
3 minute read
IIOM
Obsolescence Management - A New Business Essential
Stuart Broadbent
UK Chapter Chairman at IIom
With 25 years’ experience in obsolescence management and a broad spectrum of members, the International Institute of Obsolescence Management (IIOM) is the right choice for helping to tackle today’s supply chain hurdles.
IIOM is 25 years old this year. Having started in the UK as the Component Obsolescence Group (COG) in 1997 to bring together asset owners and operators, manufacturers, public bodies and obsolescence solution providers, it now boasts a global membership and a professional recognition scheme, and has four active chapters - in France, Germany, UK, and USA.
We all love the buzz of getting the latest technology but how often does it not work as planned with integrated systems or require other support? The modern world is a whirlwind of technological creativity and advancement. However, there are many applications for which newer, smarter, and faster means an existing system or product no longer works and is pushed towards a premature end-ofservice or obsolescence.
Electronic systems such as air traffic control, aviation flight computers, railway signalling, nuclear powerplant controls, medical scanners, and communication infrastructure have always been susceptible to being overtaken by new technology, but could we have foretold a situation where today’s electronic component supply chain would be so badly affected by long lead-times shortages and where even the most common parts would be hard to find, and then liable to being declared obsolete? For equipment with long development and service lifecycles, the original design requirement remains unchanged, sometimes for several decades, meaning
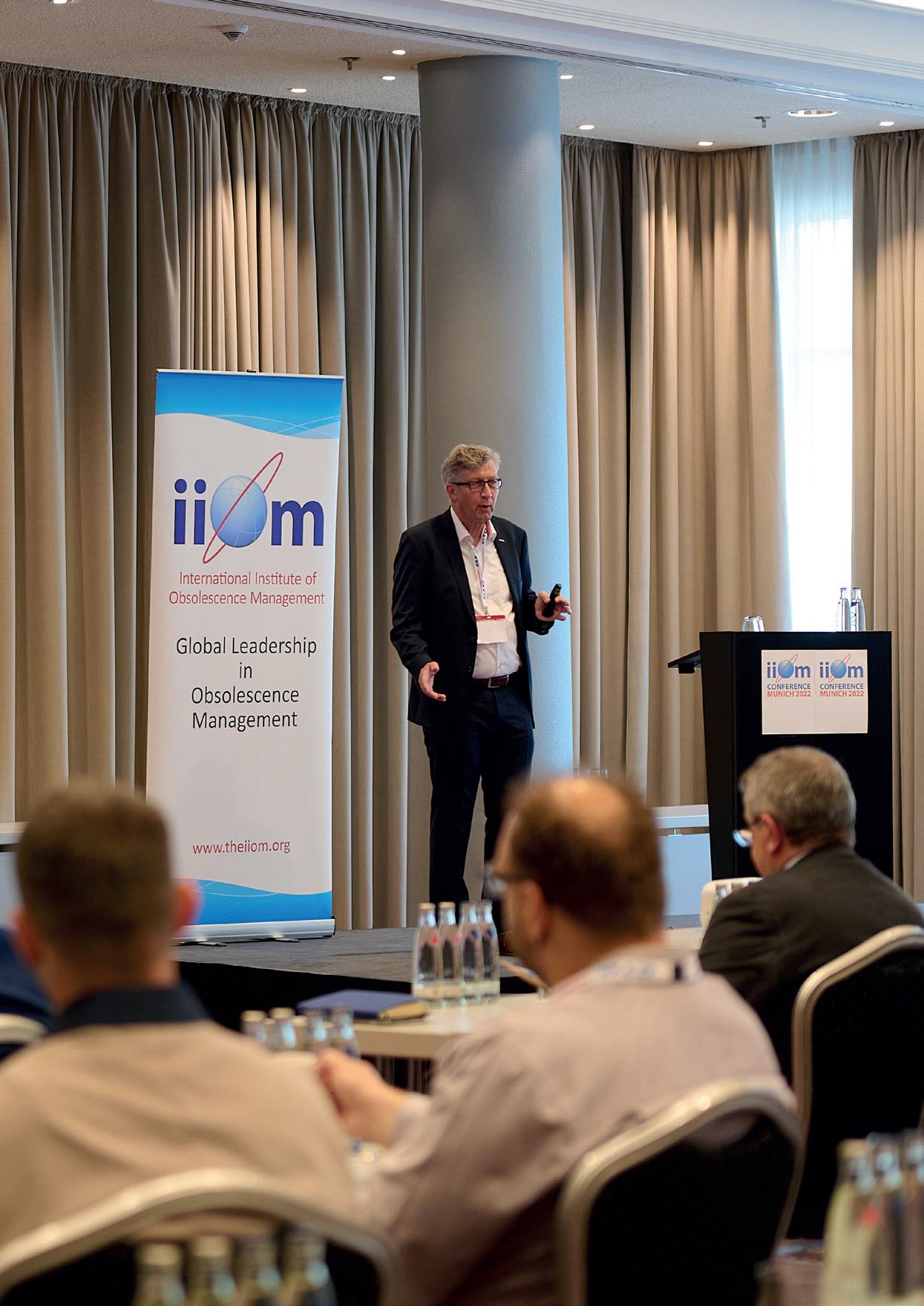
that proactive obsolescence management has become a necessity to ensure delivery to the customer in a cost effective and timely manner.
Organisations with good obsolescence management processes have been less affected by current supply chain issues, and companies in sectors such as automotive that were previously immune to obsolescence are employing engineers with obsolescence skills to develop their supply chain resilience.
In the International Standard IEC62402:2019, developed with a major contribution from IIOM members, obsolescence is defined as the nonavailability of parts that were previously available, but it is about much more than electronic components. For example, non-availability of materials, processes, skills, and software can occur at all stages of an equipment’s life cycle, such as development, design, production and in service. Using obsolescence management as a tool in an organisation creates an understanding of why this may happen and to plan and mitigate for these instances in the future. It is also now recognised as a vital part of support and through-life strategy by many progressive companies.
IIOM is the professional body for those involved in obsolescence management. The Institute is for professionals worldwide who wish to further their knowledge and understanding of the obsolescence management discipline, obtain professional recognition and network with like-minded individuals. The organisation welcomes corporate and individual members and has obsolescence solution providers among its corporate membership, as well as manufacturers and operators. These solution providers offer various obsolescence management services, including component monitoring; counterfeit avoidance; reverse engineering; sustainable solutions for obsolete designs; stocks of obsolete and end-oflife components; and training.
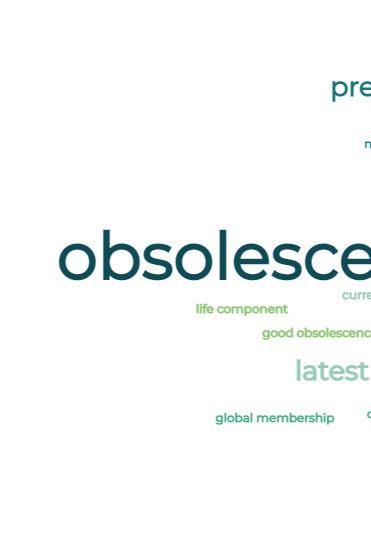
Formal obsolescence management training is available from IIOM endorsed trainers that offer online and in-person training at the introductory level, enabling successful trainees to become AIIOM (Associate) level. Experienced practitioners may opt to apply for MIIOM (Member) or FIIOM (Fellow) level accreditation if they have the appropriate experience. Regular meetings in each chapter country provide a mix of formal presentations and informal events at which obsolescence engineers, buyers and solution providers can exchange ideas—not just on obsolescence but also on key issues such as REACH, conflict minerals and counterfeiting. Meetings also provide access to suppliers of the latest tools and systems developed to support obsolescence monitoring and management.
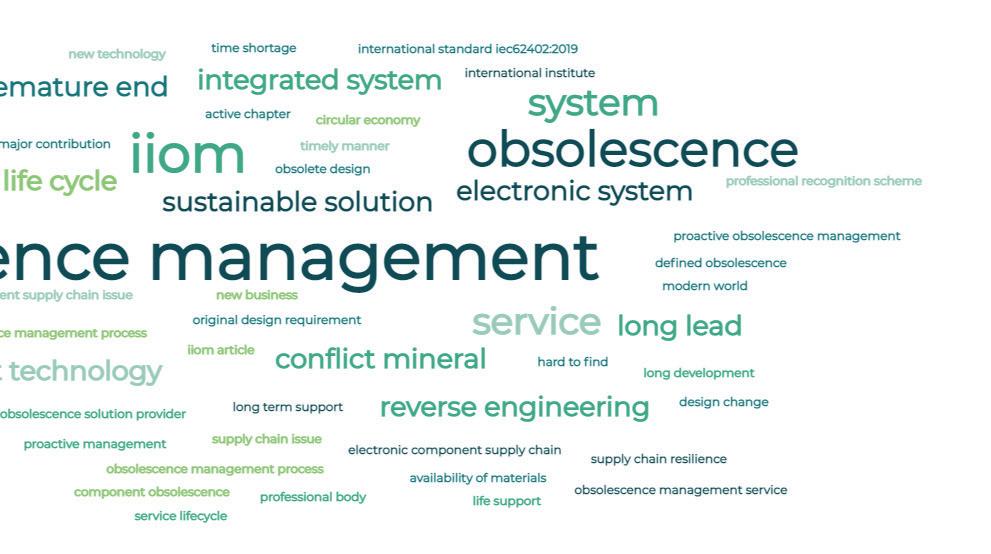
After a successful conference in Munich in May 2022, IIOM’s next international conference will be held in London in October 2023 and the call for papers will be issued soon.
Obsolescence is here to stay but you can manage the risk to your business. The good news is that with 25 years’ experience and a diverse membership, IIOM is here to help wherever you are. To join your local chapter, or to participate at the international conference, please contact the support team at admin@theiiom.org
You can follow IIOM on LinkedIn, subscribe to IIOM channel on YouTube and go to the website
www.theiiom.org
Right: Stuart Broadbent - IIom UK Chapter Chairman
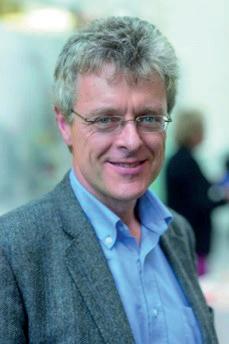