
3 minute read
TOP 20 PRODUCTS CARBON CONTRIBUTORS
This repurposing is roughly at the same cost as a new piece of furniture, depending on whether elements require new veneers or finishes. We emphasize the use of biogenic materials wherever possible. These materials can have long lifespans – such as solid wood items –or short lifespans – such as acoustic panels made of paper that can be readily composted after their useful life.
If a technological item is required, it should have a long service life and be fully reparable so that the item becomes an investment. Some items we have purchased for clients include a minimum resale value back to the manufacturer after a fixed term, to ensure the product cycle is continued. Certain elements lend themselves better to this methodology, such as materials that are made of a single material (as opposed to composites that are glued together) with the minimum number of parts. The more parts a product has, the less easily it is recycled or reused, due to the increased difficulty places the various parts in their correct process streams.
Whenever we specify casework or furniture, we request a full set of assembly and disassembly drawings. This discourages the use of glues, nails, rivets, and other destructive fasteners that damage the material, so elements of furniture can be easily repaired or rebuilt. Naturally, this leads to solutions that are more modular and can be readily repurposed for client needs.

When considering long-lifespan products, we need to know the ingredient list of the chemicals within the products, to ensure long term exposure to these materials will be non-toxic for human health. The most problematic chemicals are often found within surface finishes, paints and varnishes. Reporting the transparency of products is key, and avoiding products with high VOCs or Red List chemicals is crucial for ensuring human health.
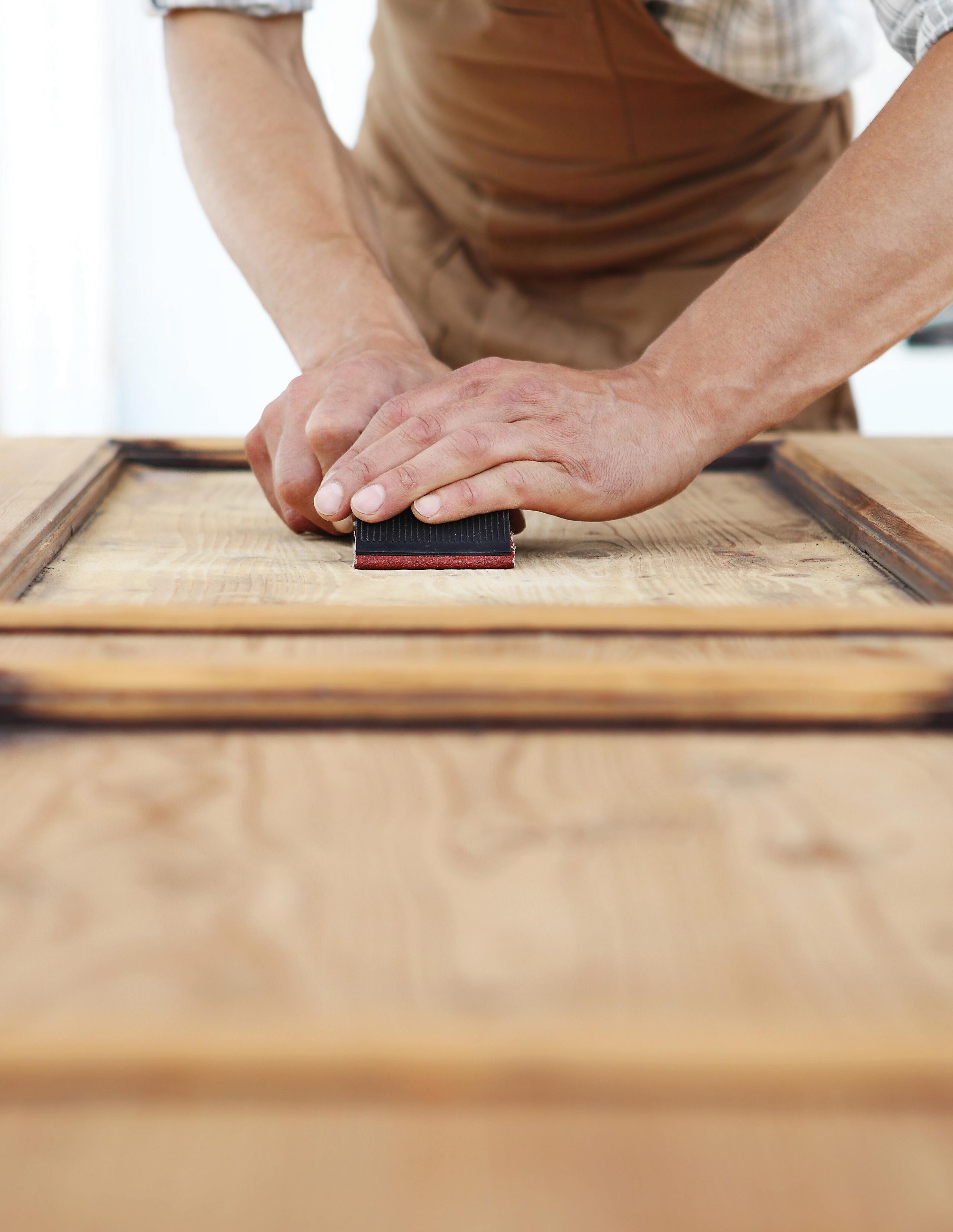
Specifying materials from sources as close as possible to the location of final use alleviates the burden of large fluctuations in component pricing. These fluctuations are becoming increasingly common, due to large supply chains which in many cases are global. By keeping the supply chain shorter, more certainty in pricing and delivery times can be obtained, allowing for design within a tighter (circular) loop.
We have encountered numerous barriers to this circular approach. Clients often request sequencing requirements when moving from one property to another, which has required us to demonstrate an order of operations to ensure that existing materials are preserved, restored, and delivered to the new location, rather than simply being discarded. Within our new designs, we have enhanced our Building Information Modeling to Building Asset Modeling, developing a live operations and maintenance manual that can be handed to facility managers. This requires each material to be recorded with passporting information - i.e. ingredients, remaining service life, end of life processes, structural properties, etc. to provide the next user/designer with enough information on its characteristics and properties to take it from this life cycle to the next.
The material information not only includes the physical attributes and ingredients, but also manufacturer contracts and the identification of which elements can be recycled into various material streams. This allows users to return the components to their point of origin, along with assisting in tracking manufacturer buyback prices as mentioned earlier. Some of this is included in the extended producer responsibility laws that we are now seeing emerge. This can be complemented with other alternate business models such as leasing and maintenance contracts, allowing products to be “rented” long-term and returned when no longer needed. Transitioning to a fully circular economy will require new ways of thinking. The notion of “possessions” needs to be dissolved. We must move away from thinking we are owners of products, and rather view ourselves as custodians, caring for the materials until they can be handed over to someone who will find the material more useful. This hand-off should occur regardless of the financial transaction that accompanies it. By implementing the strategies described above, we are seeing the carbon balance (rather than thinking of a static carbon figure, even if it is split into life cycle stages) of our new fit outs to be in the region of a 70% reduction compared to a business-as-usual model.
This new thinking is not without its consequences on aesthetics. It often requires the use of more natural materials and colors, and a close examination of potential failure points, such as fasteners. Fasteners pose several pitfalls: firstly, exposed fasteners present problems with security, as they are more easily tampered with or removed. Specialized fasteners – such as screws with star or allen heads –lead to the risk that items are not disassembled properly at the end of their service life. As a rule, we specify standard fasteners –Phillips or flat head screws – but recommend concealing them. This approach allows the products to be readily taken apart, but requires instructions to do so properly, which ensures careful disassembly. We are now designing with remanufactured client furniture alongside a mix of vintage pieces, complemented with robust new products that have good design elements and information to make sure they are fit for their next life. We hope to apply this methodology of circular economy in all our future work, not just in interior retrofits.
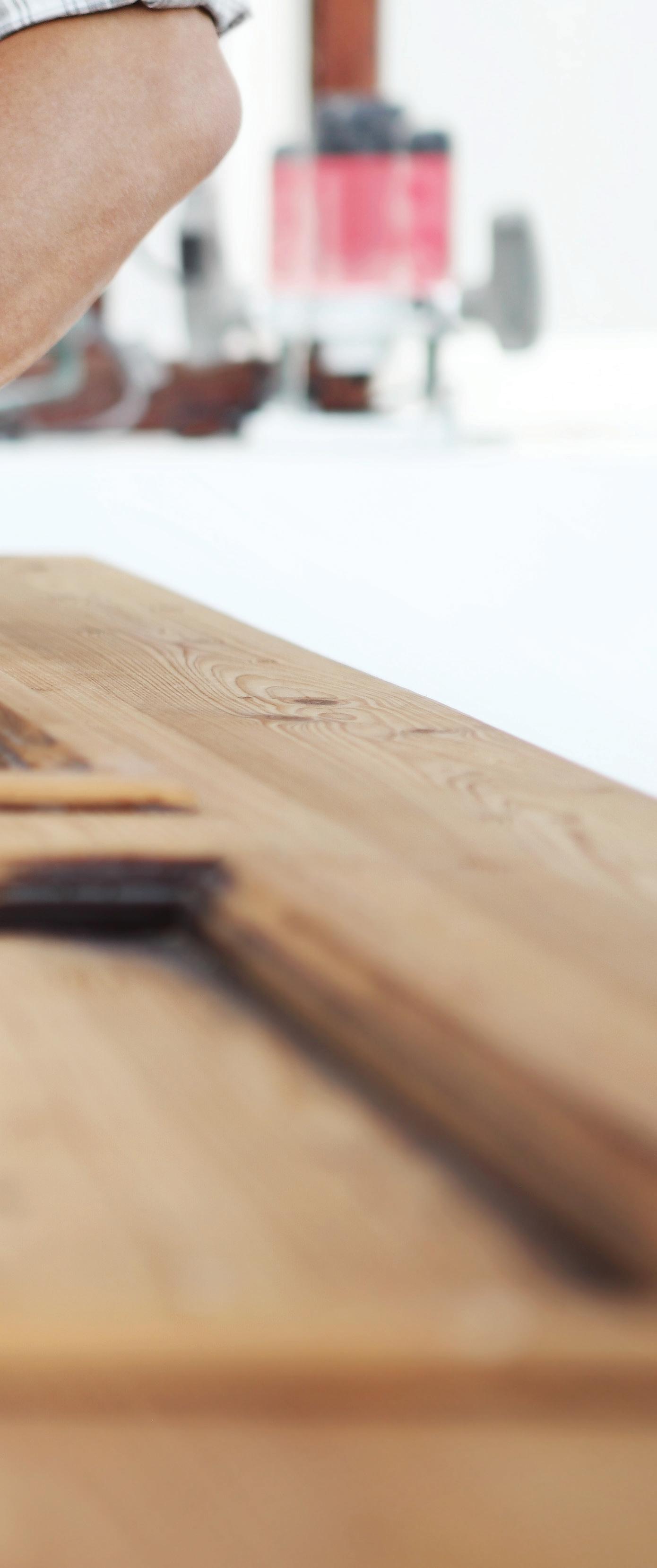
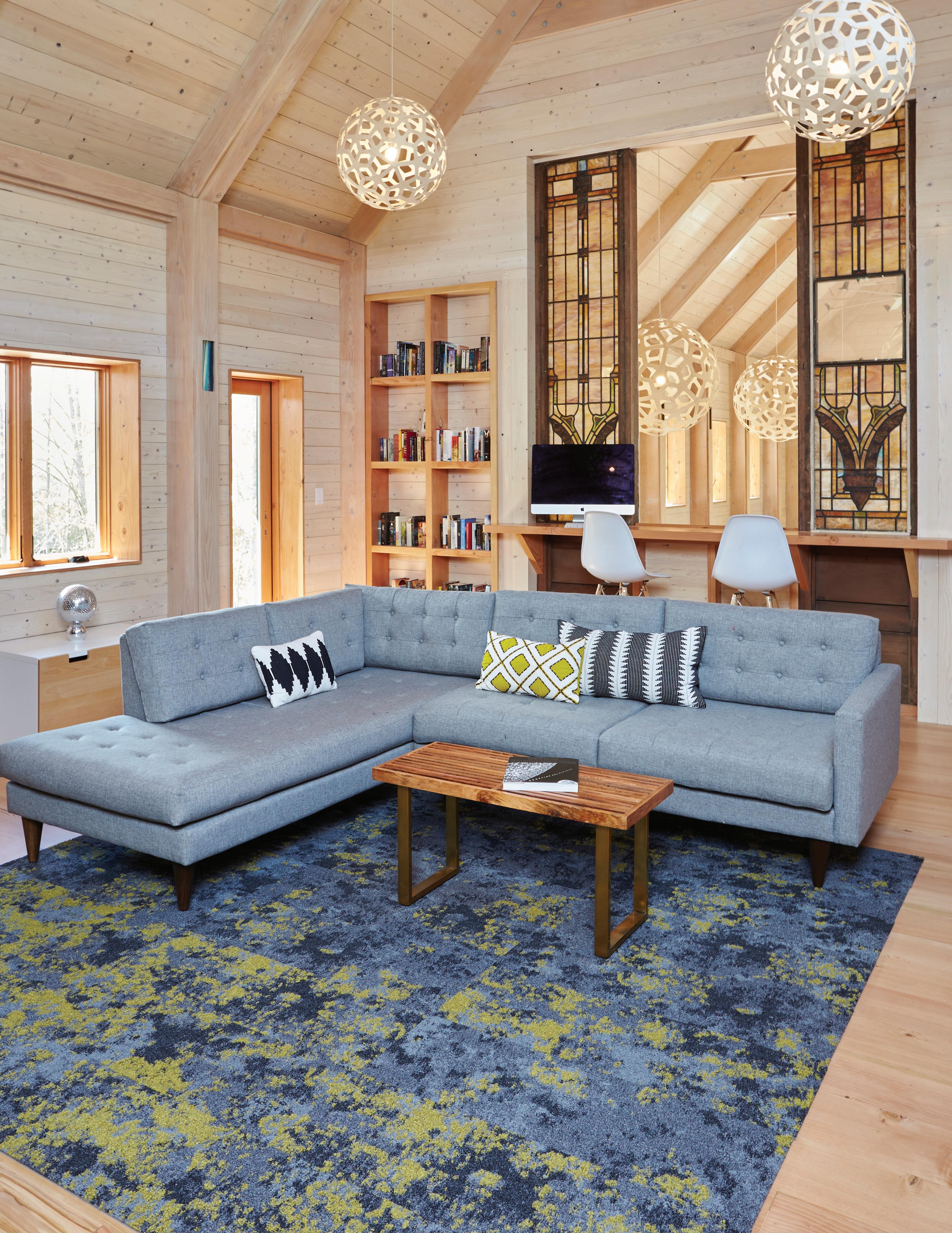