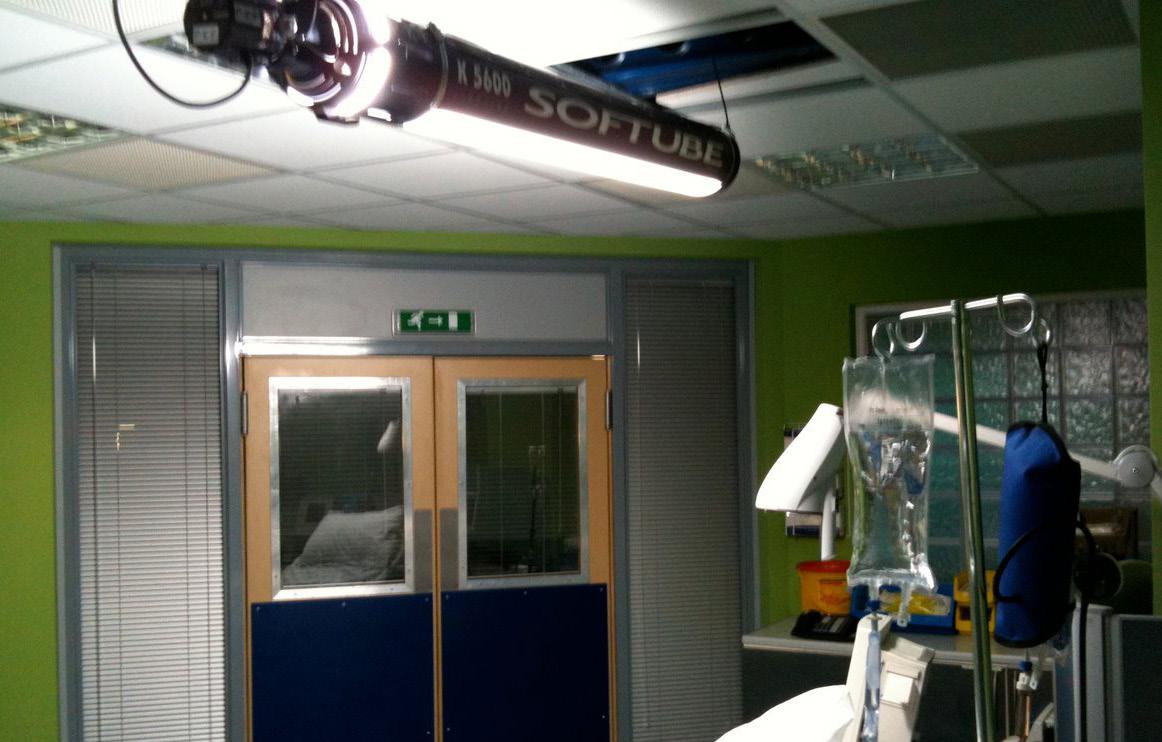
