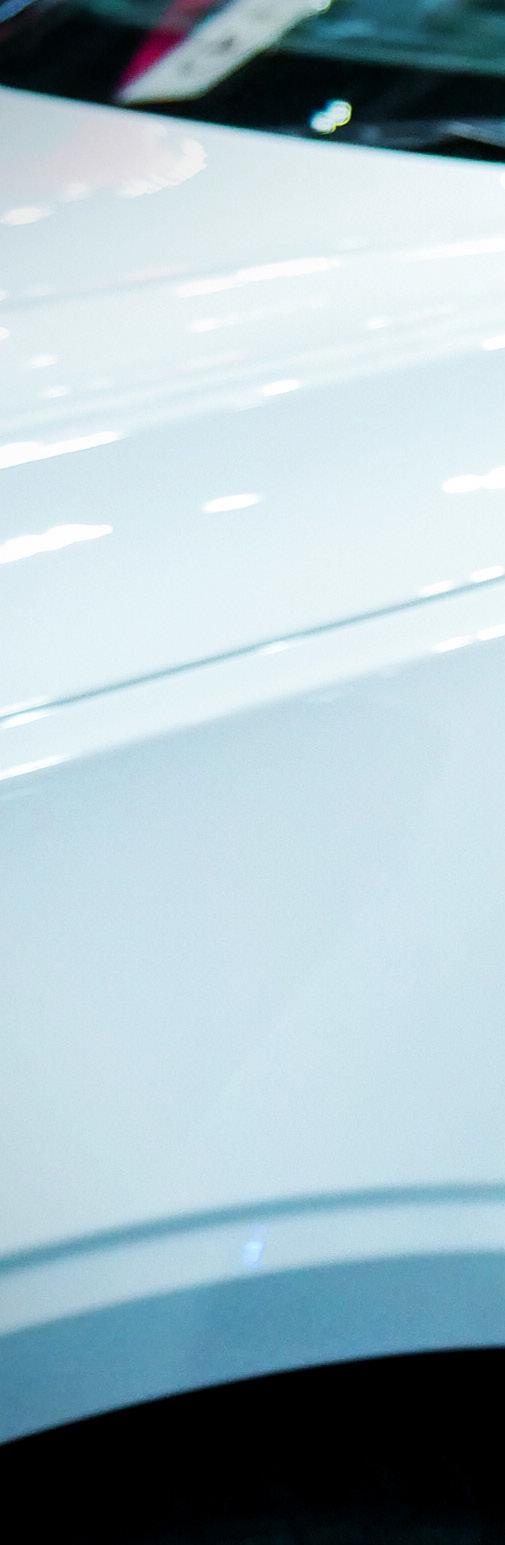
2 minute read
Driving Change – The Continuing Evolution of UV Curing Materials
UV conformal coatings have been gaining popularity since they were first introduced nearly twenty years ago. HumiSeal remains, at the cutting edge of developing and bringing these new types of materials to the market as replacements for water based and ultimately traditional solvent based coatings.
Though, as time moves on and technology evolves, conformal coating manufacturers must refine and develop new generations of these 100% solid materials to not only keep up with demand, but also anticipate future needs.
HumiSeal has recently announced the launch of its 3rd generation UV curing material line that meest these new industry demands, providing environmental protection to sensitive electronic assemblies.
Before we look at these innovative new products, let’s recap on what the drivers for change have been and how HUmiSeal materials have responded to these challenges.
2000 – 2010 | UV Generation 1 –Easy to use, high performance UV Materials
HumiSeal’s first generation UV curing materials were UV40 and UV40 250; the latter being developed specifically for swirl coating applications. They were easy to use and apply, displayed high chemical resistance properties, were rated to IPC- CC830, Mil-I plus UL-V0 and are still widely used to this day. But why were they developed?
Water-based coatings offered a convenient solution to the European Unions Volatile Organic Compound Directive 1999, but suffered from the fact that they took longer to cure and performance did not match that of classic solvent based coatings.
HumiSeal’s UV40, offered a route to significantly improve the quality of the conformal coating protection, whilst largely eliminating VOC emissions and yet dramatically increasing the speed of curing.
HumiSeal found that customers using its UV40 were able to reduce the floor space requirements of a typical coating curing cell by at least 50 percent using UV cure against conventional thermal ovens.
2010 – 2020 | UV Generation 2 –Improved Performance & Easier Application
Fast forward ten years and as technology evolved, a new generation of coating materials was needed. This included UV50, UV50LV, UV500 and UV500-2. But why move from a winning formula; what was the drive for improvement?
This product development was based on the requirements from the Automotive industry for extended T-Shock for coatings over lead free solder and up to 1000 hours of SIR testing.
The new products were built on the success of its highly successful and popular predecessors. They significantly increased performance to meet and exceed the stringent test requirements that were being introduced.
2020 – Present | UV Generation 3 – Highly Developed Materials, Unique Properties, Low Energy Cure & improved performance
With the recent introduction of our third generation UV curing materials, HumiSeal continues to anticipate and address the needs of the electronics industry.
What is driving this shift in performance characteristics now?
The introduction by volume automotive manufactures of electric powered vehicles and associated charging stations. Continued miniaturisation of PCB assemblies with introduction into ever more harsh environments, has resulted in a new generation of materials.
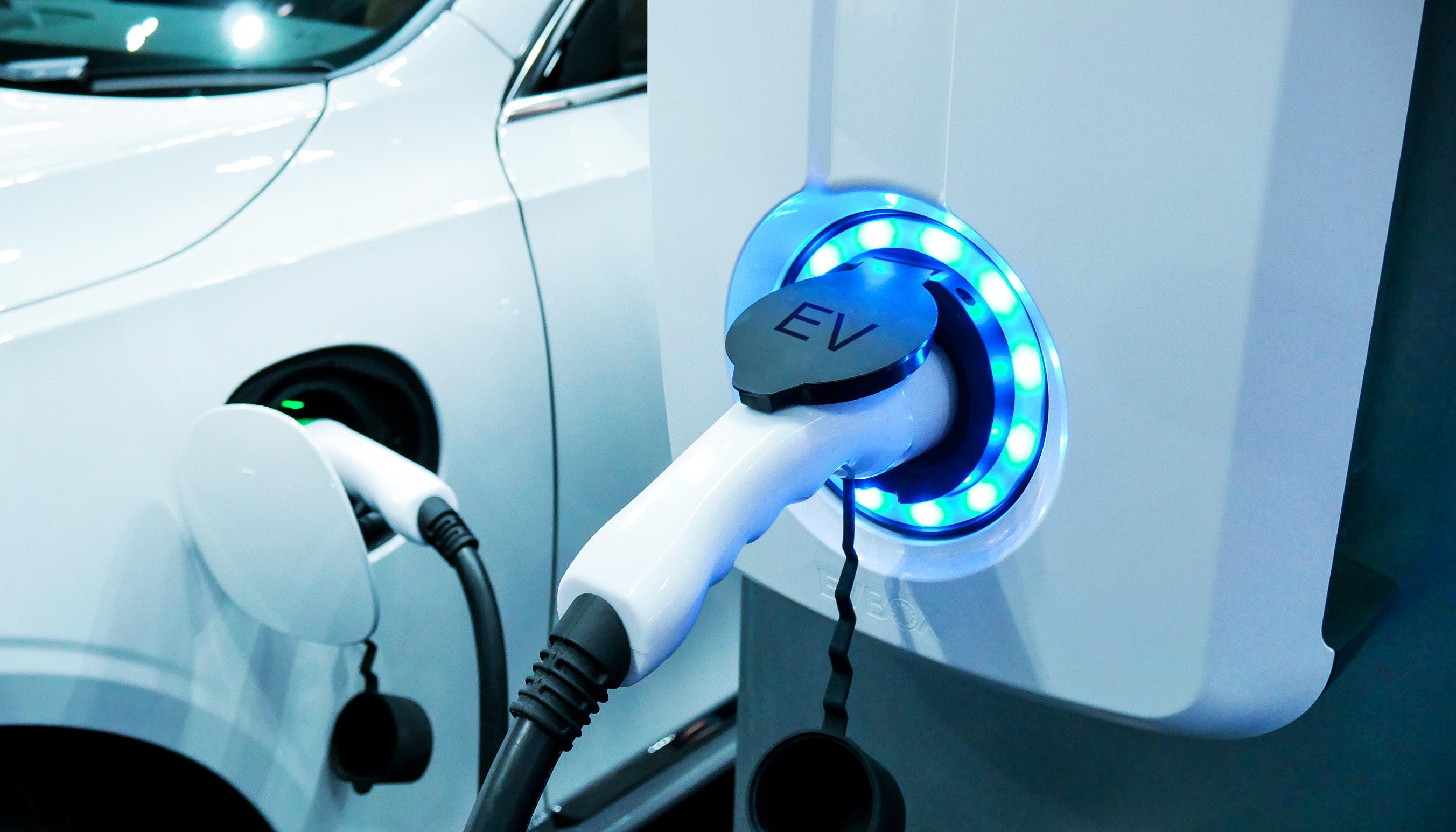